高炉钢结构详解
高炉本体和附属设备介绍

2、高炉炉衬
工作条件
1. 热力作用 ①温度升高,耐火材料可能发生膨胀, 个别情况也会因晶体组织改变而发生体积收缩;② 温度波动超过一定限度,热应力超过砖衬的强度极 限, 引起耐火砖的破裂; ③温度高,也会引起耐火 砖软化甚至熔化;
2. 化学作用 ①高温下液态渣铁的渗透和化学侵蚀; ②碱金属及其化合物对炉衬的化学侵蚀;③锌和氟 的破坏及适宜温度下发生的碳素沉积等破坏作用;
1. 从原料进厂到高炉矿槽 完成卸、堆、 取、运输作业,根据需要进行破碎、筛分、 混均等过程。
2. 作用:贮存、处理、供应作用 2. 从高炉矿槽到高炉炉顶 按规定原料品
种、数量分批向高炉及时供料,根据需要 进行筛分。 3. 有料车斜桥上料和皮带上料。
现代高炉对原料供应系统的要求:
①保证连续地、均衡地供应高炉冶炼所需的原 料,并为进一步强化冶炼留有余地; ②在贮运过程中应考虑为改善高炉冶炼所必需 的处理环节,如混匀、破碎、筛分等。焦炭在 运输过程中应尽量减少破碎率; ③应该尽可能实现机械化和自动化,提高配料、 称量的准确度; ④在各转运环节和落料点,应有通风除尘设施;
选用碳砖
炉喉
1) 破损机理: 机械撞击、摩擦、气流冲刷。
2) 对策: 安装金属保护钢砖。
高炉冷却设施
高炉炉体的合理冷却,对保护砖衬和金属构件、 维护合理的炉型有决定性的作用。 其主要作用是: 1)降低炉衬温度,使砖衬保持一定的强度,维护 炉型,延长寿命。 2)形成保护性渣皮,保护炉衬。 3)保护炉壳、支柱等金属结构,免受高温影响。
3. 水的硬度: 指每m3水中钙、镁离子的摩尔数。
根据硬度不同,水可分为三类: 软 水:硬度<3mol/m3 硬 水:硬度在3~9mol/m3 极硬水:硬度>9mol/m3
高炉钢结构
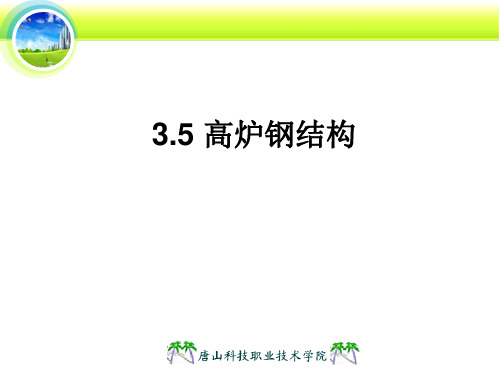
三. 炉壳厚度
可由下式计算:
kD
式中:
——计算部位炉壳厚度,mm;
D—— 计算部位炉壳外弦带直径(对 圆锥壳体采用大端直径),m; k ——系数,mm/m;与弦带位置有 关(见下页图),其值见下表。
高炉各弦带k的取值
炉顶封板与 炉喉 当 50° <β <55° β >55° 4.0 3.6 2.0 2.2 2.7 3.0
一. 炉缸支柱:
1. 作用:
用来承担经炉腰支圈传递下来的全部荷载。
2. 数目:
支柱的数目常为风口数目的一半或三分之 一,均匀地分布在炉缸周围。 支柱向外倾斜6º 左右,以使炉缸周围宽敞。
二. 炉身支柱
1. 作用:
支承炉顶框架及炉顶平台上的荷 载、炉身部分的平台走梯、给排水管 道等。
一般为 6 根,下端应与炉缸支柱 相对应。
3.5 高炉钢结构
一. 设计高炉钢结构考虑的因素:
(1)考虑到各种设备安装、检修、更换的可行性,要考虑 到大型设备的运进运出,吊上吊下,临时停放等可能性 ;
(2)具有耐高温高压、耐磨和可靠的密封性; (3)应留有足够的净空尺寸,并且要考虑到安装偏差和受 力变形等因素 ;
(4)对于支撑构件,要认真分析荷载条件,做强度计算 ;
高炉炉身 高炉炉身下弦带 风口带到炉腹上折点 炉缸及炉底
高炉炉体各弦带分界示意图 炉身下弦带高度一般不超过炉身高度的1/4~1/3.5。
我国某些高炉炉壳厚度(mm)
高炉容积,m3 高炉结构型式 100 炉缸 支柱 14 14 14 14 16 8 14 8 255 自立 式 16 16 16 16 - 14 14 12 620 炉缸 支柱 25 25 22 22 30 18 25 18 620 自立式 1000 炉体 框架 28/32 32 28 28 - 25 25 20 1513 炉缸 支柱 36 32 30 30 36 30 36 24 2025 炉体 框架 36 36 32 30 - 28 32 24 4063 炉体 框架 65, 铁口区 90 90 60 60 - 炉身由下至 上依次为 55,50,40, 32,40
新冶钢1780m3高炉讲解
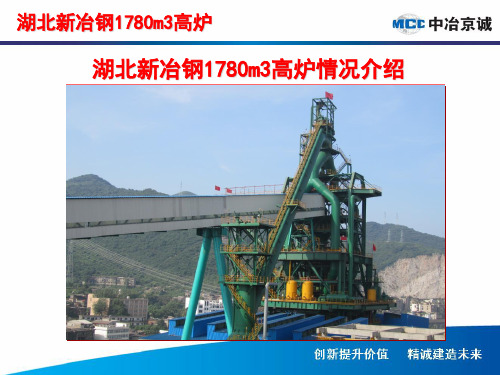
高炉内型
高炉实际有效容积为2005.6m3。炉缸直径D=10100mm、炉缸高度 h=4400mm,高径比Hu/D=2.4159。高炉内型设计时特别注意适当加深死铁 层,死铁层深度h0=2100mm,h0/d=20.54%。以尽可能减少铁水环流对炉 缸侧墙的冲刷,减轻“象脚”区的侵蚀。高炉设置26个风口和2个铁口。
完善的高炉本体自动化检测
高炉本体设置了完善的自动化检测, 为高炉操作者提供可靠的操作依据,做 到及时发现,及时处理,保证高炉稳定 顺行。 炉底满铺炭砖部分设置了4层热电偶 ,共65点。 在炉缸不同高度上布置8层热电偶, 共108点。特别是炉缸异常侵蚀区每层 均有热电偶,且按照7个方位布置。 炉缸第1~3段冷却壁设置9+9+8=26支 冷却壁壁体测温。
湖北新冶钢1780m3高炉
温度偏高标高
温度变化趋势
温度偏高方位
湖北新冶钢1780m3高炉
四.原因分析及结论
局部温度升高原因分析 新冶钢针对高炉炉缸温度急剧升高的问题,召集了国内 炼铁界知名专家如刘云彩、宋木森、汤清华、陈志焕以及湘 钢、安钢等类似问题高炉的企业进行会诊。 专家结论如下: (1)此高炉锌负荷较高,对炉衬造成一定破坏。 (2)根据调研了解的情况,当前铁口深度3200mm,基本 排除因为铁口泥包断裂导致的炉缸温度急剧飙升。 (3)认为目前高炉炉缸温度较高是侵蚀造成的。 (4)炭素捣打料质量影响炉缸传热,是影响炉缸长寿的重 要环节。
高炉冷却结构
炉体冷却结构设计采用薄壁、薄炉衬方式,炉底炉缸采用4段光面铸铁 冷却壁(材质为RTCr),每块设4根φ76x6冷却水管,冷却水设计流速 ≥1.8m/s, 水管间距235mm。冷却壁设计表比面积为1.015。在国内同类高 炉设计中冷却强度相对比较高,完全满足冷却要求。
高炉钢结构设计

高炉钢结构设计 (steel structure design of blast furnace)炼铁高炉专用钢结构的设计。
高炉钢结构设计主要内容包括高炉本体和炉顶、上料系统、热风炉系统、粗煤气除尘系统、出铁场和辅助设施钢结构的设计,做好系统间整体配合联系、进行结构的材料选择和采取安全防护措施。
高炉系统钢结构见图1。
设计时要进行结构形式的选择,构件强度稳定性、变形的计算和合理的构造处理,以保证结构安全使用与经济合理。
设计应按《钢结构设计规范》及其它有关规范规定进行。
对于地震区的高炉钢结构,其抗震设计要求还要符合抗震设计规范规定。
高炉钢结构的大部分是高炉生产设备的主要组成部分,其特点是:(1)种类繁多,形式特殊。
有多层空间框架的炉体框架、多折点壳体的炉壳、异形壳体组成的热风炉壳、圆或椭圆形筒壳的通廊等。
(2)结构尺寸及构件断面较大。
如:5000m3 左右高炉全高可达120m,炉壳直径为20m,炉壳厚度可达90~120mm,炉体框架箱形柱的断面尺寸达2.0m×4.0m。
(3)钢材用量多,如5000m3 高炉,包括运输、动力、管线在内钢结构用量近9万t。
(4)工作条件较苛刻。
如:炉体及周围结构受高温影响及水气锈蚀作用,热风炉外壳上部有时受晶间应力腐蚀开裂作用,上料料车卷扬机的作业率高达80%,壳体构件还要承受煤气爆炸等事故性内压力和砖衬被侵蚀后高炉外壳局部温度过热的作用。
(5)各系统间结构穿插交错,荷载辗转传递。
要控制其变形,使其相互协调。
高炉本体和炉顶钢结构高炉本体结构形式主要有自立式和非自立式两种(图2),也有介于两者之间的过渡形式。
自立式高炉包括高炉外壳、炉体框架和炉顶刚架。
炉壳独自承受炉内有关全部竖向荷载,而在炉周设炉体框架支承上部设备及平台。
大中型高炉多用此种形式。
非自立式高炉在炉壳下部设托圈和炉缸支柱,以支持炉内荷载,且多不设炉体框架,而将炉身平台及炉顶刚架支承在炉壳上,小型高炉多用此种形式。
高炉本体知识讲解

高炉本体3.2 高炉炉衬优化高炉炉型我国炼铁工作者历来重视高炉炉型设计,通过研究总结高炉破损机理和高炉反应机理,优化高炉炉型设计的基本理念已经形成。
(1)加深死铁层深度实践证实,高炉炉缸炉底“象脚状”的异常侵蚀,主要是由于铁水渗透到碳砖中,使碳砖脆化变质,再加之炉缸内铁水环流的冲刷作用而形成的。
加深死铁层深度,是抑制炉缸“象脚状”异常侵蚀的有效措施。
死铁层加深以后,避免了死料柱直接沉降在炉底上,加大了死料柱与炉底之间的铁流通道,提高了炉缸透液性,减免了铁水环流,延长了炉缸底部寿命。
理论研究和实践表明,死铁层深度一般为炉缸直径的15%~20%。
(2)适当加高炉缸高度高炉在大喷煤操作条件下,炉缸风口回旋区结构将发生变化。
适当加高炉缸高度,不仅有利于煤粉在风口前的燃烧,而且还可以增加炉缸容积,以满足高效化生产条件下的渣铁存储,减少在强化冶炼条件下出现炉缸“憋风”的可能性。
近年我国已建成或在建的大型高炉都有炉缸高度增加的趋势,高炉炉缸容积为有效容积的16%~18%。
(3)加深铁口深度铁口是高炉渣铁排放的通道,铁口区的维护十分重要。
研究表明,适当加深铁口深度,对于抑制铁口区周围炉缸内衬的侵蚀具有显著作用,铁口深度一般为炉缸半径的45%左右。
这样可以减轻出铁时在铁口区附近形成的铁水涡流,延长铁口区炉缸内衬的寿命。
(4)降低炉腹角降低炉腹角有利于炉腹煤气的顺畅排升,从而减少炉腹热流冲击,而且还有助于在炉腹区域形成比较稳定的保护性渣皮,保护冷却器长期工作。
现代大型高炉的炉腹角一般在800以下,本钢1号高炉2600(上标)炉腹角已降低到75.370。
3.3 炉体冷却方式长寿炉缸炉底的关键是必须采用高质量的碳砖并辅之合理的冷却。
通过技术引进和消化吸收,我国大型高炉炉缸炉底内衬设计结构和耐火材料应用已达到国际先进水平。
以美国UCAR公司为代表的“导热法”(热压炭砖法)炉缸设计体系已在本钢、首钢、宝钢、包钢、湘钢等企业的大型高炉上得到成功应用;以法国SAVOIE公司为代表的“耐火材料法”(陶瓷杯法)炉缸设计体系在首钢、梅山、宝钢、鞍钢等企业的大型高炉上也得到了推广应用。
高炉炼铁设计与设备知识点

高炉炼铁设计与设备知识点高炉是一种用于炼铁的设备,它起着至关重要的作用。
在高炉炼铁的过程中,设计和设备的选择十分关键。
本文将介绍一些与高炉炼铁设计和设备相关的知识点。
一、高炉的结构高炉通常由炉身、崩塌室、渣口、风口和煤气出口等部分组成。
炉身是高炉的主体部分,由内、外砌砖层构成。
炉身内部分为上、中、下三段,分别进行还原、融化和收集铁水的过程。
二、高炉的炉料高炉的炉料是指进入高炉的原料,通常包括铁矿石、焦炭和石灰石等。
其中,铁矿石是炉料的主要成分,通常由赤铁矿、磁铁矿和针铁矿组成。
焦炭是炉料的还原剂,而石灰石用于脱硫。
三、高炉的还原还原是高炉炼铁的关键步骤之一。
在高炉内,焦炭的碳与铁矿石中的氧发生化学反应,生成一氧化碳和一氧化碳二氧化碳等还原气体。
这些还原气体与铁矿石中的氧反应,将铁矿石还原成为金属铁。
四、高炉的融化和冶炼在高炉的融化和冶炼过程中,铁矿石被还原成金属铁,然后与渣、石灰石等杂质形成熔融的铁水。
随后,铁水收集在高炉的下部,并通过渣口排出。
五、高炉的煤气排放在高炉炼铁过程中,除了产生铁水外,还会产生大量的高炉煤气。
这些煤气含有一氧化碳、氢气、一氧化碳二氧化碳等成分。
为了充分利用这些煤气,通常会对其进行净化和脱硫处理,然后用于发电或供热等用途。
六、高炉炼铁的控制高炉炼铁的过程需要进行精确的控制。
通过对炉温、煤气成分、料层厚度等参数的监测和调整,可以提高炼铁效率,减少能耗和杂质含量,并延长高炉的使用寿命。
七、高炉炼铁的应用高炉炼铁广泛应用于钢铁行业。
炼铁产出的铁水,经过进一步的炼钢处理,可以制成各种钢材,被用于建筑、制造、交通等领域。
总结:通过了解高炉炼铁的设计和设备知识点,我们可以更好地理解高炉炼铁的工作原理和过程。
高炉的结构、炉料、还原、融化和冶炼、煤气排放、控制等方面都对高炉的炼铁效果和效率有着重要的影响。
只有合理设计和选择设备,并进行科学的操作和控制,才能保证高炉炼铁的顺利进行,提高钢铁生产的效益和质量。
炼铁原理与工艺6(高炉炉体与维护)

6. 2高炉炉衬的选择与砌筑
② 高炉炉腹、炉腰和炉身耐火材料用陶瓷质耐火 材料的要求: A. 化学成分中AL2O3要高,Fe2O3含量要少。 B. 耐火度要高。测温锥测定 C. 荷重软化点要高。0.2Mpa载荷下的软化温度 D. 重烧收缩率要小。残余收缩,是表示耐火材料 升到高温后产生的裂纹可能性大小的一种性质。 E. 气孔率要低。
6. 2高炉炉衬的选择与砌筑
B. 从从传热学角度讲分为: 综合炉底结构和全碳砖炉底结构两大 流派。综合炉底是绝热和导热的结合,全 碳砖炉底则是完全的导热基理。目前国内 外炉底、炉缸结构主要有以下几种: a. 大块炭砖砌筑,炉底设陶瓷垫。 b. 热压小块炭砖砌筑,炉底设陶瓷垫。 c. 大块或小块炭砖砌筑,炉底和炉缸设陶瓷 杯。
炉型尺寸各符号表示的意义
• • • • • • • • • • • • • • Hu---有效高度 Vu---有效容积 D---炉腰直径 d---炉缸直径 d1---炉喉直径 h0---死铁层高度 h1--炉缸高度 h2---炉腹高度 h3---炉腰高度 h4---炉身高度 h5---炉喉高度 hf---风口高度 α---炉腹角 β---炉身角
NMA
3层大块炭砖
2层刚玉砖
NMD
刚玉砖
炉缸侧壁:
NMA和NMD小块炭砖
NMA
大块炭砖
石墨砖
6. 2高炉炉衬的选择与砌筑
2. 炉腹、炉腰和炉身 ① 破损机理: 炉身、炉腰部位主要是考虑抗热应力 破坏性能,和炉料、煤气的冲刷。一般以 黏土质和高铝质耐火砖,但是在高炉大型 化和强化后也对砖衬材质提高了要求。
6.1高炉本体结构
③ 美国料式高炉的零位是取大钟开启时底 面以下915mm处。零料线位置到风口中 心线之间的容积为工作容积。 欧美也有用高炉全容积的。全容积 是指零料线到炉底砖衬表面之间(包括 死铁层)的容积。
第三章 高炉炼铁

的碳化硅砖或高导热的炭砖为主,高
炉下部以高导热的石墨质炭砖为主,
图 5.7 炉缸、炉底砌筑结构
6
图 3.7 为炉缸、炉底砌筑结构示意图。 3)冷却设备
冷却设备的作用是降低炉衬温度,提高炉衬材料抗机械、化学和热产生的侵蚀能力, 使炉衬材料处于良好的服役状态。高炉使用的冷却设备主要有冷却壁、冷却板和风口。冷却 壁紧贴着炉衬布置,冷却面积大;而冷却板水平插入炉衬中,对炉衬的冷却深度大,并对炉 衬有一定的支托作用。
(3)鼓风:空气通过高炉鼓风机加压后成为高压空气(鼓风),经过热风炉换热,将温 度提高到 1100~1300℃,再从高炉风口进入炉缸,与焦炭和煤粉燃烧产生热量和煤气。鼓风 带入高炉的物理热占高炉热量总收入的 20%左右。在鼓风中加入氧气可提高鼓风中的氧含 量(称为富氧鼓风)。采用富氧鼓风可提高风口燃烧温度,有利于高炉提高喷煤量和高炉利
4000m3 级高炉日产生铁量达到 10000 t 以
上。
hf
d1
β D
α
风口 中心线
d
铁口 中心线
h1
h2
h3
h4
h5
h6
炉 喉
炉 身
炉 腰 炉 腹 炉 缸 死铁层
Hu H
h0
3.2.3 高炉生产主要技术经济指标
图 5.3 高炉内型
(1)有效容积利用系数(ηu ):每 m3 高炉有效容积每天生产的铁水量( t / m3 ⋅ d ),
KΣ
=
每天装入高炉的焦炭量+ 每天喷入高炉的煤粉量×置换比 高炉每天出铁量
(3.4)
煤粉置换比通常小于 1.0,一般在 0.75~0.90 之间。
(6)冶炼强度( I ):每 m3 高炉有效容积每天消耗的(干)焦炭量( t / m3 ⋅ d )。
- 1、下载文档前请自行甄别文档内容的完整性,平台不提供额外的编辑、内容补充、找答案等附加服务。
- 2、"仅部分预览"的文档,不可在线预览部分如存在完整性等问题,可反馈申请退款(可完整预览的文档不适用该条件!)。
- 3、如文档侵犯您的权益,请联系客服反馈,我们会尽快为您处理(人工客服工作时间:9:00-18:30)。
一. 设计高炉钢结构考虑的因素:
(1)考虑到各种设备安装、检修、更换的可行性,要考虑 到大型设备的运进运出,吊上吊下,临时停放等可能性 ;
(2)具有耐高温高压、耐磨和可靠的密封性;
(3)应留有足够的净空尺寸,并且要考虑到安装偏差和受 力变形等因素 ; (4)对于支撑构件,要认真分析荷载条件,做强度计算 ;
高炉基础
1-冷却壁;2-水冷管;3-耐火砖;4-炉底砖;5-耐热混凝土基墩;6荷:
2. 动负荷:
3. 热应力的作用 :
四. 对高炉基础的要求
①高炉基础应把高炉全部荷载均匀 地传给地基,不允许发生沉陷和不 均匀的沉陷。
②具有一定的耐热能力。
五. 基墩: 基墩断面为圆形,直径与炉底相同 ,高度一般为2.5~3.0m 。
高炉炉身 高炉炉身下弦带 风口带到炉腹上折点 炉缸及炉底
高炉炉体各弦带分界示意图
炉身下弦带高度一般不超过炉身高度的1/4~1/3.5。
我国某些高炉炉壳厚度(mm)
高炉容积,m3 高炉结构型式 100 炉缸 支柱 14 14 14 14 16 8 14 8 255 自立 式 16 16 16 16 - 14 14 12 620 炉缸 支柱 25 25 22 22 30 18 25 18 620 自立式 1000 炉体 框架 28/32 32 28 28 - 25 25 20 1513 炉缸 支柱 36 32 30 30 36 30 36 24 2025 炉体 框架 36 36 32 30 - 28 32 24 4063 炉体 框架 65, 铁口区 90 90 60 60 - 炉身由下至 上依次为 55,50,40, 32,40
3. 缺点:
耗费钢材较多、投资高。
三. 炉体框架式——大型高炉多用
1. 特点:
①由四根支柱连结成一个大框架;
②框架本身是一个与高炉本体不相连接的独 立结构。
③框架下部固定在高炉基础上,顶端支撑在 炉顶平台上。 ④因此除装料设备重量经炉壳传给基础外, 其余所有重量均由大框架直接传给基础。
2. 优点: 风口平台宽敞,炉前操作方便, 有利于大修时高炉容积的扩大。
六. 基座:
基座直径与荷载和地基土质有关,基 座底表面积可按下式计算:
A P
式中:
KS 允
A ——基座底表面积,m2; P ——包括基础质量在内的总荷载,t; K ——小于1的安全系数,取值视土质而定;
S允 ——地基土质允许的承压能力,t/m2。一般
建在>2.0kg/cm2的土质上 。
四. 自立式 ——小型高炉多用
1. 特点:
不设任何支柱,全部荷载均由炉壳承受, 并传递到基础上。 2. 优点: 钢材消耗少,结构简单,炉前宽敞。 3. 注意: 设计时应尽量减少炉壳转折点;高炉生产 过程中应加强炉壳冷却;高炉大修时炉顶设备 需要另设支架。
3.5.2 炉 壳
一. 作用: ①固定冷却设备;
②保证高炉砌砖的牢固性;
③承受炉内压力和起到炉体密封作用。 ④有的要承受炉顶荷载和起到冷却内衬 作用(外部喷水冷却时)。
二. 设计时注意的问题: ①炉壳折点和开孔应避开在同一个截面; ②炉缸下部折点应在铁口框以下100mm以上; ③炉腹折点应在风口大套法兰边缘以上大于 100mm处; ④炉壳开口处需补焊加强板。
与上下炉壳连接处,两侧都用角钢加固, 在外侧边缘也用角钢加固,以加强其刚性。
炉腰支圈
四. 支柱座圈 为了使支柱作用于炉基上的力比较
均匀,在每根支柱下面都有用铸铁或型
钢做成的单片垫板,并且彼此用拉杆或
整环连接起来 。
3.6 高炉基础
一. 作用: 将高炉全部荷载均匀地传递到地基。
二. 组成:
由埋在地下的基座部分和地面上的基 墩部分组成,见图:
4. 应用:目前小高炉多用这种结构。
二. 炉缸、炉身支柱式——五、六十年代大型高炉 1. 特点: ①炉顶装料设备和煤气导出管、上升管等的重 量经过炉身传递到炉腰托圈; ②炉顶框架、大小钟荷载则通过炉身支柱传递 到炉腰托圈; ③传递到炉腰托圈的重量再通过炉缸支柱传递 到基础上。
2. 优点: 降低了炉壳负荷,安全可靠。
2. 数目:
支柱的数目常为风口数目的一半或三分之 一,均匀地分布在炉缸周围。 支柱向外倾斜6º 左右,以使炉缸周围宽敞。
二. 炉身支柱 1. 作用:
支承炉顶框架及炉顶平台上的荷 载、炉身部分的平台走梯、给排水管 道等。
一般为 6 根,下端应与炉缸支柱 相对应。
三. 炉腰支圈 1. 作用:
将其承托的上部均布荷载(砌砖重量及压 力等)变成几个集中载荷传给炉缸支柱,同时 也起着密封作用。
(5)避免积尘积水;
(6)合理设置走梯、过桥和平台 。
3.5.1. 高炉本体钢结构
高炉本体钢结构
a-炉缸支柱式;b-炉缸、炉身支柱式;c-炉体框架式;d-自立式
一. 炉缸支柱式——曾用于中小型高炉 1. 特点: 炉顶荷载及炉身荷载由炉身外壳通过炉缸 支柱传到基础上。 2. 优点: 节省钢材。 3. 缺点: 风口平台拥挤,炉前操作不方便。
炉底 风口区 高炉炉 壳 厚度, mm 炉腹 炉腰 托圈 炉身下部 炉顶及炉喉 炉身其它部位
28 28 28 22 - 20 25 18
3.5.3 炉体框架
炉体框架由四根支柱组成,上至 炉顶平台,下至高炉基础,与高炉中 心成对称布置,保证支柱与热风围管 有250mm间距。
3.5.4 炉缸炉身支柱、炉腰支圈和支柱座圈 一. 炉缸支柱: 1. 作用: 用来承担经炉腰支圈传递下来的全部荷载。
三. 炉壳厚度 可由下式计算:
kD
式中:
——计算部位炉壳厚度,mm;
D—— 计算部位炉壳外弦带直径(对 圆锥壳体采用大端直径),m; k ——系数,mm/m;与弦带位置有 关(见下页图),其值见下表。
高炉各弦带k的取值
炉顶封板与 炉喉 当 50° <β<55° β>55° 4.0 3.6 2.0 2.2 2.7 3.0