机械加工过程中机械振动解决措施
机械加工过程中机械振动的成因及解决措施

机械加工过程中机械振动的成因及解决措施摘要:在我国机械加工行业发展日益加快的背景下,机械管理工作迎来更高的挑战。
虽然在一定程度上提高了我国机械加工的效率和精确度,但由于在加工过程中,刀具和被加工机械做周期性往复运动,因此加工过程中产生机械振动是难以避免的。
而一旦发生机械振动不仅会影响到机械加工质量,甚至也会导致加工机械出现损坏。
因此,研究机械加工振动的解决措施,对于促进我国机械加工行业的发展具有重要的意义。
关键词:机械加工;机械振动;成因;解决措施引言在以往的机械加工过程中,经常会出现振动现象,使加工的精准度和精细度受到严重影响。
引起机械振动的原因是多样的,本文分析了机械加工过程中机械振动的不同成因,并针对成因提出了解决措施。
一、机械加工过程中机械振动形成的原因(一)强迫振动形成的原因在整个机械加工过程中,设备加工生产会受到各类外界因素的影响,强迫振动作为主要出现的振动类型,是受到外界因素影响最多的一种振动。
强迫振动就是指在周期性外力的影响之下形成的受破振动,他主要代表的是一种驱动力,由外力影响而诞生的一种额外的驱动性力量。
[1]关于强迫振动,有以下几个特征。
首先是强迫振动本身不会影响到干扰力,因此在加工生产的工程中,强迫振动的体现并不直接,在生产加工阶段我们无法对强迫振动进行额外的干扰,只有后续技术工艺阶段加入进来之后,强迫振动的现象才会停止。
其次是强迫振动受到的外部影响很深,因此其发生频率与外界干扰的周期频率是非常相似的,大部分的强迫振动频率都保持在干扰周期频率的整倍数上。
最后是强迫振动还具有一定的辐射性,它很可能会引起机械的共振现象,进一步的影响到机械设备的作业情况,影响设备生产的精度。
因此总的来看,在思考强迫振动形成原因的时候,更多的是需要关注外部影响和干扰因素对强迫振动的影响,外部的干扰因素越多那么强迫振动的振幅也就越高。
(二)自激振动形成的原因自激振动同其他振动之间有明显的区别,也就是说,在开展自激振动的过程中,外力的影响没有相对应的周期性。
机械加工过程中机械振动的原因及对策分析
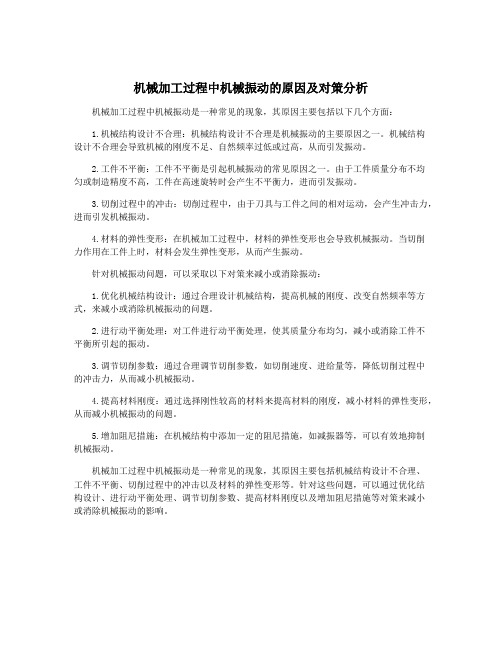
机械加工过程中机械振动的原因及对策分析机械加工过程中机械振动是一种常见的现象,其原因主要包括以下几个方面:1.机械结构设计不合理:机械结构设计不合理是机械振动的主要原因之一。
机械结构设计不合理会导致机械的刚度不足、自然频率过低或过高,从而引发振动。
2.工件不平衡:工件不平衡是引起机械振动的常见原因之一。
由于工件质量分布不均匀或制造精度不高,工件在高速旋转时会产生不平衡力,进而引发振动。
3.切削过程中的冲击:切削过程中,由于刀具与工件之间的相对运动,会产生冲击力,进而引发机械振动。
4.材料的弹性变形:在机械加工过程中,材料的弹性变形也会导致机械振动。
当切削力作用在工件上时,材料会发生弹性变形,从而产生振动。
针对机械振动问题,可以采取以下对策来减小或消除振动:1.优化机械结构设计:通过合理设计机械结构,提高机械的刚度、改变自然频率等方式,来减小或消除机械振动的问题。
2.进行动平衡处理:对工件进行动平衡处理,使其质量分布均匀,减小或消除工件不平衡所引起的振动。
3.调节切削参数:通过合理调节切削参数,如切削速度、进给量等,降低切削过程中的冲击力,从而减小机械振动。
4.提高材料刚度:通过选择刚性较高的材料来提高材料的刚度,减小材料的弹性变形,从而减小机械振动的问题。
5.增加阻尼措施:在机械结构中添加一定的阻尼措施,如减振器等,可以有效地抑制机械振动。
机械加工过程中机械振动是一种常见的现象,其原因主要包括机械结构设计不合理、工件不平衡、切削过程中的冲击以及材料的弹性变形等。
针对这些问题,可以通过优化结构设计、进行动平衡处理、调节切削参数、提高材料刚度以及增加阻尼措施等对策来减小或消除机械振动的影响。
述机械加工中振动原因及控制措施

论述机械加工中振动原因及控制措施摘要:随着我国经济的飞速发展,机械化加工技术在我国得到了前所未有的发展,机械加工中的振动是一种十分有害的物理现象。
通过分析机械加工中各种振动产生的原因和特性,提出了相应的减振措施。
在实际生产中,合理采用这些措施对保证零件表面品质、提高生产率有着积极的意义。
关键词:机械加工;振动;控制措施中图分类号:th161 文献标识码:a 文章编号:1、引言随着机械加工技术的不断广泛的应用,显现的问题也越来越突出,机械加工中的振动对加工表面质量和生产率有很大的影响,是一种十分有害的物理现象。
若加工中产生了振动,刀具与工件间将产生相对位移,会使加工表面产生振痕,严重影响零件的表面质量和性能;振动使刀具受到附加动载荷,加速刀具磨损,有时甚至崩刃;同时振动使机床、夹具等的连接部分松动,从而增大间隙,降低刚度和精度,缩短使用寿命,严重时甚至使切削加工无法继续进行,振动中产生的噪声还将危害操作者的身体健康。
为减小振动,有时不得不降低切削用量,使机床加工的生产效率降低。
因此,研究分析机械加工中的振动原因和特性,寻求控制振动的有效途径是很有必要的。
机械振动的类型分为自由振动、受迫振动和自激振动三类。
自由振动是在初始干扰力的作用下破坏了系统的平衡,仅靠弹性恢复力来维持的振动。
由于系统中总存在阻尼,自由振动会迅速衰减,所以对机械加工的影响不大。
受迫振动和自激振动都属于不衰减的振动,对机械加工的影响不容忽视。
下面主要分析这两种振动。
2、振动的类型及特征机械加工中产生的振动主要有受迫振动和自激振动(颤振)两种类型。
2.1受迫振动由外界周期性干扰力(工艺系统内部或外部振源)所激发的振动。
其主要特征是:(1)除由切削过程本身不均匀性所引起的受迫振动外,干扰力一般同切削过程无关。
干扰力消除,受迫振动停止。
(2)受迫振动的频率与外界周期性干扰力的频率相同或是它的整数倍。
(3)受迫振动的振幅与干扰力的振幅、工艺系统的刚度及阻尼大小有关。
机械振动研究机械振动的原因特性和控制方法

机械振动研究机械振动的原因特性和控制方法机械振动研究:机械振动的原因、特性和控制方法机械振动是指机械装置在工作过程中产生的波动现象,它会影响机械设备的正常运行和寿命。
本文将探讨机械振动的原因、特性以及一些常用的控制方法。
一、机械振动的原因1. 不平衡:机械设备中存在的不平衡质量会导致振动。
比如旋转部件的质量分布不均匀,转子中心轴偏离几何中心等。
2. 轴承问题:轴承的损坏、磨损或不良安装都可能引起机械振动。
轴承的故障会导致旋转部件的不规则运动,进而引起振动。
3. 动力装置问题:能源输入装置(如电机)的问题可能导致机械振动。
比如电机在转子动平衡或接线不良的情况下会引发振动。
4. 摩擦与间隙:摩擦力和间隙会导致机械部件的不稳定运动,产生振动。
此外,润滑不良也可能触发机械振动。
5. 外界激励:机械设备所处的工作环境也可能成为外界激励的源头。
例如,设备周围的振动源、流体力学问题或地震等都可引发机械振动。
二、机械振动的特性1. 振动的频率:振动的频率是指单位时间内振动的次数。
机械振动的频率通常以赫兹(Hz)为单位进行测量。
2. 振动的幅值:振动的幅值是指振动过程中的最大偏移距离或最大速度。
它可以用来描述振动的强度。
3. 振动的相位:振动的相位是指振动过程中的位置关系。
它可以描述不同振动源的相对运动状态。
4. 振动的频谱:机械振动的频谱是指将振动信号在频域上的表示方法。
通过分析振动频谱可以得到振动源的特性和故障信息。
三、机械振动的控制方法1. 动平衡技术:对于不平衡产生的振动问题,可以通过动平衡技术来解决。
动平衡是利用平衡机或振动仪等设备,在设备运行时进行动态平衡调整,使设备达到平衡状态。
2. 轴承维护与保养:定期对轴承进行维护和保养,包括润滑、紧固、检修等,可以减少机械振动的发生。
3. 振动隔离技术:通过使用减振器、隔振垫等装置来减小振动的传导和辐射,降低机械设备对周围环境的振动影响。
4. 减少摩擦与间隙:优化机械组件的设计和加工工艺,减小摩擦力和间隙,从根本上减少振动产生。
机械加工过程中机械振动的原因及对策分析
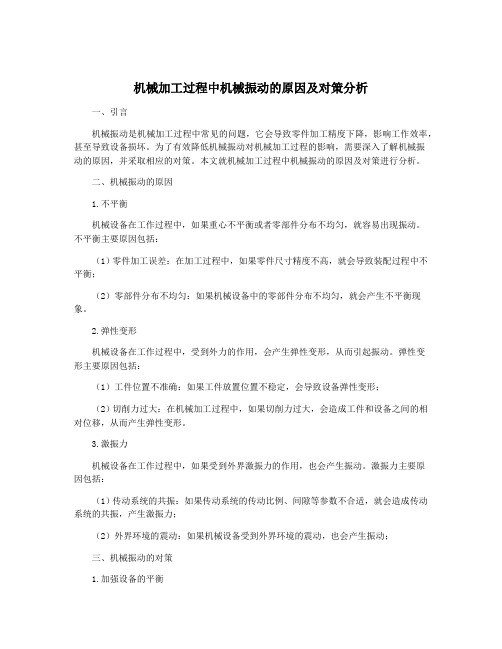
机械加工过程中机械振动的原因及对策分析一、引言机械振动是机械加工过程中常见的问题,它会导致零件加工精度下降,影响工作效率,甚至导致设备损坏。
为了有效降低机械振动对机械加工过程的影响,需要深入了解机械振动的原因,并采取相应的对策。
本文就机械加工过程中机械振动的原因及对策进行分析。
二、机械振动的原因1.不平衡机械设备在工作过程中,如果重心不平衡或者零部件分布不均匀,就容易出现振动。
不平衡主要原因包括:(1)零件加工误差:在加工过程中,如果零件尺寸精度不高,就会导致装配过程中不平衡;(2)零部件分布不均匀:如果机械设备中的零部件分布不均匀,就会产生不平衡现象。
2.弹性变形机械设备在工作过程中,受到外力的作用,会产生弹性变形,从而引起振动。
弹性变形主要原因包括:(1)工件位置不准确:如果工件放置位置不稳定,会导致设备弹性变形;(2)切削力过大:在机械加工过程中,如果切削力过大,会造成工件和设备之间的相对位移,从而产生弹性变形。
3.激振力机械设备在工作过程中,如果受到外界激振力的作用,也会产生振动。
激振力主要原因包括:(1)传动系统的共振:如果传动系统的传动比例、间隙等参数不合适,就会造成传动系统的共振,产生激振力;(2)外界环境的震动:如果机械设备受到外界环境的震动,也会产生振动;三、机械振动的对策1.加强设备的平衡对于不平衡造成的振动,可以采取以下对策:(1)提高零件加工精度:在零件加工过程中,应严格控制尺寸精度,避免误差导致的不平衡;(2)调整零部件分布:改变零部件的位置,使得机械设备的重心分布更加均匀。
2.增加刚度对于弹性变形引起的振动,可以采取以下对策:(1)稳定工件位置:通过改进夹具结构,提高工件的抓紧力,稳定工件的位置,减少弹性变形;(2)优化切削参数:通过调整切削速度、切削深度等参数,降低切削力,减少工件和设备之间的相对位移,减小弹性变形。
3.减少激振力对于激振力引起的振动,可以采取以下对策:(1)改善传动系统的设计:优化传动系统的传动比例、间隙等参数,避免传动系统的共振;(2)加强设备的隔振措施:通过在机械设备底部安装隔振装置,降低设备受外界环境震动的影响。
机械加工中振动的产生机理以及防治措施

机械加工中振动的产生机理以及防治措施一、机械加工过程中振动的危害振动会在工件加工表面出现振纹,降低了工件的加工精度和表面质量,低频振动时会产生波度;振动会引起刀具崩刃打刀现象并加速刀具或砂轮的磨损;振动使机床夹具连接部分松动,影响运动副的工作性能,并导致机床丧失精度;产生噪声污染,危害操作者健康;影响生产效率;二、机械加工过程中振动的类型机械加工过程中振动的类型:自由振动、强迫振动、自激振动。
1.自由振动工艺系统受到初始干扰力而破坏了其平衡状态后,系统仅靠弹性恢复力来维持的振动称为自由振动。
由于系统中存在阻尼,自由振动将逐渐衰弱,对加工影响不大。
2.强迫振动由稳定的外界周期性的干扰力(激振力)作用引起;除了力之外,凡是随时间变化的位移、速度和加速度,也可以激起系统的振动;强迫振动振源:机外+机内。
机外:其他机床、锻锤、火车、卡车等通过地基把振动传给机床机内:1)回转零部件质量的不平衡(旋转零件的质量偏心)2)机床传动件的制造误差和缺陷(如齿轮啮合时的冲击、皮带轮圆度误差及皮带厚度不均引起的张力变化,滚动轴承的套圈和滚子尺寸及形状误差)3)切削过程中的冲击(如往复部件的冲击;液压传动系统的压力脉动;断续切削时的冲击振动)强迫振动的特征:频率特征:与干扰力的频率相同,或是干扰力频率整倍数幅值特征:与干扰力幅值、工艺系统动态特性有关。
当干扰力频率接近或等于工艺系统某一固有频率时,产生共振相角特征:强迫振动位移的变化在相位上滞后干扰力一个φ角,其值与系统的动态特性及干扰力频率有关强迫振动的运动方程:图示:内圆磨削振动系统a) 模型示意图b)动力学模型c)受力图3.自激振动在没有周期性外力(相对于切削过程)作用下,由系统内部激发反馈产生的周期性振动;自激振动过程可用传递函数概念说明;切削过程本身能引起某种交变切削力,而振动系统能通过这种力的变化,从不具备交变特性的能源中周期性的获得补充能量,从而维持住这个振动。
机械加工中的振动问题分析及其控制措施探讨

制造 企业 在进行 零件的机械加 工中往往会遇到不 同程度 的振动 问题 , 振动 问题对机械加工的影响程度大小不一,但 是都会对加工生产的产品及 生产效率产生不 良影响,制造企业一般将机械 加工 定义为有害于加工质量 的现象 。 假 如机械加工 中出现了振动问题 , 加工工件与刀具都会发 生不 同程 度 的位移 , 位 移导致零件表 面的划 痕, 大大降低了产品 的生产质 量和性能; 机械加工 中出现的振动也会使 刀具受到振动带来的附加压力 ,导致刀具磨 损程度加深, 严重时则会 出现崩刃现象; 机械加 工中出现的振动也会使生产 加工 的夹具、 机床 等工具发生结构松动 , 增 加工具构件之 间的空隙, 一定程 度上减轻生产精度和刚度 , 减少工具的应用生命 , 严重情况下的振动 问题会 导致切削加工停止;机械加工 中出现的振动还会对技术人员造成不 同程度 的身体伤害 为了避免机械加工 中振动 问题的 出现, 制造企业很多情况下选 择减轻切削量, 延长 了加工生产的工期, 降低 了零件的生产效率。针对上述 问题 , 机械加 工中的振动 问题分析及其控 制措施探 讨显得十分必要。 机械 加工振动类型 常见的机械加工振动有三种, 即 自由振动、 受迫振动、 自激振动。 自由振 动 比较容易理解 , 一般是 由于外界干扰力发生的振动, 外界干扰力将 系统 的 平衡力破坏, 就会 出现不 同程度的弹性造 成的振动 。 制造企业 的机械加工系 统 自身具有一定阻尼 , 因此 , 自由振动会相对减弱 , 不会 对机械加工产 生过
2 . 2受 迫 振 动 的特 性
系学说 。 但 因为振动原理及振动缘 由说法不一, 自激振动产生的原 因至今为 止未能有一个统一说法 。 3 . 2自激振动的特性 首先 , 自激振动 不属于衰减类型的振动 , 这是 自激振动不 同于上述受迫 振动 的明显标志 , 当切削工作进行时 自激振动产生 , 切 削停 止, 自激振动也
机械加工振动产生的原因及消除方法

机械加工振动产生的原因及消除方法摘要:众所周知,在机械加工的过程中,存在着一个普遍的现象那就是机械振动,其实,机械振动是由多方面的因素造成的。
本文主要对机械加工过程中,机械振动的分类和特点进行了阐述,对机械振动的成因和影响展开了分析,同时对如何更好的解决机械振动产生的不利影响进行了深入的研究。
关键词:机械加工;振动产生;原因;消除方法引言机械加工是一项长期、循环往复的过程,由于长时间的运行,刀具和工件往往会受到很大的影响,因而不可避免的出现机械振动的情况。
在振动现象的影响下,加工部件的精度大大被降低,这对生产率的提高是非常不利的。
所以,应根据机械加工中出现的振动类型和产生的原因加以分析,采取有效的手段来降低或消除振动,从而提高机械生产的效率和质量。
1 机械加工振动类型在长时间的分析和实践中,按照机械振动产生的原因来分可以分为三类:自由振动、强迫振动和自激振动。
在机械运转时如果振动系统受到激振力的作用时会破坏机械的平衡状态,把能约束激振力的方式叫做自由振动,制造企业的机械加工系统自身具有一定阻尼,因此,自由振动会相对减弱,不会对机械加工产生过多的负面影响,属于机械加工振动中影响最小的一种振动。
而不同于自由振动,受迫振动和自激振动本身不能靠系统自身减弱振动,相反会对机械加工产生严重影响,本文接下来将对受迫振动及减振措施和自激振动及减振措施进行详细的分析和探讨。
2 振动产生的原因分析2.1自由振动产生的原因发生自动振动形式的主要原因是由于机械系统自身的弹力、重力作用下形成的,而没有任何外力参与。
因为组你和内耗都是振动系统中的一部分,比如简谐振动等,因此产生自由振动的原因是由于弹性元件或者惯性元件引发的。
2.2强迫振动产生的原因2.2.1高速回转出现不平衡状态,机械机床中高速回转的零件非常多,其中包括主轴、电机、皮带、磨床中的砂轮等等,就是由于出现不平衡状态导致出现离心惯性作用。
2.2.2机床传动零件缺陷所引起的周期性变化的传动力。
- 1、下载文档前请自行甄别文档内容的完整性,平台不提供额外的编辑、内容补充、找答案等附加服务。
- 2、"仅部分预览"的文档,不可在线预览部分如存在完整性等问题,可反馈申请退款(可完整预览的文档不适用该条件!)。
- 3、如文档侵犯您的权益,请联系客服反馈,我们会尽快为您处理(人工客服工作时间:9:00-18:30)。
机械加工过程中机械振动解决措施【摘要】机械加工过程中,由于机械内部结构、外部环境影响等因素,很容易出现机械振动问题,不仅会增加加工中的噪音,同时对机械本身也是一种损害。
因此,必须要找出机械加工中产生振动的原因,进而针对问题提出一系列的解决措施,保障机械运作的安全性与稳定性。
【关键词】机械加工;振动成因;有效措施;维护措施 1前言
随着我国科学技术不断发展,数控技术在机械生产中的应用愈加广泛。
机械生产能够一改传统生产的弊端,不仅能过提高生产效率,同时也能够提高生产精度,保障产品质量,是企业获得更多的经济效益与社会效益。
但由于我国企业自动化生产模式、技术还不够完善,机械加工过程中很容易出现振动问题。
机械振动问题不仅会影响生产环境,同时也会影响生产精度,产品质量无法获得保障。
因此,企业必须要重视机械振动问题,搞好机械运作质量。
2机械加工过程中振动产生的原因
2.1自然振动
由于机械的构造非常复杂,在通电之后,机械会受到电力驱使进行运作。
由于机械内部的机械零部件非常多,在使用过程中机械零件急速运转,不同零件受空气阻力,进而产生振动。
可以说,自然振动是机械运转中不可避免的振动问
题,也是最常见、原理最为简单的振动类型。
同时,自然振动还包括外部因素影响,生产地不平、风力因素等影响。
通常情况下,机械各个运作零件都有一个磨合期,在刚刚接通电流时会产生明显振动,随着不同零件正常运转,起振动力机会逐渐削弱。
总之,自然振动是受技术、环境的影响,是不可避免的振动问题,对机械整体运作不会产生明显影响。
2.2自激振动
有关调查研究显示,自然振动虽然是一种不可控问题,但如果不加以限制即会产生自激振动。
自激振动相比自然振动来说,就会对机械主体产生一定的伤害,轻则运作零部件松动、重则造成机械短路烧毁电线以及零件破损。
自激振动即是机械主体颤振,机械在正常加工中出现高频率振动,严重影响工业生产。
机械加工产生颤动的原因主要表现在以下几点:
(1)机械在加工过程中,由于加工主体硬度突然变化,刀具运作频率突然改变,进而发生刀崩问题后,即会因为内部零件运作不协调而产生自激振动。
(2)机械中的各个零部件在生产中,由于刀具与零件之间契合度不足或生产规格不规范,而产生运作冲突,进而产生自激振动。
(3)机械刀具质量不过关,刚性较差,在生产过程中刀杆振动,进而带动机械整体振动。
(4)在机械生产过程中,由于生产刀具与产品生产规格相冲突,导致切削量无法满足标准,进而出现自激振动。
总体来说自激振动主要是由机械内部因素所引起的问题,主要是机械刀具或零部件之间的问题而产生的自激振动。
但是在自激振动中,振动周期会出现一定变化。
2.3强迫振动
强迫振动与自激振动不同,强迫振动通常受外界因素与内部因素所产生的振动问题。
其内部因素主要是指:机械加工生产中,会由于机械各个部门零件所产生的离心振动,继而导致机械整体振动。
在加工中由于机械内的砂轮、皮带轮、齿轮、电机转子在快速运作中会产生一定的能量偏移(见图1),即机械运作中不平衡现象,进而造成运作惯性,迫使机械产生振动。
再者,导致强迫振动的原因可能由于机械质量不过关或机械故障引起,例如轴承轨道规格不过关或损坏等问题。
外部因素主要是由于人为因素影响,在实际操作中,由于工作人员常关常开,由于机械在启动中需要一定的适应期,让各个零件相磨合,进而出现振动问题。
3机械加工过程中振动问题解决措施
3.1自然振动解决措施
自然振动是机械运作中不可避免的振动现象,因此,为了减少噪音影响,避免产生自激振动,要避免机械直接接触刚性物质,如钢铁工具等,同时,也可以在机械支撑点安放
“脚垫”,避免机械金属直接接触地面,减少机械与地面之间的互刚性。
3.2自激振动解决措施
产生自激振动的主要原因是由于机械内部问题,因此,必须要从机械自身作出发点。
对于大型生产企业来说,在生产机械过程中,可以将振动源进行分离,或者在机械内部添加一些软性垫板,形成振动缓冲,减少振动频率,进而减低机械整体振动频率。
想要缓解自激振动,可以从以下几点出发:
(1)机械零部件参数对机械自激振动有着较大影响。
因此,可以针对自激振动原理或者生产主体参与,合理选择机械零部件,通常情况下,由于刀具参数都是固定的,其具有一定的运作范围,通常在生产中,想要减低刀具在生产中的自激振动,必须要保障生产参与刀具参数在0.7mm之内,进而满足刀具标准生产范围中。
同时,工作人员可以对刀具偏角进行调整,扩大刀具主偏角或前角。
刀具的后角角度尽量控制在一定角度内,尽量保障后角角度较小,提高切割面深度,减低生产中的摩擦,进而减少自激振动的发生几率(见图2)。
(2)降低重叠系数能够减少机械振动频率。
通常情况下,重叠系数主要是以“μ”来表示,通过加工形式、刀具纹理、加工工具纹理、运作用量来表示。
经实践表明,通过增加刀
具、交工工具纹理能够有效降低自激振动率。
在进行螺纹零部件加工生产中,μ值通常为0,这时机械整体不会发生自激振动。
刀具在切断零部件时,其μ值会达到1,机械再生效果非常明显,因此,可以通过改变交工工具、刀具的纹理来降低μ值,进而减少机械自激振动概率。
3.3强迫振动的解决方法
机械受内部、外部因素影响,在正常运作中会产生强迫振动,其主要因素是由于周期性外部因素所导致,因此,需要以周期外部因素为着手点:
(1)隔离外来振动:在生产加工时,需要尽量保障内部生产与外界相隔离,即阻隔外部振动干扰因素。
同时,也可以在机械表面添加一块软件垫板,进而降低外部振动因素对机械影响。
(2)降低激振力:激振力主要是由于机械内部零件运转速度不均而产生的振动,通过降低机械运作中的离心力与冲击力即可降低强迫振动。
首先针对砂轮、电机转子、高速运转元件等进行平衡调试,并安装平衡装置。
再者,就是提高机械内传动装置的稳定性,减少传动中的振动力,将传动皮带规格设置成长短一致,尽量减少皮带接头,并用斜齿轮来替代直齿轮,减少运作中的内部振动,进而减少强迫振动率。
4结语
机械振动产生原因有很多种,大体上可分为外部因素与
内部因素;可控因素与不可控因素。
但主要原因是机械主体因素,是由于科学技术并未达到一定高度。
因此,机械振动问题通常只能缓解、改善,无法从根本上解决。
参考文献:
[1]秦海亮.机械加工过程中机械振动的成因及解决措施探讨[J].现代职业教育,2016(17):30~31.
[2]吴舒.机械加工过程中机械振动成因及改善措施研究[J].橡塑技术与装备,2015(24):81~82.
[3]孙海峰.机械加工过程中机械振动的成因及解决措施[J].科技与企业,2016(08):219.。