整体硬质合金麻花钻常用槽型性能实验研究
硬质合金麻花钻涂层性能试验研究
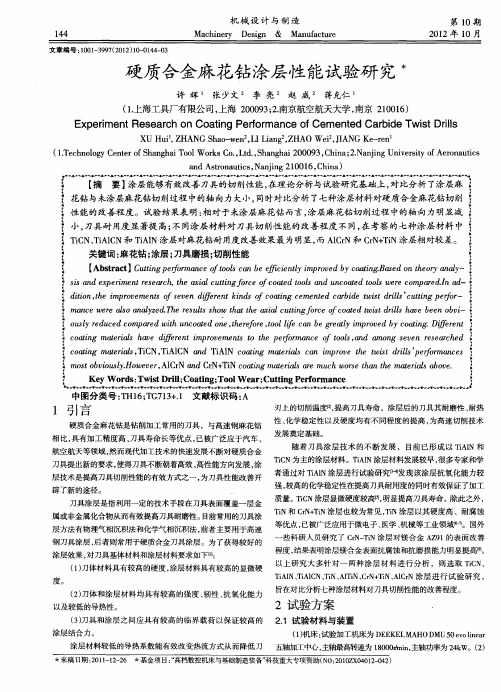
【 摘
要】 涂层 能够有效改善刀具的切削性能 , 在理论分析与试验研究基础上 , 对比分析 了涂层麻
花钻 与未涂层麻 花钻切 削过程 中的轴 向力 大小 , 同时对 比分析 了七种 涂层材 料对硬 质合金麻 花钻 切 削
性能的改善程度。试验结果表 明: 相对于未涂层麻花钻而言 , 涂层麻花钻切 削过程中的轴向力明显减 小, 刀具耐用度显著提高; 不同涂层材料对刀具切削性能的改善程度 不同, 在考察的七种涂层材料 中
mo t b i u l. we e , C N a d C N+ i o ig mae i s a e mu h w re t a e m t r s a o e s v o syHo v r A1 r r T N c a n t r r c o s h t a e i b . o n t l a n h l a v Ke o d : y W r s Twit i ; a i g; 0 e r Cu tn e f r a c s l C0 tn T0 l Dr l W a ; ti g P r o m n e
XU Hu Z i HANG S a - e L in- Z 。 h o w n , ILa g , HAO W e JANG Ke rn z i,I —e
( . c n l yC ne h nh i ol rs o,t. h n h i 0 0 3 C ia 2N nigU i r t eo at s 1 e h oo e t o S a g a T o Wok . d, ag a 2 0 9 , hn ;.a j nv syo A rn ui T g rf C L S n ei f c a dA t n uisN nig2 0 1 ,hn ) n s o at , aj 1 0 6 C ia r c n
硬质合金切削工具材料性能研究
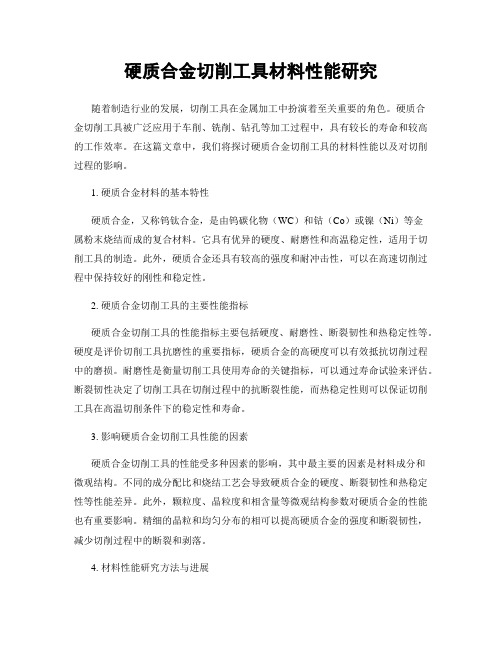
硬质合金切削工具材料性能研究随着制造行业的发展,切削工具在金属加工中扮演着至关重要的角色。
硬质合金切削工具被广泛应用于车削、铣削、钻孔等加工过程中,具有较长的寿命和较高的工作效率。
在这篇文章中,我们将探讨硬质合金切削工具的材料性能以及对切削过程的影响。
1. 硬质合金材料的基本特性硬质合金,又称钨钛合金,是由钨碳化物(WC)和钴(Co)或镍(Ni)等金属粉末烧结而成的复合材料。
它具有优异的硬度、耐磨性和高温稳定性,适用于切削工具的制造。
此外,硬质合金还具有较高的强度和耐冲击性,可以在高速切削过程中保持较好的刚性和稳定性。
2. 硬质合金切削工具的主要性能指标硬质合金切削工具的性能指标主要包括硬度、耐磨性、断裂韧性和热稳定性等。
硬度是评价切削工具抗磨性的重要指标,硬质合金的高硬度可以有效抵抗切削过程中的磨损。
耐磨性是衡量切削工具使用寿命的关键指标,可以通过寿命试验来评估。
断裂韧性决定了切削工具在切削过程中的抗断裂性能,而热稳定性则可以保证切削工具在高温切削条件下的稳定性和寿命。
3. 影响硬质合金切削工具性能的因素硬质合金切削工具的性能受多种因素的影响,其中最主要的因素是材料成分和微观结构。
不同的成分配比和烧结工艺会导致硬质合金的硬度、断裂韧性和热稳定性等性能差异。
此外,颗粒度、晶粒度和相含量等微观结构参数对硬质合金的性能也有重要影响。
精细的晶粒和均匀分布的相可以提高硬质合金的强度和断裂韧性,减少切削过程中的断裂和剥落。
4. 材料性能研究方法与进展研究硬质合金切削工具材料性能的方法主要包括实验测试和数值模拟。
实验测试可以通过切削试验、硬度测试、显微镜观察等手段来获取硬质合金的性能数据。
数值模拟则通过计算机模拟切削过程中的材料应力、变形和热传导等物理过程,预测硬质合金切削工具的性能。
近年来,基于人工智能和机器学习的模型也逐渐应用于硬质合金材料性能研究中,提高了研究效率和准确性。
5. 切削工具性能改善的途径为了改善硬质合金切削工具的性能,研究人员采取了多种途径。
加工不锈钢硬质合金群钻钻尖的试验研究
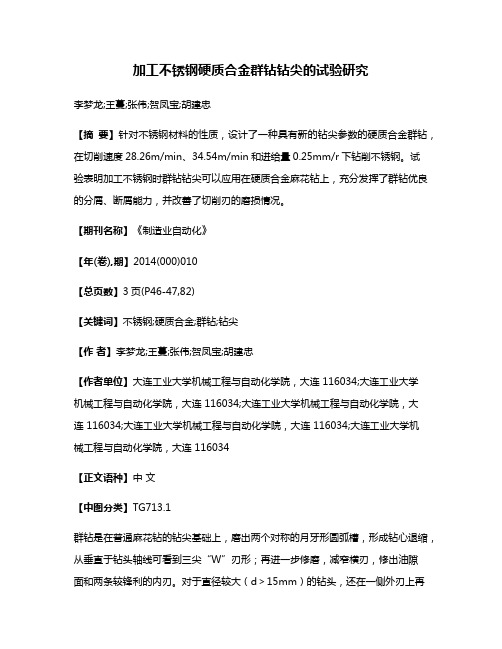
加工不锈钢硬质合金群钻钻尖的试验研究李梦龙;王蔓;张伟;贺凤宝;胡建忠【摘要】针对不锈钢材料的性质,设计了一种具有新的钻尖参数的硬质合金群钻,在切削速度28.26m/min、34.54m/min和进给量0.25mm/r下钻削不锈钢。
试验表明加工不锈钢时群钻钻尖可以应用在硬质合金麻花钻上,充分发挥了群钻优良的分屑、断屑能力,并改善了切削刃的磨损情况。
【期刊名称】《制造业自动化》【年(卷),期】2014(000)010【总页数】3页(P46-47,82)【关键词】不锈钢;硬质合金;群钻;钻尖【作者】李梦龙;王蔓;张伟;贺凤宝;胡建忠【作者单位】大连工业大学机械工程与自动化学院,大连 116034;大连工业大学机械工程与自动化学院,大连 116034;大连工业大学机械工程与自动化学院,大连 116034;大连工业大学机械工程与自动化学院,大连 116034;大连工业大学机械工程与自动化学院,大连 116034【正文语种】中文【中图分类】TG713.1群钻是在普通麻花钻的钻尖基础上,磨出两个对称的月牙形圆弧槽,形成钻心退缩,从垂直于钻头轴线可看到三尖“W”刃形;再进一步修磨,减窄横刃,修出油隙面和两条较锋利的内刃。
对于直径较大(d>15mm)的钻头,还在一侧外刃上再磨出1―2条分屑槽[1](如图1所示)。
群钻的这种特殊刃形使其排屑效果明显。
某公司在使用普通麻花钻钻不锈钢时出现了断屑不好,切屑缠刀、粘刀,崩刃现象,刀具磨损严重。
为了解决断屑问题,本文设计了具有群钻钻尖的硬质合金麻花钻。
而群钻钻尖传统应用于高速钢麻花钻,应用在硬质合金材料时原有的钻尖参数已不再适用[2]。
鉴于此本论文设计一种具有新的钻尖参数的硬质合金群钻,使在加工不锈钢时,可以起到良好的断屑作用,提高刀具的使用寿命。
不锈钢(1Cr18Ni9)因为良好的综合机械性能而被广泛应用,故对其进行钻削试验具有实际的指导意义。
本试验采用三支具有不同钻尖参数的硬质合金群钻,直径为φ10mm,槽长60mm,总长100mm。
麻花钻结构参数及刃磨方法的研究(毕业论文钻头部分)
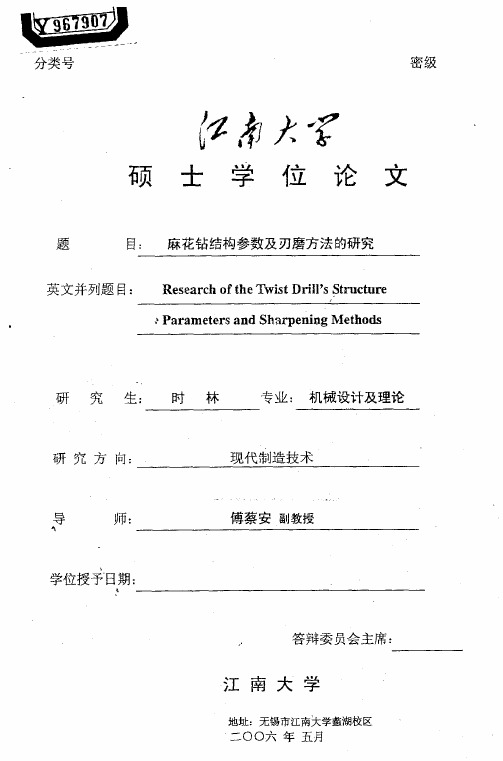
江南大学十学位论文2.1引言第二章螺旋前刀面方程的推导麻花钻的前刀面一一即螺旋槽表面,是切屑沿着流出的表面。
切削刃上任一点的前角是这一点的基面与前而(或前面的切平面)之间的夹角。
”。
在麻花钻钻削过程中,各切削刃及前、后刀面会出现磨损或破损的情况,或者为了适麻不同的加工材料,要改变某些角度或钻头的形式,这时就要求对麻花钻进行修磨,比较常见的就是对麻花钻后刀而进行修磨。
然而,我们在对麻花钻后刀面进行修磨之后,其土刀刃为前刀面和后刀面的交线,如果没有前刀面方程,我们就无法求出修磨后主刀刃的方程,也就无法求出沿主刀刃上各点处的后角的大小,因此,必须要建立起前刀面的方程。
经翻阅相关资料,虽然有些文中给出了前刀面的方程,但并未指出是在一个什么样的坐标系下建立的方程,也没有给出前刀面方程的推导过程,而且各种资料中的前刀而方程不尽致。
为此,本文在研究麻花钻前刀面的性质后,建立了麻花钻前刀面的数学模型。
2.2前刀面的数学建模麻花钻前刀面如图2.1所示,这个前刀面足一个螺旋面,是由过直线刃上一系列等螺距的螺旋线组成。
图2.1麻花钻前刀面根据这个原理,建立了其数学模型,其过程如r图2.2中相关符号的说明:R——麻花钻的半径“直线刃上任一点的、卜径第七章其于Pro/E的麻花钻前、后刀面的参数化建模机器刃磨参数的优化7.2.1直线主刀刃及轴线绘制—1Od0i一.图7.1生成钻头轴线和直线刃b蕊秘毽鼬鲻’一‘一州崮F¨eEdnlnsert眦nniesShow日a品电Bxl舻I扣嘲国=?F团国{——CurrentComext—叫I口sz嘲ss]I湖m_sd0=sqrtl瞰R-Rc’Rc)Aanl59)■l-_-*1^1¨TⅢ-厂五]勋setIcance-l引呷llIU娥l』江南大学士学位论文图7.8生成砂轮然后,将圆锥母线E绕其轴线F旋转900生成一个圆锥砂轮s1,由此砂轮磨出的后刀面后角为O度,为了使刃磨出的后刀面有后角,将此砂轮绕一个由点1指向点11的向量旋转一个角度a(在模型中没茕为afa),生成另一个砂轮S2。
硬质合金金相实验方法及实验结果

硬质合金金相实验方法及实验结果硬质合金是一种金属陶瓷材料,主要由WC-Co或WC-TiC-Co合金组成。
它具有高熔点、高硬度、高耐磨性和比高速钢更高的热硬性等特点,可以在金属切削中代替一般钢制刀具,使用寿命也比钢制品高得多。
硬质合金主要用于制造切削刀具刀头、各种模具、轧棍、矿山及石油钻探工具等。
硬质合金的低倍组织应均匀一致,不允许有黑心、气孔、分层、裂纹及脏污等缺陷。
高倍组织主要观察硬质合金中各相的组成、晶粒的大小、分布情况等,允许有个别粗大的碳化钨相晶粒存在,但不允许有大量堆积或普遍晶粒长大现象。
硬质合金金相试样的制备方法与一般钢铁试样不同。
一般取制品的折断面或者剖面作为金相试样的磨面,若无法破坏和折断,则可取比较有代表性的表面进行检查。
试样制备包括取样和磨制、抛光等步骤。
磨制时要均匀用力,并随时观察,抛光时需使用金刚石粉末和水。
总之,硬质合金的制造和应用已经得到广泛的研究和应用,其性能和用途也得到了不断扩大和深入的探索。
在制造和检测过程中,要注意组织和缺陷的要求,采取适当的制备和检验方法。
温时间过长导致的,需要在制备过程中加强控制。
为了得到光滑的试样表面,我们使用经过研磨的样品,使用细小的小号金刚石粉末进行抛光。
我们使用与研磨相同的抛光布,并确保其清洁。
将小号金刚石粉末均匀涂抹在半径为5cm的圆周上,使用相同的方法进行抛光,直到研磨面非常光亮。
使用100倍物镜的金相显微镜观察,当看到浅黄色的平面且几乎没有划痕或者划痕非常浅的时候,说明抛光成功。
如果划痕很明显,则说明抛光失败,需要继续抛光直到达到成功的标准。
在显微镜下放大100倍观察未经腐蚀的试样,以鉴定孔隙、石墨、污垢和其他缺陷。
我们可以根据分布参考图进行直接对比评定或拍照评定。
使用化学试剂侵蚀或者氧化着色法来显示显微组织。
本实验使用新配的20%铁氰化钾和20%氢氧化钾水溶液的混合液进行腐蚀,腐蚀时间大约为30-60秒,视腐蚀情况而定。
一般磨面用肉眼所见显示为青灰色即基本腐蚀好。
钻头实验报告

钻头实验报告钻头实验报告引言:钻头是一种常见的工具,用于在各种材料上钻孔。
它的设计和材料选择对于钻孔效果和工作寿命至关重要。
本篇文章将对钻头实验进行介绍和分析,探讨不同因素对钻头性能的影响。
实验目的:本实验旨在研究不同类型和材料的钻头在不同条件下的钻孔效果和寿命,以便为实际工作中的钻孔操作提供参考和指导。
实验方法:1. 实验材料:- 钻头:包括高速钢钻头、硬质合金钻头和陶瓷钻头。
- 钻孔材料:选择了钢板、混凝土和木材作为钻孔材料。
- 实验设备:钻床、钻孔夹具、测量工具等。
2. 实验步骤:- 第一步:选择不同类型和材料的钻头,并进行初步测试,记录下初始状态。
- 第二步:根据实验需求,选择不同的钻孔材料和钻孔直径进行钻孔。
- 第三步:记录钻孔时间、钻孔深度和钻孔质量。
- 第四步:观察和记录钻头磨损情况。
- 第五步:根据实验数据进行分析和总结。
实验结果与分析:1. 钻孔时间:- 高速钢钻头:在钢板上钻孔时间较长,但在木材上表现较好。
- 硬质合金钻头:在各种材料上钻孔时间相对较短,但在混凝土上易产生振动。
- 陶瓷钻头:在木材上钻孔时间最短,但在钢板和混凝土上容易受到磨损。
2. 钻孔深度和质量:- 高速钢钻头:在钢板上钻孔深度较浅,但钻孔质量较好。
- 硬质合金钻头:在各种材料上钻孔深度和质量均较为稳定。
- 陶瓷钻头:在钢板上钻孔深度较浅,且钻孔质量较差。
3. 钻头磨损情况:- 高速钢钻头:易受到磨损,尤其在钻孔硬度较高的材料上。
- 硬质合金钻头:相对耐磨损,但在钻孔混凝土时容易受到振动影响。
- 陶瓷钻头:磨损较为明显,尤其在钻孔钢板和混凝土时。
结论:根据实验结果和分析,可以得出以下结论:- 钻头的类型和材料对钻孔效果和寿命有显著影响。
- 高速钢钻头适用于木材等较软材料的钻孔,但在钻孔硬度较高的材料时易受到磨损。
- 硬质合金钻头在各种材料上表现较为稳定,但在钻孔混凝土时易受到振动影响。
- 陶瓷钻头在钻孔时间上表现较好,但在钻孔质量和磨损方面存在一定问题。
硬质合金刀具材料性能和特点
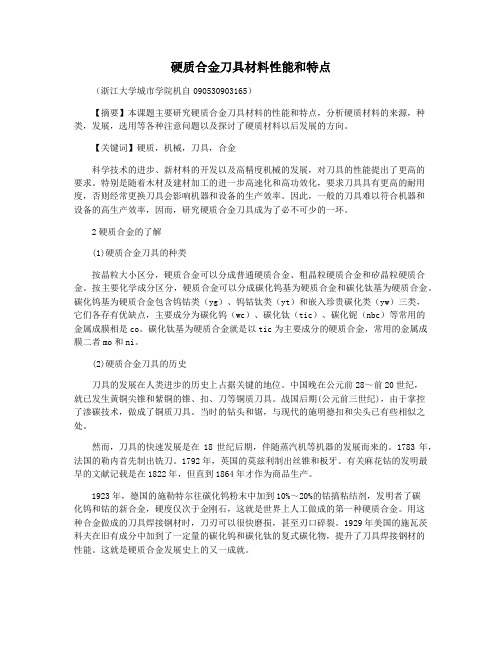
硬质合金刀具材料性能和特点(浙江大学城市学院机自************)【摘要】本课题主要研究硬质合金刀具材料的性能和特点,分析硬质材料的来源,种类,发展,选用等各种注意问题以及探讨了硬质材料以后发展的方向。
【关键词】硬质,机械,刀具,合金科学技术的进步、新材料的开发以及高精度机械的发展,对刀具的性能提出了更高的要求。
特别是随着木材及建材加工的进一步高速化和高功效化,要求刀具具有更高的耐用度,否则经常更换刀具会影响机器和设备的生产效率。
因此,一般的刀具难以符合机器和设备的高生产效率,因而,研究硬质合金刀具成为了必不可少的一环。
2硬质合金的了解(1)硬质合金刀具的种类按晶粒大小区分,硬质合金可以分成普通硬质合金、粗晶粒硬质合金和矽晶粒硬质合金。
按主要化学成分区分,硬质合金可以分成碳化钨基为硬质合金和碳化钛基为硬质合金。
碳化钨基为硬质合金包含钨钴类(yg)、钨钴钛类(yt)和嵌入珍贵碳化类(yw)三类,它们各存有优缺点,主要成分为碳化钨(wc)、碳化钛(tic)、碳化铌(nbc)等常用的金属成膜相是co。
碳化钛基为硬质合金就是以tic为主要成分的硬质合金,常用的金属成膜二者mo和ni。
(2)硬质合金刀具的历史刀具的发展在人类进步的历史上占据关键的地位。
中国晚在公元前28~前20世纪,就已发生黄铜尖锥和紫铜的锥、扣、刀等铜质刀具。
战国后期(公元前三世纪),由于掌控了渗碳技术,做成了铜质刀具。
当时的钻头和锯,与现代的施明德扣和尖头已有些相似之处。
然而,刀具的快速发展是在18世纪后期,伴随蒸汽机等机器的发展而来的。
1783年,法国的勒内首先制出铣刀。
1792年,英国的莫兹利制出丝锥和板牙。
有关麻花钻的发明最早的文献记载是在1822年,但直到1864年才作为商品生产。
1923年,德国的施勒特尔往碳化钨粉末中加到10%~20%的钴搞粘结剂,发明者了碳化钨和钴的新合金,硬度仅次于金刚石,这就是世界上人工做成的第一种硬质合金。
硬质合金刀具槽型结构对切屑的影响_龙新延
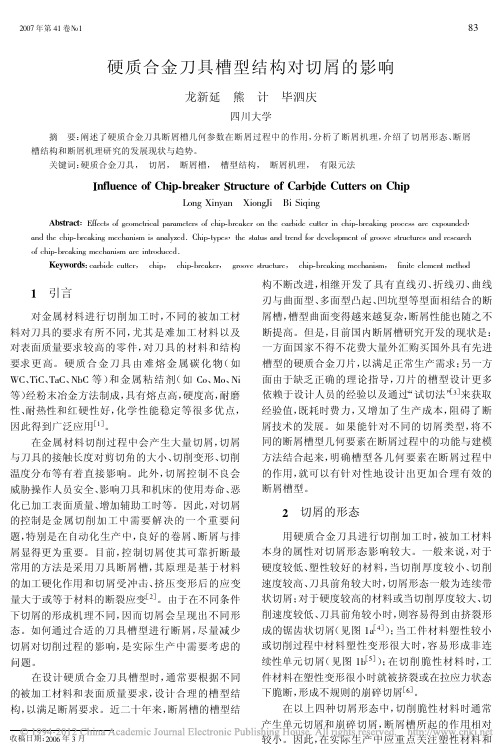
。
在金属材料切削过程中会产生大量切屑, 切屑 与刀具的接触长度对剪切角的大小、 切削变形、 切削 温度分布等有着直接影响。此外, 切屑控制不良会 威胁操作人员安全、 影响刀具和机床的使用寿命、 恶 化已加工表面质量、 增加辅助工时等。因此, 对切屑 的控制是金属切削加工中需要解决的一个重要问 题, 特别是在自动化生产中, 良好的卷屑、 断屑与排 屑显得更为重要。目前, 控制切屑使其可靠折断最 常用的方法是采用刀具断屑槽, 其原理是基于材料 的加工硬化作用和切屑受冲击、 挤压变形后的应变 量大于或等于材料的断裂应变
屑越容易折断。但是, 槽宽过小容易产生积屑, 限制 刀具的切削深度和进给量, 且切屑变形较大, 容易产 生小块飞溅切屑; 槽宽过大则难以保证有效的卷屑 或断屑。在设计断屑槽时, 应根据工件材料和切削 用量确定槽宽, 一般可选取 ! 2 3 (+ - .0) (切削中 " 碳钢时可取上限, 切削合金钢时可取下限) 。 确定断屑槽深度 # 时, 通常应与槽宽 ! 一起 考虑, 即应考虑其比值 ! $ # 。 ! $ # 比值增大, 相当 于槽型卷曲部分半径增大, 前角减小。此时最小进 给量 " 4#2 明 显 减 小, 切 屑 不 易 折 断, 但刀具强度增 大。 (() 断屑槽的刃口高度 刃口高度 % 是指棱带顶面与刀片基面之间的 。降低棱带高度, 会减小有效槽深 高度差 (见图 /) 和刀片的法向前角, 使断屑槽对切屑的弯曲力矩增 大, 加大切屑变形, 增大断屑范围。但如刃口高度 % 过大, 除可能降低刀片强度外, 还会影响双面刀片的 安装稳定性。此外, % 太大还会使标准刀杆的刀刃 低于工件中心线, 使实际工作前角减小。因此, 对于 某些专用刀片或单刀片, 可考虑采用较大的 % , 而在 一般情况下, % 不宜取得过大。国外的一些复杂三 维断屑槽型 (双面刀片) 的 % 一般选取为 05.44 左 右。
- 1、下载文档前请自行甄别文档内容的完整性,平台不提供额外的编辑、内容补充、找答案等附加服务。
- 2、"仅部分预览"的文档,不可在线预览部分如存在完整性等问题,可反馈申请退款(可完整预览的文档不适用该条件!)。
- 3、如文档侵犯您的权益,请联系客服反馈,我们会尽快为您处理(人工客服工作时间:9:00-18:30)。
2.麻花钻螺旋槽作用
Company Logo
螺旋槽直接形成钻头的前刀面,影响钻头的容屑及排屑能 力,螺旋槽与钻头的后刀面(后刀面为双平面)相交形成 钻头的主切削刃直接控制钻头法前角的大小及分布,从而 直接影响钻头的切削性能。在钻削过程中,钻身承受着钻 削力,从钻孔中排出钻屑,同时随切屑、冷却液及钻身将 切削热挥发出去。
凹型槽
46 14.2 30° 加工测量 2.09 105.5° 4.1 15.24
误差 -0.47% 0.95%
0.59% -0.58%
7.主切削刃形状
Company Logo
8.三种槽型的切削实验
Company Logo
机床:美国HASS VOP-D VF5型加工中心主要性能 参数:最高钻速8000rad/mim;功率 20马力;直线 分辨率 0.001mm
2500mm/min 0.15mm/r、
2500mm/min 0.2mm/r
四种切削参数下分别加工三种不同材料,这三种材料分别 为HT200(铸铁)、42crmo(合金钢)、 1cr18ni9ti(不锈钢)三种材料,测量扭矩和轴向力。 后面将分析切屑
9.轴向力对比
Company Logo
1.选题意义和背景
Company Logo
在当今的汽车制造行业中,孔加工占的比重可达60%以上, 许多零部件都采用各种新型材料来制造。麻花钻的精度、 使用寿命以及加工效率,对机械加工的效率和质量及最终 产品的成本起着至关重要的作用。在麻花钻螺旋槽研究上, 多见槽型成形原理的报道,而对当今常用的三类槽型针对 不同材料在多种切削参数下进行切削实验较少。
13.凹型槽的改进
Company Logo
加工材料:合金钢 切削速度:62.8m/min
进给量:500mm/min 孔深:20mm(通孔)
使用设备:日本牧野数控机床
Company Logo
工件直径 φ2~3mm φ4~5mm φ6~7mm φ8~12mm φ13~20mm φ21~26mm
倒棱深度 0.15~0.25 0.25~0.35 0.35~0.45 0.45~0.55 0.55~0.65 0.65~0.75
展望
Company Logo
本论文通过实验来验证三种槽型的性能,希望能够对加
工铸铁、合金钢和不锈钢的企业有所帮助。但是如果要把 螺旋槽研究透彻,还需要大量的工作要做。
随着刀具技术的高速发展,槽型前部的形状也不在局限于 以上所研究的三种,而有了更多的变化,需要后面的工作 者再加以研究。
凹型槽弯曲的趋势也不完全相同,有大有小,可能这也会 有不同的性能,需要再加以研究。
3.螺旋槽数学模型
螺旋槽数学模型
Company Logo
4.双平面后刀面数学模型
后刀面数学模型
Company Logo
5.典型槽型的提出
Company Logo
6.螺旋槽的测量
Company Logo
中心距 偏心距 螺旋角
芯厚 螺旋槽圆周角
刃背宽 螺旋槽长
软件仿真 2.1
106.5° 4.076 15.33
进给量:500mm/min 孔深:20mm
使用设备: 美国HASS VOP-D VF5型加工中心
Company Logo
12.径向前角的定义
Company Logo
8mm直径的测量深度L为0.4-0.5,径向前角对切削的影响,径向 前角的大小影响切屑的形状和大小
凸型槽
直线型 槽
凸型槽
-18° 0° 17°
结论
Company Logo
与直线型、凸型螺旋槽相比,凹型槽在轴向力和扭矩的值 整体上是最低的,切屑的形状也是非常好的,凹型槽在加 工HT200,42CrMo,1Cr18Ni9Ti是比直线型和凸 型好些。但凹型槽的钻头由于径向前角过大,在高进给穿 透工件时容易崩刃。这时就需要在槽型周刃上加工一个保 护倒棱,就是让凹型槽的径向前角为负,这种边缘负角的 设计,可以有效抑制高进给穿透工件时造成的崩刃。
10.扭矩对比
Company Logo
11.切屑对比
加工材料:1Cr18Ni9Ti(不锈钢) 切削速度:62.8m/min
进给量:500mm/min 孔深:20mm
使用设备: 美国HASS VOP-D VF5型加工中心
Company Logo
加工材料:42CrMo(合金钢) 切削速度:62.8m/min
测量装置:使用压电式测量仪。该测量仪主要有三个压 电式二维力传感器组成,可测量轴向力力和钻削扭矩。
实验说明
Company Logo
为验证三种槽型钻头的性能,对三种槽型的钻头进行对比 试验。让三种槽型钻头在
切削速度
进给量
1500mm/min 0.15mm/r、
1500mm/min 0.2mm/r、