液压缸试验台电控系统设计
液压试验台PLC控制系统设计完整

第一章绪论1.1 概述液压传动技术是机电一体化技术的重要组成部分,而且液压传动相对于机械传动来说是一门新技术,随着流体力学、自动控制、计算机等技术的不断发展,液压传动技术已经发展成为包括传动、控制、检测技术、机电一体化的一门完整的自动化技术,并且在工业生产、设备控制等方面都得到了广泛应用。
液压实验台是生产和开发液压元件和液压系统的重要实验设备。
传统的液压实验台内容固定、控制方式单一。
随着液压技术和现代控制技术的发展,传统液压实验台的缺陷愈来愈明显,已不能很好地适应生产和研究的需要。
为了可以更好的适应教学的发展,增强学生解决实际问题的能力,以及满足现代科研的需求,在传统液压试验台的基础上,加入PLC先进控制技术,构建了由PLC作为下位机控制现场设备,由PC作为上位机在线监控的控制系统,可以实现机、电、液、计算机的完美结合,实现实验处理的自动化,实时监控等。
采用了由PLC控制技术来控制液压试验台的自动控制响应快、智能化,学生不仅可以根据需求搭建各种液压回路或液压系统,还可以独立的进行液压设计、安装、调试、编写PLC程序、等,有利于提高学生在机电液计算机综合控制等方面的综合能力。
1.2液压传动的发展及其研究对象液压传动技术的发展,可追溯到17世纪帕斯卡提出了著名的帕斯卡定律,开始奠定了流体静压传动的理论基础。
从18世纪末英国制成了世界上第一台水压机算起,已经有近300年的历史,但真正的发展只是在第二次世界大战后,液压技术由军用工业迅速转向民用工业,而我国的液压工业只经过40余年的发展,就已经形成门类齐全、有一定的技术水平并初具规模的生产科研体系,其生产的液压产品广泛应用于工业、农业和国防等各个部门。
近20年来,我国液压工业通过引进先进技术,科研攻关,产品应用技术飞快发展,设计生产了许多新型的液压元件。
此外通过计算机辅助技术(Computer Aided Design,简称CAD)、计算机辅助测试(Computer Aided Translation,简称CAT)、污染控制、故障诊断、机电一体化等方面研究成果的应用,液压技术水平得到很大的提高。
一种多功能液压试验台控制系统设计

一种多功能液压试验台控制系统设计摘要:本文介绍了一种多功能液压试验台控制系统设计,液压控制模块的设计采用了模块化设计方式,可以缩短产品设计开发周期减少开发成本。
液压系统采用LUDV负载反馈控制技术能实现对不同负载压力的多个执行元件同时系统流量自动按比例分配。
关键词:液压试验台;控制系统;负载反馈;模块化设计中图分类号:TP271 文献标识码:A 文章编号:1006-4311(2015)09-0051-030 引言随着液压元件制造技术的飞速发展,液压系统的测试技术已经发展成为多门学科的集成技术,主要包括:液压技术、计算机辅助控制技术、传感器技术、仪器仪表技术、测试技术以及为电子技术等五个技术。
该多功能液压测试试验台主要用于对掘进机液压系统液压元件进行检测和分析。
试验台液压系统对测试元件提供高压液压油,主要针对旧液压元件进行检测时元件内部容易有脏物污染系统,专门开发了液压系统清洗装置;该系统可将系统主要液压元件都集成到同一试验台上进行综合性能测试,也可以分别测试液压泵、液压阀和液压缸的性能参数。
1 液压系统的模块化设计多功能液压测试试验台的基于目前煤矿井下用一种掘进机液压系统的需求而开发的,要求对掘进机液压系统和液压元件进行功能和特性试验。
而整个试验台液压系统有许多基本回路组成,而这些系统回路在测试不同液压元件时是回路是相同的,因此在该试验台液压系统设计时将这些基本回路或作用相同的几个回路设计成液压模块部件,再根据试验台的使用要求把这些液压模块进行合理的组合。
模块化产品的构成模式主要是用一个简单地公式来表达的:新产品(系统)=通用模块(不变部分)+专用模块(变动部分)。
采用模块化思想开发非标设备,可以实现产品在小批量生产时尽可能选用通用模块减少产品的设计开发成本,模块化设计能实现产品的多样化和效益最大。
该试验台液压系统可以划分为四个模块:油液存储及处理模块,压力源产生模块,液压阀控制模块,油路测试输出模块。
液压缸智能化控制系统设计与实现

液压缸智能化控制系统设计与实现液压技术在现代工业生产中得到了广泛的应用,尤其是液压缸的智能化控制系统,不仅可以提高生产效率,降低产品制造成本,还可以提高产品的质量和使用寿命,同时也可以降低人工操作过程中的安全风险。
本文将从液压缸智能化控制系统的概念、设计原理、关键技术及实现方法等多个方面进行探讨,以便更好地理解和应用液压技术。
一、液压缸智能化控制系统的概念液压缸智能化控制系统是将微电子技术、液压技术、机械技术和电气自动化技术相结合的一种高精度、高可靠性、高端控制系统。
它通过改进分析、命令给出和反馈控制等手段,可以实现液压缸的动态控制、自适应控制、各种工况下的总控制和监测参数的自动检测与调整等目标。
因此,液压缸智能化控制系统可以大大提高液压缸的稳定性和性能,并实现节能、环保、自动化等多重效益。
二、液压缸智能化控制系统的设计原理液压缸智能化控制系统的设计原理主要包括以下几点:1. 变量控制原理液压缸智能化控制系统的设计原则是基于变量控制原理,也就是将设定值与采集的反馈信号进行比较,以控制液压缸的动作。
此外,此类系统还可实现动态控制、自适应控制、质量监控,以适应不同的工作场景。
2. 传感器原理液压缸智能化控制系统需要多种传感器来收集数据,包括压力传感器、速度传感器、位移传感器和温度传感器等。
传感器可以收集实时数据或提供基准值,以完成对液压缸的控制。
3. 实时控制原理液压缸智能化控制系统主要采用实时控制原理,通过检测工况参数和反馈控制信息来实现动态的调整和控制。
此类系统需要具有可靠性、稳定性、实时性以及长期运行时间等特性。
三、液压缸智能化控制系统的关键技术1. 传感器技术传感器在液压缸智能化控制系统中是至关重要的,因为准确地获取和传输数据是实现系统性能和稳定性的关键。
液压缸智能化控制系统需要多种传感器,比如压力传感器、温度传感器、位移传感器和速度传感器等。
这些传感器需要同时具备高灵敏度、高稳定性、高精度度、抗干扰和抗干脆性等特性。
毕业设计_液压缸试验台设计

第 4 页 共 39 页
6.4 供油泵出口处溢流阀的选择 ........................................28 6.5 补油泵出口处溢流阀的选择 ........................................28 6.6 单向阀的选择 ....................................................29 6.7 三位四通换向阀的选择 ............................................29 6.8 单向节流阀的选择 ................................................29 6.9 背压阀的选择 ....................................................29 6.10 管道的选择 .....................................................29 6.11 确定油箱容量 ...................................................30 6.12 滤油器的选择 ...................................................32 6.13 液压油的选择 ...................................................32 7.液压系统性能验算 .....................................................33 8.液压系统的安装、调试及使用与维护 .....................................34 8.1 液压系统调度前的准备工作 ........................................34 8.2 液压系统跳调度骤 ................................................34 8.2.1 调试前的检查 ..................................................34 8.2.2 启动液压泵 ....................................................34 8.2.3 系统排气 ......................................................34 8.2.4 系统耐压试验 ..................................................34 8.2.5 空载调试 ......................................................35 8.2.6 负载试车 ......................................................35 8.3 液压系统的验收 ..................................................35 8.4 液压系统的维护及检修 ............................................35 结语 ...................................................................36 致谢 ...................................................................38 参考文献................................................................39
液压缸综合性能试验台测控系统总体设计

业要求的侧向为试验 ,检验液压缸在侧 向负载下的运行稳定性和可靠性。具
体 的试 验项 目和 试验 方 法 如下所 示 。 ( 1 )试 运行 :确保 被 试缸 在 无负 载 工况 下起 动 ,在 全行 程 范围 内往 复运
行数次 ,完全排 出液压缸内残留的空气 。
( 2 )起 动皮 力 试验 :试运 行 后 ,在无 负 载条 件下 ,逐步 升 高被 试缸 无杆
方案 。 2液压 缸综 合 性能 试验 台组成 及工 作分 析
液 压 缸 综 合性 能 试 验 台 ( 以下 简称 液 压 缸 试验 台 )为对 象 ,对 其 测 控系 统 的硬 、软 件进 行 设 计 与研 发 ,液 压化 试 验 台 结构 主 要 由试 验 台架 、液压 系
统和 测 控系 统 H部 分组 成 。
( 1 )试 验 台架 。试 验 台架 部 分主 要 由机 架 、被试 缸 、导 轨 、轴 向和 侧 向 加 载装 置 等 组 成 。其 中 ,机 架 采 用 整体 式 结 构 ,辅 w 合适 的 肋板 加 强 刚 度 ,
并通过有限元分析方法验证了机架的稳定性 ;轴 向和侧向加载装置用w模拟 被试缸运行过程 中所受 的负载 ,侧 向加载装置对被试缸耳环施加侧 向作用
拉
姆
罗
红
英
控制 :数据采集卡和传感器负责对压力 、位移 、速度等试验数据进行采集 ;
触摸 屏用 选 定 液压 缸 试 验 项 目 ,并 对 试验 参 数 进行 设 置 ,同时 对 试验 过 程 中 的 各项 参 数 和 系统 状 态 进 行实 时显 示 ;工 控 机 作 为上 位 机监 控 管理 平 台 ,实 现数 据 通信 、二 维 码生 成 、数 据处 理 、存储 及 分析 等 多项功 能 。
液压泵试验台系统设计
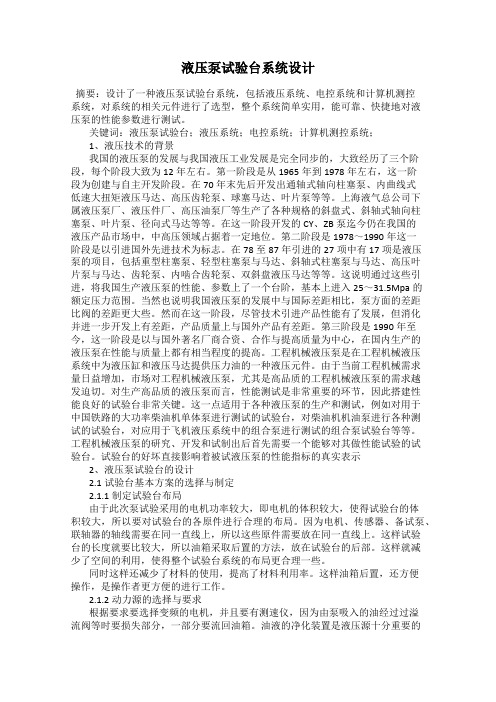
液压泵试验台系统设计摘要:设计了一种液压泵试验台系统,包括液压系统、电控系统和计算机测控系统,对系统的相关元件进行了选型,整个系统简单实用,能可靠、快捷地对液压泵的性能参数进行测试。
关键词:液压泵试验台;液压系统;电控系统;计算机测控系统;1、液压技术的背景我国的液压泵的发展与我国液压工业发展是完全同步的,大致经历了三个阶段,每个阶段大致为12年左右。
第一阶段是从1965年到1978年左右,这一阶段为创建与自主开发阶段。
在70年末先后开发出通轴式轴向柱塞泵、内曲线式低速大扭矩液压马达、高压齿轮泵、球塞马达、叶片泵等等。
上海液气总公司下属液压泵厂、液压件厂、高压油泵厂等生产了各种规格的斜盘式、斜轴式轴向柱塞泵、叶片泵、径向式马达等等。
在这一阶段开发的CY、ZB泵迄今仍在我国的液压产品市场中,中高压领域占据着一定地位。
第二阶段是1978~1990年这一阶段是以引进国外先进技术为标志。
在78至87年引进的27项中有17项是液压泵的项目,包括重型柱塞泵、轻型柱塞泵与马达、斜轴式柱塞泵与马达、高压叶片泵与马达、齿轮泵、内啮合齿轮泵、双斜盘液压马达等等。
这说明通过这些引进,将我国生产液压泵的性能、参数上了一个台阶,基本上进入25~31.5Mpa的额定压力范围。
当然也说明我国液压泵的发展中与国际差距相比,泵方面的差距比阀的差距更大些。
然而在这一阶段,尽管技术引进产品性能有了发展,但消化并进一步开发上有差距,产品质量上与国外产品有差距。
第三阶段是1990年至今,这一阶段是以与国外著名厂商合资、合作与提高质量为中心,在国内生产的液压泵在性能与质量上都有相当程度的提高。
工程机械液压泵是在工程机械液压系统中为液压缸和液压马达提供压力油的一种液压元件。
由于当前工程机械需求量日益增加,市场对工程机械液压泵,尤其是高品质的工程机械液压泵的需求越发迫切。
对生产高品质的液压泵而言,性能测试是非常重要的环节,因此搭建性能良好的试验台非常关键。
(完整word版)千斤顶液压缸加工机床电气控制系统设计

(完整word版)千斤顶液压缸加工机床电气控制系统设计XXXXX学院课程设计说明书设计题目:千斤顶液压缸加工机床电气控制系统设计学生姓名:XXXXX学号:XXXXX专业班级:XXXXX指导教师:XXXXX2012年12月13日内容摘要在本设计中采用装在动力滑台上左,右两个动力头同时进行切削。
动力头的快进、工进及快退由液压缸驱动。
液压系统采用两位四通电磁阀控制,并用调整死挡铁的方法实现位置控制。
主要介绍了通过PLC控制系统,设计了千斤顶液压缸加工机床电气控制,并设计了千斤顶液压缸加工机床电气控制梯形图,千斤顶液压缸加工机床控制硬件配置连线图,基于PLC的机床电气控制系统的控制电路图。
关键字:液压缸;PLC控制系统;梯形图;主电路目录第1章引言 (1)1.1设计内容 (1)1.2控制要求 (1)第2章系统总体方案设计 (3)2.1设计思路 (3)2.2 系统硬件配置 (3)第3章PLC控制系统设计 (4)3.1 主电路图的设计 (4)3.2 确定I/O数量,选择PLC类型 (5)3.3 I/O地址的分配 (5)3.4 元器件明细表 (7)3.5 硬件配置接线图 (7)3.6控制程序梯形图与语句表 (9)3.6.1梯形图 (9)3.6.2指令表 (10)3.6.3程序调试 (10)结论 (11)设计总结 (12)谢辞 (13)附录1 (14)附录2 (22)附录3 (22)参考文献 (32)第1章引言1.1设计内容千斤顶液压缸加工机床电气控制系统的设计。
1.2控制要求本机床用于千斤顶液压缸两个端面的加工,采用装在动力滑台上的左、右两个动力头同时进行切削。
动力头的快进、工进及快退由液压缸驱动。
液压系统采用两位四通电磁阀控制,并用调整死挡铁的方法实现位置控制。
机床的工作程序是:(1)工件定位人工将零件装入夹具后,定位液压缸动作,工件定位。
(2)工件夹紧零件定位后,延时15s,夹紧液压缸动作使零件固定在夹具内,同时定位液压缸退出以保证滑台入位。
超高压油缸出厂试验台设备-设计方案及主要参数说明
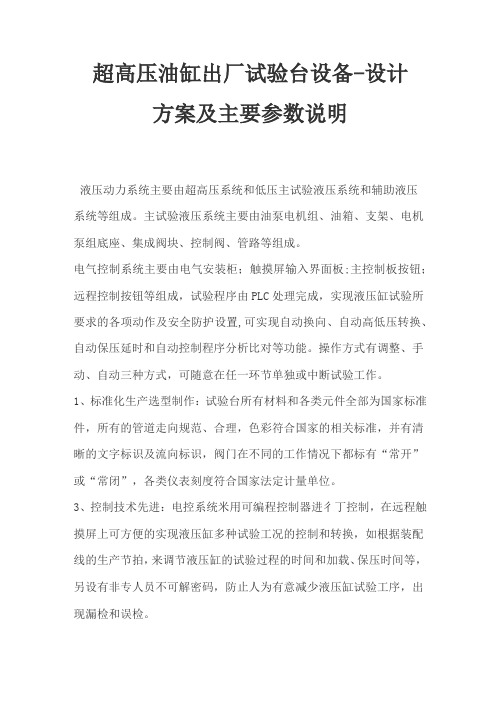
超高压油缸出厂试验台设备-设计方案及主要参数说明液压动力系统主要由超高压系统和低压主试验液压系统和辅助液压系统等组成。
主试验液压系统主要由油泵电机组、油箱、支架、电机泵组底座、集成阀块、控制阀、管路等组成。
电气控制系统主要由电气安装柜;触摸屏输入界面板;主控制板按钮;远程控制按钮等组成,试验程序由PLC处理完成,实现液压缸试验所要求的各项动作及安全防护设置,可实现自动换向、自动高低压转换、自动保压延时和自动控制程序分析比对等功能。
操作方式有调整、手动、自动三种方式,可随意在任一环节单独或中断试验工作。
1、标准化生产选型制作:试验台所有材料和各类元件全部为国家标准件,所有的管道走向规范、合理,色彩符合国家的相关标准,并有清晰的文字标识及流向标识,阀门在不同的工作情况下都标有“常开”或“常闭”,各类仪表刻度符合国家法定计量单位。
3、控制技术先进:电控系统米用可编程控制器进彳丁控制,在远程触摸屏上可方便的实现液压缸多种试验工况的控制和转换,如根据装配线的生产节拍,来调节液压缸的试验过程的时间和加载、保压时间等,另设有非专人员不可解密码,防止人为有意减少液压缸试验工序,出现漏检和误检。
一、试验项目:2、液压缸启动压力试验;4、液压缸泄漏试验;6、液压缸有效行程检测试验。
二、测试压力:液压缸试运行启动压力根据液压缸内径和行程不同,大概为一0.5-2MPa;试验工作压力一16-26MPa;最高试验耐压压力一24-60Mpa。
四、操作方式:电动按钮操作、触摸屏设置、PLC可编程输入设置和手动操作等,分别为各液压缸工位,放置了远程操作调节控制箱。
主要控制操作分别附有一试验油预热:预热可以由PLC按预定的时间自动启动预热(启动时间可在触摸屏界面上设定),也可由操作人员通过手动预热启动按钮,启动加热器系统进入预热状态。
在预热过程中会自动控制温度,根据当地使用环境温度和油泵自身要求的油温,来设置最高点和最低点。
一试验循环处理:各试验项目均可作为一个自动试验循环处理,即按钮按下以后,试验台上各试验项目连续完成,也可以任意在各个项目间设置断点,人工控制项目继续执行。
- 1、下载文档前请自行甄别文档内容的完整性,平台不提供额外的编辑、内容补充、找答案等附加服务。
- 2、"仅部分预览"的文档,不可在线预览部分如存在完整性等问题,可反馈申请退款(可完整预览的文档不适用该条件!)。
- 3、如文档侵犯您的权益,请联系客服反馈,我们会尽快为您处理(人工客服工作时间:9:00-18:30)。
液压缸试验台电控系统设计
针对传统的液压缸测试效率低、精度差等缺点,设计了一种计算机控制的液压缸试验台,不仅精度高,而且操作方便,性能可靠,通过实际的应用,体现了它的优越性。
标签:液压缸;PLC;自动控制
1 前言
液压油缸是液压传动系统的一个重要执行元件,它可以将液压能转变为直线往复运动的机械能,它结构简单,工作可靠,在机械系统中得到了广泛应用。
液压缸性能的好坏决定了整个液压系统的性能,因此对液压油缸的各项性能检测就显得尤为重要。
传统的液压缸测试主要采用手工操作的方式,不仅劳动强度大,而且工作效率低,测试数据精度也不高。
针对这些问题,本文设计了一种计算机控制的液压缸试验台,保留了手动控制的同时增加了计算机自动控制方式,便于从传统控制方式到自动控制方式的过度。
2 试验台的结构和功能
本液压试验台主要由三大部分组成:液压系统,电气控制系统,数据的采集与显示系统,通过本试验台可以完成液压油缸的出厂检验,包括对油缸的启动压力测试、往复性能测试、耐压测试、泄露量测试和报表打印等。
2.1 液压系统
液压系统主要包括液压油箱总成1套、液压油泵及电动机组3台套、压力调节和压力输出及回油总管系统、测试接口管路及液压阀。
通过高压软管,将被测油缸接入液压管路,系统中每台油泵的出口压力可以通过接入的溢流阀进行手动调节,压力大小主要采用机械式压力表进行测量和显示。
2.2 电气控制系统
电气控制系统的核心为计算机和PLC,可以分别通过试验台面板和人机界面对每台液压泵的起、停控制,过载保护,液压缸的加载控制,故障报警等功能。
由于电机的容量比较大,控制中采用Y-△启动方式。
另外,通过对相关电磁阀的控制可以实现对液压总管压力的加载或卸载,控制油缸连杆的伸出或缩回等功能。
控制方式有手动操作和计算机控制操作两种。
2.3 数据采集与显示系统
显示系统由试验台操作面板显示和计算机人机界面显示组成。
系统中数据的采集主要是通过各个传感器来完成的,传感器获取的数据分别传送至数字显示单
片机和数据采集卡,分别用于试验台操作面板数字显示和人机界面显示。
试验台面板上除了有7个压力表和4个数码表外,还指示了系统中电动机及溢流阀的工作状态,报警状况等。
在上位机界面中,系统元件的工作状态则由数据采集卡不断更新显示。
3 电气控制系统设计
3.1 设计方案
在整体的设计中,选用计算机和PLC作为控制的核心,采用主从式控制方式。
即计算机作为上位机进行集中的监控,通过软件完成可视化人机界面的设计、数据库的建立、报表的打印等功能;PLC作为下位机,完成对现场数据的不断采集和输出控制。
上位机和PLC之间通过RS232转RS485转换接头连接,整个系统方案的原理框图如图1所示,为了实现上位机的实时监控,各个传感器的数据通过数据采集卡传送至计算机。
另外传感器的数据也要传送到单片机,以便于试验台面板上的数字显示。
3.2.1 上位机
按照控制系统的要求计算机采用Intel的双核处理器E7400,配联想17寸方屏显示器;数据采集卡选用研华生产的PCI-8333多功能模入模出接口卡,不仅使用方便而且转换速度快。
传感器现场采集的数据经数据采集卡传送至计算机,上位机的人机操作界面利用面向对象的Visual Basic 6.0集成环境设计,选择其中的串行通信控件MSComm与PLC进行数据交换,上位机的操作界面如图2所示。
上位机操作界面为了形象地反应出试验中油泵及溢流阀的状态,界面
中模拟出了液压系统的示意图,如图2右上部分所示。
液压系统中电机、溢流阀、油缸等的状态,传感器的读数都可以实时地显示出来,起到监视的作用。
在控制方面,人机界面可以设定试验相关的参数,点击按钮直接完成相关的试验,并保存试验数据。
3.2.2 下位机
下位机PLC选用西门子的S7-200性价比较高的CPU224,它集成了14个数字量输入点,10个数字量输出点,由于I/O点不能完全满足系统监控的要求,硬件上还扩展了一个数字量输入模块EM221和一个数字量输出模块EM222,它们分别集成了8个输入、输出点,保证系统可靠性的同时也留有一定余量,便于系统后期的更新和拓展。
其中,使用输入点20个,输出点15个,主要起控制作用的I/O分配如表1所示,另外还包含了滤器堵塞、油温高、油位低等参量的输入与输出。
3.3 试验过程的控制
手动操作方式中,只需通过试验台上的按钮或动作开关按照一定的流程选择相应动作,就可以进行试验,试验中注意观察现场动作,另外,还要记录相关的参数和实验结果。
利用计算机进行控制时,先要做好一定的试验准备,比如在人机界面中输入油缸参数,往返次数,耐压时间等,一旦选择开始进行某个试验,计算机可以自动完成并且记录试验数据。
4 结论
本试验台通过某液压缸生产厂的实际运行证明系统运行稳定,降低了操作人员劳动强度的同时也提高了生产效率和自动化程度,有一定的实际意义。
参考文献
[1]张晓东.液压缸试验台计算机控制系统的设计[J].机械工程与自动化,2010,(4).
[2]马俊功.液压油缸试验台研制[J].机床与液压,2007,(1).。