(新)塑胶产品知识-产品设计_
塑胶常识

1.胶厚(胶位):塑胶产品的胶厚(整体外壳)通常在0.80-3.00左右,太厚容易缩水和产生汽泡,太薄难走满胶,大型的产品胶厚取厚一点,小的产品取薄一点,一般产品取1.0-2.0为多。
而且胶位要尽可能的均匀,在不得已的情况下,局部地方可适当的厚一点或薄一点,但需渐变不可突变,要以不缩水和能走满胶为原则,一般塑料胶厚小于0.3时就很难走胶,但软胶类和橡胶在0.2-0.3的胶厚时也能走满胶。
2.加强筋(骨位):塑胶产品大部分都有加强筋,因加强筋在不增加产品整体胶厚的情况下可以大大增加其整体强度,对大型和受力的产品尤其有用,同时还能防止产品变形。
加强筋的厚度通常取整体胶厚的0.5-0.7倍,如大于0.7倍则容易缩水。
加强筋的高度较大时则要做0.5-1的斜度(因其出模阻力大),高度较矮时可不做斜度。
3.脱模斜度:塑料产品都要做脱模斜度,但高度较浅的(如一块平板)和有特殊要求的除外(但当侧壁较大而又没出模斜度时需做行位)。
出模斜度通常为1-5度,常取2度左右,具体要根据产品大小、高度、形状而定,以能顺利脱模和不影响使用功能为原则。
产品的前模斜度通常要比后模的斜度大0.5度为宜,以便产品开模事时能留在后模。
通常枕位、插穿、碰穿等地方均需做斜度,其上下断差(即大端尺寸与小端尺寸之差)单边要大于0.1以上。
4.圆角(R角):塑胶产品除特殊要求指定要锐边的地方外,在棱边处通常都要做圆角,以便减小应力集中、利于塑胶的流动和容易脱模。
最小R通常大于0.3,因太小的R模具上很难做到。
5.孔:从利于模具加工方面的角度考虑,孔最好做成形状规则简单的圆孔,尽可能不要做成复杂的异型孔,孔径不宜太小,孔深与孔径比不宜太大,因细而长的模具型心容易断、变形。
孔与产品外边缘的距离最好要大于1.5倍孔径,孔与孔之间的距离最好要大于2倍的孔径,以便产品有必要的强度。
与模具开模方向平行的孔在模具上通常上是用型心(可镶、可延伸留)或碰穿、插穿成型,与模具开模方向不平行的孔通常要做行位或斜顶,在不影响产品使用和装配的前提下,产品侧壁的孔在可能的情况下也应尽量做成能用碰穿、插穿成型的孔。
塑胶模具设计的基本知识

塑胶模具设计的基本知识塑胶模具设计的基本知识近年来,随着塑料工业的飞速发展和通用工程塑料在强度和精度等方面的不断提高,塑料制品的应用范围也在不断扩大,如:家用电器、仪器仪表、建筑器材、汽车工业、日用五金等众多领域,塑料制品所占的比例正迅猛增加。
一个设计合理的塑料件往往能够代替多个传统的金属件。
工业产品和日用产品塑料化的趋势不断上升。
让我们来了解一下,有关模具设计的一些基本常识吧!1.模具基本知识模具分铸造模、锻造模、压铸模、冲压模等非塑胶模具,以及塑胶模具。
2.模具的一般定义在工业生产中,用各种压力机和装在压力机上的'专用工具,通过压力把金属或非金属材料制出所需形状的零件或制品,这种专用工具统称为模具。
3.注塑过程说明注塑模具是一种生产塑料制品的工具。
它由几组零件部分构成,这个组合内有成型模腔。
注塑时,模具装夹在注塑机上,熔融塑料被注入成型模腔内,并在型腔内冷却定型,然后动定模分开,经由顶出系统将制品从模腔顶出离开模具,最后模具再闭合进行下一次注塑,整个注塑过程是循环进行的。
4.模具的一般分类可分为塑胶模具及非塑胶模具。
(1)非塑胶模具有:铸造模、锻造模、冲压模、压铸模等。
A.铸造模--水龙头、生铁平台;B.锻造模--汽车身;C.冲压模--计算机面板;D.压铸模--超合金、汽缸体;(2)塑胶模具根据生产工艺和生产产品的不同又分为:A.注射成型模--电视机外壳、键盘按钮(应用最普遍);B.吹气模--饮料瓶;C.压缩成型模--电木开关、科学瓷碗碟;D.转移成型模--集成电路制品;E.挤压成型模--胶水管、塑胶袋;F.热成型模--透明成型包装外壳;G.旋转成型模--软胶洋娃娃玩具。
(3)注塑模具是由若干块钢板配合各种零件组成的,基本分为:A.成型装置(凹模、凸模);B.定位装置(导柱、导套);C.固定装置(工字板、码模坑);D.冷却系统(运水孔);E.恒温系统(加热管、发热线);F.流道系统(唧咀孔、流道槽、流道孔);G.顶出系统(顶针、顶杆等)。
塑胶产品结构设计基本规则

塑胶产品结构设计基本规则设计基本规则壁厚的大小取决于产品需要承受的外力、是否作为其它零件的支撑、承接柱位的数量、伸出部份的多少以及选用的塑胶材料而定。
一般的热塑性塑料壁厚设计应以4mm为限。
从经济角度来看,过厚的产品不但增加物料成本,延长生产周期”冷却时间〔,增加生产成本。
从产品设计角度来看,过厚的产品增加引致产生空穴”气孔〔的可能性,大大削弱产品的刚性及强度。
最理想的壁厚分布无疑是切面在任何一个地方都是均一的厚度,但为满足功能上的需求以致壁厚有所改变总是无可避免的。
在此情形,由厚胶料的地方过渡到薄胶料的地方应尽可能顺滑。
太突然的壁厚过渡转变会导致因冷却速度不同和产生乱流而造成尺寸不稳定和表面问题。
对一般热塑性塑料来说,当收缩率”Shrinkage Factor〔低于0.01mm/mm时,产品可容许厚度的改变达;但当收缩率高于0.01mm/mm时,产品壁厚的改变则不应超过。
对一般热固性塑料来说,太薄的产品厚度往往引致操作时产品过热,形成废件。
此外,纤维填充的热固性塑料于过薄的位置往往形成不够填充物的情况发生。
不过,一些容易流动的热固性塑料如环氧树脂”Epoxies〔等,如厚薄均匀,最低的厚度可达0.25mm。
此外,采用固化成型的生产方法时,流道、浇口和部件的设计应使塑料由厚胶料的地方流向薄胶料的地方。
这样使模腔内有适当的压力以减少在厚胶料的地方出现缩水及避免模腔不能完全充填的现象。
若塑料的流动方向是从薄胶料的地方流向厚胶料的地方,则应采用结构性发泡的生产方法来减低模腔压力。
平面准则在大部份热融过程操作,包括挤压和固化成型,均一的壁厚是非常的重要的。
厚胶的地方比旁边薄胶的地方冷却得比较慢,并且在相接的地方表面在浇口凝固后出现收缩痕。
更甚者引致产生缩水印、热内应力、挠曲部份歪曲、颜色不同或不同透明度。
若厚胶的地方渐变成薄胶的是无可避免的话,应尽量设计成渐次的改变,并且在不超过壁厚3:1的比例下。
下图可供叁考。
塑胶产品结构设计准则--壁厚篇
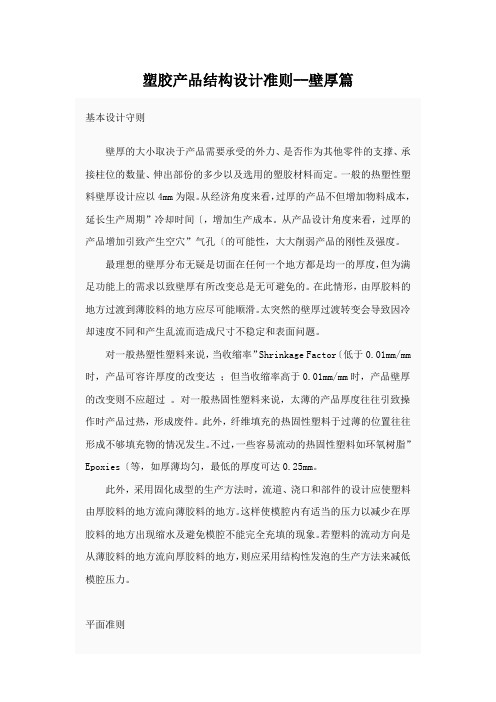
塑胶产品结构设计准则--壁厚篇基本设计守则壁厚的大小取决于产品需要承受的外力、是否作为其他零件的支撑、承接柱位的数量、伸出部份的多少以及选用的塑胶材料而定。
一般的热塑性塑料壁厚设计应以4mm为限。
从经济角度来看,过厚的产品不但增加物料成本,延长生产周期”冷却时间〔,增加生产成本。
从产品设计角度来看,过厚的产品增加引致产生空穴”气孔〔的可能性,大大削弱产品的刚性及强度。
最理想的壁厚分布无疑是切面在任何一个地方都是均一的厚度,但为满足功能上的需求以致壁厚有所改变总是无可避免的。
在此情形,由厚胶料的地方过渡到薄胶料的地方应尽可能顺滑。
太突然的壁厚过渡转变会导致因冷却速度不同和产生乱流而造成尺寸不稳定和表面问题。
对一般热塑性塑料来说,当收缩率”Shrinkage Factor〔低于0.01mm/mm 时,产品可容许厚度的改变达;但当收缩率高于0.01mm/mm时,产品壁厚的改变则不应超过。
对一般热固性塑料来说,太薄的产品厚度往往引致操作时产品过热,形成废件。
此外,纤维填充的热固性塑料于过薄的位置往往形成不够填充物的情况发生。
不过,一些容易流动的热固性塑料如环氧树脂”Epoxies〔等,如厚薄均匀,最低的厚度可达0.25mm。
此外,采用固化成型的生产方法时,流道、浇口和部件的设计应使塑料由厚胶料的地方流向薄胶料的地方。
这样使模腔内有适当的压力以减少在厚胶料的地方出现缩水及避免模腔不能完全充填的现象。
若塑料的流动方向是从薄胶料的地方流向厚胶料的地方,则应采用结构性发泡的生产方法来减低模腔压力。
平面准则在大部份热融过程操作,包括挤压和固化成型,均一的壁厚是非常的重要的。
厚胶的地方比旁边薄胶的地方冷却得比较慢,并且在相接的地方表面在浇口凝固后出现收缩痕。
更甚者引致产生缩水印、热内应力、挠曲部份歪曲、颜色不同或不同透明度。
若厚胶的地方渐变成薄胶的是无可避免的话,应尽量设计成渐次的改变,并且在不超过壁厚3:1的比例下。
塑胶产品结构设计常识

塑胶产品结构设计常识塑胶产品结构设计⼩常识⽬录:第⼀章塑胶结构设计规范1、材料及厚度1.1、材料选择1.2、壳体厚度1.3、零件厚度设计实例2、脱模斜度2.1、脱模斜度要点3、加强筋3.1、加强筋与壁厚的关系3.2、加强筋设计实例4、柱和孔的问题4.1、柱⼦的问题4.2、孔的问题4.3、“减胶”的问题5、螺丝柱的设计6、⽌⼝的设计6.1、⽌⼝的作⽤6.2、壳体⽌⼝的设计需要注意的事项6.3、⾯壳与底壳断差的要求7、卡扣的设计7.1、卡扣设计的关键点7.2、常见卡扣设计8、装饰件的设计8.1、装饰件的设计注意事项8.2、电镀件装饰斜边⾓度的选取8.3、电镀塑胶件的设计9、按键的设计9.1 按键(Button)⼤⼩及相对距离要求10、旋钮的设计10.1 旋钮(Knob)⼤⼩尺⼨要求10.2 两旋钮(Knob)之间的距离10.3 旋钮(Knob)与对应装配件的设计间隙11、胶塞的设计12、镜⽚的设计12.1 镜⽚(LENS)的通⽤材料12.2 镜⽚(LENS)与⾯壳的设计间隙13、触摸屏与塑胶⾯壳配合位置的设计13.1、触摸屏相对应位置塑胶⾯壳的设计注意事项第⼀章塑胶结构设计规范1、材料及厚度1.1、材料的选取a. ABS:⾼流动性,便宜,适⽤于对强度要求不太⾼的部件(不直接受冲击,不承受可靠性测试中结构耐久性的部件),如内部⽀撑架(键板⽀架、LCD⽀架)等。
还有就是普遍⽤在电镀的部件上(如按钮、侧键、导航键、电镀装饰件等)。
⽬前常⽤奇美PA-757、PA-777D等。
b. PC+ABS:流动性好,强度不错,价格适中。
适⽤于作⾼刚性、⾼冲击韧性的制件,如框架、壳体等。
常⽤材料代号:拜尔T85、T65。
c. PC:⾼强度,价格贵,流动性不好。
适⽤于对强度要求较⾼的外壳、按键、传动机架、镜⽚等。
常⽤材料代号如:帝⼈L1250Y、PC2405、PC2605。
d. POM具有⾼的刚度和硬度、极佳的耐疲劳性和耐磨性、较⼩的蠕变性和吸⽔性、较好的尺⼨稳定性和化学稳定性、良好的绝缘性等。
塑胶产品结构设计重点

塑胶产品结构设计重点一、材料选择塑胶产品的结构设计首先要考虑材料选择。
材料的选择直接关系到产品的性能、质量和成本,因此需要根据产品的具体要求和使用环境,选择适合的塑胶材料。
常见的塑胶材料有聚乙烯(PE)、聚丙烯(PP)、聚氯乙烯(PVC)、聚苯乙烯(PS)、聚酯(PET)等。
在选择材料时需要考虑产品的机械性能、耐热性、耐化学性、耐候性、电气性能、透明度等因素。
同时还需要考虑材料的加工性能,如流动性、热稳定性、收缩率等。
材料的选择不合理会导致产品性能不达标或加工工艺困难,因此需要在产品设计之前进行充分的材料筛选和试验。
二、结构设计塑胶产品结构设计主要包括外形设计和内部结构设计。
外形设计需要考虑产品的功能、美观和人机工程学等因素。
合理的外形设计可以提升产品的市场竞争力和用户体验。
内部结构设计需要考虑产品的强度、稳定性和装配性等因素。
合理的内部结构设计可以提高产品的性能和质量,减少生产和使用过程中的故障和损坏。
此外还需要考虑产品的可制造性和生产效率。
在进行结构设计时,需要采用CAD软件进行三维建模和仿真分析,以验证设计的可行性和优化设计。
三、模具设计塑胶产品的生产需要模具进行注塑成型。
模具设计是塑胶产品结构设计中非常重要的一部分,直接影响产品的质量和生产效率。
模具设计需要考虑产品的尺寸、形状和结构特点,选择合适的注塑工艺,确定模具的结构和加工工艺。
模具的设计要求高精度、高效率、长寿命和低成本,需要充分考虑模具的结构强度、冷却系统、顶出系统、塑胶流道等因素。
合理的模具设计可以提高产品的精度和表面质量,降低生产成本和生产周期。
四、加工工艺塑胶产品的加工工艺是塑胶产品结构设计的最后一步,直接影响产品的成型质量和效率。
常见的塑胶加工工艺有注塑成型、吹塑成型、挤出成型、压缩成型等。
在选择和优化加工工艺时,需要考虑产品的形状、尺寸、材料特性和生产要求等因素。
合理的加工工艺可以提高产品的质量和生产效率,降低生产成本和能耗。
塑胶产品柱子和孔的设计
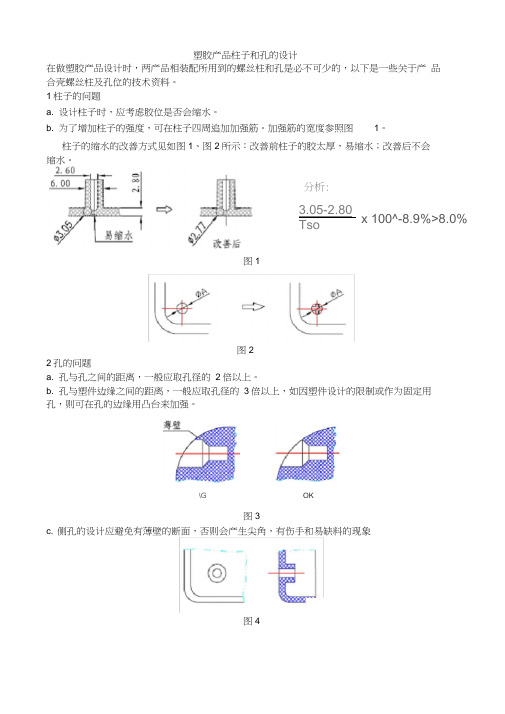
塑胶产品柱子和孔的设计在做塑胶产品设计时,两产品相装配所用到的螺丝柱和孔是必不可少的,以下是一些关于产 品合壳螺丝柱及孔位的技术资料。
1柱子的问题a. 设计柱子时,应考虑胶位是否会缩水。
b. 为了增加柱子的强度,可在柱子四周追加加强筋。
加强筋的宽度参照图1。
柱子的缩水的改善方式见如图1、图2所示:改善前柱子的胶太厚,易缩水;改善后不会 缩水。
图22孔的问题a. 孔与孔之间的距离,一般应取孔径的 2倍以上。
b. 孔与塑件边缘之间的距离,一般应取孔径的 3倍以上,如因塑件设计的限制或作为固定用孔,则可在孔的边缘用凸台来加强。
图3c. 侧孔的设计应避免有薄壁的断面,否则会产生尖角,有伤手和易缺料的现象分析:3.05-2.80x 100^-8.9%>8.0%图1\GOK图43减胶”的问题图52、螺丝柱的设计2.1通常采取螺丝加卡扣的方式来固定两个壳体,螺丝柱通常还起着对PCB板的定位作用。
2.2用于自攻螺丝的螺丝柱的设计原则是为:其外径应该是Screw外径的2.0~2.4倍。
设计中可以取:螺丝柱外径=2X螺丝外径;螺柱内径(ABS , ABS+PC)=螺丝外径-0.40mm;螺柱内径(PC)=螺丝外径-0.30mm或-0.35mm (可以先按0.30mm来设计,待测试通不过再修模加胶);两壳体螺柱面之间距离取0.05mm。
曾進牙螺丝|| 02,0 02.3 02.6 如8 03.0 03 .5 ]工程塑料公差孔径孔径孔径公羞孔爸孔径ABS 1.70 1.90 ■+0JD5€2.20 +0-0.05 Z40 *0 -0.05 2.50+0.05 2.90 *0.05 -0.05PC170 2.00 2.30 +0Z40 -0 2.60+04),053.QQ *0.05POM 1.60+Q.05 -G 1,80 40.05CJ2,10 +0.05 -2.30 *0 2.40+C.Q5£2.80 +0.10 -0PA 1,60 ♦0.05-0 1.80 ^0.05-C2J0 +0.Q5 -C 230+04)32-40 +C.Q5 -C 2.80♦0J0-0PP 2-00 +0.10 -0 Z20-0,052.30 +C.10 -2.70♦0.10 -0PC+ABS 1.70 +0+05 2.00 -0_05 Z30 +0 -0.05 2-40 +0,05 -2駁-0.05 3,00 +0.05-0.052.312螺丝规榕快牙螺丝02.0 02.3 02.6 0Z8 03-0 03.5工荐塑料孔耗公君孔径公差孔径孔径孔色孔径ABS 1.60 1.90 +0■0.052-10 +0.05■0Z3D+0-0.W2.50 +0<052.90 +0.05-0.05PC V60 +0,05 1.90 +o,os -0 2.20 +0,05 -Q 2.4 D -0,05 2.60■+043,05 3.00+0,05-0r05POM1,60 *0 1.80 +0.05 -0 2-00 +0.05-0Z20 + O.OS-0 2.40+0.052.80 +0.05 -0PA 1.60 +0005 1B0 +0.0$-02*00+0.05-02.20■02.40 乜帖-0 280 -0FF 2-C0 +Q.05 2.10 + 0,10 -0 2.30 *0,054).052,70 +0,05^0.05PC+ABS 1X0 +0.05-0 1S0 +0.05-02.20+0.05 -0 2.40十D -0,06- 2.60■+0-O L OS3,00+0.05-0r05it廣氏④晶出珊懒1=0。
塑胶产品设计常识

塑胶产品设计常识1.胶厚(胶位):塑胶产品的胶厚(整体外壳)通常在0.80-3.00左右,太厚容易缩水和产生汽泡,太薄难走满胶,大型的产品胶厚取厚一点,小的产品取薄一点,一般产品取1.0-2.0为多。
而且胶位要尽可能的均匀,在不得已的情况下,局部地方可适当的厚一点或薄一点,但需渐变不可突变,要以不缩水和能走满胶为原则,一般塑料胶厚小于0.3时就很难走胶,但软胶类和橡胶在0.2-0.3的胶厚时也能走满胶。
2.加强筋(骨位):塑胶产品大部分都有加强筋,因加强筋在不增加产品整体胶厚的情况下可以大大增加其整体强度,对大型和受力的产品尤其有用,同时还能防止产品变形。
加强筋的厚度通常取整体胶厚的0.5-0.7倍,如大于0.7倍则容易缩水。
加强筋的高度较大时则要做0.5-1的斜度(因其出模阻力大),高度较矮时可不做斜度。
3.脱模斜度:塑料产品都要做脱模斜度,但高度较浅的(如一块平板)和有特殊要求的除外(但当侧壁较大而又没出模斜度时需做行位)。
出模斜度通常为1-5度,常取2度左右,具体要根据产品大小、高度、形状而定,以能顺利脱模和不影响使用功能为原则。
产品的前模斜度通常要比后模的斜度大0.5度为宜,以便产品开模事时能留在后模。
通常枕位、插穿、碰穿等地方均需做斜度,其上下断差(即大端尺寸与小端尺寸之差)单边要大于0.1以上。
4.圆角(R角):塑胶产品除特殊要求指定要锐边的地方外,在棱边处通常都要做圆角,以便减小应力集中、利于塑胶的流动和容易脱模。
最小R通常大于0.3,因太小的R模具上很难做到。
5.孔:从利于模具加工方面的角度考虑,孔最好做成形状规则简单的圆孔,尽可能不要做成复杂的异型孔,孔径不宜太小,孔深与孔径比不宜太大,因细而长的模具型心容易断、变形。
孔与产品外边缘的距离最好要大于1.5倍孔径,孔与孔之间的距离最好要大于2倍的孔径,以便产品有必要的强度。
与模具开模方向平行的孔在模具上通常上是用型心(可镶、可延伸留)或碰穿、插穿成型,与模具开模方向不平行的孔通常要做行位或斜顶,在不影响产品使用和装配的前提下,产品侧壁的孔在可能的情况下也应尽量做成能用碰穿、插穿成型的孔。
- 1、下载文档前请自行甄别文档内容的完整性,平台不提供额外的编辑、内容补充、找答案等附加服务。
- 2、"仅部分预览"的文档,不可在线预览部分如存在完整性等问题,可反馈申请退款(可完整预览的文档不适用该条件!)。
- 3、如文档侵犯您的权益,请联系客服反馈,我们会尽快为您处理(人工客服工作时间:9:00-18:30)。
塑料制品制作设计
工程塑料制品大部分是用注射成型方法加工而成的,制件的设计必须在满足使用要求和符合塑料本身的特性前提下,尽可能简化结构和模具、节省材料、便于成型。
制件设计中应分别考虑如下因素:
一、制件的形状应尽量简单、便于成型。
在保证使用要求前提下,力求简单、便于脱模,尽量避免或减少抽芯机构,如采用下图例中(b)的结构,不仅可大大简化模具结构,便于成型,且能提高生产效率。
二、制件的壁厚确定应合理。
塑料制件的壁厚取决于塑件的使用要求,太薄会造成制品的强度和刚度不足,受力后容易产生翘曲变形,成型时流动阻力大,大型复杂的制品就难以充满型腔。
反之,壁厚过大,不但浪费材料,而且加长成型周期,降低生产率,还容易产生气泡、缩孔、翘曲等疵病。
因此制件设计时确定制件壁厚应注意以下几点:
1.在满足使用要求的前提下,尽量减小壁厚;
2.制件的各部位壁厚尽量均匀,以减小内应力和变形;
3.承受紧固力部位必须保证压缩强度;
4.避免过厚部位产生缩孔和凹陷;
5.成型顶出时能承受冲击力的冲击。
国外的一些常用塑料的推荐壁厚如下表:
材料壁厚(mm)
PA、POM 0.45-3.2
PC、PSV 0.95-4.5
ABS 0.8-3.2
三、必须设置必要的脱模斜度
为确保制件成型时能顺利脱模,设计时必须在脱模方向设置脱模斜度,其大小与塑料性能、制件的收缩率和几何形状有关,对于工程塑料的结构件来说,一般应在保证顺利脱模的前提下,尽量减小脱模斜度。
下表为根据不同材料而推荐的脱模斜度:
材料脱模斜度
PA、POM、ABS 40' -10°30'
PC、PSV 50'-2°
PE、PP 30'-1°
热固性塑料20'-1°
具体确定脱模斜度时应考虑以下几点:
1.对于收缩率大的塑料制件应选用较大的脱模斜度;
2.对于大尺寸制件或尺寸精度要求高的制件应采用较小的脱模斜度;
3.制件壁厚较厚时,成型收缩增大,因此脱模斜度应取大;
4.对于增强塑料脱模斜度宜取大;
5.含自润滑剂等易脱模塑料可取小;
6.一般情况下脱模斜度不包括在制件公差范围内。
四.强度和刚度不足可考虑设计加强筋
为满足制件的使用所需的强度和刚度单用增加壁厚的办法,往往是不合理的,不仅大幅增加了制件的重量,而且易产生缩孔、凹痕等疵病,在制件设计时应考虑设置加强筋,这样能满意地解决这些问题,它能提高制件的强度、防止和避免塑料的变形和翘曲。
设置加强筋的方向应与料流方向尽量保持一致,以防止充模时料流受到搅乱,降低制件的韧性或影响制件外观质量。
五.在满足使用要求的前提下制件的所有的转角尽可能设计成圆角,或者用圆弧过渡。
圆角具有以下特点:
1、圆角可避免应力集中,提高制件强度
在制件的转角处易产生应力集中,在受力或受冲击、振动时会发生破裂,尤其像常用的工程塑料――聚碳酸酯,如果成型条件不当或制件结构不合理,则会产生很大的内应力,特别容易产生应力开裂。
实验数据证明,当圆角半径小于制件壁厚0.3倍/时应力集中急剧增大,当大于壁厚0.8倍/时,应力集中明显变小。
2、圆角可有利于充模和脱模
对于一些流动性差的塑料或加入填料的塑料,制件设计圆角尤为重要,不仅可改善充模性能,而且可提高制品使用性能。
3、圆角有利于模具制造,提高模具强度
制件上设计了圆角,模具的对应部位也呈圆角,这就增加了模具的坚固性,模具在淬火或使用时不致因应力集中而开裂,因而也增加了模具的强度。
六.应根据制件的使用要求和塑料材料的特性合理确定制件的尺寸公差。
影响塑料制件尺寸精度的因素很多而且十分复杂,归纳起来主要有以下几方面:
1、塑料原料本身的特性,一般结晶型和半结晶型的塑料的收缩率比无定型的大,范围也宽,因此制件尺寸精度也就有差异。
2、成型工艺条件如料温、模温、注射压力、保压压力、塑化背压、注射速度、成型周期等都会影响成型收缩率的大小和波动范围。
3、模具的结构如分型面选择、浇注系统的设计、排气、模具的冷却和加热等以及模具的刚度等都会影响制件尺寸精度。
4、模具在使用过程中的磨损和模具导向部件的磨损也会直接影响制件的尺寸精度。
因此在制件设计中正确合理确定尺寸公差是非常重要的。
对于工程塑料制件、尤其是以塑代钢的制件,设计者往往简单地套用机械零件的尺寸公差,这是很不合理的,许多工业化国家都根据塑料特性制定了塑料制件尺寸公差。
我国也于1993年发布了GB/T14486-93 《工程塑料模塑塑料件尺寸公差》,设计者可根据所用的塑料原料和制件使用要求,根据标准中的规定确定制件的尺寸公差。
七.工程塑料的制件设计除了要注意上述各点外,还应注意各种孔、侧凹(凸)、螺纹和嵌件的设计,这里不再一一详述,如有需要了解,可参阅有关专业书利,也欢迎与我们交流讨论。