模具主要零件加工工艺规范页
模具加工规范及规范流程图

模具加工工艺及流程图一.拉延模1.OP10下模座-凸模 一.模座毛坯铸件的龙铣数控加工方法. 1. 吊上毛坯铸件先光正合模用的安全平面,作为加工底面的基准.翻转模座加工底面,按微夹紧的状态精加工底面,保证底面加工精度, 精加工底面完成后打表测量底面四个角,检查底面平面度. 同时按图铣出十字键槽.铣基准边并打上钢印,并记录在案. 2. 模座毛坯铸件码槽已铸好的,按图检查码槽,不合尺寸的重新加工.如果码槽未铸出的在铣底面时一次加工到位.(注意一旦底面所有尺寸一次加工到位以后,不管正面够不够加工只能以底面基准为准,不能再偏中心,如果偏中心底面铣好的一些尺寸将全部报废.)3. 铣正面时按底面铣好的基准取中, 在加工前必须先测试2D 轮廓,导板确定是否够加工,验证程序是否正确。
验证正确后在数控上完成凸模2D轮廓分模线, 安全平面,到底限位块安装面, 与压边圈配合的Y 向导板,与压边圈配合的X 向导板,按图纸尺寸加工. 导板高度方向铣穿不留台阶.精加工完成后按图纸坐标尺寸钻出3销基准孔,打上钢印,并记录在案.。
4. 压边圈加工好与下模座组立3D 成型面.因下模压边圈与下模座组立后, 3销基准孔会被挡住,为方便组立后取基准加工,可以在安全平面凸台上多钻两个对称的基准孔.2.OP10压边圈与压边圈配合的Y 向内导板 合模用的安全平面凸台压边圈安装的到底限位块凸模2D 轮廓分模线安全螺杆安装孔起重吊装用的起重棒共4处压型时合模机的顶杆过孔底面加工余量百位线, 底面加工好到百位线为100豪米 装模快速定位用的十字键槽,也用在数控加工快速定位模具装模快速定位,常用于冲压另件流水线 装夹用固定模座的码槽,及装压板的压板面 凸模成型面模具的送料方向上下模连接板安装面 模座底面与压边圈配合的X 向内导板3销基准孔1. 压边圈按以上提到的铣底面的方法加工底面,同时把与与下模座配合的X向导板安装面, Y 向导板安装面按图纸尺寸加工, 耐磨板安装背托不能铣掉.同时铣X 向,Y 向基准边,打上钢印并记录.2. 按底面基准边取中心加工正面与凸模2D 配合的压边圈2D 分模线, 在加工前必须先测试2D轮廓,导板确定是否够加工,验证程序是否正确。
模具零件切削加工作业规程(doc 23页)

模具零件切削加工作业规程(doc 23页)模具零件切削加工作业规范1.目的本标准为切削加工提供作业规范和加工条件,确保加工工件的质量,为客户提供满意的产品。
2.适用范围本标准适用于切削加工工段从接工件到工件完成过程的作业。
3.参考文件3.1 《模具零件加工异常处理程序》STG043.2 《切削加工条件设定与确认作业规范》STH0305 4.主要职责与权限4.1 课长:提高生产效率.确保产品交期及质量,进行技术及工艺改善.工段与工段协调.督导组长与加工者严格按照作业标准操作加工.解决各种作业问题。
4.2 组长:审核蓝图,将工件排配到组员,并保证本规范贯彻加工作业始终。
4.3 加工者:依加工作业规范,在确保工件质量的前题下提高生产效率。
5.2.2 对上工序工件的数量、尺寸及加工余量进行检测,确认是否合格,如判定异常依<<模具零件加工异常处理程序>>处理。
5.2.3 认真审清蓝图上的每一个视图,看懂每条虚实线、符号及尺寸的数字标注,想象出工件完工后的形状、结构,并根据连络单上所注明的制程来考虑安排自己的加工工艺与程序制作工艺是否相符。
在保正质量前题下,提高生产效率。
5.2.4 工段主管依新生管系统日计划.根据现场生产情况进行组内排配加工.必要时可作适当调配。
5.3 加工条件的选择与设定5.3.1 加工用刀具的选择及其使用方法,目前使用的刀具主要有:5.3.1.1 粗铣刀为成型加工的重要刀具,其特点为切削量大、吃刀深、切削阻力小,多用于插孔、铣槽、铣台阶等粗加工。
5.3.1.2 精铣刀用此类刀具加工的工件,工件表面粗糙度低、且加工尺寸精确,在工件成型加工的最后过程用此类刀具,可以确保工件外观漂亮以及尺寸正确。
5.3.1.3. 键槽刀:一般多用于加工键槽。
5.3.1.4. 圆弧刀(内R刀、外R刀)为成型刀具,加工中根据不同的需要,选择适当直径的圆弧刀进行加工。
5.3.1.5 钨钢铣刀和钴钢铣刀特点为硬度高、轫性差,可对热处理后的工件进行加工。
模具零件加工工艺过程卡片

铣刀
游标卡尺
30
平面磨床
外形尺寸达到精度要求
磁性吸盘
砂轮
游标卡尺
高度规
底图号
50
QC
检查加工部位尺寸
55
钳工
标记
处数
更改文件号
签字
日期
标记
处数
更 改
文 件
号
签字
日期
编制日期
校对日期
标准化日期
会签日期
审核日期
机械加工工艺过程卡片
产 品 型 号
零部件图号
产 品 名 称
鼓风机外壳铝合金压铸模
零部件名称
加工CNC无法加工到位的
放电机
通用夹具
紫铜电极
三次元
慢走丝加工
加工高精度孔,落边料
慢走丝加工
通用夹具
铜丝
游标卡尺
底图号
50
QC
检查加工部位尺寸
55
钳工
标记
处数
更改文件号
签字
日期
标记
处数
更 改
文 件
号
签字
日期
编制日期
校对日期
标准化日期
会签日期
审核日期
机械加工工艺过程卡片
产 品 型 号
零部件图号
产 品 名 称
慢走丝加工
通用夹具
铜丝
游标卡尺
底图号
50
QC
检查加工部位尺寸
55
钳工
标记
处数
更改文件号
签字
日期
标记
处数
更 改
文 件
号
签字
日期
编制日期
校对日期
标准化日期
模具标准加工工艺.
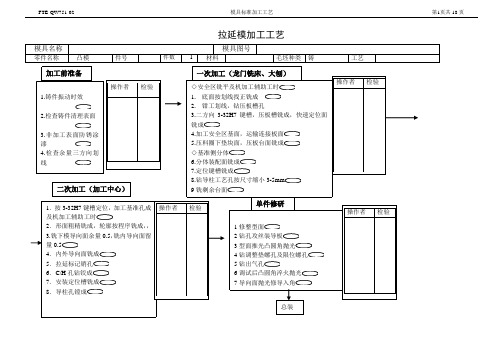
操作者
检验
单件修研
1. 按 DL 图修拉延圆角 2. 压料面推光 3. 清根修型面 4. 导 板 面 推 光 钻 螺 孔 , 装 导 板
操作者
检验
5. 钻出气孔 6. 制螺孔装顶件器 7 调试后工作部分淬火抛光 8 导向面推光,修导入角
模具名称
拉延模加工工艺
总装
模具图号
FTE-QW751-02
零件名称 总装工艺
9 加工镶块安装面,挡墙面成,定位键槽成
10 配作镶块丝孔,组装,仅中间前后两拼块同钻铰销孔成,装销钉定位(钳)
操作者
检验
二次加工(加工中心)
1.按 3-32H7 键槽定位,加工基准孔成
2.型面按程序粗、精铣成,铣上模导 向面基面余量 0.5 3.导向面铣成 4.拉延标记销孔 5.C/H 孔钻铰成 6.导套孔镗成
拼块同钻铰销孔成,装销钉定位(钳)
工艺
操作者 检验
二次加工(加工中心)
1.按键槽定位加工基准孔成及辅助工 时 2.轮廓按程序铣成,型面粗精铣成
3. 铣内导向或外导向面基面余量 0.5,
4.内外导向面铣成 5 上调整垫面铣成
操作者 检验
单件修研
1. 修拉延筋凸圆角,推光压料面 2. 导板面推光,,修倒入角 3. 制顶销,定位板,调整垫各螺孔 4. 调试后拼块真空淬火抛光 5. 制导板安装丝孔,安装导板
操作者
拉延模加工工艺
模具图号
1 材料
毛坯种类 铸
工艺
一次加工(龙门铣床、大刨)
◇安全区铣平及机加工辅助工时 1. 底面按划线找正铣成 2. 钳工划线,钻压板槽孔 3.二方向 3-32H7 键槽,压板槽铣成,快速定位面 铣成 4.加工安全区基面,运输连接板面 5.压料圈下垫块面,压板台面铣成 ◇基准侧分体 6.分体装配面铣成 7.定位键槽铣成 8.钻导柱工艺孔按尺寸缩小 3-5mm 9 铣剩余台面
注塑模具相关零件加工工艺过程卡片

实做工时
制造者
检验
等级
10
铣削
铣六面
20
平磨
磨上下面
30
钳工划线
划出型槽的轮廓线和各孔的位置线
40
铣削
铣型槽
50
钳工加工
钻螺纹孔和螺杆孔,攻螺纹
60
磨削
磨型槽及上下面达到设计要求
70
检验
工艺员
年月日
零件质量等级
定模座板工艺过程卡片
零件名称
定பைடு நூலகம்座板
模具名称及编号
充电器外壳
零件编号
CDQ-09-04
30
钳工划线
划出ø16螺孔中心线
40
钻削
钻削螺纹孔
50
钳工划线
划出ø8螺孔中心线
60
钻削
钻削螺纹孔
70
热处理
淬火
80
检验
工艺员
年月日
零件质量等级
型芯板工艺过程卡片
零件名称
型芯板
模具名称及编号
充电器外壳
零件编号
CDQ-09-15
材料名称
45钢
毛坯尺寸
300mm×280mm×70mm
件数
1
工序
机号
工种
施工简要说明
施工简要说明
定额工时
实做工时
制造者
检验
等级
10
铣削
铣六面
20
平磨
磨上下面
30
钳工划线
划出型槽的轮廓线和各孔的位置线
40
铣削
铣型槽
50
电火花
电火花加工精密部位
60
钳工加工
钻螺纹孔和螺杆孔,攻螺纹
模具标准零件加工工艺

标准零件加工工艺1、目的:有效地控制异常,提高效率,提高品质。
2、范围:适用标准零件的加工。
3、职责:无4、定义:无5、内容:5.1 油板(耐磨板):(如图)5.1.1工艺路线:铣床组→磨床组→锯床→铣床组→磨床组→铣床组→热处理→磨床组→铣床组→品检;5.1.2 铣床加工零件长宽方向的正四面体,单边留余量0.5mm;5.1.3 磨床见光零件长宽方向的正四面体,加工直角后送铣床;5.1.4 锯床加工零件Z方向的厚度,留余量1mm-2mm;5.1.5 铣床用飞刀加工零件Z方向的厚度,留余量0.5mm-0.6mm;5.1.6 送磨床加工Z方向的平面,留余量0.3mm-0.4mm;5.1.7 铣床加工平头螺丝扩孔及杯头;5.1.8 铣床倒角,去毛刺后送品检检测;5.1.9 送热处理加硬,硬度 52℃±2°;5.1.10 磨床精磨至图纸尺寸;5.1.11 铣床加工油槽;5.1.12 送品检检测;5.2 压块(斜顶座耐磨板);5.2.1工艺路线:铣床组→磨床组→锯床→铣床组→磨床组→铣床组→品管组→热处理→磨床组→铣床组→品检5.2.2 铣床加工零件长宽方向的正四面体,单边留余量0.5mm;5.2.3 磨床见光零件长宽方向的正四面体,加工直角后送铣床;5.2.4 锯床加工零件Z方向的厚度,留余量1mm-2mm;5.2.5 铣床用飞刀加工零件Z方向的厚度,留余量0.5mm-0.6mm;5.2.6 送磨床加工Z方向的平面,留余量0.3mm-0.4mm;5.2.7 铣床加工螺丝底孔,并倒角攻牙;5.2.8 品检检测后送热处理,HRC52℃±2°;5.2.9 磨床精磨至图纸要求尺寸;5.2.10 铣床加工油槽;5.2.11送品检检测;5.3 斜顶座:5.3.1工艺路线:磨床→铣床→磨床组→线切割→品检5.3.2 磨床开料Z、宽方向的正四面体并精磨到图纸要求尺寸;5.3.3 铣床开粗T形台阶,A、B尺寸留余量0.15mm-0.25mm;5.3.4 磨床精磨T形台阶B尺寸,尺寸公差为±0.01mm;5.3.5 磨床精磨A尺寸,尺寸公差为±0.02mm;5.3.6 送慢走丝加工长方向的尺寸及导向槽,导向槽尺寸公差要求+0.015mm至+0.01mm;5.3.7 送品检检测;5.4 运输板:5.4.1工艺路线:铣床组→磨床组→锯床→铣床组→磨床组→品检;5.4.2 铣床开粗长宽方向的正四面体,长宽尺寸留余量0.4mm-0.5mm;5.4.3 磨床加工长宽尺寸至要求尺寸,公差为±0.5mm;5.4.4 送锯床加工Z方向的厚度,留余量1mm-1.5mm;5.4.5 铣床加工Z方向的厚度,留余量0.3mm-0.4mm;5.4.6 铣床加工螺丝扩孔和螺丝槽公差标准为-0.3mm至+0.1mm;5.4.7 铣床倒C角;5.4.8 送磨床精磨至图纸尺寸公差标准为±0.5mm;5.4.9 送品检检测;5.5 压线板:5.5.1工艺路线:铣床组→磨床组→锯床→铣床组→磨床组→品管5.5.2 铣床开粗长宽方向的正四面体,长宽尺寸留余量0.4mm-0.5mm;5.5.3 磨床加工长宽尺寸至要求尺寸,公差为±0.5mm;5.5.4 送锯床加工Z方向的厚度,留余量1mm-1.5mm;5.5.5 铣床加工Z方向的厚度,留余量0.3mm-0.4mm;5.5.6 铣床加工平头螺丝扩孔和平头螺丝杯头;5.5.7 铣床倒C角;5.5.8 送磨床精磨至图纸尺寸公差标准为±0.5mm;5.5.9 送品检检测;5.6 摆杆:5.6.1工艺路线:铣床组→磨床组→锯床→铣床组→磨床组→铣床组→品检5.6.2 铣床加工长宽方向的正四面体,留余量0.4mm-0.5mm;5.6.3 磨床加工至图纸尺寸,公差为长宽方向+0.03mm至+0.05mm;5.6.4 锯床锯Z方向的厚度,留余量1mm-1.5mm,;5.6.5 铣床加工Z方向的厚度,留余量0.3mm,并加工A尺寸,留余量0.2mm;5.6.6 磨床精磨Z方向和A尺寸的厚度至图纸尺寸,公差±0.1mm;5.6.7 铣床加工螺丝扩孔和螺丝杯头孔;5.6.8 铣床用分度转盘加工图示R位置;5.6.9 铣床将各部位倒角;5.6.10送品检检测;5.7 击杆导正块:5.7.1工艺路线:铣床组→磨床组→锯床→铣床组→磨床组→铣床组→品检5.7.2 铣床开粗长宽方向的正四面体,留余量0.3mm-0.5mm;5.7.3 磨床加工长宽方向的尺寸至图纸尺寸,公差为+0.00mm至+0.03mm;5.7.4 锯床加工Z方向的厚度,留余量1mm至1.5mm;5.7.5 铣床加工Z方向尺寸及A、B尺寸,留余量0.3mm;5.7.6 铣床钻螺丝扩孔及螺丝杯头孔后加工斜面至图纸要求尺寸;5.7.7 磨床加工Z方向尺寸及A尺寸,公差为±0.2mm,磨床精磨B尺寸,公差为±0.02mm;5.7.8 铣床倒角;5.7.9 送品检检测;5.8 急回击杆;5.8.1工艺路线;铣床组→磨床组→品检5.8.2 铣床领精料;5.8.3 铣床组钻螺丝扩孔及销钉孔并倒角;5.8.4 铣床加工斜面至图纸尺寸,公差±0.2mm;5.8.5 铣床倒角后送磨床;5.8.6 磨床精磨宽尺寸,公差为±0.02mm;5.8.7 送品检检测;5.9 行位座5.9.1工艺路线:铣床组→磨床组→锯床→铣床组→磨床组→铣床组→磨床组→品检5.9.2 铣床领精料并加工T槽各部位尺寸,留余量0.3mm;5.9.3 磨床精磨T槽各位尺寸,公差见公差标准;5.9.4 锯床切断长方向的尺寸,留余量1mm-1.5mm;5.9.5 铣床加工长度尺寸,留余量0.3mm-0.5mm;5.9.6 磨床精磨长度尺寸,公差±0.1mm;5.9.7 送铣床加工斜面、斜孔及镶件挂台槽,斜面留余量0.5mm-0.6mm,斜孔公差为+0.2mm至0.5mm,镶件挂台槽留余量0.2mm-0.3mm;5.9.8 磨床精磨斜面,留余量0.3mm,精磨镶件挂台槽,公差见公差标准;5.9.9 送品检检测;5.10 铲基:5.10.1工艺路线:铣床组→磨床组→锯床→铣床组→磨床组→铣床组→磨床组→品检5.10.2 铣床领精料;5.10.3 铣床加工A及螺丝孔,A尺寸留余量0.3mm-0.5mm;5.10.4 送磨床精磨A尺寸,公差为+0mm至+0.02mm;5.10.5 锯床切断长度方向尺寸,留余量1mm-1.5mm;5.10.6 铣床加工长度方向尺寸,留余量0.2mm-0.4mm;5.10.7 磨床精磨长度尺寸,公差为-0.1mm至-0.3mm;5.10.8 铣床粗加工斜面,留余量0.3mm;5.10.9 磨床精磨斜面,留余量0.15mm钳工Fit模;5.10.10 送品检检测;6、相关文件:6.1 标准图纸;7、相关表格:7.1 «零件加工控制表»;7.2 «零件\铜公交接表»。
模具零件加工工艺流程图(底盖)
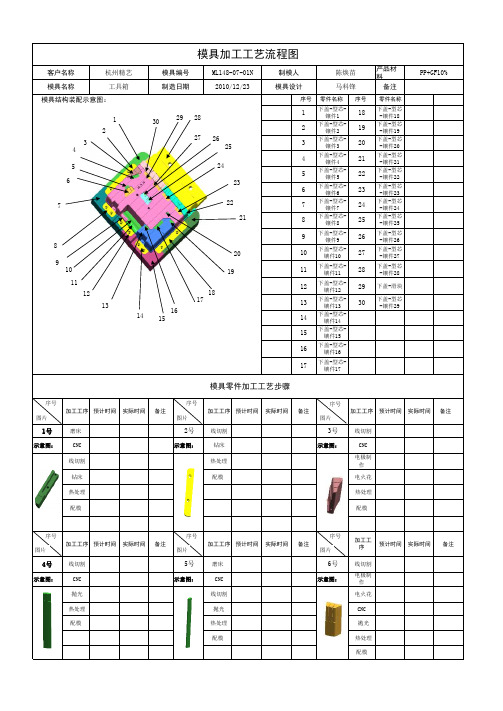
产品材料备注序号 零件名称序号零件名称1下盖-型芯-镶件118下盖-型芯-镶件182下盖-型芯-镶件219下盖-型芯-镶件193下盖-型芯-镶件320下盖-型芯-镶件204下盖-型芯-镶件421下盖-型芯-镶件215下盖-型芯-镶件522下盖-型芯-镶件226下盖-型芯-镶件623下盖-型芯-镶件237下盖-型芯-镶件724下盖-型芯-镶件248下盖-型芯-镶件825下盖-型芯-镶件259下盖-型芯-镶件926下盖-型芯-镶件2610下盖-型芯-镶件1027下盖-型芯-镶件2711下盖-型芯-镶件1128下盖-型芯-镶件2812下盖-型芯-镶件1229下盖-滑块13下盖-型芯-镶件1330下盖-型芯-镶件2914下盖-型芯-镶件1415下盖-型芯-镶件1516下盖-型芯-镶件1617下盖-型芯-镶件17加工工序 预计时间 实际时间备注加工工序 预计时间 实际时间备注加工工序 预计时间 实际时间 备注1号磨床 2号线切割 3号线切割示意图:CNC 示意图:钻床示意图:CNC 线切割 热处理 电极制作 钻床配模电火花 热处理 热处理配模配模加工工序 预计时间 实际时间备注加工工序 预计时间 实际时间备注加工工序 预计时间 实际时间备注4号线切割 5号磨床 6号线切割示意图:CNC 示意图:CNC 示意图:电极制作 抛光 线切割 电火花 热处理 抛光CNC配模热处理 抛光配模热处理配模制模人模具设计模具零件加工工艺步骤模具结构装配示意图:陈焕苗马科锋杭州精艺模具加工工艺流程图PP+GF10%ML148-07-01N 2010/12/23客户名称模具名称模具编号工具箱制造日期234578910111213141719202425262723222118166图片序号图片序号图片序号图片序号图片序号图片序号129302815。
模具加工规范

安徽福臻技研有限公司
安徽福臻技研有限公司
)、后序模具
下模CH孔制作同销孔加工标准,上模(或压料芯)为CH 头选用比CH冲头直径稍大一些,深度15-20mm
30°附件铣头90°附件铣头
G154
G158
G157
G155
G156
例:
M53 C0. ; (应用5面加工时先要将C轴旋转到对应的位置)
G155 A32. I_ J_ K_ H_ U_ V_ W_ ;
.
.
G160; (5面加工取消)
I 5面加工旋转定位后的加工G54相对于垂直G54中X的偏置量
J 5面加工旋转定位后的加工G54相对于垂直G54中Y的偏置量
K 5面加工旋转定位后的加工G54相对于垂直G54中Z的偏置量
H 刀具长度补偿号
U 滑枕伸出上限
W 横梁距工作台面的高度
同理可有G154 G156 G157 G158
在5面加工中,Z,W轴合成为一轴,如Z轴行程不够,W轴自动补偿,这也是G54和G154 5面加工也就是加工坐标原点的旋转与重置,判定方向时可沿图示箭头指向右为X+, 前为C轴旋转逆时针方向为正,刀具轴指向X—时为C0°
安徽福臻技研有限公司。
- 1、下载文档前请自行甄别文档内容的完整性,平台不提供额外的编辑、内容补充、找答案等附加服务。
- 2、"仅部分预览"的文档,不可在线预览部分如存在完整性等问题,可反馈申请退款(可完整预览的文档不适用该条件!)。
- 3、如文档侵犯您的权益,请联系客服反馈,我们会尽快为您处理(人工客服工作时间:9:00-18:30)。
毕业设计(论文)论文(设计)题目冷冲压模具设计专业名称模具设计与制造班级名称学生姓名指导教师完成时间施加压力,使其产生分离或塑冲压所使用的模具称为冲压模具,简称冲模。
冲模是将材料(金属或非金属)批量加工成所需冲件的专用工具。
冲模在冲压中至关重要,没有符合要求的冲模,批量冲压生产与自动化。
(2)冲压时由于模具保证了冲压件的尺寸与形状精度,且一般不破坏冲压件的表面质量,而模具的寿命一般较长,因此冲压的质量稳定,互换性好,具有“一模一样”的特征。
(3)冲压可加工出尺寸范围较大、形状较复杂的零件,如小到钟表的秒表,大到汽车纵梁、覆盖件等,加上冲压时材料的冷变形硬化效应,冲压的强度和刚度均较高。
(4)冲压一般没有切屑碎料生成,材料的消耗较少,且不需其它加热设备,因而是一种省料,节能的加工方法,冲压件的成本较低。
由于冲压加工的零件种类繁多,各类零件的形状、尺寸和精度要求又各不相同,因而生产中采纳的冲压工艺方法也是多种多样的。
概括起来,可分为分离工序和成形工序两大类;分离工序是指使坯料沿一定的轮廓线分离而获得一定形状、尺寸和断面质量的冲压(俗称冲裁件)的工序;成形工序是指使坯料在不破裂的条件下产生塑性变形而获得一定形状和尺寸的冲压件的工序。
上述两类工序,按差不多变形方式不同又可分为冲裁、弯曲、拉深和成形四种差不多工序,每种差不多工序还包含有多种单一工序。
在实际生产中,当冲压件的生产批量较大、尺寸较少而公差要求较小时,若用分散的单一工序来冲压是不经济甚至难于达到要求。
这时在工艺上多采纳集中的方案,即把两种或两种以上的单一工序集中在一副模具内完成,称为组合的方法不同,又可将其分为复合-级进和复合-级进三种组合方式。
复合冲压——在压力机的一次工作行程中,在模具的同一工位上同时完成两种或两种以上不同单一工序的一种组合方法式。
级进冲压——在压力机上的一次工作行程中,按照一定的顺序在同一模具的不同工位上完成两种或两种以上不同单一工序的一种组合方式。
复合-级进——在一副冲模上包含复合和级进两种方式的组合工序。
冲模的结构类型也专门多。
通常按工序性质可分为冲裁模、弯曲模、拉深模和成形模等;按工序的组合方式可分为单工序模、复合模和级进模等。
但不论何种类型的冲模,都可看成是由上模和下模两部分组成,上模被固定在压力机工作台或垫板上,是冲模的固定部分。
工作时,坯料在下模面上通过定位零件定位,压力机滑块带动上模下压,在模具工作零件(即凸模、凹模)的作用下坯料便产生分离或塑性变形,从而获得所需形状与尺寸的冲件。
上模回升时,模具的卸料与出件装置将冲件或废料从凸、凹模上卸下或推、顶出来,以便进行下一次冲压循环。
此设计针对所给的零件进行了一套冷冲压模具的设计,其中设计内容为分析零件的冲裁工艺性(材料、工件结构形状、尺寸精度),拟定零件的冲压工艺方案及模具结构,排样,裁板,计算冲压工序压力,选用压力机及确定压力中心,计算凸凹模刃口尺寸,要紧零、部件的结构设计和加工工艺编制,压力机的校核。
冲裁模设计题目如图1所示零件:垫扳生产批量:大批量材料:08F t=2mm设计该零件的冲压工艺与模具2 零件的工艺分析2.1 结构与尺寸该零件结构简单,形状对称。
硬钢材料被自由凸模冲圆形孔,查《冷冲压工艺及模具设计》表3-8,可知该工件冲孔的最小尺寸为1.3t,该工件的孔径为:Φ6>1.3t=1.3×2=2.6。
由于该冲裁件的冲孔边缘与工件的外形的边缘不平行,故最小孔边距不应小于材料厚度t,该工件的空边距(20)>t=2,(10)>t=2,均适宜于冲裁加工。
2.2 精度零件内、外形尺寸均未标注公差,属自由尺寸,可按IT14级确定工件尺寸的公差,经查表得,各尺寸公差分不为:, 38062.0-, 30052.0-, 16043.0-, 零件外形:58074-.08036.0-零件内形:630.00+孔心距:18±0.215,利用一般冲裁方式能够达到零件图样要求。
2.3 材料08F,属于碳素结构钢,查《冷冲压工艺及模具设计》附表1可知抗剪强度τ=260MPa,断后伸长率=32%。
此材料具有良好的塑性和较高的弹性,其冲裁加工性能好。
依照以上分析,该零件的工艺性较好,能够进行冲裁加工。
3 确定冲裁工艺方案该零件包括落料、冲孔两个差不多工序,能够采纳以下几种工艺方案:(a)先落料,再冲孔,采纳单工序模生产;(b)采纳落料——冲孔复合冲压,采纳复合模生产;(c)用冲孔——落料连续冲压,采纳级进模生产。
方案(a)模具结构简单,但需要两道工序,两套模具才能完成零件的加工,生产效率低,难以满足零件大批量生产的要求。
由于零件结构简单,为了提高生产效率,要紧采纳复合冲裁或级进冲裁方式。
采纳复合冲裁时,冲出的零件精度和平直度好,生产效率高,操作方便,通过设计合理的模具结构和排样方案能够达到较好的零件质量。
依照以上分析,该零件采纳复合冲裁工艺方案。
4 确定模具总体结构方案4.1 模具类型依照零件的冲裁工艺方案,采纳复合冲裁模。
复合模的要紧结构特点是存在有双重作用的结构零件——凸凹模,凸凹模装在下模称为倒装式复合模。
采纳倒装式复合模省去了顶出装置,结构简单,便于操作,因此采纳倒装式复合冲裁模。
4.2 操作与定位方式尽管零件的生产批量较大,但合理安排生产,可用手工送料方式能够达到批量要求,且能降低模具成本,因此采纳手工送料方式。
考虑到零件尺寸大小,材料厚度,为了便于操作和保证零件的精度,宜采纳导料板导向,固定挡料销挡料,并与导正销配合使用以保证送料位置的准确性,进而保证零件精度。
为了保证首件冲裁的正确定距,采纳始用挡料销,采纳使用挡料销的目的是为了提高材料利用率。
4.3 卸料与出件方式采纳弹性卸料的方式卸料,弹性卸料装配依靠橡皮的弹力来卸料,卸料力不大,但冲压时可兼起压料作用,能够保证冲裁件表面的平面度。
为了方便操作,提高零件生产率,冲件和废料采纳由凸模直接从凹模洞口推下的下出件方式。
4.4 模架类型及精度考虑到送料与操作的方便性,模架采纳后侧式导柱的模架,用导柱导套导向。
由于零件精度要求不是专门高,但冲裁间隙较小,因此采纳I级模架精度。
4.5 凸模设计凸模的结构形式与固定方法:落料凸模刃口部分为非圆形,为便于凸模与固定板的加工,可设计成固定台阶式,中间台阶和凸模固定板以H7/m6过渡配合,凸模顶端的最大台阶是用其台肩挡住凸模,在卸料时不至于凸模固定板中拉出。
并将安装部分设计成便于加工的长圆形,通过接方式与凸模固定板固定。
5 工艺设计计算5.1 排样设计与计算零件外形近似矩形,轮廓尺寸为58×30。
考虑操作方便并为了保证零件精度,采纳直排有废料排样。
如图1所示:查《冷冲压工艺及模具设计》表3-13,工件的搭边值a=2,沿边的搭边值a1=2.2。
级进模送料步距为S=30+2=32mm条料宽度按表3-14中公式计算:B -0△=(D max+2a1)-△0查表3-15得:△=0.6B=(58+2×2.2)06.0-=62.406.0-(㎜)由零件图近似算得一个零件的面积为1354.8㎜2,一个进距内的坏料面积B×S=62.4×32=1996.8㎜2。
因此一个进距内的材料利用率为:η=(A/BS)×100﹪=67.8﹪查《冷冲压工艺及模具设计》附表3选用板料规格为710×2000×2。
采纳横裁时,剪切条料尺寸为62.4。
一块板可裁的条料为32,每间条可冲零件个数22个零件。
则一块板材的材料利用率为:η=(n×A0/A)×100﹪η=(22×32×1354.8/710×2000)×100﹪=67.2﹪采纳纵裁时,剪切条料尺寸为62.4。
一块板可裁的条料为11,每条可冲零件个数62个零件,则一块板材的材料利用率为:η=(n×A0/A)×100﹪η=(11×62×1354.8/710×2000)×100﹪=59.2﹪依照以上分析,横裁时比纵裁时的板材的材料利用率高,因此采纳横裁。
5.2 计算冲压力与压力中心,初选压力机冲裁力:依照零件图可算得一个零件外周边长度:L1=16π+8+28+38×2=162.27 内周边长度之和:L=2π×3=18.84㎜查《冷冲压工艺及模具设计》附表1可知:260τMP a;=查《冷冲压工艺及模具设计》附表3可知:K x=0.05, K T=0.055.落料力:F落=KL1 t T=1.3×162.27×2×260=109.69KN冲孔力:F孔=KL2 t T=1.3×6 ×2×260=12.74KN卸料力:Fx=KxF落=0.05×109.69=5.48KN推件力:依照材料厚度取凹模刃口直壁高度h=6,故:n=h/t=3F T=nKtF孔=3×0.055×25.47=4.20KN总冲压力:FЁ= F落+ F孔+Fx+ F T则FЁ=109.69+12.74+5.48+4.20=132.11KN应选取的压力机公称压力:25t.因此可初选压力机型号为J23-25。
当模具结构及尺寸确定之后,可对压力机的闭合高度,模具安装尺寸进行校核,从而最终确定压力机的规格。
确定压力中心:画出凹模刃口,建立如图所示的坐标系:由图可知,该形状关于X轴上下对称,关于Y轴左右对称,则压力中心为该图形的几何中心。
即坐标原点O。
该点坐标为(0,0)。
5.3 计算凸、凹模刃口尺寸及公差由于模具间隙较小,固凸、凹模采纳配作加工为宜,由于凸、凹模之间存在着间隙,使落下的料或冲出的孔都带有锥度。
落料件的尺寸接近于凹模刃口尺寸,而冲孔件的尺寸接近于凸模刃口尺寸。
固计算凸模与凹模刃口尺寸时,应按落料与冲孔两种情况分不进行。
由此,在确定模具刃口尺寸及其制造公差时,需遵循以下原则:(I )落料时以凹模尺寸为基准,即先确定凹模刃口尺寸;考虑到凹模刃口尺寸在使用过程中因磨损而增大,固落料件的差不多尺寸应取工件尺寸公差范围较小尺寸,而落料凸模的差不多尺寸则按凹模差不多尺寸减最小初始间隙;(II )冲孔时以凸模尺寸为基准,即先确定凸模刃口尺寸,考虑到凸模尺寸在使用过程中因磨损而减小,固冲孔件的差不多尺寸应取工件尺寸公差范围内的较大尺寸,而冲孔凹模的差不多尺寸则按凸模差不多尺寸加最小初始间隙;(III )凸模与凹模的制造公差,依照工件的要求而定,一般取比工件精度高2~3级的精度,考虑到凹模比凸模的加工稍难,凹模比凸模低一级。
a): 落料凹模刃口尺寸。