合成催化剂钝化方案
铜基催化剂钝化具体方案

铜基催化剂钝化具体方案方案:1.,准备工作:a将系统内所有残液排放掉,用氮气对整个系统吹扫,(注意要保持系统正压)防止系统进氧(钝化的整个过程,要保证系统是正压)b准备两个三通,一个在气包A(纯氮)上接一个短接(三通的,一头接外来氮气,一头接反应器底部),还一个接在反应器底部。
C配真空缓冲罐里的混合气体,怎样配比呢?先配1%的氧气打3公斤的氮气设空气体积为y(3+y)1%=21%y y=0.15 所以打0.15公斤的空气总压力又开始的0.3MPa变为0.315MPa如要配2%的氧气则打3公斤的氮气,设空气体积为y(3+y)2%=21% y=0.335%的氧气则y=1公斤这由原来的0.3MPa变为0.4MPa如果是在已是混合气的基础上再补空气,则注意了,假设我们之前用2%的混合气体吹扫后,发现这时温度稳定了,我们要加大氧的含量,我们要把氧的含量配到5%,假设这时真空缓冲罐里的压力为2公斤,则设冲入得空气为y 21%y+2%*2=5%(2+y)y=0.55 所以配得的气包压力为0.255再由2公斤的5%混合气配到10%的混合气,应加的空气为1公斤开始钝化:现场两人(一人调节气包a出口阀门开口度,一人控制真空缓冲罐的阀门开启度,两人要有很好的默契感,要时刻听主控温度情况,可以适当的调节阀门,注:混合气开口“只小不大”纯氮开口“只大不小”防止误操作引起催化剂烧结)主控,要班长,主要是懂这个钝化过程的,温度是关键,要起到指挥作用。
对于350方的钝化,则不需要使反应温度达到200c°,200c°时催化剂已经烧结了,因为里面只剩下催化剂了,还有就是没有导热油进行冷油循环了,催化剂只要遇到氧气会迅速氧化,放出大量的热,这时候里面全是催化剂(催化剂的量比较大,),热量会很难带走,所以我建议,混合气最开始的配入得氧的比例要小,建议最好不要超过2%。
还有最开始进气时,要使纯氮先进,然后开启混合气阀门,使之反应一段时间,根据温度情况调节纯8氮阀门开启度,建议不要动混合气阀门,防止手误导致结焦。
转化系统停车及催化剂钝化程序
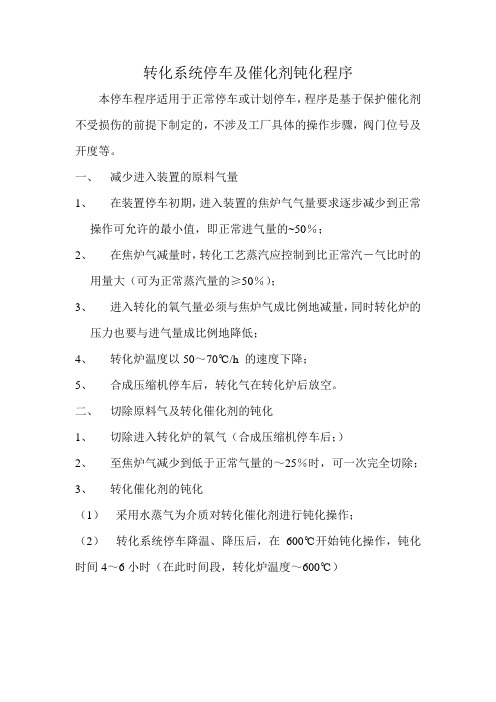
转化系统停车及催化剂钝化程序
本停车程序适用于正常停车或计划停车,程序是基于保护催化剂不受损伤的前提下制定的,不涉及工厂具体的操作步骤,阀门位号及开度等。
一、减少进入装置的原料气量
1、在装置停车初期,进入装置的焦炉气气量要求逐步减少到正常
操作可允许的最小值,即正常进气量的~50%;
2、在焦炉气减量时,转化工艺蒸汽应控制到比正常汽-气比时的
用量大(可为正常蒸汽量的≥50%);
3、进入转化的氧气量必须与焦炉气成比例地减量,同时转化炉的
压力也要与进气量成比例地降低;
4、转化炉温度以50~70℃/h 的速度下降;
5、合成压缩机停车后,转化气在转化炉后放空。
二、切除原料气及转化催化剂的钝化
1、切除进入转化炉的氧气(合成压缩机停车后;)
2、至焦炉气减少到低于正常气量的~25%时,可一次完全切除;
3、转化催化剂的钝化
(1)采用水蒸气为介质对转化催化剂进行钝化操作;
(2)转化系统停车降温、降压后,在600℃开始钝化操作,钝化时间4~6小时(在此时间段,转化炉温度~600℃)
4、转化催化剂钝化要点
(1)当转化出口水蒸气中基本不含不凝性气体时,可认为钝化操作已结束;
(2)钝化过程应密切关注转化炉的床层温度变化;
(3)由于转化炉直径较大,气流沿整个转化炉截面分布不易均匀,(超温、混合器运转异常等现象即为转化炉气流分布不均匀的表现特征)需根据钝化时床层温度的变化调整钝化时间;
(4)“钝化”完成后可用N2或空气吹除系统中的水蒸气,并进一步降温;若采用空气置换降温,应在~200℃,逐渐缓慢加空气,严格观察温升情况,防止超温事故发生。
(5)“钝化”完成后,转化催化剂在温度降到常温后才可暴露在空气里。
氨合成催化剂装填升温方案

目录1、74-1-H/74-1型催化剂装填升温还原参考方案2、74-1-H/74-1型催化剂生产工艺简图3、74-1-H/74-1型催化剂钝化方案4、74-1-H/74-1型催化剂的计算机模拟计算NC(ICI)74-1-H /74-1型氨合催化剂装填和升温还原参考方案1、总则德州华鲁恒升化工股份有限公司拟采用南化催化剂厂生产的NC(ICI)74-1-H /74-1(以下简称为74-1-H、74-1)型氨合成催化剂,用于新建的三十万吨/年的的合成氨装置中。
为了配合华鲁集团顺利完成这次工作,中国石化集团南京化学工业有限公司催化剂厂对催化剂的装填和升温还原工作特制作此参考方案。
2、技术要求2.1 催化剂装填要均匀密实,避免出现架桥和沟流现象,保证合成气体均匀分布。
2.2 催化剂升温还原要平稳,要防止水汽超标而引起的反复氧化还原现象的发生,还原要彻底,使催化剂发挥最佳性能。
3、催化剂装填要求氨合成塔催化剂筐共分三床层,装填时先装入第三床层氧化态催化剂(最下面一层,74-1),次之装填第二层(74-1),最后装填第一床层预还原催化剂(74-1-H)。
3.1 装填前准备工作3.1.1 对合成塔内件进行全面的检查,确认内件完好后,对内件催化剂筐壁进行清理,去除油污等杂物。
3.1.2 对内件进行一次试安装,以确保安装质量。
3.1.3 安装一个装催化剂的平台,备好过筛工具(包括1×1mm网孔的筛网、振动筛、运输和开桶工具等)。
3.1.4 备好吊桶,手提铁桶,1000Kg的磅称,起动吊车。
3.1.5 用干净的白布把内件与催化剂筐环隙等气体及所有气体通道密封,防止装填时催化剂进入,堵塞气体通道。
3.1.6 安装好塔内照明装置(必须是安全电压)。
安装进入塔内连接振动器的电源(注意应加装漏电保护装置)。
3.1.7 按要求必须先进行催化剂装填堆密度的试验。
取一个直径为800mm,高约为1500mm的圆柱形铁桶,事先计出每装入300mm高度所需的催化剂重量。
甲醇催化剂钝化选择

甲醇催化剂钝化选择作者:陈林来源:《科学与财富》2020年第17期摘要:催化剂钝化时局部温升过高或温差猛增,由于膨胀应力可能造成合成塔内件某些零部件的变形、拉裂、催化剂烧结,从而使内件损坏。
对于催化剂的钝化选择方法很重要。
关键词:甲醇;催化剂;钝化1; 前言泸天化绿源醇业有限公司年产40万吨甲醇装置是以天然气为原料。
装置是日本东洋公司的工藝包及MRF-Z甲醇合成塔,催化剂使用的是IC151-8型催化剂。
2; 催化剂钝化在本装置MRF-Z甲醇合成塔中装填的IC151-8型催化剂(主要化学组成(CuO-ZnO-Al2O3),铜基催化剂在使用时被还原成Cu+或金属铜,CuO+H2=Cu+H2O+86.7KJ/mol;原子态铜在卸出时,与空气中的氧气直接接触,会氧化放出大量热,以至于产生局部温升过高,或温差猛增,由于膨胀应力可能造成合成塔内件某些零部件的变形,从而使内件损坏。
催化剂的钝化是指在将催化剂卸出催化剂炉之前,利用氧化物质进行缓慢的催化剂氧化,在其外表形成氧化覆盖膜,该氧化膜可阻隔氧气与金属原子铜进一步反应,从而防止在卸出铜催化剂时造成催化剂筐的损坏,达到保护塔内件的目的。
3; 钝化方法3.1; 合成塔催化剂采用氮循环气中加氧气钝化(1)工艺原理,见图1。
氮气作载气循环时需开压缩机带动整个合成回路循环;J0301为10.3MPa高压蒸汽驱动压透平缩机,压缩机蒸汽来源为转化废热锅炉产气,运行负荷耗气量为80 t/h。
(2)氧气钝化理论时间根据甲醇合成塔装填量用氧气钝化需时间:反应方程:2Cu+O2=2CuO-ΔH=314.6 kJ/mol因单质铜与氧气反应放出大量热,每1%O2大约可导致100 ℃的温升,为避免这一温升烧坏塔内件,按循环量的0.5%左右氧浓度配置的量进行反应,所以钝化时间:t=催化剂总铜量/循环气量×0.5%÷22.4×2铜分子量理论钝化总时间约为28小时。
低压甲醇系统合成催化剂钝化总结

( 2 ) 系 统 置换 合 格 后 ,系统 充 氮 气 压 力 保 持0 . 6 MP a ,温度 控制在 1 0 0 o C,开启 2 、3 循
环 机 建立 系 统 氮 气 循 环 ,开 启 1 循 环 泵 建 立 水 路 循环 ,关 闭 汽包蒸 汽 出 口阀 ,打开放 空 阀 。 ( 3 )由 D N 1 0配 氧 口缓 慢 配 入 O : ,在 塔 进 口取 样分 析 ,每半 小 时 1次 ,初 始 O 。 含 量 控 制
响进度 。为避免 上述 现象 的发 生 ,需 对 老催化 剂 做 钝 化处理 。
1 钝 化原 理
( 1 ) 系 统 循 环 降 温 泄 压 结 束 后 ,用 氮 气 对
系 统 进 行 置 换 ,系 统 内 ( C O +H )含量 <
0 . 5 %为 合格 。
系统置 . 6 M P a ,
艺进一步 降低 合成气 中 C O 、C O 的含 量 ,其低 压 甲醇系统 采用 湖南 安淳 高新 技术 有 限公 司开发
的J J D低 压恒温 悬挂 水管 式 甲醇合 成塔 技 术 ,已
运行 数年 ,装 置运行 稳定 。每 套低 压 甲醇 系统主
首先要 保证 甲醇 合 成塔 内温度 ≤1 0 0 o C,还
氧 口进行 配氧 。
( 4 ) 当 塔 进 、出 口氧 含 量 稳 定 在 2 0 %后 ,
继续 钝化 5 h无 温升 则视 为钝 化结束 。
第 4期
单 吉友 等 :低压 甲醇 系统合成 催 化剂钝 化 总结
2 0 % 左右 。 4 . 2 合 理 控 制 系统 空 速
・ 6 1・
河南 心 连 心 化 肥 有 限公 司 “ 2 4・ 4 0 ”项 目
低压合成甲醇催化剂钝化方案

C307型合成甲醇催化剂钝化方案
一、钝化应具备的条件及准备工作
1、详细对合成系统设备、仪表、阀门、取样点作全面检查。
2、格氮气、空气、冷软水备用。
3、场胶管备用。
4、循环机完好备用。
5、分析取样器具、仪器完好,齐全备用。
二、钝化方法
循环机满量运行,系统压力保持0.7Mpa,出口温度保持在150℃左右,塔出口分析CO+H2+CO2≤0.3%为合格。
系统气体循环,初始控制进塔气体中氧含量≤0.2%,以塔入口取样分析,逐步提高入塔气中的氧浓度,直至出口氧含量达20%,出口温度≤150℃,钝化结束。
三、具体钝化步骤:
1、用氮气对系统进行置换,分析塔出口CO+H2+CO2≤0.3%为合格。
2、系统置换合格后,系统压力保持0.7Mpa,温度控制在150℃,开始配入
O 2,塔进口取样分析,每半小时一次。
起始O
2
浓度为0.2%,在温升不大于25℃
的情况下,逐步提高氧含量,直至氧含量为20%,继续钝化5小时,钝化结束。
四、钝化终点的判断
1、塔进出口氧含量无变化或变化不大。
2、塔出口无明显温升。
五、注意事项
1、塔出口分析CO+H2+CO2≤0.3%,确定合格后,才准系统配氧。
2、配氧钝化,必须小心谨慎,有专人负责指挥。
3、配氧过程中,发现汽包压力上升趋势加快,塔出口温度上升幅度较大时,应减少配氧,加大上水量,降低温度,待温度正常后重新配氧。
4、环机故障停止运转后,应立即停止配氧,塔后放空,补充合格氮气。
5、配氧时,由于催化剂活性较高,遇氧反应强烈,应严格控制起始配氧浓度和配氧速率。
加氢催化剂表面成膜钝化处理技术

一般渣油加氢卸催化剂都采用以下两种方法:1.在停工的时候注成膜剂,这是专利技术,完了之后再卸剂,这样催化剂中的硫化亚铁不易自燃,卸剂的时候也不用再反应器里充氮气保护。
2.卸剂的时候不用成膜剂,然后反应器头盖拆开之后立即通氮气进行保护,这样的话浪费氮气,而且卸剂的时候到处都是油,很脏,很复杂,也很不安全。
最近还看到一种卸剂方法,是雪佛龙的工艺,在美国的帕斯卡格拉炼厂用过的,使用水力除焦卸剂,跟延迟焦化水力除焦的工艺差不多,只不过会产生大量的水,不太好处理。
但是卸剂很快。
一、序言自从石油加氢处理以及加氢裂化精制工艺流程开始以来,炼油厂就面临着怎样从反应器里把催化剂卸出来的难题。
加氢装置的反应器多以固定床反应器为主,其催化剂因床层压差以及活性的问题需要定期更换。
由于加氢催化剂的活性组分(Co、Mo、Ni、W等)在未经再生时是硫化态,在生产过程中也有大量的金属硫化物(以FeS为主)沉积在催化剂里,这些物质遇空气极易发生氧化放热反应而自燃并产生有毒有害物质。
因此,空气下的卸剂不仅有发生火灾的危险,还有可能对人或反应器设备造成损伤。
对于小型反应器而言,在卸剂之前首先向反应器里通入蒸气、空气或氮气、空气的混合气对催化剂进行烧焦,使金属硫化物转变成金属氧化物,然后将催化剂卸出。
但是,这种方法有现场再生时间太长、再生时要向空气中排出二氧化硫等有毒有害气体、损伤反应器设备等缺点,随着二十世纪七十年代世界各国防止大气污染相关法规的实施,器内再生的卸剂方法就被淘汰。
对于大型反应器而言,卸剂操作是在氮气保护下进行。
在卸剂过程中向反应器内连续充入氮气,阻止空气进入反应器内防止催化剂自燃,卸剂人员配备救生设备进器卸剂。
卸出的催化剂要加干冰密闭保存或用水浸泡以防止其自燃,然后送去再生、金属回收或者废弃。
这种方法施工人员工作环境比较恶劣、危及生命安全、污染环境。
氮气保护下的卸剂是很危险的,发生过多起重大的事故,而且危险程度随着催化剂装填床层的增多以及反应器塔盘构造的复杂而增高。
中变催化剂钝化方案

中变催化剂钝化方案
中变催化剂的钝化温度和使用活性温度有密切关系,也就是说还原态的催化剂使用活性温度低,那么钝化温度也要低,如B113型催化剂在250℃就有很好的活性,钝化温度控制在250~350℃。
中变催化剂钝化温度比较好控制,但由于使用了一段时间后避免不了床层结块及偏流等因素,不容易彻底钝化,中变催化剂按下面过程进行,钝化过程中可能有放硫现象,不可避免造成局部环境污染。
1、系统停车后,用过热蒸汽或氮气进行吹扫,在吹扫过程中使床层温度达到钝化指标250~350℃,出口CO+H2<0.5%以下。
2、在载体气中配入空气,初始氧含量控制在0.2~0.5%,严格控制温度在钝化温度范围。
3、随着钝化过程的进行,在此氧含量下,温度有所下降,逐渐增加氧含量,当氧含量达到3%时,如温度有所下降,逐步减少载体气量,增加空气量,当系统全部切换为空气时,床层温度不再上涨,视为钝化以结束,将床层温度降到60℃左右,等待催化剂的卸出。
钝化过程严格控制,不能超温,避免烧坏催化剂和设备损坏。
催化剂钝化进度表。
- 1、下载文档前请自行甄别文档内容的完整性,平台不提供额外的编辑、内容补充、找答案等附加服务。
- 2、"仅部分预览"的文档,不可在线预览部分如存在完整性等问题,可反馈申请退款(可完整预览的文档不适用该条件!)。
- 3、如文档侵犯您的权益,请联系客服反馈,我们会尽快为您处理(人工客服工作时间:9:00-18:30)。
合成催化剂钝化方案 Document number:PBGCG-0857-BTDO-0089-PTT1998
京宝新奥合成催化剂钝化方案
编制
批准:
河南京宝新奥新能源有限公司
2014年5月26日
合成催化剂钝化方案
京宝新奥合成催化剂钝化方案由于一、三段反应器内部的催化剂活性下降比较明显,已经满足不了长周期稳定运行,根据新一段反应器准备情况和生产实际情况,决定在这次大修中将一三段反应器的催化剂进行更换,由于二段反应器中的催化剂不更换,要对二段反应器的催化剂进行保护,所以给一三段反应器催化剂钝化带来了难度,为了保证二段反应器催化剂不受氧化,一三段催化剂顺利进行钝化,特制订次钝化方案。
1.准备工作:
合成系统置换降温结束
对二段反应器进、出口和循环气进口加上盲板
精脱硫出口阀后加盲板
钝化用的氮气、仪表空气等已准备完毕
确认分析条件具备每30分钟分析一次反应器进出口气体的能力。
2.钝化步骤
将反应器R0302隔离出系统,氮气吹扫置换R301和
R303,检测反应器出口气体CO+H2含量,确定CO+H2含量≤0. 5%之后才进行钝化。
建立反应器到循环压缩机的循环圈,合成系统开始做氮气循环,此时系统压力保持在以下。
利用仪表空气向系统内补入氧气。
开始通入氧气时,反应器进口处取样中氧含量应低于%,密切观察反应器床层温度变化,如有温度上升,在床层温度略有下降或稳定时才可以继续加大氧气加入量。
在反应器进口氧气含量小于1%之前,每次以%的速度递增氧气含量。
整个钝化过程中,应该保持反应器床层温度低于60℃,每次增加氧气含量的时候,应保持催化剂床层瞬时温升小于5℃。
密切注意反应器床层热点下移的情况。
当反应器进口处氧气含量高于8-10%时,可以适当提高氧气补入速度,但仍要注意上述要求。
逐步提高反应器进口氧气含量,直至反应器出口氧气含量大于20%,进出口氧气含量相同时,钝化结束。
催化剂钝化过程中可以保持一定排放量,以控制系统压力稳定,钝化后期可以适当减少氮气用量。
钝化结束后,拆开反应器人孔及卸料口,用布袋或软管控制催化剂流出速率,将催化剂过筛处理后,装桶封好以备再次装填。
具体钝化过程如下表:
注1:当床层温度高于55℃时,需控制氧气含量,高于60℃时要采取措施控制床层温度。
注2:此时间为最短保持时间,根据实际操作工况适当延长保持时间。
3、钝化终点判断
反应器进出口气体氧含量无变化或变化不大。
反应器床层没有明显温度变化。
4、注意事项
反应器出口气体分析CO+H2含量,确定合格后,才可以向系统中通入氧气。
钝化过程中,发现反应器床层温度上升幅度较大时,应减少氧气含量,甚至切断仪表风供氧,若床层温度有大幅度上升,需要通入一定量蒸汽,待床层温度正常后才能继续进行钝化。
钝化过程中,由于催化剂活性较高反应强烈,应严格控制起始氧气浓度和氧气浓度提高速度。
钝化过程中要有人专门负责,现场指挥。
钝化流程见图三。