内蒙古科技大学炉外精炼论文
炉外精炼基本方法与工艺分析
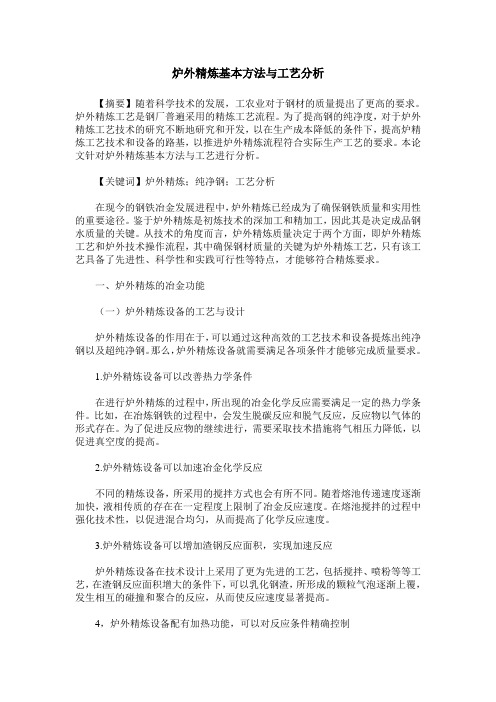
炉外精炼基本方法与工艺分析【摘要】随着科学技术的发展,工农业对于钢材的质量提出了更高的要求。
炉外精炼工艺是钢厂普遍采用的精炼工艺流程。
为了提高钢的纯净度,对于炉外精炼工艺技术的研究不断地研究和开发,以在生产成本降低的条件下,提高炉精炼工艺技术和设备的路基,以推进炉外精炼流程符合实际生产工艺的要求。
本论文针对炉外精炼基本方法与工艺进行分析。
【关键词】炉外精炼;纯净钢;工艺分析在现今的钢铁冶金发展进程中,炉外精炼已经成为了确保钢铁质量和实用性的重要途径。
鉴于炉外精炼是初炼技术的深加工和精加工,因此其是决定成品钢水质量的关键。
从技术的角度而言,炉外精炼质量决定于两个方面,即炉外精炼工艺和炉外技术操作流程,其中确保钢材质量的关键为炉外精炼工艺,只有该工艺具备了先进性、科学性和实践可行性等特点,才能够符合精炼要求。
一、炉外精炼的冶金功能(一)炉外精炼设备的工艺与设计炉外精炼设备的作用在于,可以通过这种高效的工艺技术和设备提炼出纯净钢以及超纯净钢。
那么,炉外精炼设备就需要满足各项条件才能够完成质量要求。
1.炉外精炼设备可以改善热力学条件在进行炉外精炼的过程中,所出现的冶金化学反应需要满足一定的热力学条件。
比如,在冶炼钢铁的过程中,会发生脱碳反应和脱气反应,反应物以气体的形式存在。
为了促进反应物的继续进行,需要采取技术措施将气相压力降低,以促进真空度的提高。
2.炉外精炼设备可以加速冶金化学反应不同的精炼设备,所采用的搅拌方式也会有所不同。
随着熔池传递速度逐渐加快,液相传质的存在在一定程度上限制了冶金反应速度。
在熔池搅拌的过程中强化技术性,以促进混合均匀,从而提高了化学反应速度。
3.炉外精炼设备可以增加渣钢反应面积,实现加速反应炉外精炼设备在技术设计上采用了更为先进的工艺,包括搅拌、喷粉等等工艺,在渣钢反应面积增大的条件下,可以乳化钢渣,所形成的颗粒气泡逐渐上覆,发生相互的碰撞和聚合的反应,从而使反应速度显著提高。
转炉炼钢车间设计
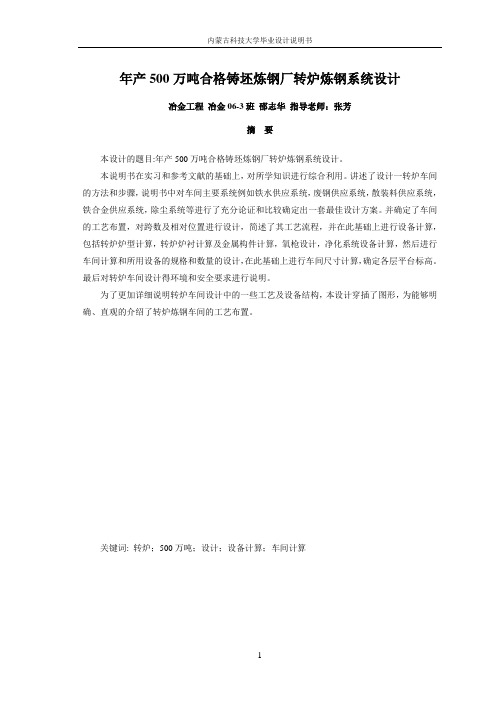
年产500万吨合格铸坯炼钢厂转炉炼钢系统设计冶金工程冶金06-3班邵志华指导老师:张芳摘要本设计的题目:年产500万吨合格铸坯炼钢厂转炉炼钢系统设计。
本说明书在实习和参考文献的基础上,对所学知识进行综合利用。
讲述了设计一转炉车间的方法和步骤,说明书中对车间主要系统例如铁水供应系统,废钢供应系统,散装料供应系统,铁合金供应系统,除尘系统等进行了充分论证和比较确定出一套最佳设计方案。
并确定了车间的工艺布置,对跨数及相对位置进行设计,简述了其工艺流程,并在此基础上进行设备计算,包括转炉炉型计算,转炉炉衬计算及金属构件计算,氧枪设计,净化系统设备计算,然后进行车间计算和所用设备的规格和数量的设计,在此基础上进行车间尺寸计算,确定各层平台标高。
最后对转炉车间设计得环境和安全要求进行说明。
为了更加详细说明转炉车间设计中的一些工艺及设备结构,本设计穿插了图形,为能够明确、直观的介绍了转炉炼钢车间的工艺布置。
关键词: 转炉;500万吨;设计;设备计算;车间计算第一章 文献综述 第二章 生产规模及产品方案2.1 金属平衡计算87%铁水 510.78万吨入炉金属料 587.1万吨13%废钢 76.32万吨 93%转炉钢水 546万吨97%钢包 529.62万吨 LF 精炼 529.62万吨3%损失 16.38万吨2%损耗 10.59万吨98%RH 精炼 519.03万吨0.7%损失 3.63万吨99.3%中间包 515.40万吨0.03%氧化铁皮 0.15万吨97.5%钢坯 502.51万吨1.2%连铸切头 6.18万吨1%中间罐结壳 5.15万吨0.5%连铸废品 2.51万吨99.5%合格坯500万吨图2.1 金属平衡表2.2 生产规模的确定该转炉车间的生产规模是年产合格铸坯500万吨。
2.2.1 转炉座数和大小的确定设计年产500万吨合格铸坯的转炉炼钢系统。
由金属平衡表计算可知,所需的转炉钢水年产量为546万吨。
炉外精炼生产实习报告

一、实习背景炉外精炼是炼钢生产过程中非常重要的一环,其主要作用是去除钢水中的非金属夹杂物、气体和有害元素,提高钢水的纯净度,保证钢的质量。
为了更好地了解炉外精炼工艺,提高自己的专业技能,我于2023年6月至8月在某钢铁有限公司进行了为期两个月的炉外精炼生产实习。
二、实习内容1. 实习期间,我主要了解了炉外精炼的生产流程,包括钢水脱硫、脱磷、脱氧、合金化、调整成分等环节。
2. 学习了炉外精炼设备的使用和维护,如LF炉、VOD炉、RH炉等。
3. 参与了炉外精炼生产操作,包括脱硫、脱磷、脱氧等工艺操作。
4. 了解炉外精炼过程中可能出现的故障及处理方法。
5. 收集并整理了炉外精炼生产的各项数据,进行分析和总结。
三、实习过程1. 实习初期,我主要了解了炉外精炼的生产流程和设备,通过阅读相关资料、请教师傅和同事,逐渐掌握了炉外精炼的基本知识。
2. 在师傅的指导下,我参与了LF炉、VOD炉、RH炉等设备的使用和维护,学习了设备的操作规程和注意事项。
3. 在实际操作过程中,我学会了脱硫、脱磷、脱氧等工艺操作,掌握了炉外精炼生产的基本技能。
4. 在实习过程中,我遇到了一些故障,如设备故障、钢水成分不稳定等,通过查阅资料、请教师傅和同事,成功解决了这些问题。
5. 实习期间,我收集并整理了炉外精炼生产的各项数据,包括钢水成分、设备运行状况等,进行了分析和总结,为提高生产效率和质量提供了依据。
四、实习体会1. 通过实习,我对炉外精炼生产有了更深入的了解,掌握了炉外精炼的基本工艺和操作技能。
2. 实习过程中,我学会了如何处理生产过程中遇到的问题,提高了自己的解决问题的能力。
3. 实习让我认识到团队合作的重要性,学会了与同事沟通交流,共同完成生产任务。
4. 实习让我更加坚定了学习炼钢专业的信念,为今后从事相关工作打下了坚实的基础。
五、实习总结1. 炉外精炼是炼钢生产过程中至关重要的一环,对提高钢水纯净度和钢的质量具有重要作用。
硅系合金生产中SiC的生成及其对炉内反应的影响

内蒙古科技大学硕士学位论文硅系合金生产中SiC的生成及其对炉内反应的影响姓名:张明亮申请学位级别:硕士专业:钢铁冶金指导教师:董方20070615独创性说明本人郑重声明:所呈交的论文是我个人在导师指导下进行的研究工作及取得研究成果。
尽我所知,除了文中特别加以标注和致谢的地方外,论文中不包含其他人已经发表或撰写的研究成果,也不包含为获得内蒙古科技大学或其他教育机构的学位或证书所使用过的材料。
与我一同工作的同志对本研究所做的任何贡献均已在论文中做了明确的说明并表示了谢意。
签名:___________ 日期:____________关于论文使用授权的说明本人完全了解内蒙古科技大学有关保留、使用学位论文的规定,即:学校有权保留送交论文的复印件,允许论文被查阅和借阅;学校可以公布论文的全部或部分内容,可以采用影印、缩印或其他复制手段保存论文。
(保密的论文在解密后应遵循此规定)签名:___________ 导师签名:___________ 日期:____________摘要硅系合金主要指硅铁、硅钙、工业硅、硅铝等,常用于炼钢的脱氧剂和合金添加剂,也是机械铸造、电子工业和化学工业中的重要原料。
硅系合金主要在还原电炉(矿热炉)中以碳作还原剂,还原硅石生产的。
碳质还原剂还原硅石是一个复杂的还原反应过程,还原反应过程对于硅系合金的工业生产有重要意义。
碳质还原剂还原硅石时有中间产物SiC产生,生产过程中矿热炉内SiC的生成和分解对还原反应起着重要作用,影响硅系合金生产的能量消耗,工艺的稳定顺行和炉子的使用寿命等经济技术指标。
本文根据矿热炉内碳还原硅石的热力学条件,以蓝碳、冶金焦为还原剂,在不同反应气氛和加入少量CaO、Al2O3等杂质的条件下,在实验室还原硅石,对中间产物SiC 的晶型、数量、微观组织形貌等开展研究,分析以上条件对矿热炉内硅系合金生产的中间产物SiC生成的影响。
对现场矿热炉炉内结厚物取样分析以验证实验室研究结果。
万吨炼钢毕业设计方案

内蒙古科技大学本科生毕业设计说明书题目:年产300万吨钢转炉炼钢<2×150)工程设计学生姓名:学号:专业:冶金工程班级:导师:冀中年<教授)目录摘要1第一章文献综述21.1 转炉的发展历程21.2 我国转炉炼钢发展现状31.2.1 转炉钢产量31.2.2转炉钢的比例组成31.2.3 转炉原材料消耗及能耗41.2.4 转炉炉龄51.3 我国转炉炼钢发展趋势51.3.1转炉条件和机遇51.3.2钢产量的增长方式61.3.3 冶金自动化技术61.3.4小结81.4 转炉炼钢存在的问题81.4.1 强化冶炼水平81.4.2 产业结构分布8第二章炼钢工程设计92.1 主要设计决定和特点92.1.1 概述92.1.2 基本工艺路线102.1.3 炼钢车间系统102.2 生产规模及产品方案122.2.1 生产规模122.2.2 产品大纲122.3 转炉车间产量计算和钢铁料平衡142.3.1 车间转炉作业率及钢产量计算142.3.2 钢铁料平衡计算152.4 生产工艺流程以及生产操作说明272.4.1 工艺流程272.4.2 炼钢车间生产操作282.5 炼钢车间的组成302.6 车间工艺布置说明与计算312.6.2 加料跨312.6.3 转炉跨332.6.4 钢水接受跨372.6.5 其它跨372.6.6 废气处理及回收系统372.7 主要工艺设备选择及其性能参数392.7.1 转炉本体392.7.2 转炉托圈392.7.3 转炉倾动装置392.7.4 氧枪及传动装置402.7.5 废钢料槽主要设备性能及参数432.7.6 脱硫站的喷枪系统432.7.7 钢包性能参数442.8 主要经济指标及原材料动力消耗442.8.1 主原料442.8.2 散状原料452.9 120吨氧气顶底复吹转炉炉型设计462.9.1 炉型设计462.9.2 炉衬材料厚度的选择48第三章专题论述503.1 转炉溅渣护炉技术503.1.1 转炉的溅渣护炉操作原理503.1.2 氧、氮气流量和压力503.1.3 溅渣护炉工艺特点及设备503.1.4 操作顺序513.1.5 溅渣护炉工艺存在的问题及解决办法讨论523.1.6 展望543.2 转炉冶炼纯净钢工艺543.2.1 纯净钢概述543.2.2冶炼时夹杂物产生的过程及去除途径563.2.3 纯净钢生产技术的进步573.2.4小结59参考文献60附录:外文及翻译62致谢81摘要本次设计的是年产300万吨的转炉炼钢车间,主要对转炉炼钢生产的工艺流程、车间组成和工艺布置进行设计,并对转炉炼钢过程的物料平衡和热平衡、氧枪的选择设计、转炉跨、加料跨的厂房高度和跨度以及120吨顶底复吹转炉炉型进行了设计计算。
内蒙古科技大学冶金工程生产实习报告范文炼钢部分
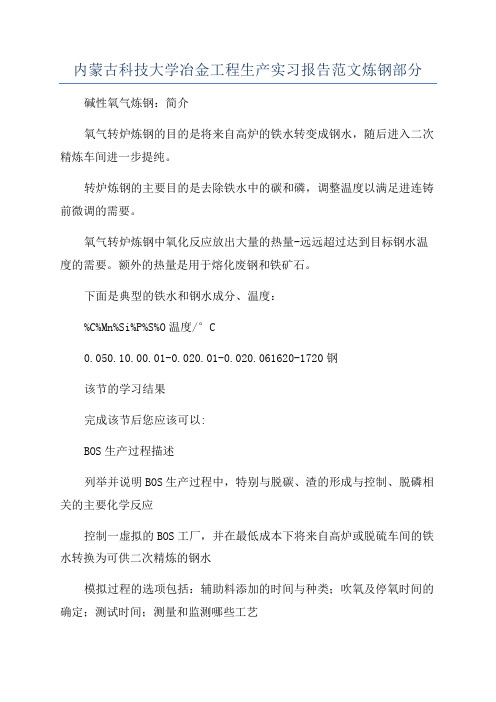
内蒙古科技大学冶金工程生产实习报告范文炼钢部分碱性氧气炼钢:简介氧气转炉炼钢的目的是将来自高炉的铁水转变成钢水,随后进入二次精炼车间进一步提纯。
转炉炼钢的主要目的是去除铁水中的碳和磷,调整温度以满足进连铸前微调的需要。
氧气转炉炼钢中氧化反应放出大量的热量-远远超过达到目标钢水温度的需要。
额外的热量是用于熔化废钢和铁矿石。
下面是典型的铁水和钢水成分、温度:%C%Mn%Si%P%S%O温度/°C0.050.10.00.01-0.020.01-0.020.061620-1720钢该节的学习结果完成该节后您应该可以:BOS生产过程描述列举并说明BOS生产过程中,特别与脱碳、渣的形成与控制、脱磷相关的主要化学反应控制一虚拟的BOS工厂,并在最低成本下将来自高炉或脱硫车间的铁水转换为可供二次精炼的钢水模拟过程的选项包括:辅助料添加的时间与种类;吹氧及停氧时间的确定;测试时间;测量和监测哪些工艺参数;突发事件的处理;出钢时间转炉炉体及其它辅助设备的描述各种过程控制参数、测试元件及模式说明炼钢热力学铁水中饱和碳含量一般而言,来自高炉铁水中的碳是无法分析出来。
但铁水中碳的饱和值Caturation可通下式计算:%Caturation=1.3+0.00257某THM(°C)–0.27%Si–0.33%P+0.027%Mn–0.36%S普通渣系1600、1650和1700°C下,在CaO-SiO2-FeO-2%P2O5-1.5%Al2O3-3%MnO-5%MgO渣系中温度对液相渣的影响通常认为碱性氧气炼钢炉渣比较接近三元渣系即CaO-SiO2-FeO。
但真正炉渣并不完全是三元的,而是超过三种成分,某些性质的合理估值可使用多元相图来得到。
原料、辅助料和产品装入转炉内的原材料有:来自高炉,经过脱硫或脱磷预处理后的铁水其它含铁的添加物,尤其是废钢和铁矿石,是用来调整热平衡、获得钢水所要求的温度添加物形成适当炉渣成分所需加主要物质有石灰(CaO)和白云石(CaO-MgO),其块度大小为20到40mm通过氧枪或底吹喷孔喷射的工业纯氧吹炼操作后的产品:钢液;富含CO(大约80-90%)的废气,回收后通常用于烘烤炉衬;出钢后倾倒出来的炉渣;如果正确的回收和贮存,废气和炉渣都是有价值的副产品。
炉外精炼的工艺技术发展终稿

炉外精炼的工艺技术发展摘要随着科学技术的迅速发展,钢材性能和质量越来越被重视,钢材质量主要包括钢材的洁净度、均匀性能和高的精度。
而各种炉外精炼方式恰是获得高纯度、高均匀性和高精度钢材的重要措施。
本文首先论述了炉外精炼技术现状及发展趋势;其次,论述了炉外精炼工艺参数的优化;第三论述了低硫钢炉外精炼生产工艺,最后论述了在炉外精炼喂丝吹氩操作实践。
关键词:洁净度;均匀性;高精度;工艺参数优化;低硫钢;喂丝吹氩;摘要 (1)前言 (3)1 炉外精炼技术发展现状及发展趋势 (5)1.1炉外精炼发展现状 (5)1.2炉外精炼发展趋势 (6)2 炉外精炼工艺参数优化 (8)2.1AHF精炼设备组成 (8)2.1.1 AHF精炼装置的主要设备组成 (8)2.1.2 AHF精炼化学升温装置的主要设备 (9)2.2AHF精炼工艺参数优化 (9)2.2.1钢包顶渣的最佳渣量及排渣工艺 (9)2.2.2AHF浸渍罩尺寸及插入深度控制 (10)2.2.3AHF升温设备及工艺参数 (10)2.2.4AHF钢水降温处理和成分调整 (11)2.3AHF精炼结果 (12)3 脱硫工艺技术发展 (14)3.1吹氩对脱硫的影响 (14)3.2钢包渣的组成控制 (15)3.3精炼渣的渣系 (17)3.4精炼渣化学成分对脱硫的影响 (19)4 炉外精炼的喂线、吹氩操作 (22)4.1喂线-吹氩工艺参数的确定 (22)4.2试验对比 (23)4.3小结 (23)结论 (24)参考文献 (25)致谢 (26)最近,随着时代的不断进步,炼钢炉容量不断扩大,超高功率电炉的普遍应用,直流电弧炉的出现,连续铸钢技术的迅速发展以及生产多种特殊钢和合金(超低碳不锈钢,超纯铁素体钢等)的需要,炼钢方法发生了巨大变化,由一步炼钢发展为两步炼钢,即炉内初炼和炉外精炼。
炉外精炼技术之所以有了较为迅猛的发展,是由于其能够提高钢质量和产量,降低成本,改善劳动条件等优点。
炉外精炼结课论文
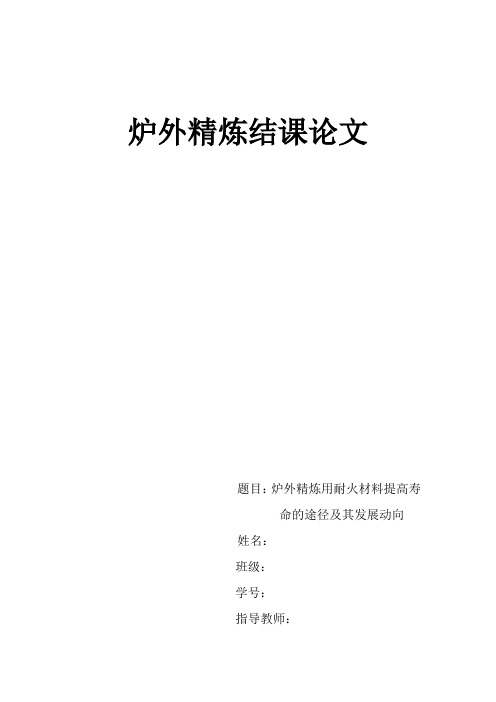
炉外精炼结课论文题目:炉外精炼用耐火材料提高寿命的途径及其发展动向姓名:班级:学号:指导教师:炉外精炼用耐火材料提高寿命的途径及其发展动向我国2005年钢产量虽高达3. 49亿吨,但一些高档的钢种却需要大量高价进口;而我国铁矿石短缺,国际上铁矿石随之抬高价格,大大上涨。
显然,这样一种供求、生产方式与结构是十分不合理的,不仅会对环境造成大的破坏,对资源利用也不合适。
其出路就是压缩一般钢产量,扩大炉外精炼,多生产技术含量高、附加值高的高档钢种。
为了有效和经济地炼出各种高质量的特殊钢,氧气转炉与电炉成了初步脱碳、升温与熔化废钢或冶炼一些普通钢的容器;而钢液的精炼过程则转移到了氧气转炉与电炉之外的精炼炉内进行;所以氧气转炉、电炉之外的精炼称之为炉外精炼或二次精炼。
炉外精炼的主要任务是除去钢中杂质与夹杂物、脱气、调整化学成分和均匀化等。
采用的手段有吹氧、吹Ar脱碳,电加热或化学加热,调温,真空脱气,喷入脱硫粉剂,吹Ar或电磁搅拌使夹杂物上浮排除,加合金调整钢液成分与成分均匀化等。
炉外精炼的种类与方法甚多,主要有VODAOD,V AD或VHD,DH,RH,RH-OB,LF,LF-VD,ASEA-SKF,CAS,一种吹Ar、排渣、降下隔离浸渍罩,在封闭条件下吹Ar调整钢液成分的简易钢包精炼法)等。
随着对钢质量、品种与成本的要求,炉外精炼也在不断改进与变化。
例如RH过去只是钢液循环流动真空脱气,减少钢中杂质与夹杂物。
现在RH真空室顶部及下部炉墙装置有氧枪、吹Ar喷嘴等,可以吹O2进行钢液真空脱碳,吹Ar搅拌,喷脱硫粉剂等。
于是有了RH-OB 或RH-TOB,RH-KTB, RH-MFB与RH-PB等。
再如CAS现在又有了在浸渍罩内进行顶吹氧的CAS-OB法等。
20世纪90年代以前发展较多的是AOD、VOD、V AD等,90年代以后发展最快的是能吹O2、吹Ar、喷粉剂的RH以及LF与LF-VD。
由于LF投资少,操作简便;而RH对钢水质量有保证,因此LF与RH发展甚快。
- 1、下载文档前请自行甄别文档内容的完整性,平台不提供额外的编辑、内容补充、找答案等附加服务。
- 2、"仅部分预览"的文档,不可在线预览部分如存在完整性等问题,可反馈申请退款(可完整预览的文档不适用该条件!)。
- 3、如文档侵犯您的权益,请联系客服反馈,我们会尽快为您处理(人工客服工作时间:9:00-18:30)。
炉外精炼论文题目LF精炼过程钢中硫、磷、氮、氧含量控制及非金属夹杂物的行为研究姓名学号班级冶金四班LF精炼过程钢中硫、磷、氮、氧含量控制及非金属夹杂物的行为研究摘要:将转炉、平炉或电炉中初炼过的钢液移到另一个容器中进行精炼的炼钢过程,也叫“二次炼钢”。
炼钢过程因此分为初炼和精炼两步进行。
初炼:炉料在氧化性气氛的炉内进行熔化、脱磷、脱碳和主合金化。
精炼:将初炼的钢液在真空、惰性气体或还原性气氛的容器中进行脱气、脱氧、脱硫,去除夹杂物和进行成分微调等。
这样将炼钢分两步进行,可提高钢的质量,缩短冶炼时间,简化工艺过程并降低生产成本,主要介绍转炉钢水过LF精炼时,钢水中硫、磷、氮、氧含量的控制以及非金属夹杂物的行为研究。
进而通过对工艺的优化和精炼炉的精炼效果,提高钢水纯净度。
完善,在生产中提高LF关键词:LF精炼;脱硫;脱磷;氮、氧含量;非金属夹杂物1引言:钢材的质量及性能是根据需要而确定的,不同的需要,要有不同的元素含量。
硫;是钢中的有害杂物,含硫较高的钢在高温进行压力加工时,容易脆裂,通常叫做热脆性。
磷;能使钢的可塑性及韧性明显下降,特别的在低温下更为严重,这种现象叫做冷脆性。
通常情况下,氮被视为钢中的有害元素,而氧元素主要以氧化物系非金属夹杂物的形式存在于钢中。
减少LF炉精炼工艺过程钢液增氧、去除钢中氢含量是生产优质钢的关键环节。
此外,控制钢中夹杂物是提高钢材使用性能的有效途径。
2转炉LF精炼脱硫与脱磷122.1脱硫2.11脱硫方法硫是钢中的长存元素之一,它会使大多数钢种的加工性能和使用性能变坏,因此除了少数易切削钢种外,它是需要在冶炼中脱除的有害元素。
硫在钢中以[FeS]形式存在,常以[S]表示。
钢中含锰高时,还会有一定的[MnS]存在。
目前炼钢生产中能有效脱除钢中硫的方法有碱性氧化渣脱硫、碱性还原渣脱硫和钢中元素脱硫三种。
2.1.2脱硫影响因素脱硫影响因素与碱性氧化渣脱硫不同,LF 碱性还原渣脱硫反应方程式为:[FeS]+(CaO)=(CaS)+(FeO)(1)[MnS]+(CaO)=(CaS)+(MnO)(2)由于钢中的[S]大部分以[FeS]形式存在,因此脱硫反应主要以式(1)为主。
从式中可以发现,影响脱硫的主要因数有:①炉渣中(CaO)的含量,即碱度高低的影响;②炉渣中(FeO)含量;③该反应是渣钢界面反应,炉渣流动性影响;④渣量的影响等。
具体如下:①由脱硫的反应式可见,渣中含有(CaO)是脱硫的首要条件,由于酸性渣中的(CaO)全部被(SiO2)所结合而无脱硫能力,所以脱硫要在碱性渣下才能进行。
随着碱度的增大,渣中自由的(CaO)含量增多,炉渣的脱硫能力增大。
但碱度过高会引起炉渣的黏度增大,恶化双相反应的动力学条件而不利于脱硫反应的进行。
生产经验表明,炉渣碱度2.5-3.5时,脱硫效果最好。
炉渣碱度与硫的分配系数Ls 的关系如图1所示。
②渣中(FeO)的含量。
在LF 精炼造渣过程中,随着扩散脱氧的进行,渣中(FeO)的含量逐渐降低。
从脱硫反应式(1)中可以看出,渣中氧化铁(FeO)含量的降低有利于脱硫反应向右进行。
在还原气氛下,只要保持炉渣具有较高的碱度脱硫效果就极为显著,这表明了脱硫与脱氧的一致性。
因此在冶炼过程中,脱氧越完全,对脱硫也越有利。
同时炉渣中(FeO)+(MnO)含量%与硫的分配系数有以下关系,(FeO)+(MnO)含量%越高,硫的分配系数越低(参见图2)。
③由于该反应是渣钢界面反应,只有保持流动性良好的炉渣,保证钢渣界面传递畅通无阻,才能使得反应向脱硫方向进行。
因此在精炼过程中必须保持全程良好的炉渣流动性。
④在保证炉渣碱度的条件下,适当加大渣量可以稀释渣中脱硫产物(CaO)的浓度,对去硫有利;但渣量过大时会使渣层变厚,脱硫反应不活泼,钢液中的硫并不随渣量的增加而按比例下降。
一般渣量控制在3%-5%较为合理。
2.2脱磷2.2.1磷元素转化趋势分析炼钢过程中,钢水中磷进入炉渣有两种方式,即氧化脱磷和还原脱磷,如图1所示.当体系氧势高于某一临界值,磷元素以P5+形式进入炉渣(氧化脱磷),并且氧势越高,进入炉渣的磷元素越多,氧势减小,渣中磷将返回钢中(回磷);当体系氧势等于这一临界值时,氧化脱磷和还原脱磷的趋势相同;当体系氧势低于临界值,磷元素将主要以P3-形式进入炉渣(还原脱磷),并且体系氧势越低该过程越易进行.考虑到碱性渣中主要的阳离子是Ca2+,若发生氧化脱磷,则脱磷产物为3CaO·P2O5或4CaO·P2O5,若发生还原脱磷,则脱磷产物为Ca3P2。
342.2.2LF 精炼过程还原脱硫的可能性分析LF 精炼是对钢水脱氧后开始的.宝钢EAF 出钢过程进行脱氧,BOF 是在RH 内脱氧合金化,所以钢水进入LF 工位时,钢水中的溶解氧含量已经于3·0×10-5,在LF 精炼过程中向渣内加入扩散脱氧剂,使渣中氧和钢中氧迅速下降,致使LF 精炼后期,钢水中溶[w(O)/%]已经小于1·0×0-3,渣中FeO 质量分数为0·1~0·5%,当采用钡系脱氧剂时,钢中氧[w(O)/%]可达到2·0×10-4~3·0×10-4,渣中FeO 质量分数小于0·04%.LF 精炼终点典型炉渣化学成分见表3.经试验研究,在LF 内热力学上具备了还原脱磷的条件。
另外,LF 精炼过程具有较高的温度,采用还原脱磷优于氧化脱磷.在较高温度下,采用铝钙合金,可以避免钙的过分气化损失.LF 炉内衬采用镁质耐火材料,使还原脱磷剂对炉衬的侵蚀减小到最低.所以,在LF 精炼过程中进行还原脱磷是可行的,并可同时降低钢中硫含量。
3LF 精炼过程中氮、氧元素含量的控制研究3.1钢中氮氧含量在各个工序中的变化3.1.1钢中氮含量在各个工序中的变化图1列出各工序钢中氮含量的变化情况,其中20号、45号钢在出钢、LF 炉精炼和浇注过程氮含量有所增加,而普通船板钢氮含量略有增加。
3.1.2钢中氧含量在各个工序中的变化由图3中看出45号、20号、普通船板钢3个钢种经过转炉出钢到形成铸坯的整个过程,钢中全氧含量逐步下降,且LF炉精炼过程对减少钢中全氧含量(即夹杂物含量)的作用十分显著,LF炉精炼成为脱氧控制的关键环节。
上述3个钢种酸溶铝含量均小于0.005%,钢的脱氧由「Si〕控制。
LF炉精炼通过造渣、吹氛制度控制钢的脱氧水平。
在钢水浇注到中间罐、结晶器的过程,钢中「O]呈现出明显的下降趋势,即夹杂物上浮脱离钢水。
从LF炉搬出到浇注到中间罐、结晶器内,随温度下降,钢水中溶解的氧析出,在中间罐、结晶器内与钢中的脱氧元素结合形成夹杂物上浮去除。
在洁净钢的生产中,控制好LF炉搬出钢水温度和中间罐内钢水温度,在中间罐、结晶器内创造有利于夹杂物上浮的条件,提高钢水的洁净度。
3.2LF精炼过程减少钢水增氮、降低钢中全氧含量3.2.1LF精炼过程减少钢水增氮LF炉实施泡沫渣工艺可以减少精炼过程钢水增氮。
在高强船板钢上做了巧炉泡沫渣试验。
每炉试验在电极加热期间加人两批发泡剂,间隔7min。
在钢水搬人LF炉和搬出LF炉时取钢样,分析钢中氮、氧、酸溶铝含量。
钢水增氮量为(1一13)x10-6,平均增氮5.27 x10-6。
未采用泡沫渣工艺时钢水增氮0一20x10-6,平均增氮6.43x10-6。
对严格控制5钢中氮含量的钢种应根据加热和精炼时间的长短加人3--4批发泡剂,精炼中间不加铝。
生产低氮含量钢应在LF精炼后期喂线加铝、钦;需要真空处理的钢种,应在真空下通过合金加人装置在破真空前Smin加人铝、钦。
3.2.2降低钢中全氧含量实施炉外精炼以后,转炉出钢后的钢水罐内脱氧操作对钢水净化作用大大减弱,LF 炉精炼操作显著地改善了钢水的洁净度。
根据钢种的不同,在LF炉内造碱度不同的顶渣,即使碱度在1.0--1.5的情况下,Si含量也提高了脱氧能力,钢水中全氧含量明显降低,见4表4.1实验探究H13钢是热作模具钢中应用最广泛的钢种之一,夹杂物对其性能有严重危害结合某钢厂生产实际情况,以现场取样为基础,用金相显微镜、扫描电镜系统地研究了LF-VD精炼过程中的夹杂物,计算和分析了H13钢冶炼过程中生成AL2O3、Mg0.A1203类夹杂物的热力学条件研究结果表明:钢液经LF精炼,VD处理后,钢中夹杂物的数量和面积明显减少,但随着炉渣中A1203活度的增大,炉渣吸附A1203类夹杂物的能力减弱,去除A120夹杂物的速度减慢;夹杂物在LF精炼前主要以A120-3、FeS、Mg0.A1203类夹杂为主,LF精炼结束后为A1203、-FeS、Ca0.A1203类夹杂,VD处理后为A1203类夹杂。
4.2典型夹杂物形貌65结论5.1通过以下控制,转炉LF精炼可以得到极低硫钢:1)炉渣碱度控制在2.5~3.5;2)炉渣中(FeO)+(MnO)≤0.5%;3)良好的炉渣流动性;4)炉渣渣量控制在80mm内;5)保证充足的通电时间和吹氩时间5.2LF精炼条件下对钢水还原脱磷是可行的.但必须满足下列条件:1)钢种对氮含量没有特殊要求;2)在满足钢种要求的情况下,尽量降低炉内温度;3)须采用沉淀脱氧与扩散脱氧相结合的脱氧方法降低钢中溶解氧[O]和渣中(FeO)活度,降低渣钢界面氧势;4)要求一定的吹氩量,赶净体系内的空气,保证体系氧势足够小;5)还原脱氧剂加入到钢水内部。
5.3确定控制钢中氮、氧含量的关键技术:71)采用LF炉精炼渣洗和明〕炉真空渣洗生产洁净钢,根据钢种的质量要求和液相线温度,选用不同碱度的渣系进行渣洗。
真空渣洗后补加铝、钦等成分应在破真空前实施。
2)生产洁净钢时应严格控制I_F(或VD)搬出钢水温度及中间罐钢水温度。
3)LF炉采用泡沫渣工艺、强化连铸保护浇注等措施,可以有效地减少钢中的氮含量。
连铸长水口采用新型密封垫非常有效,浇注过程钢水增氮量在8X10-6以下。
5.4随着脱氧剂的加入,炉渣成分在LF精炼前、LF精炼结束后,VD处理后发生了变化,渣中A1203的活度分别变为0.01966,0.02299,0.034580随着炉渣中Al_03活度的增大,炉渣吸附Al_03类夹杂物能力减弱,钢中A1203夹杂物的去除速度减慢。
钢液在LF精炼前卞要以Al203,FeS,Mg0.A1203类夹杂为主;LF精炼结束后以A1203和FeS类夹杂为卞,还有少量的Ca0.A1203类复合夹杂物;VD处理后以A1203类夹杂为主。
随着精炼的进行,夹杂物数量和面积逐渐减少,并由不规则形状变为规则形状。
在铝脱氧钢的Ca0-Si0-A1203-Mg0四元渣系中,钢中[A1]含量分别为1.2,5.02,31.9ppm,当[Mg]含量分别在0.6726.05,1.739766.735,5.568232ppm会形成Mg0.Al2O3;当[Mg]含量分别小于0.67,1.7397, 5.568ppm时,Mg0.Al203则会分解形成A12O3。