汽车内饰件产品材料工艺汇总
10大汽车内外饰常用工艺方法5

10大汽车内外饰常用工艺方法510大汽车内外饰常用工艺方法5汽车内外饰常用工艺方法是指在汽车生产过程中,为了美化和提升汽车的品质,采用各种工艺方法进行处理的过程。
下面是10大汽车内外饰常用工艺方法的前5个:1.电泳涂装电泳涂装是一种常见的汽车外饰工艺方法,它采用直流电场作用下的电解作用原理,将涂装颜料均匀附着在汽车金属表面上。
通过电泳涂装,可以保证涂层的均匀性和附着力,同时还能提高汽车的耐腐蚀性和耐磨性。
电泳涂装工艺还可以实现环保生产,因为它不需要使用有机溶剂,减少了对环境的污染。
2.喷涂工艺喷涂工艺是汽车内外饰中常用的一种工艺方法,通过喷枪将涂料喷射在汽车表面上,形成均匀的涂层。
喷涂工艺可以实现丰富的颜色选择,同时还能够增加汽车的光泽度和耐久性。
在喷涂工艺中,还可以采用多种喷涂技术,如隐形喷涂、喷绘等,以满足消费者对个性化汽车外观的需求。
3.冲压成型冲压成型是汽车内饰常用的一种工艺方法,通过将金属板料放置在冲压模具中,利用冲压机的力量将其形成所需的形状。
冲压成型可以实现内饰件的快速生产和一致性,而且还能够提高零件的强度和刚度。
冲压成型工艺还可以实现零件的轻量化设计,减少汽车整体重量,提高燃油经济性。
4.熔融粉末冷喷涂熔融粉末冷喷涂是一种常用的汽车外饰工艺方法,它采用喷枪将熔融态的金属粉末喷射在汽车外饰表面上,然后快速凝固形成均匀的涂层。
熔融粉末冷喷涂可以实现高强度、高耐腐蚀性和高装饰性的涂层,同时还能够实现多种颜色和纹理的选择,以满足消费者对汽车外观的不同需求。
5.仿真皮革工艺仿真皮革工艺是一种常用的汽车内饰工艺方法,它通过采用合成材料制成类似皮革的材料,然后进行染色和纹理处理,达到与天然皮革相似的效果。
仿真皮革工艺可以实现更加经济和环保的生产方式,同时还能保证材料的一致性和耐磨性。
而且,采用仿真皮革工艺还可以扩大对动物皮革的需求,减少对动物的伤害。
汽车内饰主流的六大制造工艺的设计说明

汽车内饰主流的六大制造工艺的设计说明汽车内饰的制造工艺是指在生产过程中使用的技术和方法。
以下是汽车内饰主流的六大制造工艺的设计说明:1.注塑工艺:注塑工艺是汽车内饰制造中最常用的制造工艺之一、它通过将熔化的塑料材料注入金属模具中,然后用高压将其压实成型。
注塑工艺的优点是制作速度快、成本低、复杂的形状容易实现。
同时,注塑工艺还可以实现多种颜色和纹理效果的定制,满足消费者对个性化内饰的需求。
2.真皮工艺:真皮工艺是汽车内饰制造中高端豪华车型常用的制造工艺。
它使用动物皮革作为材料,在经过多道工序的处理后制成内饰面板。
真皮工艺的优点是具有独特的质感和舒适度,且更耐磨损。
然而,真皮工艺的制造成本较高,并且需要定期的保养和清洁。
3.木纹工艺:木纹工艺是一种将人造木材或真实木材应用于汽车内饰的工艺。
木纹工艺可以通过涂装或贴膜的方式实现。
其优点是能够给车内带来自然、温馨的氛围,提升整体质感。
同时,木纹材料也具备防火和防腐蚀的特性。
4.金属工艺:金属工艺是一种将金属材料制作成汽车内饰部件的工艺。
这种工艺可以通过冲压、焊接、打磨和抛光等方式实现。
金属工艺的优点是坚固耐用、外观美观,并且能够提供高质量的触感。
然而,金属工艺的加工难度较大,成本较高。
5.布艺工艺:布艺工艺是一种使用织物材料制作汽车内饰的方法。
布艺工艺可以通过织造、坯布定型、缝制等步骤来完成。
布艺工艺的优点是柔软舒适、透气性好,并且可以提供丰富多样的颜色和图案选择。
然而,布艺内饰容易吸尘和污染,需要定期清洗和保养。
6.涂装工艺:涂装工艺是一种使用涂料来改变汽车内饰表面颜色和质感的方法。
涂装工艺可以通过喷涂、刷涂、滚涂等方式来完成。
涂装工艺的优点是色彩鲜艳、外观平整,并且能够保护内饰表面不受损坏。
然而,涂装工艺的缺点是容易刮花和褪色,需要定期修补和保养。
汽车内饰的制造工艺在不同的车型和厂家中有所不同,每种工艺都有其适用的范围和特点。
汽车制造商通常会根据车辆定位、市场需求和成本考虑来选择适合的制造工艺,以确保内饰的质量和用户体验的提升。
汽车内饰件材料与成型工艺

•
•
•Байду номын сангаас
–27
二、塑料制品特性要求及成型工艺
2)、阴模吸塑成型:是阳模真空吸塑与搪塑 技术的有机结合,它是一种热模成型技 术,即将不带皮纹的热片材 (0.8mmTPO表皮+2.0mm泡沫)放置在 发泡层与阴模的型腔间,通过真空吸附使 片材与模具型腔(模具型腔已做出了皮纹) 接触成型。冷却时片材收缩,并与发泡层 吸附贴合成型。 • 优点:不会出现皮纹拉伸现象,而且在一 个零件上实现不同的皮纹形式,皮纹均 匀、清晰且手感好,与搪塑效果相当。模 具寿命比搪塑模具提高了3-6倍,生产效 率高。 • 缺点:材料利用率低,对设备要求高,模 具一次性投入高
注射吹塑
拉伸吹塑
多层吹塑
二、塑料制品特性要求及成型工艺
• (7)、挤出成型 • 又叫挤塑、挤压、挤出模塑,是借助螺杆和柱塞的挤压作用,使塑化均 匀的塑料强行通过模口而成为具有恒定截面和连续制品的成型方法。 • 特点:连续化,效率高,质量稳定;应用范围广;投资少,见效快;劳 动强度低;适于大批量生产。
• 混合充分,泡孔细而均匀,外 观品质好
型过程使其膨胀发泡的方法
利用化学发泡剂加热后分解放出的 注射 化学发泡 气体或原料组份间的化学反应所放 出的气体使塑料熔体发泡
• 原料损耗大,劳动生产率低
• 工艺参数可控,模腔压力小, 生产成本低 • 表面光洁度差
–32
二、塑料制品特性要求及成型工艺
• (6)、吹塑工艺(Blow molding) • 目前最新开发的一项工艺,对TPU材料的吹塑成型。 • 优点:能耗低,模具采用镍壳模,与阴模成型模具类似,但无须加热, 寿命很长,一次成型二个产品。TPU本身耐摩擦,机械性能良好,花纹 保持性好,可生产厚度较薄的表皮。
汽车内饰主流的六大制造工艺
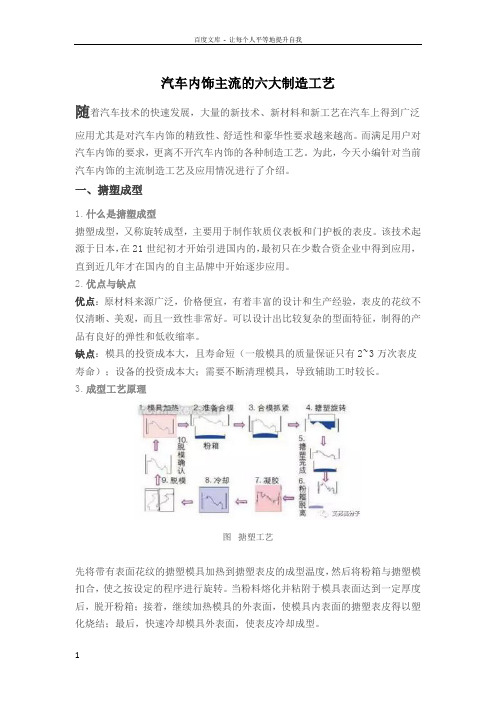
汽车内饰主流的六大制造工艺随着汽车技术的快速发展,大量的新技术、新材料和新工艺在汽车上得到广泛应用尤其是对汽车内饰的精致性、舒适性和豪华性要求越来越高。
而满足用户对汽车内饰的要求,更离不开汽车内饰的各种制造工艺。
为此,今天小编针对当前汽车内饰的主流制造工艺及应用情况进行了介绍。
一、搪塑成型1. 什么是搪塑成型搪塑成型,又称旋转成型,主要用于制作软质仪表板和门护板的表皮。
该技术起源于日本,在21世纪初才开始引进国内的,最初只在少数合资企业中得到应用,直到近几年才在国内的自主品牌中开始逐步应用。
2. 优点与缺点优点:原材料来源广泛,价格便宜,有着丰富的设计和生产经验,表皮的花纹不仅清晰、美观,而且一致性非常好。
可以设计出比较复杂的型面特征,制得的产品有良好的弹性和低收缩率。
缺点:模具的投资成本大,且寿命短(一般模具的质量保证只有2~3万次表皮寿命);设备的投资成本大;需要不断清理模具,导致辅助工时较长。
3. 成型工艺原理图搪塑工艺先将带有表面花纹的搪塑模具加热到搪塑表皮的成型温度,然后将粉箱与搪塑模扣合,使之按设定的程序进行旋转。
当粉料熔化并粘附于模具表面达到一定厚度后,脱开粉箱;接着,继续加热模具的外表面,使模具内表面的搪塑表皮得以塑化烧结;最后,快速冷却模具外表面,使表皮冷却成型。
二、PU(聚氨酯)喷涂PU喷涂工艺是近几年迅速发展起来的一种新的表皮成型工艺,主要用于仪表板的表皮和护板的表皮等。
1. 成型工艺图 PU喷涂表皮的生产流程PU喷涂是指先在表皮成型模表面喷上脱模剂,而后再喷涂模内漆(可根据产品需要喷涂不同颜色的模内漆),随后喷涂液态的PU原料(可通过喷涂机械手控制表皮的厚度),最后冷却起模。
2. 相比于搪塑工艺的优势第一部分搪塑工艺和PU喷涂工艺都是软质仪表板表皮的主要制作工艺,但相对于搪塑工艺而言,PU喷涂有许多优点,比如:可实现双色仪表板表面,使得造三、模内转印(IMD)1. 模内转印概念与应用模内转印是一种在成型过程中与装饰同步进行的工艺。
汽车内饰制造工艺图文详解

适用范 围
设备柔 性
控制程 序
加工精 度
设备成 本
特殊要 求
冷刀 弱化表皮
机械式
非机械式
热刀
铣刀
激光
弱化表皮、骨架 弱化、切割骨架 一体式弱化
高
低
高
高
较复杂
ห้องสมุดไป่ตู้简单
较复杂
复杂
高
较高
高
最高
低
较高
低
最高
环境温度恒 控制弱化线平行 定
处理碎屑
废气处理装 置
工序七:焊接工艺
Process 7: Welding
Equipment:
•EMB Foaming Machine •HK Foaming Machine
General Mold Carrier:
•HEIDEL FRIMO
Capacity:400,000 parts Customer:
•SVW: SAN 3000 •SGM: REGAL
Close pouring
木纹饰板: ABS 注塑 水转印
嵌饰板: ABS 注塑 PU革包覆
杂物盒后衬板: PP 注塑 本体: PP 注塑
SGM Excelle
总成: 螺钉 保护垫: PS 发泡
SGM T-car
SGM T-car
上装饰板: PP+EPDM-T15 注塑 PU软触漆
Equipment:
•NOMAFA Hot Knife •H&G Cold Knife
Capacity:600,000 parts Customer:
•SVW: POLO •DPCA: T53 •CAF: C307
NOMAFA Hot Knife
汽车内饰件材料与成型工艺
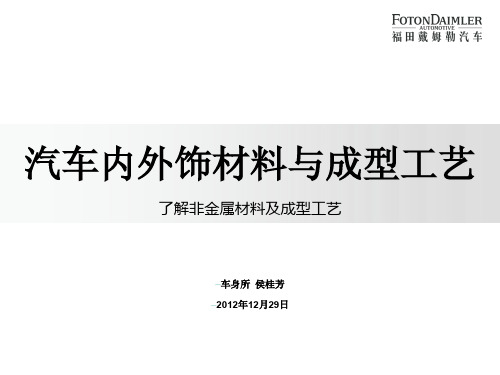
分类及其特点:
类别
特点
适用性
优缺点
挤出吹塑 注射吹塑 拉伸吹塑 多层吹塑
先挤出型坯(型坯不需型芯支 对形状要求不太 1、生产效率高,投入成本低,模具和机械的选择范围广
撑),再对型坯吹塑
严格的中空产品, 2、废品率较高,废料的回收、利用差,产品的厚度控制、
如 空调出风管 原料的分散性受限制,成型后必须进行修边
–(5)、发泡成型:即两种或两种以上的塑料液体在催化剂、发泡剂、稳 定剂等作用下,混合后在一下压力下产生的联合发泡反应,混合原液充填 至整个模腔,在一定温度下使塑料产生微孔结构,并熟化为固体,脱模后 可得到产品。常用的树脂有PS、PU、PP、PE、PVC等。
物料搅匀
入模发泡
切割成型
–热模塑 –冷模塑
• 特点:适用于热固性材料;投资少;压力损失小;无流道及浇口, 材料浪费少;缺点固化时间长,效率低,易产生飞边,自动化程度 低,复杂形状或带嵌件的制品不易成型。
加料
合模
加热
加压
成品
拔模
冷却
成型
–36
二、塑料制品特性要求及成型工艺
–(9)、滚塑成型:又称旋转成型、旋转浇铸成型。是一种热塑性塑 料中空成型方法。
冷却固化,开模得到定型的塑料制品的方法。包括低压注射成型、气体辅助成 型、熔芯注射、双色注射成型等类型。其加工过程:
–退火 调湿
–按需
–9
二、塑料制品特性要求及成型工艺 注塑设备工作原理:
–10
二、塑料制品特性要求及成型工艺
类别 高压注塑
低压注塑
特点
适用性
在较高的注射压力下,在封 生产一般塑料制
–原理:利用加热以及沿两条轴线的旋转生产中空的单个零件。 将熔化
汽车饰件材料及成型工艺大全-推荐

汽车饰件材料及成型工艺大全目录• 一、塑料的组成 • 二、塑料的分类 • 三、常用的塑料 • 四、常见的成型工艺 • 五、内饰典型代表—仪表板及其成型工艺2一、塑料的基本组成塑料 —— 以树脂为主要成分,以增塑剂、填充剂、润滑剂、着色剂等添加剂 为辅助成分,加工过程中在一定温度和压力的作用下能流动成型的高分子聚合 物(高分子有机材料),是以石油、天燃气、煤为基础原料的各种单体通过聚合、 树脂粘合、树脂添加、附加缩合等复杂化学反应而生成的高分子材料。
塑料 —— 树脂+添加剂 按树脂的分子结构和热性能分: 热塑性塑料—— 指在特定温度范围内能反复加热软化和冷却硬化的塑料,其分 子结构是线型或支链线型结构。
(变化过程可逆) 热固性塑料—— 在受热或其它条件下能固化成不熔不溶性物质的塑料 ,其分 子结构最终为体型结构。
(变化过程不可逆)塑料的名称往往就是其主要成分树脂的名称。
3热塑性塑料的可逆过程和热固性塑料的不可逆过程塑料破碎机41.1、树脂树脂 ——指受热时通常有熔融范围,受外力作用具有流动性,常温下呈 固态或液态的高分子聚合物,它是塑料最基本的,也是最重要的成分,其 在塑料中的含量一般在40%~100%。
塑料的主要成分 决定塑料的类型和基本性能树脂的作用: 1、胶粘其它成分材料 2、赋予塑料可塑性和流动性51.2.添加剂⑴ 填充剂(填料) 重要的但非必不可少的成分;作用:(20~50%) 减少树脂用量,降低塑料成本; 改善塑料某些性能,扩大塑料的应用范围。
按形状: 粉状:木粉、纸浆、滑石粉、云母粉、石棉粉等 纤维状 :棉花、亚麻、玻璃纤维、碳纤维等 层状(片状):纸张、棉布、麻布、玻璃布等 按化学性能可分为:有机、无机例如:酚醛压缩粉若无填充剂,则既不能进行成型加工又无实用价值;PE、 PVC+CaCO3 =廉价的具有足够刚性和耐热性的钙塑料;玻璃纤维提高塑料 的力学性能;石棉提高耐热性;61.2.添加剂(2)增塑剂 能够增加塑料的塑性、流动性、柔韧性,改善成型性能,降低刚性和脆性; 它是能与树脂相溶的、不易挥发的高沸点有机化合物。
汽车内饰件产品材料工艺汇总

汽车内饰件产品材料工艺汇总1.软质材料:汽车内饰产品中最常见的软质材料包括皮革、织物和合成革。
皮革通常用于高端车型的座椅和内饰面板上,具有舒适感和豪华感。
织物通常用于经济型车型的座椅和内饰面板上,具有良好的透气性和保暖性。
合成革是一种人造材料,具有类似皮革的外观和手感,但更容易维护和清洁。
2.塑料材料:汽车内饰件中大部分的零件都是使用塑料材料制成的。
塑料材料具有良好的加工性能和耐用性,可满足不同内饰件的形状和功能要求。
例如,中控台面板、门板、仪表盘、扶手等都是由塑料材料制成的。
在塑料制品生产中,常见的工艺包括注塑、挤出和吹塑等。
3.金属材料:汽车内饰产品中的一些零件也使用金属材料制成。
金属材料可以增加内饰件的强度和韧性,同时也提供了一种坚固和高档的感觉。
例如,门把手、开关按钮、座椅调节杆和音响面板等都是由金属材料制成的。
常见的金属材料包括铝合金和不锈钢,通过压铸和折弯等工艺加工成型。
4.木材和木纹材料:木材在一些高端车型的内饰中被广泛使用,以增加豪华感和高贵感。
例如,方向盘、中控台面板和车门饰板等部件通常采用木材或木纹材料制作。
这些材料可以通过真实的木材切割和修整,或者通过印刷和贴膜等工艺来实现。
5.陶瓷材料:近年来,一些汽车制造公司开始将陶瓷材料应用于内饰产品,以增加高档感和独特性。
例如,陶瓷材料可以用于制作方向盘和换挡杆等配件,通过其质感和光泽,为汽车内饰增加一种奢华和时尚的氛围。
总而言之,汽车内饰件产品的材料和工艺多种多样,每一种材料和工艺都有其独特的优势和适用范围。
汽车制造企业需要根据不同车型的定位和消费者需求,选择合适的材料和工艺来打造出令人满意的内饰产品。
随着科技的不断发展和消费者对内饰品质的不断追求,我们可以期待未来更多创新的汽车内饰件材料和工艺的出现。
- 1、下载文档前请自行甄别文档内容的完整性,平台不提供额外的编辑、内容补充、找答案等附加服务。
- 2、"仅部分预览"的文档,不可在线预览部分如存在完整性等问题,可反馈申请退款(可完整预览的文档不适用该条件!)。
- 3、如文档侵犯您的权益,请联系客服反馈,我们会尽快为您处理(人工客服工作时间:9:00-18:30)。
PET+玻纤+PET
(附件可选:铝箔/透气铝箔)
PET+半固化毡+PET (附件可选:铝箔/透气铝箔)
PET+聚氨酯轻质泡沫 (附件可选:铝箔/透气铝箔)
EVA EVA+吸音棉
EVA+半固化毡
滚切 热压 热压 热压 热压 热压 滚切
童座椅安全带挂钩盖/声学件)
原材料加热、冷模压
模具刀口方式:剁切;烘烤温度:200±20°;加热时 间90±10s;成型压力:15-20Mpa;保压60±10s
针刺面料PET +天然纤维成型毡(可选附件:手动/自动遮阳帘/音响罩/装配用 附件/儿童座椅安全带挂钩盖/声学件)
原材料加热、冷模压
模具刀口方式:剪切;烘烤温度:230±20°;加热时 间80±10s;成型压力:7±2Mpa;保压:90s±10s
TPO+重涂层EPDM (附件可选:聚氨酯泡沫/棉毡/成型毡)
滚切 热压 热压
工艺条件
烘烤温度:190±10°;烘烤时间50±5s;保压时 间:60±5s 压力:5-7Mpa
烘烤温度:190±10°;烘烤时间50±5s;保压时 间:60±5s 压力:5-7Mpa
烘烤温度:190±10°;烘烤时间15±5s;保压时 间:25±5s 压力:5-7Mpa
针织面料PET +PP/GF 玻纤成型毡(可选附件:手动/自动遮阳帘/音响罩/装配 用附件/儿童座椅安全带挂钩盖/声学件)
原材料加热、冷模压
模具刀口方式:剪切;烘烤温度:220±20°;加热时 间60±10s;成型压力:15-20Mpa;保压90±10s
针刺面料PET +木粉板(可选附件:手动/自动遮阳帘/音响罩/装配用附件/儿
滚切压力:3-5Mpa
烘烤温度:190±10°;烘烤时间60±5s;保压时 间:60±5s 压力:3-5Mpa TPO:烘烤温度:190±10°;烘烤时间60±5s;保压 时间:60±5s 压力:3-5Mpa(以上参数根据EPDM厚度 决定)
汽车内饰件产品材料工艺汇总
行李箱轮罩 行李箱地毯
隔音隔热垫
式:剁切
10-15Mpa
热压、模具刀口方 模具温度:170±10°;加热时间:350±20s;压力
式:剁切
10-15Mpa
热压、模具刀口方 模具温度:170±10°;加热时间:300±20s;压力
式:剁切
10-15Mpa
吸塑
EVA:烘烤温度:170±10°;烘烤时间80±5s;保压 时间:30s 吸力:3-5Mpa
滚切压力:3-5Mpa
烘烤温度:200±10°;烘烤时间50±5s;保压时 间:90±5s PS:烘烤温度:200±10°;烘烤时间50±5s;保压 时间:90±5s 压力:3-5Mpa(以上参数根据EPDM厚度 决定)
烘烤温度:190±10°;烘烤时间:50±5s;成型压 力:5-7Mpa;保压时间:35±5s
烘烤温度:180±10°;烘烤时间40±5s;保压时 间:60±5s 压力:5-7Mpa
PVC:烘烤温度:160±10°;烘烤时间80±5s;保压 时间:120±5s 吸力:3-5Mpa
滚切压力:3-5Mpa
PVC:烘烤温度:170±10°;烘烤时间80±5s;保压 时间:60±5s 压力:3-5Mpa(以上参数根据EPDM厚度 决定)
衣帽架 顶棚
汽车内饰件产品材料工艺汇总
EVA+PU发泡
吸塑+发泡
EVA:烘烤温度:170±10°;烘烤时间80±5s;保压 时间:30s 发泡:依据B16地毯为例设置参数如下: A转速:334 B转速:180/四个浇注口,浇注时间如 下:3.3s/4.5s/4.8s/3.2s
EPDM 针织面料PET +木粉板(可选附件:手动/自动遮阳帘/音响罩/装配用附件/儿 童座椅安全带挂钩盖/声学件)
热压 热压 热压 热压 热压
簇绒 PA PP P +重涂层EVA(附件可选:PU发泡/棉毡/成型毡)
热压
簇绒 PA PP P +成型毡(附件可选:PU/棉毡/成型毡) PVC(附件可选:聚氨酯泡沫/棉毡/成型毡)
热压 吸塑 滚切
PVC+重涂层EPDM (附件可选:聚氨酯泡沫/棉毡/成型毡)
热压
TPO 塑料地毯
汽车内饰件产品材料工艺汇总
类别
材料结构
工艺
针刺地毯PET +SBR+PE(附件可选:PU/棉毡/成型毡 )
热压
针刺地毯PET +SBR+PET(附件可选:PU/棉毡/成型毡/重涂层EPDM )
针刺地毯PET +SBR(附件可选:PU/棉毡/成型毡/重涂层EPDM )
车厢地毯
针刺地毯PET +EVA+无纺布(附件可选:PU发泡/棉毡/成型毡) 针刺地毯PET +PET(附件可选:PU/棉毡/成型毡/重涂层EPDM ) 簇绒 PA PP P +重涂层EPDM(附件可选:PU/棉毡/成型毡)
烘烤温度:230±20°;烘烤时间80±10s;成型压 力:7-9Mpa;保压:50±5s
滚切压力:3-5Mpa 烘烤温度:190±10°;烘烤时间:60±5s;成型压 力:5-7Mpa;保压时间:40±5s
批准
针刺面料PET +PP/GF 玻纤成型毡(可选附件:手动/自动遮阳帘/音响罩/装配 用附件/儿童座椅安全带挂钩盖/声学件)
原材料加热、冷模压
模具刀口方式:剪切;烘烤温度:220±20°;加热时 间60±10s;成型压力:15-20Mpa;保压90±10s
针织面料PET +聚氨酯和玻纤
加热模
加热温度:110°成型压力:7±1Mpa;保压时间:70 ±5s
滚切
滚切压力:3-5Mpa
原材料加热、冷模压
模具刀口方式:剁切;烘烤温度:200±20°;加热时 间90±10s;成型压力:15-20Mpa;保压60±10ss
针织面料PET +天然纤维成型毡(可选附件:手动/自动遮阳帘/音响罩/装配用 附件/儿童座椅安全带挂钩盖/声学件)
原材料加热、冷模压
模具刀口方式:剪切;烘烤温度:230±20°;加热时 间80±10s;成型压力:7±2Mpa;保压:90s±10s
吸塑、高频焊接 吸塑、热压
EVA:烘烤温度:170±10°;烘烤时间80±5s;保压 时间:30s 吸力:3-5Mpa
EVA:烘烤温度:170±10°;烘烤时间80±5s;保压 时间:30s 吸力:3-5Mpa;半固化毡:烘烤温度: 180±10°时间:35±5s;压力:3-5Mpa;保压时 间:30±5s
PS
PS+重涂层EPDM (附件可选:聚氨酯泡沫/棉毡/成型毡)
PET+PP+PET(附件可选:棉毡/后尾灯维修孔卡扣/EPP、PU支撑块)
PET+SBR (附件可选:棉毡/后尾灯维修孔拉刺/PU支撑块)
PET+PET (附件可选:棉毡/后尾灯维修孔拉刺/PU支撑块)
PET+PET (附件可选:中密度板/PP蜂窝板/棉毡/再生PU块/塑料把手/尼龙 拉手)
ห้องสมุดไป่ตู้加热模
加热温度:110°成型压力:7±1Mpa;保压时间:70 ±5s
针刺面料PET +天然纤维成型毡
原材料加热、冷模压
加热温度:220±20°;加热时间:150±10s;成型 压力:10Mpa;保压时间:50±5s
针刺面料PET +玻纤成型毡
原材料加热、冷模压
加热温度:220±20°;加热时间:150±10s;成型 压力:10Mpa;保压时间:50±5s
烘烤温度:190±10°;烘烤时间80±5s;保压时 间:90±5s 压力:5-7Mpa
烘烤温度:190±10°;烘烤时间40±5s;保压时 间:50±5s 压力:5-7Mpa
烘烤温度:190±10°;烘烤时间80±5s;保压时 间:90±5s 压力:5-7Mpa
烘烤温度:190±10°;烘烤时间80±5s;保压时 间:90±5s 压力:5-7Mpa
烘烤温度:180±10°;烘烤时间:25±5s;成型压 力:5-7Mpa;保压时间:30±5s
烘烤温度:180±10°;烘烤时间:30±5s;成型压 力:5-7Mpa;保压时间:30±5s
滚切压力:3-5Mpa
滚切
滚切压力:3-5Mpa
热压、模具刀口方 模具温度:170±10°;加热时间:400±20s;压力
针织面料PET +天然纤维成型毡
原材料加热、冷模压
加热温度:220±20°;加热时间:150±10s;成型 压力:10Mpa;保压时间:50±5s
针织面料PET +玻纤成型毡
原材料加热、冷模压
加热温度:220±20°;加热时间:150±10s;成型 压力:10Mpa;保压时间:50±5s
针刺面料PET +聚氨酯和玻纤
外轮罩
PET+PP+PE PET+ SBR
PET+天然纤维成型毡 后背门护板 PP蜂窝板
PET+PP+无纺布
编制
汽车内饰件产品材料工艺汇总
热压 热压
热压 滚切 热压
审核
烘烤温度:190±10°;烘烤时间:70±5s;成型压 力:5-7Mpa;保压时间:30±5s
烘烤温度:180±10°;烘烤时间:25±5s;成型压 力:5-7Mpa;保压时间:50±5s