塑料齿轮疲劳寿命分析
塑料齿轮疲劳寿命分析
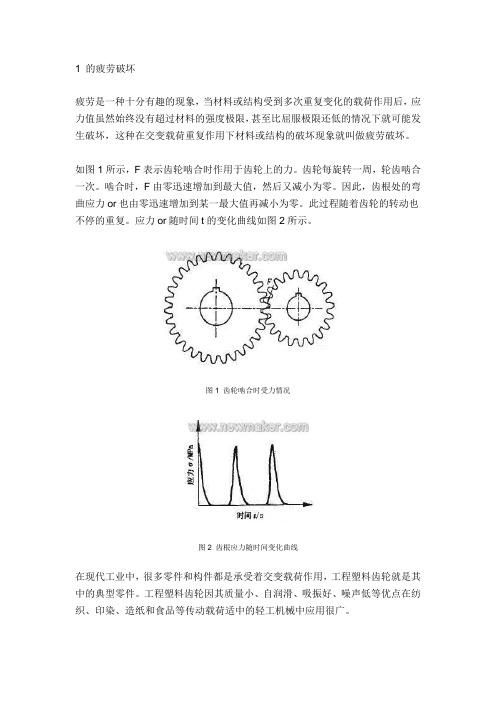
1 的疲劳破坏疲劳是一种十分有趣的现象,当材料或结构受到多次重复变化的载荷作用后,应力值虽然始终没有超过材料的强度极限,甚至比屈服极限还低的情况下就可能发生破坏,这种在交变载荷重复作用下材料或结构的破坏现象就叫做疲劳破坏。
如图1所示,F表示齿轮啮合时作用于齿轮上的力。
齿轮每旋转一周,轮齿啮合一次。
啮合时,F由零迅速增加到最大值,然后又减小为零。
因此,齿根处的弯曲应力or也由零迅速增加到某一最大值再减小为零。
此过程随着齿轮的转动也不停的重复。
应力or随时间t的变化曲线如图2所示。
图1 齿轮啮合时受力情况图2 齿根应力随时间变化曲线在现代工业中,很多零件和构件都是承受着交变载荷作用,工程塑料齿轮就是其中的典型零件。
工程塑料齿轮因其质量小、自润滑、吸振好、噪声低等优点在纺织、印染、造纸和食品等传动载荷适中的轻工机械中应用很广。
疲劳破坏与传统的静力破坏有着许多明显的本质差别:1)静力破坏是一次最大载荷作用下的破坏;疲劳被坏是多次反复载荷作用下产生的破坏,它不是短期内发生的,而是要经历一定的时间。
2)当静应力小于屈服极限或强度极限时,不会发生静力破坏;而交变应力在远小于静强度极限,甚至小于屈服极限的情况下,疲劳破坏就可能发生。
3)静力破坏通常有明显的塑性变形产生;疲劳破坏通常没有外在宏观的显着塑性变形迹象,事先不易觉察出来,这就表明疲劳破坏具有更大的危险性。
工程塑料齿轮的疲劳寿命,是设计人员十分关注的课题,也是与实际生产紧密相关的问题。
然而,在疲劳载荷作用下的疲劳寿命计算十分复杂。
因为要计算疲劳寿命,必须有精确的载荷谱,材料特性或构件的S-N曲线,合适的累积损伤理论,合适的裂纹扩展理论等。
本文对工程塑料齿轮疲劳分析的最终目的,就是要确定其在各种质量情况下的疲劳寿命。
通过利用有限元方法和CAE软件对工程塑料齿轮的疲劳寿命进行分析研究有一定工程价值。
2 工程塑料齿轮材料的确定超高分子量聚乙烯(UHMWPE)是一种综合性能优异的新型热塑性工程塑料,它的分子结构与普通聚乙烯(PE)完全相同,但相对分子质量可达(1~4)×106。
齿轮弯曲疲劳寿命系数

齿轮弯曲疲劳寿命系数齿轮是机械传动中常见的零件,广泛应用于机械装置和设备中。
作为常规的机械部件,齿轮需要具备极高的稳定性和耐久性,才能够保证其正常运行和服务寿命。
而齿轮弯曲疲劳寿命系数是刻画齿轮性能的一个指标,本文将详细探讨齿轮弯曲疲劳寿命系数的相关内容。
1. 齿轮弯曲疲劳寿命系数的定义齿轮弯曲疲劳寿命系数是指在齿轮传动装置的设计寿命内,齿轮齿根处应力的分布与疲劳寿命之间的关系。
齿轮弯曲疲劳寿命系数越大,即表示齿轮具备更高的耐久性和可靠性,能够承受更大的工作负荷和更长时间的使用寿命。
2. 影响齿轮弯曲疲劳寿命系数的因素齿轮弯曲疲劳寿命系数的大小受到多种因素的影响,主要包括以下几个方面:(1)齿轮材料齿轮材料的物理性能和力学性能对齿轮弯曲疲劳寿命系数的影响非常明显。
一般来说,强度高、韧性好、疲劳寿命长、组织均匀的材料更适合作为齿轮材料,能够提高齿轮弯曲疲劳寿命系数。
(2)齿轮的设计几何参数齿轮的设计几何参数也会对齿轮弯曲疲劳寿命系数产生较大的影响。
齿轮参数的合理设计可以减小齿轮齿根处的应力集中程度,从而提高齿轮弯曲疲劳寿命系数。
(3)负荷条件负荷条件是齿轮弯曲疲劳寿命系数的另一个重要影响因素。
在负荷条件相同的情况下,齿轮弯曲疲劳寿命系数越大,表示齿轮具备更好的承载能力和耐久性。
(4)轴承和润滑条件轴承和润滑条件是影响齿轮弯曲疲劳寿命系数的另一因素。
良好的轴承和润滑条件有助于减少齿轮的磨损和摩擦,降低应力水平,提高齿轮弯曲疲劳寿命系数。
3. 齿轮弯曲疲劳寿命系数的测试方法齿轮弯曲疲劳寿命系数的测试是对齿轮性能进行评估和确认的重要手段。
一般采用模拟试验或数值模拟两种方法进行测试,具体方法如下:(1)模拟试验模拟试验是指利用齿轮模拟器或齿轮试验台等设备进行实物测试的方法。
通过不断重复负荷的作用,观察齿轮的磨损程度和变形情况,推算齿轮弯曲疲劳寿命系数和寿命预测模型。
(2)数值模拟数值模拟是通过建立齿轮弯曲疲劳寿命的有限元模型,采用ANSYS、ABAQUS等有限元软件进行计算、模拟和预测的方法。
塑料齿轮疲劳寿命分析报告

1 齿轮的疲劳破坏疲劳是一种十分有趣的现象,当材料或结构受到多次重复变化的载荷作用后,应力值虽然始终没有超过材料的强度极限,甚至比屈服极限还低的情况下就可能发生破坏,这种在交变载荷重复作用下材料或结构的破坏现象就叫做疲劳破坏。
如图1所示,F表示齿轮啮合时作用于齿轮上的力。
齿轮每旋转一周,轮齿啮合一次。
啮合时,F由零迅速增加到最大值,然后又减小为零。
因此,齿根处的弯曲应力or也由零迅速增加到某一最大值再减小为零。
此过程随着齿轮的转动也不停的重复。
应力or随时间t的变化曲线如图2所示。
图1 齿轮啮合时受力情况图2 齿根应力随时间变化曲线在现代工业中,很多零件和构件都是承受着交变载荷作用,工程塑料齿轮就是其中的典型零件。
工程塑料齿轮因其质量小、自润滑、吸振好、噪声低等优点在纺织、印染、造纸和食品等传动载荷适中的轻工机械中应用很广。
疲劳破坏与传统的静力破坏有着许多明显的本质差别:1)静力破坏是一次最大载荷作用下的破坏;疲劳被坏是多次反复载荷作用下产生的破坏,它不是短期内发生的,而是要经历一定的时间。
2)当静应力小于屈服极限或强度极限时,不会发生静力破坏;而交变应力在远小于静强度极限,甚至小于屈服极限的情况下,疲劳破坏就可能发生。
3)静力破坏通常有明显的塑性变形产生;疲劳破坏通常没有外在宏观的显著塑性变形迹象,事先不易觉察出来,这就表明疲劳破坏具有更大的危险性。
工程塑料齿轮的疲劳寿命,是设计人员十分关注的课题,也是与实际生产紧密相关的问题。
然而,在疲劳载荷作用下的疲劳寿命计算十分复杂。
因为要计算疲劳寿命,必须有精确的载荷谱,材料特性或构件的S-N曲线,合适的累积损伤理论,合适的裂纹扩展理论等。
本文对工程塑料齿轮疲劳分析的最终目的,就是要确定其在各种质量情况下的疲劳寿命。
通过利用有限元方法和CAE软件对工程塑料齿轮的疲劳寿命进行分析研究有一定工程价值。
2 工程塑料齿轮材料的确定超高分子量聚乙烯(UHMWPE)是一种综合性能优异的新型热塑性工程塑料,它的分子结构与普通聚乙烯(PE)完全相同,但相对分子质量可达(1~4)×106。
齿轮齿面接触疲劳特性与寿命预测
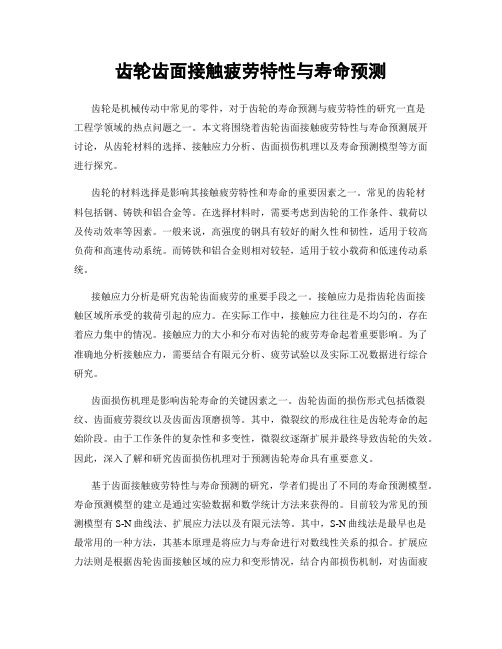
齿轮齿面接触疲劳特性与寿命预测齿轮是机械传动中常见的零件,对于齿轮的寿命预测与疲劳特性的研究一直是工程学领域的热点问题之一。
本文将围绕着齿轮齿面接触疲劳特性与寿命预测展开讨论,从齿轮材料的选择、接触应力分析、齿面损伤机理以及寿命预测模型等方面进行探究。
齿轮的材料选择是影响其接触疲劳特性和寿命的重要因素之一。
常见的齿轮材料包括钢、铸铁和铝合金等。
在选择材料时,需要考虑到齿轮的工作条件、载荷以及传动效率等因素。
一般来说,高强度的钢具有较好的耐久性和韧性,适用于较高负荷和高速传动系统。
而铸铁和铝合金则相对较轻,适用于较小载荷和低速传动系统。
接触应力分析是研究齿轮齿面疲劳的重要手段之一。
接触应力是指齿轮齿面接触区域所承受的载荷引起的应力。
在实际工作中,接触应力往往是不均匀的,存在着应力集中的情况。
接触应力的大小和分布对齿轮的疲劳寿命起着重要影响。
为了准确地分析接触应力,需要结合有限元分析、疲劳试验以及实际工况数据进行综合研究。
齿面损伤机理是影响齿轮寿命的关键因素之一。
齿轮齿面的损伤形式包括微裂纹、齿面疲劳裂纹以及齿面齿顶磨损等。
其中,微裂纹的形成往往是齿轮寿命的起始阶段。
由于工作条件的复杂性和多变性,微裂纹逐渐扩展并最终导致齿轮的失效。
因此,深入了解和研究齿面损伤机理对于预测齿轮寿命具有重要意义。
基于齿面接触疲劳特性与寿命预测的研究,学者们提出了不同的寿命预测模型。
寿命预测模型的建立是通过实验数据和数学统计方法来获得的。
目前较为常见的预测模型有S-N曲线法、扩展应力法以及有限元法等。
其中,S-N曲线法是最早也是最常用的一种方法,其基本原理是将应力与寿命进行对数线性关系的拟合。
扩展应力法则是根据齿轮齿面接触区域的应力和变形情况,结合内部损伤机制,对齿面疲劳寿命进行预测。
有限元法则通过建立齿轮的数值模型,对接触应力进行详细分析,从而得到齿面疲劳寿命的预测结果。
总之,齿轮齿面接触疲劳特性与寿命预测是机械工程领域中的重要研究方向。
塑料的抗疲劳性与寿命评估
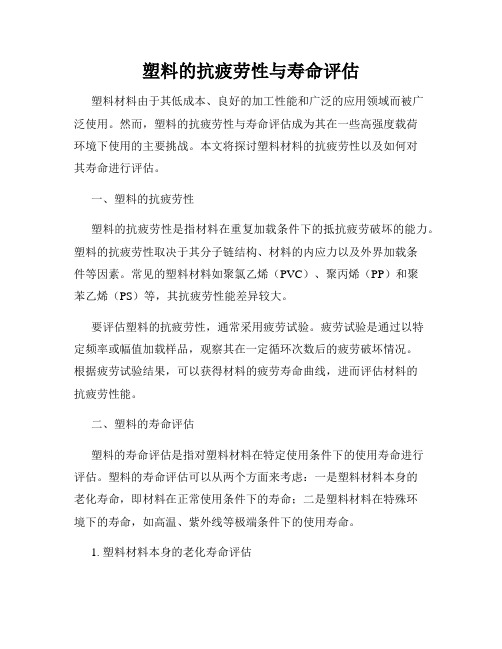
塑料的抗疲劳性与寿命评估塑料材料由于其低成本、良好的加工性能和广泛的应用领域而被广泛使用。
然而,塑料的抗疲劳性与寿命评估成为其在一些高强度载荷环境下使用的主要挑战。
本文将探讨塑料材料的抗疲劳性以及如何对其寿命进行评估。
一、塑料的抗疲劳性塑料的抗疲劳性是指材料在重复加载条件下的抵抗疲劳破坏的能力。
塑料的抗疲劳性取决于其分子链结构、材料的内应力以及外界加载条件等因素。
常见的塑料材料如聚氯乙烯(PVC)、聚丙烯(PP)和聚苯乙烯(PS)等,其抗疲劳性能差异较大。
要评估塑料的抗疲劳性,通常采用疲劳试验。
疲劳试验是通过以特定频率或幅值加载样品,观察其在一定循环次数后的疲劳破坏情况。
根据疲劳试验结果,可以获得材料的疲劳寿命曲线,进而评估材料的抗疲劳性能。
二、塑料的寿命评估塑料的寿命评估是指对塑料材料在特定使用条件下的使用寿命进行评估。
塑料的寿命评估可以从两个方面来考虑:一是塑料材料本身的老化寿命,即材料在正常使用条件下的寿命;二是塑料材料在特殊环境下的寿命,如高温、紫外线等极端条件下的使用寿命。
1. 塑料材料本身的老化寿命评估塑料材料的老化寿命是指材料在正常使用条件下,在长时间内不发生性能下降或破坏的能力。
塑料的老化寿命与其分子结构、添加剂、环境温度等因素相关。
常见的老化寿命评估方法包括热老化试验、紫外老化试验和湿热老化试验等。
热老化试验是将塑料样品置于高温环境中,观察其物理性能的变化情况。
紫外老化试验是模拟阳光照射对塑料材料的影响,通过观察样品的颜色变化、表面裂纹等来评估其老化寿命。
湿热老化试验是将塑料样品置于高温高湿环境中,通过观察其强度、伸长率等物理性能的变化来评估其老化寿命。
2. 特殊环境下的寿命评估在一些特殊环境下,如高温、紫外线、化学品等腐蚀性环境中,塑料材料的使用寿命可能会大大降低。
因此,对于这些特殊环境下的塑料材料,需要进行特殊的寿命评估。
对于高温环境下的塑料材料,可以进行高温老化试验,观察其热稳定性和老化寿命。
塑料齿轮的疲劳寿命如何估算

塑料齿轮的疲劳寿命如何估算现代工业中塑料齿轮的重要性在逐年增加,对工程技术人员而言,塑料齿轮使用寿命的评估与分级是一项非常艰难的任务。
目前,尚无针对齿轮强度分析的国际标准可用,被业界普遍公认的方法是德国VDI 2545标准所提出的准则,除此之外,还缺少测量材料特性所需要的计算方法,小维今天想和大家一起讨论下关于塑料齿轮使用寿命的估算问题,包括如何对塑料齿轮使用寿命进行评级,如何处理缺乏可用材料数据的问题,使其适合于有效的计算方法,塑料齿轮的数量正在急剧增多,主要原因是齿轮传动的很多新的应用被开发出来,特别是近十年来智能家居等新的应用市场的蓬勃发展,同时适合于做齿轮的新的材料的不断涌现,比如苏州维本工程塑料Wintone Z33耐磨静音齿轮专用工程塑料,解决了十年之前齿轮要降噪有时扭矩与弹性难以兼顾的问题,大大拓宽了小微型减速齿轮箱在静音要求比较高、同时又要耐疲劳优异的应用场景。
与钢等金属相比,塑料的属性发生变化的范围更大,完全可以基于包括强度、耐磨性、刚度、阻尼和噪声大小等材料属性,来选择其中一种来满足某一特定要求的理想材料。
尽管塑料齿轮的应用越来越多,但与用于金属齿轮的研究资源相比,塑料齿轮的科学研究水平和资源相对比较欠缺,可用标准之少便是反映该状况的一个典型例子,相比分别用于金属齿轮的AGMA 2001和ISO 6336标准,用于圆柱塑料齿轮强度分析的标准就只有德国的VDI 2545.AGMA 909-A 06、ANSI/AGMA 1006-A 97和ANSI/AGMA 1106-A 97,虽然是用于塑料齿轮,但仅仅是在德国使用。
ANSI/AGMA 920-A 01只提供了大量关于塑料材料齿轮应用的说明,并阐述了典型的检测程序,但并没有被真正推广使用。
而VDI 2545已被废除,并且在整体上缺乏对塑料齿轮的研究。
因此,在没有可用标准和科学的材料研究数据情况下,设计人员要掌握如何成功的设计新的塑料齿轮,还必须依靠实践经验和知识。
减速器齿轮疲劳寿命预测研究
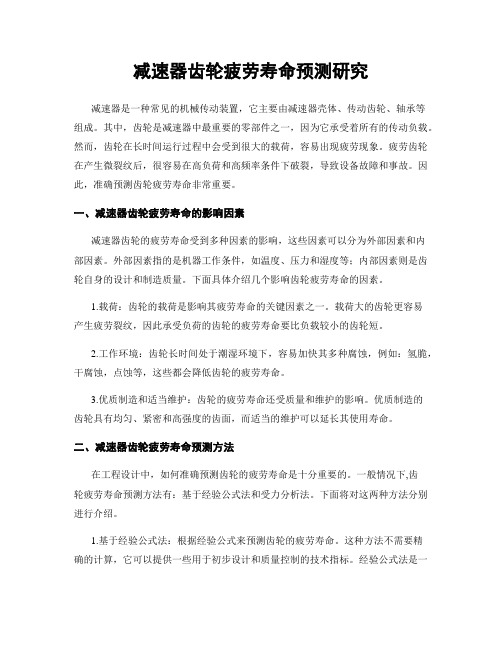
减速器齿轮疲劳寿命预测研究减速器是一种常见的机械传动装置,它主要由减速器壳体、传动齿轮、轴承等组成。
其中,齿轮是减速器中最重要的零部件之一,因为它承受着所有的传动负载。
然而,齿轮在长时间运行过程中会受到很大的载荷,容易出现疲劳现象。
疲劳齿轮在产生微裂纹后,很容易在高负荷和高频率条件下破裂,导致设备故障和事故。
因此,准确预测齿轮疲劳寿命非常重要。
一、减速器齿轮疲劳寿命的影响因素减速器齿轮的疲劳寿命受到多种因素的影响,这些因素可以分为外部因素和内部因素。
外部因素指的是机器工作条件,如温度、压力和湿度等;内部因素则是齿轮自身的设计和制造质量。
下面具体介绍几个影响齿轮疲劳寿命的因素。
1.载荷:齿轮的载荷是影响其疲劳寿命的关键因素之一。
载荷大的齿轮更容易产生疲劳裂纹,因此承受负荷的齿轮的疲劳寿命要比负载较小的齿轮短。
2.工作环境:齿轮长时间处于潮湿环境下,容易加快其多种腐蚀,例如:氢脆,干腐蚀,点蚀等,这些都会降低齿轮的疲劳寿命。
3.优质制造和适当维护:齿轮的疲劳寿命还受质量和维护的影响。
优质制造的齿轮具有均匀、紧密和高强度的齿面,而适当的维护可以延长其使用寿命。
二、减速器齿轮疲劳寿命预测方法在工程设计中,如何准确预测齿轮的疲劳寿命是十分重要的。
一般情况下,齿轮疲劳寿命预测方法有:基于经验公式法和受力分析法。
下面将对这两种方法分别进行介绍。
1.基于经验公式法:根据经验公式来预测齿轮的疲劳寿命。
这种方法不需要精确的计算,它可以提供一些用于初步设计和质量控制的技术指标。
经验公式法是一种基于经验、基于数据的方法,但是其普适性不强。
因为这种方法主要是基于试验数据的规律,只能预测一定条件下的疲劳寿命。
2.受力分析法:这种方法基于受力分析,通过数学模型来计算齿轮受到的载荷、应力和应变,然后获取其疲劳寿命。
这种方法比经验公式法更加准确和精确,但是需要高度的科学技术,分析齿轮的动力学和强度问题。
三、结语减速器齿轮的疲劳寿命预测是机械传动领域中一个重要的研究方向,它直接关系到减速器的使用寿命和安全性。
齿轮疲劳试验标准

齿轮疲劳试验标准
齿轮疲劳试验标准有多种,以下提供两种:
1. GB/T :测试目的为模拟齿轮长时间受到交变载荷作用,观察根部是否产生裂纹,并发生断齿现象。
主要通过模拟试验测取轮齿的S-N疲劳强度寿
命曲线,统计分析轮齿的条件疲劳强度均值和样本疲劳强度的标准离差。
该标准为齿轮的设计验证、定型鉴定、批量生产提供评估依据。
2. GB/T:该标准通过齿面点蚀程度来判断齿轮接触疲劳强度试验的失效。
对于表面硬化齿轮,包括渗碳齿轮,当单齿点蚀面积率达到4%或者齿轮副
点蚀面积率达到%,即判定齿面失效。
此外,进行齿轮弯曲疲劳极限安全系数测试时,需要使用专门的试验台架,并根据齿轮材料的实际情况进行设计和制造,真实反映齿轮材料实际的接触和弯曲疲劳特性。
以上内容仅供参考,建议咨询相关行业协会或权威机构,获取最准确的信息。
- 1、下载文档前请自行甄别文档内容的完整性,平台不提供额外的编辑、内容补充、找答案等附加服务。
- 2、"仅部分预览"的文档,不可在线预览部分如存在完整性等问题,可反馈申请退款(可完整预览的文档不适用该条件!)。
- 3、如文档侵犯您的权益,请联系客服反馈,我们会尽快为您处理(人工客服工作时间:9:00-18:30)。
精心整理
1
齿轮的疲劳破坏
疲劳是一种十分有趣的现象,
当材料或结构受到多次重复变化的载荷作用后,应力值虽然始终没有超过材料的强度极限,甚至比屈服极限还低的情况下就可能发生破坏,这种在交变载荷重复作用下材料或结构的破坏现象就叫做疲劳破坏。
如图1所示,F表示齿轮啮合时作用于齿轮上的力。
齿轮每旋转一周,轮齿啮合一次。
啮合时,F 由零迅速增加到最大值,然后又减小为零。
因此,齿根处的弯曲应力or也由零迅速增加到某一最大值再减小为零。
此过程随着齿轮的转动也不停的重复。
应力or随时间t的变化曲线如图2所示。
图1齿轮啮合时受力情况
图2齿根应力随时间变化曲线
在现代工业中,很多零件和构件都是承受着交变载荷作用,工程塑料齿轮就是其中的典型零件。
工程塑料齿轮因其质量小、自润滑、吸振好、噪声低等优点在纺织、印染、造纸和食品等传动载荷适中的轻工机械中应用很广。
疲劳破坏与传统的静力破坏有着许多明显的本质差别:
1)静力破坏是一次最大载荷作用下的破坏;疲劳被坏是多次反复载荷作用下产生的破坏,它不是短期内发生的,而是要经历一定的时间。
2)当静应力小于屈服极限或强度极限时,不会发生静力破坏;而交变应力在远小于静强度极限,甚至小于屈服极限的情况下,疲劳破坏就可能发生。
3)静力破坏通常有明显的塑性变形产生;疲劳破坏通常没有外在宏观的显著塑性变形迹象,事先不易觉察出来,这就表明疲劳破坏具有更大的危险性。
工程塑料齿轮的疲劳寿命,是设计人员十分关注的课题,也是与实际生产紧密相关的问题。
然而,
材料特性或构件的S-N曲线,合适的累积损伤理论,合适的裂纹扩展理论等。
本文对工程塑料齿轮疲劳分析的最终目的,就是要确定其在各种质量情况下的疲劳寿命。
通过利用有限元方法和CAE软件对工程塑料齿轮的疲劳寿命进行分析研究有一定工程价值。
2工程塑料齿轮材料的确定
超高分子量聚乙烯(UHMWPE)是一种综合性能优异的新型热塑性工程塑料,它的分子结构与普通聚乙烯(PE)完全相同,但相对分子质量可达(1~4)×106。
随着相对分子质量的大幅度升高,UHMWPE表现出普通PE所不具备的优异性能,如耐磨性、耐冲击性、低摩擦系数、耐化学性和消音性等。
UHMWPE耐磨性居工程塑料之首,比尼龙66(PA66)高4倍,是碳钢、不锈钢的7—8倍。
摩擦因数仅为0.07~0.11,具有自润滑性,不粘附性。
因此,本文选用UHMWPE作为工程塑料齿轮材料进行研究。
UHMWPE性能见表1。
由于UHMWPE导热性能较差,所以与其啮合的齿轮选用钢材料。
这样导热性好、摩损小,并能弥补工程塑料齿轮精度不高的缺点。
2啮合齿轮均为标准直齿圆柱齿轮,参数为:UHMWPE齿轮齿数30,钢齿轮齿数20,模数4mm,齿宽20mm,压力角取为20°。
表1超高相对分子质量聚乙烯性能
3UHMWPE材料齿轮疲劳分析模型的建立
齿轮在啮合过程中,轮齿如同受线载荷的悬臂梁,齿根所受的弯矩最大,因此齿根处的弯曲疲劳强度最弱。
当轮齿在齿顶处啮合时,处于双对齿啮合区,此时弯矩的力臂虽然最大,但力并不是最大,因此弯矩并不是最大。
根据分析,齿根所受的最大弯矩发生在齿轮啮合点位于单对齿啮合区最高点时。
因此,在建立UHMWPE材料齿轮疲劳分析模型时,应该建立载荷作用于单对齿啮合区最高点。
由机械原理渐开线齿轮连续传动条件分析方法,可以得出单对齿轮啮合最高点。
然后利用CAXA 软件的齿轮建模功能和数据转换功能建立UHMWPE材料齿轮疲劳分析模型如图3所示。
图3UHMWPE材料齿轮疲劳分析模型
4利用ANSYS分析UHMWPE材料齿轮疲劳寿命
ANSYS是以有限元分析为基础的大型通用CAE软件,是世界上第一个通过IS09001认可的有限元分析软件。
因此,通过准确地建立模型、合理的网格划分与载荷施加以及边界条件设定,就能得到可靠性较好的计算结果。
对于工程塑料齿轮,由于其材料的力学性能、热性能等都与金属材料有很大区别,其失效形式及失效机理与金属齿轮也有很大区别。
由于塑料齿轮的弹性模量较低,与钢齿轮啮合过程中其赫兹接触区较大,接触应力较小,一般不会出现点蚀等表面失效,所以轮齿在弯曲应力作用下疲劳断裂或折断是塑料齿轮的主要失效形式。
因此主要对3种情况下的UHMWPE材料齿轮的疲劳寿命进行分析。
4.1UHMWPE材料齿轮无缺陷情况的疲劳寿命分析
在利用ANSYS进行齿轮的疲劳分析前,需要对2啮合齿轮进行接触分析。
按照上文所分析的实际接触情况,确定2齿轮单齿啮合区域最高点位置,并定义接触类型为柔体对柔体的面对面接触。
取钢齿轮啮合面为目标面,用单元Targel69来定义,取UHMWPE材料齿轮啮合面为接触面,用
单元Contal71来定。
可以从菜单(MainMenu>Preprocessor>Modeling>Create>ContactPair)进入接触向导,来建立目标面接触面的“接触对”。
也可以采用其他途径建立接触对,这属于ANSYS基本操作,本文不再详述。
接触对建立完成后进入静强度求解过程,主动齿轮为钢齿轮,传递力矩为6N·m,ANSYS计算所得UHMWPE材料齿轮齿根处的应力如图4所示。
从应力云图中可以看出:最大应力发生在UHMWPE材料齿轮齿根处,节点号为:2279,应力值为:32.1MPa。
图4UHMWPE材料齿轮齿根处应力云图
工程塑料齿轮ANSYS疲劳分析的步骤为:首先进入后处理POST1,恢复数据库,然后提取齿根最大弯曲应力处的节点应力并将其储存,并确定重复次数,最后采用Miner疲劳积累理论计算疲劳寿命并查看结果。
UHMWPE材料齿轮疲劳寿命预测需要的较关键疲劳性质是材料的S-N曲线,所研究的UHMWPE 材料的S-N曲线如图5所示。
图5UHMWPE材料S-N曲线
疲劳分析结果如图6所示。
可见在文中所设定工作载荷下,该UHMWPE材料齿轮轮齿的疲劳寿命为132800次,累计疲劳系数为0.75301。
图6无缺陷UHMwPE材料齿轮疲劳计算结果
4.2齿问存在熔接痕时UHMWPE材料齿轮的疲劳寿命分析
UHMWPE材料齿轮注塑工艺复杂。
工艺控制不当很容易产生熔接痕等注塑缺陷。
因此,对存在熔接痕缺陷的UHMWPE材料齿轮进行分析,可以确定该缺陷的不同位置对齿轮疲劳破坏的影响程度。
这对工程塑料齿轮的注塑工艺,浇口位置安排等都有一定的指导意义。
在利用ANSYS分析存在熔接痕缺陷的工程塑料齿轮时,将熔接痕等效为I型裂纹问题,并采用KSCON命(MainMenu>Preprocessor>MeshShape&Size>ConcentratKPs-Create),使ANSYS自动围绕熔接痕尖端关键点生成奇异单元,然后进行分析求解。
假设在两轮齿间存在一条长为1.5mm 的熔接痕,熔接痕位置和尺寸如图7所示。
图7齿间熔接痕尺寸
疲劳分析结果显示:在齿间存在较小熔接痕缺陷情况下,UHMWPE材料齿轮轮齿的疲劳寿命为124600次,累计疲劳系数为0.80257。
疲劳产生的位置仍未齿根处。
可见,齿间存在较小熔接痕缺陷情况下,缺陷对UHMWPE齿轮疲劳寿命无较大影响。
4.3齿根存在熔接痕时UHMWPE材料齿轮的疲劳寿命分析
假设在齿根处存在一条长为1.5mm的熔接痕,熔接痕位置和尺寸如图9所示。
图9齿根熔接痕尺寸
疲劳分析结果为:疲劳破坏发生在熔接痕尖端,如图10所示。
齿轮轮齿的疲劳寿命仅为5631次。
可见,在齿根存在较小熔接痕缺陷情况下齿轮很快进人疲劳并断裂破坏。
图l0疲劳破坏发生位置
5结论与展望
1)采用ANSYS有限元技术可以计算复杂边界条件下的疲劳问题,对工程塑料齿轮的疲劳寿命的确定有一定价值。
2)通过ANSYS分析得出:所研究的UHMWPE材料齿轮在无缺陷情况下的疲劳寿命远高于齿根存在熔接痕情况下的寿命。
3)
工艺进行优化,避免在齿轮齿根处出现熔接痕。
4)很多性能优异的工程塑料均可用作为中等载荷的齿轮材料,例如POM,PA66等,利用有限元方法校核其疲劳寿命会加快设计速度,同时也提高了可靠性。
(end)。