陶瓷注浆模具制作、泥浆性能、成型方法分析
陶瓷注浆成型技术
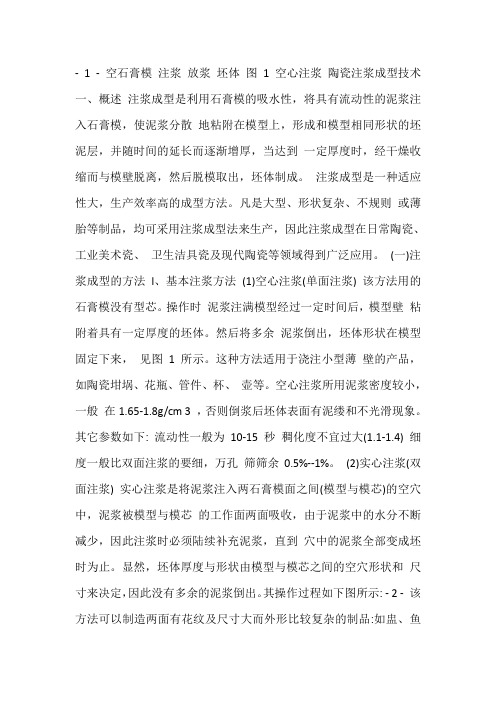
- 1 - 空石膏模注浆放浆坯体图1 空心注浆陶瓷注浆成型技术一、概述注浆成型是利用石膏模的吸水性,将具有流动性的泥浆注入石膏模,使泥浆分散地粘附在模型上,形成和模型相同形状的坯泥层,并随时间的延长而逐渐增厚,当达到一定厚度时,经干燥收缩而与模壁脱离,然后脱模取出,坯体制成。
注浆成型是一种适应性大,生产效率高的成型方法。
凡是大型、形状复杂、不规则或薄胎等制品,均可采用注浆成型法来生产,因此注浆成型在日常陶瓷、工业美术瓷、卫生洁具瓷及现代陶瓷等领域得到广泛应用。
(一)注浆成型的方法l、基本注浆方法(1)空心注浆(单面注浆) 该方法用的石膏模没有型芯。
操作时泥浆注满模型经过一定时间后,模型壁粘附着具有一定厚度的坯体。
然后将多余泥浆倒出,坯体形状在模型固定下来,见图 1 所示。
这种方法适用于浇注小型薄壁的产品,如陶瓷坩埚、花瓶、管件、杯、壶等。
空心注浆所用泥浆密度较小,一般在1.65-1.8g/cm 3 ,否则倒浆后坯体表面有泥缕和不光滑现象。
其它参数如下: 流动性一般为10-15 秒稠化度不宜过大(1.1-1.4) 细度一般比双面注浆的要细,万孔筛筛余0.5%--1%。
(2)实心注浆(双面注浆) 实心注浆是将泥浆注入两石膏模面之间(模型与模芯)的空穴中,泥浆被模型与模芯的工作面两面吸收,由于泥浆中的水分不断减少,因此注浆时必须陆续补充泥浆,直到穴中的泥浆全部变成坯时为止。
显然,坯体厚度与形状由模型与模芯之间的空穴形状和尺寸来决定,因此没有多余的泥浆倒出。
其操作过程如下图所示: - 2 - 该方法可以制造两面有花纹及尺寸大而外形比较复杂的制品:如盅、鱼盘、瓷板等。
实心注浆常用较浓的泥浆,一般密度在1.8g/cm 3 以上,以缩短吸浆时间。
稠化度(1.5 -2.2),细度可粗些,万孔筛筛余1%--2%。
2、强化注浆法为缩短注浆时间,提高注件质量,在两种基本注浆方法的基础上,形成了一些新的注浆方法,这些方法统称为强化注浆。
陶瓷高压注浆成型工艺

陶瓷高压注浆成型工艺陶瓷是一种非常重要的材料,它具有高硬度、高耐磨、高耐腐蚀等优良性能,因此被广泛应用于各种领域,如建筑、电子、化工、医疗等。
而陶瓷的制造过程中,高压注浆成型工艺是一种非常重要的工艺,它可以使陶瓷制品具有更高的密度和更好的性能。
高压注浆成型工艺是一种将陶瓷粉末和液体添加剂混合后,通过高压注入模具中,然后在高温高压下进行成型的工艺。
这种工艺可以使陶瓷制品具有更高的密度和更好的性能,同时还可以大大提高生产效率和降低成本。
高压注浆成型工艺的主要步骤包括:原料制备、混合、注浆、压制、烧结等。
其中,原料制备是非常重要的一步,它直接影响到陶瓷制品的质量和性能。
一般来说,陶瓷粉末的制备需要经过多道工序,如研磨、筛分、干燥等,以保证粉末的均匀性和细度。
而液体添加剂的制备则需要根据不同的陶瓷材料和工艺要求进行选择和调配。
混合是将陶瓷粉末和液体添加剂混合均匀的过程,这一步的目的是使粉末和液体充分结合,形成均匀的浆料。
混合的方法有很多种,如干法混合、湿法混合、球磨混合等,不同的方法适用于不同的陶瓷材料和工艺要求。
注浆是将混合好的浆料注入模具中的过程,这一步需要使用高压注浆机进行操作。
高压注浆机可以将浆料注入模具中,并在一定的时间内保持一定的压力,以保证浆料充分填充模具中的空隙。
压制是将注入模具中的浆料进行压制的过程,这一步需要使用压力机进行操作。
压力机可以将模具中的浆料进行压实,使其具有更高的密度和更好的性能。
烧结是将压制好的陶瓷制品进行高温处理的过程,这一步可以使陶瓷制品具有更高的硬度、密度和耐磨性。
烧结的温度和时间需要根据不同的陶瓷材料和工艺要求进行选择和调整。
总的来说,高压注浆成型工艺是一种非常重要的陶瓷制造工艺,它可以使陶瓷制品具有更高的密度和更好的性能,同时还可以大大提高生产效率和降低成本。
随着科技的不断发展和进步,高压注浆成型工艺也在不断地改进和完善,相信在不久的将来,它将会在更多的领域得到应用。
注浆成型
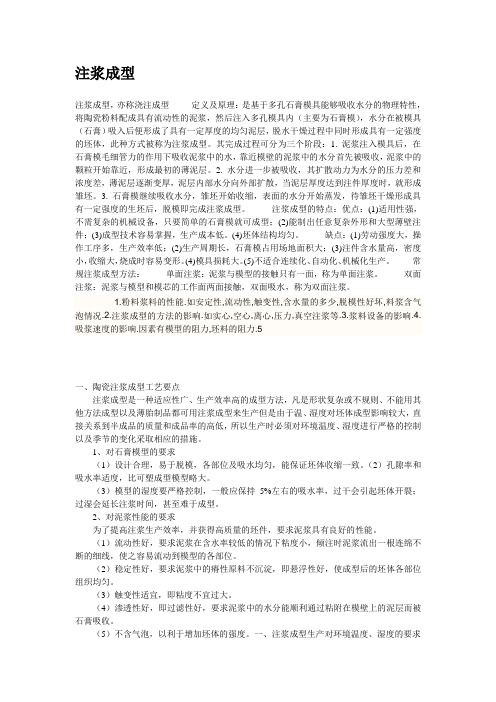
注浆成型注浆成型,亦称浇注成型定义及原理:是基于多孔石膏模具能够吸收水分的物理特性,将陶瓷粉料配成具有流动性的泥浆,然后注入多孔模具内(主要为石膏模),水分在被模具(石膏)吸入后便形成了具有一定厚度的均匀泥层,脱水干燥过程中同时形成具有一定强度的坯体,此种方式被称为注浆成型。
其完成过程可分为三个阶段:1. 泥浆注入模具后,在石膏模毛细管力的作用下吸收泥浆中的水,靠近模壁的泥浆中的水分首先被吸收,泥浆中的颗粒开始靠近,形成最初的薄泥层。
2. 水分进一步被吸收,其扩散动力为水分的压力差和浓度差,薄泥层逐渐变厚,泥层内部水分向外部扩散,当泥层厚度达到注件厚度时,就形成雏坯。
3. 石膏模继续吸收水分,雏坯开始收缩,表面的水分开始蒸发,待雏坯干燥形成具有一定强度的生坯后,脱模即完成注浆成型。
注浆成型的特点:优点:(1)适用性强,不需复杂的机械设备,只要简单的石膏模就可成型;(2)能制出任意复杂外形和大型薄壁注件;(3)成型技术容易掌握,生产成本低。
(4)坯体结构均匀。
缺点:(1)劳动强度大,操作工序多,生产效率低;(2)生产周期长,石膏模占用场地面积大;(3)注件含水量高,密度小,收缩大,烧成时容易变形。
(4)模具损耗大。
(5)不适合连续化、自动化、机械化生产。
常规注浆成型方法:单面注浆:泥浆与模型的接触只有一面,称为单面注浆。
双面注浆:泥浆与模型和模芯的工作面两面接触,双面吸水,称为双面注浆。
1.粉料浆料的性能.如安定性,流动性,触变性,含水量的多少,脱模性好坏,料浆含气泡情况.2.注浆成型的方法的影响.如实心,空心,离心,压力,真空注浆等.3.浆料设备的影响.4.吸浆速度的影响.因素有模型的阻力,坯料的阻力.5一、陶瓷注浆成型工艺要点注浆成型是一种适应性广、生产效率高的成型方法,凡是形状复杂或不规则、不能用其他方法成型以及薄胎制品都可用注浆成型来生产但是由于温、湿度对坯体成型影响较大,直接关系到半成品的质量和成品率的高低,所以生产时必须对环境温度、湿度进行严格的控制以及季节的变化采取相应的措施。
陶瓷注浆模具制作、泥浆性能、成型方法
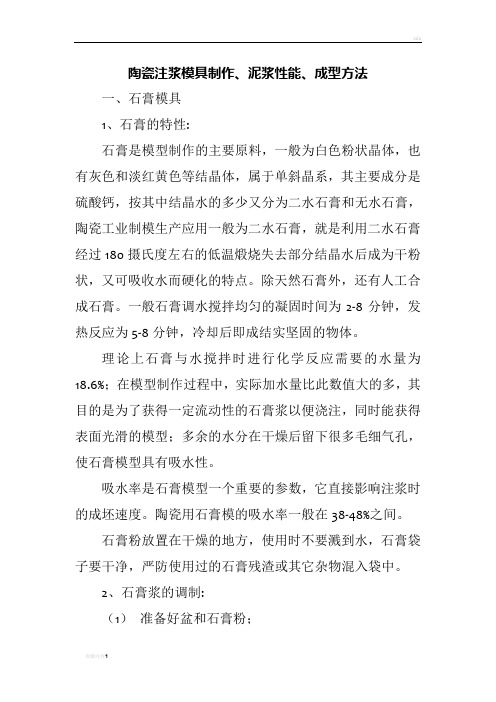
陶瓷注浆模具制作、泥浆性能、成型方法一、石膏模具1、石膏的特性:石膏是模型制作的主要原料,一般为白色粉状晶体,也有灰色和淡红黄色等结晶体,属于单斜晶系,其主要成分是硫酸钙,按其中结晶水的多少又分为二水石膏和无水石膏,陶瓷工业制模生产应用一般为二水石膏,就是利用二水石膏经过180摄氏度左右的低温煅烧失去部分结晶水后成为干粉状,又可吸收水而硬化的特点。
除天然石膏外,还有人工合成石膏。
一般石膏调水搅拌均匀的凝固时间为2-8分钟,发热反应为5-8分钟,冷却后即成结实坚固的物体。
理论上石膏与水搅拌时进行化学反应需要的水量为18.6%;在模型制作过程中,实际加水量比此数值大的多,其目的是为了获得一定流动性的石膏浆以便浇注,同时能获得表面光滑的模型;多余的水分在干燥后留下很多毛细气孔,使石膏模型具有吸水性。
吸水率是石膏模型一个重要的参数,它直接影响注浆时的成坯速度。
陶瓷用石膏模的吸水率一般在38-48%之间。
石膏粉放置在干燥的地方,使用时不要溅到水,石膏袋子要干净,严防使用过的石膏残渣或其它杂物混入袋中。
2、石膏浆的调制:(1)准备好盆和石膏粉;(2)在盆中先加入适量的水,再慢慢把石膏粉沿盆边撒入水中,一定要按照顺序先加水再加石膏。
(3)直到石膏粉冒出水面不再自然吸水沉陷,稍等片刻,就用搅拌棒搅拌,要快速有力、用力均匀。
成糊状即可。
(4)石膏在调制时的比例为:水:石膏=1:1.4-1.8左右。
(5)注意挑除石膏浆里的硬块和杂质。
3、模型翻制操作:常用的材料和工具有:钢锯条、锯条刀,直尺三角板、毛刷、海绵、脱模剂等。
a、清理工作台,把石膏母模清理干净,在石膏母模上均匀涂抹脱模剂,一定注意各个部位必须均匀涂上,不能遗漏。
b、按顺序合模夹紧,并安放好各种模具内配件。
c、调制石膏浆,缓缓注入围好的空腔内,并不断搅动或震动石膏浆,使气泡排出,直至注满母模。
d、静置一段时间,等石膏发热固化后,可开模,如不容易打开,可以用轻敲、气冲、水冲泡等方法打开。
陶瓷工艺学(4.4)--注浆成型最终
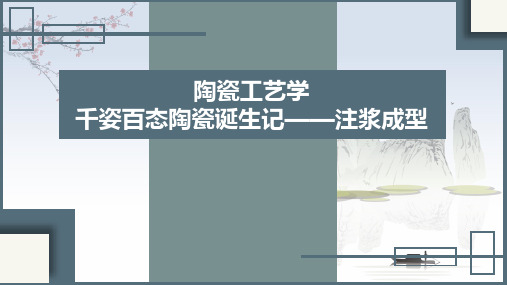
间,还可减少坯体的干燥收
为
缩和脱模后坯体的水分。注
浆压力越高,成型速度越大
生坯强度越高,但是受模型
强度的限制。模型材料可以
采用石膏模型、多孔树脂模
型和无机填料模型。
微压注浆 一般压力在0.05MPa以下 中压注浆 一般压力在0.15MPa——0.20MPa之间 高压注浆 一般压力在0.20MPa以上
单面注浆 双面注浆
压力注浆 真空注浆 离心注浆
其他注浆成型 方法
热压铸成型
成组注浆
热浆注浆
4.4 注浆成型方法
单面注浆
将泥浆注入模型中,待泥浆在模型中停留一段时间,形成所需注件厚度 时,倒出多余泥浆,随后带模干燥,待注件干燥收缩后脱模,取出注件。
单面注浆操作示意图
4.4.1 基本注浆方 法
双面注浆
本节课主要内容
4.1、
注浆过程Leabharlann 4.2、注浆成型的特点
4.3、
注浆成型对泥料的要求
4.4、
注浆方法
4.1 注浆过程
第一阶段
从泥浆注入 石膏模吸入开 始到形成薄泥 层;
第二阶段
形成薄泥层 后,泥层逐渐 增厚,知道形 成注件;
第三阶段
从雏坯成型 后到脱模为收 缩脱模阶段;
4.1 注浆过程
为了提高注浆速率,通常从以下三种方式:
陶瓷工艺学 千姿百态陶瓷诞生记——注浆成型
课程导入
川剧变脸
川剧脸谱,是川剧表演艺术中重要的组成部分,是历代川剧艺人 共同创造并传承下来的艺术瑰宝。
川剧《白蛇传》中的许仙
川剧变脸大师
课程导入
千姿百态陶瓷诞生记
泥浆
石膏模具
百态陶瓷
课程导入
【陶瓷生产】注浆泥料的工艺性能

【陶瓷生产】注浆泥料的工艺性能注浆泥料的工艺性能,主要有如下要求:(1)泥浆的粘度和流动性:注浆成形的泥浆,要求具有良好的流动性,故其含水率比塑性成形的泥料高,即使加入电解质稀释,它的含水率通常也在2836%之间。
如过分减少泥浆的水份,则粘度增大,流动性降低,不仅会造成注浆成形时难以注满模型的所有部位,而且易引起气泡和针孔等缺陷产生,还会减慢注成速度。
若是增加泥浆的含水率,虽可改善泥浆的流动性,但易使泥浆中的粗颗粒沉淀而引起坏体开裂,还会延长模型吸浆时间,降低生产效率。
影响泥浆流动性的因素主要有:①泥浆颗粒的粗细:在同一浓度下,颗粒越细泥浆的粘性大。
②泥浆的温度;如泥浆温度升高,作为泥浆分散介质的水分粘度下降,泥浆的流动性增加。
③泥浆的处理方法:如泥浆经过真空处理,不仅可以提高泥浆的流动性,还能增加坯体的密度和强度。
④稀释剂的种类及用量;如前所述,各种电解质对不同粘土所起的稀释作用是有差别的,其用量也要适宜。
(2)泥浆的稳定性:泥浆的稳定性,是指泥浆在较长时间的存放下,不发生沉淀、分层和触变性变坏的性能。
通常来说,固体颗粒越细,泥浆越稳定,即使泥浆中含有大量的瘠性原料,只要颗粒细度适宜,也会悬浮而不易沉淀。
在泥浆中加入适宜种类和数量的电解质,也可增强泥浆的稳定性。
(3)泥浆的触变性:泥浆的触变性,又称稠化性,是指泥浆在静置后变稠而一经搅拌立即恢复流动的性质。
如泥浆的触变性很大,会影响注浆操作的效率降低,注成的坯体在脱模后稍遇震动就会变形甚至塌陷。
若触变性太小,则泥浆的悬浮性较差,易引起泥浆中的粗颗粒沉淀。
注浆时泥料在模型内难以形成一定的厚度,而且脱模困难。
影响泥浆触变性的因素较多,如泥浆的含水率太低;固体颗粒形状不规则或颗粒太细;电解质加入过多;泥浆的温度太低等,都易使泥浆的触变性增大。
(4)泥浆的渗透性:泥浆的渗透性,是指泥浆中水分的过滤性,即去水性。
如泥浆的渗透性差,会影响在注浆操作过程中泥浆中的水分不易被模型吸出,不仅会延长注浆时间,还易引起实心注浆的坯体内部分层或出现“溏心”,造成坯件开裂、冲泡等缺陷发生。
陶瓷注浆成型技术

空石膏模 注浆 放浆 坯体 图1空心注浆陶瓷注浆成型技术一、概述注浆成型是利用石膏模的吸水性,将具有流动性的泥浆注入石膏模内,使泥浆分散 地粘附在模型上,形成和模型相同形状的坯泥层,并随时间的延长而逐渐增厚,当达到 一定厚度时,经干燥收缩而与模壁脱离,然后脱模取出,坯体制成。
注浆成型是一种适应性大,生产效率高的成型方法。
凡是大型、形状复杂、不规则 或薄胎等制品,均可采用注浆成型法来生产,因此注浆成型在日常陶瓷、工业美术瓷、 卫生洁具瓷及现代陶瓷等领域得到广泛应用。
(一)注浆成型的方法l 、基本注浆方法(1)空心注浆(单面注浆)该方法用的石膏模没有型芯。
操作时泥浆注满模型经过一定时间后,模型内壁粘附着具有一定厚度的坯体。
然后将多余泥浆倒出,坯体形状在模型内固定下来,见图1所示。
这种方法适用于浇注小型薄壁的产品,如陶瓷坩埚、花瓶、管件、杯、壶等。
空心注浆所用泥浆密度较小,一般在1.65—1.8g/cm 3,否则倒浆后坯体表面有泥缕和不光滑现象。
其它参数如下:流动性一般为10—15秒稠化度不宜过大(1.1—1.4)细度一般比双面注浆的要细,万孔筛筛余0.5%--1%。
(2)实心注浆(双面注浆)实心注浆是将泥浆注入两石膏模面之间(模型与模芯)的空穴中,泥浆被模型与模芯 的工作面两面吸收,由于泥浆中的水分不断减少,因此注浆时必须陆续补充泥浆,直到穴中的泥浆全部变成坯时为止。
显然,坯体厚度与形状由模型与模芯之间的空穴形状和尺寸来决定,因此没有多余的泥浆倒出。
其操作过程如下图所示:该方法可以制造两面有花纹及尺寸大而外形比较复杂的制品:如盅、鱼盘、瓷板等。
实心注浆常用较浓的泥浆,一般密度在1.8g/cm3以上,以缩短吸浆时间。
稠化度(1.5—2.2),细度可粗些,万孔筛筛余1%--2%。
2、强化注浆法为缩短注浆时间,提高注件质量,在两种基本注浆方法的基础上,形成了一些新的注浆方法,这些方法统称为强化注浆。
强化注浆主要有以下几种:(1)压力注浆采用加大泥浆压力的方法来加速水分扩散,从而加速吸浆速度。
瓷器注浆工艺

瓷器注浆工艺瓷器注浆工艺,作为传统瓷器生产工艺的重要环节之一,承载着瓷器的质量和美观度。
它是将瓷泥填充到瓷器模具中,经过一系列工艺加工,最终形成瓷器的过程。
本文将介绍瓷器注浆工艺的具体过程和技术要点,以及对瓷器质量的影响。
瓷器注浆工艺的第一步是选择瓷泥。
瓷泥是由瓷土、岩石粉末和其他添加剂经过混合、研磨、过筛等工艺制成的。
其中,瓷土是瓷泥的主要成分,它决定了瓷器的质地和质量。
常见的瓷土有高岭土、长石和石英等。
在选择瓷土时,要根据瓷器的用途和要求,选择合适的瓷土配方,以保证瓷器的强度和透明度。
选好瓷泥后,接下来是注浆的过程。
注浆是将瓷泥填充到瓷器模具中的过程。
在注浆过程中,需要掌握好注浆的速度和压力,以保证注浆均匀而不产生气泡。
同时,还要注意维持瓷泥的流动性,避免过早凝固。
注浆过程中,工人需要根据经验掌握好时间和技巧,以确保注浆质量的稳定和一致性。
注浆完毕后,瓷器需要经过一段时间的自然陈化。
陈化是指将瓷器在自然环境中逐渐干燥,以使其内部结构更加稳定。
在陈化过程中,瓷器会慢慢失去水分,逐渐变硬。
这个过程需要根据瓷器的大小和厚度来决定,一般需要几天到几周的时间。
陈化过程中,要注意避免瓷器受到外界的突然温度变化和震动,以免导致瓷器开裂或变形。
陈化完成后,瓷器需要进行修整和修补。
修整是指将瓷器表面的不平整部分修整平整,以便后续的磨光和装饰工艺。
修补是指修复瓷器在注浆和陈化过程中产生的瑕疵和裂纹。
修整和修补需要经验丰富的工匠进行,以确保瓷器的外观和质量。
修整和修补完成后,瓷器需要进行磨光和装饰。
磨光是指将瓷器表面进行打磨,使其光滑细腻。
装饰是指对瓷器进行彩绘、贴花等工艺,以增加瓷器的艺术价值和观赏性。
磨光和装饰需要精细的工艺和细致的手工操作,以确保瓷器的质量和美观度。
瓷器注浆工艺在整个瓷器生产过程中起着至关重要的作用。
它决定了瓷器的质量和美观度,直接影响着瓷器的市场竞争力和附加值。
因此,在进行瓷器注浆工艺时,需要严格按照工艺要求进行操作,注重细节和精益求精。
- 1、下载文档前请自行甄别文档内容的完整性,平台不提供额外的编辑、内容补充、找答案等附加服务。
- 2、"仅部分预览"的文档,不可在线预览部分如存在完整性等问题,可反馈申请退款(可完整预览的文档不适用该条件!)。
- 3、如文档侵犯您的权益,请联系客服反馈,我们会尽快为您处理(人工客服工作时间:9:00-18:30)。
陶瓷注浆模具制作、泥浆性能、成型方法一、石膏模具1、石膏的特性:石膏是模型制作的主要原料,一般为白色粉状晶体,也有灰色和淡红黄色等结晶体,属于单斜晶系,其主要成分是硫酸钙,按其中结晶水的多少又分为二水石膏和无水石膏,陶瓷工业制模生产应用一般为二水石膏,就是利用二水石膏经过180摄氏度左右的低温煅烧失去部分结晶水后成为干粉状,又可吸收水而硬化的特点。
除天然石膏外,还有人工合成石膏。
一般石膏调水搅拌均匀的凝固时间为2-8分钟,发热反应为5-8分钟,冷却后即成结实坚固的物体。
理论上石膏与水搅拌时进行化学反应需要的水量为18.6%;在模型制作过程中,实际加水量比此数值大的多,其目的是为了获得一定流动性的石膏浆以便浇注,同时能获得表面光滑的模型;多余的水分在干燥后留下很多毛细气孔,使石膏模型具有吸水性。
吸水率是石膏模型一个重要的参数,它直接影响注浆时的成坯速度。
陶瓷用石膏模的吸水率一般在38-48%之间。
石膏粉放置在干燥的地方,使用时不要溅到水,石膏袋子要干净,严防使用过的石膏残渣或其它杂物混入袋中。
2、石膏浆的调制:(1)准备好盆和石膏粉;(2)在盆中先加入适量的水,再慢慢把石膏粉沿盆边撒入水中,一定要按照顺序先加水再加石膏。
(3)直到石膏粉冒出水面不再自然吸水沉陷,稍等片刻,就用搅拌棒搅拌,要快速有力、用力均匀。
成糊状即可。
(4)石膏在调制时的比例为:水:石膏=1:1.4-1.8左右。
(5)注意挑除石膏浆里的硬块和杂质。
3、模型翻制操作:常用的材料和工具有:钢锯条、锯条刀,直尺三角板、毛刷、海绵、脱模剂等。
a、清理工作台,把石膏母模清理干净,在石膏母模上均匀涂抹脱模剂,一定注意各个部位必须均匀涂上,不能遗漏。
b、按顺序合模夹紧,并安放好各种模具内配件。
c、调制石膏浆,缓缓注入围好的空腔内,并不断搅动或震动石膏浆,使气泡排出,直至注满母模。
d、静置一段时间,等石膏发热固化后,可开模,如不容易打开,可以用轻敲、气冲、水冲泡等方法打开。
e、每块模具做完,都要及时用钢锯条刮平修整,模具子口要吻合。
f、做好的模具要烘干后用,烘干时温度不得高于60摄氏度,以免模具粉化报废。
注意:整个制作模具的过程要求胆大心细,必须牢记涂抹脱模剂、开牙口、刮平。
要求模具整体光滑,表面平整,内部光洁,不允许有飞棱和毛边。
二、注浆泥浆的质量要求1. 细度有恰当的细度并有一定的颗粒级配,泥浆细度是涉及泥浆流动性、制品收缩、高温液相、产品吸水率等的重要因素。
它将会影响泥浆的悬浮性、渗透性及坯体的抗折强度,注浆成型所要求的泥浆细度比较严格。
泥浆细度过粗,抗折强度低,造成较多的半成品破损,加工性能差。
待别是双面吃浆产品及立浇座便器等在双面吃浆部位,易造成接触不实,分层而在烧成中出现分层或凸起等现象,同时在烧成过程中,颗粒间接触面少,瓷化不完全,产品吸水率大,易出现风惊、炸裂。
泥浆细度的控制,首先是入磨前控制硬质原料的粒度。
它不仅影响到球磨的时间,而且影响到球磨后泥浆中的颗粒级配。
目前我国在卫生陶瓷的实际生产中,对粒度的控制普通用万孔筛(250目)筛余来表示。
其实是不科学的。
因为我们从有关资料及实践中得知,卫生陶瓷泥浆中350目筛筛余量在5-10%,小于10微米颗粒占44-55%的泥浆性能优良。
为达此目的,一方面要从配方上着手,另一方面要设法控制球磨前硬质原料粒度。
对泥浆粒度的检验也应按上述方法进行。
这对泥浆性能的稳定较有好处。
2.水分在保证流动性及成型性能的前提下,水分越少越好,通常为28%~35%,生产上习惯用控制泥浆密度来控制含水率,泥浆密度一般为 1.65~1.85g/cm3,一般小件制品可取下限,而大件制取其上限。
3.流动性泥浆的流动性要好,保证注浆时泥浆能充满整个模型。
生产上习惯用控制相对粘度即流动度来控制流动性。
要求涂-4粘度计30s,陈腐后达到45s左右,相对粘度主要与泥浆的含水率和稀释用电解质的种类和数量有关,生产上通过加入电解质来获得含水率低、流动性好的浓泥浆。
4.触变性用稠化度来衡量,它等于100ml泥浆在恩氏粘度计中静置30min后流出时间与静置30s后流出时间的比值。
一般希望泥浆稠化度较小,以便于管道输送又能保证成坯。
触变性是指泥浆在静止时粘性会增加,一经搅拌或振动,稠化的泥浆又获得流动性,如再恢复静止状态,则又重新稠化,这种可逆变化的性能称为触变性。
泥浆的触变性主要来源于黏土性能及杂质的我少,触变性的测定方法,一般都有是测定两次流动时间,一次是搅拌后静止一分钟的流动时间a,一次是静止30分钟后的流动时间b,b/a叫做厚化系数。
稍有触变性的泥浆,坯体的加工性能要好些。
如果触变性太强,会使泥浆漏浆困难,排浆性不好,坯体还会出现糖心,易变形,模型的狭窄部位容易出现存浆裂,同时给操作带来困难,根据有关资料介绍及证明肥复实践。
5.悬浮性浆料中的固体颗粒能较长时间呈悬浮状态,这样便于泥浆的输送及贮存,在成型过程中也不易分层。
6.、泥浆的真空处理泥浆在制备、储存和输送过程中,难免会混入一定数量的空气。
为了使制品表面光洁平具有较高的机械强度、良好的物理性能,在浇注前一般要对泥浆进行真空脱气处理,另外泥浆经真空脱气处理后还可以改善其流动性。
在盛满泥浆的封闭式浆塔中,先用压缩空气进行搅拌,作用是使泥浆的组合成均匀并保持悬浮状态,减少分层现象,并使电解质的作用更加完全。
在搅拌过程中有一些细小的气泡可以随同压缩空气溢出,但是有大部分气体仍残留在泥浆中。
如果不使用真空脱气处理,泥浆中的大量气体就无法排除这样就容易使坯体产生气泡、棕眼等缺陷。
为保证制品的质量,应进行真空脱气处理,根据资料介绍,利用真空脱气装置,将50升泥浆经真空处理10-15分钟,可使干坯及制品的强度提高15-20%。
实践证明,通常要用700-720mmHg的真空度进行脱气并保持一定时间,才能起到真空脱气的作用,从而使干坯及制品的强度提高。
三、注浆料的制备流程及选择注浆料的制备流程大致与可塑料制备流程中泥浆压滤前的流程相似。
所不同的是注浆料中必须加入电解质以稀释泥浆,获得流动性好、含水率低的浓泥浆。
泥浆稀释泥浆的稀释要控制下列工艺参数。
1.合理控制泥浆的密度和颗粒细度。
当泥浆的容积密度过大,或颗粒太细时,颗粒间距较小,颗粒间引力较大,泥浆的流动阻力就大,当引力大于胶粒间的斥力时就会聚沉,反之,如果泥浆的密度过小,或颗粒太粗,则会降低成坯密度和坯体强度,泥浆也会因颗粒沉淀而破坏稳定性。
2.添加电解质及其稀释机理根据泥浆的组成和性质,选用合适的电解质作稀释剂是泥浆制备的重要措施之一。
在粘土—水系统中,粘土颗粒由于断键、同晶取代(如硅氧四面体中的Si4+被Al3+所取代,铝氧八面体中的Al+被二价的Mg+、Ca+所取代),总是带有电荷的(通常为负电荷)。
由于化水化作用,被粘土颗粒吸附的只能是水化阳离子。
距离粒子表面越远,引力也越弱,吸附阳离子浓度就越小,粘土颗粒周围形成包括吸附层和扩散层的水化膜。
粘土胶团开成了三个不同层次:胶核(粘土颗粒本身)、胶粒(胶核加吸附层)、胶团(胶粒加扩散层),胶团结构见图3-4-11。
当粘土颗粒移动时,只有吸附层随之移动。
吸附层表面对溶液存在电位差,称之为ζ电位。
胶粒的ζ电位大,则胶粒间的斥力大,不易相互聚合产生絮凝从而使泥浆稳定,流动性也好。
ζ电位主要取决于扩散层厚度和胶核表面电荷密度并与它们成正比关系。
电解质中的一价阳离子(H+除外)的电价比二价、三价的要小,但水化离子的半径却比二价三价阳离子的大,因此在泥浆中加入由一价阳离子(Na+)组成的电解质后,由于一价离子(H+除外)吸附能力弱,所以进入胶团吸附层的离子数少,使整个胶粒呈现的负电荷较多。
同时,一价离子水化能力强,进入扩散层厚度增加,水化膜加厚,导致ζ电位增加使泥浆的稳定性、流动性增强。
此外,泥浆的pH值对泥浆的稳定也有重要意义,因为粘土颗粒是片状的,一般边上带正电,面上带负电,如果加入电解质后使溶液呈碱性OH-过剩)则可使部分颗粒边上也带负电,从而防止颗粒的边-面之间因带不同电荷而相互吸引导致凝聚,促使泥浆稀释。
陶瓷工业用电解质分无机和有机两大类(多为相应钠盐),其中最常用字的有水玻璃纯碱(Na2CO3)三聚磷酸钠、六偏磷酸钠、腐殖酸钠等。
生产是常常同时使用水玻璃和纯碱作电解质以调整吸浆速度和坯体强度。
水玻璃与纯碱的质量比可取1:3。
单用水玻璃的泥浆成坯时泥浆渗水性差,易粘模,坯体致密,强度较大;而单用纯碱的泥浆成坯体疏松吸浆速度快、脱模快,但干坯强度小。
在使用水玻璃时要选用适当的模数,即SiO2/Na2O的比值,通常取3左右。
纯碱必须防止受潮,变成NaHCO3,从而使泥浆絮凝。
电解质的用量要合适,太少不能充分置换H+、Ca2+等,太多则会使部分扩散层离子压入吸附层,使胶粒的净电荷减少,扩散层厚度减少,导致颗粒ζ电位减小,泥浆发生絮凝。
四、注浆成型操作:注浆成型主要是利用石膏模具吸收水分的特性,使泥浆吸附在模具壁上而形成均匀的泥层,在一定时间内达到所需的厚度,再倾倒出多余的泥浆,在模具中的其余泥层水分继续受石膏模具吸收而逐渐硬化,经干燥并产生体积收缩与模具脱离,即获得完好的粗坯。
(1)模具的准备和清理包括:按标准对新模型进行检查,模型内表面有油污及残缺的地方必须清除干净,新模型的水分一般为6—8%,但形状复杂小而薄的可以高一些,反之则可低一些,最低不小于4%;模型的烘干,一般控制在室温28~35℃温度,防止因干燥不均而使制品变形:使用前要将模型上附着的灰土等杂质清除干净,使模型能对合严实以避免跑浆漏泥;增强坯体在模型上的附着力,有利于防止杂质对坯体造成污染。
(2)对模型吃浆面根据脱模情况刷模,分刷滑石粉和刷水(包括清水和泥浆水)。
当脱模困难时刷滑石粉,用细纱布包裹滑石粉在吃浆面上轻轻拍打;如脱模时发现模具不挂坯,则可少刷滑石粉或者不刷滑石粉,不刷滑石粉仍不挂坯的就要用清水或者泥浆水擦模。
(3)正确进行组装对已处理好需要组合使用的模型,对正合严、夹紧、塞紧注浆管和微气压管准备注浆。
(4)泥浆要做到浆内无泥块、杂质,不可随意加水。
经真空滤气后打入注浆管道。
(5)将泥浆轻缓地注满模型,应避免“泥浆冲击”造成斑点、圈纹等缺陷。
(6)使用试验浇注杯,判断正确的放浆浆时间,从而达到要求的浇注件厚度。
(7)回浆时应预先敞开气孔,避免“抽吸”现象。
目前有三种空浆方法:自然压力回浆,即利用管道的坡度,将放出的泥浆在自然压力下流回泥浆池;利用泥浆泵,通过回浆管道,将管道及模型里多余的泥浆抽回泥浆池,这种方法往往因管道漏气影响效果;气压回浆,即利用注浆线上的微压气管打入压缩空气,压出泥浆,回浆压力控制在0.01-0.015Mpa。
(8)判断脱模所要求达到的固化程度(巩固时间)。