电弧炉熔炼节能技术应用现状与发展
电熔窑炉节能技术优化及应用

电熔窑炉节能技术优化及应用电熔窑炉是一种常见的工业设备,广泛应用于冶金、建材、化工等领域。
由于其高温、高能耗的特点,其能耗一直是工业生产中的一个难题。
为了解决这一问题,近年来人们对电熔窑炉进行了节能技术优化及应用研究,取得了一系列显著成果。
电熔窑炉节能技术优化主要包括节能技术和节能措施两个方面。
节能技术是指通过技术创新来提高设备的能效,从而实现节能的目的;而节能措施则是指通过一系列管理和操作上的改进,来减少能源的消耗。
下面将就电熔窑炉节能技术优化及应用进行详细介绍。
一、技术优化:电熔窑炉采用多项技术来提高能效,减少能源消耗,降低生产成本。
最主要的技术包括下面几种:1. 电熔技术改进:通过改进加热方式和温度控制方式,提高电熔窑炉的能效。
目前,有一些公司利用新型的电磁感应加热技术,可以让熔化过程更为高效,进而减少能耗。
2. 电熔炉内部结构优化:通过改进炉内结构、提高炉体材料的导热性能等措施,减少能量的损失,从而提高能效。
3. 废气余热利用:利用余热回收装置,将炉内产生的废气余热转化为电能或热水,进一步提高能效。
4. 先进的控制系统:采用智能化的控制系统,对电熔窑炉的运行进行智能监测和调控,提高设备的稳定性和能效。
5. 能源替代技术:如利用生物质能替代化石能源、采用太阳能、风能等可再生能源,减少对传统能源的依赖,从而降低能耗。
二、节能措施:除了技术改进外,一些管理和操作上的改进也能在一定程度上减少能源消耗,具体包括以下几个方面:1. 电熔炉合理设计和选型:在选购设备时,应根据生产需求和能源利用情况,选择合适的电熔炉型号和规格。
2. 定期检查和维护:定期对电熔窑炉进行检查和维护,保持设备的良好状态,减少因设备损耗而带来的能量损失。
3. 优化生产流程:合理调整生产参数,避免空转和过剩消耗,降低生产过程中的能耗。
4. 培训和技术支持:对操作人员进行专业的操作培训,提高其对设备操作的技术水平以及对能源消耗的认知水平。
2023年真空电弧炉行业市场分析现状

2023年真空电弧炉行业市场分析现状真空电弧炉是一种重要的热处理设备,主要用于金属材料的熔炼和热处理。
在现代工业发展中,真空电弧炉在航空、汽车、船舶、机械制造等领域有着广泛的应用。
本文将对真空电弧炉行业的市场分析现状进行详细的介绍。
首先,真空电弧炉行业在近年来取得了较快的发展。
随着国内经济的不断发展和技术的不断进步,真空电弧炉在金属材料热处理领域的应用越来越广泛。
据统计,2019年我国真空电弧炉的产量达到了1000多台,产值超过了10亿元,行业规模较大,市场潜力巨大。
其次,真空电弧炉在航空航天领域的应用较为广泛。
航空航天领域对金属材料的质量和性能要求非常高,而真空电弧炉具有高温、高真空度、高熔化能力等特点,可以有效的熔炼和热处理各种金属材料,满足航空航天领域的需求。
因此,在航空航天领域,真空电弧炉有着广阔的市场前景。
再次,汽车制造领域也是真空电弧炉的主要应用领域之一。
汽车制造业的发展对金属材料的需求量非常大,对材料的性能和质量要求也很高。
真空电弧炉可以对汽车制造常用的钢材、铝材、镍基合金等进行熔炼和热处理,提高材料的强度、硬度和耐磨性,提高汽车的安全性和使用寿命。
因此,在汽车制造领域,真空电弧炉也有着较为广泛的应用。
最后,随着科技的不断进步,真空电弧炉技术也在不断的创新和发展。
近年来,随着新材料和新工艺的涌现,真空电弧炉也不断更新和升级。
目前,一些企业已经研究出了新型的真空电弧炉,具有高温度、高真空度、高加热速度、低能耗等特点,使得真空电弧炉在更多的领域有着更好的应用前景。
综上所述,真空电弧炉行业在我国市场的发展前景广阔。
随着国内经济的不断发展和技术的不断进步,真空电弧炉行业有望在航空、汽车、机械制造等领域得到更广泛的应用。
同时,随着科技的不断创新,真空电弧炉的技术也将不断更新,为行业带来更多的发展机遇。
电熔窑炉节能技术优化及应用

电熔窑炉节能技术优化及应用电熔窑炉是冶金、化工等领域最为常用的热处理设备之一。
其通过电加热将原料熔化,然后进行混合、浇铸、喷涂等工艺流程,是重要的工业生产装备。
但随着国内外经济发展,能源短缺和环境问题越来越严重,如何节约能源、降低碳排放成为电熔窑炉设备优化的重要方向。
近年来,国内外的电熔窑炉节能技术得到快速发展,主要包括以下几个方面:1.电磁感应加热技术电磁感应加热技术是目前电熔窑炉节能效果最突出的一种技术。
该技术通过产生强磁场,使金属材料产生涡流,从而使其产生热量,实现加热的效果。
相比传统燃气、电阻加热,电磁感应加热的能源利用率更高,热效率几乎可以达到100%。
同时,该技术不需要燃料,不产生废气和废水,能大幅度降低能源消耗和环境污染。
2.燃料气体回收技术在传统电熔窑炉中,燃料气体可以通过排放管道排出去,造成能源和环境的浪费。
而燃料气体回收技术则可以将排放的燃气通过净化、液化等手段进行回收再利用,从而最大限度地节约能源和减少环境污染。
3.废热回收技术在电熔窑炉生产过程中,大量热能会被释放出来,如果不进行回收利用,将会造成能源的浪费和环境的污染。
废热回收技术可以将释放的废热进行回收再利用,如用于供热、供水等领域,从而实现能源的节约和环境的减排。
4.智能控制技术智能控制技术可以通过传感器、计算机等技术手段实现对电熔窑炉生产过程的自动监测和调节。
如对于温度、压力、氧化还原等指标的实时监测和调控,可以大幅度提高生产效率和生产质量,同时避免了能源和材料的浪费。
电熔窑炉节能技术的应用可以提高生产效率、降低成本、减少能源消耗和环境污染,具有广泛的应用前景。
未来,随着科技的不断发展,电熔窑炉节能技术将会得到更加广泛和深入的应用。
电熔窑炉节能技术优化及应用

电熔窑炉节能技术优化及应用电熔窑炉是一种利用电能作为能源进行熔炼的设备,广泛应用于金属冶炼、玻璃熔化、陶瓷制造等工业领域。
传统的电熔窑炉在高温高能耗的情况下存在能源浪费、环境污染等问题。
为了提高电熔窑炉的能源利用率、降低排放物的产生,节能技术优化及应用显得尤为重要。
1. 燃烧系统优化传统电熔窑炉的燃烧系统存在着燃烧不充分、热量损失大的问题。
通过采用先进的燃烧控制技术和燃料预热技术,可以有效提高燃烧效率,降低燃料消耗和热量损失,从而实现节能降耗的目的。
2. 高效热传递技术利用换热器等设备实现余热回收和热量利用,可以将废气中的热能回收再利用,降低能源消耗。
采用高效隔热材料和热工设计,减小窑炉的散热损失,提高热传递效率,也是提高窑炉能源利用率的重要手段。
3. 智能控制系统智能控制系统可以实时监测窑炉的工作状态,根据熔炼的需要进行智能调节,优化能源利用,提高生产效率。
通过精细化的控制和优化,可以减少窑炉的能源消耗,降低生产成本。
4. 节能设备应用在电熔窑炉中,引入新型节能设备如能量回收设备、超导电磁加热技术等,可以有效提高窑炉能源利用效率。
通过技术改造和设备升级,实现能源的合理利用,减少能源浪费。
1. 炼钢行业钢铁行业是电熔窑炉的重要应用领域,传统的电熔窑炉在炼钢过程中能源消耗较大。
近年来,一些炼钢企业通过优化窑炉的燃烧系统,引入高效的热传递技术和智能控制系统,实现了能源消耗的大幅度降低。
2. 玻璃制造业玻璃制造业对电熔窑炉的能耗要求较高,而且排放物易对环境造成污染。
一些玻璃企业通过引入热能回收设备和换热器,在生产过程中充分利用余热,减少了能源消耗和排放物的排放。
3. 金属冶炼业金属冶炼业对电熔窑炉的能源要求也较为严格。
一些金属冶炼企业通过采用超导电磁加热技术和高效的隔热材料,提高了窑炉的能源利用效率,减少了能源消耗和生产成本。
三、电熔窑炉节能技术优化的发展趋势1. 绿色能源应用随着环保意识的不断提高,绿色能源在电熔窑炉中的应用将会逐渐增加。
电弧炉炼钢工艺的现状及发展趋势

绪论改革开放以来,我国电弧炉炼钢技术紧跟世界电炉炼钢工业的发展趋势,得到了快速发展。
特别是冶金工艺流程的革命性变换,如电炉从三期操作发展到只提供初炼钢水的两期操作,从模铸到连铸,从出钢槽到偏心底出钢,以及为了满足连铸生产的快节奏提高炉子生产率而采用多能源的综合利用等等,所有这些改变都是促使为冶金工艺服务的电炉装备也取得了突破性的发展。
近十年,我国从国外先后引进了交流超高功率电弧炉、直流电弧炉、高阻抗电弧炉、双壳炉和竖炉。
通过这些设备的调试、操作、维护以及备品的制造,提高了我国电炉制造的设计制造水平。
在消化吸收与创新的基础上,我国大容量电弧炉的国产化奠定了基础。
当前电弧炉正朝着大型电弧炉、超高功率供电技术、采用各种炉外精炼、发展直接还原法炼钢、逐步扩大机械化自动化及用电子计算机进行过程控制等的发展,所以我们进行了电炉炼钢的设计,以适应潮流的发展。
本设计机密结合实际,包括八个部分,配料计算,炉型设计,电气设备选择,炉外精炼,连铸设计,烟气净化系统设计,车间布局设计。
本设计由内蒙古科技大学高等职业技术学院武哲毅设计。
在编写的过程中得到了张芳老师的指导,在此特别表示感谢。
摘要当前电弧炉正朝着大型电弧炉、超高功率供电技术、采用各种炉外精炼、发展直接还原法炼钢、逐步扩大机械化自动化及用电子计算机进行过程控制等的发展,所以我们进行了电炉炼钢的设计,以适应潮流的发展。
电炉的主要产品是钢材,而钢的质量取决于电炉冶炼技术和工艺,目前我国钢铁产业大量整合趋向于集中,整合资源优化升级。
本设计根据指导老师的课题范围,查阅相关资料,结合南京地区实际条件,优化设计150t直流电弧炉炼钢车间。
本次设计查阅国内大型电炉车间设计的相关内容和文献资料,明确本次设计的目的、方法,并向老师请教可行性方案。
结合《炼钢设备及车间设计.》、《炼钢设计原理》、《炼钢设计原理》等资料进行设计提纲的书写。
对电炉进行配料计算,计算出电炉炼钢的原料配比。
国内外电炉炼钢技术现状与发展趋势
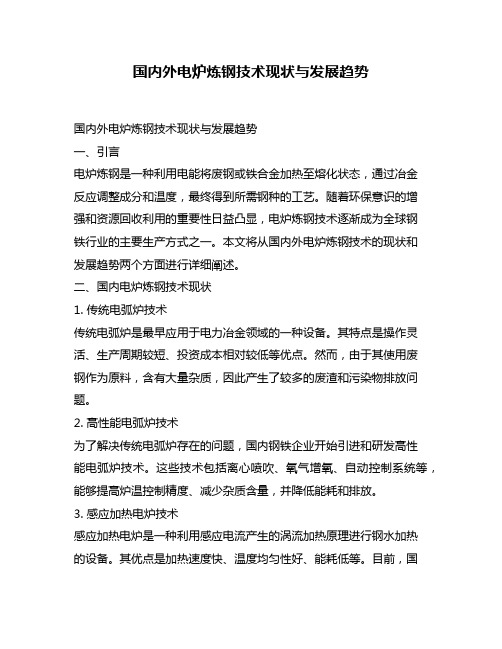
国内外电炉炼钢技术现状与发展趋势国内外电炉炼钢技术现状与发展趋势一、引言电炉炼钢是一种利用电能将废钢或铁合金加热至熔化状态,通过冶金反应调整成分和温度,最终得到所需钢种的工艺。
随着环保意识的增强和资源回收利用的重要性日益凸显,电炉炼钢技术逐渐成为全球钢铁行业的主要生产方式之一。
本文将从国内外电炉炼钢技术的现状和发展趋势两个方面进行详细阐述。
二、国内电炉炼钢技术现状1. 传统电弧炉技术传统电弧炉是最早应用于电力冶金领域的一种设备。
其特点是操作灵活、生产周期较短、投资成本相对较低等优点。
然而,由于其使用废钢作为原料,含有大量杂质,因此产生了较多的废渣和污染物排放问题。
2. 高性能电弧炉技术为了解决传统电弧炉存在的问题,国内钢铁企业开始引进和研发高性能电弧炉技术。
这些技术包括离心喷吹、氧气增氧、自动控制系统等,能够提高炉温控制精度、减少杂质含量,并降低能耗和排放。
3. 感应加热电炉技术感应加热电炉是一种利用感应电流产生的涡流加热原理进行钢水加热的设备。
其优点是加热速度快、温度均匀性好、能耗低等。
目前,国内一些大型钢铁企业已经开始采用感应加热电炉进行生产。
三、国外电炉炼钢技术现状1. 电弧顶吹转底吹技术欧洲一些先进的钢铁企业采用了电弧顶吹转底吹技术,即在高温下通过底部喷吹气体将冶金反应进行到底部。
这种技术可以提高冶金反应效率,减少杂质含量,并且可以利用多种原料进行冶金。
2. 水冷壳体技术美国的一些电炉炼钢企业采用了水冷壳体技术,通过在电炉壳体内部设置水冷设备,有效降低了电炉温度,减少了能耗,并且延长了设备寿命。
四、国内外电炉炼钢技术发展趋势1. 环保型电炉技术随着环保意识的增强,国内外钢铁企业开始重视电炉炼钢过程中的排放问题。
未来的发展趋势将是开发和应用更加环保的电炉技术,减少废气、废水和固体废弃物排放。
2. 智能化控制系统随着信息技术的快速发展,智能化控制系统在电炉炼钢领域得到了广泛应用。
未来的发展趋势将是进一步提高控制精度和自动化程度,实现智能化生产。
电熔窑炉节能技术优化及应用

电熔窑炉节能技术优化及应用电熔窑炉是目前广泛应用于工业生产领域中的一种高温设备,其主要用于各种金属和非金属材料的熔化和热处理,同时也可以用于生产玻璃、陶瓷等产品。
但是,由于其运行中需要大量耗能,所以其能源消耗成为限制其应用范围的主要因素之一。
为了解决这一问题,研究人员对电熔窑炉的节能技术进行了深入探索和优化。
在实践应用中,主要采用以下几种方法:1、提高电熔窑炉的热效率电熔窑炉运行中会产生大量的热能,其中绝大部分都会散失。
因此,通过提高电熔窑炉内部的热效率来降低能源消耗就成为了一个非常有效的方法。
首先,可以采用有效的隔热材料对窑炉进行保温。
这样可以减少窑炉散热的程度,提高内部温度,并在一定程度上降低加热所需的电能,从而达到节能的目的。
其次,可以尝试采用先进的加热方式,通过提高电熔窑炉内部的温度来提高其热效率。
其中,利用感应加热技术,通过变压器和感应线圈将电能转化为热能,直接作用于金属物料内部来加热其熔化,可以大大提高电熔窑炉的热效率。
2、改进电熔窑炉的结构设计电熔窑炉的结构设计对其能源消耗也有着重要的影响。
因此,改进电熔窑炉的结构设计也可以成为一种有效的节能方法。
电熔窑炉的结构设计首先应该考虑到能够降低能量损失。
在设计时,可以采用多层绝缘体结构,使得其内部的热量不易流失,从而大大提高其热效率。
同时,合理设计窑炉进、出口的位置和尺寸,以保证制品出入和气流循环畅通,进一步提升电熔窑炉的能效。
3、合理使用电熔窑炉合理使用电熔窑炉也是节能的一个重要的方面。
操作人员需要从以下几个方面出发来减少电熔窑炉的能源消耗:(1)合理调节加热功率电熔窑炉的加热功率应该根据其工作状态和熔炼物料的特点进行调整。
过大的加热功率会造成能量浪费,同时也会增加生产成本,因此必须在使用时合理调节。
(2)减少窑炉空转时间在电熔窑炉开始工作前,需要花费一定的时间将其预热。
如果在这个过程中发生空转,将会造成大量的能量浪费。
因此,操作人员应尽量缩短空转时间,减少能源的消耗。
钢铁冶炼中的电弧炉熔炼技术

钢铁冶炼中的电弧炉熔炼技术钢铁是现代工业的基础材料之一,其应用广泛,被运用于建筑、制造、汽车制造、航空等领域。
在钢铁生产过程中,冶炼技术的进步对钢铁品质和生产效率的提高起着至关重要的作用。
而电弧炉熔炼技术作为钢铁冶炼的一种先进技术,由于其高效率、低成本等优点,在现代钢铁冶炼工业中已成为主流。
电弧炉熔炼技术是一种将废旧钢材、废钢料和矿石等铁原料直接熔炼成新钢材的技术。
相比传统钢铁冶炼技术,电弧炉熔炼技术不需要过多的预处理工作,能够有效地回收废钢和废料,可以大大降低生产成本,同时熔炼的新钢材品质也更为优异。
电弧炉熔炼技术是利用电弧放电的高温高压作用将原料熔化,再通过加入不同的合金元素和杂质来调整质量,最终获得钢铁坯料。
具体而言,熔炼的过程是将铁原料放置在电极之间,然后将电极启动电弧放电,放电过程中产生的高温可以使原料熔融,并在熔融的过程中控制加入不同的元素和调整温度和成分,以获得高强度、高硬度和高韧性的钢材。
电弧炉熔炼技术的优点在于它的高效率和低成本。
除了可以回收大量的废弃物和废料外,电弧炉还可以根据需要调整温度和成分,以生产不同质量的钢材。
此外,电弧炉熔炼还可以通过适当的控制工艺参数和操作过程来减少钢材中的空泡和杂质,最终获得更高品质的钢材。
然而,与传统钢铁冶炼技术相比,电弧炉熔炼技术在一些方面还存在一些局限性。
首先,电弧炉熔炼工艺中需要大量的电能和电极材料,这也意味着生产成本相对较高。
其次,在工艺参数的选择和加热的过程中,误操作可能导致不必要的损失,影响钢材的质量。
另外,电弧炉还存在噪声和气味等环境污染问题,这些也是需要解决的难题。
对于电弧炉熔炼技术的未来发展,一方面,随着环保意识的不断提高,人们对于电弧炉对环境的负面影响也越来越关注。
因此,电弧炉的生产过程需要更加精细化和规范化,以避免污染环境。
另一方面,通过相关的技术创新,电弧炉的生产成本可以不断下降,比如大规模应用新型节能高效电极或者减小生产过程中的能量消耗。
- 1、下载文档前请自行甄别文档内容的完整性,平台不提供额外的编辑、内容补充、找答案等附加服务。
- 2、"仅部分预览"的文档,不可在线预览部分如存在完整性等问题,可反馈申请退款(可完整预览的文档不适用该条件!)。
- 3、如文档侵犯您的权益,请联系客服反馈,我们会尽快为您处理(人工客服工作时间:9:00-18:30)。
电弧炉熔炼节能技术应用现状与发展胜山 (工业大学机电研究 430070)摘 要:叙述了电弧炉在采用熔炼新技术,降低电气设备电能损耗,控制出钢温度、渣量和留钢量,加强炉料管理和生产组织管理等方面的节能措施及其应用效果,探讨了电弧炉熔炼节能技术的发展趋势。
关键词:电弧炉;熔炼;节能电弧炉和感应电炉是铸钢的两种主要熔炼设备。
与感应电炉比较,电弧炉具有如下主要优点:电弧炉炉渣参与冶金反应,可有效去除硫和磷;对原材料的要求较低,可以使用废钢和铸造回炉料以任何比例组成的炉料;钢水质量容易得到保证,适于生产各种铸钢件。
但是也有不足,例如:有电弧超高温作用,元素烧损较多;无电磁搅拌作用,不利于钢液温度均匀和夹渣上浮;加热速度较慢,热效率较低,能耗较高。
据测算:输入电弧炉的能量只有约 57%直接用于电弧炉炼钢,其余43%左右为损失热量。
损失的热量中,约12.5%为炉盖和炉壁冷却水损失,约23%为废气带走的损失,约7.5%为炉渣带走的损失。
因此,电弧炉的节能是一个重要课题。
近40年来,电弧炉节能降耗的多种技术措施得到发展和应用。
图1定量描述了这些技术措施在降低电弧炉的熔炼时间、电耗与电极消耗方面的预期效果。
但是,能源和电极的实际消耗量要比图中数据高:德国在2005年的能耗是525kW·h /t+天然气11m 3/t ;美国2000年的能耗数据是电500kW·h /t+煤23kg/t+氧气34m 3/t+天然气8.5m 3/t 。
图1 电弧炉熔炼技术措施的发展历程及其效果 可见:电弧炉的节能还是一项需要广大铸造工作者继续努力的长期课题。
电弧炉节能可从以下三个方面着手:一是采用新技术减少热损失;二是降低电弧炉有关电气设备的电能损耗;三是加强生产管理,降低能耗。
1 采用新技术1.1 高功率炼钢法高功率炼钢法是通过增大熔化功率,加大熔化电流,缩短熔化时间,来达到节能目的。
许多企业采用这项技术后,取得了较好的节能效果。
如某厂的3t电弧炉,原变压器容量为650kVA,在变压器容量改为1250kVA后,熔化期时间缩短了一半左右,吨钢电耗也随之降低。
但在采用高功率炼钢法时,应注意供电曲线的合理选用,不能整个过程都采用高功率炼钢,否则不但不会使炼钢单耗降低,反而会使单耗增加。
如某厂一台5t电弧炉,变压器扩容后,整个过程都采用高功率炼钢,结果炼钢单耗反而上升了46kW·h/t。
实际生产中,应根据电弧炉的特性曲线确定作业电流,同时按熔炼各时期的特点确立用电规。
目前,我国铸钢行业所用的电弧炉数量很多,却很少有测定电弧炉用电特性曲线的。
图2图2 交流电弧炼钢炉的用电特性曲线从图2可见:(1)电压一定时,随电流增大,来自电网的功率P1增大。
到达P曲线的峰值以后,由于设备的功率因数COSφ降低,无功功率P3增大,P1不但不增大,反而急剧下降。
可见,盲目增大电流不仅无益,而且对电网和设备都非常有害。
(2)实际上用于炼钢的有用功率P2的峰值与P1峰值所对应的电流并不一致。
P2峰值对应的电流I0,一般都小于P1峰值所对应的电流I0′。
P l最大时,由于电器设备的阻抗而损失的无功功率P3增大,电效率η下降,有用功率P2并不最大。
因此,电弧炉运行的作业电流应该是I0,无论如何也不应超过I0′。
(3)目前还不可能用仪表显示有用功率P2并用以控制电炉的供电,一般都用电流控制。
电流控制是灵敏的,但如无特性曲线为依据,就可能导致效率降低,电耗增大。
例如:当作业电流为I1时,认为功率不足而增大电流,当然是正常的,但如简单地将作业电流增大到I2,输入的功率大幅度增加,而有用功率并未增加。
电弧炉炼钢过程中,由于各熔炼阶段具有不同的特点,所以还应根据每一熔炼阶段的炉况确定各自的作业电压,以便在尽可能的发挥变压器的供电能力的同时,减少热损失,并提高炉衬的寿命。
作业电压愈高,则输入功率愈大。
但电压愈高,电弧也会愈长,对炉墙、炉盖的辐射也增强,热损失增大。
只有在熔化期间,电弧埋入炉料后,才可用最高电压,正好这时需要最大的功率。
氧化期间,钢液处于沸腾状态,而且炉渣的黑度系数大,易于吸热,电弧的能量较易于传递到炉渣和钢液,可用适中的作业电压。
由于此时电弧是裸露的,不宜用最高电压。
还原期间,钢液静止,不利于提温,且此时炉渣黑度系数小,易反射电弧热量于炉衬、炉盖,故应避免电弧太长,宜用低电压作业。
每一台电弧炼钢炉安装完毕后,都应根据电气设备配置的具体情况,通过短路试验测定线路的基本参数,再计算每一电压下线路的平均参数,画出每一级电压下的用电特性曲线。
每一铸钢厂都应按照电炉设备特点和所炼钢种冶炼要求,制定合理用电规,规定冶炼各阶段作业电压;再根据电炉在每一种电压下作业时的特性曲线,规定作业电流。
据初步估算,如采用合理用电规,熔炼电耗至少可降低5%。
前述5t电弧炉,在重新合理选用供电曲线后,单耗下降了104kw·h/t,取得了较好的节能效益。
1.2 辅助熔化技术及设备随着电弧炉炼钢技术的发展,辅助熔化技术及设备越来越完善。
常见的辅助熔化技术有吹氧助熔、煤气或油助熔和底气搅拌等。
在电弧炉冶炼过程中进行强化用氧的目的除了加快脱碳速度以外,还充分利用氧气与原料中易氧化元素发生化学反应所放出的热量,达到节能降耗的效果。
各种元素氧化的理论热值如表1所示。
吹氧助熔可以使熔化期缩短20~30min,钢水熔炼能耗可下降 80~100kw·h/t。
强化用氧技术已经成为电弧炉炼钢重要的技术方向。
表1 熔池中各元素氧化产生的理论热值元素产物反应热相对成本(参考值)kJ/kg kW·h/kgAl Si Mn Fe C C Al2O3SiO2MnOFeOCOCO214 57211 3292 1764 25011 63934 8384.053.150.601.183.239.683.73.26.01.80.5~0.60.3~0.6合理的吹氧助熔时间,不但可以达到快速化料的目的,还可以节约氧气,减少炉料烧损。
一般应在炉料大部分发红、炉底出现熔池时,开始吹氧助熔,压力掌握在0.4~0.6MPa。
可采用废电极块、焦炭提高配碳量,适当提高用氧强度。
在钢中磷含量不高的情况下,尽量不要使用矿石,因为矿石氧化是吸热反应,受影响环节多,脱碳速度慢,而氧气氧化是放热反应,脱碳速度快,明显缩短熔氧时间。
如每吨钢氧化掉 0.1%碳,用氧气氧化比用矿石氧化省电16 kW·h。
煤气助熔是将煤气和氧气由喷枪送入炉,在炉膛燃烧以加热炉料。
喷枪的结构较为简单,即用2根不同直径的不锈钢管,同心地套在一起而成,并安装在炉前一侧的旋转架上。
油氧喷枪可安装在炉膛的低温区,渣线以上 150~200 mm的炉墙上与水平线成13°~18°夹角。
一般采用煤气助熔后,可节电 15%~20%,效果显著。
电炉炼钢中应用喷粉技术,在国外已十分普遍。
部分辅料如石灰粉、碳粉、铁合金粉、铝渣粉剂、脱硫剂等,依靠设置在炉前的料罐和粉体输送计量装置,以压缩空气或氮气作载体,直接喷吹到电炉溶池里。
粉状料的喷吹输送强化了冶炼过程,可有效地控制炉况,提高脱磷、脱硫反应速度,对节电、缩短冶炼时间均有良好的效果,同时改善了作业环境。
底气搅拌等技术可使熔化时间由原先的3~4h降至50~60min,也有着较好的节能效益。
1.3 泡沫渣埋弧冶炼技术泡沫渣埋弧冶炼技术是指:在电弧炉冶炼过程中,吹氧的同时向熔池喷碳粉或碳化硅粉,加剧碳氧反应,在渣层形成大量的CO气体泡沫,使渣层厚度达到电弧长度的2.5~3.0倍,电弧完全被屏蔽,从而减少电弧辐射,提高电弧炉的热效率,缩短冶炼时间,降低电能消耗,延长炉衬和炉顶的使用寿命,大幅度地提高生产率。
实现泡沫渣冶炼的方法很多.但无论哪种方法都是使渣中的FeO与C反应生成 CO气体,弥散在渣中,形成液渣膜分隔的密集排列的气孔状结构,CO气泡缓慢地从渣中溢出,使炉渣保持泡沫化的状态。
泡沫渣的碱度、渣中FeO质量分数等是影响发泡性能的重要参数。
图3、图4分别表明了泡沫渣碱度和成分对泡沫渣高度的影响。
图3 炉渣碱度对泡沫渣高度的影响图4 炉渣中w(FeO) 对泡沫渣高度的影响炉渣的粘度也影响泡沫渣的形成。
熔渣粘度低,发泡性能差。
随粘度的升高,熔渣发泡幅度增大,粘度为8Pa·s时达到最大值。
主要原因是:当熔渣粘度适当增大,气泡聚集长大上浮逸出的速度减慢,而使泡沫渣稳定时间持续延长。
若熔渣粘度过高,弹性较差,液渣膜易破裂,使气泡稳定性减小,故炉渣泡沫化的程度反而降低。
电弧炉炼钢采用泡沫渣埋弧冶炼工艺,能有效节能降耗。
因此无论是超高功率电弧炉还是普通功率电弧炉,采用泡沫渣冶炼工艺都很普遍。
其具体使用效果如下:(1)提高传热效率电弧炉炼钢是靠电弧加热。
若电弧过长,则对炉衬和炉顶的热辐射增加,使热损失增大,同时也使炉衬和炉顶的寿命降低,耐火材料消耗增加,生产率受到影响。
为克服上述缺点,不得不采用短电弧和大电流供电。
但是,电流过大会使电能消耗增加。
而泡沫渣冶炼工艺可使电弧被泡沫渣屏蔽,故可采用长电弧高电压供电,因而使电能消耗减少,同时也使传热效率得到提高,功率因数由0.63提高到0.88。
由于没有剧烈的沸腾,熔池的升温速度持续稳定,可达6~12℃/min。
图5为国某厂5 t电弧炉采用泡沫渣冶炼工艺与普通渣工艺的升温速度的关系曲线。
又由于电弧被屏蔽,使电弧稳定,电压和电流的波动减小,电弧闪烁亦相应减小,变压器的功率得以充分发挥,并能稳定电网,使传热效率由30%提高到60%。
图5 氧化期泡沫渣工艺与普通渣工艺升温过程比较(2) 降低电能消耗用长电弧高电压供电,可使电能消耗降低。
采用泡沫渣冶炼工艺,必须向熔池大量吹氧,形成以氧代电。
据某厂统计:采用泡沫渣冶炼工艺后,可使每炉钢的平均冶炼时间缩短 17 min,每吨钢节电116.3kW·h,炉衬寿命提高65%。
另外,由于加入碳粉等还原剂,使渣中FeO的还原率可达60%,使金属收得率得到提高。
(3)降低电极消耗电弧炉炼钢过程中电极消耗的50%~70%是由电极表面的氧化造成。
据测定,碳和石墨的氧化大约从500℃开始,超过750℃氧化急剧增加,且随着温度的升高而加剧。
电极表面氧化消耗的量 G与氧化速度V、电极表面积S、工作时间t有关,其表达式为:G ∝V·S·t可见电极在恶劣工作环境中工作时间越长,电极在高温下暴露在环境中的表面积越大,电极氧化损失也越大。
而采用泡沫渣埋弧冶炼工艺后,由于电弧被渣层屏蔽,电弧的辐射热相对于普通渣工艺减少,环境温度相对较低,因而可减少电极的氧化,又有利于提高二次电压,降低二次电流,使电能消耗减少,电极消耗减少2 kg/t钢以上,使生产成本降低,生产率提高,同时也使噪音减小,噪声污染得到控制。