脱硫石膏蒸汽二步法生产建筑石膏粉工艺简介
国内生产脱硫石膏的工艺
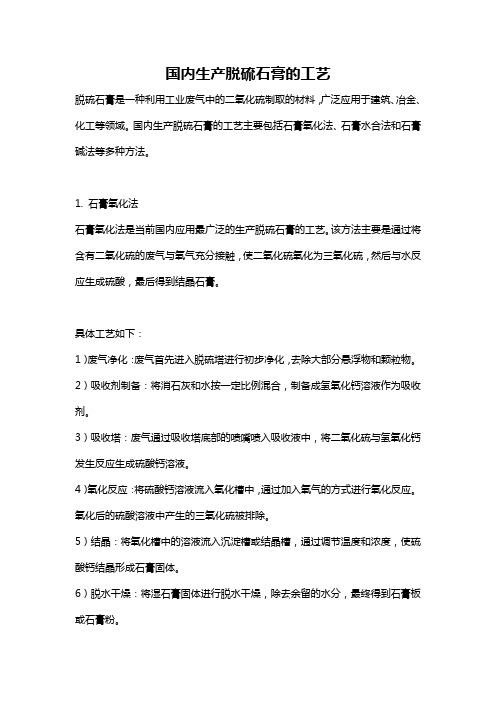
国内生产脱硫石膏的工艺脱硫石膏是一种利用工业废气中的二氧化硫制取的材料,广泛应用于建筑、冶金、化工等领域。
国内生产脱硫石膏的工艺主要包括石膏氧化法、石膏水合法和石膏碱法等多种方法。
1. 石膏氧化法石膏氧化法是当前国内应用最广泛的生产脱硫石膏的工艺。
该方法主要是通过将含有二氧化硫的废气与氧气充分接触,使二氧化硫氧化为三氧化硫,然后与水反应生成硫酸,最后得到结晶石膏。
具体工艺如下:1)废气净化:废气首先进入脱硫塔进行初步净化,去除大部分悬浮物和颗粒物。
2)吸收剂制备:将消石灰和水按一定比例混合,制备成氢氧化钙溶液作为吸收剂。
3)吸收塔:废气通过吸收塔底部的喷嘴喷入吸收液中,将二氧化硫与氢氧化钙发生反应生成硫酸钙溶液。
4)氧化反应:将硫酸钙溶液流入氧化槽中,通过加入氧气的方式进行氧化反应。
氧化后的硫酸溶液中产生的三氧化硫被排除。
5)结晶:将氧化槽中的溶液流入沉淀槽或结晶槽,通过调节温度和浓度,使硫酸钙结晶形成石膏固体。
6)脱水干燥:将湿石膏固体进行脱水干燥,除去余留的水分,最终得到石膏板或石膏粉。
2. 石膏水合法石膏水合法是利用石膏半水化的特性,将硫酸钙水合成石膏的工艺。
该方法适用于含水量较高的废气处理。
具体工艺如下:1)原料准备:将消石灰与二氧化硫废气以一定比例混合,并添加适量的水蒸气。
2)水合反应:消石灰和二氧化硫在适当的温度和湿度条件下发生水合反应,生成石膏半水合物。
3)结晶:将石膏半水合物放在低温高湿的条件下,进行结晶,形成纯度较高的石膏晶体。
4)脱水干燥:将石膏晶体通过脱水干燥的方式去除余留的水分,最终得到石膏板或石膏粉。
3. 石膏碱法石膏碱法是利用氨水或碱性废液与含二氧化硫废气中的二氧化硫反应生成硫酸铵,并通过浓缩、结晶等工艺得到脱硫石膏。
具体工艺如下:1)原料准备:将氨水或碱性废液与二氧化硫废气进行混合,使其发生反应。
2)硫酸铵制备:将氨水或碱性废液中的氨与二氧化硫反应生成硫酸铵溶液。
3)浓缩:将硫酸铵溶液进行浓缩,使其达到一定浓度。
利用脱硫石膏年产万吨建筑石膏粉生产线

利用脱硫石膏年产30万吨建筑石膏粉生产线工艺方案(回转烘干机+沸腾流化床)1.工艺要求:a.生产能力:≥42吨/小时β型半水石膏粉。
?b.产品质量:按《建筑石膏》国标执行,满足纸面石膏板用粉要求。
?c.环保要求:粉尘排放浓度应达到GB16297-1996标准要求。
?2.工艺方案:a.煅烧:因为脱硫石膏含有超过10%的游离水,结合国内磷石膏制备建筑石膏粉的成功经验,采用二水石膏预烘干、沸腾流化床煅烧的二步法工艺煅烧建筑石膏粉。
具体为:用装载机将原料从原料堆场送至进料斗,经计量后由皮带输送机送入双筒回转烘干机烘干去除游离水(该处热源为燃煤热风炉),出料后经集料收尘器收料,经提升输送设备送入流化床煅烧(采用导热油锅炉为热源),煅烧完毕后送入球磨机进行研磨改性和冷却,然后送入熟粉料仓备用。
b.环保:烘干、油炉、煅烧系统的烟气尾气与炒制沸腾炉的热气采用旋风(多管)加电除尘(详见工艺布置图),?3.工艺布置图:附后4.主要设备介绍:A、烘干系统(回转烘干机):a、该设备采用多区段和独特的中心扬料板,可有效增加物料和热介质的接触面积,大大提高了烘干效率,起到了节能、降耗的作用。
另外因为该设备主体是建材行业标准设备,所以在技术、维修、备件维护等方面都很方便,是一台非常理想的烘干干燥设备。
b、燃烧炉:沸腾燃煤热风炉。
B、炒制沸腾炉:沸腾炉煅烧的特点:(1)设备小巧,生产能力大沸腾炉生产能力的大小实质上由热源通过加热器壁传递给物料的热量多少来决定。
沸腾炉由于物料实现了彻底的流态化,因此炉内不需要安装搅拌设备。
在炉内就可以高密度地安装很多加热管,因此尺寸不大的炉子就可以有非常大的传热面积。
另外,沸腾炉采用的热源为饱和蒸气或载热油,其传热系数比热烟气为热源的传热系数高出一个数量级。
从传热方程式就可看出,由于传热系数和传热面积都较大,总传热量也就大。
(2)结构简单,不易损坏由于物料实现了流态化,炉子就不需要有转动的部件,投产后也几乎不需要维修保养。
脱硫石膏生产工艺

脱硫石膏生产工艺脱硫石膏是一种石膏产品,广泛应用于建筑材料、农田改良和环境治理等领域。
其生产工艺主要包括以下几个步骤:原料准备、石膏制备、澄清、过滤、石膏干燥和包装。
下面将对这些步骤进行详细介绍。
首先,原料准备是脱硫石膏生产的第一步。
原料主要包括石膏和脱硫废水。
石膏是从矿石中提取的石膏矿石,经过破碎、磨粉和筛分等工艺处理得到。
而脱硫废水则是指含有二氧化硫和其他污染物的废水,通常来自于火力发电厂和化工厂的排放。
接下来,石膏制备是将石膏和脱硫废水通过混合和搅拌等工艺制备成脱硫石膏的过程。
在制备过程中,需要保证石膏与脱硫废水的比例恰当,并加入一定的助剂以促进反应。
通过反应,二氧化硫被氧化生成硫酸根离子和水,从而形成脱硫石膏。
制备完成后,需要进行澄清和过滤等工艺。
澄清过程是将混合物静置一段时间,使其中的悬浮物和杂质沉淀下来。
过滤过程则是将澄清液中的悬浮物通过过滤器进行过滤,进一步提高脱硫石膏的纯度和质量。
过滤完成后,需要对脱硫石膏进行干燥。
干燥过程可以采用自然干燥或机械干燥的方式。
自然干燥是将脱硫石膏摊放在通风良好的场地上,利用自然气候条件进行干燥。
机械干燥则是通过干燥设备对脱硫石膏进行加热和干燥,以提高干燥速度和效果。
最后,将干燥后的脱硫石膏进行包装。
包装过程主要是将脱硫石膏装入袋子或其他容器中,并加入标签和说明书等信息。
包装完成后,脱硫石膏可以进行储存和销售。
综上所述,脱硫石膏生产工艺主要包括原料准备、石膏制备、澄清、过滤、石膏干燥和包装等步骤。
通过这些工艺的处理,可以生产出质量稳定的脱硫石膏产品,以满足不同领域的需求。
脱硫石膏生产工艺

脱硫石膏生产工艺概述:脱硫石膏是一种重要的环保材料,广泛应用于建筑材料、水泥制造、农业等领域。
其生产工艺主要包括石膏矿石的选矿、石膏脱硫、石膏纯化、石膏干燥等步骤。
本文将详细介绍脱硫石膏的生产工艺。
一、石膏矿石的选矿脱硫石膏的生产首先需要从石膏矿石中提取出纯净的石膏。
石膏矿石一般通过矿山开采获取,然后经过破碎、研磨等工艺处理,将石膏矿石变成适合后续工艺处理的石膏粉末。
二、石膏脱硫石膏脱硫是整个生产工艺的核心步骤,通过脱硫工艺可以将含硫物质从石膏中去除,提高石膏的纯度。
常用的脱硫方法包括湿法脱硫、干法脱硫和半干法脱硫等。
1. 湿法脱硫:湿法脱硫是将石膏与脱硫剂进行反应,采用水作为媒介,通过化学反应将石膏中的硫化物转化为易溶于水的硫酸盐。
常见的脱硫剂有石灰石、氧化钙等。
湿法脱硫工艺简单易行,但耗水量较大。
2. 干法脱硫:干法脱硫是将石膏与脱硫剂进行高温煅烧,采用物理吸附和化学反应的方式去除石膏中的硫化物。
常见的脱硫剂有活性炭、活性白土等。
干法脱硫工艺适用于水资源紧缺的地区,但能耗较高。
3. 半干法脱硫:半干法脱硫是湿法和干法脱硫的结合,将湿法脱硫和干法脱硫的优点相结合,以降低耗水量和能耗。
该工艺将石膏颗粒喷洒脱硫剂,通过石膏颗粒表面水分的蒸发和脱硫剂的吸附作用,实现石膏脱硫。
三、石膏纯化脱硫后的石膏中仍然含有一定的杂质,需要进行纯化处理。
石膏纯化主要通过洗涤、沉淀、过滤等工艺,去除石膏中的杂质,提高石膏的纯度。
洗涤过程中,可以使用水进行多次冲洗,以将杂质从石膏中洗掉。
沉淀和过滤则可以将石膏中的悬浮物和固体颗粒分离出来。
四、石膏干燥纯化后的石膏含有一定的水分,需要进行干燥处理。
石膏干燥可以采用自然干燥或机械干燥的方式。
自然干燥是将石膏晾晒在通风良好的地方,使其逐渐失去水分。
机械干燥则是通过干燥设备,如烘干机、流化床干燥机等,将石膏快速干燥,提高生产效率。
五、石膏产品制备经过干燥处理的石膏可以用于制备各种石膏产品。
脱硫石膏生产工艺技术及装备

脱硫石膏生产工艺技术及装备工艺方案对比与设备确定根据电厂的热源情况,可应用的热源为低温蒸汽,其蒸汽温度为250℃—320℃,压力为1.3MPa,通过减温后可转变为1.3MPa的饱和蒸汽作为本项目的热源。
依据热源的确定,从而确定由硫石膏生产建筑石膏的工艺与设备方案。
硫石膏是化学石膏一类,表面含水一般在≥10%左右,粒度小于天然石膏,分子结合力较小,表面能较高,目前在国内还没有适用于硫石膏生产建筑石膏的专用设备,简单采取传统的天然石膏煅烧方式和工艺,难以保证产品质量的稳定性,并且易形成操作环境的污染。
在确定热源方式条件后,采取干燥与煅烧二步法工艺,将干燥与煅烧分二步工艺进行,有利于硫石膏生产建筑石膏。
在二步法工艺中干燥与煅烧设备选型对比如下:5.1.1 干燥设备选型对比依据电厂情况选取蒸汽为热源,由于脱硫石膏含有表面水,物料表观较松散,适用于硫石膏干燥的设备主要有管束内置式回转干燥机,沸腾流态化干燥机,斯德(气流)干燥机。
管束内置式回转干燥机是一种间接加热传导式干燥方式,可适用于硫石膏干燥。
存在的主要问题是设备占地面积大,维修费用高,管束表面易粘料,干燥效率低,窑头、窑尾密封不严,易漏料,形成粉尘污染,运行中电耗高,一次性投资大,是逐步淘汰产品。
沸腾流态化干燥机仅适用于含水量较低的物料干燥,如用于硫石膏干燥易造成沟流或死床影响生产。
斯德(气流)干燥机属于气流干燥一类干燥机。
气流干燥机具有占地面积小,系统微负压操作作业,环境无污染,干燥效率高。
斯德(气流)干燥机具有上述特点同时带有分散、打散功能,占地空间面积低于普通气流干燥机(仅是回转窑干燥1/3占地面积)。
采用自动化操作,适用于硫石膏干燥,是国内外一种先进干燥方式(见干燥对比附表)。
综上所述,采用斯德(气流)干燥机、采用蒸汽换热为热源是一种可靠先进的干燥方式,目前在国内有多家类似物料干燥设备在应用。
5.1.2 煅烧设备选型对比依据电厂情况选用蒸汽为煅烧热源。
脱硫石膏的工艺流程

脱硫石膏的工艺流程脱硫石膏是一种重要的工业原料,广泛应用于建筑材料、农业、环保等领域。
脱硫石膏的生产过程主要是通过燃煤或燃油等燃料进行燃烧产生的废气中的二氧化硫进行脱除,从而得到的一种固体废物。
下面我们将详细介绍脱硫石膏的工艺流程。
1. 石膏熔融工艺。
石膏熔融工艺是一种常用的脱硫石膏生产工艺。
首先,将石膏粉末加入熔融炉中,通过高温加热使石膏熔化成液态。
在熔融炉中,加入适量的矿物质和添加剂,如石灰石、氢氧化钙等,用于调节石膏的成分和性质。
经过一定时间的熔融,石膏液体逐渐冷却凝固成块状,即可得到脱硫石膏。
2. 湿法石膏脱硫工艺。
湿法石膏脱硫工艺是另一种常用的生产工艺。
首先,将石膏粉末与水混合,形成石膏浆料。
然后将石膏浆料加入脱硫反应器中,同时向反应器中通入含有二氧化硫的废气。
在反应器中,二氧化硫与石膏浆料发生化学反应,生成硫酸钙。
经过一定时间的反应,硫酸钙沉淀在反应器中,即可得到脱硫石膏。
3. 干法石膏脱硫工艺。
干法石膏脱硫工艺是一种较为节能的生产工艺。
首先,将石膏粉末加入干法脱硫设备中,通过喷射或气流等方式将含有二氧化硫的废气与石膏粉末充分接触。
在接触过程中,二氧化硫被吸附到石膏粉末表面,形成硫化钙。
经过一定时间的吸附,硫化钙逐渐沉淀,即可得到脱硫石膏。
4. 石膏干燥工艺。
无论是采用熔融工艺、湿法工艺还是干法工艺,得到的脱硫石膏都需要进行干燥处理。
首先,将脱硫石膏块状物料送入干燥设备中,通过加热和通风等方式将石膏中的水分蒸发。
经过一定时间的干燥,脱硫石膏中的水分得到蒸发,即可得到干燥的脱硫石膏。
5. 石膏粉碎工艺。
最后一步是对干燥的脱硫石膏进行粉碎处理。
首先,将干燥的脱硫石膏送入破碎设备中,通过冲击、挤压等方式将块状石膏粉碎成粉末状。
经过粉碎处理,即可得到成品的脱硫石膏粉末。
通过以上工艺流程,我们可以得到成品的脱硫石膏。
脱硫石膏在建筑材料、农业、环保等领域有着广泛的应用,对于减少二氧化硫等污染物的排放,保护环境具有重要的意义。
脱硫石膏生产工艺
脱硫石膏生产工艺脱硫石膏生产工艺是一种将煤矿、火电厂和冶金厂等工业废气中的二氧化硫转化为有用资源的技术。
通过这种工艺,可以减少大气污染物排放,同时生产出具有一定经济价值的脱硫石膏。
脱硫石膏生产工艺的主要步骤包括废气收集、石膏生成、石膏浓缩和石膏脱水等环节。
废气收集是整个工艺的第一步。
煤矿、火电厂和冶金厂等工业生产过程中产生的废气中含有二氧化硫,需要通过专门的收集设备进行收集。
常见的废气收集设备包括静电除尘器、湿式除尘器、喷淋塔和吸收塔等。
这些设备能够有效地将废气中的二氧化硫捕集下来。
石膏生成是脱硫石膏生产工艺的关键步骤之一。
收集到的废气中的二氧化硫经过一系列的反应转化为石膏。
常见的石膏生成方式有湿法石膏生成和干法石膏生成两种。
湿法石膏生成是指将废气中的二氧化硫通过吸收塔中的吸收液吸收,并与吸收液中的氧化剂进行反应生成石膏。
这种方法的优点是反应速度快、转化效率高,但需要消耗大量的吸收液和氧化剂。
干法石膏生成是指将废气中的二氧化硫与一定量的氧气和水蒸气在高温条件下进行反应生成石膏。
这种方法的优点是工艺简单、设备投资少,但反应速度较慢,转化效率较低。
石膏浓缩是将生成的石膏浆液进行浓缩处理,去除其中的水分,提高石膏的固体含量。
常见的石膏浓缩设备有真空过滤机、压滤机和离心机等。
通过这些设备,可以将石膏浆液中的水分含量从80%左右降低到40%以下。
石膏脱水是将浓缩后的石膏进一步去除水分,使其成为具有一定固体含量的石膏产品。
常见的石膏脱水设备有矿用离心机、压滤机和烘干机等。
通过这些设备,可以将石膏中的水分含量进一步降低,提高石膏的固体含量。
脱硫石膏生产工艺的应用前景广阔。
脱硫石膏作为一种有用资源,可以应用于建材、水泥、石膏板和石膏制品等行业。
同时,脱硫石膏还可以作为土壤改良剂、污水处理剂和废水处理剂等。
通过合理利用脱硫石膏,可以实现废气资源化和循环利用,减少环境污染,促进可持续发展。
脱硫石膏生产工艺是一种将工业废气中的二氧化硫转化为有用资源的技术。
脱硫石膏粉生产工艺
脱硫石膏粉生产工艺
脱硫石膏粉是一种用于燃煤电厂烟气脱硫后产生的石膏废渣的再利用产品。
脱硫石膏粉生产工艺主要包括石膏破碎、石膏磨碎、石膏干燥、石膏粉碎和石膏分级等环节。
首先,将石膏废渣经过破碎设备破碎成小块,然后进入磨碎设备进行粉碎。
破碎和磨碎的目的是将石膏废渣粉碎成所需的粒度,提高后续处理的效率。
接下来,将粉碎后的石膏废渣送入干燥设备进行干燥处理。
干燥的目的是去除石膏废渣中的水分,提高石膏粉的质量和稳定性,同时也便于后续的粉碎和分级。
干燥后的石膏废渣进入粉碎设备进行细碎处理。
细碎的目的是进一步将石膏废渣粉碎成所需的细度,便于后续的分级处理。
最后,将细碎后的石膏废渣送入分级设备进行分级处理。
分级的目的是根据不同的粒度要求将石膏废渣分成不同的粒度级别,以满足不同应用领域对石膏粉的要求。
整个脱硫石膏粉生产工艺需要依靠多台设备进行连续操作,同时还需要控制好各个环节的参数,以确保石膏废渣的充分利用和石膏粉的质量稳定。
脱硫石膏粉的生产工艺可以实现石膏废渣的重复利用,减少环境污染,同时也满足了石膏粉在建筑材料、冶金行业等领域的需求,具有重要的经济和社会意义。
脱硫石膏加工成石膏粉方案
脱硫石膏加工成石膏粉方案一、硫石膏及脱其形成:1. 脱硫石膏又称排烟脱硫石膏、硫石膏,是对含硫燃料(煤、油等)燃烧后产生的烟气进行脱硫净化处理后,得到的工业副产石膏。
其定义为:脱硫石膏是来自排烟脱硫工业,颗粒细小、品位高的湿态二水硫酸钙晶体。
2.脱硫石膏的形成过程:将通过除尘处理后的烟气导入吸收器中,细石灰石粉与水充分搅拌的料浆,通过喷淋的方式在吸收器中洗涤烟气,与烟气中的二氧化硫反应生成亚硫酸钙,然后通入大量空气强制将其氧化成二水硫酸钙。
从吸收器中出来的石膏悬浮液通过浓缩器和离心器脱水,最终产物为颗粒细小、品位高、残余含水量在5~15%之间的脱硫石膏,也叫二水石膏或生石膏。
这种人工制备的二水石膏,主要成分和天然石膏一样,其物理、化学特征和天然石膏具有共同的规律。
国内电厂采用湿式石灰/石灰石——石膏法脱硫工艺,开始于上世纪90年代,且近些年来,规划投资脱硫的工程越来越多。
在我国,具有一定代表性的就是国华北京热电分公司,它是引进世界上先进的德国湿法脱硫技术,在对电厂烟气脱硫的过程中,每年不但消纳了1.15万吨的二氧化硫,还产生了纯度高达95%的脱硫石膏,为净化首都环境作出了突出的贡献,同时充分利用脱硫石膏,生产出符合国家环保要求的新型脱硫石膏砌块。
二、脱硫石膏的用途:脱硫石膏的应用主流是把它烘干后作为水泥的缓凝剂使用;或锻烧成β型半水石膏,用于制造石膏板、石膏砌块、粉刷石膏。
三、脱硫石膏的利用与前景:脱硫石膏在建材行业中应用十分广泛,通过不同手段进行处理,基本上能代替绝大部分用天然石膏生产的建材制品。
国内脱硫石膏的综合处理和应用已起步,利用前景蕴藏着巨大的市场机遇,特别是那些天然石膏缺乏而脱硫石膏资源丰富的经济发达地区,经应用实践证明脱硫石膏是一种品位较高的宝贵资源,它可适合于不同用途的石膏建材制品的生产,处理后的脱硫石膏是一种比天然石膏还要好的胶凝材料。
脱硫石膏通过干燥,脱水处理成为熟石膏,熟石膏按制品可分:浇注石膏,灰泥石膏,陶瓷工业用石膏,铸造工业用石膏,牙料用石膏,骨科绷带医用石膏,煤矿防火加强巷壁用石膏,土壤改良用石膏等等,用量最大的是建筑用熟石膏(建筑石膏)四、脱硫石膏煅烧成石膏粉设备:(一)、结构组成:脱硫石膏烘干机简称ZDSG间歇转筒石膏粉炒锅机主要由钢结构机座、炒锅、炒锅内装有扬料和导料装置、滚圈托轮和传动机构组成。
石膏脱硫工艺流程
石膏脱硫工艺流程
石膏脱硫是一种常用的烟气脱硫技术,它通过石膏和烟气中的二氧化硫发生反应,将二氧化硫转化为石膏,并达到减少二氧化硫排放的目的。
下面将介绍一种常用的石膏脱硫工艺流程。
首先,石膏脱硫过程中需准备工艺设备。
包括石膏磨机、脱水设备、石膏脱硫反应器、石膏输送设备等。
这些设备的作用是将石膏从破碎、磨碎到脱水再到输送过程中进行处理。
然后,石膏脱硫过程中需要进行石膏制备。
首先将去除杂质的原料石膏通过破碎、磨碎等工艺步骤制成合适的粒度。
然后将制备好的石膏送到脱水设备进行脱水处理,使其达到一定的干燥程度。
接下来,进入石膏脱硫反应阶段。
在石膏脱硫反应器中,将烟气通过一定的喷淋方式与石膏接触,使二氧化硫与石膏中的钙离子发生反应,生成硫酸钙。
这个过程需要控制好反应器内的温度、压力和喷淋速度等参数,以保证二氧化硫的充分吸收。
最后,脱硫后的石膏通过输送设备运出反应器。
这些石膏可以被用于石膏板的制作,也可以作为建筑材料进行利用。
同时,还可以回收部分石膏用于下一次的脱硫反应。
总结起来,石膏脱硫工艺流程主要包括石膏制备、脱水、脱硫反应和石膏输送等步骤。
通过这一工艺流程,可以将石膏与烟气中的二氧化硫进行反应,达到减少二氧化硫排放的目的,同时也可以利用脱硫后的石膏进行资源回收利用。
这种石膏脱硫
工艺流程在目前的烟气治理中得到广泛应用,有效地保护了环境和人类健康。
- 1、下载文档前请自行甄别文档内容的完整性,平台不提供额外的编辑、内容补充、找答案等附加服务。
- 2、"仅部分预览"的文档,不可在线预览部分如存在完整性等问题,可反馈申请退款(可完整预览的文档不适用该条件!)。
- 3、如文档侵犯您的权益,请联系客服反馈,我们会尽快为您处理(人工客服工作时间:9:00-18:30)。
(3)回转式烘干机。内部按照圆周方向设置多根换热管 道,蒸汽通过换热管道,在窑体的转动下不断接触原料,热量
·102·
第 4 期(总第 216 期)
生产技术■
传递给原料,以达到烘干的目的。优点是生产能力较大,管道 基本不受其他外力作用,不易损坏,故障少,维修费用低;缺 点是投入成本高,占地面积大,物料的温度不容易控制,无搅 拌功能,原料进入设备时粘性较大,容易粘成团,使有效换热 面积变小,蒸发效率低;适用于物料粘性较低的生产线。 2.3 煅烧工序
(1)桨叶烘干机。设备内部轴上密集排列着中空桨叶,蒸 汽通过中空桨叶,使湿物料在桨叶的搅动下,与热表面充分 接触,从而与石膏换热干燥。优点是热量利用率高,设备结构 紧凑,占地面积小,投资低;缺点是浆叶在滚筒旋转时受力, 容易磨损开裂,维护维修量较大,物料粘性较强,若不及时清 理的情况,会影响干燥效果和设备干燥能力,产能较低;适用 于单体产能要求不高的生产线。
目前脱硫石膏生产建筑石膏粉主要以蒸汽、天然气、煤 等为热源。其中以煤炭为最便宜,但污染严重;天然气较清 洁,但成本较高;蒸汽清洁又经济,但周边需有供热电厂。由 于脱硫石膏主要是由电厂烟气脱硫得到的副产品,紧邻电 厂,所以主要选择蒸汽作为热源。以蒸汽为热源的生产工艺 分为一步法和二步法两类。一步法是将石膏的干燥、煅烧两 个工艺过程在一台装备中完成。该工艺生产适用于规模小、 附着水含量多在 10%以内的脱硫石膏。生产工艺流程具有简 单、热损失小、投资成本少等特点;二步法是把石膏的干燥、 煅烧两个工艺过程分别在二台装备中完成。烘干 + 煅烧的二 步法模式,对于采用蒸汽作为热源、大规模(年单机产能大于 10 万 t)及高含水量(附着水含量大于 10%)的生产线,具有较 明显的优势。以下主要对脱硫石膏蒸汽二步法生产建筑石膏 粉工艺进行简介。
(2)均化。由于同一电厂的脱硫石膏,其各批次的品质也
不尽相同,这样就造成脱硫石膏原料质量的不均匀性。原料 质量的不均匀性给石膏煅烧工艺控制及产品质量的稳定性 带来了非常大的困难,因此脱硫石膏原料煅烧前必须进行均 化处理。目前主要有两种处理方式:①根据场地情况,必须有 足够大的原料均化堆场,在原料进场时每批次采用纵向堆 料,取料时在垂直的纵向方向的横截面上取料;②对堆场内 的原料进行多点取样分析,根据分析的结果进行搭配取料, 混合使用,以保证原料水分及成分的均匀性。 2.2 烘干工序
(1)煅烧温度的控制。煅烧工艺是决定建筑石膏性能及 品质的关键因素,若脱硫石膏煅烧温度过低(欠烧),则二水硫 酸钙含量会较高,产品质量下降;若煅烧温度过高(过烧),则 硫酸钙含量会较大。结合实验表明,煅烧温度在 105℃左右 时,脱硫石膏结晶水开始脱水;加热到 170~190℃,会迅速脱 掉 1.5 个结晶水,形成半水石膏,此时石膏晶体发育完整、生 长致密,在凝结时间、标准稠度及强度等方面品质最佳;若加 热到 200~220℃,半水石膏继续脱水,转变为Ⅲ型无水石膏, 转化率下降。选定不同的煅烧温度分别对脱硫石膏进行煅 烧,及时对设备温度和压力等参数进行调节,可以使建筑石 膏粉产品质量达到不同品质指标的需求。
1 概述
脱硫石膏主要成分为二水硫酸钙,是采用石灰 - 石灰石 回收燃煤烟气中的二氧化硫后得到的工业副产品。脱硫石膏 通过烘干、煅烧、陈化、改性等,使二水石膏脱水分解,脱掉 1.5 个结晶水,得到的以 β 半水石膏为主要成分的产品,即为建 筑石膏粉。随着石膏产业的发展和进步,各行各业对石膏粉 的需求越来越大,对质量要求也越来越高,石膏粉的生产制 造工艺也在不断进步。
■膏粉工艺简介
蔡彦煌 (福能环保新材(泉州)有限责任公司 ,福建 石狮 362700)
摘 要 以蒸汽作为热源采用二步法为例,对利用脱硫石膏煅烧建筑石膏粉生产环节中的预处理、上料、烘干、煅 烧、陈化冷却、改性、包装等系统进行了阐述。
关键词 脱硫石膏;蒸汽二步法:建筑石膏粉;烘干;煅烧
2 工艺流程简介
2.1 原料品质及均化 (1)原料品质。脱硫石膏主要品质要求:湿度<15%、pH
值为 6~9、纯度(二水硫酸钙)>90%、C(l 水溶性)<0.1%、白 度>80%、MgO(水溶性)<0.021%、烟灰<1.6%、Al2O3<0. 2%、 SiO2<1%、CaCO3<3%。其中氯离子作为脱硫石膏中主要的 杂质元素,对脱硫石膏及其制品性能的影响最大。由于氯离 子会与钙离子结合形成结晶水合物,其吸湿性很强,造成脱 硫石膏的附着水含量高,其深加工过程中脱水难度增大;且 氯离子具有腐蚀性,对后期石膏制品的影响也较大。
(2)管束烘干机。在壳体内设置蒸汽换热管道,电机通过 传动装置带动管束外周抄板,把物料抄起,运行时壳体不动, 并搅拌壳体内物料换热及运动。优点是动力消耗低,热效率 高,产能大,换热管在滚筒旋转时不承受扭矩,管道焊缝开 裂、泄漏的情况较少;缺点是对于水分高、易粘的物料,壳体 粘料后对管道的旋转产生很大的阻力,易造成轴损坏或管道 变形,粘料后清理较困难,容易发生堵磨糊磨事故;适用于物 料粘性较低的生产线。
(2)煅烧设备的选择。煅烧设备一直是影响建筑石膏制 品质量和应用的主要因素,目前生产常用的煅烧设备有炒 锅、回转窑、沸腾炉等。①炒锅。优点是物料温度容易控制、产 品均匀、结构简单;缺点是热效率较低,设备维护费用高,工 作环境较差。②回转窑。优点是可连续进料、连续出料,能适 应原料粒度的不同变化,运转稳定,可靠性高;缺点是占地面 积较大、流程长、初期投资较大、物料的温度不容易控制,煅 烧的产品质量不容易控制,能耗较高。③沸腾炉。优点是有效 换热面积大、操作控制准确。无机械搅拌装置和采用内管换 热,使设备易于维修;缺点是物料易粘壁、堵塞,需经常清理。 适用于过热蒸汽作为热源的生产线。