汽车零部件的失效模式及其分析
FMEA(失效模式与影响分析)简介

没有影响;事件发生的频率要记录特定的失效原因和机理多长时间发生一次以及发生的几率。
如果为10,则表示几乎肯定要发生,工艺能力为0.33或者ppm大于10000。
5.2检测等级是评估所提出的工艺控制检测失效模式的几率,列为10表示不能检测,1表示已经通过目前工艺控制的缺陷检测。
5.3计算风险优先数RPN(riskprioritynumber)。
RPN是事件发生的频率、严重程度和检测等级三者乘积,用来衡量可能的工艺缺陷,以便采取可能的预防措施减少关键的工艺变化,使工艺更加可靠。
对于工艺的矫正首先应集中在那些最受关注和风险程度最高的环节。
RPN最坏的情况是1000,最好的情况是1,确定从何处着手的最好方式是利用RPN的pareto图,筛选那些累积等级远低于80%的项目。
推荐出负责的方案以及完成日期,这些推荐方案的最终目的是降低一个或多个等级。
对一些严重问题要时常考虑拯救方案,如:一个产品的失效模式影响具有风险等级9或10;一个产品失效模式/原因事件发生以及严重程度很高;一个产品具有很高的RPN值等等。
在所有的拯救措施确和实施后,允许有一个稳定时期,然后还应该对修订的事件发生的频率、严重程度和检测等级进行重新考虑和排序。
在设计和制造产品时,通常有三道控制缺陷的防线:避免或消除故障起因、预先确定或检测故障、减少故障的影响和后果。
FMEA正是帮助我们从第一道防线就将缺陷消灭在摇篮之中的有效工具。
FMEA是一种可靠性设计的重要方法。
它实际上是FMA(故障模式分析)和FEA(故障影响分析)的组合。
它对各种可能的风险进行评价、分析,以便在现有技术的基础上消除这些风险或将这些风险减小到可接受的水平。
及时性是成功实施FMEA的最重要因素之一,它是一个"事前的行为',而不是"事后的行为'。
为达到最佳效益,FMEA必须在故障模式被纳入产品之前进行。
FMEA实际是一组系列化的活动,其过程包括:找出产品/过程中潜在的故障模式;根据相应的评价体系对找出的潜在故障模式进行风险量化评估;列出故障起因/机理,寻找预防或改进措施。
(DFMEA)汽车行业设计失效模式分析
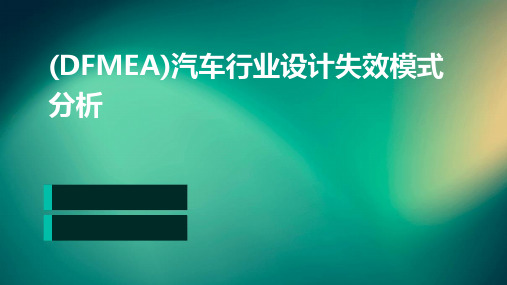
性能下降
随着使用时间的增加,发动机性能可能会逐渐下 降,导致汽车动力不足、加速缓慢等问题。这可 能是由于发动机内部零件磨损、燃油系统堵塞或 点火系统故障等原因引起的。
振动过大
发动机振动过大可能会对车辆的舒适性和稳定性 产生不良影响,同时也会增加零部件的磨损和疲 劳破坏。振动过大的原因可能包括发动机平衡性 差、零部件松动或损坏等。
不断更新表格,以反 映产品设计的更改和 改进。
确保表格内容完整、 准确,为后续分析提 供基础数据。
绘制设计流程图
01 详细绘制产品设计的流程图,包括各个组件的相 互关系和作用。
02 明确各个设计阶段的输入和输出,以便更好地理 解设计的整体流程。
03 分析流程图,找出可能存在的设计缺陷和失效模 式。
优化方法
采用先进的优化算法和仿真技术,对设计方案进行多目标优化。
优化过程
充分考虑制造工艺、材料特性等因素,确保优化方案的可行性。
提高制造质量
制造工艺
采用先进的制造工艺,提高零部件和整车的制造 精度和质量。
质量控制
建立严格的质量控制体系,确保每个环节的制造 质量符合要求。
质量检测
采用多种质量检测手段,如无损检测、功能检测 等,确保产品合格率。
03
基于影响评估,为每个故障模式制定相应的改进措施
和优先级。
03 汽车行业中的设计失效模 式
发动机系统
总结词
发动机系统是汽车的核心部分,其设计失效模式 主要表现在性能下降、过热、振动过大等方面。
过热
发动机过热是常见的失效模式之一,可能导致拉 缸、润滑油变质等严重后果。过热的原因可能包 括冷却系统故障、发动机负荷过大、散热器堵塞 等。
传动系统
汽车零部件的失效机理及其分析教材

第五节 汽车零部件变形失效机理
零件在使用过程中,由于承载或内部应力的作 用,使零件的尺寸和形状改变的现象称为零件的变形。 零件变形失效的类型有:
弹性变形失效
塑性变形失效 蛹变失效
第六节 汽车零部件失效分析方法
一.失效分析的基本思路
按分析检验项目进行失效分析
按失效模式进行分析 系统工程分析方法
影响因素 防治措施
思考题
1. 气缸-活塞环的磨损规律是什么? 为什么? 2. 零件磨损量如何测定?
参考答案
1. 气缸-活塞环的磨损规律是什么?为什么?
规律:高度方向,上大下小;圆周方向不规则
影响因素:磨料、工作气体压力、润滑和腐蚀 物质。 2. 零件磨损量如何测定?
直接测量法:表面测量法、称重法、刻痕法和 快速磨损法; 间接测量法:光谱分析法和同位素法。
四.提高汽车零件抗疲劳断裂的方法
延续疲劳裂纹萌生时间 降低疲劳裂纹扩展的速率 提高疲劳裂纹门槛值△km长度
思考题
1.
疲劳断裂与磨损的区别
损伤形式 比较因素 损坏形式 受力情况 表面变形 初始裂纹 疲劳磨损 疲劳断裂
第四节 汽车零部件腐蚀失效及其机 理
零件受周围介质作用而引起的损坏称为零件的 腐蚀。按腐蚀机理可分为化学腐蚀和电化学腐蚀, 汽车上约20%的零件因腐蚀而失效。
第一节 汽车零部件失效的概念及分 类
一.失效的概念
汽车零部件失去原设计所规定的功能称为失 效。 失效不仅是指完全丧失原定功能,而且还包 含功能降低和有严重损伤或隐患、继续使用 会失去可靠性及安全性的零部件。
二、失效的基本类型
三.零件失效的基本原因
整车设计失效模式分析-DFMEA

有毒有害物质 检测
3
座椅VOC超标
2
按 2005/673/EC 有毒有害物质
设计
检测
3
动力系统匹配不 当
5
整车总布置报告
NVH测试
2
噪声大:
传动系统匹配不 当
4
整车总布置报告
NVH测试
4
驾驶员耳旁
噪声不合 格; 车内噪声不
顾客抱怨,引 起驾驶疲劳
6
S
合格;
行驶系统设计不 当
4
车身各总成刚度 设计值不足
1999测定;
S
制动系统设计不 合理
3
设计评审 与参考车型对比
3
制动异响
顾客抱怨制动 有异响
7
S
制动系统设计不 合理
4
设计评审 与参考车型对比
样车动态评价
4
灯光照度不 够
影响行车安 全,违反法规
9
R
灯光照明系统设 计不合理
3
计算校核设计评 审
按 GB 459994附录D测 定;
2
灯光指示和信号 报警系统设计不 3 设计评审
2
设计计算
按GB
2
T6323.6-1994
悬架匹配计算
测定;
3
FMEA日期
造型
车身造型不美观 5
不美观
造型不美观顾 客不满意
6
R
外装饰系统造型 美观
5
造型评审 造型评审
样车评价 2 样车评价 2
跑偏
制动时方向
侧滑
稳定性差 失去转向能力
9
影响乘员安全
S
制动系统泄露
3
设计评审 与参考车型对比 按 GB 12676-
新版fmea案例

新版fmea案例在一家汽车零部件制造厂中,由于近期发生了多起产品质量问题,导致公司遭受了较大的经济损失和声誉受损,高层管理层意识到必须采取有效的措施来改善产品的质量。
因此,他们决定引入新版FMEA(失效模式与影响分析)方法来提前预防可能的失效模式,并采取相应的措施来减轻损失。
以下是一种新版FMEA方法的案例:首先,公司成立了一个由不同岗位的员工组成的跨部门团队,负责进行新版FMEA分析。
该团队包括设计人员、生产技术人员、品质控制人员以及售后服务人员。
他们共同制定了一个详细的工作计划,包括收集相关数据、分析失效模式和确定相应的控制措施。
团队首先收集了各个部门的历史数据,包括产品质量记录、客户投诉和售后服务的问题反馈。
通过对这些数据的分析,他们确定了几个重要的失效模式,包括产品组装不良、材料使用不当和设备故障等。
接下来,团队进行了详细的失效模式和影响分析。
他们根据每个失效模式的可能性、严重性和检测能力来对它们进行评估。
例如,对于产品组装不良这个失效模式,他们评估了造成客户事故的可能性、产品质量的影响程度以及生产线检测装置的能力。
在评估每个失效模式之后,团队开始制定相应的控制措施。
他们首先关注一些高风险的失效模式,采取主动的控制措施来减轻损失。
例如,对于产品组装不良的失效模式,他们决定增加更为严格的产品组装过程控制和检测步骤,以确保每个产品组装质量的稳定性。
同时,团队还制定了一系列培训计划,以提高员工的技能和意识。
他们认识到单纯的控制措施是不够的,员工的专业技能和操作规范同样重要。
因此,他们组织了一系列培训课程,包括质量控制、产品组装和设备维护等内容,以提高员工的整体素质。
最后,团队设立了一个监控机制,定期对已经实施的控制措施进行检查和评估。
他们收集相关的数据,并根据事故和客户投诉的情况调整控制措施。
这种迭代的过程使得FMEA分析更加灵活和有效。
通过引入新版FMEA方法,该厂成功地改进了产品质量并减少了损失。
FMEA失效模式及其影响分析
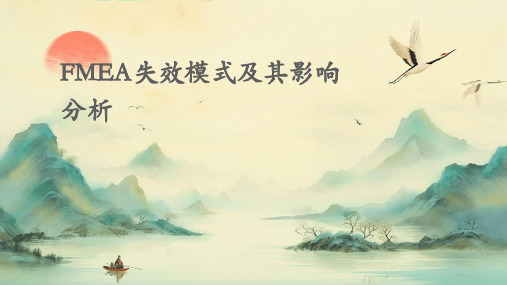
03
FMEA失效影响分析
直接和间接影响
直接影响
指失效模式对产品或系统的性能、安 全性、可靠性和可用性等直接造成的 影响。例如,电池的充电功能失效会 导致设备无法正常工作。
间接影响
指失效模式引发的连锁反应或次生问 题,可能涉及到供应链、生产、销售 和服务等环节。例如,关键零部件的 失效可能导致整条生产线停产。
制中的问题,提高产品的可靠性和安全性。
识别和评估
总结词
在FMEA失效模式分析中,识别和评估是关键步骤,需要全面考虑各种可能的失效模式,并对其影响进行量化评 估。
详细描述
在识别阶段,团队需要充分了解产品或过程的设计、制造和使用环境,找出可能出现的各种失效模式。这些失效 模式可能包括机械、电气、化学、热学等多个方面。在评估阶段,团队需要分析每种失效模式的发生概率、严重 程度以及可检测性,为后续的优先级排序提供依据。
静态性
FMEA通常在产品设计阶段进行,对后续生产和使用的动 态变化考虑不足,可能无法全面反映产品在实际使用中的 失效模式。
高成本
FMEA需要投入大量时间和资源进行数据收集、分析和改 进措施制定,对于小型企业或项目可能存在成本压力。
06
案例研究
案例一:汽车制造业的FMEA应用
总结词
汽车制造业是FMEA应用的重要领域,通过分析失效 模式及其影响,可以优化产品设计、生产和质量控制 。
FMEA失效模式及其影响 分析
• 介绍 • FMEA失效模式分析 • FMEA失效影响分析 • FMEA实施步骤 • FMEA的优点和局限性 • 案例研究
01
介绍
FMEA的定义
• FMEA(Failure Modes and Effects Analysis)即失效模式与影响分析, 是一种预防性的质量工具,用于评估 产品设计或流程中潜在的失效模式及 其对系统性能的影响。它通过识别、 评估和优先处理那些可能对产品或流 程性能产生最大影响的失效模式,帮 助组织减少或消除潜在的问题,提高 产品和流程的可靠性和安全性。
汽车零部件的失效模式及分析
汽车零部件的失效模式及分析专业:班级学号:姓名:指导教师:年月摘要汽车零件失效分析,是研究汽车零件丧失其规定功能的原因、特征和规律;研究其失效分析技术和预防技术,其目的在与分析零部件失效的原因,找出导致失效的责任,并提出改进和预防措施,从而提高汽车可靠性和使用寿命。
目录第一章汽车零部件失效的概念及分类 (1)一、失效的概念 (1)二、失效的基本分类型 (1)三、零件失效的基本原因 (2)第二章汽车零部件磨损失效模式与失效机理 (3)一、磨料磨损及其失效机理 (3)二、粘着磨损及其失效机理 (4)三、表面疲劳磨损及其失效机理 (5)四、腐蚀磨损及其失效机理 (5)五、微动磨损及其失效机理 (6)第三章汽车零部件疲劳断裂失效及其机理 (8)第四章汽车零部件腐蚀失效及其机理 (9)第五章汽车零部件变形失效机理 (10)参考文献 (11)第一章汽车零部件失效的概念及分类一、失效的概念汽车零部件失去原设计所规定的功能称为失效。
失效不仅是指完全丧失原定功能,而且功能降低和严重损伤或隐患、继续使用会失去可靠性及安全性的零部件。
机械设备发生失效事故,往往会造成不同程度的经济损失,而且还会危及人们的生命安全。
汽车作为重要的交通运输工具,其可靠性和安全性越来越受到重视。
因此,在汽车维修工程中开展失效分析工作,不仅可以提高汽车维修质量,而且可为汽车制造部门提供反馈信息,以便改进汽车设计和制造工艺。
二、失效的基本分类型按失效模式和失效机理对是小进行分类是研究失效的重要内容之一。
失效模式是失效件的宏观特征,而失效机理则是导致零部件失效的物理、化学或机械的变化原因,并依零件的种类、使用环境而异。
汽车零部件按失效模式分类可分为磨损、疲劳断裂、变形、腐蚀及老化等五类。
汽车零件失效分类一个零件可能同时存在几种失效模式或失效机理。
研究失效原因,找出主要失效模式,提出改进和预防措施,从而提高汽车零部件的可靠性和使用寿命。
三、零件失效的基本原因引起零件是小的原因很多,主要可分为工作条件(包括零件的受力状况和工作环境)、设计制造(设计不合理、选材不当、制造工艺不当等)以及使用与维修等三个方面。
第二章 汽车零部件失效理论
汽车维修工程习题第二章汽车零部件的失效模式及分析一、名词解释1.汽车零件失效:指汽车在运行过程中,零部件逐渐丧失原有的性能或技术文件所要求的的性能,从而引起汽车技术状况变差,直至不能履行规定的功能。
2.混合摩擦:两摩擦表面间干摩擦、液体摩擦和边界摩擦混合存在的摩擦,称为混合摩擦。
3.磨料磨损:摩擦表面间存在的硬质颗粒引起的磨损,称为磨料磨损。
4.边界摩擦:两摩擦表面被一层极薄的边界膜隔开的摩擦,称为边界摩擦。
5.磨损:零件摩擦表面的金属在相对运动过程中不断损失的现象,称为零件的磨损。
6.穴蚀:与液体相对运动的固体表面,因气泡破裂产生的局部高温及冲击高压所引起的疲劳剥落现象。
7.疲劳断裂:零件在交变载荷作用下,经过较长时间工作而发生的断裂现象。
8.失效度:产品在规定的条件下,在规定的时间内丧失规定功能(即发生故障)的概率。
9。
粘着磨损:摩擦副相对运动时由于固相焊合接触表面的材料发生转移的现象。
二、填空题1、汽车早期失效期的基本特征是开始时失效率( )。
2、汽车失效类型有(磨损)、(疲劳断裂)、腐蚀、变形、老化。
3、微动磨损一般发生在交变载荷或振动作用的()配合表面部位。
4、腐蚀按机理不同,可分为()腐蚀、()腐蚀。
5、润滑油中加入适量的活性添加剂,可以()磨合过程,提高磨合质量。
6、引起零件失效的原因分为工作条件、设计制造以及()。
7、粘接剂的种类有环氧树脂胶、酚醛树脂胶和( )。
8、汽车零部件腐蚀失效分为化学腐蚀失效和( )失效。
9、影响汽车零件磨损的因素有()、()、()。
三、判断题1、低温条件下随着温度下降,汽油粘度、相对密度增加,发动机启动困难()四、简答题1、什么是干摩擦?其磨损特征是什么?在汽车上,一般将摩擦副表面间完全没有润滑油或其他润滑介质时的摩擦称为干摩擦。
其特征是:摩擦表面直接接触,产生强烈地阻碍摩擦副表面相对运动的分子吸引和机械啮合作用,消耗动力,转化为有害的摩擦热。
伴随着强烈的摩擦副表面磨损。
汽车零部件的失效模式及其分析
扩展的横向裂纹。
总之,磨料磨损机理是属于 磨料的机械作用,这种机械作用 在很大程度上与磨料的性质、形 状及尺寸大小、固定的程度及载 荷作用下磨料与被磨表面的机械
性能有关。
四、粘着磨损及其失效机理
v 定义:摩擦副相对运 动时,由于固相焊合 作用的结果,造成接 触面金属损耗的现象 称为粘着磨损。
v 是缺油或油膜破坏 后发生干摩擦的结果; 是指一个零件表面上 的金属转移到另一个 零件表面上,而产生 的磨损。
第一节汽车零部件失效的概念及分类 一、失效的概念; 二、失效的基本类型; 三、零件失效的基本原因;
一、失效的概念 汽车零部件失去原设计所 规定的功能称为失效。失效不 仅是指完全丧失原定功能,而 且还包含功能降低和有严重损 伤或隐患、继续使用会失去可 靠性和安全性的零部件。
二、失效的基本形式
按失效模式和失效机理对失效进行分
第二章汽车零部件的失效模式及其分析
❖ 难点: ❖ 1.汽车摩擦学-混合摩擦; ❖ 2.粘着磨损;微动磨损; ❖ 3.腐蚀磨损; ❖ 4.提高汽车零件抗疲劳断裂的方法; ❖ 5.基础件析,是研究 汽车零部件丧失其功能的原因、特 征和规律;目的在于:分析原因, 找出责任,提出改进和预防措施, 提高汽车可靠性和使用寿命。
磨料磨损的失效机理(假说)
以 微 量 切 削 为 主 的 假 说 ;塑 性 金 属 同固定的磨料摩擦时:磨屑呈螺旋形、 弯 曲 形 等 ;在 金 属 表 面 内 发 生 ⑴ 塑 性 挤 压 、形 成 擦 痕 ;⑵ 切 削 金 属 ,形 成 磨 屑 ;
以压痕为主的假说:对塑性较大的 材料;磨料在压力作用下压入材料表 面,梨耕另一金属表面,形成沟槽,使 金属表面受到严重的塑性变形压痕两 侧金属已经破坏,磨料极易使其脱落。
DFMEA设计失效模式及后果分析
设计评审
3
设计评审
中间开口、 开孔或边沿 无尖角、无
尖边缘
中间开口、开孔 或边沿有尖角、
尖边缘
外观不良,易产生飞边,并导致 后期修整困难
6
圆柱、卡扣 座、安装筋 等结构强度
足够
圆柱、卡扣座、 安装筋等结构强 加强筋少、矮,壁厚太薄 度不够,易断裂
6
安装方便
安装困难 效率低、拆卸不方便
8 SC 材料不合格 2
耐高温性 不耐高温性 性能下降、强度下降发粘异臭味 8 SC 材料不合格 2
耐热循环性 能良好
耐热循环性能差 易变形、早期失效
耐振动性性 能良好
耐振动性性能差
易变形、断裂、脱落
振动性耐久 振动性耐久性能
性能良好
差
易断裂、早期失效
耐气候老化 耐气候老化性能
性能良好
差
变色、早期失效
试验验证
3
将窄、细、薄等部位加强
设计评审
3
将要求明确的告知造粒车间
试验验证
4
增加定位点
设计评审
3
将要求明确的告知造粒车间
试验验证
4
设计定位面、槽、柱等结构
设计评审
5
图样评审、数模验证
2
设计评审
2
设计评审
2
在三维数模进行面分析
设计评审
壁厚不能超过本体壁厚的1/3,最大不 3 能超过1/2。必须超过时,须对根部进
6
产品易于涂 装
产品难涂装 外观不良
6
尽量避免嵌 件结构 嵌件数量多
效率低、不安全、易损伤模具或 产品
6
嵌件不脱落 、不转动
- 1、下载文档前请自行甄别文档内容的完整性,平台不提供额外的编辑、内容补充、找答案等附加服务。
- 2、"仅部分预览"的文档,不可在线预览部分如存在完整性等问题,可反馈申请退款(可完整预览的文档不适用该条件!)。
- 3、如文档侵犯您的权益,请联系客服反馈,我们会尽快为您处理(人工客服工作时间:9:00-18:30)。
⒈机械理论
⒉分子吸附 理论
当两固体表面接触时,由于表面凹凸不平,相互啮合,产 生了阻碍两固体接触表面相对运动的作用。(只适用于固 体的粗糙表面)
摩擦力产生得主要原因在于两摩擦表面分子之间的相互吸 引力。
⒊粘着理论 摩擦力主要取决于剪断金属粘着和冷焊点所需的剪切力。
⒋分子-机 械理论
发生在接触点处分子吸引和机械啮合所构成的合成阻力就 是所谓的摩擦力。在载荷作用下的接触表面的相互作用可 分为机械作用(取决于表面变形)和分子作用(取决于原 子相互吸引),在摩擦过程中所占比例与材料的表面粗糙 度、载荷大小、材料种类等因素有关。
基本原因 工作条件
三、零件失效的基本原因
⒈工作条件
主要内容
应用举例
零件的受力状况
曲柄连杆机构在承受气体压力过程 中,各零件承受扭转、压缩、弯曲载荷 及其应力作用;
齿轮轮齿根部所承受的弯曲载荷及 表面承受的接触载荷等;
绝大多数汽车零件是在动态应力作 用下工作的。
工作环境;
汽车零件在不同的环境介质和不同
精选ppt失去原设计所
规定的功能称为失效。失效不
仅是指完全丧失原定功能,而
且还包含功能降低和有严重损
伤或隐患、继续使用会失去可
靠性和安全性的零部件。
精选ppt
5
二、失效的基本形式
按失效模式和失效机理对失效进行分
类是研究失效的重要内容。
汽车零部件按失效模式分类可分为磨 损、疲劳断裂、变形、腐蚀及老化等五类;
点、凹坑等
曲轴断裂、齿轮轮齿折断等
湿式汽缸套外壁麻点、孔穴 曲轴弯曲、扭曲,基础件(汽缸体、
变速器壳、驱动桥壳)变形
老化
龟裂、变硬
精选ppt
橡胶轮胎、塑料器件
7
三、零件失效的基本原因
⒈工作条件 包括零件的受力状况和工作环境;
⒉设计制造 设计不合理、选材不当、制造工艺不 当等;
⒊使用维修
精选ppt
8
形式只在某些特定条件下才会发生。
精选ppt
15
三、磨料磨损及其失效机理
定义:物体表面与硬质颗
粒或硬质凸出物(包括硬金属•)
相互摩擦引起表面材料损失的 现象称为磨料磨损;
磨料的来源; 粒 度 为 20μm ~ 30μm的尘埃将引起 曲轴轴颈、气缸表
在 各 类 磨 损 形 式 中 大 约 占 磨 损 总 消 耗 的 50% ; 危 害 最 为 严 重的磨损形式;
10
第二节汽车零部件磨损失效模式与失效机理
汽车或机械运动在其运动中都是一个物体与另一物体
相接触、或与其周围的液体或气体介质相接触,与此同时 在运动过程中,产生阻碍运动的效应,这就是摩擦。由于 摩擦,系统的运动面和动力面性质受到影响和干扰,使系 统的一部分能量以热量形式发散和以噪音形式消失。同时, 摩擦效应还伴随着表面材料的逐渐消耗,这就是磨损。
精选ppt
13
分类方式
按摩擦副 的相对运 动形式
按摩擦副 表面的润 滑状况
⒉摩擦分类
内容 滑动摩擦 滚动摩擦 复合摩擦
固体摩擦
举例 活塞与活塞环在气缸孔的往复运动 滚动轴承滚柱、滚珠与内、外圈滚 道表面间的摩擦 凸轮轴凸轮与气门挺杆表面间、齿 轮传动机构轮齿表面所发生的摩擦
汽车离合器、制动器
流体摩擦 边界摩擦
一个零件可能同时存在几种失效模 式或失效机理。
精选ppt
6
汽车零件失效分类
失效类型
失效模式
举例
磨损
疲劳断裂 腐蚀 变形
粘着磨损、磨料磨损、表 面疲劳磨损、腐蚀磨损、
微动磨损
低应力高周疲劳、高应力 低周疲劳、腐蚀疲劳、热
疲劳
化学腐蚀、电化学腐蚀、 穴蚀
过量弹性变形、过量塑性 变形
汽缸工作表面“拉缸”、曲轴“抱 轴”、齿轮表面和滚动轴承表面的麻
面的严重磨损,而 1μm 以 下 的 尘 埃 同 样会使凸轮挺杆副 磨损加剧;
精选ppt
16
磨料磨损的失效机理(假说)
以 微 量 切 削 为 主 的 假 说 ;塑 性 金 属 同固定的磨料摩擦时:磨屑呈螺旋形、 弯 曲 形 等 ;在 金 属 表 面 内 发 生 ⑴ 塑 性 挤 压 、形 成 擦 痕 ;⑵ 切 削 金 属 ,形 成 磨 屑 ;
磨损是摩擦效应的一种表现和结果。“磨损是构件由 于其表面相对运动而在承载表面上不断出现材料损失的过 程。”
据统计有75%的汽车零件由于磨损而报废。因此磨损 是引起汽车零件失效的主要原因之一。
精选ppt
11
一、摩擦学基础理论
• ⒈摩擦理论;
• ⒉摩擦分类;
精选ppt
12
⒈几种主要的摩擦理论
名称
主要内容
精选ppt
2
第二章汽车零部件的失效模式及其分析
汽车零部件失效分析,是研究 汽车零部件丧失其功能的原因、特 征和规律;目的在于:分析原因, 找出责任,提出改进和预防措施, 提高汽车可靠性和使用寿命。
精选ppt
3
第一节汽车零部件失效的概念及分类 一、失效的概念; 二、失效的基本类型; 三、零件失效的基本原因;
第二章汽车零部件的失效模式及其分析
重点: 1.汽车零件失效的基本原因; 2.汽车摩擦学理论; 3.磨损的分类与失效; 4.汽车零件疲劳; 5.汽车零件的变形; 6.汽车零件的腐蚀;
精选ppt
1
第二章汽车零部件的失效模式及其分析
• 难点: • 1.汽车摩擦学-混合摩擦; • 2.粘着磨损;微动磨损; • 3.腐蚀磨损; • 4.提高汽车零件抗疲劳断裂的方法; • 5.基础件的变形;
的工作温度作用下,可能引起腐蚀磨损、 磨料磨损以及热应力引起的热变形、热 膨胀、热疲劳等失效,还可能造成材料 的脆化,高分子材料的老化等。
精选ppt
9
三、零件失效的基本原因
⒉设计制造;⒊使用维修;
基本原因
主要内容
应用举例
设计制造 使用维修
设计不合理;
轴的台阶处直角过渡、过小的圆角
半径、尖锐的棱边等造成应力集中;
桶面活塞环与气缸壁、轴颈与轴瓦
发动机活塞环与缸套上部、配汽机 构凸轮与挺杆、齿轮传动副的齿面
精选ppt
14
二、磨损的分类
磨损与零件所受的应力状态、工作与润滑条
件、加工表面形貌、材料的组织结构与性能以及 环境介质的化学作用等一系列因素有关;
按表面破坏机理和特征,磨损可分为磨料磨 损、粘着磨损、表面疲劳磨损、腐蚀磨损和微动 磨损等;前两种是磨损的基本类型,后两种磨损
花键、键槽、油孔、销钉孔等处,
设计时没有考虑到这些形状对截面的削 弱和应力集中问题,或位置安排不妥当;
选材不合理; 制动蹄片材料热稳定系数不好;
制造工艺过程中 产生裂纹、高残余内应力、表面质量不 操作不合理; 良;
使用; 维修;
汽车超载、润滑不良,频繁低温冷启动;
破坏装配位置,改变装配精度;
精选ppt