乳液聚合工艺学
乳液聚合工艺学_3乳液聚合原理
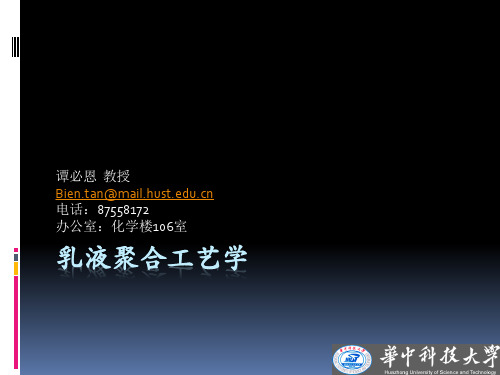
一种乳化剂的CMC值低,则在相同浓度下其胶束 浓度就大。 这与乳化剂在水中的溶解度有关,乳化剂的种 类和温度不同则CMC值不同。
胶束的增溶作用
(1)增溶作用的定义: 增溶作用的定义: 增溶作用的定义 是指在溶剂中完全不溶或者微溶的物质(可以是固体、 液体或者是气体), 借助于添加第三种成分——表面活性剂而得到溶解, 并成为热力学上稳定的、各向同性的均一溶液, 这种作用称为增溶作用。
胶束的增溶作用
(2)胶束增溶的几种模型 胶束增溶的几种模型
当增溶物与亲油基相容性好时,则为夹心型;相容性次之的 为栏栅型,再次之的为吸附型。 当增溶物亲水性较大时,如图3-3(d)所示,则在亲水基氧 乙烯链之间增溶。
图3-3 胶束增溶的几种模型 夹心型;( ;(b 栏栅型(其中1为浅伸入; 为深伸入); (a)夹心型;(b)栏栅型(其中1为浅伸入;2为深伸入); 吸附型;( ;(d (c)吸附型;(d)在亲水基氧乙烯链之间增溶
2 1/ 3
2/3
θ = (36πµ )
2 1/ 3
a (τ , t ) = θ (t − τ )
2/3
为了从(2-4)式计算出乳胶粒数,则t 必须得计算出来,那么为了得到时间,可 以通过计算每毫升水中在时刻t所含有的乳 胶粒总表面积来得到。 τ τ至 τ+d τ 的时间微元所生成的乳胶粒数 在 应为ρdτ ,这些乳胶粒中的每一个乳胶粒到 时刻t都具有表面积 α(τ,t) 。
谭必恩 教授 Bien.tan@ 电话:87558172 办公室:化学楼106室
乳液聚合工艺学
乳液聚合工艺学
丙烯酸乳液聚合工艺

丙烯酸乳液聚合工艺丙烯酸乳液聚合是一种制备丙烯酸乳液聚合物(通常是聚丙烯酸乳液)的化学过程。
这种聚合过程涉及将丙烯酸单体分散在水中,然后通过引发剂引发聚合反应,最终形成乳液聚合物。
以下是一般的丙烯酸乳液聚合工艺步骤:1. 原材料准备丙烯酸单体:丙烯酸是聚合的基本单体,需要确保其纯度和质量。
分散剂:用于将丙烯酸单体在水中分散。
乳化剂:有助于形成稳定的乳液结构。
引发剂:引发剂引发聚合反应,促使丙烯酸单体形成聚合物。
2. 乳化水相准备:准备含有适当浓度的水溶液。
分散丙烯酸:将丙烯酸单体添加到水相中,并使用分散剂确保丙烯酸均匀分散在水中。
添加乳化剂:添加乳化剂,形成乳液结构。
3. 聚合反应引发剂添加:将引发剂加入乳液中。
聚合反应:引发剂引发丙烯酸单体的聚合反应,生成聚合物颗粒。
反应控制:控制温度、搅拌速度等条件以确保反应进行良好。
4. 终点控制和停止反应终点控制:监测聚合反应的进程,确定聚合物颗粒的大小和分布。
停止反应:在适当的时机停止引发剂的添加,结束聚合反应。
5. 产品调整和稳定化调整pH值:可能需要调整乳液的pH值以获得所需的产品性能。
添加稳定剂:添加稳定剂以提高乳液的稳定性。
6. 过滤和包装过滤:过滤掉未反应的物质和固体颗粒。
包装:将成品乳液聚合物进行包装,以便存储和运输。
7. 质量控制和检验检测颗粒大小和分布:使用仪器或显微镜等工具检测聚合物颗粒的大小和分布。
检验产品性能:对产品进行物理性能和化学性能的检验,确保符合要求。
丙烯酸乳液聚合工艺的具体步骤和条件可能会因制备目的、产品用途和生产规模而有所不同。
在实际生产中,需要根据具体情况进行优化和调整。
乳液聚合生产工艺培训

乳液聚合生产工艺培训一、引言乳液是一种由溶剂、聚合物以及辅助添加剂混合而成的胶状物质。
它具有优异的粘结力和维持力,广泛用于涂料、胶粘剂、化妆品等行业中。
本文将针对乳液的聚合生产工艺进行讲解,以提供乳液生产工艺培训的相关知识。
二、乳液生产工艺概述乳液的生产工艺主要包括原料准备、乳液聚合、乳液稳定剂添加、调节pH值和包装等步骤。
下面将详细介绍每个步骤的工艺流程和操作要点。
2.1 原料准备原料准备是乳液生产中的重要步骤,直接关系到乳液的质量和稳定性。
主要原料包括水相、油相、乳化剂、增稠剂、PH调节剂等。
水相和油相的准备一般采用预混法。
首先将水相和油相分别加热至合适温度,然后分别加入乳化剂,搅拌均匀。
待水相和油相温度相近时,将水相缓慢加入到油相中,继续搅拌。
乳化剂的选择应根据乳化体系的特性和要求来确定,常用的乳化剂有阴离子型乳化剂、非离子型乳化剂和阳离子型乳化剂等。
乳化剂的加入量一般为总配方的1-5%。
2.2 乳液聚合乳液聚合是乳液生产中的核心步骤,是将乳化剂稳定体系中的聚合单体进行聚合反应,形成高分子聚合物颗粒的过程。
乳液聚合的反应体系一般需要控制在一定的温度范围内,一般在60-80℃之间。
聚合反应中常用的引发剂有过硫酸钠、过硫酸铵等,引发剂与乳液中的聚合物进行生成自由基反应,从而开启聚合反应。
选择合适的聚合装置和控制条件对乳液聚合过程的质量和产能有重要影响。
常用的聚合装置有搅拌釜、反应釜和连续流动聚合器等。
2.3 乳液稳定剂添加乳液聚合后,稳定剂的加入可以增加乳液的稳定性和粘稠度,并能提供一定的润湿性能。
常用的乳液稳定剂有复合稳定剂、天然胶黏剂等。
稳定剂的选择应根据乳液的具体用途和要求来确定。
一般情况下,稳定剂的加入量为总配方的1-10%。
2.4 调节pH值乳液的稳定性和性能受pH值的影响较大,因此需要调节乳液的pH值来保持其稳定性。
一般使用乙醇胺、氢氧化钠等碱性物质进行pH值的调节,调节范围一般为7-9。
乳液聚合工艺学_5_性能

研究聚合物乳液稳定性的方法
由于聚合物乳胶粒的尺寸在0.01~5μm之间,正
好落在胶体颗粒范围内,因此可以运用胶体理 论来指导提高聚合物乳液的稳定性和加速凝聚 过程。 胶体的稳定性和电性能与界面能有密切关系。
乳胶粒的本质
乳胶粒内包含的聚合物的性质与其它方法
合成的聚合物是一样的,也可分为结晶态、 橡胶态和玻璃态。 乳胶粒干燥过程与乳胶粒的Tg有很大的关 系
(5)稀释稳定性
将乳液稀释到固体含量为3%,再把30m1稀释后的乳
液倒入试管中,液柱高为20cm,放置72h,测量上 部清液和沉淀部分的体积即可知其稀释稳定性。
乳液相对密度的测定
粘度小于5Pas没有气泡的聚合物乳液可用
标准韦氏相对密度天平来测定其相对密度, 或是比重计测定。 粘度大且有气泡的聚合物乳液,可以在一 高型量筒中,装入已知体积的试样并进行 称重,由此可以计算得近似的相对密度。
乳胶粒的静电斥力越大,则ζ电位越高,乳液 越稳定。
(1)(2)(3)来自 (2) 非水介质中的“毛发”乳胶粒结构
用聚12-羟基硬脂酸链在十二烷介质中接枝在甲
基丙烯酸甲酯乳胶粒。
(3) 聚电解质接枝稳定乳胶粒的结构
此种乳胶粒中同时存在静电稳定作用和空间 位阻作用
影响乳胶粒稳定性的作用力
(1)静电力
当Tg大于干燥温度时得到粉末状树脂; 当Tg小于干燥温度时,干燥到一定的程度,乳
胶粒发生聚结,形成连续的薄膜
乳液聚合中使乳液稳定的物质
吸附在乳胶粒表面的乳化剂; 引发剂引入聚合物链末端的离子基团; 在乳胶粒表面上吸附或接枝的聚合物
不同稳定机理的乳胶粒的结构
(1) 带负电乳胶粒的双电层结构
乳液聚合工艺学_12_细乳液聚合
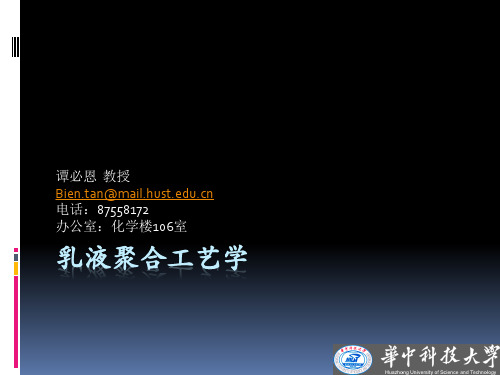
子单体、缩聚型单体、聚合物杂混体系等 在常规乳液聚合中无法实现, 但在细乳液中却可以 很好地聚合
细乳液的主要组分
稳定剂的亲水性
助稳定剂的亲水性越差, 亲油性越好, 其对
细乳液的稳定作用越强, 而且这种稳定作用 不受助稳定剂化学性质的影响。
随着烷烃链长增加, 其稳定作用增强。 在相同的链长下, 长链烷烃的疏水性(如HD在水
细乳液的制备步骤
乳化温度的影响
以HDL/ SDS 为乳化体系,SDS 为10 mmol ,HDL/SDS为
4 ,与St/ BA 混合单体制成细乳液。
细乳液的制备步骤
均质化方式的影响
分别以高速搅拌和超声波处理制备乳液
超声时间的影响
以HDL/ SDS , St/ BA 制备的细乳液为例。SDS为10
聚合动力学
当转化率达到60 %左右时,凝胶效应产生,使
自由基终止速率降低,从而聚合速率开始上 升,即进入阶段Ⅲ。 当转化率达到80 %左右时,聚合物颗粒接近 了它的玻璃化转变点,再次使链增长速率减 慢,从而使聚合速率降低,进入阶段Ⅳ
聚合动力学
聚合动力学
聚合动力学
细乳液胶乳粒子大小及分布
发现随着助稳定剂浓度增大, 单体液滴变小; 当其浓度超
助稳定剂的浓度对单体液滴尺寸影响很小, 只起到减弱单
助稳定剂浓度一般控制在单体浓度的1-4%之间, 过量助稳
定剂对细乳液稳定性和单体液滴数目影响不大。
细乳液的主要组分
助稳定剂的相对分子质量
低相对分子质量助稳定剂在相同质量比下
可以产生较大的渗透压, 从而稳定细乳液。
细乳液的主要组分
连续相 (水)
高疏水化合物
共稳定剂
乳液聚合生产工艺
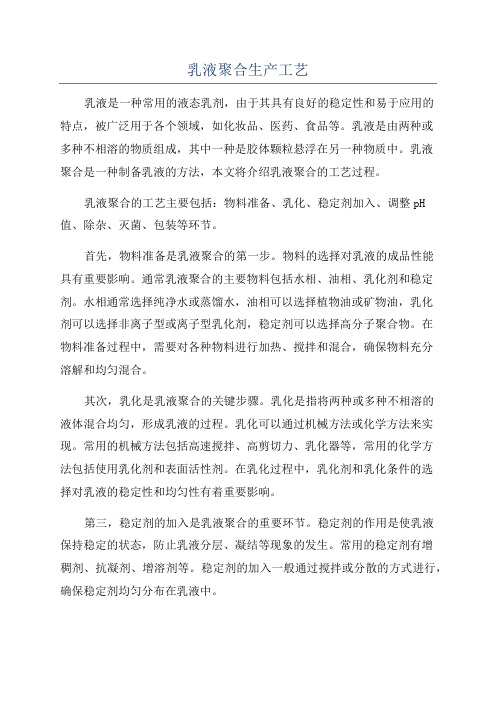
乳液聚合生产工艺乳液是一种常用的液态乳剂,由于其具有良好的稳定性和易于应用的特点,被广泛用于各个领域,如化妆品、医药、食品等。
乳液是由两种或多种不相溶的物质组成,其中一种是胶体颗粒悬浮在另一种物质中。
乳液聚合是一种制备乳液的方法,本文将介绍乳液聚合的工艺过程。
乳液聚合的工艺主要包括:物料准备、乳化、稳定剂加入、调整pH 值、除杂、灭菌、包装等环节。
首先,物料准备是乳液聚合的第一步。
物料的选择对乳液的成品性能具有重要影响。
通常乳液聚合的主要物料包括水相、油相、乳化剂和稳定剂。
水相通常选择纯净水或蒸馏水,油相可以选择植物油或矿物油,乳化剂可以选择非离子型或离子型乳化剂,稳定剂可以选择高分子聚合物。
在物料准备过程中,需要对各种物料进行加热、搅拌和混合,确保物料充分溶解和均匀混合。
其次,乳化是乳液聚合的关键步骤。
乳化是指将两种或多种不相溶的液体混合均匀,形成乳液的过程。
乳化可以通过机械方法或化学方法来实现。
常用的机械方法包括高速搅拌、高剪切力、乳化器等,常用的化学方法包括使用乳化剂和表面活性剂。
在乳化过程中,乳化剂和乳化条件的选择对乳液的稳定性和均匀性有着重要影响。
第三,稳定剂的加入是乳液聚合的重要环节。
稳定剂的作用是使乳液保持稳定的状态,防止乳液分层、凝结等现象的发生。
常用的稳定剂有增稠剂、抗凝剂、增溶剂等。
稳定剂的加入一般通过搅拌或分散的方式进行,确保稳定剂均匀分布在乳液中。
然后,需要调整乳液的pH值。
pH值的调整对乳液的稳定性和成品的质量有着重要影响。
一般来说,乳液的pH值应处于中性或略酸性范围内。
pH值的调整可以通过酸碱中和的方式进行,需要根据具体的产品要求进行调整。
接下来,对乳液进行除杂处理。
除杂的目的是去除乳液中的杂质和残留物,确保乳液的纯度和质量。
除杂的方法有过滤、离心等。
除杂过程中需要注意避免对乳液的物理性能产生影响。
最后,对乳液进行灭菌处理。
灭菌是为了防止乳液中的微生物污染,确保乳液的质量和安全性。
乳液聚合生产工艺
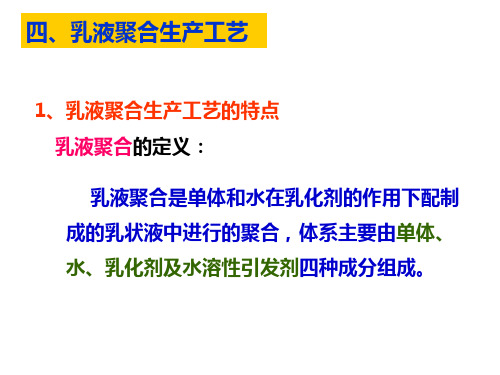
作为O/W型乳化剂
乳化剂的基本特征参数
CMC值:
能够形成胶束的最低浓度称 为临界胶束浓度 。当乳化剂浓 度达到CMC值以后,再增加乳 化剂的浓度只能增加胶束的数量 而不能改变乳液中界面的性质 。 从乳化剂的结构而言,疏
水基团越大,则CMC值越小。
乳化剂浓度变化与乳化剂行为的关系
乳化剂的基本特征参数
当乳化剂浓度在CMC值以
下时,溶液的表面张力与界面张 力均随乳化剂浓度的增大而降低。 而当乳化剂浓度达到CMC值后, 随着乳化剂浓度的增长,其表面
张力和界面张力变化相对很小。
此时,溶液的其他性质,如电导 率、粘度、渗透压等性质随乳化 剂浓度增长的变化规律在CMC
十二烷基硫酸钠水溶液的物理性质变化
值二边也有显著不同。
乳液聚合的影响因素
1、乳化剂的影响(种类和数量) 乳化剂的种类不同,其胶束稳定机理,临界胶束浓度 CMC 、胶束大小及对单体的增容度亦各不相同,从而会 对乳胶粒的稳定性、直径、聚合反应速度和聚合物分子量
产生不同的影响。
乳化剂的浓度对乳液聚合得到的分子量有直接影响,例 如:乳化剂浓度越大,胶束数目越多,链终止的机会小, 链增长的时间长,故此时乳液聚合得到的分子量很大。
• 分散阶段(聚合前段)
• 乳胶粒长大阶段(聚合II段)
• 乳胶粒生成阶段(聚合I段) • 聚合完成阶段(聚合III段)
乳液聚合过程和机理
(1)分散阶段
加入乳化剂,浓度低于CMC时形成真溶液,高于CMC 时形成胶束。
加入单体 按在水中的溶解度以分子 状态溶于水中,更多的溶 解在胶束内形成增溶胶束, 还有的形成小液滴,即单 体液滴。 单体、乳化剂在单体液滴、 水相及胶束间形成动态平 衡。
第五章 乳液聚合生产工艺20170322
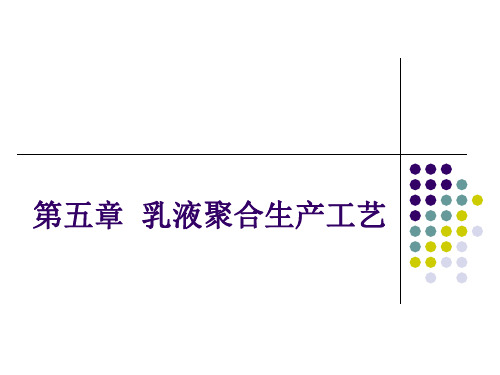
表面张力(气-液界面)
界面张力(液-液界面)
气体
液体1 液体2
பைடு நூலகம்液体
某些液体的表面张力(20oC)
表面张力和界面张力单位是 N/m或mN/m。
某些液体对水的界面张力
表面张力和界面张力单位是 N/m或mN/m。
加入乳化剂,浓度低于CMC时形成真溶液,高于CMC时形 成胶束。 加入单体 按在水中的溶解度以分子 状态溶于水中,更多的溶 解在胶束内形成增溶胶束, 还有的形成小液滴,即单 体液滴。 单体、乳化剂在单体液滴、 水相及胶束间形成动态平 衡。
(2)乳胶粒生成阶段
引发剂溶解在水中,分解形成初始自由基。 引发剂在不同的场所引发单体——生成乳胶粒
(2)乳液的稳定性原理
a. 高分散性的粉末状固体物质:其主要作用是吸附于分散相液滴表 面,好似在液滴表面形成 。
b. 某些可溶性天然高分子化合物:其主要作用是在分散相液滴表面 形成了 。
(3)表面活性剂的作用原理
a. 降低分散相和分散介质的界面张力,降低了界面自由能,从而使 液滴自然聚集的能力大为降低。 b. 表面活性剂分子在分散相液滴表面形成规则排列的表面层,形成 了薄膜层。乳化剂分子在表面层中排列的紧密程度越高,乳液稳定 性越好。
某些表面活性剂的临界胶束浓度(在50oC纯水)
c. 浊点和三相点
非离子表面活性剂被加热到一定温度,溶液由透明变为浑浊,出现 此现象时的温度称为浊点(Cloud Point), 。 离子型乳化剂在一定温度下会同时存在乳化剂真溶液、胶束和固体 乳化剂三相态,此温度点称三相点。 。
(4) 表面活性剂的类别
- 1、下载文档前请自行甄别文档内容的完整性,平台不提供额外的编辑、内容补充、找答案等附加服务。
- 2、"仅部分预览"的文档,不可在线预览部分如存在完整性等问题,可反馈申请退款(可完整预览的文档不适用该条件!)。
- 3、如文档侵犯您的权益,请联系客服反馈,我们会尽快为您处理(人工客服工作时间:9:00-18:30)。
因此聚合应发生在胶束中,理由是: (1)胶束数量多,为单体液滴数量的100倍; (2)胶束比表面积大,内部单体浓度较高; (3)胶束表面为亲水基团,亲水性强,因此自由基 能进入胶束引发聚合。 胶束的直径很小,因此一个胶束内通常只能 允许容纳一个自由基。但第二个自由基进入时,就 将发生终止。前后两个自由基进入的时间间隔约为 几十秒,链自由基有足够的时间进行链增长,因此 分子量可较大。
压力对乳液聚合的影响
聚合反应为液相反应,压力对反应本身影响不 大,但考虑以下因素,反应在加压条件下进行 防止空气中大氧进入体系 避免丁二烯蒸发,反应压力要大于丁二烯饱和 蒸汽压。 防止氨泄露 克服系统阻力。
单体转化率的影响
转化率过高,引起较多的支链和交联,质量变 坏。 转化率控制在65—70%。
C11H23COONa
36℃;
C15H31COONa
62℃;
3.
临近胶束浓度
在达到CMC时,溶 液许多性能发生突变, 如图所示。 在乳液聚合中,乳化 剂浓度约为CMC的100 倍,因此大部分乳化剂 分子处于胶束状态。
十二烷基硫酸钠水溶液性能与浓度的关系
形成胶束的最低乳化剂浓度,称为临界胶束浓度(CMC) 不同乳化剂的CMC不同,愈小,表示乳化能力愈强。
Ⅰ阶段 不断增加 直到消失 数目不变 体积缩小 不断增加
Ⅱ阶段 恒定 - 直到消失
恒定
Ⅲ阶段 恒定 - -
下降
(I)增速阶段。乳胶颗粒不断增加。由于聚合发生在乳胶 颗粒中,因此聚合总速率不断增加。转化率可达15%; (II)恒速阶段。乳胶颗粒数量稳定,聚合总速率不再变化; (III)降速阶段。单体液滴消失,乳胶颗粒中单体也减少,聚 合总速率降低。
5、聚合反应机理
自由基反应类型,整个聚合过程主要由链引发、链 增长、链转移、链终止基元反应组成。
链引发
Fe2+ +ROOH→ Fe3+ + RO● + OH– Fe3++NaHSO2HCHO→Fe2++NaHSO3+HCHO RO● + M → ROM ● → M ●
链增长
M ● + nM → ~ M ●
反应时间
在一定转化率下 反应时间短:胶粒过细,质量不好 反应时间长:胶乳稳定性好,但生产效率降低。 反应时间控制在7.5—10小时。
加入单体的情况
在形成胶束的水溶液中加入单体 极小部分单体 以分子分散状 态溶于水中 小部分单体 可进入胶束 的疏水层内 体积由 4~5nm增 至6 ~10 nm 相似相容,将这种 溶有单体的胶束称 为增溶胶束。 大部分单体 经搅拌形成 细小的液滴 体积约为 1000 nm
部分单体进入胶束 内部,宏观等于增 加了单体在水中的 溶解度,这一过程 称为“增溶”。
液滴中的单体通过水相可补充胶束内的聚合消耗。
Fe2+的控制
在氧化还原引发体系中,Fe2+如何控制 产生1个活性基,需要1和Fe2+; 若一次投入Fe2+,反应过快,过早耗尽,无法 得到高转化率产品。 措施 加入络合剂EDTA,本工艺采用。
影响聚合的主要因素
单体配比 本工艺配比,丁二烯/苯乙烯(质量比) 79/30 结合苯乙烯含量 23.5%
胶束的形状
图4-3
球状 ( 低浓度时 ) 直径 4 ~ 5 nm
棒状 ( 高浓度时 ) 直径 100 ~ 300 nm
胶束的大小和数目取决于乳化剂的用量: 乳化剂用量多,胶束的粒子小,数目多。
4. 乳液聚合机理
单体 液滴
单体和乳化 剂在聚合前 的三种状态
极少量单体和少量乳化剂以分子分散状态溶解在水中 大部分乳化剂形成胶束 聚合场所 在胶束内 大部分单体分散成液滴
影响聚合的主要因素—杂质1
丁二烯中杂质影响 丁二烯低聚体、多种异构体、乙腈或溶剂:对 聚合有阻聚作用,0.2—0.3%时,单体转化率时 间延长10%;0.5%时,聚合物门尼黏度下降 10%。 乙烯基乙炔:强交联剂,0.04%时门尼黏度上升 10个单位;0.1%时,门尼黏度上升30个单位。
影响聚合的主要因素—杂质2
聚合反应机理(续)
链转移 链终止
~M● + RtSH → ~MH + RtS ● ~ M● +RzSz ● ~MRzSz
总反应表达式:
(x+y)CH2CH-CHCH2 +zCH3CH2(Ph)
[CH2CH=CHCH2 ] x1-3─[CH(CH=CH2)CH2 ] y1-2 ─[CH(Ph)CH2 ] z
聚合反应机理(续)
反应温度 首釜:5~9℃ 二釜至五釜:4.5~7.5℃ 六釜至八釜:4.5~8.5℃ 反应压力:200~450KPa 反应热:1255.2kJ/Kg(SBR)
聚合反应曲线
图 乳液聚合动力学曲线
聚合过程
根据聚合物乳胶粒的数目和单体液滴是否存在,乳液 聚合分为三个阶段:
乳胶粒 胶束 单体液滴 RP
乳化剂的分类
阴离子型
烷基、烷基芳基的羧酸盐,如硬脂酸钠 硫酸盐,如十二烷基硫酸钠 磺酸盐,如十二、十四烷基磺酸钠 在碱性溶液中比较稳定,遇酸、金属盐、硬水, 会失效。 在三相平衡点以下将以凝胶析出,失去乳化能力。
三相平衡点:是指乳化剂处于分子溶解状态、胶束、凝胶三 相平衡时温度。 高于此温度,溶解度突增,凝胶消失,乳化剂只以 分子溶解和胶束两种状态存在。
丁苯橡胶 乳液聚合原理 与工艺学
丁苯橡胶反应特点
聚合工艺实施方法为乳液聚合
高聚物反应机理为自由基共聚合反应
连续聚合工艺,每条聚合线的反应釜
数量为10台,单釜容积30立方米
1、 乳液聚合
乳液聚合 单体在乳化剂作用和机械搅拌下,在 水中分散成乳液状态进行的聚合反应
基本组分 单体:一般为油溶性单体,在水中形 成水包油型。 引发剂:氧化-还原引发体系 水:脱盐水
苯乙烯中杂质影响 含氧化合物(醛和酮类):延缓聚合。 二乙烯基苯:强交联剂,0.1%时门尼黏度上升 17--31个单位;1%时,产生较多凝胶。 TBC:阻聚剂,超过15PPM时,用碱洗掉。
温度对乳液聚合的影响
温度上升 自由基产生速率增加 形成的胶束数增加,乳胶粒也增多 乳胶粒中单体浓度降低 单体和自由基扩散入乳胶粒的速率增加 结果: 温度上升,聚合速率增加,聚合 度降低,支化、交联严重,凝胶增加。 温度越低,分子量分布窄。一般聚合温 度为5~7℃。
2、乳化剂和乳化作用
(1) 乳化剂
是一类使互不相容的油(单体)和水转变成相当 稳定、且难以分层的乳液的物质。 分子通常由两部分组成 亲水的极性基团 亲油的非极性基团
亲水基(羧酸钠)
如长链脂肪酸钠盐
亲油基(烷基)
2 乳化作用
乳化剂使互不相容的油、水转变为相当稳定 难以分层的乳液的过程,称为乳化。
周围吸附了一层 乳化剂分子,形 成带电保护层, 乳液得以稳定
聚合场所:
在乳液聚合体系中,存在以下几种组成: (1)少量单体和乳化剂溶于水; (2)大部分乳化剂形成胶束、增容胶束; (3)大部分单体形成液滴。
聚合场所 在胶束内
成核机理
成核是指形成聚合物乳胶粒的过程。
当胶束内进行链增长时,单体不断消耗,溶 于水中的单体不断补充进来,单体液滴又不断溶 解补充水相中的单体。因此,单体液滴越来越小、 越来越少。而胶束粒子越来越大。 胶束成核: 自由基由水相进入胶束引发单体增长的过 程称为“胶剂溶于水时,若浓度很低,则大部分 乳化剂以分子状态分散于水中,并在水面上定向 排列。亲水基团伸向水中,亲油基团指向空气层。 但浓度达到一定值时,乳化剂分子在水面上 排满,多余的分子就会在水中聚集成胶束(约 50~150个分子), (图) 。
乳化剂的作用 (1)降低界面张力,使单体分散成 细小液滴。 (2)液滴保护层,防止聚集。 (3)形成胶束,使单体增溶。