模具设计外文翻译
模具设计外文翻译资料4
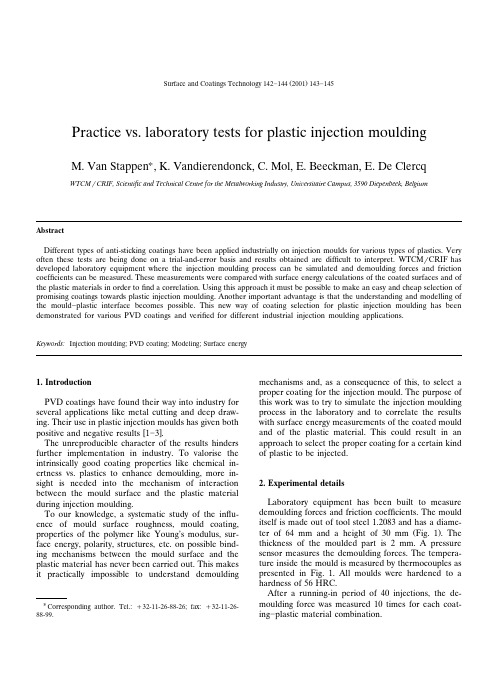
Ž.Surface and Coatings Technology142᎐1442001143᎐145Practice boratory tests for plastic injection mouldingM.Van Stappen U,K.Vandierendonck,C.Mol,E.Beeckman,E.De ClercqWTCM r CRIF,Scientific and Technical Centre for the Metalworking Industry,Uni¨ersitaire Campus,3590Diepenbeek,BelgiumAbstractDifferent types of anti-sticking coatings have been applied industrially on injection moulds for various types of plastics.Very often these tests are being done on a trial-and-error basis and results obtained are difficult to interpret.WTCM r CRIF has developed laboratory equipment where the injection moulding process can be simulated and demoulding forces and friction coefficients can be measured.These measurements were compared with surface energy calculations of the coated surfaces and of the plastic materials in order tofind a ing this approach it must be possible to make an easy and cheap selection of promising coatings towards plastic injection moulding.Another important advantage is that the understanding and modelling of the mould᎐plastic interface becomes possible.This new way of coating selection for plastic injection moulding has been demonstrated for various PVD coatings and verified for different industrial injection moulding applications.Keywords:Injection moulding;PVD coating;Modeling;Surface energy1.IntroductionPVD coatings have found their way into industry for several applications like metal cutting and deep draw-ing.Their use in plastic injection moulds has given bothw xpositive and negative results1᎐3.The unreproducible character of the results hinders further implementation in industry.To valorise the intrinsically good coating properties like chemical in-ertness vs.plastics to enhance demoulding,more in-sight is needed into the mechanism of interaction between the mould surface and the plastic material during injection moulding.To our knowledge,a systematic study of the influ-ence of mould surface roughness,mould coating, properties of the polymer like Young’s modulus,sur-face energy,polarity,structures,etc.on possible bind-ing mechanisms between the mould surface and the plastic material has never been carried out.This makes it practically impossible to understand demouldingU Corresponding author.Tel.:q32-11-26-88-26;fax:q32-11-26-88-99.mechanisms and,as a consequence of this,to select a proper coating for the injection mould.The purpose of this work was to try to simulate the injection moulding process in the laboratory and to correlate the results with surface energy measurements of the coated mould and of the plastic material.This could result in an approach to select the proper coating for a certain kind of plastic to be injected.2.Experimental detailsLaboratory equipment has been built to measure demoulding forces and friction coefficients.The mould itself is made out of tool steel1.2083and has a diame-Ž.ter of64mm and a height of30mm Fig.1.The thickness of the moulded part is2mm.A pressure sensor measures the demoulding forces.The tempera-ture inside the mould is measured by thermocouples as presented in Fig.1.All moulds were hardened to a hardness of56HRC.After a running-in period of40injections,the de-moulding force was measured10times for each coat-ing᎐plastic material combination.()M.Van Stappen et al.r Surface and Coatings Technology 142᎐1442001143᎐145144Fig.1.A cylindrical plastic part injection moulded around a mould.Surface energy was measured on the surface of the coating and on the surface of the plastic material using the model of Owens and Wendt.A Digidrop GBX apparatus has been used based on water and di-iodomethane as testing liquids.To measure the total surface energy,the dispersive surface energy and the polar surface energy are measured.Injection moulding was carried out as follows.In the first application,a polyurethane plastic material with tradename DESMOPAN 385S was injection moulded using uncoated moulds and moulds coated with,respec-tively,a TiN and a CrN coating.In the second applica-tion,three types of polymers were tested on a TiN coated mould and an uncoated mould.Two elastomers Žtrade name HYTREL G 3548W,which is a block-copolyester,and SANTOPRENE 101-73,which is a .blend of polypropylene and EPDM ,and EVOPRENE,which consists of polystyrene and butadiene.3.Results and discussionThe demoulding forces measured for the first appli-cation are given in Table 1.The demoulding forces for the second application are given in Fig.2.This demoulding behaviour has also been observed in industrial practice,so the demoulding laboratory apparatusis a good simulation of reality.To explain these results,an attempt was made to find a correlation with the surface energy measurements.Both total surface energy as well as polar surfaceTable 1Ž.Demoulding forces N for DESMOPAN Uncoated mould 7757N TiN coated mould -2810N CrN coated mould<415NŽ.Fig. 2.Demoulding forces in N for three materials:HYTREL,EVOPRENE,SANTOPRENE.energy in mJ r m 2were compared for both coated sur-Ž.faces and plastic materials Fig.3.In order to explain the demoulding behaviour,an attempt was made to make a correlation between de-moulding forces measured and the surface energy val-ues.It should be expected that when the surface energy of the coated surface is lower than the surface energy of the plastic material,an easy demoulding behaviour could result as a consequence of low material affinity between coating and plastic material.Because the ratio of polar vs.dispersive surface energy varies for the different plastic materials,both surface energy values are taken into account.For the demoulding forces measured in the first case Ž.Table 1,it could be seen that a CrNcoating,espe-cially,could offer good demoulding behaviour.When Ž.we compare Fig.3the surface energy values of DESMOPAN with the values for the mould surfaces Ž.ᎏSTAVAX s uncoated ,CrN and TiN ᎏthen it can be seen,for both total surface energy as polar surface energy,that the measured values for DESMO-Ž2.Fig.3.Total surface energies mJ r m of the different coatings and plastic materials.()M.Van Stappen et al.r Surface and Coatings Technology142᎐1442001143᎐145145Ž2.Fig.4.Polar surface energies mJ r m of the different coatings and plastic materials.PAN are lower compared to the mould surface values. This means that there is no correlation between the demoulding forces measured and the surface energy values.It seems,however,that a CrN surface has the lowest surface energy compared to a TiN coated sur-face and an uncoated surface.When one looks to the total surface energy values Ž.Fig.3,one can see that SANTOPRENE has the lowest value and HYTREL the highest.If our hypothesis was correct from the beginning,we should conclude that the demoulding force for HYTREL should be small and should be large for SANTOPRENE.One can see from Fig.2that this is not the case.When one looks at the polar surface energy values Ž.Fig.4,the three plastic materials have a lower value than the mould surface and SANTOPRENE and EVOPRENE have a lower value than HYTREL. Even when other surface energy criteria are used, e.g.the lower the energy of the mould surface theŽ.lower the demoulding force3,even then no correla-tion can be found.It can be seen that a TiN coating always increases the surface energy and,on the other hand,good de-moulding is sometimes seen, e.g.for HYTREL and DESMOPAN,and sometimes bad demoulding results, e.g.for EVOPRENE.Hence,we can conclude that,based on the surface energy values measured,no correlation could be found within the demoulding forces.Obviously,other parameters,such as roughness and injection tempera-ture,also play an important role in explaining the demoulding behaviour.In order to continue the research work to explain the demoulding behaviour,we will focus onfive industrial demonstrations and try to incorporate all relevant parameters:coating properties,plastic material proper-ties and injection parameters.4.ConclusionsNo correlation could be found between the demould-ing behaviour of plastics vs.coated moulds and the measured surface energy values.Other parameters must also influence this demould-ing behaviour.Further research will focus on other parameters like coating properties,plastic properties and injection parameters.Referencesw x1Annonymous,Big savings made with coated injection mouldingŽ.tool,Precision Toolmaker61998,138w x2O.Kayser,PVD-Beschichtungen schutzen werkzeug und¨Ž.schmelze,Kunststoffe7199598.w x3M.Grischke,Hartstoffschichten mit niedriger Klebneigung,JOT Ž.1199615.。
模具英语词汇大全

汽车冲压模具英语词汇Die / Tool= 模具Prog. Die=progressive die 级进模Ball bearing guide posts and bushings=球形滚珠导柱和轴套Casting die=铸造模Cage=套Part=钣件Rigidity=强度Die material=制模材料Thin=薄Tool design=模具设计Strip design=料条设计Using material thickness radii where sharp corners are shown on the part reduces the occurrence of chipped punch or die corners in the tool. =在尖角处使用与材料厚度一样的R角减少冲头碎裂或模具中有“刀口”Tool design approval=模具设计审核Tool design modification/revision=模具设计更改Tool parts design (detail) = 模具钣件设计(详细)Heeled die sets, internally heel form & trim sections=带箱根的模架,成形与切刃冲头带导引FMC Make=保丽龙制作Construction method=结构方法modification= 更改Check & measure=检查& 测试Machining= 机器加工Large machining=在大型机器上加工上下模架(铣、车等)Small machining=在小型机器上加工模块等Lower die trim inserts=下模切刃块Lower trim inserts retainer=下模切刃块承盘Assemble inserts=组立镶块Punch stripping plates=冲头压料板Assembly=组立Trim punch backing plates=切刃冲头背板NC Machining=NC雕刻加工Stripper window inserts=料条窗户镶块Fitting=研磨组立Spotting=合模Die tryout=试模Cushing stroke=缓冲行程Dowel pin=定位销Guide lift pin=导引升降销Assemble gas spring=安装氮气缸Stamp parts=冲钣件Adjustment=调试Run off parts=冲钣件Lower trim steels=下刃块Hit parts=冲钣件Section=冲头断面Lifters=提升器Trim punch=切刃冲头Coil=卷材jack screw hole=起重[千斤顶]螺旋孔Guide block=导引块Die set, lower plate=下模架Guide the coil through the tool=导引卷材Die set, upper plate=上模架layout inspection=全尺寸检验Die inspection & approval=模具检查和审核Stretch carriers=拉伸运送装置delivery=发货Punch stripping plates=冲头压料板Rejected=拒收Trim punch backing plates=切刃冲头背板Scrapped=报废Stripper window inserts=料条窗户镶块Rework=返工Heel plates=背托stop block=停止块Prepare for delivery=准备发货Hydro form 液压成形Key=键Shear=剪切For locating retainer blocks=承盘键Sensor=传感器For holding buttons or pilots=冲母座或导销键Stretch web=拉伸网For fixed heel or positive stop=镶根键Layout the parts=设计钣件Construction method=结构方法Preceding into the design=继续设计Manual Surface Grinder=手动平面磨床Guide the coil through the tool=导引卷材Spotting red=合模用丹红Checking aid /checking gage=检具Layout ink=试模用蓝墨水Jig=夹具Masking tape=黄色不透明胶带(遮蔽胶带) Fixture=夹具Pliers=尖嘴钳,老虎钳Ball bearing guide posts and bushings=球形滚珠轴套Cresent wrench=可调扳手Guide post=导柱Bushings=导套Pump pipe=泵管Using material thickness radii where sharp corners are shown on the part reduces the occurrence of chipped punch or die corners in the tool. =在尖角处使用与材料厚度一样的R 角减少冲头碎裂或模具中有“刀口”CMM=三次元测量仪Symmetric=对称的The axis of symmetry=对称轴Technical=技术上的Diagonal=对角线Heeled die sets, internally heel form & trim sections=带箱根的模架,成形与切刃冲头带导引One two three block=一二三模块Adjustable parallels=可调平行块Stop block=阻止块Granite Table=花岗岩平台Backing Plate=背板Plotter= .描绘器, 图形显示器, 绘图器, 坐标自记器, 标图员Shoulder Bolt=肩头螺丝(Stripper bolt)Belt Sander=带磨机Keeper Block=行程块Metal Cutting Band Saw=立式带锯床Corner Guide Block=导块Blanchard Grinder=大型平面磨床Dowel pin=定位销Joe Blocks=精密量块Set Screw=螺塞Whirly Gig=筒夹式冲子成形器Jig & fixture =夹具Chamfer Tools=倒角刀具组Checking fixture=检具Angle Plate=L形直角座Guide Block=导块Gage Pins=英寸塞规Plunger=柱塞Sine Plate (magnetic)=正弦磁台Pierce=冲孔Flute End Mill=硬质合金钢铣刀Wear Strip=耐磨板Mill Cutter=波纹粗铣刀(标准型)Mating area=组立的接触面C’bore/ counter bore=六角沉头铣刀Accommodate=适应Radius Dresser=砂轮修整器Wiping hard (very shiny)= 过分摩擦闭合[接触](闪光)Boring Head & Boring Bar=搪孔器、搪刀杆Pin=销Increase the die clearance between the form steels=增加成形块间隙Reamer=绞刀Clearance=间隙Approval=确认Oil paper=油纸Impact wrench=气动扳手0-11” Micrometer=0-11”千分尺Air pin=空气销Trim line=切边bumper[‘bQmpE(r)] n.缓冲器+/-0.5mm unless otherwise specified除非另有规定,否则公差为+/-0.5mmV endor [‘vendE(r), -dC:(r)] n.卖主Part tolerance=钣件公差stripper layout=排样图Ball nose=球刀drawing of panel #987415&16=钣件设计图(公差)Bore=镗Line tap=攻丝校直Arbor =柄轴;心轴Borer=镗刀,镗床Drill chuck=钻夹头Chamfer=倒角Button=冲母座Radius=半径Nitrogen Cylinder=氮气缸Coolant=切削液Pilot=导销Punch=冲头Retainer=承盘Distribution Blocks=接头座Button=冲母座Screw=螺丝Hose Straps=软管夹(塑料)Shop=车间Flat Feet Keepers=顶料销Crib=仓库Ejector Pin=顶出销CNC mill= CNC机床Spring=弹簧Jack=千斤顶Straight Port Adapter=直管接头Strips=料条Y-205 Hose=软管(塑料)Styrofoam [`stairEfEum]n.聚苯乙烯泡沫塑料(保丽龙材料)Short Neck Adapter=短接头Cut off=落料45。
模具设计外文翻译

Four-Cavity Hot-runner Stack Mold for Producing Automotive Inner SillTrim Made from PolypropyleneTo produce the inner sill trim used in an automobile as the transition the carpeting and vehicle frame, a four-cavity hot-runner stack mold was designed. Interconnecting tubes with a sliding fit inate the thermal expansion of the hot-runner systenm ..Depending on the car mold ,there is a left-hand and a right-hand version as well as a long and a short sill.General Mold DesignThe dimensions of the inner sills are 1250 mm*60 mm*2.5 mm, so that the parts are relatively large in area but with comparatively little material content (fig.1). The molded parts weigh 180 and 150 g respectively. Producing these parts by means of a stack mold was the obvious solution, as this doubles the output of the injection molding machine although the claming force requirements remain the same. The name of parts needed to obtain optimum machine utilization resulted in a four-cavity mold with two different cavities for the left-hand and right-hand versions (fig.2 to 5)) . The variation in the lengh of the trim is taken care of by interchangeable mold inserts. To achieve warp-free polypropylene copolymer (hostalon ppr 1042,supplier: Hoechst AG , Germany)required that the flow lengths be limited to approximately 170 mm. Five injection points are needed to along the inside of the trim.The design of the mold provides for simultaneous opening of the two part lines with the aid of two racks (40) and a pinion (36) for each side. As it is essential that no gate marks show on the front of the inside. The mounting attachment and spacers for the carpeting, which require ejector assistance for part release, are also located in this area ,however. Some of the mounting attachment are not at right angles to the part line ,so that hydraulically operated ejectors have been incorporated in hot-runner plates (3) and (5). The cylinders have been specially designed to permit utilization in the immediate vicinity of the hot-runner manifolds at temperatures of about 260 cMold Temperature ControlThree independent circuits have been provide in cach of the mold plates (2) and (3) as well as (5) and (6) for mold temperature control. This permits the temperatures of the outer regions of the 1250 mm long part to be controlled independently of the center region .At a mold width of 1500 mm and with several channels per plate, division into several circuits is also much more favorable with regard to pressure losses, which otherwise would occur.Hot-Rnner DesignA hot-runner system utilizing indirectly heated thermally conductive torpedodes has been selected to distriute melt within the mold.Incorporating the hydraulically operated ejectors in reduce the available space ,thereby forcing a partial reduction of the torpedo diameter.By modifying other design parameters, it was possible to compensate for the resulting change in heat transfer. The chosen injection points require the hot-runner manifold to be 888 mm long. To reduce the ensuing thermal expansion of approx .2 mm total, four indibidual manifold blocks 8 to 11 that are connected to one another by means ofmelt-conbeying pipes 12 to 14 with sliding fits have been provided. The feed pipes 15 divides the central manifold 11 into a right-hand and a left-hand half, each with its own termperature control Eachmaniflod contains four thermally conducting torpecdoes. The left-hand side of manifold block 11 contains only three cartridge heaters, the heating for the feed pipe compensating for any possible heat loss in this area. It is thus possible to vary the temperature at each gate.The melt-conveying pipes of the hot-runner system are fitted with connercially available heater bands with integral thermocouples. The hot-runner system thus contains five heater circuits for the manifold blocks and four heater circuits four the melt-conveying pipes 12 and 13 was not needed. These pipes received adequate heat from the neighboring manifold blocks 8 to 11. No measurable temperature loss occurred .All of the cartridge heaters have the same dimension of 200 mm*16 mm dia. and a heating capacity of 1250w. The watt density in this case lies at 12.5w/cm ,a value guaranteeing long cartridge life even with negligible play in the heater cartridge well. The result is an installed heating capacity of 5000w per manifold or heater circuit power is supplied bia a temperature controller with thyristorcontrol and an output current of 25 A The four controllers for the melt-conveying pipes were chosen to have the same specifications, although an output current of 6 to 10 A would have been adequate. This mesure that if one temperature controller fails, operation of the most important manifold can be ensured by a simple wiring change. The total installed heating capacity thus amounts to 25 kw. The manifolds were designed to have 250w per kg .with this specific heating capacity, balanced heating can be achieved for temperatures of up to approx. 300 c at a mold temperature of 40 c .The warm-up time is approximately 15 minutes, not including the soft start provided bu the controls. The integral soft start limits the supplied power to 50% and thus protects the cartridge heaters.The manifold popes have been produced from hot work steel to ensure that there is no loss in hardness at a possible temperature of 300 c .The sealing lips which slide with the thermal expansion are designed to provide favorable flow characteristics. They have additionally been protected against proven to be leakproof in operation.The threaded section has been produced with a toleranced press fit. The feed pipe 15 is providedwith a decom-pression bushing 16 at the end; this bushing has a stroke of about 5 mm.The length of the feed pipe is such that no dripping material can possibly drop into the parting line of the mold .The melt covers a distance of 940 mm to the farthest gates .The nearest gates are 530 mm away from the decompression bushing. During operation,the hot runner is completely filled with melt. The pressure is thus transmitted almost uniformly up to the individual gates in the stationary melt (or during creep flow ).The holding pressure is therefore also uniformly applied. When the melt is flowing ,however, thereis a pressure drop along the flow path. A moldflow analysis conduted with the objective of providing identical pressure losses in the flowing melt up to each gate yielded different diameters for the runner channels. The primary runner channel has a diameter of 18 mm ,while the vertical secondary runners have a diameter of 6 mm in the center of the mold and one of 8 mm in the outer regions.The torpedoed\s are 110 mm long,17 mm in diameter with an insulating gap of 7.5 mm. At a hot runner manifold temperature of 260 c ,the temperature at the torpedo tip is still at least 235 c. This value is sufficient for polypropylene. Start-up even after a prolonged production inter-ruption does not present any problems. The gate inserts 21 are insulated from the mold plate by a 0.5 mm annular air pocket.A CuCrZr alloy (material no.2.1293) wsa selected for the torpedoes (3) .The torpedoes have been chemically plated with hard nickel 4 to prevent a chemical reaction between the copper and the pp and then subsequently coated with thin ;ayer of chrome to give better adhesive properties.The four hot-runner manifolds 8 to 11 have been provided with central pressure pads 17and 18 which serve to locate the manifolds and transmit the resulting forces into the adjacent mold plates .Four dowel pins in grooves prevent the manifolds from turning. The manifolds are not bolted to the adjacent nozzle plates, but are allowed to float. The distance between the torpedo retainer bushings 20 has been over dimensioned by 0.1 mm in relation to the center frame 4 to ensure that the sustem remains leak-proof even in the eyent of plate deflection or an angular displacement . It was found that, in spite of the size of the mold, the increased thermal expansion of the hot-runner system with respect to the mold frame is sufficient to provide an difficient seal . As a result of the separation into four separate manifolds with axially sliding melt conveying pipes, hermal expansion perpendicular to the mold axis did not have to be taken into account. The torpedoes themselves were shortened by 0.4 mm when cold. As they heat up ,they pxpand into the precalculated insulating ;lates 22 clad with aluminum foil to reduce radiation losses.The total volume of melt in the system is approxi-mately 840; the volume of the four sill trim moldings is 650. The ensures a short residence time for the melt in the manifold system. Changing to a different color for the sill trim does not present any problems during production and can be accomplished quickly.MOLD CONSTRUCTIONMolds for processing of thermosetting molding compounds are generally heated electrically. The heat needed for the crosslinking reaction is drawn from the mold .once in contact with the cavity surface the viscosity of the melt passes through a minimum,i.e. the melt becomes so low in viscosity that it can penetrate into very narrow gaps and produce flash. The molds must thus exhibit very tight fit ,while at the same time providing for adequate venting of the cavity. These largely oppssing requirements are the reason that formation of flast cannot be completely climinated. Molds should be designed to be extremely stiff so that formation of flash are avoided. The use of pressure sensors to determine and monitor the injection pressures, on the basis of which the mechanical properties of the mold are calculated,is recom-mended. The pressure actually required depends on the size an geometry of the molded parts. Material selection is of great importance with regard to the life wcpectancy of the molds, a subject which must already be addressed during the quoting phase what was said in this regard for thermoplastics applies analogously here. Through-hardening steels are to be preferred for the part-forming surfaces and must exhibit a resistance to tempering consistent with the relatively high operating temperatures of stick,e.g. unsaturated polyester resins, steels with >13%chrome content have proven useful, e.g.tool steel no. 1.208, since the thermosetting molding compounds are sometimes modified with abrasive fillers, special attention must be given to the resulting wear. Fillers such as stone flour, mica, glass gibers and the like , for instance ,promote wear. In wear prone regions of the mold such as the gate, for example, metal carbide inserts should be provided. Other wear-prone mold components should gener-ally be designed as easily replace inserts.EJECTION/VENTINGDepending on the geometry of molded part and type of molding compound, different amounts ofdraft for part release must be provided,usually between 1 and 3 .At the time of ejection,theroset parts exhibit very little shrinkage because of the relatively high temperature. As a result, parts are not necessarily retained on the mold cores, but rather may be held in the cavity by a vacuum. To avoid problems during production, measures must be taken to ensure that the parts can always be ejected from the same half of the mold .。
模具毕业设计外文翻译(英文+译文)
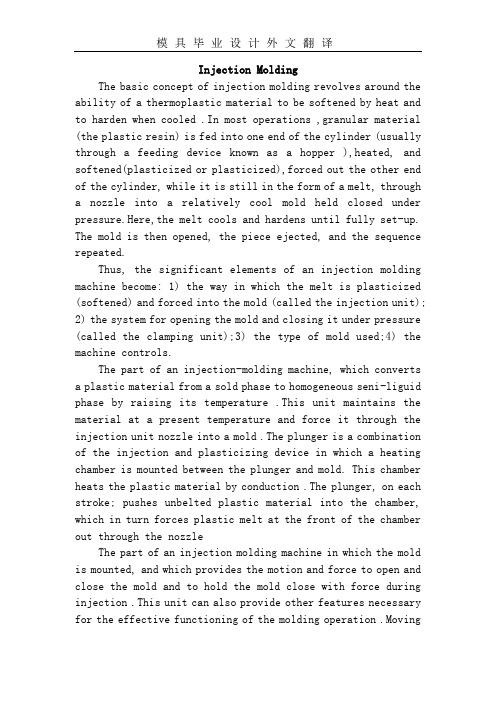
Injection MoldingThe basic concept of injection molding revolves around the ability of a thermoplastic material to be softened by heat and to harden when cooled .In most operations ,granular material (the plastic resin) is fed into one end of the cylinder (usually through a feeding device known as a hopper ),heated, and softened(plasticized or plasticized),forced out the other end of the cylinder, while it is still in the form of a melt, through a nozzle into a relatively cool mold held closed under pressure.Here,the melt cools and hardens until fully set-up. The mold is then opened, the piece ejected, and the sequence repeated.Thus, the significant elements of an injection molding machine become: 1) the way in which the melt is plasticized (softened) and forced into the mold (called the injection unit);2) the system for opening the mold and closing it under pressure (called the clamping unit);3) the type of mold used;4) the machine controls.The part of an injection-molding machine, which converts a plastic material from a sold phase to homogeneous seni-liguid phase by raising its temperature .This unit maintains the material at a present temperature and force it through the injection unit nozzle into a mold .The plunger is a combination of the injection and plasticizing device in which a heating chamber is mounted between the plunger and mold. This chamber heats the plastic material by conduction .The plunger, on each stroke; pushes unbelted plastic material into the chamber, which in turn forces plastic melt at the front of the chamber out through the nozzleThe part of an injection molding machine in which the mold is mounted, and which provides the motion and force to open and close the mold and to hold the mold close with force during injection .This unit can also provide other features necessary for the effective functioning of the molding operation .Movingplate is the member of the clamping unit, which is moved toward a stationary member. the moving section of the mold is bolted to this moving plate .This member usually includes the ejector holes and mold mounting pattern of blot holes or “T” slots .Stationary plate is the fixed member of the clamping unit on which the stationary section of the mold is bolted .This member usually includes a mold-mounting pattern of boles or “T” slots. Tie rods are member of the clamping force actuating mechanism that serve as the tension member of the clamp when it is holding the mold closed. They also serve as a gutted member for the movable plate .Ejector is a provision in the clamping unit that actuates a mechanism within the mold to eject the molded part(s) from the mold .The ejection actuating force may be applied hydraulically or pneumatically by a cylinder(s) attached to the moving plate, or mechanically by the opening stroke of the moving plate.Methods of melting and injecting the plastic differ from one machine to another and are constantly being implored .conventional machines use a cylinder and piston to do both jobs .This method simplifies machine construction but makes control of injection temperatures and pressures an inherently difficult problem .Other machines use a plasticizing extruder to melt the plastic and piston to inject it while some hare been designed to use a screw for both jobs :Nowadays, sixty percent of the machines use a reciprocating screw,35% a plunger (concentrated in the smaller machine size),and 5%a screw pot.Many of the problems connected with in ejection molding arise because the densities of polymers change so markedly with temperature and pressure. thigh temperatures, the density of a polymer is considerably cower than at room temperature, provided the pressure is the same.Therefore,if molds were filled at atmospheric pressure, “shrinkage” would make the molding deviate form the shape of the mold.To compensate for this poor effect, molds are filled at high pressure. The pressure compresses the polymer and allows more materials to flow into the mold, shrinkage is reduced and better quality moldings are produced.Cludes a mold-mounting pattern of bolt holes or “T” slots. Tie rods are members of the clamping force actuating mechanism that serve as the tension members of clamp when it is holding the mold closed. Ejector is a provision in the calming unit that actuates a mechanism within the mold to eject the molded part(s) form the mold. The ejection actuating force may be applied hydraulically or pneumatically by a cylinder(s) attached to the moving plate, or mechanically by the opening stroke of the moving plate.The function of a mold is twofold: imparting the desired shape to the plasticized polymer and cooling the injection molded part. It is basically made up of two sets of components: the cavities and cores and the base in which the cavities and cores are mounted. The mold ,which contains one or more cavities, consists of two basic parts :(1) a stationary molds half one the side where the plastic is injected,(2)Moving half on the closing or ejector side of the machine. The separation between the two mold halves is called the parting line. In some cases the cavity is partly in the stationary and partly in the moving section. The size and weight of the molded parts limit the number of cavities in the mold and also determine the machinery capacity required. The mold components and their functions are as following:(1)Mold Base-Hold cavity (cavities) in fixed, correctposition relative to machine nozzle.(2)Guide Pins-Maintain Proper alignment of entry into moldinterior.(3)Spree Bushing (spree)-Provide means of entry into moldinterior.(4)Runners-Conroy molten plastic from spree to cavities.(5)Gates-Control flow into cavities.(6)Cavity (female) and Force (male)-Control the size,shape and surface of mold article.(7)Water Channels-Control the temperature of mold surfacesto chill plastic to rigid state.(8)Side (actuated by came, gears or hydrauliccylinders)-Form side holes, slots, undercuts and threaded sections.(9)Vent-Allow the escape of trapped air and gas.(10)Ejector Mechanism (pins, blades, stripper plate)-Ejectrigid molded article form cavity or force.(11)Ejector Return Pins-Return ejector pins to retractedposition as mold closes for next cycle.The distance between the outer cavities and the primary spree must not be so long that the molten plastic loses too much heat in the runner to fill the outer cavities properly. The cavities should be so arranged around the primary spree that each receives its full and equal share of the total pressure available, through its own runner system (or the so-called balanced runner system).The requires the shortest possible distance between cavities and primary sprue, equal runner and gate dimension, and uniform culling.注射成型注射成型的基本概念是使热塑性材料在受热时熔融,冷却时硬化,在大部分加工中,粒状材料(即塑料树脂)从料筒的一端(通常通过一个叫做“料斗”的进料装置)送进,受热并熔融(即塑化或增塑),然后当材料还是溶体时,通过一个喷嘴从料筒的另一端挤到一个相对较冷的压和封闭的模子里。
项目 模具英语

项目模具英语模具英语是指在模具制造和使用过程中所涉及的英语词汇和表达方式。
模具是一种用于制造各种产品的工具或设备,通常由金属或塑料制成。
在国际贸易和合作中,模具行业的英语交流已经成为一种必备技能。
以下是模具英语的标准格式文本:一、模具制造过程中的英语词汇和表达方式1. 模具设计(Mold Design)- Design concept: 设计理念- 3D modeling: 三维建模- Draft angle: 脱模锥度- Parting line: 分模线- Core and cavity: 芯和腔- Cooling system: 冷却系统- Ejection system: 脱模系统- Runner system: 浇注系统- Gate design: 浇口设计- Mold flow analysis: 模流分析2. 模具制造(Mold Manufacturing)- CNC machining: 数控加工- EDM (Electrical Discharge Machining): 电火花加工 - Wire cutting: 线切割- Grinding: 磨削- Polishing: 抛光- Assembly: 组装- Trial production: 试产- Inspection: 检验- Modification: 修改3. 模具使用(Mold Application)- Injection molding: 注塑- Blow molding: 吹塑- Compression molding: 压塑- Thermoforming: 热成型- Extrusion molding: 挤出成型- Rotational molding: 旋转成型- Overmolding: 双色注塑- Insert molding: 嵌入式注塑- Molding defects: 成型缺陷- Mold maintenance: 模具维护二、模具行业常用的英语表达方式和句型1. 询盘和报价(Inquiry and Quotation)- We are interested in your mold products and would like to request a quotation.- Could you please provide us with the price list for your mold products?- Can you give us a detailed breakdown of the costs involved in manufacturing the mold?- We would like to know the delivery time for the mold products.2. 技术交流和合作(Technical Communication and Cooperation)- We would like to discuss the mold design and specifications in detail.- Could you provide us with the CAD files or 3D drawings of the mold?- We are open to any suggestions or improvements regarding the mold design.- We are willing to cooperate with your company on mold manufacturing and development.3. 合同和支付(Contract and Payment)- We would like to sign a contract for the mold manufacturing project.- What are the payment terms and conditions for the mold products?- We will make the payment in installments according to the agreed schedule.- The payment will be made by bank transfer or letter of credit.4. 售后服务和保修(After-sales Service and Warranty)- We expect a warranty period for the mold products.- In case of any problems or defects, we would like to know your after-sales service policy.- Could you provide us with the spare parts and maintenance manual for the mold?- We appreciate your prompt response and support in resolving any issues with the mold.以上是关于模具英语的标准格式文本,涵盖了模具制造过程中的英语词汇和表达方式,以及模具行业常用的英语表达方式和句型。
模具加工方法英语词汇大全

模具加工方法英语词汇大全在模具加工领域,掌握相关英语词汇是非常重要的。
本文将为你提供一个模具加工方法英语词汇大全,帮助你更好地理解和交流相关的知识。
1. 模具加工方法基础词汇Mold (模具)•Cavity: 空腔•Core: 芯子•Ejector Pins: 推杆•Draft Angle: 脱模锥度•Runner: 浇口Machining (加工)•Milling: 铣削•Turning: 车削•Drilling: 钻削•Grinding: 磨削•Boring: 镗削Surface Treatment (表面处理) •Polishing: 抛光•Electroplating: 电镀•Anodizing: 阳极氧化•Coating: 涂层•Sandblasting: 喷砂Measurement (测量)•Caliper: 卡尺•Micrometer: 千分尺•Height Gauge: 高度规•CMM (Coordinate Measuring Machine): 三坐标测量机•Profile Projector: 轮廓投影仪2. 模具加工方法高级词汇CNC Machining (数控加工)•CNC Milling: 数控铣削•CNC Turning: 数控车削•CNC Grinding: 数控磨削•CNC Wire EDM (Electrical Discharge Machining): 数控线切割•CAM (Computer-ded Manufacturing): 计算机辅助制造Injection Molding (注塑)•Mold Design: 模具设计•Mold Flow Analysis: 模流分析•Mold Temperature Control: 模具温度控制•Gate Design: 浇口设计•Venting: 排气Die Casting (压铸)•Die Design: 压铸模具设计•Die Lubrication: 压铸模具润滑•Die Casting Defects: 压铸缺陷•Cold Chamber Die Casting: 冷室压铸•Hot Chamber Die Casting: 热室压铸Stamping (冲压)•Progressive Die: 渐进模具•Blanking: 冲裁•Piercing: 穿孔•Bending: 弯曲•Deep Drawing: 深冲3. 模具加工方法其他相关词汇Mold Materials (模具材料)•Tool Steel: 工具钢•Stnless Steel: 不锈钢•Aluminum: 铝•Copper: 铜•Plastic: 塑料Mold Components (模具部件)•Guide Pins: 导柱•Ejector Sleeves: 推杆套筒•Sprue Bushing: 浇口套筒•Inserts: 嵌件•Lifter: 脱模销Mold Mntenance (模具维护)•Cleaning: 清洁•Lubrication: 润滑•Repr: 修复•Storage: 存储•Replacement: 更换以上是一个模具加工方法英语词汇大全,涵盖了基本和高级词汇以及其他相关词汇。
注塑成型的模具设计外文翻译

Figure 1. Organization of the IKEM Project2 Intelligent Mold Design ToolThe mold design tool in its basic form is a Visual Basic application taking input from a text file that contains information about the part and a User Input form. The text file contains information about the part geometry parsed from a Pro/E information file. The input is used to estimate the dimensions of mold and various other features.2.1 Literature ReviewDesign of molds is another stage of the injection molding process where the experience of an engineer largely helps automate the process and increase its efficiency. The issue that needs attention is the time that goes into designing the molds. Often, design engineers refer to tables and standard handbooks while designing a mold, which consumes lot of time. Also, a great deal of time goes into modeling components of the mold in standard CAD software. Differentresearchers have dealt with the issue of reducing the time it takes to design the mold in different ways. Koelsch and James have employed group technology techniques to reduce the mold design time. A unique coding system that groups a class of injection molded parts, and the tooling required ininjection molding is developed which is general and can be applied to other product lines.A software system to implement the coding system has also been developed. Attempts were also directed towards the automation of the mold design process by capturing experience and knowledge of engineers in the field. The development of a concurrent mold design system is one such approach that attempts to develop a systematic methodology for injection mold design processes in a concurrent engineering environment. The objective of their research was to develop a mold development process that facilitates concurrent engineering-based practice, andFigure 2. Organization of the Mold Design Module.While most of the input, like the number of cavities, cavity image dimensions, cycle time are based on the client specifications, other input like the plasticizing capacity, shots per minute etc., can be obtained from the machine specifications. The output of the application contains mold dimensions and other information, which clearly helps in selecting the standard mold base from catalogs. Apart from the input and output, the Figure 2 also shows the various modules that produce the final output.2.5 Framing rulesAt this stage, the expert’s knowledge is represented in the form of multiple If-Then statements. The rules may be representations of both qualitative and quantitative knowledge. By qualitative knowledge, we mean deterministic information about a problem that can be solved computationally. By qualitative we mean information that is not deterministic, but merely followed as a rule based on previous cases where the rule has worked. A typical rule is illustrated below:If Material = “Acetal” AndRunner Length <= 3 AndRunner Length > 0 ThenRunner Diameter =0.062End IfWhen framing the rules it is important that we represent the information in a compact way while avoiding redundancy, incompleteness and inconsistency. Decision tables help take care of all the above concerns by checking for redundancy and comprehensive expression of the problem statement. As an example, in the process of selecting an appropriate mold base, the size of mold base depends on the number of cavities and inserts. To ensure that all possible combinations of。
模具中英对照

模具中英对照模具是一种用来制造复杂形状的工具,广泛应用于汽车、航空、电子、医疗等领域。
在国际贸易中,模具领域是一个重要的行业,涉及到的技术术语和行业术语繁多,因此,建立起一个模具中英对照的文档对于学习和应用模具领域具有重要的意义。
下面我们将列出一些常见的模具术语及其中英对照:1. 模具设计:mould design2. 模具制造:mould making3.模具材料:mould material4. 模具钢:mould steel5. 模具试样:mould trial sample6. 模具寿命:mould life7. 塑料注塑模具:plastic injection mould8. 金属冲压模具:metal stampingmould9. 模具零件:mould parts10. 设计参数:design parameter11. 模具尺寸:mould dimension12. 模具重量:mould weight13. 模具结构:mould structure14. 成型工艺:forming process15. 模具表面处理:mould surface treatment16. 冷却系统:cooling system17. 模具加工:mould machining18.精度控制:precision control19. 模具维护:mould maintenance20. 模具修复:mould repair随着模具行业的发展,中英对照文档需要不断地进行更新和完善。
在实际应用中,我们需要根据需求来确定需要掌握的技术和行业术语,并及时查阅相关的中英对照文档,以便更好地理解和使用模具技术。
除了上述列出的术语,模具领域还涉及到很多具有专业性的技术术语和行业术语,例如模具热处理、模具注塑成型、模具表面处理等方面的专业术语。
因此,掌握和应用模具技术需要具备较高的专业素养和知识储备,这需要我们持续地学习、实践和总结。
- 1、下载文档前请自行甄别文档内容的完整性,平台不提供额外的编辑、内容补充、找答案等附加服务。
- 2、"仅部分预览"的文档,不可在线预览部分如存在完整性等问题,可反馈申请退款(可完整预览的文档不适用该条件!)。
- 3、如文档侵犯您的权益,请联系客服反馈,我们会尽快为您处理(人工客服工作时间:9:00-18:30)。
外文原文Abstract:Die designing is a demanding and hard work.To design a separate die for each product is time consuming and expensive task.This paper presents an idea of sets of standard reference dies.it gives a concept of flexible die designing using a reference standard die designed in a popular commercial CAD/CAM software—Pro/Engineer.Rather than designing a separate die for each part,just update the die design by selecting the die dimensions as required.The use of this concept will prove to reduce time and cost of product in manufacturing industry.Key words:die;flexible die designing system ;standardization;Pro/E;secondary developmentAt present, the industrial developed countries and regions in the mold industry has been gradually standardize and serialization. In China, although the majority die within the enterprises have business standards, but generally not high degree of standardization, standardization of stamping die in the die-limited parts of the parts. To achieve real savings stamping die design time and shorten the processing cycle, cost savings, reduce design and manufacturing staff workload purposes, it needs to develop a flexible stamping die design system. At the same time, stamping die serialization of the scope of standardization and can not be confined to die-part of the fixed panels, boards, the top plate unloading device commonly used components such as stamping or even die structure, we should achieve serialization and standardization.As CAD / CAM technology in the design and manufacture die in the course of extensive application, it should first be standardized stamping die from the CAD system began. Some large-scale commercialization of the CAD / CAM software, such as Pro / E, UG, and so on. Have developed a specialized injection mold design package. And stamping die design for the special software, users need to be developed.l The application tools Pro / E in stamping die design flexibility in the system developmentPro / Engineer by the United States has developed a set of PTC CAD / cAM / CAE software. Pro / E using a single database And feature-based, the design parameters of the model, provides users with 1 The development is very convenient for stamping die flexible system of tools juice1.1 Family TableFanaily Fable known as the Family Table, the structure used to create the same or similar parts of the size and characteristics of the standardized database tables, is devoted to the establishment of a standard parts library tool. The use of the formerfirst family table to create a generic representation of the components (the generic), according to the need to target and then added to the family table a series of management.Family sheet management can be the object of a size (dimension), features (feature), parameters (parameter) and assembly parts (component), and so on.A family table can have multiple levels, that is a generic parts can contain multiple sub-components (instance, also known as examples), and each Instance can contain their own Sub Instance. Discharge screw (stripper-bolt) the family table structure as shown in Figure 1.Figure 1 Family Table hierarchy1.2 RelationsRelations (relations) between mathematics and procedures, including grammar, and its main role is to be part or assembly of the relevance of the data by size symbols, and other parameters of grammar (syntax) to establish mathematical formula to meet the design requirements. Pro / E system of relations can be found in Sketch, Feature, Part and in the Assembly. Simple sentence, judgement and sentence is to establish relations of common format. Simple sentence that a simple mathematical relationship between the size of direct response associated situation. The use of simple format, such as d6 = L. BP 1 2 * d3. Judgement on the sentence for certain occasions, by specifying conditions to express design intent, grammar structure: "IF… ENDIF" or "IF… ELSE… ENDIF" in the "ELSE… ENDIF" between conditional statements can be multi-nested. Relations in the standardization and flexible stamping die design system in the building process plays a very important role, it has decided to parts of the geometric shape and characteristics of relations between the digital Xiao, partsrelations between the assembly and parts assembly in the presence of middle - A number of features.1.3 Pro/ProgramPro / Program (program) is the Pro / E of a procedural tool, similar to its grammar VBA and Office software in the Macro (Acer). When users use of Pro / engineer to design .The product of various kinds of information to document the format will be recorded. Through the Pro / Progran document editing, can be achieved on the characteristics of the hide, delete and re-order the assembly of components to add and replacement operation. These features stamping dies for the establishment of standard parts library, standards and flexible design structure of the system is very useful.Program files in the structure can be broadly classified into the title, set of parameters relationship, to add features (parts) and updating the quality attributes, such as five parts. In "INPUT… END INPUT" Xiao located between the parameters of the "RE1 ATIONS… ENDREALATIONS" relations between the various add in the "ADD… END ADD" and added features (part module) or parts (assembly module). Pro / Program provides three types of parameters: NUMBER (numerical) STRING (string) and YES-NO (it).2. Standards moldbase of the development2.1 Standards moldbase Classification and organizationsDie-stamping die is an important part. The typical model-there are three types: rear-guided-mode (back pillar sets), the middle-guided-mode (center pillar sets) and the guided-mode-angle (diagonal pillarsets). Each type of die-also includes a variety of specifications. According to Die boundary demarcation size, rear-guided, in a L ×B-22 specifications, D0 specifications 6 (L = B), middle-guided, in the nine-D0 specifications, the guided-mode-Kok L × B specifications 7 [2-3].In order to facilitate the management and data calls, the standard mode of the directory of the best-established in the Pro / E installation directory. As three categories-the larger structural differences, it may die-the root of the establishment of three other subdirectories, each subdirectory contains all the component parts-mode, and each type of parts can be adopted Pro / E Software for the family table, and toolssuch as the establishment of standard procedures for the database.2.2 Standards moldbase library buildingDie-stamping die from the main mode on the Block (upper.shoe), nder-Block (1 ower.shoe), I. column (guide.pillar) and I. Case (guidebushing), and other components. In order to make structural integrity of mold, can also die stalk (shank) assembly to die-in. Here are rear-die I.Establishment of the standard method.First of all the various components to create three-dimensional model, and then the standard manual data in the table a series of symbolic dimension added to the group on January 1 Editor (can also use Excel for editing). Add in the size of symbols, Size will be the best symbol to revise the manual and the size of the same symbol. Because people can not distinguish between Table Capitalization is, when both the same size letters, proposed to use capital letters to distinguish between pairs of characters, such as that for the d D, and D that will become a DD.Standard on two-Block: When the L ×B> 200 mm ×160 mn-i have installed Boss, and when L × B is less than or equal to the scope of non-installation of Boss, shown in Figure 2. Determine whether Boss in two ways: one way is to use Family Table, will generate the Boss Extrude Offset two characteristics and the way to Feature added to the family table, and in these two characteristics of the list Enter in the "Y" or "N", to determine the specifications of a certain mode on the Block, whether these two features; Another method is to find these two features in the Pro / Program in the location and characteristics of the process to add Extrude His statement before the judge "IF L> 200 1 B> 160", adding the Offset characteristics of the procedures used "END IF" the end of judgement.Figure2. die on the ground in two types2.3 The establishment of Standards moldbase forIn Pro / Assembly in the same module can be generated by the use of family die-standard database. Family structure in the assembly, when selected COrnponent, select the mode of all the parts-and enter a different group in the table-model specifications required by the standards of sub-components of the name, as shown in Figure 3.Figure 3 rear-guided, in the standard mode of Family TableCommon mode handles four types: pressure-in-stalk, the flange-stalk, Screw-mode and floating stems die stalk. If the four types of module assembly to handle all the common-mode model (Figure 3 in the assembly only two kinds), in the group table by the need to enter the module handles parts of the name, set the parameters of INPUT, with Regenerate Called when the parameters of renewable order to choose the mode of different types of handles. Of course, people can also die of the table do not have to handle characters with "N" to curb, as shown in Figure 3-mode system is used in this method.3 The development of standard stamping die3.1 The typical combination of stamping dieStamping die in the larger structural differences and establish flexible stamping die design systems using the best combination of the typical mold. Use of combinations to determine the structure of the typical mold of the structure, and thus determine the composition of the various components die sizes and assembly relations. Commonly used combination of stamping die typical structure: a fixed combinationof unloading, Tanya unloading combinations, composite model portfolio, such as plate-portfolio. Mold can not be separated from the structure of ISO standardization of parts, in the Pro / Engineer Dies in the standardization of parts can be used in the design of the bottom-up approach can also be used top-down design.3.2 die in the process of assembling data transferBecause of complicated, so stamping die by the standardization of the factors to consider-Modulus than standardized by many more factors to consider, one of the most important factor is the size of the correlation between the components. In the mold of a standard combination, assembly and components, parts and components between the need for data transmission, and in the Pro / Assembly can be very easy to achieve this objective.3.2.1 by the assembly of components to the data transferPro / Program can use the assembly EXECUTE statement will be down the parameters in a sub-assembly or parts delivery, the use of syntax is as follows: EXECUTE PART / ASSEMBLY file name components or sub-assembly of the parameters in the assembly of = END EXECUTE EXECUTE statement parameters can not leapfrog data transmission, not by the assembly to sub-assembly of components in the direct transmission of data.3.2.2 data transfer between the componentsWhen added to the assembly of components are in a Id, it can complete the assembly of components between the data transfer. Id assembly of components, can be used in the menu RELATIONs Session Id command to query. Figure 4 is the combination of Tanya discharge standards in the spring of unloading assembly diagram. As assembly to die in the spring have a pre-compression and thus the length of its assembly (Hs) are no longer equal to the length of freedom (H.). In determining H, you can use the following mathematical relationship:Hs:38= L:32一tbp:0In this way can always guarantee equal to the length of spring assembly from the surface to Dianban discharge board under the surface height, thus eliminating the relevant parts were replaced after the size of Laws. In the design of this mold is very practical, because the mold assembly in a similar situation there are many. Again, in determining the discharge screw on the seat-hole diameter (dI34), they can use thefollowing mathematical relationship:d134:8=D:32+2This Id, established by the mathematical relationship between the need to use Regenerate order to take effect, so different parts on the size of the location of as little as possible in this way, so as not to die in the initial call model will appear at the wrong result will be displayed. But if the parts in between and parameters to transfer data, the location of the various components of size parameters to create a mathematical relationship, the trouble can be avoided.3.2.3 standard replacement partsFamily Table used to establish the standard parts can lookup. inst Replacement statement. Lookup inst allows users to find the standard parts that match the sub-components, if not find the results, then return to a generic [4 J.Lookup.inst :lookup inst(generic—name,match-mode,paramnamel,match—valuel,param-name2,match—value2…)One match. preferred mode of three, representing different meanings: one is to find parameters of less than or equal to find the value of components; parameter values 0 to find an exact match to find value of the sub-components; to find parameters of greater than or equal to find value The sub-components.3.3 structure of the assemblyDie parts to complete the establishment and rationalize the assembly relations between the components, you can generate mold assembly model. Figure 5 for the development of the author Tanya unloading combination of specifications for the 200 mm × 160 mm of die structure (omit all the characteristics of thread).3.4 stamping die callStamping die in the Pro / Assembly call directly, but also can be used Pro / TOOLKIT development of visual user interface to call. Pro / TOOLKIT Pro Ecuador is the second development system software package, its main purpose is to allowusers or third parties through the expansion of C code Pro / E function, based on the development of Pro / E system of application modules to meet user Special needs. Pro/T00LKIT use of the UI dialog, the menu VC + + and Visual Interface technology, designed to facilitate flexible and practical stamping die design system for interactive interface. Use interface called the structure of various stamping dies, the choice of different specifications of the parts, enter a different parameters to determine sheet parameters as well as their positioning in the mold, and further in the system design punch, die and other structures, Thus greatly enhance the efficiency of stamping die design.4 ConclusionSince stamping process a wide range of complex processes, and the shape of various parts die, stamping dies in achieving standardization and development of flexible design system and the process is very complicated, but flexible stamping die design system of stamping die CAD is to improve the level of the cornerstones . Pro / E powerful components, the assembly of the criteria for the establishment of the functions of stamping dies for the standardization and flexible design of the feasibility of developing systems to provide a strong guarantee. In the development of flexible design system, should ingenious application of Pro / E software provided by an effective tool, considering the different types of standard structural composition of the assembly relations. Between the parts and components meet requirements of size structure changes, and the best use RELATIONS Pro / Program prepared by the mathematical relations systems and procedures to increase the flexibility and practicality. Die flexible design and application development system to avoid a mold designers unnecessary duplication of labor, so that the programme will focus on the concept, process optimization, and other creative work, thus mold the rapid design and production standards have a practical application Significance.外文资料翻译译文摘要:模具设计是一个苛刻的辛勤工作。