年产530万吨生铁的高炉炼铁车间工艺设计毕业论文
毕业论文:高炉炼铁系统设计-精品【范本模板】
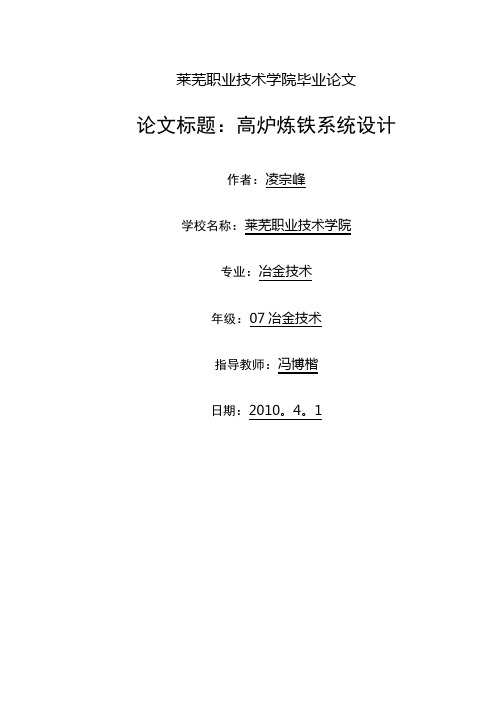
莱芜职业技术学院毕业论文论文标题:高炉炼铁系统设计作者:凌宗峰学校名称:莱芜职业技术学院专业:冶金技术年级:07冶金技术指导教师:冯博楷日期:2010。
4。
1目录内容提要与关键词¨¨¨¨¨¨¨¨¨¨¨3手抄在论文本上,最后再根据内容补填目录,要求手写!正文¨¨¨¨¨¨¨¨¨¨¨¨¨¨¨¨¨4参考文献¨¨¨¨¨¨¨¨¨¨¨¨¨¨¨¨58摘要本设计要求建年产量为200万吨生铁的高炉系统。
高炉车间的七大系统:即高炉本体系统、上料系统、渣铁处理系统、喷吹系统、送风系统、除尘系统和冷却系统都做了较为详细的叙述。
高炉炼铁是获得生铁的主要手段,是钢铁冶金过程中最重要的环节之一,在国民经济建设中起着举足轻重的作用。
高炉是炼铁的主要设备,本着优质、高产、低耗和对环境污染小的方针,在预设计建造一座年产生铁200万吨的高炉炼铁系统,本设计说明书详细的对其进行了高炉设计,其中包括绪论、工艺计算(包括配料计算、物料平衡和热平衡)、高炉炉型设计、高炉各部位炉衬的选择、炉体冷却设备的选择、风口及出铁场的设计、原料系统、送风系统、煤气处理系统、渣铁处理系统、高炉喷吹系统等。
设计的同时还结合国内外相同炉容高炉的一些先进的生产操作经验和相关的数据,力争使该设计的高炉做到高度机械化、自动化和大型化,以期达到最佳的生产效益. 关键词:高炉;炼铁;设计;煤气处理;渣鉄处理;1绪论1。
1概述钢铁是重要的金属材料之一,被广泛应用于各个领域,钢铁生产水平是一个国家发展程度的标志。
年产量500万吨高炉炼铁车间设计毕业论文
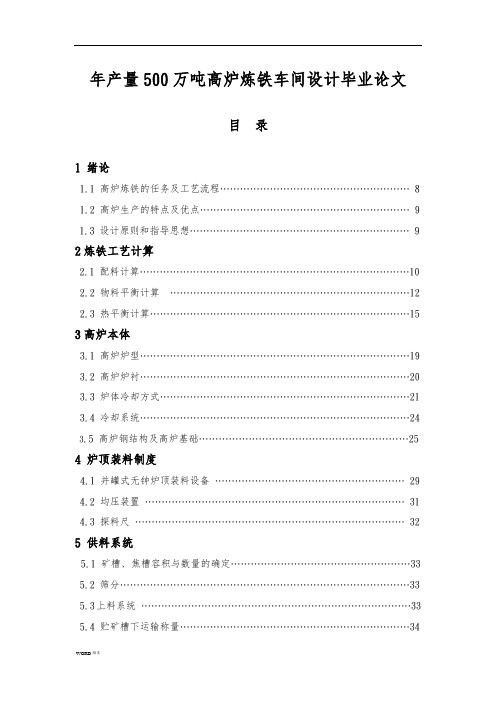
年产量500万吨高炉炼铁车间设计毕业论文目录1 绪论1.1 高炉炼铁的任务及工艺流程 (8)1.2 高炉生产的特点及优点 (9)1.3 设计原则和指导思想 (9)2炼铁工艺计算2.1 配料计算 (10)2.2 物料平衡计算 (12)2.3 热平衡计算 (15)3高炉本体3.1 高炉炉型 (19)3.2 高炉炉衬 (20)3.3 炉体冷却方式 (21)3.4 冷却系统 (24)3.5 高炉钢结构及高炉基础 (25)4 炉顶装料制度4.1 并罐式无钟炉顶装料设备 (29)4.2 均压装置 (31)4.3 探料尺 (32)5 供料系统5.1 矿槽、焦槽容积与数量的确定 (33)5.2 筛分 (33)5.3上料系统 (33)5.4 贮矿槽下运输称量 (34)6送风系统6.1 鼓风机的选择 (35)6.2 热风炉的结构 (35)6.3 热风炉常用耐火材料 (37)6.4 燃烧器及送风制度的选择 (37)6.5 热风炉主要管道直径的选定 (37)7.渣铁处理系统7.1 风口平台及出铁场 (39)7.2 炉前设备 (39)7.3 炉渣处理 (41)8 煤气除尘系统8.1 除尘设备及原理 (44)8.2 有关设备 (45)8.3 重力除尘器 (45)9 喷吹设备9.1 设计为喷吹煤粉 (47)9.2 高炉喷煤设备 (48)10车间布置形式10.1 车间布置 (50)10.2 本设计车间平面布置形式 (50)结束语 (52)参考文献 (53)1 绪论1.1 高炉炼铁的任务及工艺流程高炉炼铁的任务是用还原剂(焦炭、煤粉)在高温条件下将铁矿石或含铁原料还原成液态生铁的过程。
高炉生产要求以最小的投入获得最大的产出,即做到高产、优质、低耗、有良好的经济效益。
高炉生产时借助高炉本体和其辅助设备来完成的。
高炉本体是冶炼生铁的主体设备,它是由耐火材料砌筑的竖立式圆筒形炉体,最外层是由钢板制成的炉壳,在炉壳和耐火材料之间有冷却设备。
高炉炼铁论文

高炉炼铁论文时间:2010-11-12 08:12:40|浏览:112次|评论:0条 [收藏] [评论] [进入论坛]本文针对高炉炼铁工艺的生产现状进行了其技术性研究,使其高炉炼铁具有规模大、效率高、成本低等诸多优势,随着技术的发展,高炉正朝着大型化、高效化和自动化迈进。
实现渣铁分离。
已熔化的渣…本文针对高炉炼铁工艺的生产现状进行了其技术性研究,使其高炉炼铁具有规模大、效率高、成本低等诸多优势,随着技术的发展,高炉正朝着大型化、高效化和自动化迈进。
实现渣铁分离。
已熔化的渣铁之间及与固态焦炭接触过程中,发生诸多反应,最后调整铁液的成分和温度达到终点。
故保证炉料均匀稳定的下降,控制煤气流均匀合理分布是高质量完成冶炼过程的关键。
关键词: 固态焦炭渣铁分离炉料均匀煤气流分布绪论高炉是炼铁的专用设备。
虽然近代技术研究了直接还原、熔融技术还原等冶炼工艺,但它们都不能取代高炉,高炉生产是目前获得大量生铁的主要手段。
高炉生产是可持续的,他的一代寿命从开炉到大修的工作日一般为7-8年,有的已达到十年或十年以上。
高炉炼铁具有规模大、效率高、成本低等诸多优势,随着技术的发展,高炉正朝着大型化、高效化和自动化迈进。
1.1我国钢铁工业生产现状近代来高炉向大型化发方向发展,目前世界上已有数座5000立方米以上容积的高炉在生产。
我过也已经有4300立方米的高炉投入生产,日产生铁万吨以上,日消耗矿石等近2万吨,焦炭等燃料5千吨。
这样每天有数万吨的原、燃料运进和产品输出,还需要消耗大量的水、风、电气,生产规模及吞吐量如此之大,是其他企业不可比拟的。
1.2加入世贸对我国钢铁经济的影响钢铁工业是人类社会活动中占有着极其重要的地位,对发展国民经济起着极其重要的作用。
无论工业、农业、交通、建筑及国防均离不开钢铁。
一个国家的钢铁生产水平,就直接反映了这个国家的科学技术发展和人民的生活水平。
那么自中国加入世贸组织之后,自2001年底以来,全球钢铁价格已上涨2倍,提升了该行业的盈利水平。
设计年产395万吨合格连铸坯的转炉炼钢车间毕业设计

设计年产395万吨合格连铸坯的转炉炼钢车间毕业设计目录摘要............................................... 错误!未定义书签。
Abstract ........................................... 错误!未定义书签。
目录 (I)绪论 (1)1 设计方案的确定与论证 (2)1.1 产品大纲的制定 (2)1.1.1 产品大纲制定的原则及方法 (2)1.1.2 产品大纲 (2)1.1.3 典型钢种(IF钢)的介绍 (3)1.1.4 E36船板钢 (4)1.1.5 Q235结构钢 (5)1.1.6 X80管线钢 (6)1.1.7 耐候钢 (6)1.2 方案的选择与论证 (7)1.2.1 炉容量与座数的确定 (7)1.2.2 冶炼与精炼方法的选择与论证 (8)1.2.3 连铸机的选择 (13)2 物料平衡和热平衡计算 (15)2.1原始数据 (15)2.1.1铁水成分及温度 (15)2.1.2原材料成分 (15)2.1.3冶炼钢种成分 (16)2.1.4平均比热 (16)2.1.5反应热效率(认为25℃与炼铁温度下两者数值近似) (16)2.1.6有关参数的选用 (17)2.2 物料平衡计算 (17)2.2.1炉渣量及炉渣成分的计算 (17)2.2.2 矿石及烟尘中的铁量和氧量的计算 (22)2.2.3 炉气成分及重量的计算见表2-14 (22)2.2.4 未加废钢时氧气的消耗量的计算见表2-15 (23)2.2.5 钢水量计算 (24)2.2.6 未加废钢时的物料平衡表见表2-16 (24)2.3 热平衡计算(取冷料为25℃) (25)2.3.1 热收入项 (25)2.3.2 热支出项 (25)2.3.3 热平衡表见表2-17 (27)2.4 加入废钢后的物料平衡计算 (28)2.4.1 加入废钢的物料平衡计算 (28)3 车间主体设备的设计 (30)3.1 转炉炉型的设计 (30)3.1.1 原始数据 (30)3.1.2 炉容比 (30)3.1.3 熔池尺寸的计算 (30)3.1.4 炉帽尺寸的确定 (32)3.1.5 炉身尺寸的确定 (32)3.1.6 出钢口尺寸确定 (32)3.1.7 炉衬厚度确定 (33)3.1.8 炉壳厚度确定 (33)3.1.9 验算高宽比 (33)3.1.10 转炉主要参数 (33)3.2 喷头及氧枪的设计计算 (34)3.2.1 喷头参数的选择 (34)3.2.2 氧枪枪身设计 (35)3.3 氧枪的升降机构与更换装置 (38)3.3.1 氧枪的升降机构 (39)3.3.2 升降卷扬机变速方式 (39)3.3.3 升降小车和固定导轨 (40)3.3.4 安全装置 (40)3.3.5 氧枪更换装置 (40)3.4 连铸机的主要设计参数 (40)3.4.1 钢包允许浇铸时间 (40)3.4.2 铸坯断面的选择 (41)3.4.3 理论拉速与工作拉速的确定 (41)3.4.4 冶金长度的计算 (42)3.4.5 连铸机圆弧(外弧)半径的计算R (43)3.4.6 连铸机的流数的计算 (44)3.4.7 连铸机生产能力的计算 (45)3.5 盛钢桶的计算 (47)3.5.1盛钢桶容积计算 (47)3.5.2 钢包需要量计算 (49)3.5.3 钢包质量计算 (50)3.6 RH精炼 (51)3.6.1 处理容量 (51)3.6.2 处理时间 (51)3.6.3 循环因数 (52)3.6.4 循环流量 (52)3.6.5 真空度 (53)3.6.6 真空泵的抽气能力 (53)3.7 钢包回转台 (54)3.7.1 直臂式钢包回转台 (54)3.7.1 双臂式钢包回转台 (55)3.8 中间包的主要设计参数 (55)3.8.1 中间包的作用 (55)3.8.2 中间包的形状与构造 (56)3.8.3 中间包小车 (59)3.9 结晶器的主要设计参数 (59)3.9.1 结晶器结构型 (59)3.9.2 结晶器结构参数的确定 (59)3.9.3 结晶器的振动与振动装置 (60)3.10 二次冷却系统的设计 (61)3.10.1 二次冷却装置 (61)3.10.2 喷水冷却系统。
年产350万吨炼钢生铁车间毕业设计

喷吹燃料系统 ●喷吹工艺:直接喷吹工艺 喷吹工艺: 喷吹工艺 喷吹设备: ●喷吹设备:由混合器或经 过分配器输送煤粉, 过分配器输送煤粉,通过喷枪送 到高炉直吹管吹入炉内
10
炉顶设备 ●并罐式无料钟炉顶 ●旋转溜槽布料
11
车间平面布置 • 半岛式布置 • 高炉和热风炉列线与车间调度线交角增 大到45° 大到 °; • 设有摆动流嘴,出一次铁可放置多个铁 设有摆动流嘴, 水罐车; 水罐车 • 在高炉两侧各有三条独立的有尽头的铁 水罐车停放线和一条辅助材料运输线。 水罐车停放线和一条辅助材料运输线。 出铁场与铁水罐车停放线垂直. 出铁场与铁水罐车停放线垂直
3
高炉炉型
★炉缸直径:d=10.8m ★死铁层厚度:1.5m ★ 炉腹角:810 ★炉喉直径 :8.1m ★炉身角:840 ★炉腰高度:2.8m ★炉缸高度 :h1=3.5m ★炉腰直径 :11.8m; ★炉腹高度:3.5m ★炉喉高度:2.0m ★炉身高度 :29.8m
4
高炉炉衬
• • • • • • 炉底: 炉底:采用全炭砖炉底 炉缸:采用炭砖炉缸, 炉缸:采用炭砖炉缸,以薄缝连接 炉腹:一层高铝砖, 炉腹:一层高铝砖,厚345mm 炉喉: 炉喉:炉喉钢砖 炉身: 炉身:冷却模块 炉腰:过度式, 炉腰:过度式,230+345高铝砖 高铝砖
8
送风系统、渣铁系统、 送风系统、渣铁系统、除尘系统 送风系统: ●送风系统: • 高炉鼓风机用离心式二座高炉装三座,一台备 高炉鼓风机用离心式二座高炉装三座 离心式二座高炉装三座, 用; • 每座高炉配备 座改进型内燃式热风炉。 每座高炉配备3座改进型内燃式热风炉 座改进型内燃式热风炉。 ●渣铁系统: 渣铁系统: 渣铁系统 • 采用轮法粒化渣处理工艺; 采用轮法粒化渣处理工艺; • 铁水处理采用铁水罐车和铸铁机。 铁水处理采用铁水罐车和铸铁机。 采用 ●除尘系统 : 除尘系统 • 高炉煤气为传统的湿法除尘; 高炉煤气为传统的湿法除尘; • 出铁均采用布袋
年产万吨生铁的高炉炼铁车间工艺设计

年产万吨生铁的高炉炼铁车间工艺设计1. 引言高炉炼铁车间是钢铁企业中重要的生产部门之一,承担着将铁矿石通过高温还原产生生铁的任务。
本文旨在设计一套年产万吨生铁的高炉炼铁车间工艺,以确保高效、稳定地生产高质量的生铁。
2. 工艺流程为了实现年产万吨生铁的目标,我们采用以下工艺流程:2.1 矿石预处理矿石预处理是高炉炼铁的第一步,目的是将原始矿石进行破碎、筛分、洗选等工序,以去除杂质并获得合适的粒度分布。
矿石预处理的具体工艺流程包括: 1.矿石破碎:通过破碎设备将原始矿石破碎至适合进一步处理的大小; 2. 筛分:经过筛分设备将破碎后的矿石按照粒度分布分级,分别进入不同的处理线路; 3. 洗选:利用洗选设备去除矿石中的杂质和尾矿,获得洗选后的矿石。
2.2 炼铁炉料配料炼铁炉料配料是将预处理好的矿石与其他辅助炼铁原料按照一定的配比混合,以形成合适的炉料,满足高炉内燃烧和还原的需求。
炼铁炉料配料的工艺流程包括:1. 矿石称量:将预处理后的矿石按照设定的配比进行称量,并放入配料设备中; 2. 辅料添加:将其他辅助炼铁原料如焦炭、石灰石等按照一定比例添加到配料设备中;3. 搅拌混合:通过搅拌设备对矿石和辅料进行混合,确保配料均匀。
2.3 高炉炉缸操作高炉炉缸操作是指将配料装入高炉内,并控制高炉内的温度、气氛和流动状态,使炉料逐渐进行还原反应并生成生铁。
高炉炉缸操作的工艺流程包括: 1. 入炉:将配料从炼铁炉料配料设备中装入高炉的料斗中,并通过配料装置均匀地投放到炉缸中; 2. 点火:在炉缸底部点火,通过引入适量的空气使焦炭燃烧,形成高温的还原气体; 3. 加料:在还原气氛下,定期加入炉料和燃料以保持高炉的运行; 4.排渣:定期排出炉缸内产生的废渣和不可燃物,以保持炉缸的畅通。
2.4 生铁产出在高炉炼铁的过程中,生铁通过熔化和融合的过程逐渐生成,并且由底部口出高炉。
生铁的质量受到炉料配比、温度和操作的影响,需要进行质量监控和调整。
高炉车间系统设计毕业论文
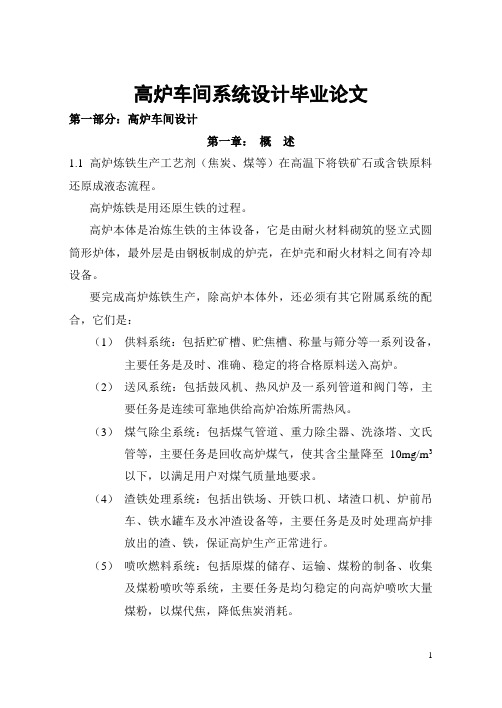
高炉车间系统设计毕业论文第一部分:高炉车间设计第一章:概述1.1 高炉炼铁生产工艺剂(焦炭、煤等)在高温下将铁矿石或含铁原料还原成液态流程。
高炉炼铁是用还原生铁的过程。
高炉本体是冶炼生铁的主体设备,它是由耐火材料砌筑的竖立式圆筒形炉体,最外层是由钢板制成的炉壳,在炉壳和耐火材料之间有冷却设备。
要完成高炉炼铁生产,除高炉本体外,还必须有其它附属系统的配合,它们是:(1)供料系统:包括贮矿槽、贮焦槽、称量与筛分等一系列设备,主要任务是及时、准确、稳定的将合格原料送入高炉。
(2)送风系统:包括鼓风机、热风炉及一系列管道和阀门等,主要任务是连续可靠地供给高炉冶炼所需热风。
(3)煤气除尘系统:包括煤气管道、重力除尘器、洗涤塔、文氏管等,主要任务是回收高炉煤气,使其含尘量降至10mg/m3以下,以满足用户对煤气质量地要求。
(4)渣铁处理系统:包括出铁场、开铁口机、堵渣口机、炉前吊车、铁水罐车及水冲渣设备等,主要任务是及时处理高炉排放出的渣、铁,保证高炉生产正常进行。
(5)喷吹燃料系统:包括原煤的储存、运输、煤粉的制备、收集及煤粉喷吹等系统,主要任务是均匀稳定的向高炉喷吹大量煤粉,以煤代焦,降低焦炭消耗。
1.2主要技术经济指标(1)高炉有效容积利用系数(ηv):高炉有效容积利用系数是指每昼夜生铁的产量P与高炉有效容积V有之比,即每昼夜,每1m³高炉有效容积的生铁产量。
ηv是高炉冶炼的一个重要指标,ηv俞大,高炉生产率俞大。
目前,一般大型高炉超过2.0 t / m3·d,一些先进高炉可达2.2~2.3 t / m3·d 。
小型高炉的ηv更高,100~300 m3高炉的利用系数为2.8~3.2t / m3·d。
本设计ηv =2.15 t / m3 ·d 。
(2)焦比(K):焦比即每昼夜焦碳消耗量Q K与每昼夜生铁产量P之比,即冶炼每吨生铁消耗的焦碳量。
K=Q K/P焦炭消耗量约占生铁成本的30%~40%,欲降低生铁成本必须降低焦比。
高炉炼铁技术论文(2)
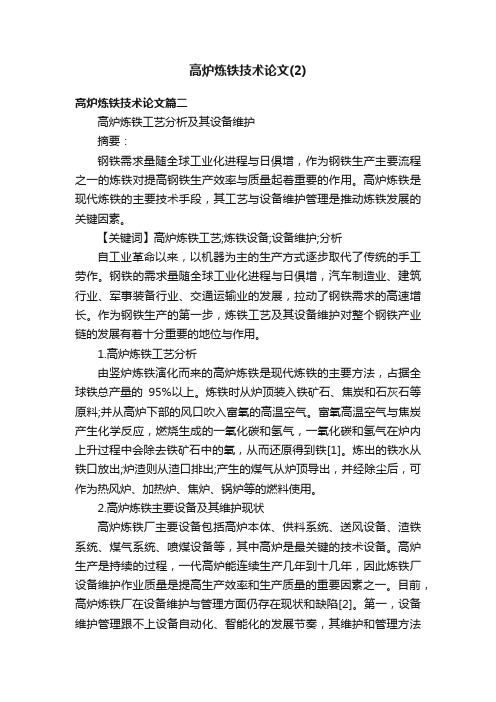
高炉炼铁技术论文(2)高炉炼铁技术论文篇二高炉炼铁工艺分析及其设备维护摘要:钢铁需求量随全球工业化进程与日俱增,作为钢铁生产主要流程之一的炼铁对提高钢铁生产效率与质量起着重要的作用。
高炉炼铁是现代炼铁的主要技术手段,其工艺与设备维护管理是推动炼铁发展的关键因素。
【关键词】高炉炼铁工艺;炼铁设备;设备维护;分析自工业革命以来,以机器为主的生产方式逐步取代了传统的手工劳作。
钢铁的需求量随全球工业化进程与日俱增,汽车制造业、建筑行业、军事装备行业、交通运输业的发展,拉动了钢铁需求的高速增长。
作为钢铁生产的第一步,炼铁工艺及其设备维护对整个钢铁产业链的发展有着十分重要的地位与作用。
1.高炉炼铁工艺分析由竖炉炼铁演化而来的高炉炼铁是现代炼铁的主要方法,占据全球铁总产量的95%以上。
炼铁时从炉顶装入铁矿石、焦炭和石灰石等原料;并从高炉下部的风口吹入富氧的高温空气。
富氧高温空气与焦炭产生化学反应,燃烧生成的一氧化碳和氢气,一氧化碳和氢气在炉内上升过程中会除去铁矿石中的氧,从而还原得到铁[1]。
炼出的铁水从铁口放出;炉渣则从渣口排出;产生的煤气从炉顶导出,并经除尘后,可作为热风炉、加热炉、焦炉、锅炉等的燃料使用。
2.高炉炼铁主要设备及其维护现状高炉炼铁厂主要设备包括高炉本体、供料系统、送风设备、渣铁系统、煤气系统、喷煤设备等,其中高炉是最关键的技术设备。
高炉生产是持续的过程,一代高炉能连续生产几年到十几年,因此炼铁厂设备维护作业质量是提高生产效率和生产质量的重要因素之一。
目前,高炉炼铁厂在设备维护与管理方面仍存在现状和缺陷[2]。
第一,设备维护管理跟不上设备自动化、智能化的发展节奏,其维护和管理方法滞后于设备的更新。
第二,炼铁厂在追求单位时间产量的同时忽略了设备的正常维护,致使设备超长时间、超负荷工作。
第三,工厂没有注重设备的前期管理。
设备出故障的原因往往来自设备的设计和制造。
选用先进、合理的设备,才能真正发挥其应有的作用,降低故障突发率。
- 1、下载文档前请自行甄别文档内容的完整性,平台不提供额外的编辑、内容补充、找答案等附加服务。
- 2、"仅部分预览"的文档,不可在线预览部分如存在完整性等问题,可反馈申请退款(可完整预览的文档不适用该条件!)。
- 3、如文档侵犯您的权益,请联系客服反馈,我们会尽快为您处理(人工客服工作时间:9:00-18:30)。
年产530万吨生铁的高炉炼铁车间工艺设计毕业论文目录前言 (1)1 高炉配料计算 (2)1.1原始资料 (2)1.1.1 矿石的选配 (4)1.2原始资料的整理 (4)1.3冶炼条件的确定 (4)1.4物料平衡 (11)1.4.1 根据碳平衡计算风量 (11)1.4.2 煤气的成分和数量计算 (13)1.4.3物料平衡表的编制 (15)1.5热平衡 (16)1.5.1 计算热量收入项 (16)1.5.2 计算热量支出项 (18)1.5.3 列出热量平衡表 (21)1.5.4 高炉热工指标的分析 (22)2 高炉本体设计 (23)2.1高炉内型相关计算 (23)2.2高炉内衬设计 (26)2.2.1炉底 (26)2.2.2炉缸 (27)2.2.3炉腹 (27)2.2.4炉腰 (28)2.2.5炉身 (28)2.3高炉炉壳和高炉基础 (32)2.4炉体设备 (35)2.4.1 炉体冷却设备 (35)2.4.3 铁口套 (36)2.4.4炉喉钢砖 (36)2.4.5 炉顶保护板 (36)3 料运系统计算及装料布料设备 (37)3.1贮矿槽 (37)3.1.1 平面布置 (37)3.1.2 槽上运输方式 (37)3.1.3 储矿槽工艺参数 (37)3.1.4 槽下供料 (37)3.2料坑设备 (38)3.3碎焦运送设施 (39)3.4上料设备 (39)4 高炉鼓风机的选择 (40)4.1高炉鼓风量及鼓风压力的确定 (40)4.1.1 高炉入炉风量 (40)4.1.2 鼓风机出口风量 (40)4.1.3 高炉鼓风压力 (41)4.2高炉鼓风机能力的确定 (41)4.2.1 大气状况对高炉鼓风的影响 (41)4.2.2 鼓风机工况的计算 (42)4.3高炉鼓风机的工艺过程 (43)5 热风炉 (44)5.1计算的原始数据 (44)5.2燃烧计算 (45)5.2.1 煤气成分换算 (45)5.2.2 煤气发热值计算 (45)5.2.3 燃烧1标米3煤气的空气需要量 (46)5.2.4燃烧1标米3煤气生成的烟气量百分组成 (46)5.2.5理论燃烧温度和实际燃烧温度计算 (47)5.3热平衡计算 (50)5.3.1 计算鼓风从80℃提高到1200℃所增加的热含量 (50)5.3.3 煤气消耗量及烟气量 (51)5.4蓄热室热工计算 (51)5.4.1 热工计算的原始条件 (54)5.4.2 蓄热室各部位的烟气及鼓风温度 (55)5.4.3 蓄热室面积及各段砖格子高度的计算 (56)5.4.4 蓄热室面积及蓄热室各段高度的调整 (57)5.5热风炉的蓄热面积指标 (58)6 风口平台及渣铁处理系统 (60)6.1风口平台和出铁场布置 (60)6.1.1 铁口及出铁场数目的确定 (60)6.1.2 渣、铁沟及其流嘴布置 (61)6.2风口平台和出铁场设备 (61)6.2.1 泥炮 (61)6.2.2 开铁口机 (62)6.2.3堵渣口机 (62)6.2.4炉前吊车 (63)6.2.5铁水罐车 (63)6.2.6渣罐车 (64)6.3风口平台和出铁场结构 (65)6.3.1风口平台 (65)6.3.2 出铁场 (65)6.4铁水处理 (65)6.5渣的处理 (65)7 高炉煤气处理系统 (67)7.1工艺流程 (67)7.2煤气除尘设备 (67)7.2.1 粗除尘设备——重力除尘器 (67)7.2.2 精细除尘设备——布袋除尘器 (68)7.2.3 脱水器 (68)7.3煤气除尘系统附属设备 (69)7.3.1 粗煤气管道 (69)7.3.2 调节阀组 (69)7.3.3 煤气遮断阀 (69)7.3.4 煤气放散阀 (69)8 高炉喷吹煤粉系统 (71)8.1喷煤系统 (71)8.2喷吹工艺 (71)8.3主要设备 (72)8.3.1 混合器 (72)8.3.2 分配器 (72)8.3.3 喷煤枪 (72)8.3.4 喷氧枪 (72)9 部分车间布置与总图运输 (73)9.1车间平面布置 (73)9.2厂区的选择 (73)9.3总图运输 (73)10 参考文献 (74)致谢 (75)专题浅析高炉煤气的综合利用 (76)前言毕业设计是大学学习过程中的最后一个环节,对每个大学生的学习能力和以后的工作实践能力都会有很大的帮助与提高。
毕业设计是为了更好地将理论和实践结合起来,达到学以致用的目的。
本设计说明书是作者赴陕西省汉中钢铁集团有限公司实习后,经杨双平老师悉心指导的年产530万吨生铁的高炉的工艺设计说明书。
本设计参照了近年来国内外炼铁工艺方面的资料。
本设计说明书着重以工艺角度论述生铁冶炼工艺所涉及的基本流程和主要设备的基本结构,工作原理设计原则及设计方法。
本设计说明书的设计原则是,拟建两座高炉其中每座高炉有效容积2518m3,尽可能采用通用的工艺和技术,关键工艺装备水平达到国家同类型高炉水平,本设计说明书主要包括高炉配料计算、高炉本体设计、料运系统方案设计、高炉炉顶、高炉鼓风机、内燃式热风炉、渣铁处理系统及煤气处理系统设计等几大部分,同时对炼铁的其他工艺流程式进行了设计说明。
其中高炉配料计算,先从原料入手,对各种原料的化学分析结果进行成分处理。
接着进行高炉配料计算,包括产品方案的确定,对物料平衡的计算,生铁炉渣性能指标的计算及校核等。
高炉部分包括高炉的选型及高炉内型的计算,配砖的计算,冷却设备及本体结构设计等,热风炉部分包括热工计算,结构设计。
这两部分作为炼铁设计的主体部分。
其它工艺流程包括出铁场的设计,渣铁处理系统,高炉鼓风机,煤气处理系统的工艺设计及主要设备的选型。
车间平面布置及总图运输方案,以联合企业为背景,尽量使车间布置趋向合理。
本设计说明书附有高炉砖量图,热风炉剖面图,车间平面布置图各一张。
由于编者缺乏实作和经验,如有疏忽和错误,还望见谅和批评指正!1 高炉配料计算1.1 原始资料配料计算所需的铁矿石、炉尘、及喷吹物的整理成分见表1-1、表1-2、表1-3、表1-4、表1-5。
表1-1 球团矿和烧结矿的化学成分(%)类型TFe FeO SiO2CaO MgO Al2O3S P MnO 烧结矿58.85 7.62 5.10 9.70 3.40 2.85 0.035 0.061 1.2 球团矿61.22 0.75 8.12 1.2 0.91 1.48 0.028 0.035 1.3表1-2 块矿的化学成份(%)TFe FeO SiO2CaO MgO Al2O3S P MnO61.5 1.04 6.62 0.55 0.48 1.47 0.06 0.049 0.09表1-3 焦炭工业分析表(%)固定炭灰份挥发份硫合计游离水87.46 9.94 1.17 0.87 100 3.2表1-4 燃料灰份分析表(%)MgO SiO2Al2O3P2O5CaO Fe2O3SO3FeO 合计焦炭0.95 49.99 34.09 0.37 3.02 0.88 1.24 9.46 100煤粉 1.03 48.31 35.82 0.30 3.68 2.98 0.93 6.95 100表1-5 焦炭挥发份成分(%)CO 2 CO H 2 CH 4 N 2 合计 34.237.86418100表1-6 煤粉成分(%)C Ad 灰分 S H 2O 合计 75.738.004.040.261.85100表1-7 生铁成分表(%)Si Mn P C Fe S 合计 0.320.940.1454.0194.550.035100表1-8 炉渣成分表(%)MgO SiO 2Al 2O 3BaO CaO FeO S/2 MnO 合计 8.1436.13 9.933.7238.910.900.931.34100表1-9 炉顶煤气成分表(%)CO 2 CO H 2 CH 4 N 2 合计 17.125.31.30.655.7100表1-10 炉尘分析表(%)T F ePSFe 2O 3 FeO CaO SiO 2 Al 2O 3 MnO MgO BaO固C 烧损合计重力尘 41.42 0.04 0.40 51.45 7.01 8.30 8.61 2.61 1.12 1.97 0.84 17.64 15.78 100文氏尘44.67 0.04 0.40 56.62 7.03 8.24 8.63 2.11 1.03 2.03 0.90 12.97 14.6 1001.1.1 矿石的选配高炉使用多种矿石冶炼时,应根据矿石的供应量及炉渣成分和渣量的要求选择适当的比例,本设计选用60%的烧结矿和35%的球团矿,5%的块矿。
为计算方便,求出混合矿的成分,计算时看作单一矿石。
在选配矿石时,应注意检查矿石含磷量不得超过生铁含磷量。
冶炼铸铁时还应检查矿石含锰量是否满足生铁的要求,否则应加锰矿。
注:烧结矿:球团矿:生矿=60:35:51.2 原始资料的整理配料计算所需的铁矿石、熔剂、炉尘及喷吹物等的整理成分如下表1-11,表1-12,表1-13,表1-14。
表1-11 原料整理后的成分TFe P S FeO Fe2O3SiO2CaO 烧结矿55.68 0.058 0.033 7.21 71.60 4.82 9.18球团矿61.22 0.035 0.028 0.75 86.46 8.12 0.89块矿61.5 0.049 0.06 1.04 86.77 6.92 0.95混合矿57.91 0.049 0.033 4.46 77.56 6.08 5.87MgO Al2O3P2O5S/2 烧损合计3.22 2.696 0.132 0.0166 0 100.001.16 1.73 0.08 0.014 0 100.000.73 1.72 0.112 0.03 1.628 100.002.37 2.31 0.113 0.017 0.081 100.001.3 冶炼条件的确定根据冶炼铁种和原燃料成分,除确定矿石的配比外,尚需要定炉渣碱度、焦比、喷物数量、尘、铁成分与各种元素在渣铁中的分配比。
(1)各种元素在炉渣、煤气、和生铁中的分配比如下表1-12。
表1-12 各种元素在炉渣、煤气、和生铁中的分配比产品Fe Mn P S生铁0.997 0.70 1.00 0.02炉渣0.003 0.30 0 0.98煤气0 0 0 0.05 (2)预定生铁成分,见表1-13:表1-13 预定生铁成分Si P C Fe S Mn 合计0.32 0.145 4.01 94.55 0.035 0.94 100(3)燃料使用量的假定:①湿焦比为480kg/吨铁;②焦炭与喷吹燃料中总碳量的1.2%与H2生成CH4;③煤粉喷吹量为150 kg /吨铁;④碎铁使用量为20 kg /吨铁;⑤选择的炉渣碱度CaO/SiO2=1.0;⑥冶炼强度i= 2.0吨焦/立方米·昼夜;⑦热风温度t=1200℃,鼓风湿度φ=1%;⑧炉尘吹出量为15 kg /吨铁;⑨直接还原度γd=0.45;炉顶煤气温度tr=200℃(4) 根据铁平衡求铁矿石的量①焦炭带入的铁量:Fe2O3~2Fe FeO~Fe159.70 111.70 71.55 55.850.0088 X1 0.0946X2故X1=0.00616 X2=0.0738所以焦炭带入的铁量:m(Fe)j=480×(1-0.032)×0.0994×(0.00616+0.0738)=3.68(㎏)②矿石的需求量:其中煤粉带入的铁量(1t生铁)m(Fe)meFe2O3~2Fe FeO~Fe159.70 111.70 71.55 55.850.0298 X1 0.0695X2故X1=0.021 X2=0.054所以煤粉带入的铁量m (Fe )m e=150×0.0404×(0.021+0.054)=0.455(㎏)t Fe (生铁)=1000×94.55%=945.5㎏ za Fe (炉渣)=945.5×0.003/0.997=2.845㎏chFe (炉尘)=15×0.4142=6.213㎏Fe m (碎铁)=20×0.85=17㎏ 故 k Q t z a c h j m ekF e F e F e F e F e Fe ++--==(945.5+2.845+6.213-17-0.45-3.68)/0.57911=612㎏式中:k Q ——矿石的需要量,kg/t(铁);t Fe ——进入生铁的铁量,kg/t(铁);zaFe ——进入炉渣的铁量 ,kg/t(铁);ch Fe ——进入炉尘的铁量 ,kg/t(铁);jFe ——焦炭带入的铁量 ,kg/t(铁); me Fe ——煤粉带入的铁量 ,g/t(铁);kFe ——矿石的含铁量 ,kg/t(铁)。