火法炼铜工艺
铜冶炼的工艺流程及原理
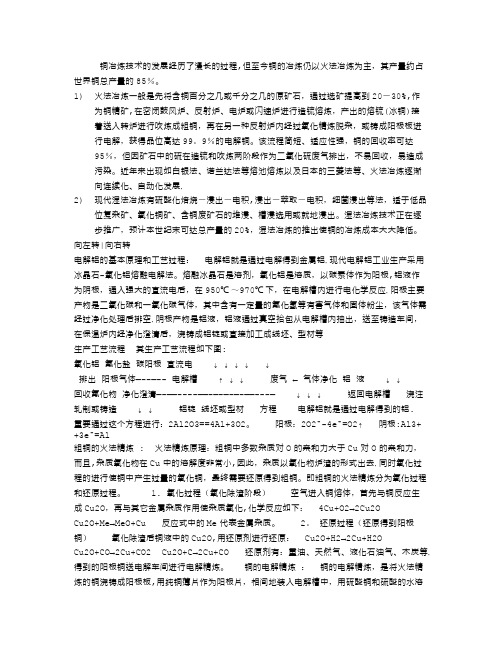
铜冶炼技术的发展经历了漫长的过程,但至今铜的冶炼仍以火法冶炼为主,其产量约占世界铜总产量的85%。
1)火法冶炼一般是先将含铜百分之几或千分之几的原矿石,通过选矿提高到20-30%,作为铜精矿,在密闭鼓风炉、反射炉、电炉或闪速炉进行造锍熔炼,产出的熔锍(冰铜)接着送入转炉进行吹炼成粗铜,再在另一种反射炉内经过氧化精炼脱杂,或铸成阳极板进行电解,获得品位高达99。
9%的电解铜。
该流程简短、适应性强,铜的回收率可达95%,但因矿石中的硫在造锍和吹炼两阶段作为二氧化硫废气排出,不易回收,易造成污染。
近年来出现如白银法、诺兰达法等熔池熔炼以及日本的三菱法等、火法冶炼逐渐向连续化、自动化发展.2)现代湿法冶炼有硫酸化焙烧-浸出-电积,浸出-萃取-电积,细菌浸出等法,适于低品位复杂矿、氧化铜矿、含铜废矿石的堆浸、槽浸选用或就地浸出。
湿法冶炼技术正在逐步推广,预计本世纪末可达总产量的20%,湿法冶炼的推出使铜的冶炼成本大大降低。
向左转|向右转电解铝的基本原理和工艺过程:电解铝就是通过电解得到金属铝.现代电解铝工业生产采用冰晶石-氧化铝熔融电解法。
熔融冰晶石是溶剂,氧化铝是溶质,以碳素体作为阳极,铝液作为阴极,通入强大的直流电后,在950℃~970℃下,在电解槽内进行电化学反应.阳极主要产物是二氧化碳和一氧化碳气体,其中含有一定量的氟化氢等有害气体和固体粉尘,该气体需经过净化处理后排空.阴极产物是铝液,铝液通过真空抬包从电解槽内抽出,送至铸造车间,在保温炉内经净化澄清后,浇铸成铝锭或直接加工成线坯、型材等生产工艺流程其生产工艺流程如下图:氧化铝氟化盐碳阳极直流电↓ ↓ ↓ ↓ ↓排出阳极气体—--—-- 电解槽↑ ↓ ↓ 废气← 气体净化铝液↓ ↓回收氟化物净化澄清—-——----——-—-—-—-——---—↓ ↓ ↓ 返回电解槽浇注轧制或铸造↓ ↓ 铝锭线坯或型材方程电解铝就是通过电解得到的铝. 重要通过这个方程进行:2Al2O3==4Al+3O2。
火法冶炼基本工艺知识1

一、炼铜原料与炼铜工艺
(三)炼铜工艺比较
• 火法工艺:受到环境和成本的压力,传统工艺逐步为现代强化熔 炼工艺所取代,生产规模不断扩大,成本优势明显,硫的捕集率 超过99%,改变了高能耗、高污染的形象 • 湿法工艺:火法难以利用的铜原料,包括低品位废石的利用;尾 矿处理;难选硫化矿;难熔矿;废弃的矿山;开采成本很高的深 矿井;高杂质(As、Sb、Bi)原料,多金属(Ni、Co、Zn)原料。 小规模生产的投资低,生产成本低成本低,不生产硫酸,无SO2 污染。操作简单,在矿山附近就近生产。贵金属回收困难,回收 率不确定。处理黄铜矿精矿的湿法工艺还没有工业应用,存在技 术障碍。 • 再生铜:单位能耗为矿产铜的20%,每利用1吨废杂铜,可少开 采矿石130吨,少产生2吨SO2 和100多吨工业废渣,节约用水535 立方米
二、火法炼铜基本工艺(二)传统炼铜工艺
熔炼:反射炉
精矿预 处理: 焙烧 烧结 混捏 制团 烟气制酸 电解精炼:常规始极片工艺 鼓风炉、电炉 冰铜吹炼: PS转炉 阳极精炼、浇铸
二、火法炼铜基本工艺
• 传统熔炼工艺的问题
目录
传统熔炼工艺:反射炉、电炉、鼓风炉,以反射炉为主;
熔炼强度低:送风氧浓低,冰铜品位低,生产效率低,能 耗高,成本高 生产能力低:单炉年产铜几千吨到几万吨 环境污染严重:SO2回收率低 自动化程度低,劳动强度大 60年代后期世界各地纷纷研究强化熔炼工艺
山东恒邦冶炼股份有限公司
火法冶炼
基本工艺原理
栾会光
一、炼铜原料与炼铜工艺 二、火法炼铜基本工艺 三、先进熔炼工艺 四、铜锍吹炼 五、冶炼二公司火法冶炼工艺
目录
一、炼铜原料与炼铜工艺
一、炼铜原料与炼铜工艺
(一)炼
铜冶炼的工艺流程及原理

铜冶炼的工艺流程及原理第一篇:铜冶炼的工艺流程及原理铜冶炼技术的发展经历了漫长的过程,但至今铜的冶炼仍以火法冶炼为主,其产量约占世界铜总产量的85%。
1)火法冶炼一般是先将含铜百分之几或千分之几的原矿石,通过选矿提高到20-30%,作为铜精矿,在密闭鼓风炉、反射炉、电炉或闪速炉进行造锍熔炼,产出的熔锍(冰铜)接着送入转炉进行吹炼成粗铜,再在另一种反射炉内经过氧化精炼脱杂,或铸成阳极板进行电解,获得品位高达99.9%的电解铜。
该流程简短、适应性强,铜的回收率可达95%,但因矿石中的硫在造锍和吹炼两阶段作为二氧化硫废气排出,不易回收,易造成污染。
近年来出现如白银法、诺兰达法等熔池熔炼以及日本的三菱法等、火法冶炼逐渐向连续化、自动化发展。
2)现代湿法冶炼有硫酸化焙烧-浸出-电积,浸出-萃取-电积,细菌浸出等法,适于低品位复杂矿、氧化铜矿、含铜废矿石的堆浸、槽浸选用或就地浸出。
湿法冶炼技术正在逐步推广,预计本世纪末可达总产量的20%,湿法冶炼的推出使铜的冶炼成本大大降低。
向左转|向右转电解铝的基本原理和工艺过程:电解铝就是通过电解得到金属铝。
现代电解铝工业生产采用冰晶石-氧化铝熔融电解法。
熔融冰晶石是溶剂,氧化铝是溶质,以碳素体作为阳极,铝液作为阴极,通入强大的直流电后,在950℃~970℃下,在电解槽内进行电化学反应。
阳极主要产物是二氧化碳和一氧化碳气体,其中含有一定量的氟化氢等有害气体和固体粉尘,该气体需经过净化处理后排空。
阴极产物是铝液,铝液通过真空抬包从电解槽内抽出,送至铸造车间,在保温炉内经净化澄清后,浇铸成铝锭或直接加工成线坯、型材等生产工艺流程其生产工艺流程如下图:氧化铝氟化盐碳阳极直流电↓ ↓ ↓ ↓↓排出阳极气体------电解槽↑ ↓ ↓废气← 气体净化铝液↓ ↓回收氟化物净化澄清-----------------------↓ ↓ ↓返回电解槽浇注轧制或铸造↓ ↓铝锭线坯或型材方程电解铝就是通过电解得到的铝.重要通过这个方程进行:2Al2O3==4Al+3O2。
古代火法炼铜的原理是什么

古代火法炼铜的原理是什么古代火法炼铜是一种古老的冶炼方法,其原理是通过高温加热将含铜矿石中的铜矿石和杂质分离,从而得到纯铜。
下面我们详细介绍一下古代火法炼铜的原理。
首先,古代火法炼铜需要先选取合适的含铜矿石作为原料。
通常,富含铜矿石的矿石有黄铜矿、赤铁矿和蓝铜矿等。
含铜矿石中铜的含量通常比较低,需要通过火法炼铜的过程将其提取出来。
火法炼铜的主要步骤分为破碎矿石、矿石烧烤、矿石熔炼、炉渣处理和铜液提取等。
首先是矿石的破碎,将原料矿石经过粉碎机破碎成适当大小的颗粒,以便后续处理。
然后,破碎后的矿石被烧烤,将其加热至适当温度,以去除矿石中的水分、二氧化碳等挥发性物质,并将铜矿石转化为氧化铜。
在矿石烧烤后,将得到的熟矿与矿石中的硅酸盐和杂质一起放入熔炉中进行熔炼。
熔炉内加入石灰石或其他辅助剂,以提高熔炉温度和铜的产率。
熔炉内的温度达到数百度甚至上千度,使得矿石中的金属与非金属成分发生熔融和分离。
在熔化过程中,铜的密度较大,会沉淀到熔炉底部,形成熔炉底的铜液。
同时,其他非铜金属和氧化物等杂质则浮于铜液之上,形成炉渣。
熔炉内的炉渣经过冷却和固化后,可以进行分离和处理,以提取其中可能有价值的金属或其他物质。
提取得到的铜液可以进行进一步的精炼和加工。
通常铜液是通过铁器制作的碳化剂来进行精炼。
在加热的过程中,铁反应性较强,会与铜液中的含氧物质进行反应,从而将铜中的杂质氧化成为炉渣,以提高铜的纯度。
最后,精炼后的铜液经过冷却和凝固,形成铜块。
铜块可以被再次加热和锻造,以改善其结构和性能,得到所需的铜质产品。
总体来说,古代火法炼铜的原理是通过高温熔炼和氧化还原反应,将含铜矿石中的铜分离出来。
矿石经过破碎和烧烤后,被放入熔炉进行熔炼。
在熔炼过程中,矿石中的铜密度较大,会沉淀到熔炉底部形成铜液,而其他杂质会浮于铜液之上形成炉渣。
炉渣经过处理后,可以得到纯铜。
最后精炼的铜液形成铜块,凝固后可进一步加工。
这就是古代火法炼铜的原理。
火法炼铜工艺讲解

3处,矿(化)点51处,
16.86万吨。成因类型有硅卡岩型、热液型、沉积型和火山岩型,以前
皇台铜矿,位于蟒岭岩体与前奥陶系大理岩形成的硅卡岩中,矿石矿
0.5~1.4%,铁品位可达
%,探明储量40365吨。柞水穆家庄铜矿,位于中泥盆统青石垭组的粉砂质千
1.07%,提交D+E级普查储量
万吨。热液型铜矿区内分布近40处,分布在商州市两水寺、古墓沟,山阳
曹异生 我国铜工业现状及前景展望 中国金属通报 2006 .
付少华 铜精矿供应瓶颈日益凸现 甘肃冶金 2007.
国土资源部信息中心 世纪之交的矿产资源形势2000 .
王红鹰 郑伟 铜的浸出-萃取-电积工艺及萃取剂 湿法冶金 2002 .
三十里铺、红铜沟,商南县过风楼等地。伴生铜矿在本区也有分布,
工艺流程图
熔剂
炼前准备
烟气处理
铜锍铜锍吹炼炉渣贫化鼓风熔剂弃渣
粗铜
渣浮选
熔剂燃料渣精矿尾矿
阳极板反熔炼胆矾鼓风
炉渣铜锍
设计的内容
火法炼铜是当今生产铜的主要方法,其产量占铜生产量的80%-90%,主要
3.1焙烧
“死焙烧”),分别脱除精矿中部分或全部
+FeO+SO2
=Fe3O4+SO2
=2Fe3O4
S+3/2O2=Cu2O+SO2
=2SO2
ห้องสมุดไป่ตู้
5/2O2=Cu2S·FeS+2SO2+FeO
+7/2O2=FeS+FeO+3SO2
=2FeO·SiO2
Fe
O4而不完全是
,也有一部分Cu
火法冶炼铜及湿法冶炼铜工艺介绍

题,不利于贵金属等有价伴生元素的回收, 因此在工业上未得到广泛应用。
• 我国铜冶炼主要以火法冶炼为主,总产量占全 部铜产量约96%,我国也是采用铜冶炼工艺种 类最多的国家,国际上先进的铜冶炼技术在我 国大多已采用,且生产规模远大于其它国家, 同时仍存在大量采用落后生产工艺、污染严重 的中小型铜冶炼企业,根据《有色金属产业调 整和振兴规划》的要求,铜冶炼行业规划目标 是:按期淘汰落后产能,节能减排取得积极成 效,企业重组取得进展,创新能力明显增强, 资源保障能力进一步提高。
• 火法炼铜的原则流程如下,流程图见图
• 铜精矿(15~30%Cu)——造锍熔炼——冰 铜 (铜锍25~70%Cu)——吹炼——粗铜 (98~99%Cu)——火法精炼——阳极铜 (99%Cu)——电解精炼——电铜(99.9599.98%Cu)。
• 火法炼铜生产过程一般由以下几个工序组 成:备料、熔炼、吹炼、火法精炼、电解 精炼,最终产品为电解铜。配套工序:阳 极泥处理、余热回收、余热发电、烟气收 尘、烟气制酸、循环水系统等。
• 火法冶炼铜主要产物环节如下:
• 除火法工艺外,近20 年来湿法炼铜工艺也取 得了长足的进步,湿法工艺不仅可以处理一些 难选的氧化矿和表外矿、铜矿废石等,而且随 着细菌浸出和加压浸出的发展,亦可以处理硫 化铜矿石,并能获得较好的经济效益,从而大 大拓宽了铜资源综合利用范围。该法是在常温 常压或高压下,用溶剂浸出矿石或焙烧矿中的 铜,经过净液,使铜和杂质分离,而后用萃取 -电积法,将溶液中的铜提取出来。对氧化矿 和自然铜矿,大多数工厂用溶剂直接浸出;对 硫化矿,一般先经焙烧,而后浸出。
火法冶炼及湿法冶炼 铜工艺介绍
• 铜的冶炼工艺有火法冶炼和湿冶炼两种 方法。
火法炼铜基本工艺
火法炼铜基本工艺
火法炼铜是一种传统的冶炼工艺,基本工艺流程如下:
1. 精选铜原料:选择含有一定铜矿物的矿石,经过破碎、分级等工艺后得到铜精矿;
2. 烧结煅烧:将铜精矿在高温下进行烧结煅烧处理,使铜矿中的硫化物和杂质被氧化,生成含铜的氧化物;
3. 氧化焙烧:将氧化铜还原为粒状的金属铜,铜粒和氧化物混合后进行氧化焙烧,使粒状铜和氧化物分离;
4. 熔炼:将铜粒通过熔炼,在高温下加入石灰、煤等辅助物质,使残留的氧化物得到还原,生成金属铜;
5. 铜的加工:将金属铜进行加工,得到不同形态的铜材料,如铜板、铜管等。
以上就是火法炼铜的基本工艺流程,这种工艺可以通过简单的设备和工艺步骤得到较高纯度的金属铜。
铜的加工冶炼工艺流程
铜的加工冶炼工艺流程火法炼铜是当今生产铜的主要方法,占铜产量的80%左右,主要是处理硫化矿。
火法炼铜的优点是原料适应性强,能耗低,效率高,金属回收率高。
火法炼铜可分两类:一是传统工艺:如鼓风炉熔炼、反射炉熔炼、电炉熔炼。
二是现代强化工艺:如闪速炉熔炼、熔池熔炼。
由于20世纪中叶以来全球性的能源和环境问题突出,能源日趋紧张,环境保护法规日益严格,劳动成本逐步上涨,促使铜冶炼技术从20世纪80年代起获得飞速发展,迫使传统的方法不得不被新的强化方法来代替,传统冶炼方法逐渐被淘汰。
随之兴起的是以闪速熔炼和熔池熔炼为代表的强化冶炼先进技术,其中最重要的突破是氧气或富氧的广泛应用。
经过几十年的努力,闪速熔炼与熔池熔炼已基本取代传统火法冶炼工艺。
1、火法冶炼工艺流程火法工艺过程主要包括四个主要步骤:造锍熔炼、铜锍(冰铜)吹炼、粗铜火法精炼和阳极铜电解精炼。
造硫熔炼(铜精矿—冰铜):主要是使用铜精矿造冰铜熔炼,目的是使铜精矿部分铁氧化,造渣除去,产出含铜较高的冰铜。
冰铜吹炼(冰铜—粗铜):将冰铜进一步氧化、造渣脱除冰铜中的铁和硫,生产粗铜。
火法精炼(粗铜—阳极铜):将粗铜通过氧化造渣进一步脱除杂质元素,生产阳极铜。
电解精炼(阳极铜—阴极铜):通过引入直流电,阳极铜溶解,在阴极析出纯铜,杂质进入阳极泥或电解液,从而实现铜和杂质的分离,产出阴极铜。
火法炼铜一般流程图2、火法冶炼工艺分类(1)闪速熔炼闪速熔炼(flash smelting)包括国际镍公司因科(Inco)闪速炉、奥托昆普(Outokumpu)闪速炉和旋涡顶吹熔炼(ConTop)3种。
闪速熔炼是充分利用细磨物料巨大的活性表面,强化冶炼反应过程的熔炼方法。
将精矿经过深度干燥后,与熔剂经干燥一起用富氧空气喷入反应塔内,精矿粒子在空间悬浮1-3s时间,与高温氧化性气流迅速发生硫化矿物的氧化反应,并放出大量的热,完成熔炼反应即造锍的过程。
反应的产物落入闪速炉的沉淀池中进行沉降,使铜锍和渣得到进一步的分离。
火法炼铜工艺讲解
火法炼铜工艺讲解1 概述铜是人类应用的最古老的金属之一,它有很长的、很光辉的历史。
考古学证明,早在一万年前,西亚人已用铜制作装饰品之类的物件。
铜和锡可制成韧性合金青铜,考古发现在公元前约3000年,历史已进入了青铜时代。
而今铜的化学、物理学和美学性质使它成为广泛应用于家庭、工业和高技术的重要材料。
铜具有优良可锻性、耐腐蚀性、韧性,适于加工;铜的导电性仅次于银,而其价格又较便宜,故而被广泛应用于电力;铜的导热性能也颇佳;铜和其他金属如锌、铝、锡、镍形成的合金,具有新的特性,有许多特殊的用途。
铜是所有金属中最易再生的金属之一,再生铜约占世界铜供应总量的40%。
铜以多种形态在自然环境中存在,它存在于硫化物矿床中(黄铜矿、辉铜矿、斑铜矿、蓝铜矿)、碳酸盐矿床中(蓝铜矿、孔雀石)和硅酸盐矿床中(硅孔雀石、透视石),也以纯铜即所谓“天然铜”的形态存在。
铜以硫化矿或氧化矿形式露天开采或地下开采,采出矿石经破碎后,再在球磨机或棒磨机中磨细。
矿石含铜一般低于1%。
1.1 国内外铜冶金的发展现状目前国内外的铜冶炼技术的发展主要还是以火法冶炼为主,湿法为辅。
铜的火法生产量占总产量的80%左右。
目前,全世界约有110座大型火法炼铜厂。
其中,传统工艺(包括反射炉、鼓风炉、电炉)约占1/3;闪速熔炼(以奥托昆普炉为主)约占1/3;熔池熔炼(包括特尼恩特炉、诺兰达炉、三菱炉、艾萨炉、中国的白银炉、水口山炉等)约占1/3。
另外,世界范围内铜冶金工业同样面临铜矿资源短缺的问题,国土资源部信息中心统计资料表明:在世界范围内,铜是仅次于黄金的第2个固体矿产勘查热点,全球固体矿产勘查支出中约20%是找铜的,并且这一比例还有增加的趋势。
相应地,铜也是各大势力集团争夺的焦点之一。
从全球角度看铜的保证年限只有约29年。
铜的主要出口国是拉美发展中国家。
1.2商洛情况全市已发现各类矿产60种,已探明矿产储量46种,其中大型矿床15处,中型矿床24处。
火法炼铜的概述
火法炼铜的概述
火法炼铜是一种利用化学反应炼制铜的方法,其介质为高温的氧
化还原环境。
这种炼铜方法广泛应用于铜矿山及冶炼厂。
首先,在火法炼铜的过程中,铜矿石被破碎成较小的颗粒,并被
投放到高温炉中。
当铜矿石在炉中进行热处理时,其大部分硫化了的
铜会与氧气结合产生氧化铜。
同时,含铁杂质也被氧气氧化成了铁氧
化物。
第二步,由于铜氧化物在高温下易于分解,故它可以在经过一段
时间的处理后被还原回铜金属。
在这个过程中,还用到了沃尔福氧化
物和火碳。
沃尔福氧化物具有还原性能,当它与空气混合时,会产生
大量的热能,这样可以使铜氧化物迅速还原。
而火碳在高温环境下会
发生还原反应,将铜氧化物还原成铜金属。
随后,铜金属被剥离出来,熔化并收集。
第三步,由于炼铜的过程涉及到诸多复杂的化学反应,故需要进
行精密的控制以保证整个过程的顺利进行。
其中包括控制炉温、燃料
供应、气流速率和化学药物的添加等诸多方面。
这些控制手段能够确
保铜的质量和纯度符合所需标准。
火法炼铜是一种十分高效的炼铜方式,它可以从铜矿石中提取出
高品质的铜金属,并且减少了需要使用的有毒化学品的量。
同时,炼
铜过程中所排放的废气、尘土等废弃物也可以得到有效的处理。
作为
一种环保的炼铜方式,它能够为地球环境做出更大的贡献。
总体来说,火法炼铜是一种高效且环保的炼铜方式,具有很高的实用价值。
它的建立对提高工业化后现代社会的科技水平发挥了重要作用,能够更好地促进铜矿开采和应用,造福了人类社会的发展。
- 1、下载文档前请自行甄别文档内容的完整性,平台不提供额外的编辑、内容补充、找答案等附加服务。
- 2、"仅部分预览"的文档,不可在线预览部分如存在完整性等问题,可反馈申请退款(可完整预览的文档不适用该条件!)。
- 3、如文档侵犯您的权益,请联系客服反馈,我们会尽快为您处理(人工客服工作时间:9:00-18:30)。
1 概述铜是人类应用的最古老的金属之一,它有很长的、很光辉的历史。
考古学证明,早在一万年前,西亚人已用铜制作装饰品之类的物件。
铜和锡可制成韧性合金青铜,考古发现在公元前约3000年,历史已进入了青铜时代。
而今铜的化学、物理学和美学性质使它成为广泛应用于家庭、工业和高技术的重要材料。
铜具有优良可锻性、耐腐蚀性、韧性,适于加工;铜的导电性仅次于银,而其价格又较便宜,故而被广泛应用于电力;铜的导热性能也颇佳;铜和其他金属如锌、铝、锡、镍形成的合金,具有新的特性,有许多特殊的用途。
铜是所有金属中最易再生的金属之一,再生铜约占世界铜供应总量的40%。
铜以多种形态在自然环境中存在,它存在于硫化物矿床中(黄铜矿、辉铜矿、斑铜矿、蓝铜矿)、碳酸盐矿床中(蓝铜矿、孔雀石)和硅酸盐矿床中(硅孔雀石、透视石),也以纯铜即所谓“天然铜”的形态存在。
铜以硫化矿或氧化矿形式露天开采或地下开采,采出矿石经破碎后,再在球磨机或棒磨机中磨细。
矿石含铜一般低于1%。
1.1 国外铜冶金的发展现状目前国外的铜冶炼技术的发展主要还是以火法冶炼为主,湿法为辅。
铜的火法生产量占总产量的80%左右。
目前,全世界约有110座大型火法炼铜厂。
其中,传统工艺(包括反射炉、鼓风炉、电炉)约占1/3;闪速熔炼(以奥托昆普炉为主)约占1/3;熔池熔炼(包括特尼恩特炉、诺兰达炉、三菱炉、艾萨炉、中国的炉、水口山炉等)约占1/3。
另外,世界围铜冶金工业同样面临铜矿资源短缺的问题,国土资源部信息中心统计资料表明:在世界围,铜是仅次于黄金的第2个固体矿产勘查热点,全球固体矿产勘查支出中约20%是找铜的,并且这一比例还有增加的趋势。
相应地,铜也是各大势力集团争夺的焦点之一。
从全球角度看铜的保证年限只有约29年。
铜的主要出口国是拉美发展中国家。
1.2情况全市已发现各类矿产60种,已探明矿产储量46种,其型矿床15处,中型矿床24处。
储量居全省首位的有铁、钒、钛、银、锑、铼、水晶、萤石、白云母和钾长石等20种,其中柞水大西沟铁矿储量3.02亿吨,占全省的46%,居全省第二位的有铜、锌、钼、铅等13种。
铜矿主要分布于丹凤、山阳、柞水和商州,矿床3处,矿(化)点51处,探明储量16.86万吨。
成因类型有硅卡岩型、热液型、沉积型和火山岩型,以前三种为主。
皇台铜矿,位于蟒岭岩体与前奥系岩形成的硅卡岩中,矿石矿物有磁铁矿、黄铁矿、黄铜矿和少量铅锌矿。
铜矿品位0.5~1.4%,铁品位可达20%,探明储量40365吨。
柞水穆家庄铜矿,位于中泥盆统青石垭组的粉砂质千枚岩、白云岩和白云质粉砂岩中,矿石平均品位1.07%,提交D+E级普查储量3.689万吨。
热液型铜矿区分布近40处,分布在商州市两水寺、古墓沟,山阳县色河干沟、三十里铺、红铜沟,商南县过风楼等地。
伴生铜矿在本区也有分布,主要见于山阳黑沟多金属矿和柞水银洞子银铅矿、大西沟。
2.工艺流程图尾矿胆矾电解铜3设计的容火法炼铜是当今生产铜的主要方法,其产量占铜生产量的80%-90%,主要用于处理硫化矿。
工艺主要包括四个步骤,即造硫熔炼、铜锍吹炼、粗铜火法精炼和阳极铜电解精炼。
主要原料是硫化铜精矿。
3.1焙烧焙烧分半氧化焙烧和全氧化焙烧(“死焙烧”),分别脱除精矿中部分或全部的硫,同时除去部分砷、锑等易挥发的杂质。
此过程为放热反应,通常不需另加燃料。
造锍熔炼一般采用半氧化焙烧,以保持形成冰铜时所需硫量;还原熔炼采用全氧化焙烧;此外,硫化铜精矿湿法冶金中的焙烧,是把铜转化为可溶性硫酸盐,称硫酸化焙烧。
3.2造硫熔炼工艺原理:利于铜与硫的亲和力大于铁和一些杂质金属,而铁与氧的亲和力大于铜的特性,在高温及控制氧化气氛条件下,使铁等杂质金属逐步氧化后进入炉渣或烟尘被除去,而金属铜则富集在铜锍等各种中间产物中,并逐步得到提纯。
造锍熔炼其目在于,把炉料中全部的铜富集在铜锍相,把脉石、氧化物及杂质汇集与熔渣相,然后使铜锍相与熔渣相完全分离,分别产出铜锍和熔渣,为了达到这个目的,造锍熔炼过程必须遵循两个原则:一是必须使炉料有相当数量的硫来形成铜锍;二是使炉渣二氧化硅含量接近饱和,以使铜锍和炉渣不致混溶。
3.2.1造锍熔炼的传统设备造锍熔炼的传统设备为鼓风炉、反射炉、电炉等,新建的现代化大型炼铜厂多采用闪速炉。
闪速熔炼是将硫化铜精矿和熔剂的混合料干燥至含水0.3%以下,与热风(或氧气、或富氧空气)混合,喷入炉迅速氧化和熔化,生成冰铜和炉渣。
其优点是熔炼强度高,可较充分地利用硫化物氧化反应热。
降低熔炼过程的能耗。
烟气中SO2浓度可超过8%。
闪速熔炼可在较大围调节冰铜品位,一般控制在50%左右,这样对下一步吹炼有利。
但炉渣含铜较高,须进一步处理。
闪速炉有奥托昆普型和国际镍公司型两种。
70年代末世界上已有几十个工厂采用奥托昆普型闪速炉,中国贵溪冶炼厂也采用此种炉型。
冰铜吹炼利用硫化亚铁比硫化亚铜易于氧化的特点,在卧式转炉中,往熔融的冰铜中鼓入空气,使硫化亚铁氧化成氧化亚铁,并与加入的石英熔剂造渣除去,同时部分脱除其他杂质,而后继续鼓风,使硫化亚铜中的硫氧化进入烟气,得到含铜98%~99%的粗铜,贵金属也进入粗铜中。
3.2.2闪速熔炼原理入炉的浮选硫化铜精矿粒度很细,一般90%以上小于0.074mm,比表面积达200m2/kg,熔炼过程中又处于悬浮状态,因而气-固或气-液间的传质和传热条件十分强化。
在高温作用下,大部分硫化物颗粒在反应塔仅停留2到3秒即可完成氧化脱硫、熔化、造渣等反应,并且放出大量的作为熔炼所需要的大部或全部能量。
分解反应分解反应包括黄铁矿、黄铜矿、高价硫化物的分解反应FeS2=FeS+1/2S2Fe n S n+1=nFeS+1/2S22CuFeS2=Cu2S+2FeS+1/2S22CuS=Cu2S+1/2S2氧化反应氧化反应是闪速熔炼代表反应,主要包括FeS+3/2O2+FeO+SO23FeS+5O2=Fe3O4+SO26FeO+O2=2Fe3O4Cu2S+3/2O2=Cu2O+SO2S+O2=2SO2高价硫化物直接氧化和造渣反应2CuFeS2+5/2O2=Cu2S·FeS+2SO2+FeO2FeS2+7/2O2=FeS+FeO+3SO22FeO+SiO2=2FeO·SiO2可见,在强氧化氛围中,铜精矿氧化不可避免地会产生Fe3O4而不完全是FeO,也有一部分Cu2S氧化成Cu2O。
另外,强氧化造成硫的大量氧化,为此需要通过控制氧化气氛来控制硫的氧化,以保证获得适当的铜锍。
氧化气氛通常用氧和硫、铁供给数量的百分比来表示,比值越大,氧化程度越大,铜锍品位越高;反之则越低。
通常控制氧和硫、铁的数量比为48%-50%。
相互反应相互反应在熔池中进行,主要反应如下:3Fe3O4+FeS=10FeO+SO23Fe3O4+FeS+5SiO2=5(2FeO·SiO2)+SO2Cu2O+FeS=Cu2S+FeO2FeO+SiO2=2FeO·SiO2反应结果使Cu2O以Cu2S形态进入铜锍,同时使部分Fe3O4还原成FeO造渣。
但是闪速熔炼时Fe3O4的还原条件是很差的,因此炉渣铜含量高。
3.2.3炉渣炉渣是矿石冶炼后的残留废弃物,但由于冶炼、提炼技术的不过关,炉渣中往往会残留很多有价值的未提取金属、矿物,这是一种极大的浪费行为。
炉渣的贫化就是提高矿石的冶炼、提炼技术,或者对炉渣进行二次处理,尽量提取矿石中的有价值物,使最终残留的炉渣"贫化",最终从而提高矿石的利用效率。
炉渣贫化技术的提高有助于提高资源的利用效率,减少企业生产成本和治三废成本,符合节约型社会的理念;同时减少炉渣对于环境的污染,有利于环境保护。
炉渣贫化方法的选择原则上取决于渣中铜的损失形态以及所要求的最终弃渣含铜水平。
贫化方法有两类:电炉贫化法和浮选法。
电炉贫化法矿热炉具有废气少、易于控制、能保证高温下有较强还原性等优点,可以提高熔渣温度,使渣中铜含量降低,有利于还原熔融渣中的氧化铜和回收细颗粒的铜粒子。
电炉贫化法可以处理各种成分的炉渣,也可以处理各种返料。
熔体中电流在电极间的流动产生的搅拌作用能够促进渣中的铜粒子的集聚长大。
电炉贫化法的最大优点是真正实现了对铅、钴、锌等易溶解于酸中金属的回收,但电耗及碳质电极材料消耗较高,需要向电耗更低、电极消耗更少的直流电炉改进。
浮选法从富氧熔炼渣(如闪速炉渣)和转炉渣中浮选回收铜,在炼铜工业上已得到广泛应用。
浮选法铜回收率高、能耗低(与电炉贫化、炉渣返回熔炼法比较),可以将Fe3O4及一些杂质从流程中除去,吹炼过程的石英用量将大幅度减少。
铜浮选收率一般在90%以上,所得的精矿中铜锍的质量分数大于20%,尾矿w(Cu)0.3%~0.5%。
王红梅等提出闪速浮选的概念,即是一种回收磨矿-分级回路循环负荷中粗粒矿物的浮选技术,随着技术的成熟,有望在炉渣选矿应用得到进一步广。
A1Sarrafi等在对反射炉渣浮选回收铜的研究中发现R407作为捕收剂可获得品位为1216%,铜回收率为72%的铜精矿,同时发现缓冷熔渣中铜的回收率可达84%。
浮选法虽然应用广、药剂用量小,但选矿药剂多数为有机物,有刺激性气味,且价格昂贵。
3.3铜锍吹炼铜锍吹炼的任务是将铜锍吹炼成含铜98.5%-99.5%的粗铜。
吹炼的实质是在一定的压力下将空气送到液体铜锍中,使铜锍中FeS氧化成FeO并与加入的石英或CaO熔剂造渣,Cu2S则与氧化生成的Cu2O发生相互反应而变成粗铜。
吹炼过程所需热量全靠熔锍中硫和铁的氧化及造渣反应所放出的热量供给,为自热过程。
吹炼过程的温度为1473-1523K。
冰铜含铜量取决于精矿品位和焙烧熔炼过程的脱硫率,世界冰铜品位一般含铜40%~55%。
生产高品位冰铜,可更多地利用硫化物反应热,还可缩短下一工序的吹炼时间。
熔炼炉渣含铜与冰铜品位有关,弃渣含铜一般在0.4%~0.5%。
熔炼过程主要反应为:2CuFeS2→Cu2S+2FeS+SCu2O+FeS→Cu2S+FeO2FeS+3O2+SiO2→2FeO·S iO2+2SO22FeO+SiO2→2FeO·SiO2吹炼一个吹炼周期分为两个阶段:第一阶段,将FeS氧化成FeO,造渣除去,得到白冰铜(Cu2S)。
冶炼温度1150℃~1250℃。
主要反应是:2FeS+3O2→2FeO+2SO22FeO+SiO2→2FeO·SiO2第二阶段,冶炼温度1200℃~1280℃将白冰铜按以下反应吹炼成粗铜:2Cu2S+3O2→2Cu2O+2SO2Cu2S+2Cu2O→6Cu+SO2冰铜吹炼是放热反应,可自热进行,通常还须加入部分冷料吸收其过剩热量。
吹炼后的炉渣含铜较高,一般为2%~5%,返回熔炼炉或以选矿、电炉贫化等方法处理。