常见液压系统故障分析和排除方法-高压胶管
液压系统常见故障及排除方法

液压系统常见故障及排除方法一液压泵常见故障分析和排除方法故障现象故障分析排除方法不出油1、电动机转向不对1、检查电动机转向输油量不足2、吸油管或过滤器堵塞2、疏通管道、清洗过滤器、换新油压力上不去3、轴向间隙或径向间隙过大3、检查更换有关零件4、连接泄露,混入空气4、紧固各连接处螺钉,避免泄露,严防空气混入5、油粘度太大或油温升太高5、正确选用油液,控制温升噪音严重1、吸油管及过滤器堵塞或过滤器容量小1、清洗过滤器使过滤器畅通、正确选用过滤器压力波动2、吸油管密封处泄露或油液中有气泡2、在连接处或密封处加点油,如果噪音减小,可拧紧接头处或更换密封圈;回油管口应在油面以下,和吸油管要有一定距离3、泵和联轴节不同心3、调整同心4、油位低4、加油液5、油温低或粘度高5、把油液加热到适当温度6、泵轴承损坏6、检查(用手触感)泵轴承部分温升温升过高1、液压泵磨损严重,间隙过大泄漏增加1、修磨零件,使其达到合适间隙2、泵连续吸气,液体在泵内受绝热高压,2、检查泵内进气部位,及时处理产生高温3、定子曲面伤痕大3、修整抛光定子曲面4、主轴密封过紧或轴承单边发热4、修整或更换内泄漏1、柱塞和缸孔之间磨损1、更换柱塞重新配研2、油液粘度过低,导致内泄2、更换粘度适当的油液二、液压缸常见故障分析和排除方法故障现象故障分析排除方法爬行1、空气入侵1、增设排气装置,如无排气装置,可开动液压系统以最大行程使工作部分快速运动,强迫排气2、不同心2、校正二者同心度3、缸内腐蚀,拉毛3、轻微者去除毛刺,严重者必须镗磨冲击1、靠间隙密封的活塞和液1、安规定配活塞和液压缸的间隙,减少泄露压缸之间间隙过大节流阀失去作用2、端头的缓冲单向阀失灵,缓冲不起作用2、修正研配单向阀和阀座推力不足1、液压缸或活塞配合间隙太大或O型密封1、单配活塞和液压缸的间隙或更换O 或工作速度圈损坏造成高低压腔互通型密封圈逐渐下降2、由于工作时经常用工作行程的某一段2、镗磨修复液压缸孔径,单配活塞甚至停止,造成液压缸孔径线性不良(局部腰鼓)至使液压缸高低压油腔互通,3、缸端油封压得太紧或活塞杆弯曲3、放松油封,以不漏油为限,校直活塞使摩擦力或阻力增加杆4、泄露过多4、寻找泄露部位,紧固各结合面5、油温太高,粘度太小,靠间隙密封或5、分析发热原因,设法散热降温,如密密封质量差的油缸行速变慢,若液压缸封间隙过大则单配活塞或增设密封环两端高低压油腔互通,运行速度逐步减慢或停止原位移动1、换向阀泄露量大1、更换换向阀2、差动用单向阀锥阀和阀座线接触不良2、更换单向阀或研磨阀座3、换向阀机能选型不对3、重新选型,有蓄能器的液压系列一般常用YX或Y型机型三、溢流阀的故障分析和排除方法故障现象故障分析排除方法压力波动1、弹簧太软或弯曲1、更换弹簧2、锥阀和阀座接触不良2、如锥阀是新的即卸下调整螺母将导杆推几下,使其接触良好,或更换锥阀3、钢球和阀座密配合不良3、检查钢球圆度,更换钢球,研磨阀座4、滑阀变形或拉毛4、更换或修研滑阀5、锥阀泄露5、检查,补装调整无效1、弹簧断裂或漏装1、更换弹簧2、阻尼孔堵塞2、疏通阻尼孔3、滑阀卡住3、拆出、检查、修整4、进出油口反装4、检查油源方向5、锥阀泄露5、检查、修补泄露严重1、锥阀或钢球和阀座的接触不良1、锥阀或钢球磨损时更换新的锥阀或钢球2、滑阀和阀体配合间隙过大2、检查阀芯和阀体的间隙3、管接头没有拧紧3、拧紧连接螺钉4、密封破坏4、检查更换密封噪音及振动1、螺母松动1、紧固螺母2、弹簧变形,不复原2、检查并更换弹簧3、滑阀配合过紧3、修研滑阀,使其灵活4、主油阀动作不良4、检查滑阀和壳体的同心度5、锥阀磨损5、更换锥阀6、油路中有空气6、排出空气7、流量超过允许值7、更换和流量对应的阀8、和其他阀产生共振8、略为改变阀的额定压力值(如额定压力值的差在0.5Mpa以内时,则容易发生共振压力过低,达1、漏装钢球或调压弹簧或锥阀1、补装不到设计要求2、滑阀被污物卡在全开的位置2、清洗3、系统元件或管道破裂大量泄漏3、检查、修复好更换压力过大,调1、油液污染滑阀被卡在关闭的位置上1、清洗滑阀及阀孔,更换新油不下来四、节流阀的故障分析和排除方法故障现象故障分析排除方法节流作用及调速1、节流阀和孔间隙过大,有泄露1、检查泄露部位零件损坏范围不大以及系统内部泄露情况,予以修复、更新、注意结合处的油封情况2、节流阻尼孔堵塞或阀芯卡住2、拆开清洗,更换新油,使阀芯运动灵活运动速度不稳1、油中杂质粘附在节流口上,通1、拆卸清洗有关零件,更定如逐渐减慢油截面减小,使速度减小换新油,并经常保持油液突然增快及跳洁净动等现象2、节流阀的性能较差,低速运动时由2、增加节流联锁装置于振动使调节位置变化3、节流阀内部、外部有泄露3、检查零件的精密配合间隙,修配或更换超差的零件,连接处要严加密封4、在简式的节流阀中因系统负荷有变4、检查系统压力和减压装置等部化使速度突变件的作用以及溢流阀的控制是否正常5、油温升高,油的粘度度降低,使速5、液压系统稳定后调整节流阀或度逐步升高增加散热装置6、阻尼装置堵塞,系统有空气,出现6、清洗零件,在系统中增设排气压力变化及跳动阀油液要保持洁净五、换向阀的故障分析和排除方法故障现象故障分析排除方法滑阀不换向1、滑阀卡死1、拆开清洗脏物,去毛刺2、阀体变形2、调节阀体安装螺钉使压紧力均匀或修研阀孔3、具有中间位置的中对弹簧断裂3、更换弹簧4、操纵压力不足4、操纵压力必须大于0.35Mpa5、电磁铁线圈烧坏或推力不足5、检查、修理、更换6、电器线路故障6、消除故障7、电液换向阀控制油路无油或被堵7、检查原因并消除8、M、.K、H型电液换向阀背压底8、调整背压或清洗或失灵电磁铁控制的1、滑阀卡住或摩擦力大1、修研或调配滑阀方向阀作用时2、电磁铁不能压到底2、校正电磁铁高度有响声3、电磁铁芯接触面不良或不平3、消除污物、修正电磁铁铁芯电磁铁过热或烧毁1、电压比规定的电压高,引起线圈发热1、检查电压电源,是其符合要求2、电磁线圈绝缘不良2、更换电磁铁3、电磁铁芯末吸到低而烧毁3、查明原因,加以排除,并更换六、液控单向阀的故障分析和排除方法故障现象故障分析排除方法油液不逆流1、控制压力过低1、提高控制压力使其达到要求值2、控制油管道接头漏油严重2、紧固接头、消除漏油3、单向阀卡死3、清洗4、油中有杂质,将锥面或钢球损坏3、更换油液逆方向不密封1、单向阀在全开位置上卡死1、修配、清洗有泄露2、单向阀锥面和阀座锥面的接触不均匀2、检修或更换保压性能差1、控制油管接头和接合面有泄露现象1、紧固接头,消除漏油2、单向阀锥阀和阀座线接触不好2、研磨阀座或更换单向阀3、单向阀卡死3、清洗使用寿命短1、换向冲击大1、消除冲击,系统增加卸压阀七、油温过高的故障分析和排除方法故障现象故障分析排除方法当系统不需要油压卸荷回路动作不良检查电气回路、电磁阀。
工程机械橡胶液压软管常见故障及原因分析

工程机械橡胶液压软管常见故障及原因分析工程机械橡胶液压软管常见故障及原因分析工程机械用橡胶液压软管常见故障及原因分析橡胶液压软管是混凝土运输车、压路机、挖掘机、装载机等工程机械液压系统的重要部件,使用中经常出现渗漏、裂纹、破裂、松脱等故障,但人们往往不分析故障原因而只是简单地更换软管,使用不久后又会重复相同的故障。
液压软管的松脱或破裂,不仅浪费液压油、污染环境,而且影响工作效率,甚至发生事故,危及人机安全。
液压橡胶软管分为高压胶管和低压胶管两种,高压胶管为钢丝编织,缠绕胶管,一般由外胶层、钢丝加强层、中胶层和内胶层4部分组成;内胶层直接与液压油接触,一般用合成橡胶制成。
胶管的承载能力取决于钢丝加强层,该层是胶管的骨架,通常用钢丝编织,缠绕而成。
高压、超高压多采用多层钢丝编织,缠绕骨架;低压胶管以编织棉、麻线代替编织钢丝,一般用于低压回油管道。
液压软管的故障原因主要有:安装与使用不当、系统设计不合理和软管制造不合格等。
1、外胶层的故障1.1 软管外表出现裂纹在寒冷环境下,软管外表出现裂纹会使软管受到弯曲。
若发现软管外表有裂纹时,要注意观察软管内胶是否出现裂纹,并决定是否立即更换软管。
因此,在寒冷环境下不要随意搬动软管或拆修液压系统,必要时应在室内进行。
如果需要长期在较寒冷环境中工作,应更换耐寒冷软管。
1.2 软管外表出现鼓泡,软管外表出现鼓泡是由于软管质量不合格或是使用不当。
如果鼓泡出现在软管的中段,多为软管生产质量问题,应及时更换合格的软管;如果鼓泡出现在软管的接头处,很可能是由于接头安装不当所致。
钢丝编织,缠绕胶管接头与胶管连接端有可拆式、扣压式两种形式,可拆式接头外套和接头芯上有六角外形,接头芯的外壁呈圆锥形,便于拆装胶管。
接头芯与螺母连接后,穿入钢丝防止松脱。
扣压式胶管接头由接头外套和接头芯组成,装配时需剥离外胶层,套人接芯头,拧紧接头外套,然后在专用设备上用模具扣压,使胶管得到一定的压缩量,以达到紧密连接。
浅谈液压系统的故障及排除方法
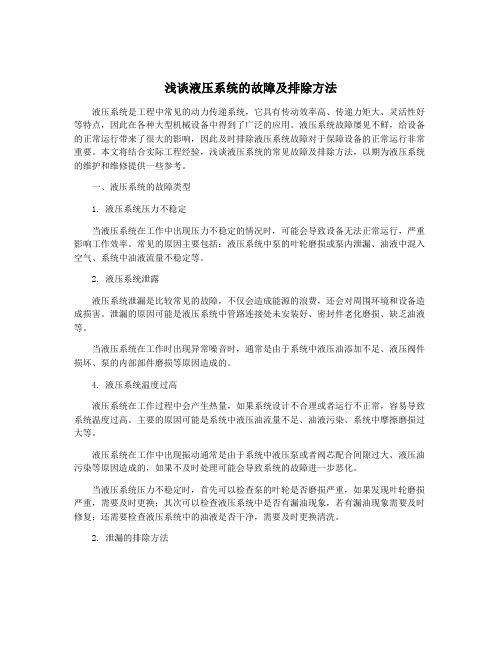
浅谈液压系统的故障及排除方法液压系统是工程中常见的动力传递系统,它具有传动效率高、传递力矩大、灵活性好等特点,因此在各种大型机械设备中得到了广泛的应用。
液压系统故障屡见不鲜,给设备的正常运行带来了很大的影响,因此及时排除液压系统故障对于保障设备的正常运行非常重要。
本文将结合实际工程经验,浅谈液压系统的常见故障及排除方法,以期为液压系统的维护和维修提供一些参考。
一、液压系统的故障类型1. 液压系统压力不稳定当液压系统在工作中出现压力不稳定的情况时,可能会导致设备无法正常运行,严重影响工作效率。
常见的原因主要包括:液压系统中泵的叶轮磨损或泵内泄漏、油液中混入空气、系统中油液流量不稳定等。
2. 液压系统泄露液压系统泄漏是比较常见的故障,不仅会造成能源的浪费,还会对周围环境和设备造成损害。
泄漏的原因可能是液压系统中管路连接处未安装好、密封件老化磨损、缺乏油液等。
当液压系统在工作时出现异常噪音时,通常是由于系统中液压油添加不足、液压阀件损坏、泵的内部部件磨损等原因造成的。
4. 液压系统温度过高液压系统在工作过程中会产生热量,如果系统设计不合理或者运行不正常,容易导致系统温度过高。
主要的原因可能是系统中液压油流量不足、油液污染、系统中摩擦磨损过大等。
液压系统在工作中出现振动通常是由于系统中液压泵或者阀芯配合间隙过大、液压油污染等原因造成的,如果不及时处理可能会导致系统的故障进一步恶化。
当液压系统压力不稳定时,首先可以检查泵的叶轮是否磨损严重,如果发现叶轮磨损严重,需要及时更换;其次可以检查液压系统中是否有漏油现象,若有漏油现象需要及时修复;还需要检查液压系统中的油液是否干净,需要及时更换清洗。
2. 泄漏的排除方法液压系统泄漏的排除方法主要包括检查管路连接处是否牢固,需要及时拧紧或更换液压管路连接件;检查液压系统中的密封件是否老化严重,需要及时更换;保证系统中油液的充足,避免系统缺油。
液压系统温度过高时,需要检查系统中的油液是否污染,需要定期更换液压油;需要检查系统中的摩擦部件是否磨损严重,需要及时更换润滑油或者润滑部件。
液压系统常见故障原因及排除方法

3、
轴向密封损坏;
3、
更换密封件;
液
4、
与之配套的安全阀损坏。
4、
更换安全阀。
控
单
1、
更换检修;
向
2、
拆检控制液管,保证畅通;
阀
1、
顶杆断折、变形顶不开钢球;
3、
更换检修,换密封件;
2、
闭锁腔不能回
2、
控制液路阻塞不通液;
4、
拆检。
液,
立柱千斤顶小
3、
顶杆处损坏,向回路串液;
回5f白
4、
顶杆与套或中间阀卡塞,使顶杆不
大且立柱千斤
液通回液;
顶动作慢
2、阀垫、中阀套处O形圈损坏。
2、更换上井拆换。
3、阀体外渗液
1、接头和片阀间O形圈损坏;
2、连接片阀的螺栓螺母松动;
3、轴向密封不好,手把端套处渗液
1、更换O形密封圈;
2、拧紧螺母;
3、更换上井,拆换密封件。
4、操作手把折断
1、重物碰击而断折;
2、与阀片垂直方向重压手把;
3、重调安全阀。
1、泵吸入空气;
泵
4、液压系统后
2、液箱中没有足够乳化液;
1、拧紧接头、更换坏管;
噪音
3、安全阀调值太低发生反作用。
2、更换安全阀;
3、更换截止阀;
1、泵站或管路漏液
4、更换蓄能器或重新充气。
站
2、安全阀损坏;
3、截止阀漏液;
1、添液、查液后盖严;
5、工作卸尢液
4、蓄能器充气压力不足。
2、清洗过滤器或更换;
流
3、分析水质、化验乳化油。
1、乳化液箱口未盖严实;
液压系统故障的检查与排除(三篇)

液压系统故障的检查与排除液压系统故障排除的五种基本方法:望、闻、摸、切、嗅一、望:看到什么。
1、看系统的配置是否正常,包括:泵、阀、执行元件、工作油液、滤油器、散热器等;2、看速度(流量):看执行机构运动速度是否有异常现象;3、看压力:看液压系统中各测压点的压力值大小及波动;4、看油液:观察油液容量是否合适,是否清洁,有无变质,油中是否有泡等;5、看泄漏:看液压管道各接头处、阀板结合处、液压缸端盖处、液压泵轴伸出处是否有渗漏、滴漏和油垢现象。
二、闻:听到什么。
1、听噪声:判断听到的声音是否属于噪声,噪声的源头在哪,是液压泵、马达、阀等液压件还是系统的管路或与元件连接的工作机构。
2、听冲击声:听系统的冲击声是否属于正常。
冲击声的时间:液压阀换向时冲击,还是莫名地发声。
冲击声的规律性:有节奏还是无规律。
3、听泄漏声:听油路内是否有细微不断的声音。
4、听敲打声:听液压件运转时是否有敲打声。
5、听相关人员反映。
三、摸:感觉到什么。
1、摸温升:用手摸运动部件表面,检查是否发热。
2、摸振动:感觉是否有振动现象。
3、摸爬行:感觉运动件有无“爬行”现象。
4、摸松紧程度:检验螺纹连接松紧程度。
5、摸密封性:对看不到的地方,检查是否有漏油现象。
四、切:用压力表判断。
1、各处的压力值是否正常:泵的吸油、出油,马达的进油、出油,油缸两腔的油压,阀的工作压力、控制压力等;2、压力是否有波动,波动是否在设计范围内。
五、用嗅觉判断。
1、闻一下油液是否发臭变质;旧车:使用时间长,油液成分会变质,发臭等怪味,新车:检查加油是否有误操作,防止加错油。
2、闻整系统是否有异味,出自何处。
液压系统故障的检查与排除(二)液压系统是一种利用液体传递能量和动量的技术,广泛应用于各种工程和机械设备中。
然而,由于使用条件和设备老化等原因,液压系统可能会出现故障。
本文将介绍液压系统故障的常见检查和排除方法。
首先,对于液压系统故障的检查,我们可以按照以下步骤进行。
液压系统常见故障以及排除

液压系统常见故障的诊断及消除方法
1 常见故障的诊断方法
1.1 简易故障诊断法
1〕询问设备操作者,了解设备运行状况。
其中包括:液压系统工作是否正常;液压泵有无异常现象;液压油检测清洁度的时间及结果;滤芯清洗和更换情况;发生故障前是否对液压元件进行了调节;是否更换过密封元件;故障前后液压系统出现过哪些不正常现象;过去该系统出现过什么故障,是如何排除的等,逐一进行了解。
2〕看液压系统压力、速度、油液、泄漏、振动等是否存在问题。
3〕听液压系统声音:冲击声;泵的噪声及异常声;判断液压系统工作是否正常。
4〕摸温升、振动、爬行及联接处的松紧程度判定运动部件工作状态是否正常。
1.2 液压系统原理图分析法
根据液压系统原理图分析液压传动系统出现的故障,找出故障产生的部位及原因,并提出排除故障的方法。
结合动作循环表对照分析、判断故障就很容易了。
1.3 其它分析法
液压系统发生故障时根据液压系统原理进行逻辑分析或采用因果分析等方
法逐一排除,最后找出发生故障的部位,这就是用逻辑分析的方法查找出故障。
为了便于应用,故障诊断专家设计了逻辑流程图或其它图表对故障进行逻辑判断,为故障诊断提供了方便。
2 系统噪声、振动大的消除方法
3 系统压力不正常的消除方法
4 系统动作不正常的消除方法
5 系统液压冲击大的消除方法
6 系统油温过高的消除方法
7 液压件常见故障及处理
7.3 液压缸常见故障及处理〔
7.4 压力阀常见故障及处理
7.4.1 溢流阀常见故障及处理。
液压系统常见故障及排除方法.

液压系统常见故障及排除方法:液压系统大部分故障并不是突然发生的,一般总有一些预兆。
如噪声、振动、冲击、爬行、污染、气穴和泄漏等。
如及时发现并加以适当控制与排除,系统故障就可以消除或相对减少。
一、振动和噪声(一液压元件的合理选择(二液压泵吸油管路的气穴现象排除方法:(1增加吸油管道直径,减少或避免吸油管路的弯曲,以降低吸油速度,减少管路阻力损失。
(2选用适当地吸油过滤器,并且要经常检查清洗,避免堵塞。
(3液压泵的吸入高度要尽量小。
自吸性能差的液压泵应由低压辅助泵供油。
(4避免油粘度过高而产生吸油不足现象。
(5使用正确的配管方法。
(三液压泵的吸空现象液压泵吸空主要是指泵吸进的油中混入空气,这种现象不仅容易引起气蚀,增加噪声,而且还影响液压泵的容积效率,使工作油液变质,所以是液压系统不允许存在的现象。
主要原因:油箱设计和油管安排不合理,油箱中的油液不足:吸油管浸入油箱太浅:液压泵吸油位置太高:油液粘度太大:液压泵的吸油口通流面积过小,造成吸油不畅:滤油器表面被污物阻塞:管道泄漏或回油管没有浸入油箱而造成大量空气进入油液中。
排除方法:(1液压泵吸油管路联接处严格密封,防止进入空气。
(2合理设计油箱,回油管要以 45度的斜切口面朝箱壁并靠近箱壁插入油中。
流速不应应太高, 防止回油冲入油箱时搅动液面而混入空气。
油箱中要设置隔板。
使油中气泡上浮后不会进入吸油管附近。
(3 油箱中油液要加到油标线所示的高度吸油管一定要浸入油箱的 2/3深度处,液压泵的吸油口至液面的距离尽可能短,以减少吸油阻力。
若油液粘度太高要更换低的油液。
滤油器堵塞要及时清除污物。
这样就能有效的防止过量的空气浸入。
(4采用消泡性好的工作油液,或在油内加入消泡剂。
(四、液压泵的噪声与控制从液压泵的结构设计上下功夫。
(五、排油管路和机械系统的振动避免措施:(1用软管连接泵与阀、管路。
(2配置排油管时防止共振与驻波现象发生。
(3配管的支撑应设在坚固定台架上。
液压管路系统常见故障原因分析及使用维护要点

液压管路系统常见故障原因分析及使用维护要点摘要:管路系统是液压系统的重要组成部件,管路一旦出现故障,整个液压系统都将失效。
通过介绍管路系统组成,分析归纳管路系统故障原因,在此基础上,总结管路系统维护注意要点,为液压管路系统维护提供参考与支撑。
【关键字】液压;管路系统;故障原因;维护0 引言液压管路系统作为液压系统工作介质的流动通道,是液压系统各部附件的纽带,也是保证液压系统正常、安全工作的关键组成。
但液压管路的工作环境较为复杂,液压泵压力脉动、高温高压油液冲击等现象,都可能引起液压管路共振,甚至导致管路疲劳断裂、密封破损等事故,因此了解液压管路系统组成,分析管路系统常见故障原因,对液压系统保持良好的运行性能尤为重要。
1. 液压管路系统基本概念液压管路可以分为工作管路和非工作管路,如压力管路、吸油管路、回油管路属于工作管路,而漏油管路、先导管路则属于非工作管路。
各类管路的主要组成都是包括液压导管、管接头和管路支撑附件等部分。
1.1 液压导管液压导管包括硬导管和软管。
常用液压硬导管有不锈钢管、铝管、钛管等。
不锈钢管多用于液压系统的压力管路及高温、振动、经常拆卸区域的管路;铝合金导管常用于液压系统的回油管路、吸油管路、放油管路等低压管路;钛合金材料强度高,重量轻,在液压系统的中低温场合应用较多。
液压软管一般用于有相对运动的部附件之间,它能够吸收液压系统中的冲击和振动[3],可以分为橡胶软管、氟塑料管、尼龙管等类型。
1.2 液压管接头液压管接头一般由接头体、连接套或连接螺母及密封件三部分组成,是用于连接管件与液压泵、液压阀、油箱等元件的液压附件,根据连接方式不同,管接头可分为卡套式、扩口式、焊接式及快速接头等类型。
2. 液压管路系统故障原因分析对液压管路系统,其故障现象通常是渗漏或泄漏。
导致该类故障现象的原因大致可分以分为管路固有缺陷、安装不当、疲劳失效、腐蚀老化等类型。
2.1 固有缺陷对导管,金属材料本身的缺陷,如材料不均匀、夹杂物等,或管道在加工制造、装配过程中,产生的一些如划痕、压痕、凹坑、裂纹等缺陷,在循环高压油液冲击下,这些有缺陷位置,很有可能出现裂纹而发生泄漏故障[4]。
- 1、下载文档前请自行甄别文档内容的完整性,平台不提供额外的编辑、内容补充、找答案等附加服务。
- 2、"仅部分预览"的文档,不可在线预览部分如存在完整性等问题,可反馈申请退款(可完整预览的文档不适用该条件!)。
- 3、如文档侵犯您的权益,请联系客服反馈,我们会尽快为您处理(人工客服工作时间:9:00-18:30)。
常见液压系统故障分析和排除方法一、故障概述:1、液压油的泄漏2、液压油的粘度与工作油度密切相关3、液压元件的磨损失效,温度对液压元件材料热胀的影响4、油液污染物对液压系统造成不确定因素的故障二、液压系统的常见故障1、压力故障:压力不够、压力不稳定、压力调节失灵、压力损失大2、动作故障:速度达不到要求,没有动作,动作方向错误,负载速度明显下降,起步迟缓、爬生,3、振动和噪音4、系统发热三、液压系统故障的特点1、故障的多样性和复杂性:压力不稳定常与振动噪声同时出现,系统压力故障往往和动作故障一起。
2、故障的隐蔽性:液压传动是依靠在密闭管道内具有一定压力能的油液来传递动力的,系统的元件内部结构及工作状况不能从外表进行直接观察。
因此,它的故障具有隐蔽性,不如机械传动系统故障那么直观,又不如电气传动那样易于检测,液压装置的损坏与失效,往往发生在系统内部,由于不便拆装,现场的检测条件也很有限,难以直接观测,使得液压系统故障分析比较困难。
3、引起同一故障的原因和同一原因引起故障的多样性一个故障有多种可能的原因,而且这些原因常常是互相交织,相互影响,如系统压力达不到要求,其产生原因可能是泵引起的,也可能是溢流阀引起的,还可能是中心回转体引起的,此外,系统的执行元件的泄漏也会引起系统压力不足。
液压系统中的一个故障可能多种多样的故障,例如:同样是混入空气,轻则会引起流量、压力的波动,严重时会引起泵吸不进油。
对于一种症状有多种可能原因的情形:应采取有效手段剔除不存在的原因,对于一个故障源产生多个症状的情形,可利用多个症状的组合来确定故障源。
故障产生的偶然性:液压系统在运行过程中,会受到各种各样的随机性因素影响,尤其是污染物的浸入,如阻尼孔的堵死、换向阀阀芯的卡死,电磁铁吸合不正常等等,这些故障没有一定的规律可循。
4、典型故障1)泄漏和堵塞,泄漏又分为内泄漏和外泄漏。
内漏是指液压元件内部的油液从高压区域到低压区域的泄漏,它会使液压系统的压力降低,执行元件不能正常工作,外漏是液压系统内的油液流到液压系统外部的泄漏,它污染环境和设备。
堵塞就是油液由于受阻不能到达指定元件(部位)或缓慢达到,它会使执行元件无法正常工作或无法工作,甚至会使液压元件损坏,例如溢流阀的阀芯或回油口堵塞,会使液压系统的压力无法控制,系统压力无限升高,造成液压元件损坏。
下车多路阀的先导溢流阀(充液阀)堵塞,会使支腿水平油缸伸出时,无杆腔的压力油过高,使油缸弯曲变形损坏。
滤油器的堵塞会造成系统背压过高,使系统动作混乱。
堵塞,就是阀芯、阀杆卡死,节流孔和油管等被异物堵塞,造成液压油不能到达需要动作的执行元件中去或流回油箱,使液压系统不能正常工作或不能工作,甚至使液压元件损坏。
例如压力控制阀内的阀芯卡死,还可能造成动力元件(液压泵)损坏。
再如油泵吸油滤芯发生堵塞,将会造成油泵吸空产生噪音,甚至使油泵损坏。
2)液压系统故障诊断方法感官诊断法:A、视觉诊断法:观察油箱内工作油有无气泡和变色(白浊、发黑)现象,油液设备的噪音、振动和爬行常与油液中有大量气泡有关。
B、观察密封部件、管接头、液压元件的安装接合面等处的漏油情况,结合观察压力表指针在工作过程中的振摆、掉压以及压力调不上去等情况,可查明密封破损、管路松动以及高低亚串腔等不正常C、观察工作状况并进行分析,同时观察设备时候抖动、爬行和运行速度不均匀等现象并查出产生故障的原因。
听觉诊断法:液压系统正常工作声音有稳定的韵律和节奏,熟悉和掌握这些正常的音律和节奏,就能准确判断液压系统中的元件是否运转正常,同时根据音律和节奏变化的情况以及不正常声音产生的部件可分析确定故障发生的部位的损伤情况。
A、高音刺耳的啸叫声通常是吸进空气,液压泵吸油管松动或油箱油面太低及液压油裂变质、有污物、消泡性能降低等原因B、嘶嘶声或哗哗声为排油口或泄漏处存在严重的漏油漏气现象C、哒哒声音表示电磁阀的电磁铁吸合不良,可能是电磁铁内可动铁芯与固定铁芯之间有污物阻隔,或者是推杆过长。
D、粗沉的噪声往往是液压泵或液压缸过载而产生。
4、自动降降臂:原因:平衡阀内部密封不严、油缸内部损伤5、变幅抖动A、起臂、降臂均都抖动在起、降臂时都抖动,有时还伴有响声,尤其是油温过高或环境温度高的情况下,此故障的原因是变幅油缸过紧,主要是变幅油缸导向套或活塞上的尼龙支撑环受温度的影响,受热膨胀。
造成导向套与活塞杆之间或活塞与缸筒之间间隙变小,形成过紧,使变幅油缸伸缩伸缩时所受阻力较大,产生爬行。
此外,导向套或活塞上用于安装支撑环的沟槽清根不好,尼龙支撑环安装时不能到位,也会造成油缸过紧,产生爬行。
处理办法为:油缸解体后,将尼龙支撑环内径或外径用车床车去一点,或将安装支撑环的沟槽进生清根处理。
B、降臂抖动:主要原因是在平衡阀上,平衡阀的开启压力调整过高,使变幅缸在回缩时要有很高的压力才能打开平衡阀,油缸无杆腔(大腔)的液压油才能够回油箱。
而一旦油缸无杆腔的液压油开始流回油箱时,压力下降,平衡阀又关闭,这样反反复复,形成了油缸回缩时快慢不均,产生了爬行、抖动。
调整平衡阀的开启压力即可解决问题。
平衡阀的问题是:平衡阀的导控活塞与阀套之间间隙过大,在推动导控活塞时,不能产生液压阻尼作用,使导控活塞快速推动滑阀,油压下降后活塞又快速复位,闭锁回缩油路,形成了油缸回缩快慢不均,产生抖动。
6、变幅缸爬行:空气的侵入会导致变幅缸爬行,可开动液压系统以最大行程使工作部件快速运动,强制排除空气,变幅缸端盖密封圈太紧或过松,应调整密封圈,使之紧松合适,保证活塞杆能用平稳拉动而无泄漏。
变幅缸内腐蚀、拉毛、可除去锈蚀和毛刺7、卷扬系统1)卷扬无动作或无压力A、压力发生系统的油泵、中心回转体、溢液阀、分流阀内泄漏故障B、卷扬操纵阀的阀体或阀杆损伤C、液压马达内泄漏过大D、操作卷扬系统时,当在操纵阀一档位置时,卷扬系统工作异常,而操纵阀在二档位置时,工作正常,此时的原因是:装有力矩限制器的起重机,液压系统上装有卸荷阀,卸荷阀内的单向阀封闭不严,也将造成这种故障8、无法降钩或降钩动作慢,且压力高A、卷扬平衡阀内的控制活塞上的阻尼孔堵塞或阻尼螺堵过紧造成堵塞,使控制活塞由于活塞后的压力油无法流出,滑阀不能推开,卷扬马达就不能回油B、平衡阀的控制活塞卡死。
9、重物自动下降卷扬制动器处于常开状态,其原因为:制动器油缸活塞在开启位置卡死,不能复位。
制动器弹簧损伤,压紧力减低。
制动带或干式制动器的制动片粘有油污,制动器打滑。
液压系统的回油滤清器滤芯堵塞,会形成回油背压升高,回油背压升高也会使制动器处于开启状态10、重物失控快速下降原因:液压马达内的配油盘损伤,在液压马达进行下降工作时马达的回油没有通过正常油路回油(马达—平衡阀—组合操纵阀—油箱)。
而是由于马达的内漏,液压油通过马达的泄油口直接流回油箱,平衡阀不能控制其下降速度,造成重物快速下降。
平衡阀内的控制活塞或滑阀在开启位置卡死。
11、卷扬下降发抖:平衡阀内的控制活塞与阀套间隙过大,在控制活塞推动滑阀时,控制活塞后部的液压油没有阻尼作用,快速推开滑阀,又快速回位,使马达的下降速度时快时慢,形成发抖(如其严重,也将会造成重物失控快速下降),或控制活塞上的阻尼螺栓(包括阻尼螺栓上的螺堵)脱落,形成阻尼孔增大,也会造成卷扬下降发抖。
12、伸缩系统无压力或压力过低,不能伸缩吊臂A、压力系统发生故障B、伸缩操纵阀阀体或阀杆损伤,形成内漏C、伸缩油缸内密封件损坏,缸筒或活塞损伤、缸筒变形、活塞杆内的通油芯管损伤D、伸臂溢流阀调整压力过低或损坏13、不能缩臂但压力高A、油缸内密封件损坏,使油缸有杆腔的液压油漏入到无杆腔,此时压力过低,无法打开平衡阀,无杆腔的液压油无法流回油箱,甚至可能会使油缸向外伸出。
B、变幅操纵阀上的二次溢流阀压力调整过低,不能打开平衡阀,变幅缸无杆腔的液压油无法流回14、吊臂伸缩发抖:A、伸缩油缸的导向套上的尼龙支撑过紧或活塞上的尼龙支撑过紧,可当地进行加工处理。
B、吊臂的滑块过紧,应进行调整C、吊臂的滑块润滑不够,尤其是吊臂尾部的滑块,应进和行涂抹润滑脂,对吊臂尾部的滑块可将吊臂全部伸出并平放,在吊臂的搭接处的上部堆放润滑脂于滑道处,然后缩回吊臂。
这样将润滑脂带入吊臂内涂抹在吊臂的内壁上,往复进行几次,就能使滑块与吊臂之间有了润滑脂。
15、吊臂自动缩回A、平衡阀内部密封件损坏,阀芯或阀座损伤、弹簧损坏等原因,造成封闭不严。
B、伸缩油缸内部密封件损坏,缸筒或活塞损伤,活塞杆内的通油芯管损伤等原因,造成油缸内漏16、其他故障:电器或机械部分发生故障,也会影响液压系统。
如:力矩限制器部分发生故障后,就可能使卸荷电磁阀线圈通电,使液压系统卸荷,系统不能形成压力。
注意事项:起重机液压系统所发生的故障大部分是由于液压油不清洁所造成,经常检查液压油是否清洁,是否产生乳化、变质、液压油的油量是否够,还要经常更换或过滤液压油、清洗油箱、更换滤油器滤芯等,使液压油时刻保持清洁状态,以减少故障的发生和延长液压元件的使用寿命。
在新出厂的起重机或大修后的起重机,初期使用三个月时,一定要更换液压油,清洗油箱。
因为起重机在初期使用时,新的液压元件磨合中产生的杂质以及管路中的杂质,会随液压油流回油箱,所以三个月时必须更换液压油和清洗油箱。
如果更换的液压油没有产生乳化和变质,可沉淀48小时,经过滤可继续使用,但液压油最多使用年限为两年。
由于故障的产生大部分是由于液压油不清洁所造成,所以我们不要为了节省费用就忽视了更换液压油的重要性。
在拆卸高压油管及部件时,应确认内部的压力去除后方可进行拆卸。
液压元件解体后,密封件应尽可能的全部更换,在安装时不要在扭曲状态下进行,密封件通过螺纹部分或有锐利边缘时,要用聚乙烯带或类似物品将螺纹或锐利边缘包住,以防密封件损坏。
在安装尼龙挡圈时应注意压力油的方向,对向压力油的方向,密封件在前,尼龙挡圈在后,不能装后,尼龙挡圈在安装后,挡圈的开口不能过大,不允许过多的突出部分超出密封件的外边缘。
液压元件在解体时,应注意做好记号,因为有些元件是对研的,形成偶件,例如,柱塞液压马达的柱塞和缸体,换向阀的阀体和阀杆等,这样在装配时就不会搞错,否则会产生内漏增大或阀杆或柱塞卡死,装配前一定要进行清洗,并用压缩空气进行吹干,装配时应涂抹润滑脂,以便于装配。