精益生产基本理论
生产八大理念有哪些.doc
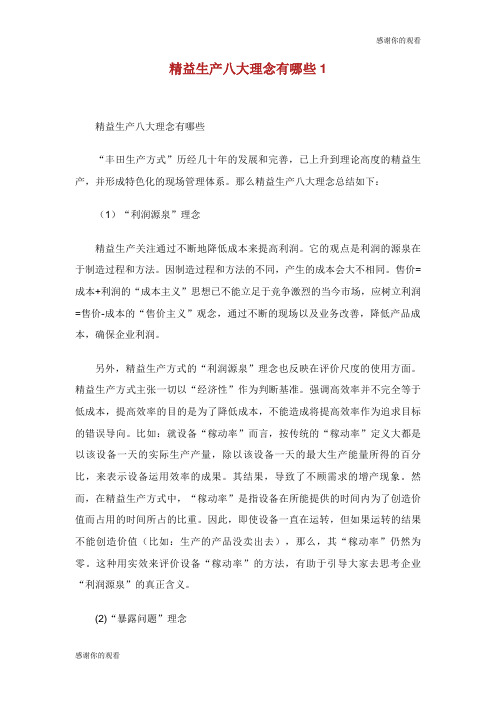
精益生产八大理念有哪些1精益生产八大理念有哪些“丰田生产方式”历经几十年的发展和完善,已上升到理论高度的精益生产,并形成特色化的现场管理体系。
那么精益生产八大理念总结如下:(1)“利润源泉”理念精益生产关注通过不断地降低成本来提高利润。
它的观点是利润的源泉在于制造过程和方法。
因制造过程和方法的不同,产生的成本会大不相同。
售价=成本+利润的“成本主义”思想已不能立足于竞争激烈的当今市场,应树立利润=售价-成本的“售价主义”观念,通过不断的现场以及业务改善,降低产品成本,确保企业利润。
另外,精益生产方式的“利润源泉”理念也反映在评价尺度的使用方面。
精益生产方式主张一切以“经济性”作为判断基准。
强调高效率并不完全等于低成本,提高效率的目的是为了降低成本,不能造成将提高效率作为追求目标的错误导向。
比如:就设备“稼动率”而言,按传统的“稼动率”定义大都是以该设备一天的实际生产产量,除以该设备一天的最大生产能量所得的百分比,来表示设备运用效率的成果。
其结果,导致了不顾需求的增产现象。
然而,在精益生产方式中,“稼动率”是指设备在所能提供的时间内为了创造价值而占用的时间所占的比重。
因此,即使设备一直在运转,但如果运转的结果不能创造价值(比如:生产的产品没卖出去),那么,其“稼动率”仍然为零。
这种用实效来评价设备“稼动率”的方法,有助于引导大家去思考企业“利润源泉”的真正含义。
(2)“暴露问题”理念精益生产方式非常强调问题的再现化。
即将潜伏着的问题点全都暴露出来,以便进一步改善。
其中采用的手段主要包括:不许过剩生产,追求零库存,目视管理,停线制度等。
过剩生产和库存的浪费与其他浪费是有本质性区别的。
因为这两者浪费因埋没其他真正的问题点,会阻碍对问题的实质性改善。
比如:本因业务流程以及协调机制设计的不合理,出现一些作业或业务的停滞等待现象。
这时,如果为了避免停滞等待的浪费进行过剩生产的话,反而把因业务设计不合理而造成的真正问题点给掩盖起来。
精益生产基础知识
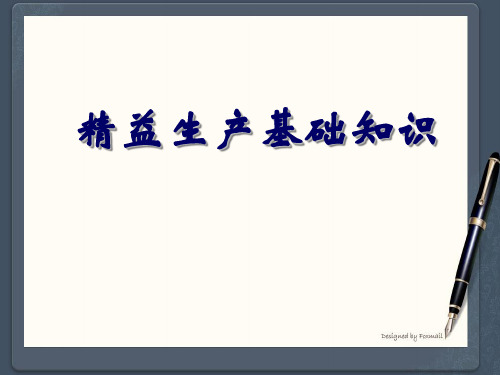
2007-6-7 工业革命
1775(英)
1868(日)
1918 77年工业化历史
1945
1978 62年
29年
2007
139年工业化历史
什么是丰田生产方式,就是丰田式工业工程。 (20世纪)五十年代全日本都在研究和学习美 国的工业工程这种赚钱的工具”
2.、IE的五个意识 问题意识:最大的问题是能否看到和提出问题。 效率意识:提高效率是IE 的基本任务。 成本意识: 降低成本是永恒的追求。 质量意识:追求完美之中质量是灵魂。 改善意识:就是创新,永五休止的创新。 IE意识→IE的理念,所以精益的概念、消除 浪费的概念都由此而来。
十、开展准时化生产方式10步: 第一步:领导决策,统一认识,制定规划。 第二步:,明确思想,清楚内涵,,了解实 施难点、要点 第三步:全员讨论,现状,有针对性地提 出实施意见、措施和办法。 第四步:设立实领导小组和办公室, 制定方案规划,,逐步实施准时化生产。 第五步:深入持久地开展生产现场达 标活动。 第六步:改进生产线布置,采用U 型线实行“一个流”生产或多品种混 流 生产。 第七步:在实施中研析总结具体业务 上的问题,边实践,边巩固,边提高。 第八步:进行现场管理准时化条 件的分析并进行不断改进和完善。 第九步:总结并评价。由试点开始 逐步全面铺开,继续巩固完善。 第十步:在本企业实行准时化生 产的条件下逐步推广到协作配套厂, 达到主机厂、协作配套厂同步实施准 时化生产。
四 精益基础词汇
JIT改善基本原则介绍

JIT改善基本原则介绍简介精益生产(Just-In-Time,简称JIT)是一种极具效率和灵活性的生产管理方法,它的核心理念是在生产过程中实现零库存、及时生产和交付,从而最大限度地减少浪费、提高生产效率和产品质量。
本文将介绍JIT改善的基本原则,包括其理论基础、实施方法以及相关案例分析。
JIT改善的基本原则1. 消除浪费(Muda)JIT改善的首要原则是消除一切形式的浪费,包括物料、人力、时间和能源等资源的浪费。
其中,日常生产中出现的七种浪费包括:•运输•库存•过程•等待•过度生产•运动•不合格品消除浪费的最终目标是实现价值流的优化和最大化。
2. 建立拉动生产JIT改善强调通过拉动生产方式,根据顾客需求进行生产,实现零库存的目标。
拉动生产系统通过顾客订单触发生产,避免了过量生产和库存积压,有利于降低生产成本和提高生产效率。
3. 建立流程改善JIT改善提倡不断优化生产流程,减少不必要的手工操作和物料运输,提高生产流程的连续性和稳定性。
通过价值流分析和流程改善,可以识别和消除生产过程中的瓶颈、阻塞和浪费,实现生产过程的流畅化和优化。
4. 实施稳定的生产计划JIT改善要求建立稳定的生产计划,确保生产节奏与顾客需求之间的平衡。
通过实施合理的生产计划和物料供应计划,可以避免生产过程中的紧急加工和库存淤积,确保生产过程的稳定性和可控性。
JIT改善的实施方法1. 价值流分析通过价值流分析,对生产过程中的价值流进行细致分析,识别和消除生产过程中的浪费,优化价值流,提高生产效率和质量。
2. 精益生产工具应用JIT改善借助精益生产工具,如5S整理、持续改善(Kaizen)、标准化工作等,促进生产的精益化和高效化。
3. 员工参与和培训JIT改善强调员工参与和培训的重要性,倡导建立团队合作和员工自治的生产文化,激发员工的创造力和工作热情。
4. 度量与持续改善JIT改善要求建立有效的生产绩效度量体系,实时监控生产过程的关键绩效指标,及时发现问题和改进空间,持续不断地优化生产过程。
精益生产五大原则
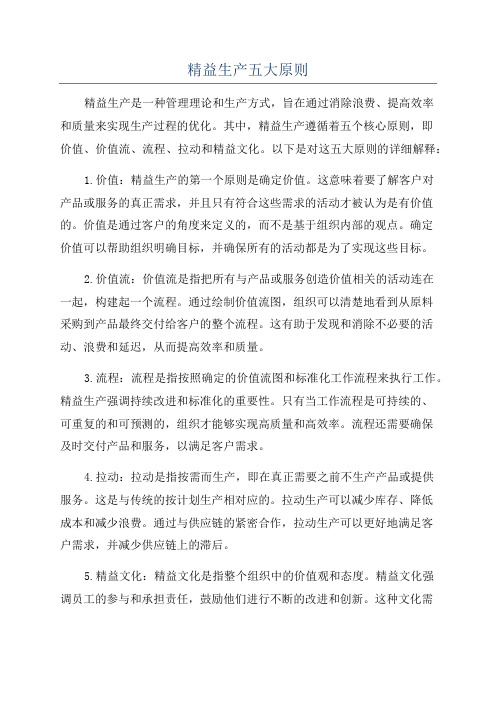
精益生产五大原则精益生产是一种管理理论和生产方式,旨在通过消除浪费、提高效率和质量来实现生产过程的优化。
其中,精益生产遵循着五个核心原则,即价值、价值流、流程、拉动和精益文化。
以下是对这五大原则的详细解释:1.价值:精益生产的第一个原则是确定价值。
这意味着要了解客户对产品或服务的真正需求,并且只有符合这些需求的活动才被认为是有价值的。
价值是通过客户的角度来定义的,而不是基于组织内部的观点。
确定价值可以帮助组织明确目标,并确保所有的活动都是为了实现这些目标。
2.价值流:价值流是指把所有与产品或服务创造价值相关的活动连在一起,构建起一个流程。
通过绘制价值流图,组织可以清楚地看到从原料采购到产品最终交付给客户的整个流程。
这有助于发现和消除不必要的活动、浪费和延迟,从而提高效率和质量。
3.流程:流程是指按照确定的价值流图和标准化工作流程来执行工作。
精益生产强调持续改进和标准化的重要性。
只有当工作流程是可持续的、可重复的和可预测的,组织才能够实现高质量和高效率。
流程还需要确保及时交付产品和服务,以满足客户需求。
4.拉动:拉动是指按需而生产,即在真正需要之前不生产产品或提供服务。
这是与传统的按计划生产相对应的。
拉动生产可以减少库存、降低成本和减少浪费。
通过与供应链的紧密合作,拉动生产可以更好地满足客户需求,并减少供应链上的滞后。
5.精益文化:精益文化是指整个组织中的价值观和态度。
精益文化强调员工的参与和承担责任,鼓励他们进行不断的改进和创新。
这种文化需要建立一个学习型组织,员工可以自由地提出问题和提出建议,同时也面对错误和挑战。
这五大原则是精益生产的核心价值和基本原则。
通过遵循这些原则,组织可以实现更高效、更质量和更具竞争力的生产过程。
精益生产不仅可以应用于制造业,也可以应用于其他各个行业,如服务业、医疗保健等。
无论是哪个行业,只要能够遵循和应用这些原则,都能够实现生产过程的优化和改进。
数控机械加工厂精益生产管理实践应用

数控机械加工厂精益生产管理实践应用数控机械加工是一种高精度、高效率的机械加工方式,已经成为现代制造业中不可缺少的重要环节。
在数控机械加工厂中,如何实现精益生产管理,提高生产效率和产品质量,是一项非常重要的课题。
本文将从精益生产管理的理论基础和实践应用角度,对数控机械加工厂精益生产管理进行探讨。
一、精益生产管理的理论基础精益生产管理,又称精益生产或精益制造,是源自于丰田生产方式的一种管理方法。
它的核心思想是通过消除浪费,提高生产效率和产品质量,实现生产过程的精益化,通过不断改善来推动企业持续发展。
精益生产管理的基本原则包括价值流分析、流程优化、持续改善和人员培训等,旨在实现高效率、低成本、高质量的生产目标。
1. 价值流分析价值流分析是精益生产管理的重要工具之一,通过对生产过程中的价值流进行分析,找出其中的浪费并进行改善。
在数控机械加工厂中,价值流分析可以从订单接收、生产加工、质量检验、产品包装等环节进行分析,找出各个环节中存在的浪费和不必要的环节,进而进行改善。
通过对价值流分析,可以发现数控机械加工厂生产过程中存在的各种浪费,如待机时间过长、机床设置调整时间长、工件运输环节不畅等问题。
在价值流分析的基础上,可以对这些问题进行改善,如优化生产计划,调整生产线布局,改善工艺流程等,从而提高生产效率和产品质量。
2. 流程优化流程优化是精益生产管理的核心之一,通过对生产流程进行优化,减少不必要的环节和浪费,提高生产效率和产品质量。
在数控机械加工厂中,流程优化可以从生产计划、工艺流程、设备配置等方面进行优化。
在生产计划方面,可以通过对订单需求进行统一排产,避免因为来料不齐导致的空闲时间和过载时间。
在工艺流程方面,可以通过对传统工艺流程进行改进和优化,采用更加有效的加工方法和技术,提高加工效率和产品质量。
在设备配置方面,可以对数控机床的布局和配置进行调整,避免机床空间的浪费和机床设置调整时间过长等问题。
3. 持续改善持续改善可以通过制定改善计划、开展改善活动、进行改善验收等方式进行,可以在生产过程中逐步进行改进,从而实现持续改善。
精益生产八大理念有哪些.doc
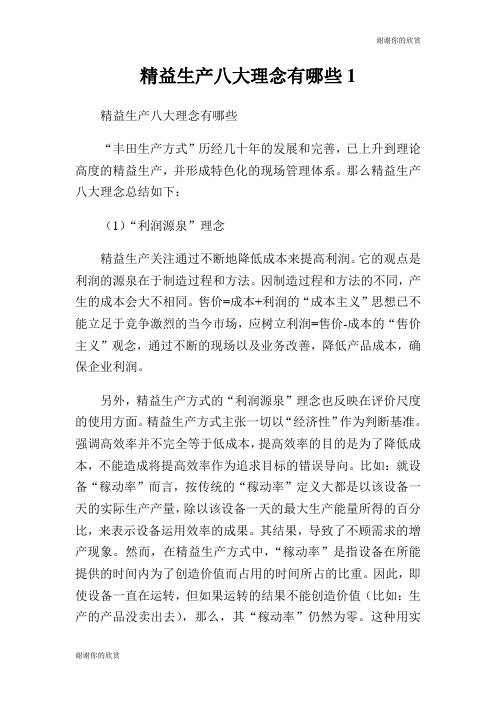
精益生产八大理念有哪些1精益生产八大理念有哪些“丰田生产方式”历经几十年的发展和完善,已上升到理论高度的精益生产,并形成特色化的现场管理体系。
那么精益生产八大理念总结如下:(1)“利润源泉”理念精益生产关注通过不断地降低成本来提高利润。
它的观点是利润的源泉在于制造过程和方法。
因制造过程和方法的不同,产生的成本会大不相同。
售价=成本+利润的“成本主义”思想已不能立足于竞争激烈的当今市场,应树立利润=售价-成本的“售价主义”观念,通过不断的现场以及业务改善,降低产品成本,确保企业利润。
另外,精益生产方式的“利润源泉”理念也反映在评价尺度的使用方面。
精益生产方式主张一切以“经济性”作为判断基准。
强调高效率并不完全等于低成本,提高效率的目的是为了降低成本,不能造成将提高效率作为追求目标的错误导向。
比如:就设备“稼动率”而言,按传统的“稼动率”定义大都是以该设备一天的实际生产产量,除以该设备一天的最大生产能量所得的百分比,来表示设备运用效率的成果。
其结果,导致了不顾需求的增产现象。
然而,在精益生产方式中,“稼动率”是指设备在所能提供的时间内为了创造价值而占用的时间所占的比重。
因此,即使设备一直在运转,但如果运转的结果不能创造价值(比如:生产的产品没卖出去),那么,其“稼动率”仍然为零。
这种用实效来评价设备“稼动率”的方法,有助于引导大家去思考企业“利润源泉”的真正含义。
(2)“暴露问题”理念精益生产方式非常强调问题的再现化。
即将潜伏着的问题点全都暴露出来,以便进一步改善。
其中采用的手段主要包括:不许过剩生产,追求零库存,目视管理,停线制度等。
过剩生产和库存的浪费与其他浪费是有本质性区别的。
因为这两者浪费因埋没其他真正的问题点,会阻碍对问题的实质性改善。
比如:本因业务流程以及协调机制设计的不合理,出现一些作业或业务的停滞等待现象。
这时,如果为了避免停滞等待的浪费进行过剩生产的话,反而把因业务设计不合理而造成的真正问题点给掩盖起来。
精益理论框架课件
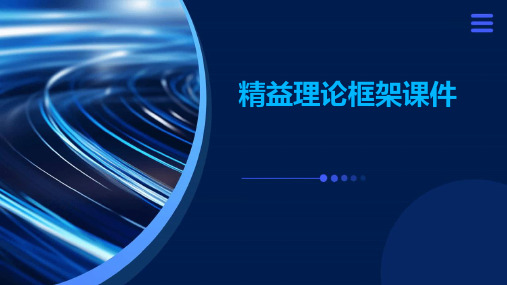
资源利用:传统管理往往存在资源闲置 和浪费,精益管理强调资源的有效利用 。
员工角色:传统管理中员工往往只是执 行者,精益管理鼓励员工参与改进和创 新。
02
CATALOGUE
精益理论框架的核心元素
价值流分析
01
02
03
定义
价值流分析是精益理论中 的一个重要工具,用于识 别、分析和优化生产过程 中的价值流动。
目的
通过消除浪费、提高效率 ,以最小的成本、最短的 时间为客户提供最大的价 值。
实施步骤
包括绘制价值流图,识别 增值活动和非增值活动, 制定改进措施等。
持续改进
定义
持续改进是精益理论中的一个核 心理念,强调在不断地寻求、实 施小的改进中,实现长期的、显
著的成果。
目的
通过持续改进,企业能够逐渐消除 浪费,提升效率,提高产品质量, 增强竞争力。
精益管理的基本理念和原则
基本理念
持续改进、尊重员工、客户至上。
原则
消除浪费、流程优化、拉动式生产、持续改进、全员参与。
精益管理与传统管理的比较
目标导向:传统管理重视计划和预算, 精益管理关注持续改进和适应变化。
以上内容仅为初步扩展,每个子标题下 可根据实际需求进一步丰富和完善内容 。
客户关系:传统管理可能更关注产品本 身而非客户需求,精益管理则强调满足 客户需求和建立长期关系。
04
CATALOGUE
精益理论框架的应用与拓展
精益理论框架在制造业的应用
生产流程优化
通过精益理论框架指导,制造业 企业可以消除生产浪费,提升生 产效率,实现流程的优化和再造
。
质量管理提升
精益理论框架强调质量是制造出 来的而非检验出来的,企业可以 通过持续改进生产过程中的质量 问题,提升整体质量管理水平。
精益生产理论基本知识
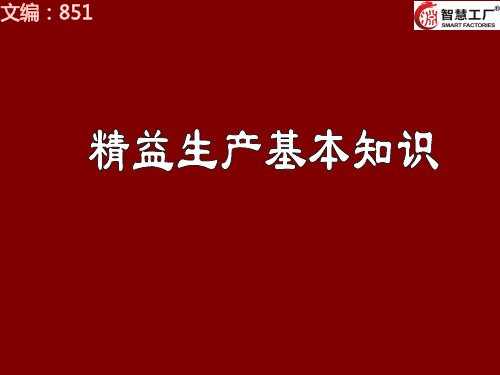
二、精益生产内容简介
准时化
必要的物品-5s 必要的时间-提高效率 必要的数量-减少库存 (专线生产和拉动生产)
丰田生产方式
准
自
时
働
化
化
5s/标准化作业
停线,暴露生产问题
停线
生产线的再启动
找出不良原因,制定对策 •防止再发备智能化 •后工序是前工序的上帝 -服务意识 •产品质量是由各个工序 创造的-生产质量是生产 出来的而不是检验出来的
897.2万辆 835万辆 623万辆
420万辆 378.3万辆 370.8万辆 295.2万辆 262.4万辆 238.2万辆
2007全球销量排名 1. 通用 2. 丰田 3. 大众 4. 福特 5. 现代起亚 6. 本田 7. 日产 8. PSA 9. 克莱斯勒 10. 菲亚特
936.9万辆 936.6万辆 619.2万辆 596.4万辆 396.2万辆 376.7万辆 367.6万辆 342.8万辆 267.6万辆 262.1万辆
不到银行融资便会倒闭、被人收购的境地。 银行答应提供资金,但有附加条件: “分离销售公司”与“裁减过剩人员”。 丰田喜一郎对分离销售公司可以忍痛接受;但他以前宣布过不裁员,既不想
放弃对员工的承诺,也不想放弃重建公司的机会。而工会方面认为“公司肯 定裁员”,在4月7日开始实行罢工。丰田面临进退两难的处境,发表了包括 “募集1600名自愿辞职员工”内容的重建方案。在此期间,丰田的汽车产量 直线下降、公司每天亏损惨重,丰田喜一郎主动承担领导责任、6月5日毅然 决定辞去总经理职务,此后1700名员工自愿辞职。 6月10日,历时二个月的罢工终于结束,丰田恢复正常生产。 留下的经营者和全体员工痛定思痛,决不想让悲剧重演,在大野耐一的领导、 推进下产生了准时化生产方式、加上自働化,进而产生了TPS 。 TPS : Toyota’s Production System
- 1、下载文档前请自行甄别文档内容的完整性,平台不提供额外的编辑、内容补充、找答案等附加服务。
- 2、"仅部分预览"的文档,不可在线预览部分如存在完整性等问题,可反馈申请退款(可完整预览的文档不适用该条件!)。
- 3、如文档侵犯您的权益,请联系客服反馈,我们会尽快为您处理(人工客服工作时间:9:00-18:30)。
6
Sequential Application of Tools 工具运用的顺序
Degree
of
Change +
Impact
变化 程度 + 影响
Time 时间 价值流是基础
GBE-KPO-2-001 Lean Basic 2 Rev.03
7
Heijunka 平准化
Level Loading 平衡生产
Heijunka is a Forcing Function平准化是强制作用
GBE-KPO-2-001 Lean Basic 2 Rev.03
10
Heijunka 平准化
生产控制 客户需求
更加平衡的生产 客户
节拍控制点
•单个计划控制点 •下游流程化
成品仓
Pacemaker Sets the Pace for Upstream Processes 节拍控制点决定上游流程的速度。
Байду номын сангаас
Stop @
Abnormality 异常停止 Autonomation 自动化 Sequencing 作业顺序
Single Piece Flow
单片流 Takt Time Production 节拍生产 Level Loading 平衡生产
GBE-KPO-2-001 Lean Basic 2 Rev.03
GBE-KPO-2-001 Lean Basic 2 Rev.03
4
Objective 目标
•
Introduce Flextronics Lean Enterprise (FLE) and its elements 伟创力精益企业介绍和它的要素 • Heijunka 平准化
• Guide to Level Load 平衡生产简介
GBE-KPO-2-001 Lean Basic 2 Rev.03
3
Overview & Scope
• Lean Manufacturing is a generic process management philosophy derived mostly from the Toyota Production System (TPS) but also from other sources.It is renowned for its focus on reduction of ‘Seven Wastes' in order to improve overall customer value. 精益生产 是一门流程管理哲学,主要来自于丰田制造系统(TPS)。其焦点在如何减少“7大浪费”以 增加客户价值。 • Toyota's achievement made "Lean" a hot topic in management science in the first decade of the 21st century.
很显然,客户的需求不可能保持不变。为了满足客户的需求,你必须通过平衡生产数量 和种类来达到拉式生产。
GBE-KPO-2-001 Lean Basic 2 Rev.03
14
From Batch to Pull 从批量生产到拉式生产
Flextronics Lean Enterprise : Answer to ‘Load & Chase’
Lean Training
Lean Basic 2
Design. Build. Ship. Service. Business Excellence
GBE-KPO-2-001 Lean Basic 2 Rev.03
1
Version Control
Document Title: Lean Basics 2 Revision: 03 Document# GBE-KPO-2-002-00 Document Owner: Chuah Khar Yee APPROVALS NAME Ganesh Maniam TITLE Director DEPT NAME Global Business Excellence Organizaation: Global Business Excellence Effective Date: December 11. 2008
GBE-KPO-2-001 Lean Basic 2 Rev.03
9
Heijunka 平准化
Leveled production 平衡生产
Customer Demand 客户需求
• How Can a Shop Resource This ?车间怎样规划? • How Can the Supply Chain Cope ? 供应链如何整合? • What if the Supply Chain is Global ?如果是全球供应链又怎样?
Stop @
Abnormality 异常停止 Autonomation 自动化 Sequencing 作业顺序
Level Loading = Process of smoothing the overall schedule by more frequent mixing of High & Low volume Sequencing = The order in which the parts on a multi-product line or cell are processed.
REVISION 03
REVISION HISTORY DESCRIPTION OF CHANGE Document formatted as per DMS policy
ORIGINATOR Chuah Khar Yee
This document is proprietary and confidential property of flextronics.
Key Elements of Level-scheduling 均衡计划的要素
Production units are stratified according to planned sales volume 按销售额将产品分类
The production sequence combines Build To Order (BTO) and Customer Forecast
GBE-KPO-2-001 Lean Basic 2 Rev.03
2
Table of Contents
Contents Slide(s)
Overview & Scope Objective 目标
概述和范围
3 4 伟创力精益型企业 5
The Flextronics Lean Enterprise (FLE)
•
丰田的成功使“精益”成为21世纪前10年管理科学的热点。
•Lean Manufacturing can be defined as 精益可以被定义为: "A systematic approach to identifying and eliminating waste (non-value-added activities) through continuous improvement by flowing the product at the pull of the customer in pursuit of perfection.“ “从客户拉货到产品源头的整个流程不断改善,识别并消除浪费(无价值活动),使之日臻 完善的一种系统方法。“
原材料超市只存储小批量产品的库存。
Fill orders first from FG, second WIP, & third sequence them (attach the order to the production plan) 从成品开始排单,然后是在制库存,最后将其序列化(排单附于生产计划上)
生产顺序由根据定单生产和根据客户需求来生产两种
Sequence is designed to achieve the combined TAKT time for all items
生产顺序应该可以满足所有产品的节拍时间
Eliminating production rate variance is required to achieve TAKT time 消除产品变化的差异是达到节拍时间的前提 Build only high volume products to FG supermarket based on business model 根据产品形态,对大量生产的品种,可在成品仓留有库存。 Lower volume items are only sequenced with firm orders小批量产品在定单不确定时不排入生产。 Hold components in Raw Materials supermarket only for low volume items.
Heijunka
平准化
7
11 17 节拍生产 23
Guide to Level Load Guide to Sequencing Takt Time Production
Single Piece Flow
Standard Work Tools for 3P
单片流
标准作业
30
38 45 50 54
Pull Production 拉式生产 Kanban System 看板系统
GBE-KPO-2-001 Lean Basic 2 Rev.03
11
Guide to Level Load
GBE-KPO-2-001 Lean Basic 2 Rev.03
12
Guide to Level Load
Purpose目的: To provide guidelines for developing the method and tools for level-loading (or level-scheduling) the shop floor.为生产现场实施均衡化生产(或均衡计划)提供指导。