数控编程-端面深孔切削循环G74指令--教案
g74端面切槽循环编程实例

g74端面切槽循环编程实例G74端面切槽循环编程实例概述本文介绍了G74端面切槽循环编程的实例,包括编程指令和参数解析,旨在帮助读者更好地理解G74端面切槽循环编程的应用。
编程指令和参数解析在G74端面切槽循环编程中,有以下几个主要的编程指令和参数:1.G74:选择G74端面切槽循环编程。
2.X:切槽的终止点X坐标。
3.Y:切槽的终止点Y坐标。
4.Z:每次切割的深度。
5.K:每次切割的间隙。
通过解析上述参数,我们可以编写G74端面切槽循环编程的实例。
示例程序N10 G21 ; 设置刀具半径编程模式为公制N20 G94 ; 设置进给率为每分钟进给N30 G90 ; 设置绝对编程模式N40 G0 X0 Y0 Z0 ; 快速定位到切槽起点N50 G74 X100 Y50 Z5 K2 ; 执行G74端面切槽循环编程,终点为X =100,Y=50,每次切割深度为5,间隙为2N60 M30 ; 程序结束参数解析在上述实例程序中,我们对编程指令进行了解析:•第10行设置刀具半径编程模式为公制。
•第20行设置进给率为每分钟进给。
•第30行设置绝对编程模式。
•第40行通过G0指令快速定位到切槽起点。
•第50行执行G74端面切槽循环编程,终点为X=100,Y=50,每次切割深度为5,间隙为2。
•第60行结束程序。
通过以上实例程序,我们可以清楚地了解到G74端面切槽循环编程的使用方法和参数的意义。
总结本文介绍了G74端面切槽循环编程的实例,通过编程指令和参数解析来说明其用法和意义。
希望这篇文章可以帮助读者更好地理解和应用G74端面切槽循环编程。
G74端面切槽循环编程实例概述本文介绍了G74端面切槽循环编程的实例,包括编程指令和参数解析,旨在帮助读者更好地理解G74端面切槽循环编程的应用。
编程指令和参数解析在G74端面切槽循环编程中,有以下几个主要的编程指令和参数:1.G74:选择G74端面切槽循环编程。
2.X:切槽的终止点X坐标。
G74 G75 切槽指令教案

教学类型:理论课
教学目标要求(分了解、熟悉、掌握三个层次):
1.熟悉 G75/G74 指令编程的格式。
2.掌握 G75/G74 指令编程的操作与加工。
教学方式、手段、媒介:
➢ 多媒体课件授课。 教学内容(多媒体课件设计并注明:*重点 #难点 ?疑点)
讨论、思考题、作业: 作业: 1. 指令格式 G75 R(e)
G75 X()Z()P(Δi)Q(Δk)R(Δd)F() 2. 指令格式 G74 R(e)
G74 X()Z()P(Δi)Q(Δk)R(Δd)F() 教学反思:
通过学生熟练掌握 G75/G74 指令去编程,在编程的过程中反 复使用 G75/G74 指令,并通过大量的练习达到举一反三的的程度。
◆ Δk 为 Z 方向的每次切深量,用不带符号的半径量表示;
三、切槽加工工艺
• 1)切槽刀具: • 包括外圆、内孔、端面切槽刀具 • • 2)切槽刀几何参数 • • 3)切槽加工方法 • ◆一般要求切槽刀刀尖与工件轴线 • 等高,而且刀头与工件轴线垂直. • • ◆精度要求较高的沟槽,一般采用 二次进给车成. • 车较宽的沟槽,可以采用多次直进法切割, • 并在槽壁及底面留精加工余量,最后一刀 • 精车至尺寸较小的梯形槽一般用成形刀车 • 削完成. 较大的梯形槽,通常先车直槽,然 • 后用梯形刀直进法或左右切削法完成.
不带符号的值表; • • ◆ Δd 为刀具在切削底部的 Z 向退刀量,无要求时可省略;
二、轴向切槽循环 G74 切槽加工 * • 1)指令格式 • G74 R(e) • G74 X()Z()P(Δi)Q(Δk)R(Δd)F() •
◆ Δi 为刀具完成一次轴向切削后,在 X 方向的偏移量, • 用不带符号的值表示;
模块四内外端面数控车床加工编程
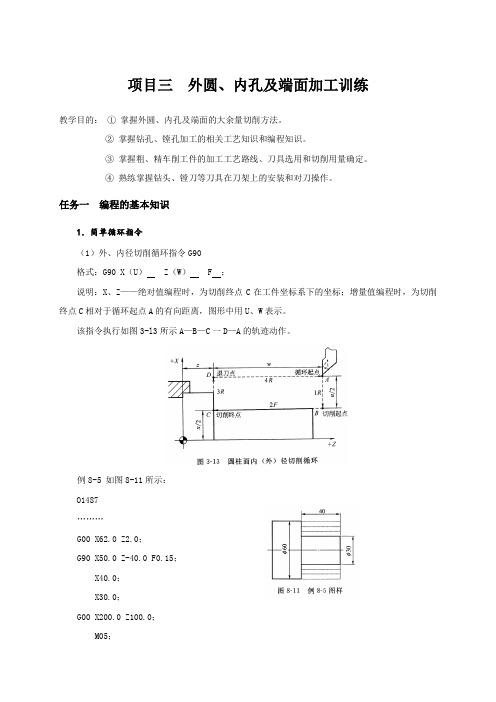
项目三外圆、内孔及端面加工训练教学目的:①掌握外圆、内孔及端面的大余量切削方法。
②掌握钻孔、镗孔加工的相关工艺知识和编程知识。
③掌握粗、精车削工件的加工工艺路线、刀具选用和切削用量确定。
④熟练掌握钻头、镗刀等刀具在刀架上的安装和对刀操作。
任务一编程的基本知识1.简单循环指令(1)外、内径切削循环指令G90格式:G90 X(U) Z(W) F ;说明:X、Z——绝对值编程时,为切削终点C在工件坐标系下的坐标;增量值编程时,为切削终点C相对于循环起点A的有向距离,图形中用U、W表示。
该指令执行如图3-l3所示A—B—C一D—A的轨迹动作。
例8-5 如图8-11所示:O1487………G00 X62.0 Z2.0;G90 X50.0 Z-40.0 F0.15;X40.0;X30.0;G00 X200.0 Z100.0;M05;M30;(2)圆锥面内(外)径切削循环指令G90 (如图8-12所示)格式:G90 X (U ) Z (W ) R F ;R ——为切出点到切入点在X 轴上的投影,与X 轴同向取正,与X 轴反向取负(无论是绝对值编程还是增量值编程)。
如图8-12所示根据相似三角形公式: 522030=-=h 2+=BE R BE h 220205+=R 5.5=R又因切出点到切入点在X 轴的投影为R 值,R 方向与X 正向相反,所以R=-5.5mm 。
O0002………G00 X42.0 Z2.0G90 X30.0 Z-20.0 R-5.5 F0.15G00 X200.0 Z100.0………(3)端平面切削循环指令G94该指令主要用于盘套类零件的平面粗加工工序。
格式:G94 X (U ) Z (W ) F ;该指令执行如图3-17所示A ——B ——C ——D ——A 的轨迹动作。
例8-6 如图8-14所示,用G94指令编写程序。
O1234………G00 X62.0 Z2.0;G94 X10.0 Z-3.0 F0.2;Z-5.0;X30.0 Z-7.0;Z-10.0;G00 X200.0 Z100.0;………(4)带锥度的端面切削循环指令 G94该指令主要用于盘套类带锥度的圆锥面零件的粗加工工序。
G74深孔加工循环指令课件
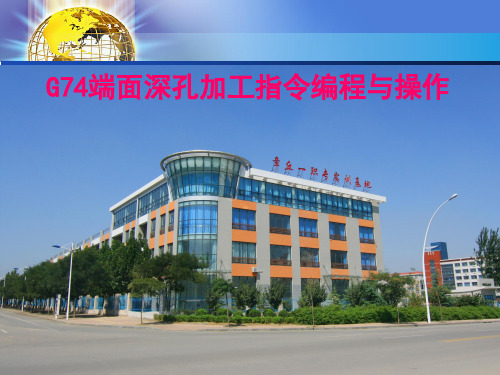
10-G74、G75指令
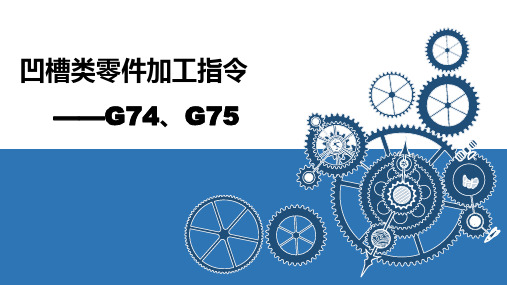
G74 R(e); G74 X(U) Z(W) P(i)Q(k)R(d)F(f);
凹槽加工指令
G74 R(e); G74 X(U) Z(W) P(i)Q(k)R(d)F(f);
式中:
e:每次沿Z方向切削k后的退刀量。没有指定R(e) 时,用参数也可以设定。
根据程序指令,参数值也改变。
X:B点的X方向绝对坐标值。 U:A到B沿X方向的增量。 Z:C点的Z方向绝对坐标值。 W:A到C沿Z轴方向的增量。 i:X方向的每次循环移动量(无符号,单位:微米)(直径)。 k:Z方向的每次切削移动量(无符号,单位:微米)。 d:切削到终点时X方向的退刀量(直径),通常不指定,省略X(U) 和i时,则视为0。 f:进给速度。
凹槽类零件加工指令 ——G74、G75
切槽基础知识介绍
凹槽加工指令
1、凹槽加工的特点
外圆切槽加工:对于粗加工宽槽或方肩间的车削,最常用的加工方法为多步切屑、陷入车削和坡走车削,需 要单独的精加工。如果槽宽比槽深小,则推荐执行多步切槽工序;如果槽宽比槽深要大,则推荐使用陷入车 削工序;如果棒材或零件细长或强度低,推荐进行坡走车削。
刀片宽度的选择:一方面要考虑到刀具强度和稳定性,另一方面又要同时考虑到节省工件材料和降低切削力。对于小 直径棒材或零件的切断,选择较小的刀片宽度和锋利的切削刃来降低切削力。切断薄壁管材时,可使用宽度尺可能小 的锋利刀片来降低切削力。
G74指令介绍
凹槽加工指令
端面深孔加工循环指令—G74
1、功能: 用于端面深孔加工
根据程序指令,参数值也改变。
X:C点的X方向绝对坐标值。 U:A到C的增量。 Z:B点的Z方向绝对坐标值。 W:A到B的增量。 i:X方向的每次循环移动量(无符号单位:微米)(直径)。 k:Z方向的每次切削移动量(无符号单位:微米)。 d:切削到终点时Z方向的退刀量,通常不指定,省略X(U) 和i时,则视为0。 f:进给速度。
数控车床g74编程实例

数控车床g74编程实例
以下是一个使用数控车床G74编程指令车削端面槽的实例:
槽大径为35.0毫米,小径为25.0毫米,槽宽为(大径-小径)/2=5.0毫米。
使用3.0毫米宽度的槽刀,以槽刀的下表面为x向的对刀点,假设槽刀的对刀点在25毫米。
编程:
G99M03 s600 T0101 M08
G0X25.2 z2.0(定位,设槽的端面为零点)
G74 R0.5(每次切削退刀)
G74X35.0(终点坐标)
z-5.0(分层第一刀,终点坐标)
p30000(x向平移量6毫米)
Q15000(z向每次背吃刀)
F0.03
G0Z2.0
Z-4.8(第二次定位进刀)
G74 R0.5
G74X35.0 z-10.0
p30000
Q15000
F0.03
G0Z2.0
G01x24.99F0.04
Z-10.0
X25.1
G0z2.0
X180.0 z180.0
M30
在使用数控车床G74编程指令时,需要根据实际情况设置合适的参数,以确保加工的顺
利进行。
如果你需要其他编程实例,可以提供更详细的加工要求,再次向我提问。
数控车床g74钻孔编程实例及解释

数控车床g74钻孔编程实例及解释数控车床是一种重要的机械加工设备,它可以通过编程自动化地进行精密加工。
其中,G74钻孔编程是常用的加工方式之一。
本文将介绍数控车床G74钻孔编程的实例及其解释。
2. G74钻孔编程实例以一个直径为10mm、深度为50mm的钻孔为例,其G74钻孔编程如下:N1 G90 G54 G00 X0. Y0. S3000 M03N2 G43 Z10. H1N3 G81 R5. Z-50. F200.N4 G80N5 M05N6 M30其中,各行指令的含义及解释如下:N1:程序号码G90:绝对编程G54:使用工作坐标系1G00 X0. Y0.:快速定位到坐标原点S3000 M03:主轴转速设定为3000转/分,主轴顺时针旋转N2:程序号码G43 Z10. H1:Z轴加工长度补偿,H1表示使用T0101工具补偿 N3:程序号码G81 R5. Z-50. F200.:钻孔循环指令,R5.表示半径为5mm,Z-50.表示加工深度为50mm,F200.表示进给速度为200mm/minN4:程序号码G80:钻孔循环结束N5:程序号码M05:主轴停止旋转N6:程序号码M30:程序结束3. 解释G74钻孔编程是一种循环加工方式,可以快速、精确地进行钻孔加工。
该编程方式可以通过设定循环开始点和循环结束点,实现自动化加工。
在上述实例中,N3行指令中的G81指令表示钻孔循环开始,G80指令表示钻孔循环结束。
此外,G43指令用于Z轴加工长度补偿,可以消除刀具长度的误差。
在实例中,H1表示使用T0101工具补偿,即补偿长度为10mm的刀具误差。
4. 结论本文介绍了数控车床G74钻孔编程的实例及其解释。
该编程方式可以实现自动化、高效、精确地进行钻孔加工,大大提高了生产效率和产品质量。
g74车锥度编程实例
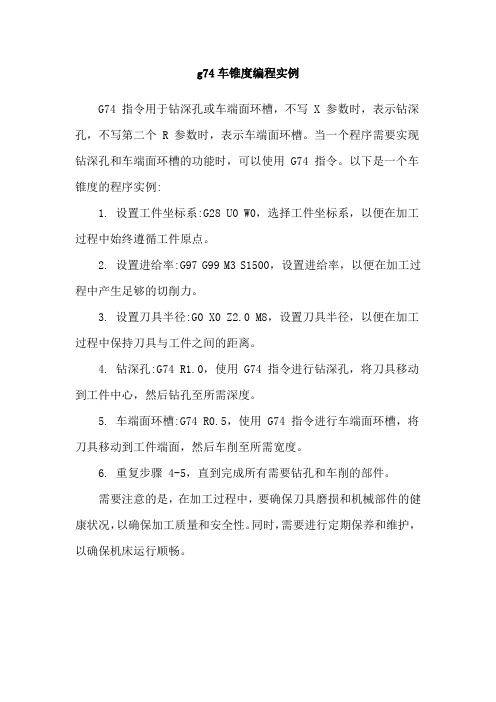
g74车锥度编程实例
G74 指令用于钻深孔或车端面环槽,不写 X 参数时,表示钻深孔,不写第二个 R 参数时,表示车端面环槽。
当一个程序需要实现钻深孔和车端面环槽的功能时,可以使用 G74 指令。
以下是一个车锥度的程序实例:
1. 设置工件坐标系:G28 U0 W0,选择工件坐标系,以便在加工过程中始终遵循工件原点。
2. 设置进给率:G97 G99 M3 S1500,设置进给率,以便在加工过程中产生足够的切削力。
3. 设置刀具半径:G0 X0 Z2.0 M8,设置刀具半径,以便在加工过程中保持刀具与工件之间的距离。
4. 钻深孔:G74 R1.0,使用 G74 指令进行钻深孔,将刀具移动到工件中心,然后钻孔至所需深度。
5. 车端面环槽:G74 R0.5,使用 G74 指令进行车端面环槽,将刀具移动到工件端面,然后车削至所需宽度。
6. 重复步骤 4-5,直到完成所有需要钻孔和车削的部件。
需要注意的是,在加工过程中,要确保刀具磨损和机械部件的健康状况,以确保加工质量和安全性。
同时,需要进行定期保养和维护,以确保机床运行顺畅。
- 1、下载文档前请自行甄别文档内容的完整性,平台不提供额外的编辑、内容补充、找答案等附加服务。
- 2、"仅部分预览"的文档,不可在线预览部分如存在完整性等问题,可反馈申请退款(可完整预览的文档不适用该条件!)。
- 3、如文档侵犯您的权益,请联系客服反馈,我们会尽快为您处理(人工客服工作时间:9:00-18:30)。
教案
【授课科目】数控车床编程与操作 7.5端面深孔加工循环(G74) 【授课日期及学时】2013年10月8日 2课时共90分钟
【授课班级】12机械【授课类型】新授课【教学目标】
1.知识目标:①了解G74指令的作用及使用时的注意事项
②了解G74指令的格式及G74指令各参数的含义
③掌握G74指令的运用
2.技能目标:①能运用G74指令编钻孔及切削内孔程序
②能熟练运用斯沃数控仿真软件
【教学重点】
1.G74指令各参数的含义及编程方法
2.G74指令的功能及运用
【教学难点】
1.指令的格式及各参数的含义
2.编程与仿真
【教学方法】讲授法、演示法、分多媒体教学法
【教具、学具准备】多媒体
讲授新课
4.刀具起点
如图7-12的走刀路线示意图所示
(1)钻孔
X轴方向为0,Z轴方向比准备钻孔的长度长一些。
(2)车孔
X方向比准备加工的孔径大些,Z方向比准备加工的孔的长度长一些。
5.刀具加工完毕停留位置
回到刀具起刀点位置。
6.刀具选择
根据孔直径的大小和长度来选择钻头、刀具。
7.钻孔、镗孔的方法
(1)钻头、镗孔刀的安装及对刀的方法
钻头、镗孔刀的安装。
同其他车刀一样装在刀架上。