基于PLC的流量控制系统完整版
基于PLC的流量监控系统设计说明
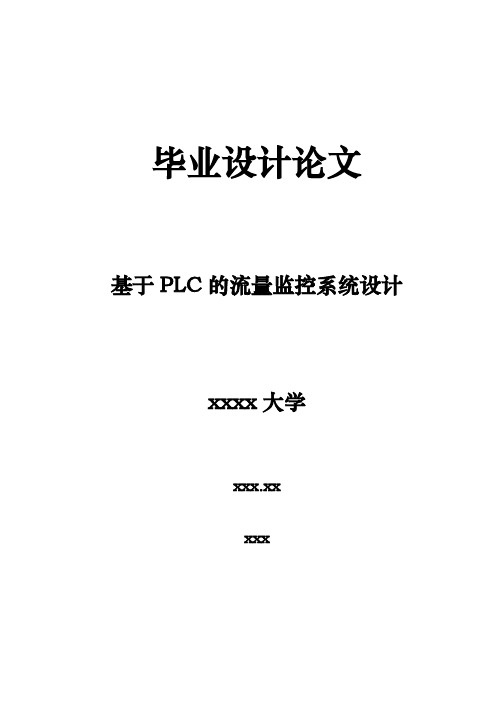
毕业设计论文基于PLC的流量监控系统设计xxxx大学xxx.xxxxx目录1 选题背景2方案论证3 开发设计过程4 结果分析5 总结参考文献致谢附录A:MAIN主程序:附录B:CPU技术规范附录C :EM 235模拟量输入,输出和组合模块的技术规范基于PLC的流量监控系统设计1 选题背景本毕业设计课题来自实验室建设。
目的是利用PLC来实现过程控制。
目前,PLC使用范围可覆盖从替代继电器的简单控制到更复杂的自动化控制。
应用领域极为广泛,覆盖所有与自动检测,自动化控制有关的工业及民用领域,包括各种机床、机械、电力设施、民用设施、环境保护设备等等。
PLC通过模拟量I/O模块,实现模拟量与数字量之间的A/D、D/A转换,并对模拟量进行闭环PID控制。
用MCGS组态软件组态配置工业控制监控系统,对数据进行实时监控。
2方案论证本毕业设计原理是利用扩展模块EM235(AI4/AQ1*12位)进行数据采集,然后把采集到的数据利用程序进行工程量转换,给定量与输入量相减得出偏换,送到执行器,从而构成的是单闭环控制。
采用增量式PID,具有以下优点:(1)增量算法控制误动作影响小。
(2)增量算法控制易于实现手动/自动无扰动切换。
(3)不产生积分失控,易获得较好的调节品质。
在实际应用中,在以步进电机或多圈电位器作执行器件的系统中,则采用增量式PID算法。
MCGS即"监视与控制通用系统",英文全称为Monitor and Control Generated System。
MCGS是为工业过程控制和实时监测领域服务的通用计算机系统软件,具有功能完善、操作简便、可视性好、可维护性强的突出特点。
MCGS 工控组态软件是一套32位工控组态软件,集流程控制、数据采集、设备控制与输出数据与曲线等诸多强大功能于一身,广泛应用于石油、电力、化工、钢铁、矿山、冶金、机械等多种工程领域。
所以用MCGS作为本次毕业设计的开发软件是很有必要的。
流量的PLC控制系统设计
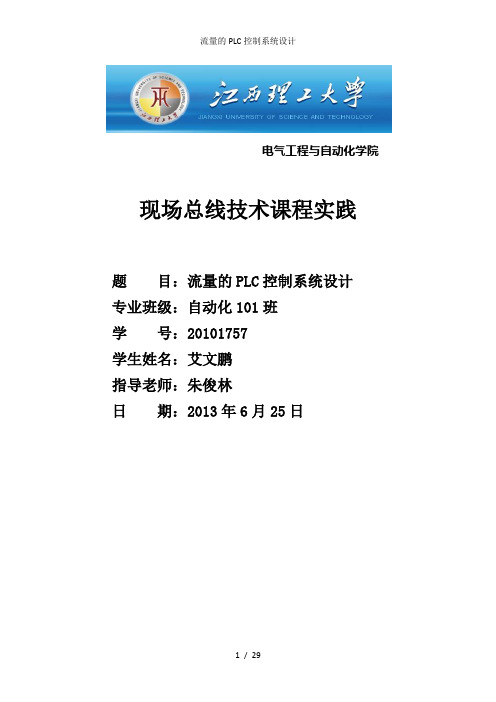
电气工程与自动化学院现场总线技术课程实践题目:流量的PLC控制系统设计专业班级:自动化101班学号:20101757学生姓名:艾文鹏指导老师:朱俊林日期:2013年6月25日流量控制是过程控制系统的一个关键。
采用工业控制计算机, 根据专家系统确定最优工况的各试验流量, 通过AD采集模块接收流量计传感器的数据, 对采集的相应数据进行处理分析并向PLC发出指令, PLC采用PI控制方法, 通过PI控制的参数设定及自整定。
根据PI调节的输出与输入的偏差成正比, 还与偏差对时间的积分成正比, 消除了控制过程中产生的静差, 实现了流量闭环调节的精确控制。
设计了监控软件、PLC软件、PLC与工控计算机的通信软件, 实现了流量的控制、数据采集和处理。
试验表明, PI控制方法对流量的调节具有较好的稳定性和动态特性。
讨论计算机水流量PLC 监控系统。
选用电磁流量计和经典文丘里管流量计系统。
结合杰控组态软件制作出人机界面,把组态与PLC 进行连接,组态与PLC 间不断进行交换数据,通过组态画面实时反映现场流量的实时变化情况,然后定义与组态王实时数据库中变量相对应的监控系统中的设备,通过PLC 采集设备的数据,并通过通信接口把数据传输给计算机。
关键词:流量计;PLC ;人机界面;控制系统; 流量调节; PI控制摘要 (2)第一章引言 (4)1.1 设计目的 (4)1.2 设计主要过程 (4)1.3 设计主要内容 (5)1.3.1 硬件模块设计 (5)1.3.2 组态软件的应用设计 (5)1.3.3 基于STEP-7的程序设计 (5)1.3.4 综合设计 (6)第二章系统的硬件选型 (7)2.1 硬件选型 (7)2.2 选型的步骤 (8)2.3 选型的结果 (8)2.4 选型技术参数 (9)第三章系统的硬件结构设计 (11)3.1 整体结构设计 (11)3.2 硬件连接图 (11)3.3 系统I/O分配表 (12)3.4 硬件组态和变频器参数 (13)3.4.1 硬件组态配置 (13)3.4.2 变频器参数设定 (14)第四章系统软件设计 (15)4.1 软件设计整体构架 (15)4.1.1 杰控组态软件设计 (15)4.1.2 组态设计 (16)4.1.3 PLC程序设计流程图 (22)4.1.4 程序设计梯形图 (22)4.2 问题及其解决方法 (25)4.3 调试过程及方法 (25)4.4 软件调试结果 (26)第五章设计总结 (28)参考文献 (29)第一章引言1.1 设计目的本次课程设计的目的是采用西门子S7-300系列PLC来实现过程控制系统的设计。
基于PLC和组态王的流量PID控制

基于PLC和组态王的流量PID控制系统基于PLC和组态王的流量PID控制系统[摘要] 随着我国社会经济的发展,人们生活水平的不断提高,供水系统的建设是其中的一个重要方面,供水的经济性、可靠性、稳定性直接影响到目前人们的正常生活和工作.传统的供水方式普遍存在效率低、可靠性差、自动化程度不高等缺点,难以满足当前经济生活的需要。
本文针对这些问题主要设计了一套由PLC、变频器、等主要设备构成的变频恒流供水及其监控系统。
可以有效地解决传统供水方式中存在的问题,增强了系统的可靠性。
关键词:流量控制 PLC 组态王 PID控制Abstract:With the development of our social economy, the continuous improvement of people’s living standard, the construction of the water supply system is one of the important aspects of water supply of the economy,reliability and stability directly affect the current people’s normal life and work. Traditional way of water supply is widespread, low efficiency,poor reliability and high degree of automation is not weakness,it is difficult to meet the needs of the current economic life. Aiming at these problems mainly devised a composed of PLC,inverter, the main equipment such as variable frequency constant current supply and its monitoring and control system. Can effectively solve the problems existing in the traditional way of water supply, enhanced the reliability of the system.Key words: Flow control PLC King view PID control1.课题要求(1).总体控制要求:可以设计一流量PID控制系统,通过西门子PLC的DA输出,控制变频器频率,可使流量处于一个稳定状态。
PLC在流量控制系统中的应用案例

PLC在流量控制系统中的应用案例流量控制系统是自动化控制中的一个重要应用领域,可以应用于水处理、工业生产、环保等诸多领域。
PLC(可编程逻辑控制器)因其在工业自动化中的功能,特别是对数字和模拟输入/输出操作的能力,成为了流量控制系统中最重要的控制器之一。
本文将探讨PLC在流量控制系统中的应用案例。
一、PLC控制阀门的开闭PLC通过控制流量阀门的开闭,实现流量控制系统中流量的准确控制。
PLC控制阀门的开闭,需要对阀门位置进行反馈控制,即需要在PLC中安装反馈传感器,以检测阀门的位置。
在阀门的开关过程中,PLC可以根据预先设定的开启/关闭时间、阀门的旋转角度等参数实现对阀门的准确控制,从而实现流量控制。
二、PLC实现PID控制PID控制是一种用于工业自动控制中的一种自适应控制方法,其基本原理是按比例调节、积分时间和微调时间来调节控制器的输出,实现对被控制物(例如流量阀门或流量传感器)的精确控制。
传统的PID控制需要使用独立的PID控制器,为了实现在线程序修改,需要对现场的设备进行频繁的调整。
而PLC可以集成PID算法并在线实时调整参数,使控制系统更加智能化,大大简化了控制系统的维护。
三、PLC控制流量传感器流量传感器是流量控制系统中最重要的感应装置之一,可以实现对流量的实时监测。
PLC可以通过传感器检测实时流量信号并将其反馈给PLC,PLC再根据预设的控制程序进行反馈,从而实现精确控制。
同时,PLC还可以使用数据采集卡将流量传感器的信号转换为数字信号,以便于对数据进行存储、处理和分析。
四、PLC实现流量的计算PLC可以通过编写测量算法,将传感器的数字信号转换为流量值,并将其储存在控制器内存中。
此外,PLC还可以将流量数据转输到上位机等设备中,以便于进行数据存储、处理和报告分析。
PLC在流量控制系统中的应用模式基本类似,但实际应用却因环境和行业不同,而存在着各自的应用要求。
在任何情况下,PLC的优势在于其灵活可塑性,可根据不同环境的要求进行定制。
基于PLC的流量与压力控制系统的研究运用

基于PLC的流量与压力控制系统的研究运用摘要随着科技的不断发展,PLC控制系统已经成为工业控制领域中最为常见和重要的控制方式之一。
本文主要介绍了基于PLC的流量与压力控制系统的研究运用。
首先对PLC技术进行了简要介绍,随后对流量与压力控制系统的原理与结构进行了详细分析,最后通过实验验证了基于PLC的流量与压力控制系统的可行性和实用性。
关键词:PLC;流量控制;压力控制;控制系统一、引言PLC是可编程逻辑控制器的缩写,它是一种专门用于工业控制领域的电子设备。
在工业生产中,PLC可以完成逻辑控制和运行控制等任务,通过其高度的灵活性和可编程性,能够满足不同工业场景的需求。
流量与压力是工业生产中重要的物理参数,对于保证生产过程的稳定性和质量具有至关重要的作用。
基于PLC的流量与压力控制系统的研究和运用具有很大的现实意义。
二、PLC技术的特点PLC是一种硬件可编程控制器,它的工作原理是通过控制不同的逻辑元件,如继电器、计数器、定时器等,来实现对工业生产过程的控制。
PLC具有以下几个特点:1. 可编程性强:PLC可以通过编程灵活地修改和调整控制逻辑,适应不同的生产需求;2. 稳定可靠:PLC的硬件结构稳定,能够在恶劣的工作环境下正常运行;3. 易于维护:PLC的模块化设计和可编程特性,使得故障检测和维护更加方便。
基于以上特点,PLC在工业控制领域得到了广泛的应用,成为了工业自动化的重要组成部分。
三、流量与压力控制系统的原理与结构流量与压力是工业生产中常见的控制对象,控制系统的主要目标是实现对流体的流量和压力进行精确的控制。
流量与压力控制系统的结构包括传感器、执行元件、控制器和执行装置等组成。
1. 传感器:传感器用于对流体的流量和压力进行检测和监控,将采集到的信息反馈给控制器;2. 控制器:控制器接收传感器反馈的信息,并根据预设的控制逻辑计算出控制命令,向执行装置发出控制信号;3. 执行装置:执行装置根据控制命令对流量阀门和压力阀门进行控制,调整流体的流量和压力。
基于S7-300PLC流量前馈反馈闭环过程控制系统

目录1引言 (1)2 基于S7-300PLC流量前馈/反馈闭环过程控制系统硬件方案计 (2)2.1流量前馈/反馈闭环系统硬件系成 (2)2.2流量前馈/反馈闭环系统硬件系统电气接线图设计 (3)3 S7-300PLC流量前馈/反馈闭环过程控制系统设计 (3)3.1流量前馈/反馈闭环系统控制原理 (3)3.2流量前馈/反馈闭环系统PLC硬件组态论述 (3)3.3流量前馈/反馈闭环系统控制程序流程图论述 (5)3.4流量前馈/反馈闭环系统控制程序功能设计 (6)4流量前馈/反馈闭环系统上位监控系统设计 (8)4.1 S7-300与WINCC建立通讯连接 (8)4.2流量前馈/反馈闭环系统数据词典论述 (8)4.3流量前馈/反馈闭环系统工艺图形组态 (9)4.4流量前馈/反馈闭环系统历史趋势组态 (10)4.5流量前馈/反馈闭环系统实时趋势组态 (11)4.6流量前馈/反馈闭环系统数据报表组态 (12)5 流量前馈/反馈闭环系统调试及结果分析 (12)5.1系统调试及结果分析 (12)5.2结果分析与总结 (13)结束语 (14)附录:带功能注释的源程序 (15)1引言设计S7-300PLC流量前馈/反馈闭环过程控制系统,实现S7-300作为主站控制器,主从站通过PROFIBUS-DP 实现通讯连接,实现主-从站的数接收与发送。
主程序OB1功能:系统启动、停止和复位:定时中断子程序OB35,每100ms 进入中断程序一次,通过功能块FC105,FC106 处理模拟量数字量间转换,采用FB41作为PID模块。
设计一个手动输出量LMN的控制器,控制电动执行器阀门开度为70%,提供流量2前馈信号。
反馈控制器设计:反馈控制器为流量内给定量700升,整定PID参数、量程上/下限、过程量采集、控制量输出等功能。
死区设定为5%。
采用FC105块实现实时读取模拟量SM331模块的流量反馈量,并进行流量物理量刻度转换,送入PID木块FB41的过程量输入端通过循环中断,定时用FB41的PID算法功能块,实时计算控制量LMN输出采用FC106块把PID模块输出的控制量转换为标准的数字量,送入模拟量输出模块SM332,作为电动机执行器输入信号,来控制阀门开度数据块DB定义参数,并作为背景数据存储系统有总启动、停止按钮操作功能同时,系统要求无超调量,稳态误差3%,加前馈扰动能克服采用WICC上位监控软件,设计出流量前馈/反馈的上位机监控系统,包括建立通信、数据变量组态、工艺图形组态、数据组态与显示、趋势组态与显示、报表组态与显示等功能。
基于PLC温度流量和压力控制系统的设计
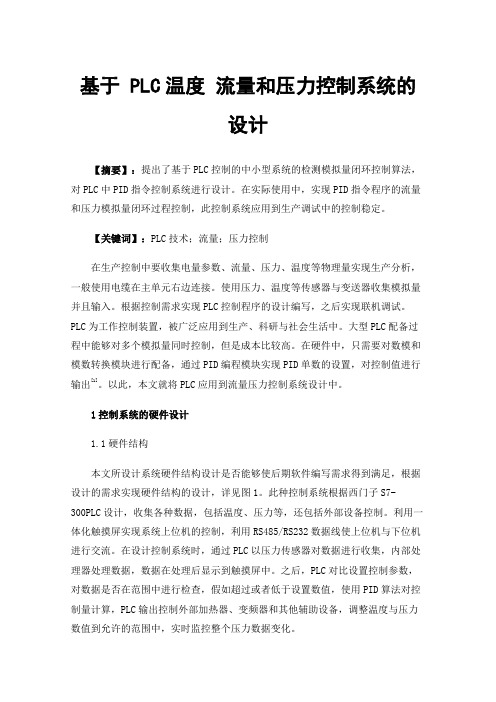
基于 PLC温度流量和压力控制系统的设计【摘要】:提出了基于PLC控制的中小型系统的检测模拟量闭环控制算法,对PLC中PID指令控制系统进行设计。
在实际使用中,实现PID指令程序的流量和压力模拟量闭环过程控制,此控制系统应用到生产调试中的控制稳定。
【关键词】:PLC技术;流量;压力控制在生产控制中要收集电量参数、流量、压力、温度等物理量实现生产分析,一般使用电缆在主单元右边连接。
使用压力、温度等传感器与变送器收集模拟量并且输入。
根据控制需求实现PLC控制程序的设计编写,之后实现联机调试。
PLC为工作控制装置,被广泛应用到生产、科研与社会生活中。
大型PLC配备过程中能够对多个模拟量同时控制,但是成本比较高。
在硬件中,只需要对数模和模数转换模块进行配备,通过PID编程模块实现PID单数的设置,对控制值进行输出[1]。
以此,本文就将PLC应用到流量压力控制系统设计中。
1控制系统的硬件设计1.1硬件结构本文所设计系统硬件结构设计是否能够使后期软件编写需求得到满足,根据设计的需求实现硬件结构的设计,详见图1。
此种控制系统根据西门子S7-300PLC设计,收集各种数据,包括温度、压力等,还包括外部设备控制。
利用一体化触摸屏实现系统上位机的控制,利用RS485/RS232数据线使上位机与下位机进行交流。
在设计控制系统时,通过PLC以压力传感器对数据进行收集,内部处理器处理数据,数据在处理后显示到触摸屏中。
之后,PLC对比设置控制参数,对数据是否在范围中进行检查,假如超过或者低于设置数值,使用PID算法对控制量计算,PLC输出控制外部加热器、变频器和其他辅助设备,调整温度与压力数值到允许的范围中,实时监控整个压力数据变化。
利用S7-300PLC实现设备控制,通过K型压簧式热电偶设计,测量温度范围设计为0-800℃,输出电流设计为4-20mA,使用MIK-P300G压力传感器,输出电流设置为4-20mA,测量范围为-20~300℃,压力范围为0-1KPa。
基于PLC控制的恒流供水系统设计

基于PLC控制的恒流供水系统设计引言本文档旨在介绍基于PLC控制的恒流供水系统的设计。
该系统旨在实现可靠的供水流量控制,并确保恒定的流量输出。
本文将详细描述系统的设计原理、硬件和软件要求,以及系统的工作流程。
设计原理PLC控制PLC(可编程逻辑控制器)是一种可编程的电子设备,用于控制各种工业自动化过程。
在恒流供水系统中,PLC被用来监测和控制流量传感器、电动阀门和泵等设备的运行。
恒流供水原理恒流供水原理基于流量传感器的反馈信号,通过控制电动阀门和泵的工作状态来实现恒定的流量输出。
当流量低于设定值时,PLC控制电动阀门逐渐开启,同时启动泵,以增加流量。
当流量高于设定值时,PLC控制电动阀门逐渐关闭,同时停止泵,以减少流量。
硬件要求恒流供水系统的硬件要求如下:- PLC控制器:用于监测和控制系统的运行。
- 流量传感器:用于测量供水流量。
- 电动阀门:用于控制水流的开启和关闭。
- 泵:用于增加或减少供水流量。
软件要求恒流供水系统的软件要求如下:- PLC编程软件:用于编写PLC的控制程序。
- 数据采集软件:用于监测和记录供水流量数据。
系统工作流程1. 接收流量信号:系统通过流量传感器获取实时的供水流量信号。
2. 比较流量值:PLC控制器将流量信号与设定值进行比较。
3. 控制电动阀门:根据流量差异,PLC控制电动阀门逐渐开启或关闭,以调整供水流量。
4. 启动/停止泵:根据电动阀门的开启程度,PLC控制系统启动或停止泵的运行,以实现恒流供水。
结论本文介绍了基于PLC控制的恒流供水系统的设计。
通过PLC 控制器、流量传感器、电动阀门和泵等设备的协调运作,该系统能够实现可靠的供水流量控制,并确保恒定的流量输出。
实施该系统可以提高供水的稳定性和效率,满足实际应用的需求。
- 1、下载文档前请自行甄别文档内容的完整性,平台不提供额外的编辑、内容补充、找答案等附加服务。
- 2、"仅部分预览"的文档,不可在线预览部分如存在完整性等问题,可反馈申请退款(可完整预览的文档不适用该条件!)。
- 3、如文档侵犯您的权益,请联系客服反馈,我们会尽快为您处理(人工客服工作时间:9:00-18:30)。
基于P L C的流量控制系统集团标准化办公室:[VV986T-J682P28-JP266L8-68PNN]辽宁工业大学电气控制与PLC技术课程设计(论文)题目:基于PLC的流量控制系统设计院(系):电气工程学院专业班级:自动化112学号: 2学生姓名:王毅指导教师:(签字)起止时间:课程设计(论文)任务及评语院(系):电气工程学院教研室:自动化注:成绩:平时20% 论文质量60% 答辩20% 以百分制计算摘要随着科技的飞速发展,自控系统的应用正在不断深入,同时代替传统控制检测技术日益更新。
自动控制技术可谓无所不能。
本文提出一种对液体流量进行实时精确控制的设计方案。
该方案以PLC控制为基础,由上位机、PLC、电动调节阀组成。
它不仅适用于流量控制,在改变动作设备后同样适用于对温度、液位、速度、高度等模拟量的控制。
论文采用文字叙述与图表相结合的方式,逐步做出解释,从而得出具体结论。
更清晰的展示了设计的全过程与每个细节之间的处理方式。
关键词:PLC;自动控制;流量控制目录第1章绪论PLC 是一种专门为在工业环境下应用而设计的数字运算操作的电子装置。
它采用可以编制程序的存储器,用来在其内部存储执行逻辑运算、顺序运算、计时、计数和算术运算等操作的指令,并能通过数字式或模拟式的输入和输出,控制各种类型的机械或生产过程。
PLC 及其有关的外围设备都应该按易于与工业控制系统形成一个整体,易于扩展其功能的原则而设计。
目前,PLC 在国内外已广泛应用于钢铁、石油、化工、电力、建材、机械制造、汽车、轻纺、交通运输、环保及文化娱乐等各个行业。
PLC 发展到今天,已经形成了大、中、小各种规模的系列化产品。
可以用于各种规模的工业控制场合。
除了逻辑处理功能以外,现代PLC 大多具有完善的数据运算能力,可用于各种数字控制领域。
近年来PLC 的功能单元大量涌现,使PLC渗透到了位置控制、温度控制、CNC 等各种工业控制中。
加上PLC 通信能力的增强及人机界面技术的发展,使用PLC 组成各种控制系统变得非常容易。
本文提出一种对液体流量进行实时精确控制的设计方案。
该方案以PLC控制为基础,由上位机、PLC、电动调节阀组成。
它不仅适用于流量控制,在改变动作设备后同样适用于对温度、液位、速度、高度等模拟量的控制。
论文采用文字叙述与图表相结合的方式,逐步做出解释,从而得出具体结论。
更清晰的展示了设计的全过程与每个细节之间的处理方式。
第2章课程设计的方案2.1概述本设计采用S7-200PLC为核心对液体流量进行控制。
随着自动控制技术的迅速发展,PLC对流量的控制技术应用越来越广泛。
本文采用PLC对流量进行控制,通过合理的设计,提高流量控制水平,进而改善流量运行的稳定性,使其更加精确。
本文主要介绍了流量的PLC控制系统总体方案设计、设计过程、组成、列出流量的梯形图,并给出了系统组成框图,分析流量逻辑关系,提出PLC 的编程方法。
能够给一些初学者点建议,能够对流量的基本原理、基本编程思路有大致的了解。
2.2系统组成总体结构2.2.1控制方案比较和确定流量控制系统主要有流量变送器、变频器、恒流控制单元、电动机组成。
系统主要的任务是利用恒流控制单元使变频器控制一台电动机,实现管道流量的恒定,同时还要能对运行数据进行传输和监控。
根据系统的设计任务要求,有以下两种方案可供选择:(1)通用变频器+单片机(包括变频控制、调节器控制)+流量传感器这种方式控制精度高、控制算法灵活、参数调整方便,具有较高的性价比,但开发周期长,程序一旦固化,修改较为麻烦,因此现场调试的灵活性差,同时变频器在运行时,将产生干扰,变频器的功率越大,产生的干扰越大,所以必须采取相应的抗干扰措施来保证系统的可靠性。
该系统适用于某一特定领域的小容量的变频恒压供水中。
(2)通用变频器+PLC(包括变频控制、调节器控制)+流量传感器这种控制方式灵活方便。
具有良好的通信接口,可以方便地与其他的系统进行数据交换,通用性强;由于PLC产品的系列化和模块化,用户可灵活组成各种规模和要求不同控制系统。
在硬件设计上,只需确定PLC的硬件配置和I/O的外部接线,当控制要求发生改变时,可以方便地通过PC机来改变存贮器中的控制程序,所以现场调试方便。
同时由于PLC的抗干扰能力强、可靠性高,因此系统的可靠性大大提高。
该系统能适用于各类不同要求的恒压供水场合,并且与供水机组的容量大小无关。
通过对以上两种方案的比较和分析,可以看出第二种控制方案更适合于本系统。
这种控制方案既有扩展功能灵活方便、便于数据传输的优点,又能达到系统稳定性及控制精度的要求。
2.2.2流量控制系统的组成及原理图基于PLC的流量控制系统主要有变频器、可编程控制器、流量变送器和水泵电机一起组成一个完整的闭环调节系统,该系统的控制流程图如图所示:图系统的控制流程图从图中可看出,系统可分为:执行机构、信号检测机构、控制机构三大部分,具体为:(l)执行机构:执行机构是由一个水泵电机组成,它用于将水供入管道,通过变频器改变电机的转速,以达到控制管道水流量的目的。
(2)信号检测机构:在系统控制过程中,需要检测的信号包括管道水流量信号,其中水流量信号是本控制系统的主要反馈信号。
此信号是模拟信号,读入PLC时,需进行A/D转换。
(3)控制机构:本系统的控制机构包括控制器(PLC)和变频器两个部分。
控制器是整个流量控制系统的核心。
控制器直接对系统中的流量信号进行采集,对来自人机接口和通讯接口的数据信息进行分析、实施控制算法,得出对执行机构的控制方案,通过变频调速器和接触器对执行机构(即水泵电机)进行控制;变频器是对水泵电机进行转速控制的单元,其跟踪控制器送来的控制信号改变水泵电机的转速控制。
流量控制系统以供水出口管道水流量为控制目标,在控制上实现出口管道的实际流量跟随设定的水流量。
设定的水流量可以是一个常数,也可以是一个时间分段函数,在每一个时段内是一个常数。
水流量控制系统的结构框图如图所示:图水流量控制系统框图水流量控制系统通过安装在管道上的流量变送器实时地测量参考点的水流量,检测管道出水流量,并将其转换为4—20mA的电信号,此检测信号是实现水流量恒定的关键参数。
由于电信号为模拟量,故必须通过PLC的A/D转换模块才能读入并与设定值进行比较,将比较后的偏差值进行PID运算,再将运算后的数字信号通过D/A转换模块转换成模拟信号作为变频器的输入信号,控制变频器的输出频率,从而控制水泵电机的转速,进而控制管道中的水流量,实现水流量恒定。
2.2.3水流量系统控制流程水流量系统控制流程如下:(l)系统通电,按照接收到有效的自控系统启动信号后,首先启动变频器拖动电动机工作,根据流量变送器测得的管道实际流量和设定流量的偏差调节变频器的输出频率,控制水泵电机的转速,当输出流量达到设定值,转速才稳定到某一定值,这期间水泵电机工作在调速运行状态。
(2)当管道水流量减小时,流量变送器反馈的水流量信号减小,偏差变大,PLC的输出信号变大,变频器的输出频率变大,所以水泵电机的转速增大,供水量增大,最终水泵电机的转速达到另一个新的稳定值。
反之,当管道水流量增加时,通过流量闭环,减小水泵电机的转速到另一个新的稳定值。
第3章硬件设计3.1PLC S7-200 介绍(1)适用范围S7-200 系列在集散自动化系统中充分发挥其强大功能。
使用范围可覆盖从替代继电器的简单控制到更复杂的自动化控制。
应用领域极为广泛,覆盖所有与自动检测,自动化控制有关的工业及民用领域,包括各种机床、机械、电力设施、民用设施、环境保护设备等等。
如:中央空调,电梯控制,运动系统。
S7-200 系列PLC 可提供4 个不同的基本型号的8 种CPU 供您使用。
(2)CPU单元设计集成的24V 负载电源:可直接连接到传感器和变送器(执行器),CPU 221,222 具有180mA 输出,CPU 224,CPU 224XP,CPU 226 分别输出280,400mA。
可用作负载电源。
CPU 221~226 各有2 种类型CPU,具有不同的电源电压和控制电压。
本机数字量输入/输出点:CPU 221 具有6 个输入点和4 个输出点,CPU 222 具有8 个输入点和6 个输出点,CPU 224 具有14 个输入点和10 个输出点,CPU 224XP 具有14 个输入点和10 个输出点,CPU 226 具有24 个输入点和16 个输出点。
本机模拟量输入/输出点:CPU 224XP 具有2 个输入点,1 个输出点。
高速计数器:CPU 221/222 :4 个高速计数器,可编程并具有复位输入,2 个独立的输入端可同时作加、减计数,可连接两个相位差为90°的A/B 相增量编码器。
CPU224/224XP/226 :6 个高速计数器,具有CPU221/222 相同的功能。
CPU 222/224/224XP/226 :可方便地用数字量和模拟量扩展模块进行扩展。
可使用仿真器(选件)对本机输入信号进行仿真,用于调试用户程序。
(3)各型号的优缺点CPU 221:本机集成6 输入/4 输出共10 个数字量I/O 点。
无I/O 扩展能力。
6K 字节程序和数据存储空间。
4 个独立的30kHz 高速计数器,2 路独立的20kHz高速脉冲输出。
1 个RS485 通讯/编程口,具有PPI 通讯协议、MPI 通讯协议和自由方式通讯能力。
非常适合于小点数控制的微型控制器。
CPU 222:本机集成8 输入/6 输出共14 个数字量I/O 点。
可连接2 个扩展模块。
6K 字节程序和数据存储空间。
4 个独立的30kHz 高速计数器,2 路独立的20kHz高速脉冲输出。
1 个RS485 通讯/编程口,具有PPI 通讯协议、MPI 通讯协议和自由方式通讯能力。
非常适合于小点数控制的微型控制器。
CPU 224:本机集成14 输入/10 输出共24 个数字量I/O 点。
可连接7 个扩展模块,最大扩展至168 路数字量I/O 点或35 路模拟量I/O 点。
13K 字节程序和数据存储空间。
6 个独立的30kHz 高速计数器,2 路独立的20kHz 高速脉冲输出,具有PID 控制器。
RS485 通讯/编程口,具有PPI 通讯协议、MPI 通讯协议和自由方式通讯能力。
I/O 端子排可很容易地整体拆卸。
具有较强控制能力的控制器。
CPU 224XP:本机集成14 输入/10 输出共24 个数字量I/O 点,2 输入/1 输出共3 个模拟量I/O 点,可连接7 个扩展模块,最大扩展值至168 路数字量I/O 点或38 路模拟量I/O 点。
20K 字节程序和数据存储空间,6 个独立的高速计数器(100KHz),2 个100KHz 的高速脉冲输出,2 个RS485 通讯/编程口,具有PPI 通讯协议、MPI 通讯协议和自由方式通讯能力。