高炉炼铁技术
高炉炼铁技术简介
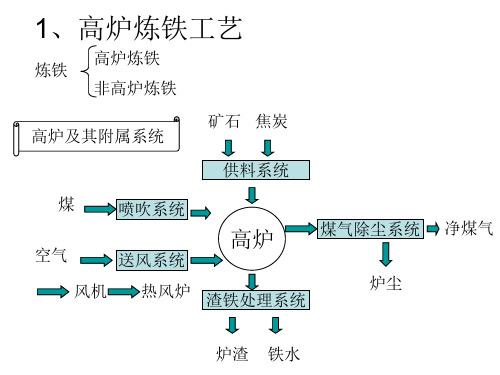
烧结 工艺 流程
精矿、粉矿 (0~10mm)
石灰石、白云石 (80~0mm)
碎焦、无烟煤 (25~0mm)
破碎
>3mm
• 炉渣中氧化物的种类:碱性氧化物、酸性氧化物 和中性氧化物。以碱性氧化物为主的炉渣称碱性 炉渣;以酸性氧化物为主的炉渣称酸性炉渣。
• 炉渣的碱度(R):炉渣中碱性氧化物和酸性氧化 物的质量百分数之比表示炉渣碱度:
• 高炉炉渣碱度一般表示式:R=w(CaO)/w (SiO2)
• 炉渣的碱度根据高炉原料和冶炼产品的不同,一 般在1.0~1.25之间。
消耗的(干)焦炭量(焦比一定的情况 下)
高炉每天消耗的焦炭量 I=
高炉的有效容积
• 生铁合格率:生铁化学成分符合国家标准的总量 占生铁总量的指标。
• 休风率:高炉休风时间(不包括计划大、中、小 修)占日历工作时间的百分数。
规定的日历作业时间=日历时间-计划大中修及
封炉时间
休风率=
高炉休风时间 规定的日历作业时间 ×100%
高炉炉渣与脱硫
• 高炉炉渣是铁矿石中的脉石和焦炭(燃料)中 的灰分等与熔剂相互作用生成低熔点的化 合物,形成非金属的液相。
– 高炉炉渣的成分 – 高炉炉渣作用 – 成渣过程 – 生铁去硫
• 高炉炉渣的来源:矿石中的脉石、焦炭(燃料)中 的灰分、熔剂中的氧化物、被侵蚀的炉衬等。
• 高炉炉渣的成分:氧化物为主,且含量最多的是 SiO2、CaO、Al2O3、MgO。
② 物理性能 包括机械强度和粒度组成等。高炉要求烧结矿机械 强度高,粉末少,粒度均匀。 烧结矿粒度小于5mm的称之为粉末。粉末含量对高 炉料柱透气性影响很大。粉末含量高,高炉透气性差, 导致炉况不顺,可能引起崩料或悬料。 反应机械强度的指标为:转鼓指数、抗磨指数、筛 分指数。 目前武钢烧结矿的转鼓强度大约在79%~80%左右。
国内外高炉炼铁技术的发展现状和趋势

国内外高炉炼铁技术的发展现状和趋势高炉炼铁技术是金属冶炼工业发展的基础,是保证金属铁质量和产量的关键技术,也是社会经济发展的重要依托。
近年来,随着金属冶炼工业的快速发展,国内外高炉炼铁技术的发展也取得了显著的成就,为保证金属铁质量、提高产量、提高经济效益发挥了重要作用。
首先,国内外高炉炼铁技术取得了重大突破,进一步提高了金属铁质量。
随着科学技术的进步,添加剂和冶炼工艺的改进,使高炉炼铁工艺取得重大进展,不仅能够有效提高铁素体组成,同时也能够改善铁水的流动性,有利于铁块的全面成型。
此外,利用新型炉料和改进的热处理技术,可以有效降低铁水的含氧量,提高铁液的液相容量,从而获得更高品质的铁。
其次,国内外高炉炼铁技术的发展,还大大提高了铁的产量。
传统的高炉炼铁工艺存在着大量的炉料损失,限制了铁的产量。
随着国内外高炉炼铁技术的发展,炉料损失大大减少,产量得到提高。
通过对炼铁工艺及其参数进行优化调整,获得合理的炉料计算和分配,进而有效提高铁的产量。
此外,结合智能技术、自动化技术和智能控制技术,还可以实现远程监控和智能化管理,可以使高炉炼铁效率更高,产量更大。
最后,国内外高炉炼铁技术的发展,对提高经济效益具有重要意义。
国内外高炉炼铁技术的发展,不仅缩短了铁的生产周期,提高了产量,而且可以减少能耗消耗和废气排放,降低了生产成本,有利于提高企业的竞争力,实现更高的经济效益。
此外,国内外高炉炼铁技术的发展还可以改善炼铁终端的工作环境,为炼铁行业的发展创造更加良好的条件。
以上是国内外高炉炼铁技术的发展现状和趋势的概述,未来的发展趋势可以简单地总结为以下几点:继续提高高炉炼铁质量和产量,推广智能技术,进一步优化炼铁工艺,合理设计炉料配比,提高炼铁效率,减少能耗和污染,改善炼铁环境,提高经济效益,实现绿色经济发展。
未来,相信国内外高炉炼铁技术将取得更好的发展,为我们社会的经济发展提供更多的依托。
高炉炼铁工艺技术标准最新

高炉炼铁工艺技术标准最新高炉炼铁工艺技术标准最新700字高炉炼铁工艺技术标准是指在高炉炼铁过程中所涉及到的各种操作和参数的标准。
这些标准的制定对于确保高炉正常运行、提高炼铁效率、降低能耗和保护环境具有重要意义。
下面将介绍高炉炼铁工艺技术标准的最新内容。
1. 原料配比标准:高炉炼铁的原料主要包括铁矿石、焦煤和石灰石。
原料的配比直接影响到炼铁的效果和产品质量。
根据不同的铁矿石和焦煤的性质,制定合理的配比标准,确保高炉内的还原和熔化反应能够顺利进行,同时减少生产成本。
2. 炉渣成分标准:高炉炼铁产生的炉渣是含有高炉灰渣、熔渣和炉渣球等物质的复杂体系,其成分对炼铁过程和产品质量有着重要影响。
制定炉渣成分标准,旨在控制炉渣中各种氧化物和杂质的含量,使炉渣具有良好的流动性、透气性和脱硫脱磷能力。
3. 炉渣脱硫脱磷标准:高炉炼铁过程中,炉渣中的主要成分之一是含有硫和磷的物质。
高炉炼铁工艺技术标准要求对炉渣进行适当的脱硫和脱磷处理,以降低钢铁中的硫和磷含量,提高产品的质量。
4. 炉温和气氛控制标准:高炉炼铁过程中,炉温和气氛对炼铁过程和产品质量起着决定性的作用。
工艺技术标准要求对炉温和气氛进行实时监测和控制,以确保高炉内的化学反应能够充分进行,并减少不良反应和产生有害气体。
5. 炉压和风速控制标准:高炉炼铁过程中,炉压和风速对炼铁效果和能耗有着直接的影响。
制定合理的炉压和风速控制标准,可以保证高炉的正常运行,提高炼铁效率,降低能耗。
6. 冷却水质量标准:高炉炼铁过程中,冷却水用于冷却高炉的各种设备和管道,其质量对设备的寿命和运行稳定性有着重要影响。
制定冷却水质量标准,对冷却水进行定期检测和处理,可以防止设备的腐蚀和水垢的产生,延长设备的使用寿命。
7. 炉外环境保护标准:高炉炼铁过程中,会产生大量的炉渣、烟尘、废水和废气等污染物。
工艺技术标准要求在高炉炼铁过程中采取有效的控制措施,减少污染物的排放,保护环境。
以上是高炉炼铁工艺技术标准的最新内容。
高炉炼铁工艺技术标准

高炉炼铁工艺技术标准高炉炼铁是一项复杂的工艺过程,需要严格遵守一系列的技术标准来保证炼铁质量和生产效率。
下面将介绍一些关键的高炉炼铁工艺技术标准。
首先,高炉的炉料配比是一项非常重要的技术标准。
炉料主要包括铁矿石、焦炭和熔剂等。
合理的炉料配比可以保证炉内的物料成分符合要求,达到理想的还原效果。
配料时需要考虑铁矿石的品质、矿石的粒度、焦炭的品质和灰分等因素。
此外,还需要根据高炉运行情况进行及时调整,确保炉料配比的稳定性。
其次,高炉炉温的控制是非常关键的技术标准。
高炉的炉温直接影响到铁矿石还原的速度和产量。
过高的炉温会导致炉内的矿石过度还原,从而产生大量的炉渣。
过低的炉温则会使得还原反应缓慢,影响生产效率。
因此,需要通过调整空气和燃料的供给来控制炉温,确保在合适的范围内。
此外,高炉的风量控制也是一项重要的技术标准。
风量的大小直接影响到炉内氧气的供应和燃烧的强度。
过大的风量会导致过量的氧气进入炉内,从而引起废气中氧含量过高,浪费燃料。
过小的风量则会导致缺氧现象,影响还原反应的进行。
因此,需要根据高炉的情况调整风量,保持合适的氧气供应和燃烧强度。
最后,高炉炼铁还需要严格遵守安全操作规程,确保生产过程的安全性。
操作人员应该经过专业培训,了解高炉的工作原理和操作技术。
在操作过程中,要注意加强高炉的维修和保养工作,及时处理设备故障和热态问题,确保设备的正常运行。
此外,还要定期进行安全检查,防止因设备老化和工程安全漏洞引发事故。
总之,高炉炼铁工艺技术标准包括炉料配比、炉温控制、风量控制以及安全操作等方面。
只有严格遵守这些标准,才能保证高炉的正常运行和炼铁的质量。
高炉炼铁的主要工艺流程

高炉炼铁的主要工艺流程
《高炉炼铁的主要工艺流程》
高炉是钢铁企业中用于炼铁的主要设备,其工艺流程是将铁矿石和焦炭加入高炉内,经过一系列的化学和物理反应,最终得到熔融的生铁。
下面将介绍高炉炼铁的主要工艺流程。
1. 搅拌坩埚法:将原铁矿石和焦炭按一定的比例混合,放入高炉的上部,即炉料层。
在高炉内,炉料层受到高温和高压的影响,发生一系列的物理和化学反应。
2. 燃烧:通过给炉料层加入空气或者氧气,点燃炉料层的顶部,使其燃烧。
燃烧产生的热量使炉料层内的焦炭燃烧,并提供高温条件,促进各种反应的进行。
3. 还原反应:当焦炭燃烧释放出一定量的一氧化碳时,与高炉内的铁矿石发生还原反应,使氧化铁还原为生铁。
4. 精炼:在高温下,生铁中的杂质和一些有害元素(如硫、磷等)会被氧化成气体,并通过炉顶排出。
这一过程称为精炼,是炉料中杂质清除的重要环节。
5. 收得生铁:经过一定时间的冶炼,高炉内的炉料最终产生了熔融的生铁。
生铁通过炉口排除,并进入铁水槽中,成为炼铁的产物。
通过上述简单介绍,可以看出高炉炼铁的主要工艺流程是一个
复杂的过程,包括搅拌坩埚法、燃烧、还原反应、精炼和收得生铁等环节。
这一流程不仅需要科学合理的原料比例和控制方法,还需要高炉操作者的丰富经验和技巧。
只有合理的工艺流程和专业的操作技术,才能保证高炉炼铁的顺利进行和生产出优质的生铁产品。
高炉炼铁技术创新实践及未来展望

千里之行,始于足下。
高炉炼铁技术创新实践及未来展望高炉炼铁技术是钢铁工业中非常重要的一个环节,对于钢铁产量和质量有着直接影响。
随着科技的不断发展和进步,高炉炼铁技术也在不断创新和实践。
本文将介绍高炉炼铁技术的创新实践及未来展望。
高炉炼铁技术主要包括焦炭冶炼、铁矿石还原和炉渣处理三个方面。
近年来,针对这几个环节进行了一系列的技术创新,以提高钢铁产量和质量,减少能源消耗和环境污染。
首先,在焦炭冶炼方面,高炉炼铁技术实践了煤炭气化技术,将煤炭转化为合成气或制备气,用来代替部分焦炭。
这样可以减少焦炭的消耗量,提高炉温和炉效,提高炼铁效果和节约能源。
其次,在铁矿石还原方面,高炉炼铁技术实践了混合还原技术,将不同种类的铁矿石混合使用,以提高还原效率和减少还原剂的消耗。
同时,还运用了制粒和球团矿技术,提高了炉料的密实度和还原性能,使得炼铁效果更好。
再次,在炉渣处理方面,高炉炼铁技术实践了炉渣处理技术,包括高炉渣套料、炉渣粉磨和炉渣稳定化等。
这些技术可以减少炉渣的生成和排放,降低对环境的污染,同时还能回收利用一部分有价值的元素。
未来,高炉炼铁技术仍将继续创新和发展。
一方面,可以进一步拓宽原料的来源,包括使用青海盐湖等资源,以降低对传统铁矿石的依赖程度。
另一方面,可以进一步提高炉渣的利用率,实现钢铁工业的循环经济。
此外,还可以用高效节能的加热方式替代传统的冶炼方法,以进一步降低能源消耗和环境污染。
第1页/共2页锲而不舍,金石可镂。
综上所述,高炉炼铁技术的创新实践为钢铁工业的发展提供了重要支撑。
未来,随着技术的不断进步和创新,高炉炼铁技术将更加高效、环保和可持续,为钢铁产量和质量的提高做出更大贡献。
同时,需要在技术创新的同时,加强对环境保护的重视,实现钢铁工业的可持续发展。
高炉炼铁工艺
高炉炼铁工艺1. 引言高炉炼铁工艺是一种重要的冶金工艺,用于将铁矿石转化为铁。
高炉炼铁工艺包括矿石的预处理、炉料的准备、高炉的操作和炉渣与铁的分离等环节。
本文将对高炉炼铁工艺进行详细介绍。
2. 高炉的结构和原理高炉通常由炉壳、炉底、炉缸、炉肩和炉体等部分组成。
炉壳一般由钢板和砖块组成,用于维持高炉的结构稳定性。
炉底用于收集和排除废气和炉渣。
炉缸用于装载矿石和焦炭。
炉肩用于收集和排除废气。
炉体是高炉的主要部分,其中进行矿石的还原和铁的生成等反应。
在高炉中,矿石和焦炭经过预处理后,被装入炉缸中。
在高炉的下部,焦炭燃烧产生的热量引发了矿石的还原反应,将铁氧化物还原为金属铁。
金属铁被熔化后,与炉渣分离,从高炉的底部流出。
3. 高炉炼铁工艺的步骤高炉炼铁工艺主要包括以下步骤:3.1 矿石的预处理矿石通常经过破碎、磨矿和磁选等预处理步骤。
破碎将矿石破碎成较小的颗粒,磨矿将其继续细分为更小的粉末。
磁选通过磁力作用分离出含有铁矿石的矿石。
3.2 炉料的准备炉料的准备包括将矿石、焦炭和燃料添加剂按比例混合,并根据需要进行搅拌和湿润。
混合后的炉料被装入炉缸中。
3.3 高炉操作炉料在高炉中逐渐下降,并在炉体内发生化学反应。
在高炉的下部,焦炭燃烧产生的热量引发了还原反应。
炉料中的铁氧化物被还原为金属铁,并与焦炭燃烧产生的一氧化碳反应生成炉渣。
3.4 炉渣与铁的分离金属铁与炉渣分离的关键是密度差异。
金属铁的密度较高,会在炉体底部汇聚并流出高炉。
而炉渣的密度较低,会在炉体内浮动,并通过炉肩和炉口排出。
4. 高炉炼铁工艺的优缺点4.1 优点•能够将不同品位的铁矿石炼制为高品位的铁产品;•炼铁过程中可以降低有害杂质的含量,提高产品质量;•高炉可以实现连续生产,提高生产效率。
4.2 缺点•高炉炼铁工艺对能源的消耗较大,对环境造成一定影响;•高炉炼铁的操作过程较为复杂,需要高度专业化的操作技术和设备。
5. 结论高炉炼铁工艺是一种重要的冶金工艺,用于将铁矿石转化为铁。
高炉炼铁技术主要工艺参数计算公式
高炉炼铁技术主要工艺参数计算公式高炉炼铁是指利用高炉设备将铁矿石还原为铁的过程。
在高炉炼铁的工艺过程中,有许多重要的工艺参数需要计算。
下面介绍一些主要的工艺参数以及它们的计算公式。
1.高炉容积高炉容积是指高炉炉腔的有效容积。
一般情况下,高炉容积的计算可采用下述公式:高炉容积=炉体截面积×炉腹高度2.放料形状系数放料形状系数是指炉料在高炉炉腔中的堆积状态与整体放料时的体积比。
它可以通过炉料体积与放料形状容积的比值来计算:放料形状系数=炉料体积/放料形状容积3.补炉系数补炉系数是指每次补炉铁量与高炉有效容积之比。
一般情况下,补炉系数的计算可采用下述公式:补炉系数=每次补炉铁量/高炉有效容积4.炉渣量炉渣量是指在高炉炼铁过程中生成的炉渣的数量。
它可以通过铁矿石中的炉渣含量与高炉铁量之比来计算:炉渣量=高炉铁量×炉渣含量5.进料系数进料系数是指进入高炉的原料中铁矿石与高炉铁量之比。
一般情况下,进料系数的计算可采用下述公式:进料系数=铁矿石量/高炉铁量6.还原度还原度是指高炉还原反应的程度,也可以理解为高炉炼铁过程中铁矿石中铁元素的转化率。
还原度可以通过炉内原料的化学成分以及进气温度等因素进行估算。
7.炉渣碱度炉渣碱度是指炉渣中碱金属氧化物与二氧化硅之比。
一般情况下,炉渣碱度的计算可采用下述公式:炉渣碱度=(Na2O+K2O)/SiO2以上是一些高炉炼铁过程中常用的工艺参数及其计算公式。
当然,实际计算过程可能会更加复杂,因为高炉炼铁是一个多参数、多反应的复杂过程。
因此,在实际操作中需要根据具体情况综合考虑各个因素,并进行相应的修正计算。
高炉炼铁工艺技术标准规范
高炉炼铁工艺技术标准规范
高炉炼铁工艺技术标准规范是指在高炉炼铁过程中,根据生产要求和技术要求,对工艺流程、工作条件、操作规程、设备要求等方面进行规范的文件。
下面将对高炉炼铁工艺技术标准规范进行讨论。
一、工艺流程:高炉炼铁是一个复杂的过程,需要经过多个工艺环节。
工艺流程规范包括原料的配料、炉顶进料、燃料的燃烧、炉渣的生成和处理、铸铁的出炉等环节。
每个环节都有一定的要求和工艺控制参数,需要遵循标准规范的要求进行操作。
二、工作条件:高炉炼铁的工作条件包括温度、压力、流量等要素。
这些要素对炼铁的质量和效率都有很大的影响。
标准规范应明确各个工作条件的要求,以确保炼铁过程的正常进行。
三、操作规程:高炉炼铁的操作规程是操作人员进行工作时应当遵循的指南。
操作规程应包括各个操作环节的步骤、注意事项、安全措施等内容。
标准规范应确保操作规程的科学合理性,以保证生产的安全性和可控性。
四、设备要求:高炉炼铁需要各种设备的支持和配合,包括高炉本体、燃烧系统、热风炉等。
设备要求方面,标准规范应明确各个设备的技术指标、性能要求、工作条件等内容,以保证设备的正常运行和高炉炼铁的顺利进行。
总之,高炉炼铁工艺技术标准规范对高炉炼铁的生产起到非常重要的指导作用。
它规范了炼铁过程中的工艺流程、工作条件、
操作规程和设备要求等方面,确保了高炉炼铁的科学性、安全性和效率性。
只有严格按照标准规范执行,才能保证高炉炼铁生产的正常进行,提高生产效率和质量,降低能耗和环境污染,为企业的可持续发展做出贡献。
高炉炼铁工艺
高炉炼铁工艺1. 预处理原料:在高炉炼铁之前,需要对原料进行一定的预处理。
首先要破碎和磨细铁矿石,以增加其表面积,便于后续的还原反应。
同时要对焦炭进行粉煤处理,以增加其反应表面积,并降低硫和灰分含量。
此外,石灰石也需要进行破碎和磨细,以便混合均匀。
2. 加料和还原反应:预处理好的原料按一定比例加入高炉中,与风推入的煤气(还原气)一起在高温下进行还原反应。
在这个过程中,煤气中的一氧化碳和二氧化碳与铁矿石中的氧化铁发生化学反应,将氧气从氧化铁中除去,从而生成熔融的铁水和气体的渣浆。
3. 收集铁水:熔融的铁水通过高炉底部的出口流出,并收集到铁水坩埚中。
铁水可以通过连续铸造机或者浇铸处理成各种规格和形状的铸铁产品。
4. 渣浆处理:在还原反应过程中,高炉内产生的含有铁和其他杂质的渣浆需要被处理。
通常,渣浆会通过热风炉或转炉处理,以及重新冶炼过程,从而提炼出有用的铁和其他金属。
高炉炼铁工艺是一项高温高压的工艺过程,需要严格控制各种工艺参数,以保证生产铁水的质量和数量。
同时,高炉炼铁工艺也是一个能耗较高的工艺过程,如何提高能源利用效率,降低生产成本,是钢铁企业一直在努力解决的问题。
随着科技的不断创新和进步,高炉炼铁工艺也在不断地完善和改进,为钢铁工业的可持续发展做出了重要贡献。
高炉炼铁工艺作为钢铁行业的核心工艺之一,对于钢铁产品的质量和产量起着至关重要的作用。
在过去的几十年里,随着工业技术的不断发展和创新,高炉炼铁工艺也在不断地完善和改进。
首先,钢铁企业在高炉炼铁工艺方面不断引入优化技术和自动化控制系统,以提高生产效率和产品质量。
通过智能化技术,高炉操作可以更加精准和稳定,从而减少了人为因素对于生产过程的影响,提高了工作效率和产品一致性。
同时,一些新型的高炉炼铁工艺还采用了先进的能源回收技术,将废热和废气重新利用,从而降低了能源消耗和环境排放,实现了资源的合理利用。
其次,高炉炼铁工艺也在材料的选用上有了新的突破。
- 1、下载文档前请自行甄别文档内容的完整性,平台不提供额外的编辑、内容补充、找答案等附加服务。
- 2、"仅部分预览"的文档,不可在线预览部分如存在完整性等问题,可反馈申请退款(可完整预览的文档不适用该条件!)。
- 3、如文档侵犯您的权益,请联系客服反馈,我们会尽快为您处理(人工客服工作时间:9:00-18:30)。
294.7 33.9 155.4 27.68 34.50 14.58 24.62
4644? 1235 0.27
1.1.高炉燃料比有所上升 近年来,世界性的原燃料供应紧张,价位攀升,成份 波动大,给高炉炼铁带来了较大的负面影响。突出表现在 入炉品位下降和成分不稳定,加大了高炉操作技术的难 度,呈现出炼铁燃料比在上升的态势。2008 年前 8 个月度 全国重点钢铁企业炼铁燃料比为 532Kg/t,比上年同期上 升 2Kg/t。燃料比较好的企业有:首钢 466Kg/t,宝钢集 团 483Kg/t,太钢 471Kg/t,武钢 492Kg/t,鞍钢 495Kg/t, 马钢 488Kg/t,冶钢 510Kg/t,天铁 510Kg/t。 全 世 界 高 炉 炼 铁 平 均 燃 料 比 为 543Kg/t , 德 国 为
504.94 496.93 521.18
南钢 2 2500 542.4
沙钢
2680 542.78
唐钢 3 2560 507.79
武钢 4 2600 487.9
首钢 1 2536 481.5
3 2536 472.5
首迁 1 2650 407.3
2 2650 465.1
3
Kg/t 入炉焦比 Kg/t 小块焦比 Kg/t 喷煤比 Kg/t 吨铁电耗 Kwh/t 吨铁氧耗 m³/t 吨铁蒸汽 耗 Kg/t 吨铁压缩 空气耗 m³/t 鼓风风量 m³/t 热风温度 ℃ 吨铁耗新 水 m³/t
表 1 全国重点钢铁企业高炉技术经济指标
项目
2008 年前 8
2007 年
个月
全国生铁产量,万 32912.11
46944.63
t
高炉利用系数, t/(m3•d)
2.610
2.677
综合焦比,kg/t 入炉焦比,kg/t 喷煤比,kg/t 热风温度,℃ 入炉矿品位,% 休风率,% 炼铁工序能耗, kgce/t
6
2008 年前 8 个月全国重点钢铁企业热风温度为 1123 ℃,比上年度下降 1℃。2007 年全国重点钢铁企业热风温 度为 1125℃。2008 年前 8 个月,风温较高的企业有:河 北德龙 1186℃、太钢 1187℃、首钢 1180℃、攀钢 1179℃、 宝钢集团 1152℃、邢台 1147℃、莱芜 1153℃、沙钢怀特 1154℃、武钢 1140℃、鞍钢 1163℃,三明 1171,天铁 1153, 邢钢 1147。
马钢 A、B 4000 294.9 38 158.8 30.7 39.7
1210
2
TRT Kwh/t 除尘方式 环保运行率 水耗 m³/t 入炉品位 %
31.22 湿法
31.86 湿法
36.86 湿法
0.541 60.32
0.559 60.22
0.656 60.34
表 3 2007 年 3200m3高炉技经指标
37.9 湿法
0.64 60.25
32.3 布袋除尘 12 万度/日 0.39 59.75
23 湿法 12.3 0.Fra bibliotek3 58.92
企业
鞍钢
天钢
武钢
唐钢
炉号
新1 新2 新3
2
6
7
5
系数,t/m2.d 焦比,kg/t
2.437 318.62
2.363 337.7
2.319 341.05
2.131 390.67
2004 年
25185.05
2.516
526 427 116 1074 58.21 1.850 466.20
表 2 2007 年度 4000 立方米级高炉经济运行指标
1#
2#
3#
年产量 万吨
3246452 3792257 3910781
容积 m³
4063
4706
4350
燃料比 Kg/t
94.22
499.7
2008 年前 8 个月,喷煤比高的企业有:太钢 180、宝 钢集团 164、石钢 165、江阴兴澄 165、酒钢 165、新兴铸 管 163、邢台 159、武钢 160、长治 179、莱钢 157、济源 157、德龙 153、鞍钢 150,天铁 150,济钢 148,湘钢 147, 永钢 147。 1.3. 热风温度在波动之中
鼓风单耗 m³/t
1051.9 968.2
959.23
热风温度 ℃
1240
1239
1244
4# 4069048 4747 499.37 266.86 17.82 214.68 62.18 56.87 11.85
918.4 1242
太钢 288.5 4350 465.75 304 18.5 181.25 34.44 31.09 10.89 55.50 983.75 1225.75
1075 0.77
369 37 156 48.35 36.11 0.047 0.029
1065 1138 4.61
457.8 23.5 79.3 154.35 16.59 29.20
1028.79 1.521
440.98 43.84 83.43 29.55 31.37
1081 0.74
393.6 21.12 121.62 30.12 16.25 91.06 16.81
环保设施运行率,%
98.39 100
100
总电耗 104 kwh 83.98 755.5 755.5
吨铁耗新水,t/t
0.653 0.726 0.709 0.425
2.24
2.74
11
企业 炉号 炉容 m³ 综合焦比
表 4 2500 m³级 高炉技经指标
鞍钢
承德 马钢
7
11
5
2580 2580 2500 2500
宝钢高炉入炉焦比在 266~288Kg/t,太钢高炉入炉焦 比为 291 Kg/t,已属国际领先水平。国际水平的入炉焦比 是在 400Kg/t 以下。2008 年前 8 个月我国有 28 个企业入 炉焦比低于 400Kg/t。炼铁燃料比是在一定范围内波动,
5
要想降低焦比,只有采取提高精料水平,喷煤比,提高热 风温度和提高高炉操作水平等措施。当前影响我国高炉生 产的最大因素是原燃料成分不稳定。 1.1 喷煤比呈下降态势
1330 1092 2.58
325.2 39.1 164.4 27.53 76.56 21.33 49.15
1175 1140 3.25
325.4 19.6 139.7 21.38 14.7 24.53
344.4 23.9 119.2 36.04 3.20 25.07
307.1 30.5 157.5 30.77 28.45 15.79 23.68
4
496Kg/t,中国台湾为 488Kg/t,欧盟 15 国为 494Kg/t, 南美为 496Kg/t,日本为 498Kg/t,南韩为 503Kg/t,北美 为 510Kg/t。
燃料比=焦比+喷煤比+小块焦比。喷煤比是不考虑置换 比。这样比较科学,企业之间有可比性。我国有些企业的 小块焦比不做统计。南韩燃料比之中的喷煤比最高,在 160Kg/t 以上,日本、南美、欧盟、中国台湾及德国的喷 煤比也是比较高的,在 130Kg/t 以上。 1.2. 入炉焦比在升高
354 49.75 136.11 41.11 28.66 0.144 43.22
1146 1123 0.652
354.37 46.25 129.41 34.68 15.07 0.143 43.22
1153 1120 0.653
462.05 9.54 63.72 66.25 12.09 40 26.3
523 399 134 1123 57.36 1.754 430.11
518 392 137 1125 57.71 1.524 426.84
2006 年
40416.70
2.675
516 396 135 1100 57.78 1.661 430.59
2005 年
33741.13
2.642
522 412 124 1084 58.03 1.846 445.71
30.4 485.4 34.3 56.54 0.095
44
鼓风消耗,m3/t
1036 1037 1019 1146.15 1006 1086 1290
热风温度,℃
1203 1194 1209
1145
1142 1170 1117
TRT发电总量 104 kwh
2128 1863.1 1538.7 1668 32.02 度/t 35.88 9.8
我国大高炉炼铁技术发展 A
王维兴
(中国金属学会 北京 100711)
近年来,我国炼铁工业处于高速发展阶段,2007 年全国 生铁产量达到 4,6944 亿吨,比上年度增长 15.19%,占世界 总产量的 49.74%。2008 年前 8 个月生铁产量达到 3.2912 亿 吨,比上年度增长 6.50%,产量的增速有所下降。预计今年 全国生铁产量会超过 5.2 亿吨,炼铁生产能力超过 6 亿吨, 但有 6000 万吨/年的生产能力居于淘汰之列(主要是 300m³ 以下容积小高炉)。
495.67
入炉焦比 Kg/t
288.7
276.7
280.65
小块焦比 Kg/t
10.94
17.53
18.94
煤比 Kg/t
194.58 205.47 196.04
电耗 Kwh/t
59.06
42.59
43.14
氧耗 m³/t
35.78
52.29
62.69
蒸汽耗 Kg/t
16
13.12
14.29