陶瓷注浆成型工艺要点及缺陷分析精选word资料5页
陶瓷注浆成型技术
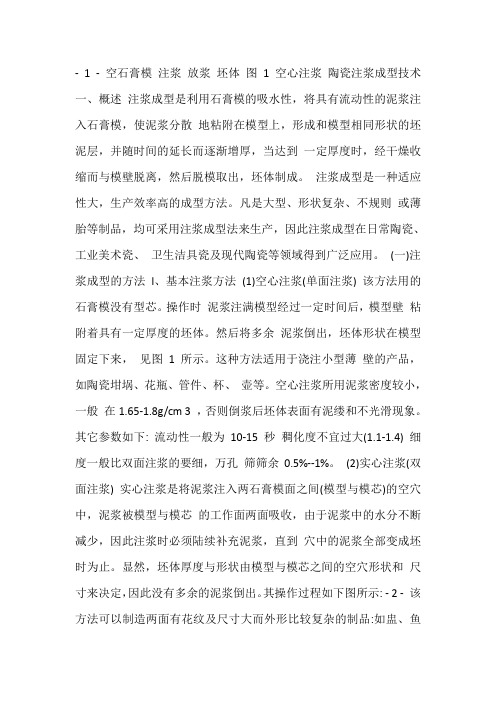
- 1 - 空石膏模注浆放浆坯体图1 空心注浆陶瓷注浆成型技术一、概述注浆成型是利用石膏模的吸水性,将具有流动性的泥浆注入石膏模,使泥浆分散地粘附在模型上,形成和模型相同形状的坯泥层,并随时间的延长而逐渐增厚,当达到一定厚度时,经干燥收缩而与模壁脱离,然后脱模取出,坯体制成。
注浆成型是一种适应性大,生产效率高的成型方法。
凡是大型、形状复杂、不规则或薄胎等制品,均可采用注浆成型法来生产,因此注浆成型在日常陶瓷、工业美术瓷、卫生洁具瓷及现代陶瓷等领域得到广泛应用。
(一)注浆成型的方法l、基本注浆方法(1)空心注浆(单面注浆) 该方法用的石膏模没有型芯。
操作时泥浆注满模型经过一定时间后,模型壁粘附着具有一定厚度的坯体。
然后将多余泥浆倒出,坯体形状在模型固定下来,见图 1 所示。
这种方法适用于浇注小型薄壁的产品,如陶瓷坩埚、花瓶、管件、杯、壶等。
空心注浆所用泥浆密度较小,一般在1.65-1.8g/cm 3 ,否则倒浆后坯体表面有泥缕和不光滑现象。
其它参数如下: 流动性一般为10-15 秒稠化度不宜过大(1.1-1.4) 细度一般比双面注浆的要细,万孔筛筛余0.5%--1%。
(2)实心注浆(双面注浆) 实心注浆是将泥浆注入两石膏模面之间(模型与模芯)的空穴中,泥浆被模型与模芯的工作面两面吸收,由于泥浆中的水分不断减少,因此注浆时必须陆续补充泥浆,直到穴中的泥浆全部变成坯时为止。
显然,坯体厚度与形状由模型与模芯之间的空穴形状和尺寸来决定,因此没有多余的泥浆倒出。
其操作过程如下图所示: - 2 - 该方法可以制造两面有花纹及尺寸大而外形比较复杂的制品:如盅、鱼盘、瓷板等。
实心注浆常用较浓的泥浆,一般密度在1.8g/cm 3 以上,以缩短吸浆时间。
稠化度(1.5 -2.2),细度可粗些,万孔筛筛余1%--2%。
2、强化注浆法为缩短注浆时间,提高注件质量,在两种基本注浆方法的基础上,形成了一些新的注浆方法,这些方法统称为强化注浆。
陶瓷高压注浆成型工艺

陶瓷高压注浆成型工艺陶瓷是一种非常重要的材料,它具有高硬度、高耐磨、高耐腐蚀等优良性能,因此被广泛应用于各种领域,如建筑、电子、化工、医疗等。
而陶瓷的制造过程中,高压注浆成型工艺是一种非常重要的工艺,它可以使陶瓷制品具有更高的密度和更好的性能。
高压注浆成型工艺是一种将陶瓷粉末和液体添加剂混合后,通过高压注入模具中,然后在高温高压下进行成型的工艺。
这种工艺可以使陶瓷制品具有更高的密度和更好的性能,同时还可以大大提高生产效率和降低成本。
高压注浆成型工艺的主要步骤包括:原料制备、混合、注浆、压制、烧结等。
其中,原料制备是非常重要的一步,它直接影响到陶瓷制品的质量和性能。
一般来说,陶瓷粉末的制备需要经过多道工序,如研磨、筛分、干燥等,以保证粉末的均匀性和细度。
而液体添加剂的制备则需要根据不同的陶瓷材料和工艺要求进行选择和调配。
混合是将陶瓷粉末和液体添加剂混合均匀的过程,这一步的目的是使粉末和液体充分结合,形成均匀的浆料。
混合的方法有很多种,如干法混合、湿法混合、球磨混合等,不同的方法适用于不同的陶瓷材料和工艺要求。
注浆是将混合好的浆料注入模具中的过程,这一步需要使用高压注浆机进行操作。
高压注浆机可以将浆料注入模具中,并在一定的时间内保持一定的压力,以保证浆料充分填充模具中的空隙。
压制是将注入模具中的浆料进行压制的过程,这一步需要使用压力机进行操作。
压力机可以将模具中的浆料进行压实,使其具有更高的密度和更好的性能。
烧结是将压制好的陶瓷制品进行高温处理的过程,这一步可以使陶瓷制品具有更高的硬度、密度和耐磨性。
烧结的温度和时间需要根据不同的陶瓷材料和工艺要求进行选择和调整。
总的来说,高压注浆成型工艺是一种非常重要的陶瓷制造工艺,它可以使陶瓷制品具有更高的密度和更好的性能,同时还可以大大提高生产效率和降低成本。
随着科技的不断发展和进步,高压注浆成型工艺也在不断地改进和完善,相信在不久的将来,它将会在更多的领域得到应用。
陶瓷新思维之缺陷分析(含注浆)

大华陶瓷杯类产品缺陷统计
大华陶瓷碟类产品缺陷统计
杯类缺陷分布图
碟类缺陷分布图
大华陶瓷应对措施
预防措施
案例总结
• 在日用陶瓷中陶瓷的装饰缺陷通过提前预防可以 达到较好的改善效果。 • 随着湿度的增大,应加强通风。若温度较低时, 应通过增大湿度以缓和湿度骤减而引起的釉裂等 缺陷的发生。缺陷控制的同时应该结合生产和人 员的管理进行,尤其随着人们环保意识的提高, 会对陶瓷装饰所用的添加剂产生一定的抵触心理 %,会在一定程度上影响产品的合格率,需要结 合一定的生产管理知识进行预防和纠正。
在此录入文字标题
(1)坯体入窑水分过高,加上预热带温度低, 碳素沉积釉中。釉的始熔温度低,釉料玻 化过早,而使沉积在釉层中的碳素不能分 解排出。 (2)坯料中碳酸盐、硫酸盐含量过高. (3)过干过热的坯体施釉,坯体与釉浆温差过 大,不能使釉料被坯体均匀吸收,导致有 些地方釉面过厚,烧成时容易封闭气孔, 使气体无法外逸。
(5)石膏模与模座不吻合
滚压常见缺陷三
产生原因
滚压成型时,滚头转速低,产生下凹花心; 滚压机转速比不合理,转速比过大则产生坯 体底心上凸的花心;滚头与模座停转时间配 合不好;热滚压成型时滚头顶部温度过高; 坯体含水率太低;泥饼在模中放置不正;使 用新模或模型与模座配合太松成型机轴承间 隙过大。
肆 瓷之物语•窑火
解决问题
• 根据结果调整了配方, 烧成有所好转。
• 请问各位问 题解决了吗?
初步结果
• 经过几次调整, 杯把把裂的情况有所好转,但 是生产不过十天又出现反复, 一直没有得到
根治。
• 因此, 技术员就大胆进行新的尝试: 用杯身 泥进行化浆注杯把的试验(行内人称之为:原 泥化浆)。
陶瓷工艺学(4.4)--注浆成型最终
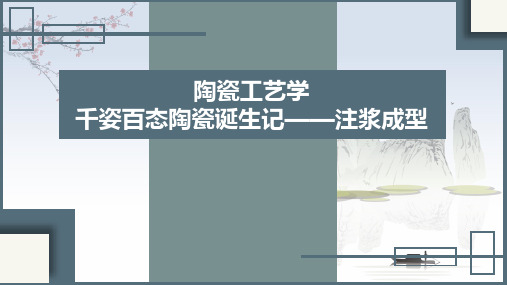
间,还可减少坯体的干燥收
为
缩和脱模后坯体的水分。注
浆压力越高,成型速度越大
生坯强度越高,但是受模型
强度的限制。模型材料可以
采用石膏模型、多孔树脂模
型和无机填料模型。
微压注浆 一般压力在0.05MPa以下 中压注浆 一般压力在0.15MPa——0.20MPa之间 高压注浆 一般压力在0.20MPa以上
单面注浆 双面注浆
压力注浆 真空注浆 离心注浆
其他注浆成型 方法
热压铸成型
成组注浆
热浆注浆
4.4 注浆成型方法
单面注浆
将泥浆注入模型中,待泥浆在模型中停留一段时间,形成所需注件厚度 时,倒出多余泥浆,随后带模干燥,待注件干燥收缩后脱模,取出注件。
单面注浆操作示意图
4.4.1 基本注浆方 法
双面注浆
本节课主要内容
4.1、
注浆过程Leabharlann 4.2、注浆成型的特点
4.3、
注浆成型对泥料的要求
4.4、
注浆方法
4.1 注浆过程
第一阶段
从泥浆注入 石膏模吸入开 始到形成薄泥 层;
第二阶段
形成薄泥层 后,泥层逐渐 增厚,知道形 成注件;
第三阶段
从雏坯成型 后到脱模为收 缩脱模阶段;
4.1 注浆过程
为了提高注浆速率,通常从以下三种方式:
陶瓷工艺学 千姿百态陶瓷诞生记——注浆成型
课程导入
川剧变脸
川剧脸谱,是川剧表演艺术中重要的组成部分,是历代川剧艺人 共同创造并传承下来的艺术瑰宝。
川剧《白蛇传》中的许仙
川剧变脸大师
课程导入
千姿百态陶瓷诞生记
泥浆
石膏模具
百态陶瓷
课程导入
陶瓷注浆成型技术

空石膏模 注浆 放浆 坯体 图1空心注浆陶瓷注浆成型技术一、概述注浆成型是利用石膏模的吸水性,将具有流动性的泥浆注入石膏模内,使泥浆分散 地粘附在模型上,形成和模型相同形状的坯泥层,并随时间的延长而逐渐增厚,当达到 一定厚度时,经干燥收缩而与模壁脱离,然后脱模取出,坯体制成。
注浆成型是一种适应性大,生产效率高的成型方法。
凡是大型、形状复杂、不规则 或薄胎等制品,均可采用注浆成型法来生产,因此注浆成型在日常陶瓷、工业美术瓷、 卫生洁具瓷及现代陶瓷等领域得到广泛应用。
(一)注浆成型的方法l 、基本注浆方法(1)空心注浆(单面注浆)该方法用的石膏模没有型芯。
操作时泥浆注满模型经过一定时间后,模型内壁粘附着具有一定厚度的坯体。
然后将多余泥浆倒出,坯体形状在模型内固定下来,见图1所示。
这种方法适用于浇注小型薄壁的产品,如陶瓷坩埚、花瓶、管件、杯、壶等。
空心注浆所用泥浆密度较小,一般在1.65—1.8g/cm 3,否则倒浆后坯体表面有泥缕和不光滑现象。
其它参数如下:流动性一般为10—15秒稠化度不宜过大(1.1—1.4)细度一般比双面注浆的要细,万孔筛筛余0.5%--1%。
(2)实心注浆(双面注浆)实心注浆是将泥浆注入两石膏模面之间(模型与模芯)的空穴中,泥浆被模型与模芯 的工作面两面吸收,由于泥浆中的水分不断减少,因此注浆时必须陆续补充泥浆,直到穴中的泥浆全部变成坯时为止。
显然,坯体厚度与形状由模型与模芯之间的空穴形状和尺寸来决定,因此没有多余的泥浆倒出。
其操作过程如下图所示:该方法可以制造两面有花纹及尺寸大而外形比较复杂的制品:如盅、鱼盘、瓷板等。
实心注浆常用较浓的泥浆,一般密度在1.8g/cm3以上,以缩短吸浆时间。
稠化度(1.5—2.2),细度可粗些,万孔筛筛余1%--2%。
2、强化注浆法为缩短注浆时间,提高注件质量,在两种基本注浆方法的基础上,形成了一些新的注浆方法,这些方法统称为强化注浆。
强化注浆主要有以下几种:(1)压力注浆采用加大泥浆压力的方法来加速水分扩散,从而加速吸浆速度。
陶瓷注浆成型技术
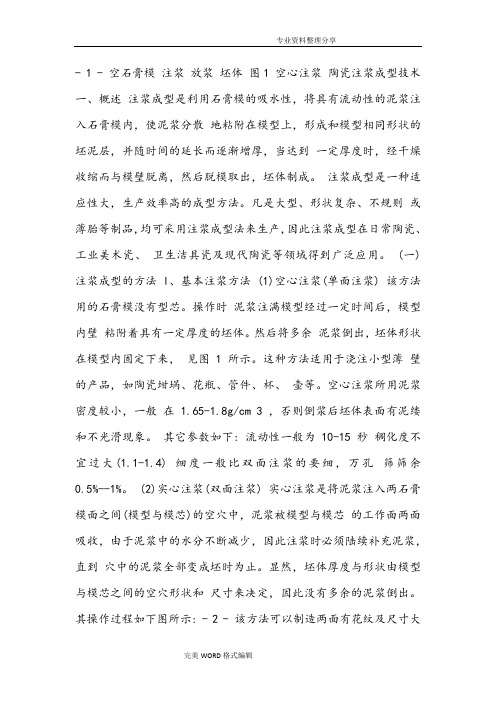
- 1 - 空石膏模注浆放浆坯体图1 空心注浆陶瓷注浆成型技术一、概述注浆成型是利用石膏模的吸水性,将具有流动性的泥浆注入石膏模内,使泥浆分散地粘附在模型上,形成和模型相同形状的坯泥层,并随时间的延长而逐渐增厚,当达到一定厚度时,经干燥收缩而与模壁脱离,然后脱模取出,坯体制成。
注浆成型是一种适应性大,生产效率高的成型方法。
凡是大型、形状复杂、不规则或薄胎等制品,均可采用注浆成型法来生产,因此注浆成型在日常陶瓷、工业美术瓷、卫生洁具瓷及现代陶瓷等领域得到广泛应用。
(一)注浆成型的方法 l、基本注浆方法 (1)空心注浆(单面注浆) 该方法用的石膏模没有型芯。
操作时泥浆注满模型经过一定时间后,模型内壁粘附着具有一定厚度的坯体。
然后将多余泥浆倒出,坯体形状在模型内固定下来,见图 1 所示。
这种方法适用于浇注小型薄壁的产品,如陶瓷坩埚、花瓶、管件、杯、壶等。
空心注浆所用泥浆密度较小,一般在 1.65-1.8g/cm 3 ,否则倒浆后坯体表面有泥缕和不光滑现象。
其它参数如下: 流动性一般为10-15 秒稠化度不宜过大(1.1-1.4) 细度一般比双面注浆的要细,万孔筛筛余0.5%--1%。
(2)实心注浆(双面注浆) 实心注浆是将泥浆注入两石膏模面之间(模型与模芯)的空穴中,泥浆被模型与模芯的工作面两面吸收,由于泥浆中的水分不断减少,因此注浆时必须陆续补充泥浆,直到穴中的泥浆全部变成坯时为止。
显然,坯体厚度与形状由模型与模芯之间的空穴形状和尺寸来决定,因此没有多余的泥浆倒出。
其操作过程如下图所示: - 2 - 该方法可以制造两面有花纹及尺寸大而外形比较复杂的制品:如盅、鱼盘、瓷板等。
实心注浆常用较浓的泥浆,一般密度在1.8g/cm 3 以上,以缩短吸浆时间。
稠化度(1.5 -2.2),细度可粗些,万孔筛筛余1%--2%。
2、强化注浆法为缩短注浆时间,提高注件质量,在两种基本注浆方法的基础上,形成了一些新的注浆方法,这些方法统称为强化注浆。
工艺学实验报告-注浆成型制作陶瓷工艺品

工艺学实验报告-注浆成型制作陶瓷工艺品第一篇:工艺学实验报告 - 注浆成型制作陶瓷工艺品注浆成型制作陶瓷工艺品一、实验目的1.应用《无机非金属材料工学》课程中所学的陶瓷工艺理论,认识原料,并确定原料组成及配比范围。
2.掌握简易石膏模具的制做方法,通过注浆成型制作陶瓷工艺品的流程。
3.以小组为单位制作一件陶瓷工艺品。
4.能对烧后制品的缺陷作合理的分析,在此基础上通过改善制备条件,获得优良的工艺品。
二、实验原理及步骤1.原料:建筑石膏:做石膏模具时使用。
钾长石:为肉红色,当块度较大时,经破碎、球磨、过筛后备用。
石英砂:白色,夹杂时带黄色。
经破碎、球磨、过筛后备用。
紫木节:为软质粘土,紫色。
可分散在水中。
大同土:为硬质粘土,白色。
经破碎、球磨、过筛后备用。
滑石:为白色。
无水碳酸钠:白色。
2.仪器及设备:电子天平,振动磨,球磨瓷瓶(带鹅卵石),空桶(陈腐料浆用),比重计,石膏模具(带捆绑绳),烧杯,小刀(或锯条),烧结炉3.步骤:①称料:总量:1kg,石英:25%,长石:27%,紫木节:22%,大同土:24%,滑石:2%,无水碳酸钠(外加):0.4%,料:水=1 :1②球磨:料:水:球=1 :1 :2(24h)③陈腐:陈腐一周。
④测比重:用比重计测定料浆比重。
⑤成型:将石膏模具组装后捆紧,从注浆口倒入搅拌均匀的泥浆,等坯体到达一定厚度后,将多于的泥浆倒出,放置4-8h。
⑥脱模:当湿坯具有一定强度后,解开模具捆绑绳,平放在桌子上,脱模。
⑦干燥:自然干燥湿坯至坯体颜色发白且具有一定强度。
⑧修坯:用小刀或锯条钝面将坯体表面凸凹不平的部分修理平整。
⑨烧成:自定烧成制度。
⑩缺陷分析:分析制品缺陷并提出解决方案以完善制备条件。
石膏模具的制作:①根据成型品的大致形状折纸模型。
②配制少量石膏浆,80%左右水,待粘稠后倒入纸模型中以粘住底部,防止漏浆。
③依据纸模型体积称量石膏粉,85%左右水,混匀并使气泡尽可能少。
粘稠后倒入纸模型内。
陶瓷注浆成型工艺

陶瓷注浆成型工艺嘿,朋友们!今天咱来聊聊陶瓷注浆成型工艺这玩意儿,可有意思啦!你想想看啊,那原本普普通通的泥浆,就像变魔术一样,能变成各种精美的陶瓷制品。
这可不是一般的神奇呀!陶瓷注浆成型呢,就像是给泥浆安了个家。
先得准备好模具,这模具就好比是个小房子,等着泥浆住进去呢。
把泥浆小心翼翼地倒进模具里,看着它慢慢地填满每一个角落,就好像给小房子穿上了一件特别的衣服。
然后呢,就得等啦!等泥浆在模具里安安稳稳地待上一段时间,让它慢慢凝固成型。
这过程就像是在等待一朵花慢慢开放,需要点耐心呢。
等泥浆凝固得差不多了,就可以把模具打开啦!哇哦,这时候你就能看到初步成型的陶瓷啦,虽然还带着点粗糙,但已经有模有样啦!不过,这可还没完事儿呢。
接下来还得给它精心修整一番,把那些不平整的地方打磨打磨,让它变得更加光滑细腻。
这就像是给一个小孩子梳妆打扮,要让它漂漂亮亮的。
你说这陶瓷注浆成型工艺是不是很有趣呀?就好像是在创造一个个小生命一样。
而且啊,通过这种方法可以做出各种各样的形状和图案,那可真是只有你想不到,没有它做不到。
你看那些摆在商店里精美的陶瓷制品,说不定就是通过陶瓷注浆成型工艺做出来的呢。
它们曾经也是普普通通的泥浆呀,经过这么一番奇妙的旅程,就变成了让人爱不释手的宝贝。
咱再想想,要是没有陶瓷注浆成型工艺,那我们的生活得少多少乐趣呀?那些漂亮的花瓶、精致的碗碟,不就都没啦?那多可惜呀!所以说呀,陶瓷注浆成型工艺可真是个了不起的发明呢!它让我们的生活变得更加丰富多彩,让我们能享受到陶瓷带来的美好。
怎么样,朋友们,是不是对陶瓷注浆成型工艺有了更深的了解呀?下次再看到那些漂亮的陶瓷制品,可别忘了它们背后的神奇工艺哦!。
- 1、下载文档前请自行甄别文档内容的完整性,平台不提供额外的编辑、内容补充、找答案等附加服务。
- 2、"仅部分预览"的文档,不可在线预览部分如存在完整性等问题,可反馈申请退款(可完整预览的文档不适用该条件!)。
- 3、如文档侵犯您的权益,请联系客服反馈,我们会尽快为您处理(人工客服工作时间:9:00-18:30)。
陶瓷注浆成型工艺要点及缺陷分析
一、陶瓷注浆成型工艺要点
注浆成型是一种适应性广、生产效率高的成型方法,凡是形状复杂或不规则、不能用其他方法成型以及薄胎制品都可用注浆成型来生产但是由于温、湿度对坯体成型影响较大,直接关系到半成品的质量和成品率的高低,所以生产时必须对环境温度、湿度进行严格的控制以及季节的变化采取相应的措施。
1、对石膏模型的要求
(1)设计合理,易于脱模,各部位及吸水均匀,能保证坯体收缩一致。
(2)孔隙率和吸水率适度,比可塑成型模型略大。
(3)模型的湿度要严格控制,一般应保持5%左右的吸水率,过干会引起坯体开裂;过湿会延长注浆时间,甚至难于成型。
2、对泥浆性能的要求
为了提高注浆生产效率,并获得高质量的坯件,要求泥浆具有良好的性能。
(1)流动性好,要求泥浆在含水率较低的情况下粘度小,倾注时泥浆流出一根连绵不断的细线,使之容易流动到模型的各部位。
(2)稳定性好,要求泥浆中的瘠性原料不沉淀,即悬浮性好,使成型后的坯体各部位组织均匀。
(3)触变性适宜,即粘度不宜过大。
(4)渗透性好,即过滤性好,要求泥浆中的水分能顺利通过粘附在模壁上的泥层而被石膏吸收。
(5)不含气泡,以利于增加坯体的强度。
一、注浆成型生产对环境温度、湿度的要求
3、对环境温度、湿度的要求
注浆成型的卫生瓷操作的温度一般控制在25度—37度为好,夜间的温度可以提高一些,但也不能超过50度,因为超过50度,一方面坯体的外表面干燥速度过快,而坯体内表面的干燥速度则相对较慢,造成坯体在干燥过程中内外收缩不均,导致坯体在干燥过程中开裂;另一方面温度超过50度容易使石膏模过干、过热,而且石膏模形状复杂,各部分干湿度不均,在成型过程中很容易造成吃浆过快以及成型后坯体气孔率增大等缺陷。
成型操作的湿度一般控制在50-70%,过高则坯体的干燥速度太慢,影响下道工序的正常进行,过低坯体干燥速度加快,收缩速度也在加快,容易产生开裂,特别是成型复杂的产品在应力集中的部位,开裂更加严重。
4.注浆成型的坯体对季节的要求
注浆成型的坯体质量对季节的变化比较敏感,特别是春秋季节对坯体成型影响最大。
因为春秋季节风比较大,空气又比较干燥,在这样的条件下,如果不采取合理的措施,坯体在成型阶段就造成大面积的风裂,严重影响坯体的收成率。
主要原因是风不可能均匀地吹到坯体的各个部位,造成坯体各个部位干燥不均匀,局部收缩过快而产生开裂。
因此,春秋季节坯体成型要注意的问题是:
(1)成型车间不能开窗户,门上要挂门帘,避免外面的风直接吹到室内的坯体上,必要时可以用薄膜全部将坯体盖起来,这样在干燥过程中收缩均匀。
(2)春秋季节要经常在成型操作室内四周喷洒一些水,喷水的目的是增加室内的湿度。
喷洒水量要求刚进入春秋季节时少喷洒,慢慢地增多,在接近夏季和冬季时慢慢减少,但要注意阴、雨天要少喷洒甚至不洒水。
夏季风比较小,湿度较大,室内不要喷洒水可以开窗户。
冬季一定要把窗户缝糊好,保证室内温度。
因此,在生产过程中根据季节的变化采取相应的保护措施以及控制好生产环境的温度和湿度,对提高产品质量和收成率是十分有益的。
二、陶瓷注浆成型缺陷分析
1、气孔与针眼
(1)泥浆的流动性差,粘度大,致使泥浆中的气泡不易排出。
(2)泥浆未经陈腐,或电解质种类及用量不当。
(3)搅拌泥浆太剧烈,或注浆速度太快,使泥浆中夹有气泡,或泥浆真空脱泡处理不严。
(4)石膏模过湿、过干、过旧,或模型表面沾有灰尘。
2、泥缕
主要原因是泥浆的粘度大,流动性差,或因倾浆操作不当,或模型工作面沾有浆滴。
还有一种情况,因进浆时集中于模型内某一局部,由于泥浆的冲击而形成这一局部颗粒取向排列不同,致使干燥收缩时隆起成筋状,即使经过车修或用刀削平,烧后仍有明显的泥缕。
3、开裂
(1)泥浆配方不当;
(2)陈腐不足、不均;
(3)操作不当、厚薄坯;
(4)脱模太早或太迟;
(5)接坯的双部分干湿不一致。
4、变形
(1)泥浆水分太高,干燥收缩过大。
(2)泥浆混合不匀,干燥收缩不一。
(3)倾浆操作不当,坯体厚薄不匀。
(4)模型过湿,或脱模过早,出模操作不当,湿坯没有放平、放正。