年产200万吨炼铁高炉车间设计
设计年生产炼钢生铁200万吨的高炉车间

设计年生产炼钢生铁200万吨的高炉车间设计年产炼钢生铁200万吨的高炉车间河北理工大学成人教育毕业设计(论文)任务书: :3河北理工大学成人教育毕业设计(论文)进程表指导教师签字:4毕业设计评定书-指导教师对设计的评语:成绩:指导教师:200 年月日5毕业设计评定书-评议人对设计的评语及评定的成绩:成绩:评议人:200 年月日6毕业设计评定书-目录摘要 (1)引言 (2)1绪论 (4)1.1概述 (4)1.2高炉生产主要经济技术指标 (4)1.3高炉冶炼现状及发展 (6)1.4本设计采用的新技术 (7)1.5高炉辅助设计和生产流程图 (7)2高炉本体设计 (8)2.1.总述 (8)2.2确定年工作日:347天 (9)2.3定容积: (9)2.4炉缸尺寸 (9)2.5死铁层厚度 (10)2.6炉腰直径炉腹角炉腹高度 (10)2.7炉喉直径炉喉高度 (10)2.8炉身角炉身高度炉腰高度 (11)2.9校核炉容 (11)3 厂址选择 (12)3.1考虑因素 (12)3.2 要求 (13)4 供料系统 (14)4.1焦矿槽容积的确定 (15)4.1.1贮矿槽和附矿槽的布置、容积及数目的确定 (15) 4.1.2 焦矿槽的布置、容积及数目的确定 (16)4.2槽上、槽下设备及参数的确定 (16)4.2.1槽上设备 (16)4.2.2槽下设备及参数选择 (16)4.3皮带上料机能力的确定 (17)—物料堆比重,1.6 3/m t....................... 错误!未定义书签。
4.4 高炉槽下上料系统的设计与改进 (18)5 送风系统 (20)5.1.1 高炉入炉风量 (20)5.1.2 鼓风机风量 (21)5.1.3高炉鼓风压力 (21)5.1.4 鼓风机的选择 (21)5.2.1 热风炉座数的确定 (22) 5.2.2 热风炉工艺布置 (22)5.2.3 热风炉型式的确定 (22) 5.2.4 热风炉主要尺寸的计算 (22) 5.2.5 热风炉设备 (25)5.2.6 热风炉管道及阀门 (25)6 渣铁处理系统 (28)6.1风口平台及出铁场 (29)6.2炉渣处理设备 (29)6.3铁水处理设备 (32)6.3.1 铁水罐车 (32)6.3.2 铸铁机 (33)6.3.3 铁水炉外脱硫设备 (33) 6.4铁沟流咀布置 (33)6.4.1 渣铁沟的设计 (33)6.4.2 流咀的设计 (34)6.5炉前设备的选择 (34)6.5.1 开铁口机 (34)6.5.2 堵铁口泥炮 (34)6.5.3 堵渣机 (35)6.5.4 换风口机 (35)。
毕业论文:高炉炼铁系统设计-精品【范本模板】
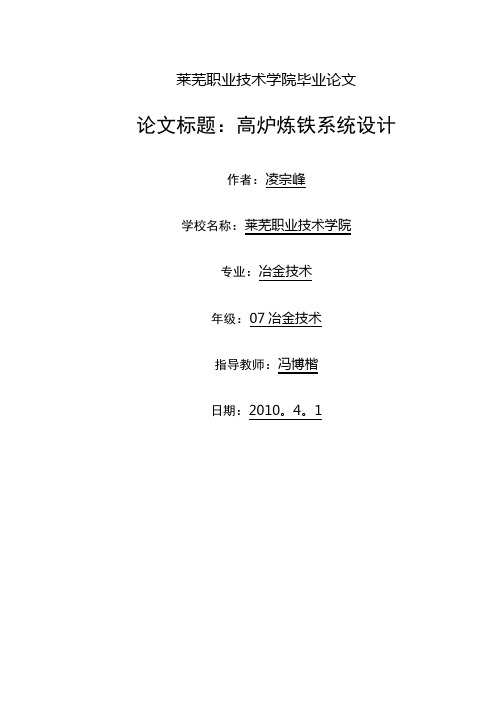
莱芜职业技术学院毕业论文论文标题:高炉炼铁系统设计作者:凌宗峰学校名称:莱芜职业技术学院专业:冶金技术年级:07冶金技术指导教师:冯博楷日期:2010。
4。
1目录内容提要与关键词¨¨¨¨¨¨¨¨¨¨¨3手抄在论文本上,最后再根据内容补填目录,要求手写!正文¨¨¨¨¨¨¨¨¨¨¨¨¨¨¨¨¨4参考文献¨¨¨¨¨¨¨¨¨¨¨¨¨¨¨¨58摘要本设计要求建年产量为200万吨生铁的高炉系统。
高炉车间的七大系统:即高炉本体系统、上料系统、渣铁处理系统、喷吹系统、送风系统、除尘系统和冷却系统都做了较为详细的叙述。
高炉炼铁是获得生铁的主要手段,是钢铁冶金过程中最重要的环节之一,在国民经济建设中起着举足轻重的作用。
高炉是炼铁的主要设备,本着优质、高产、低耗和对环境污染小的方针,在预设计建造一座年产生铁200万吨的高炉炼铁系统,本设计说明书详细的对其进行了高炉设计,其中包括绪论、工艺计算(包括配料计算、物料平衡和热平衡)、高炉炉型设计、高炉各部位炉衬的选择、炉体冷却设备的选择、风口及出铁场的设计、原料系统、送风系统、煤气处理系统、渣铁处理系统、高炉喷吹系统等。
设计的同时还结合国内外相同炉容高炉的一些先进的生产操作经验和相关的数据,力争使该设计的高炉做到高度机械化、自动化和大型化,以期达到最佳的生产效益. 关键词:高炉;炼铁;设计;煤气处理;渣鉄处理;1绪论1。
1概述钢铁是重要的金属材料之一,被广泛应用于各个领域,钢铁生产水平是一个国家发展程度的标志。
年产200万吨炼钢生铁的高炉炼铁车间

毕业设计(论文)任务书冶金与能源工程学院冶金工程专业 2008 级学生:宝富毕业设计(论文)题目:根据昆钢原、燃料条件,设计一座年产炼钢生铁200万吨的高炉炼铁车间毕业设计(论文)容:1.主要技术经济指标选择与论证;2.炼铁全计算(配料计算;物料平衡与热平衡计算);3.炉座规划、炉型计算;4.炉体结构设计与主要附属设备选型;5.绘制车间平面布置图、车间纵剖面图各一;6.编制设计说明书一份。
专题(子课题)题目:专题(子课题)容:毕业设计(论文)指导教师(签字):主管教学院(部)长(签字):年月日年产200万吨炼钢生铁的高炉炼铁车间设计说明书编制人: 宝富学号: 0专业: 冶金工程年级: 2008级学院: 冶金与能源工程学院指导教师: 丁跃华指导教师职称: 教授指导教师单位: 冶金与能源工程学院提交日期:2012年6月1日Design Specificationon a Blast Furnace Iron-making Plantwith Annual Capacity of 2.0 Million Tons of Hot MetalDesigner:School Number:Specialty:Grade:Faculty: YangBaoFu 0Metallurgical Engineering2008Metallurgical Engineering and energy, KUSTSupervisor:Title:Set-up: Ding YuehuaProfessorEngineering,KUST Faculty of Metallurgical and energySubmission Date: Jun. 1, 2012目录摘要VIABSTRACTVII前言IX第一章高炉炼铁设计11.1高炉炼铁设计概述11.1.1 高炉炼铁的发展现状11.1.2 高炉炼铁生产工艺流程31.1.3 高炉与其附属设备41.2高炉炼铁设计的基本原则51.2.1 高炉炼铁设计应遵循的基本原则51.2.2 钢铁厂的组成61.3设计任务61.4高炉生产主要技术经济指标71.5设计所采用的先进技术101.6高炉炼铁厂的厂址选择12第二章高炉炼铁综合计算132.1原始资料142.2配料计算162.2.1 铁矿石用量的计算162.2.2渣量与炉渣成分的计算192.3物料平衡计算222.3.1 鼓风量的计算22G的计算262.3.2鼓风质量b2.3.3 煤气量的计算272.3.4煤气中水蒸气量的计算322.3.5考虑炉料的机械损失后的实际入炉量322.3.6编制物料平衡表332.4高炉热平衡计算342.4.1热量收入的计算342.4.2热量支出的计算37第三章高炉炼铁车间设计453.1高炉座数与容积确定453.1.1 生铁产量的确定453.1.2 高炉炼铁车间总容积的确定453.1.3 高炉座数的确定463.2高炉炼铁车间平面布置463.2.1 高炉炼铁车间平面布置应遵循的原则463.2.2 高炉炼铁车间平面布置形式473.3高炉车间劳动定员47第四章高炉本体设计494.1高炉炉型494.1.1 五段式高炉炉型494.1.2 炉型设计与计算554.2高炉炉衬594.2.1 炉衬破损机理594.2.2 高炉用耐火材料的选择634.2.3 高炉炉衬的设计与砌筑65 4.3高炉冷却设备714.3.1 冷却设备的作用714.3.2 冷却介质714.3.3 高炉冷却结构形式724.3.4 高炉给排水系统774.3.5 高炉冷却系统784.4高炉送风管路794.4.1热风围管804.4.2 送风支管804.4.3 直吹管814.4.4 风口装置824.5高炉钢结构844.5.1 高炉本体钢结构854.5.2 炉壳864.5.3 炉体框架874.6高炉基础874.6.1 高炉基础的负荷874.6.2 对高炉基础的要求88第五章附属设备系统895.1供料系统895.1.1 贮矿槽、贮焦槽与槽下运输称量895.1.2 皮带运输925.2装料设备935.2.1 并罐式无钟炉顶装料设备935.2.2 探料装置965.3送风系统975.3.1 高炉鼓风机975.3.2 热风炉1005.3.3 提高风温的途径1035.4煤粉喷吹系统1045.4.1 煤粉制备工艺1055.4.2 喷吹工艺1075.5煤气处理系统1085.5.1 重力除尘器1095.5.2 溢流文氏管1115.5.3 脱水器1115.6渣铁处理系统1125.6.1 风口平台与出铁场设计1125.6.2 炉前主要设备1145.6.3 铁水处理设备1165.6.4 炉渣处理设备116第六章能源回收利用和环境保护118 6.1高炉炉顶余压发电1186.2热风炉烟道废气余热回收119 6.3环境保护120第七章成本核算1217.1营业收入1217.2成本费用估算122结论124总结与体会125辞126参考文献126附录一(英文原文)127附录二(翻译)146摘要本论文是根据昆钢原、燃料条件,设计一座年产200万吨炼钢生铁的高炉炼铁车间。
毕业设计_年产200万吨钢的转炉炼钢车间设计——钢包设计

攀枝花学院本科毕业设计(论文)摘要攀枝花学院本科毕业设计(论文)年产200万吨钢的转炉炼钢车间设计——钢包设计攀枝花学院本科毕业设计(论文)摘要摘要根据年产200万吨钢转炉车间设计的要求和国家相关政策的规定,确定转炉的大小为220吨,进一步得到了符合实际生产的与之匹配的钢包容量大小为250吨,通过计算确定钢包上部内径和高度均为4289mm,生产过程中所需要的钢包的数量为11个。
对钢包用耐火材料进行了设计,分为2套钢包即浇注钢包和砌筑钢包。
分别对其进行分析确定了他们的绝热层和工作层的设计方法,对于浇注钢包采用整体浇注和或剥皮浇注,对砌筑钢包采用综合砌筑的方案;通过对钢包透气砖和滑动水口系统耐火材料的外形设计,确定了透气砖系统耐火材料的尺寸和滑动水口系统耐火材料的尺寸;最后根据钢包用耐火材料的使用要求,针对不同钢种和不同部位的不同要求以及耐火材料的理化性能指标,对钢包所用的耐火材料进行了优化选择。
关键词炼钢,钢包,砌筑,浇注,耐火材料攀枝花学院本科毕业设计(论文)ABSTRACTABSTRACTAccording to the annual output of 2 million tons of steel converter workshop design requirements and relevant national policies and regulations, determine the size of the converter is 220 tons, has been further conform to the actual production of matching the ladle size capacity of 250 tons, through the calculate and determine the ladle upper inner diameter and height is 4289 mm, the production process required the number of ladles for 11. Ladle refractory materials used for the design, divided into 2 sets of ladle pouring ladle and laying the ladle. Respectively to analyze it to determine their thermal barrier and layer, the design method of the work for adopts the integral casting and or peeling pouring ladle cover in casting, for the composite masonry methods in laying the ladle; Through the vent brick of ladle refractory and slide gate system design, determine the size of the system of gas supply brick and refractory materials and refractory materials the size of the slide gate system; Finally according to the requirements of the ladle refractory material used, according to different steel grade and the different requirements of different parts and the rational index of the refractory, the ladle refractory material used in the optimized choice.Key words steelmaking, ladle, laying, casting, refractory material攀枝花学院本科毕业设计(论文)目录目录摘要 (II)ABSTRACT (III)1 绪论 (1)2 转炉的座数、公称容量及生产能力的确定 (2)2.1 转炉的容量和座数的确定 (2)2.2 计算年出钢炉数 (2)2.3 车间的年产钢量的计算 (3)3 钢包尺寸及数量的确定 (4)3.1 钢包尺寸的计算 (4)3.2 钢包质量的计算 (7)3.3 钢包重心计算 (8)3.4钢包数量的计算 (9)4 钢包用耐火材料的设计 (10)4.1浇注钢包的设计方法 (10)4.1.1包壁绝热层的设计方法 (10)4.1.2钢包工作层的设计方法 (10)4.1.2.1普通不精炼钢包 (10)4.1.2.2简单炉后处理的精炼钢包 (12)4.1.3钢包浇注的工作方案 (12)4.1.3.1整体浇注钢包的方法 (12)4.1.3.2采用剥皮套浇的浇注钢包施工方法 (13)4.2砖砌钢包的设计 (14)4.2.1砖砌钢包的结构设计 (14)4.2.1.1绝热层的设计 (14)4.2.1.2永久层的设计 (14)4.2.1.3工作层的设计 (14)4.3钢包透气砖和滑动水口系统耐火材料的外形设计 (14)4.3.1透气砖系统耐火材料的尺寸设计 (14)4.3.2滑动水口系统耐火材料的尺寸设计 (16)5 钢包用耐火材料的选择 (19)攀枝花学院本科毕业设计(论文)目录5.1钢包用耐火材料的要求 (19)5.2钢包耐火材料的选用 (21)5.2.1钢包隔热层和永久层 (21)5.2.2钢包工作层 (21)5.2.3滑动水口用耐火材料 (22)结论 (23)参考文献 (24)致谢 (1)攀枝花学院本科毕业设计(论文) 1 绪论1 绪论钢包是连接转炉和连铸中间的容器,而且几乎所有钢水的炉外精炼过程都是在钢包中进行;钢包的工作状态好坏不仅影响炼钢过程钢液质量、生产节奏、炉衬寿命;也会影响后序精炼和连铸过程中的包衬寿命、钢水质量和生产节奏,特别是影响最终的钢铁产品的制造成本和内在质量。
年产200万吨钢的转炉炼钢车间设计——钢包设计设计0000

年产200万吨钢的转炉炼钢车间设计——钢包设计设计0000攀枝花学院本科毕业设计(论文)年产200万吨钢的转炉炼钢车间设计——钢包设计学生姓名:蒲维学生学号: 200911103045院(系):资源与环境工程学院年级专业: 2009级冶金工程1班指导教师:芶淑云教授二〇一三年五月攀枝花学院本科毕业设计(论文)摘要摘要根据年产200万吨钢转炉车间设计的要求和国家相关政策的规定,确定转炉的大小为220吨,进一步得到了符合实际生产的与之匹配的钢包容量大小为250吨,通过计算确定钢包上部内径和高度均为4289mm,生产过程中所需要的钢包的数量为11个。
对钢包用耐火材料进行了设计,分为2套钢包即浇注钢包和砌筑钢包。
分别对其进行分析确定了他们的绝热层和工作层的设计方法,对于浇注钢包采用整体浇注和或剥皮浇注,对砌筑钢包采用综合砌筑的方案;通过对钢包透气砖和滑动水口系统耐火材料的外形设计,确定了透气砖系统耐火材料的尺寸和滑动水口系统耐火材料的尺寸;最后根据钢包用耐火材料的使用要求,针对不同钢种和不同部位的不同要求以及耐火材料的理化性能指标,对钢包所用的耐火材料进行了优化选择。
关键词炼钢,钢包,砌筑,浇注,耐火材料ABSTRACTAccording to the annual output of 2 million tons of steel converter workshop design requirements and relevant national policies and regulations, determine the size of the converter is 220 tons, has been further conform to the actual production of matching the ladle size capacity of 250 tons, through the calculate and determine the ladle upper inner diameter and height is 4289 mm, the production process required the number of ladles for 11. Ladle refractory materials used for the design, divided into 2 sets of ladle pouring ladle and laying the ladle. Respectively to analyze it to determine their thermal barrier and layer, the design method of the work for adopts the integral casting and or peeling pouring ladle cover in casting, for the composite masonry methods in laying the ladle; Through the vent brick of ladle refractory and slide gate system design, determine the size of the system of gas supply brick and refractory materials and refractory materials the size of the slide gate system; Finally according to the requirements of the ladle refractory material used, according to different steel grade and the different requirements of different parts and the rational index of the refractory, the ladle refractory material used in the optimized choice.Key words steelmaking, ladle, laying, casting, refractory material目录摘要 (I)ABSTRACT (II)1 绪论 (1)2 转炉的座数、公称容量及生产能力的确定 (3)2.1 转炉的容量和座数的确定 (3)2.2 计算年出钢炉数 (3)2.3 车间的年产钢量的计算 (4)3 钢包尺寸及数量的确定 (5)3.1 钢包尺寸的计算 (5)3.2 钢包质量的计算 (8)3.3 钢包重心计算 (9)3.4钢包数量的计算 (11)4 钢包用耐火材料的设计 (12)4.1浇注钢包的设计方法 (12)4.1.1包壁绝热层的设计方法 (12)4.1.2钢包工作层的设计方法 (12)4.1.2.1普通不精炼钢包 (12)4.1.2.2简单炉后处理的精炼钢包144.1.3钢包浇注的工作方案 (16)4.1.3.1整体浇注钢包的方法 (16)4.1.3.2采用剥皮套浇的浇注钢包施工方法 (16)4.2砖砌钢包的设计 (17)4.2.1砖砌钢包的结构设计 (17)4.2.1.1绝热层的设计 (17)4.2.1.2永久层的设计 (17)4.2.1.3工作层的设计 (17)4.3钢包透气砖和滑动水口系统耐火材料的外形设计 (18)4.3.1透气砖系统耐火材料的尺寸设计184.3.2滑动水口系统耐火材料的尺寸设计 (19)5 钢包用耐火材料的选择 (23)5.1钢包用耐火材料的要求 (23)5.2钢包耐火材料的选用 (25)5.2.1钢包隔热层和永久层 (25)5.2.2钢包工作层 (25)5.2.3滑动水口用耐火材料 (26)结论 (28)参考文献 (29)致谢 (30)1 绪论钢包是连接转炉和连铸中间的容器,而且几乎所有钢水的炉外精炼过程都是在钢包中进行;钢包的工作状态好坏不仅影响炼钢过程钢液质量、生产节奏、炉衬寿命;也会影响后序精炼和连铸过程中的包衬寿命、钢水质量和生产节奏,特别是影响最终的钢铁产品的制造成本和内在质量。
高炉车间设计

高炉车间设计一、引言高炉车间是钢铁生产过程中的核心环节,其设计对于生产效率和产品质量具有重要影响。
本文将详细介绍高炉车间设计的标准格式,包括车间布局、设备选型、工艺流程等方面的内容。
二、车间布局设计1. 车间总体布局:高炉车间应根据生产工艺流程,合理划分不同功能区域,包括原料区、炉缸区、煤气处理区、炉渣处理区、产品收集区等。
同时,要考虑人员流动和设备安装的便利性,确保生产操作的高效性和安全性。
2. 原料输送系统:设计合理的原料输送系统,包括铁矿石、焦炭、石灰石等原料的储存、输送和配料设备。
确保原料供应的稳定性和准确性。
3. 炉缸区设备布置:根据高炉炉缸的结构和尺寸,合理布置炉缸区的设备,包括风口、喷吹装置、温度探针等。
同时要考虑操作人员的工作空间和安全防护设施。
4. 煤气处理系统:设计完善的煤气处理系统,包括煤气净化、除尘、脱硫等设备。
确保煤气的质量达到生产要求,并减少对环境的污染。
5. 炉渣处理系统:设计高效的炉渣处理系统,包括炉渣收集、输送、处理等设备。
确保炉渣的处理安全、高效,并减少对环境的影响。
6. 产品收集系统:设计合理的产品收集系统,包括铁水和炉渣的收集、输送和贮存设备。
确保产品的质量和安全。
三、设备选型1. 高炉炉缸设备:根据高炉的规模和生产要求,选择适当的高炉炉缸设备,包括炉缸本体、风口、喷吹装置等。
确保设备的稳定性和耐久性。
2. 原料输送设备:选择可靠的原料输送设备,包括皮带输送机、斗式提升机等。
确保原料的准确输送和储存。
3. 煤气处理设备:选择高效的煤气处理设备,包括除尘器、脱硫设备等。
确保煤气的净化效果和环境的保护。
4. 炉渣处理设备:选择适当的炉渣处理设备,包括炉渣车、炉渣铲等。
确保炉渣的安全处理和回收利用。
5. 产品收集设备:选择可靠的产品收集设备,包括铁水罐、炉渣罐等。
确保产品的安全收集和贮存。
四、工艺流程设计1. 原料预处理:对铁矿石、焦炭等原料进行预处理,包括破碎、筛分等工艺。
年产200万吨炼铁高炉车间设计
年产200万吨炼铁高炉车间设计摘要人类获得生铁重要手段是通过高炉炼铁,高炉炼铁是钢铁冶金中的根底环节,同时也是最重要的环节。
本设计任务是设计一个年生产能力达200万吨炼铁高炉车间。
本次设计的高炉 1100m³。
高炉炉型为五段式,高炉炉衬设计依据各个局部的工作条件的不同以及炉衬破损的机理,选择相应的耐火材料。
热风炉采用的传统改良型内燃式热风炉,燃烧室为复合型断面,热风炉数量为3座,关于热风炉的设计局部还包括热风炉的各种设备以及相应的技术参数。
上料系统采用的是可不间断上料,原料破损率低的皮带运输上料,炉顶装料设备是并罐式无钟炉顶。
煤气处理系统的功能是降低高炉煤气粉尘含量,一般分为三个阶段--粗除尘、半精细除尘、精细除尘。
煤粉喷吹系统采用了单管路串罐式直接喷吹工艺,这种工艺大大提高了喷吹效率,改善冶炼条件。
本设计中还包括了其他一些环节的设计,例如渣铁处理系统。
在设计的同时,广泛参考借鉴前辈的研究数据和国内外同级别炉容的高炉的实际生产经验,从理论和实践并举的角度出发,努力使本设计的高炉在技术操作上实现自动化和机械化,并把对环境的损害降到最低。
关键词:高炉,冶金计算,热风炉,鼓风机,煤气处理,渣铁处理目录前言 (1)第一章高炉炼铁概况 (2)§1.1 高炉炼铁的开展概况 (2)§1.2 高炉及其附属设备 (2)§1.3 高炉炼铁设计的根本原那么 (2)第二章高炉炼铁综合计算 (4)§2.1 原始资料 (4)§2.2 配料计算 (5)§2.3 物料平衡计算 (8)§2.4 热平衡计算 (12)第三章高炉炼铁车间设计 (17)§3.1 高炉座数及容积设计 (17)第四章高炉本体设计 (18)§4.1 炉型设计 (18)§4.2 炉衬设计 (20)§4.3 高炉冷却设备 (21)§4.4 高炉冷却系统 (23)§4.5 高炉送风管路 (23)§4.6 高炉钢结构 (23)§4.7 高炉根底 (24)第五章附属设备系统 (25)§5.1 供料系统 (25)§5.2 炉顶装料系统 (26)§5.3 送风系统 (27)§5.4 煤气处理系统 (30)§5.5 煤粉喷吹系统 (33)§5.6 渣铁处理系统 (34)第六章高炉炼铁车间平面布置 (37)§6.1 应遵循的原那么 (37)§6.2 高炉炼铁车间平面布置的形式 (37)结论 (38)前言随着改革开放翻开国门,我国的经济飞速开展,也促进了钢铁业的飞速开展。
高炉车间设计
高炉车间设计标题:高炉车间设计引言概述:高炉车间是钢铁生产中重要的环节,其设计对生产效率和产品质量有着重要影响。
本文将从空间布局、设备配置、环境保护、安全防护和人员管理等方面详细介绍高炉车间设计的要点。
一、空间布局1.1 空间利用率:合理利用车间空间,确保设备布局合理,便于操作和维护。
1.2 通道设置:设置合适宽度的通道,方便设备维修和人员通行。
1.3 分区划分:根据生产工艺流程,将车间划分为不同的区域,便于管理和监控。
二、设备配置2.1 设备选型:选择适合生产需求的设备,确保生产效率和产品质量。
2.2 设备布局:合理布置设备,保证生产流程顺畅,减少生产中的瓶颈。
2.3 设备维护:建立完善的设备维护制度,定期检查设备运行状态,确保设备正常运转。
三、环境保护3.1 废气处理:安装适当的废气处理设备,减少废气排放对环境的影响。
3.2 废水处理:建立废水处理系统,确保废水排放符合环保标准。
3.3 噪音控制:采取措施减少车间噪音,保护员工听力和工作环境。
四、安全防护4.1 安全通道:设置安全通道和紧急出口,确保员工在紧急情况下能够迅速撤离。
4.2 安全标识:设置清晰的安全标识,提醒员工注意安全事项。
4.3 安全培训:定期进行安全培训,提高员工的安全意识和应急能力。
五、人员管理5.1 岗位设置:合理设置岗位,明确员工职责,提高工作效率。
5.2 培训计划:制定培训计划,提升员工技能和知识水平。
5.3 激励机制:建立激励机制,激发员工积极性,提高生产效率。
结语:高炉车间设计是一个综合性工程,需要考虑多方面因素。
通过合理的空间布局、设备配置、环境保护、安全防护和人员管理,可以提高生产效率,保证产品质量,确保员工安全和健康。
希翼本文对高炉车间设计有所启示和匡助。
高炉车间设计
高炉车间设计一、引言高炉车间是钢铁企业的核心生产区域,其设计的合理性直接影响到生产效率和产品质量。
本文将以高炉车间设计为主题,详细介绍高炉车间的布局、设备配置、安全措施和环境要求等方面的内容。
二、布局设计1. 车间总体布局:高炉车间应根据生产流程和设备布置合理确定主体结构,包括高炉本体、煤气净化装置、烟气处理装置等。
2. 车间区域划分:根据工艺流程的不同,高炉车间可分为原料处理区、高炉本体区、煤气净化区、烟气处理区、渣铁处理区、冷却区等。
3. 通道和道路布置:确保车间内各区域之间的通道畅通,同时考虑到设备维护和紧急情况下的疏散需求。
4. 办公区域:为工作人员提供舒适的办公环境,包括办公室、会议室、休息室等。
三、设备配置1. 高炉本体:根据生产规模和工艺要求,选择适当规格的高炉本体,确保高炉的正常运行。
2. 原料处理设备:包括矿石破碎机、矿石磨机、矿石筛分机等,用于对原料进行预处理。
3. 煤气净化设备:包括除尘器、脱硫装置、脱硝装置等,用于处理高炉煤气中的颗粒物和有害气体。
4. 烟气处理设备:包括除尘器、脱硫装置、脱硝装置等,用于处理高炉烟气中的颗粒物和有害气体。
5. 冷却设备:包括冷却水系统、冷却设备等,用于对高炉产出物进行冷却处理。
四、安全措施1. 防火安全:车间内应设置火灾报警系统、灭火设备和防火墙等,确保车间的火灾安全。
2. 通风安全:车间内应设置通风设备,保持空气流通,减少有害气体的积聚。
3. 电气安全:车间内的电气设备应符合相关标准,定期检修和维护,确保电气安全。
4. 人员安全:车间内应设置安全警示标识,制定相关安全操作规程,提供必要的个人防护装备。
五、环境要求1. 噪声控制:车间内应采取隔音措施,减少噪声对工作人员的影响。
2. 温度控制:车间内应根据工艺要求设置适宜的温度,提供舒适的工作环境。
3. 空气质量控制:车间内应设置空气净化设备,保持空气中的颗粒物和有害气体浓度在合理范围内。
年产200万吨钢的转炉炼钢车间设计——钢包设计设计0000
钢包是转炉炼钢车间中重要的设备,主要用于存放和运输炼钢过程中产生的钢水。
一个年产200万吨钢的转炉炼钢车间通常会配备多个钢包,以保证流程的顺畅和生产的高效。
在设计钢包时,需要考虑以下几个主要因素:1.钢包容量:钢包的容量应根据车间的产能来确定,一般根据每炉产生的钢水量来计算。
在年产200万吨钢的车间中,钢包的容量应能够容纳每炉产生的钢水量的峰值,并且要考虑到炉次之间的钢水的转运时间。
2.材质选择:钢包一般采用优质的耐火材料制造,以保证耐火性能和使用寿命。
常见的耐火材料有高铝骨料、高纯度黏土等。
此外,钢包还需要考虑到耐压性能和防渣性能,以应对高温和高压条件下的工作环境。
3.外形结构:钢包的外形结构一般为圆柱形,底部有倒角的半球形,以便于钢水的顺利流出。
钢包还需要配备上下盖板,以便于操作和维护。
4.冷却系统:钢包的冷却系统主要用于控制钢水的温度,并防止钢包过热。
冷却系统一般包括冷却水管道和冷却器,通过循环流动的水冷却钢包的壁面和底部,保持恒定的工作温度。
5.温度控制:钢包的温度控制是炼钢过程中的重要环节。
温度控制系统一般包括温度传感器和自动控制系统,通过监测钢水的温度变化,并自动调节加热或冷却装置,以保持钢水的合适温度。
6.安全设施:钢包的设计应考虑到安全因素,如防爆装置、安全阀和过压保护装置等,以保证炼钢车间的安全运行。
综上所述,年产200万吨钢的转炉炼钢车间中的钢包设计应考虑到容量、材质选择、外形结构、冷却系统、温度控制和安全设施等多个因素,以保证生产的高效和安全。
设计过程中还需要考虑车间的具体情况和要求,并结合现代化的炼钢技术和设备,提高钢包的使用寿命和工作效率。
- 1、下载文档前请自行甄别文档内容的完整性,平台不提供额外的编辑、内容补充、找答案等附加服务。
- 2、"仅部分预览"的文档,不可在线预览部分如存在完整性等问题,可反馈申请退款(可完整预览的文档不适用该条件!)。
- 3、如文档侵犯您的权益,请联系客服反馈,我们会尽快为您处理(人工客服工作时间:9:00-18:30)。
年产200万吨炼铁高炉车间设计年产200万吨炼铁高炉车间设计摘要人类获得生铁重要手段是通过高炉炼铁,高炉炼铁是钢铁冶金中的基础环节,同时也是最重要的环节。
本设计任务是设计一个年生产能力达200万吨炼铁高炉车间。
本次设计的高炉1100m³。
高炉炉型为五段式,高炉炉衬设计依据各个部分的工作条件的不同以及炉衬破损的机理,选择相应的耐火材料。
热风炉采用的传统改进型内燃式热风炉,燃烧室为复合型断面,热风炉数量为3座,关于热风炉的设计部分还包括热风炉的各种设备以及相应的技术参数。
上料系统采用的是可不间断上料,原料破损率低的皮带运输上料,炉顶装料设备是并罐式无钟炉顶。
煤气处理系统的功能是降低高炉煤气粉尘含量,一般分为三个阶段--粗除尘、半精细除尘、精细除尘。
煤粉喷吹系统采用了单管路串罐式直接喷吹工艺,这种工艺大大提高了喷吹效率,改善冶炼条件。
本设计中还包括了其他一些环节的设计,例如渣铁处理系统。
在设计的同时,广泛参考借鉴前辈的研究数据和国内外同级别炉容的高炉的实际生产经验,从理论和实践并举的角度出发,努力使本设计的高炉在技术操作上实现自动化和机械化,并把对环境的损害降到最低。
关键词:高炉,冶金计算,热风炉,鼓风机,煤气处理,渣铁处理目录前言 (1)第一章高炉炼铁概况 (2)§1.1 高炉炼铁的发展概况 (2)§1.2 高炉及其附属设备 (2)§1.3 高炉炼铁设计的基本原则 (2)第二章高炉炼铁综合计算 (4)§2.1 原始资料 (4)§2.2 配料计算 (5)§2.3 物料平衡计算 (8)§2.4 热平衡计算 (12)第三章高炉炼铁车间设计 (17)§3.1 高炉座数及容积设计 (17)第四章高炉本体设计 (18)§4.1 炉型设计 (18)§4.2 炉衬设计 (20)§4.3 高炉冷却设备 (21)§4.4 高炉冷却系统 (23)§4.5 高炉送风管路 (23)§4.6 高炉钢结构 (23)§4.7 高炉基础 (24)第五章附属设备系统 (25)§5.1 供料系统 (25)§5.2 炉顶装料系统 (26)§5.3 送风系统 (27)§5.4 煤气处理系统 (30)§5.5 煤粉喷吹系统 (33)§5.6 渣铁处理系统 (34)第六章高炉炼铁车间平面布置 (37)§6.1 应遵循的原则 (37)§6.2 高炉炼铁车间平面布置的形式 (37)结论 (38)前言随着改革开放打开国门,我国的经济飞速发展,也促进了钢铁业的飞速发展。
但是由于其是资源消耗大户,尤其是能源消耗,同时高炉所产生的废气废渣等如果不做适当的利用或处理,对环境会形成极大的破坏,因此钢铁业的发展又面临着严峻的挑战。
为了使得钢铁业朝向节能环保高效的方向发展,就必须对目前的炼铁技术进行创新和改进。
本次设计的任务是年产200万吨的炼铁高炉车间,在计算与设计时参考借鉴了许多前辈们的心血研究,以及国内外同行的生产经验,旨在设计出一座各项经济技术指标优良,而且环保的炼铁车间。
此次设计结合了当前世界高炉发展的趋势,和考虑到我国减少农田占用的基本国情,进行了合理的设计。
但由于专业知识和经验的不足,在设计过程中或多或少存在有偏差和错误的地方,欢迎各位老师同学们向我提出您珍贵的建议和意见。
第一章高炉炼铁概况§1.1 高炉炼铁的发展概况钢铁一直以来都是人类社会使用量最多,使用范围最宽的重要材料。
钢铁在我们的日常生产生活中发挥着至关重要的作用,人们所使用的生产工具和生活设施也都直接或间接地使用钢铁。
衡量一个国家工业化水平的重要标志就是这个国家的钢铁产量,而且其钢铁质量也影响着这个国家其他工业产品的质量,所以钢铁业对一个国家的工业发展具有至关重要的作用。
世界钢铁工业在20世纪迎来了前所未有大发展。
全球钢产量由1900年的2850万吨激增到2000年的8.43亿吨。
20世纪前半叶,英国钢铁业在世界上独占鳌头;20世界中期,美国与前苏联两大强国的钢铁工业在全球处于领先地位;上世纪后叶,随着日本钢铁业在世界钢铁格局中异军突起。
近年来我国钢铁行业的发展面临着巨大的挑战,特别是经济危机以来,全球经济增速放缓,以及我国正处于产业结构调整期以及越来越重视环境问题,大量高能耗的产业面临着整改甚至关闭,去年河北就关闭了一些小型钢铁厂并炸毁部分高能耗的高炉,房地产市场的长期低迷也使钢铁需求量持续下降,使得近几年来我国的钢铁生产状况供大于求。
§1.2 高炉及其附属设备冶炼生铁的最主要设备是五段式高炉本体(炉缸、炉腹、炉腰、炉身、炉喉),外形为圆筒形,炉壳材料为钢板,内村耐火材料,在炉壳和耐火材料之间布置着冷却设备。
要想把铁矿石转变成铁水,紧靠高炉本体是完不成的,还需要其它系统的配合,如供料、送风、煤气处理、渣铁处理、喷吹燃料等附属系统。
§1.3 高炉炼铁设计的基本原则新建炼铁高炉在可行性、环保、安全性、经济性等方面多做细致深入的考虑,可归纳为以下几项基本原则[1]:(1)合法性确保设计原则和设计方案符合国家工业建设的方针和政策。
(2)客观性以事实客观的数据为设计依据,保证能成功地付诸实施。
(3)先进性设计必须根据高炉的当前以及未来发展趋势,反映出钢铁研究领域的最新研究成果。
(4)经济性在综合各方面的考虑的情况下,选择单位产品经济效益最佳的方案。
(5)综合性在设计中,要从全局考虑,尽量做到各部分设计之间能相互协调,不冲突矛盾。
(6)发展远景必须充分考虑到车间将来增产扩大规模的可能性,留有足够的扩建空间。
(7)安全和环保确保生产不会对周边的生态环境造成破坏,并且保障各岗位工作人员的人生安全。
(8)标准化在设计时应尽量采用标准化的设计,这样可以缩短建设时间,节约建设成本。
第二章高炉炼铁综合计算高炉炼铁综合计算包括配料计算、物料平衡计算和热平衡计算。
这是在设计一座新高炉时或者高炉采用新冶炼技术之前选择各项生产指标、确定各物料用量以及工艺参数的重要依。
§2.1 原始资料冶炼一吨生铁需要一定数量的矿石、熔剂和燃料。
对于炼铁设计的计算工艺,燃料的用料是预先确定的,是已知的量,配料计算的主要目的是求出在满足炉渣碱度要求的条件下,冶炼规定成分生铁所需的矿石和熔剂的数量。
计算已知数据如下:一、原燃料成分如表2-1~2-3所示。
二、炼钢用生产,规定生铁成分[Si]=0.25%,[S]=0.028%。
表2-1 原料成分表注:高炉采用两种矿石混合冶炼,其中,烧结矿:生矿=9:1。
表2-2 焦炭成分表表2-3 煤份成分表三、设计焦比K=390kg ,煤比M=110kg 。
四、炉渣碱度R=CaO/SiO 2=1.2。
五、元素在生铁、炉渣与煤气中的分配率,如表2-4所示。
表2-4 表元素分配率表六、选取铁的直接还原度45.0=d r ,氢的利用率%352=H η。
七、鼓风湿度测定为12.5g/m 3(湿风)。
八、热风温度为1100℃。
九、高炉使用冷烧结矿,炉顶温度为200℃。
十、高炉有效容积利用系数)./(6.23h m Fe v =η。
§2.2 配料计算一、吨铁矿石用量计算[2] 燃料带入的铁量27.372560072.0110390)88560003.072560085.0(.=⨯⨯+⨯⨯+⨯=f Fe 矿石用量kgM P T fFe S Si A n Fe 15.17765.011.003.1148.068.0997.0528.5327.37.99-)028.0-25.073.0-7.95(10005.003.168.07.99.7.99])[][73.0-7.95(1000矿)(矿=⨯⨯+⨯+⨯⨯⨯⨯=⨯++--⨯=二、生铁成分计算(%)21.9510/997.0)27.353582.015.177610/997.0).e e (][混)(=⨯+⨯=⨯+⨯=f F F A Fe(%)03.010_/142/620001.039000145.015.1776(10/)142/62(][焦)((混)=⨯⨯+⨯=⨯⨯+⨯=P K P A P (%)10.010/5.00011.015.177610/5.0][)混(=⨯⨯=⨯⨯=Mn A Mn (%)38.4028.0026.0098.025.021.95100][][][100][=-----=---=P Mn Fe C生铁成分表如表2-5所示。
表2-5 生铁成分表(%)三、石灰石用量计算 矿石、燃料带入的CaO 的量192.29kg4005.01100087.039010602.015.1776aO aO (煤)(焦))混(=⨯+⨯+⨯=⨯+⨯+⨯=C M C K CaO A矿石、燃料带入的SiO 2量kgSiO M SiO K SiO A 5.178286025.010-0557.01100636.03900861.015.1776煤)(2焦)(2(混)2=⨯⨯⨯+⨯+⨯=⨯+⨯+⨯= 石灰石的有效熔剂性:)%(06.54031.12.1-301.55-aO )石灰石(2石灰石有效=⨯=⨯=SiO R C CaO石灰的用量kg 53.405406.0/)29.1922.15.178(=-⨯=φ 四、渣量及炉渣成分计算炉料带入的各种炉渣组分的数量为kg C 70.21455301.053.4029.192aO =⨯+=∑ ∑=⨯+=kg SiO 91.17801031.053.405.1782∑=⨯+⨯+⨯+⨯=kg MgO 41.650623.053.400023.01100012.0390035.015.1776kgO Al 75.5000117.053.400531.01100542.039001353.015.177632=⨯+⨯+⨯+⨯=∑渣中MnO 量:kg MnO 26.155/715.00001115.1776渣=⨯⨯⨯= 渣中FeO 量:kg FeO 68.356/72997.0/003.01.952渣=⨯⨯= 1t 生铁炉料带入的硫量(硫负荷):kg S22.30023.01100055.039000046.015.1776=⨯+⨯+⨯=∑进入生铁的硫量:kg S 28.010028.0生铁=⨯= 进入煤气的硫量:kg S 16.005.022.3煤气=⨯= 进入渣中的硫量:kg S 78.216.0-28.0-22.3渣==炉渣组成如表2-6所示。
表2-6 炉渣组成表炉渣性能校核:炉渣实际碱度R=214.70/178.91=1.20(与规定碱度相符); 炉渣脱硫之硫的分配系数L s =2×0.28/0.028=20; 查阅炉渣相图可知,该炉渣熔化温度为1450℃; 黏度:1500℃时,2.5泊;1400℃时,4泊。