焙烧炉工艺
氧化铝悬浮焙烧炉新工艺流程

氧化铝悬浮焙烧炉新工艺流程
氧化铝悬浮焙烧炉新工艺流程如下:
(一)原料准备:使用铝矾土作为原料,经过破碎、磨细等工序后,得到粉末状的氢氧化铝原料。
(二)气态悬浮:将氢氧化铝原料通过给料装置加入到气态悬浮焙烧炉中。
气态悬浮焙烧炉内设置有多层炉壁,通过控制炉壁温度,使得氢氧化铝原料在炉内悬浮。
同时,在炉内通入适量的气体,如氮气或空气,以保持炉内的气氛。
(三)焙烧反应:在气态悬浮焙烧炉中,氢氧化铝原料与气体中的氧气发生氧化反应,生成氧化铝。
这个过程需要在高温下进行,通常在1000-1200℃下进行。
(四)产物收集:氧化铝颗粒从炉中排出,通过输送装置输送到收集装置中。
收集到的氧化铝颗粒可以进行进一步的处理,如分级、洗涤、干燥等。
(五)尾气处理:焙烧过程中产生的尾气中含有未完全反应的气体和杂质,需要进行处理,以防止对环境造成污染。
尾气处理通常包括除尘、除杂、废气排放等步骤。
(六)工艺控制:整个工艺流程需要控制各个参数,如温度、气氛、原料质量等,以保证焙烧过程的顺利进行和获得高质量的氧化铝产品。
以上是氧化铝悬浮焙烧炉新工艺流程的基本步骤,具体操作还需要根据不同设备和工艺条件进行调整和优化。
焙烧炉岗位技术操作规程

焙烧炉岗位技术操作规程1概述:负责对原料供料的及时性和质量情况进行联系、检查,以及焙烧炉温度调整,保证其在规定指标内,确保焙烧炉安全运行,保证焙砂质量满足下道工序生产。
2工艺流程和设备表:2.1工艺流程图2.2设备表3岗位操作:3.1原料要求:焙烧使用锌精矿质量标准(%)Zn≥45、 S;28~32、 Fe≤14、 Co≤0.04 游离H2O≤10、Sb≤0.024、粒度<10mm3.2工艺条件、产品质量、工艺条件3.2.1混合焙砂质量标准(%)Zn ≥51 、 Zn可≥43、 S残<0.65、Si可≤1.2 、 Fe≤5 、粒度:+80目≤6.065%≤-200目≤80%3.2.2主要技术经济指标3.2.2.1锌回收率99.5%。
3.2.2.2脱硫率≥93.41%。
3.2.2.3系统漏气率<15%。
3.2.2.4烧成率89%。
3.2.3沸腾焙烧技术操作条件3.2.3.1流态化焙烧炉3.2.3.1.1焙烧强度:6.16 t/㎡·d3.2.3.1.2流化层温度:870 ℃~930℃ (视原料成分定) 3.2.3.1.3炉膛温度: 950±30℃3.2.3.1.4炉气出口二氧化硫浓度:9~10%3.2.3.1.5鼓风量:51570 Nm3/h3.2.3.1.6烟气量:53140 Nm3/h3.2.3.1.7流化层高度:1000㎜3.2.3.1.8炉顶压力:0~-20Pa3.2.3.1.9喷水温度:1050 ℃3.2.3.2流态化冷却器3.2.3.2.1焙砂处理量:11t/h(单组)3.2.3.2.2焙砂入口温度:870 ℃~930℃3.2.3.2.3焙砂出口温度:≤500℃3.2.3.2.4换热面积:3.3㎡3.2.3.2.5流态空气量:100Nm3/h3.2.3.2.6流态空气压力:98KPa3.2.3.3冷却圆筒3.2.3.3.1焙砂进口温度:≤500℃3.2.3.3.2焙砂出口温度:≤200℃3.2.3.3.3冷却水进口水温度:30℃3.2.3.3.4冷却水出口水温度:45℃3.2.3.3.5圆筒回转速度:5.3r/min3.2.3.3.6生产能力:22t/h3.2.3.3.7冷却水用量:110 m3/h~150m3/h3.3正常操作3.3.1正常操作:在正常情况下,为了保证炉温稳定,除了均匀加料外,还必须随时掌握原料、风量和炉温的变化情况,以便及时调整加料量。
氧化铝厂 焙烧炉工艺流程

氧化铝厂焙烧炉工艺流程A calcination furnace, also known as a roasting furnace, is an essential part of the aluminum oxide production process. 钙钛矿石产生的氧化铝需要在高温下经过焙烧才能得到纯净的氧化铝产品。
Calcination is the process of heating the aluminum oxide at high temperatures to drive off water and carbon dioxide, leaving behind pure aluminum oxide. 焙烧炉的工艺流程需要精确控制温度和气氛以确保产品的质量。
The process involves careful control of temperature and atmosphere to ensure the quality of the product.The first step in the process is the preheating stage, where the raw aluminum oxide is loaded into the furnace and heated to a certain temperature. 炉子在这个阶段会使用燃料加热,以达到合适的温度。
During this stage, any impurities in the aluminum oxide will start to break down and evaporate, leaving behind a purer product. 在预热阶段,需要适当的控制加热速度和温度以及气氛,以确保原料完全适应高温环境。
The heating rate, temperature, and atmosphere need to be carefully controlled during the preheating stage to ensure that the raw material can withstand the high temperatures.Once the preheating stage is complete, the temperature is increased further to begin the calcination process. 这个阶段需要持续一段时间,使得原料中的水分和二氧化碳得以完全挥发。
锌沸腾焙烧炉工艺操作规程
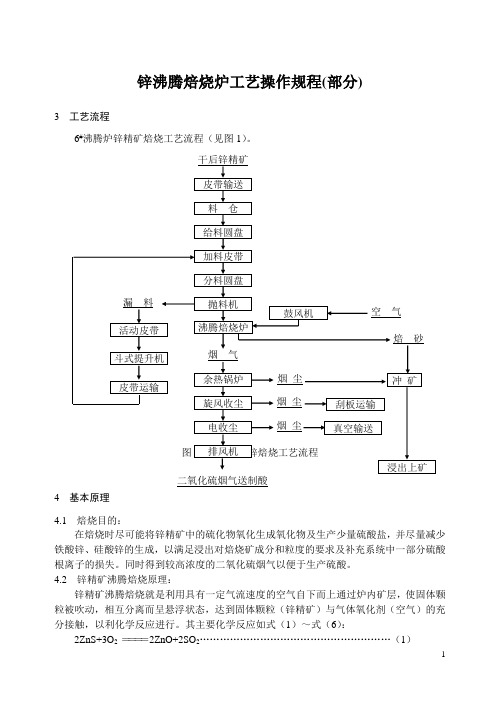
锌沸腾焙烧炉工艺操作规程(部分)3 工艺流程6#沸腾炉锌精矿焙烧工艺流程(见图1)。
44.1 焙烧目的:在焙烧时尽可能将锌精矿中的硫化物氧化生成氧化物及生产少量硫酸盐,并尽量减少铁酸锌、硅酸锌的生成,以满足浸出对焙烧矿成分和粒度的要求及补充系统中一部分硫酸根离子的损失。
同时得到较高浓度的二氧化硫烟气以便于生产硫酸。
4.2 锌精矿沸腾焙烧原理:锌精矿沸腾焙烧就是利用具有一定气流速度的空气自下而上通过炉内矿层,使固体颗粒被吹动,相互分离而呈悬浮状态,达到固体颗粒(锌精矿)与气体氧化剂(空气)的充分接触,以利化学反应进行。
其主要化学反应如式(1)~式(6):2ZnS+3O2 ====2ZnO+2SO2 (1)ZnS+2O2====ZnSO4 (2)3ZnSO4+ZnS====4ZnO+4SO2 (3)2SO2+O2 2SO3 (4)ZnO+SO3 ZnSO4 (5)XZnO+YFe2O3XZnO.YFe2O3 (6)5 原材料质量要求5.1 入炉混合锌精矿:应符合Q/ZYJ06.05.01.01—2005《混合锌精矿》的规定。
5.1.1 化学成分(%):Zn≥47 S:28~32,Fe≤12,SiO2≤5,Pb≤1.8,Ge≤0.006,A s≤0.45 ,Sb≤0.07,Co≤0.015 Ni≤0.004。
5.1.2 水分:6%~8%。
5.1.3 粒度小于14mm,无铁钉、螺帽等杂物。
5.2 工业煤气(%):应符合Q/ZYJ15.02.01—2003《工业煤气》的规定。
要求煤气压力在3000Pa以上,煤气流量不小于6500m3/h。
6 工艺操作条件6.1 沸腾焙烧6.1.1 鼓风量:14000 Nm3/h~30000Nm3/h6.1.2 鼓风机出口压力:12kPa~16kPa6.1.3 沸腾层温度:840℃~920℃6.1.4 炉气出口负压:0~30Pa6.2 余热锅炉6.2.1 出口烟气温度:340℃~390℃6.2.2 出口烟气压力:-100Pa~-200Pa6.2.3 汽包工作压力:4.01MPa±0.3MPa6.2.4 过热器出口蒸汽温度:380℃~450℃6.2.5 给水温度:100℃~105℃6.3 旋涡收尘器6.3.1 入口烟气温度:330℃~380℃6.3.2 出口烟气温度:320℃±10℃6.3.3 入、出口烟气压差:800Pa~1200Pa6.4 电收尘6.4.1 入口烟气温度:280℃~340℃6.4.2 出口烟气温度:≥235℃6.4.3 出口烟气压力:-2450Pa~-2700Pa6.5 排风机6.5.1 入口烟气温度:210℃~300℃6.5.2 入口烟气压力:-2650Pa~-2900 Pa6.5.3 出口烟气温度:≥210℃7 岗位操作法7.1 司炉岗位7.1.1 开炉操作7.1.1.1 开炉前做好设备、安全和环保方面的检查工作:应对所有设备进行一次全面细致的检查,确认各设备、仪表完全具备开炉条件;要对烟气系统各阀门、人孔门,煤气和供水、排水排汽系统进行检查,确认其符合安全环保要求。
焙烧车间调温工艺相关操作流程

焙烧车间调温工艺相关操作流程
一、焙烧车间燃烧系统移炉步骤:
1、备用挡板已插入前炉室、备用排烟架已放置到位,所有支管无漏风及摆动现象。
通知煤气站做好移炉准备。
2、关闭4P、5P、6P燃烧架煤气支管阀门,所移排烟架挡板已拔出、排烟架电源插头及通讯插头已拔出、所有连接均断开。
先打开备用排烟架滑板阀后再关闭待移排烟架滑板阀。
3、确认待移排烟架吊具安全可靠后调离排烟架,把大小火盖盖好后测温测压架前移并与控制柜连接到位,启动排烟架控制柜修改炉室号并检查各类数据是否在正常范围。
4、待移燃烧架电源及通讯插头拔出、燃烧架喷嘴及热电偶拔出并规范放置,确认燃烧架吊具是否安全可靠。
5、把原3P炉室的A、B、D孔小盖打开,待移燃烧架吊至3P指定位置并规范放置。
各热电偶及喷嘴放置到位,煤气管快速接头连接到位确认无泄露,电源插头及通讯插头连接到位。
6、启动燃烧架PLC控制柜及时修改炉室号并确认各显示是否正常。
7、检查鼓风架、冷却架吊具是否安全牢靠,拔出电源线规范放置后并相应前移一个炉室,检查各软管是否密封到位。
8、通知煤气站后恢复燃烧系统煤气供給,检查设备运行是否正常、各控制柜显示是否正常。
9、做好燃烧系统火道密封并清理作业现场保持现场整洁,移炉完毕。
二、停炉步骤:
1、通知煤气站进行降压,经煤气站同意后安排调温工打开炉面末端放散阀,直到降压完成,待煤气站通知后进行停炉。
关闭燃烧系统的时候必须关注煤气压力变化情况(煤气管道压力一般不超过20kpa),在保证安全的情况下缓慢进行。
2、安排多功能行车工、编解组工帮助调温工把燃烧架热电偶及喷嘴收起规。
焙烧车间调温工艺相关操作流程

焙烧车间调温工艺相关操作流程一、调温前的准备工作:1.确认待焙烧物料的温度范围和保温时间。
2.清理焙烧炉内的杂物和残留物,确保炉膛干净。
3.检查炉门、炉膛和加热设备的密封性能,确保无漏风现象。
4.准备好所需的仪器设备和工具。
二、调温操作步骤:1.将炉门打开,将待焙烧物料放置在焙烧炉的合适位置,并确保物料之间有足够的间隙,以便热风流通。
2.关上炉门,将炉门锁紧。
3.打开冷却水进水阀门,开始给焙烧炉进行冷却,同时打开焙烧炉的排气阀门,排出焙烧炉内的冷却水。
4.打开焙烧炉的燃气进气阀门,并通过燃气调节阀控制燃气进气量,点火将焙烧炉加热到初始温度。
过程中需要密切观察炉内温度的变化情况,确保升温平稳。
5.将焙烧炉的燃气进气阀门调至适当位置,使炉内温度保持在待焙烧物料所需的温度范围内。
根据需要,可能需要对燃气进气量进行微调,以保持稳定的温度。
6.开始计时,根据焙烧物料的要求,保持待焙烧物料在所需温度范围内的时间,确保物料充分焙烧。
7.在待焙烧物料保温时间结束后,通过减少燃气进气量逐渐降低焙烧炉的温度。
过程中需要注意控制降温速度,以防止物料破损或过度烧结。
8.当焙烧炉的温度降至安全范围后,关闭燃气进气阀门和排气阀门,停止加热和冷却。
9.打开炉门,将焙烧好的物料取出,并放置在指定位置进行冷却。
10.清理焙烧炉内的残留物,确保下次使用时的清洁。
11.记录本次焙烧的相关信息,包括温度变化、保温时间和焙烧效果等。
三、调温注意事项:1.在操作过程中要严格遵守焙烧工艺要求和操作规范。
2.在加热和冷却过程中,通过监测温度变化情况及时调整燃气进气量,保持焙烧炉内的温度稳定。
3.注意焙烧物料的堆放方式,确保物料之间有足够空间,以保证热风的充分流通。
4.确保焙烧炉的密封性能良好,避免热风泄漏或冷却水渗入炉膛。
5.在燃气调节过程中,要注意燃气进气量的控制,以避免过度加热或过快的温度升降。
6.注意工作环境的安全,遵守相关安全操作规程,必要时佩戴个人防护装备。
焙烧炉操作规程汇总
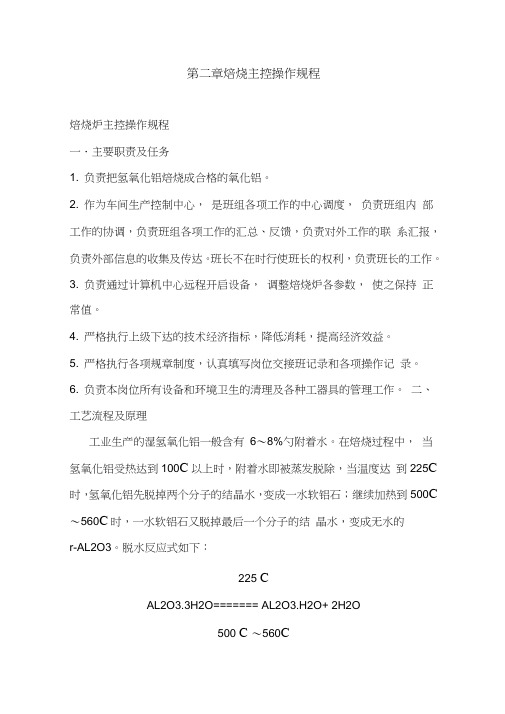
第二章焙烧主控操作规程焙烧炉主控操作规程一.主要职责及任务1. 负责把氢氧化铝焙烧成合格的氧化铝。
2. 作为车间生产控制中心,是班组各项工作的中心调度,负责班组内部工作的协调,负责班组各项工作的汇总、反馈,负责对外工作的联系汇报,负责外部信息的收集及传达。
班长不在时行使班长的权利,负责班长的工作。
3. 负责通过计算机中心远程开启设备,调整焙烧炉各参数,使之保持正常值。
4. 严格执行上级下达的技术经济指标,降低消耗,提高经济效益。
5. 严格执行各项规章制度,认真填写岗位交接班记录和各项操作记录。
6. 负责本岗位所有设备和环境卫生的清理及各种工器具的管理工作。
二、工艺流程及原理工业生产的湿氢氧化铝一般含有6〜8%勺附着水。
在焙烧过程中,当氢氧化铝受热达到100C以上时,附着水即被蒸发脱除,当温度达到225C 时,氢氧化铝先脱掉两个分子的结晶水,变成一水软铝石;继续加热到500C 〜560C时,一水软铝石又脱掉最后一个分子的结晶水,变成无水的r-AL2O3。
脱水反应式如下:225 CAL2O3.3H2O======= AL2O3.H2O+ 2H2O500 C 〜560CAL2O3.H2O===========r-AL2O3+ H2O在500 C〜560 C温度下焙烧得到的r-AL2O3是很分散的结晶质的氧化铝,需要进一步提高焙烧温度,才能结晶并且长大为粗颗粒。
将r-AL2O3加热至900C时,它开始转变为a -AL2O3,此时转化速度很慢,提高温度则转化速度加快。
在1050C〜1200C下维持足够的时间r-AL2O3 才完全转变为a -AL2O3。
从成品过滤送来的氢氧化铝(含水率W 5%卸入L01给料仓(① 3000X 8200mm经棒式阀卸到电子计量给料机(DEM1480),计量后送入螺旋给料机(①600X 3200mm.螺旋给料机将氢氧化铝送入文丘里闪速干燥器。
从P02顶部排出的烟气(320C )经烟道进入文丘里闪速干燥器的地步和氢氧化铝混合进行热交换,氢氧化铝附水在闪速干燥器内蒸发干燥。
山西铝业氧化铝焙烧流程

山西铝业氧化铝焙烧流程
山西铝业是中国最大的氧化铝生产企业之一,拥有先进的焙烧工艺流程。
焙烧是氧化铝生产的核心环节之一,其目的是将铝矾土中的结晶水和有机物质等挥发出去,使铝矾土转变为氧化铝。
一、铝矾土的预处理
山西铝业在氧化铝焙烧前,首先对铝矾土进行预处理。
铝矾土经过破碎、磨矿等工艺,得到粉碎后的铝矾土粉末。
然后,将铝矾土粉末与适量的水混合,形成矿浆。
二、矿浆的过滤
将铝矾土矿浆通过过滤设备进行过滤,去除其中的杂质和固液分离。
过滤后得到的固体物质称为滤渣,其中含有一定量的铝氧化物。
三、滤渣的焙烧
滤渣经过干燥处理后,进入焙烧炉进行焙烧。
焙烧炉内部温度高达1000℃以上,通过高温将滤渣中的结晶水和有机物质等挥发出去,使滤渣中的铝氧化物得到进一步提纯。
四、焙烧废气的处理
焙烧过程中产生的废气含有大量的有害气体和颗粒物,需要进行处理。
山西铝业采用先进的废气处理设备,如脱硫除尘装置和脱硝装置,将废气中的有害物质去除,以保护环境和员工的健康。
五、氧化铝的回收
焙烧后的滤渣经过冷却处理后,进一步加工提纯,得到高纯度的氧化铝。
氧化铝是一种重要的工业原料,广泛用于电子、建筑、化工等领域。
山西铝业通过优化焙烧工艺,不断提高氧化铝的产量和质量。
该企业还注重环保,积极推行废气处理和资源回收利用,以减少对环境的影响。
总结:
山西铝业的氧化铝焙烧流程包括铝矾土的预处理、矿浆的过滤、滤渣的焙烧、焙烧废气的处理和氧化铝的回收等环节。
通过先进的工艺和设备,山西铝业实现了氧化铝的高效生产和环保处理,为中国的氧化铝行业做出了重要贡献。
- 1、下载文档前请自行甄别文档内容的完整性,平台不提供额外的编辑、内容补充、找答案等附加服务。
- 2、"仅部分预览"的文档,不可在线预览部分如存在完整性等问题,可反馈申请退款(可完整预览的文档不适用该条件!)。
- 3、如文档侵犯您的权益,请联系客服反馈,我们会尽快为您处理(人工客服工作时间:9:00-18:30)。
四、【焙烧炉工艺】
1、工艺要求
焙烧温度:950-980℃保温时间:>30分钟
2、操作程序
1)检查焙烧炉和控温表是否正常,炉床是否平整干净。
2)仔细检查需要焙烧的型壳,型壳应完好无缺陷,有缺陷的
型壳必须修补好。
3)清理干净型壳浇口杯缘,严防砂子掉入型壳中。
4)小心将型壳浇口杯向下装入焙烧炉中,后浇注的型壳先装
炉,型壳离炉门不能低于20厘米。
5)点火升温,炉内温度约在600℃时关上炉门,继续焙烧,
至炉内温度在950-980℃之间,型壳保温时间大于30分钟,焙烧好的型壳应为白色或蔷薇色。
6)焙烧炉要与熔化炉配合,确保浇注时型壳烧好,并保持高
温,当钢水合格可浇注时,打开炉门,叉出型壳浇注,要求型壳从焙烧炉中叉出必须保持红壳,并且做到快速埋壳,快速浇注。
3、注意事项
严格控制焙烧温度和时间,并记录,如温度过高,时间过长型壳会烧坏,导致型壳强度降低和变形,如温度过低,时间过短,型壳浇不透,其透气性差,导致浇注不良,光洁度不好。
1、定期检查温度表,确保指示温度正确。
2、杜绝型壳返烧二次以上,烧好的型壳没有加注的要加温至型壳透亮才可浇注
3、定期清理焙烧炉底,焙烧炉点火时,炉前严禁站人,焙烧炉操作工必须严格遵守工艺操作规程,注意安全。