V带轮设计计算公式
皮带轮速比计算公式
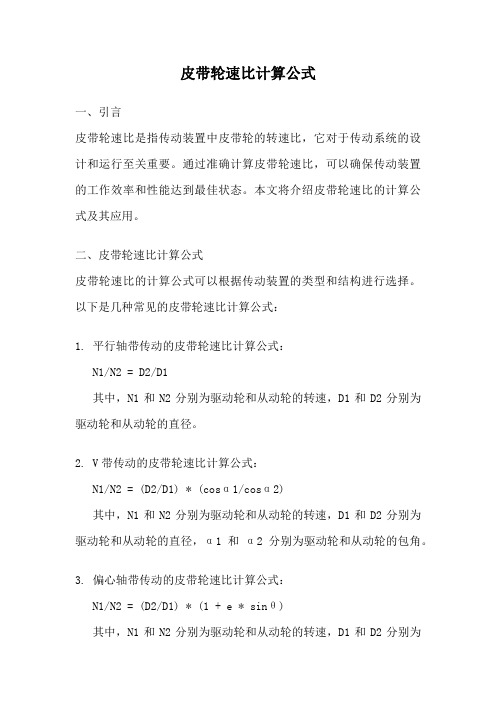
皮带轮速比计算公式一、引言皮带轮速比是指传动装置中皮带轮的转速比,它对于传动系统的设计和运行至关重要。
通过准确计算皮带轮速比,可以确保传动装置的工作效率和性能达到最佳状态。
本文将介绍皮带轮速比的计算公式及其应用。
二、皮带轮速比计算公式皮带轮速比的计算公式可以根据传动装置的类型和结构进行选择。
以下是几种常见的皮带轮速比计算公式:1. 平行轴带传动的皮带轮速比计算公式:N1/N2 = D2/D1其中,N1和N2分别为驱动轮和从动轮的转速,D1和D2分别为驱动轮和从动轮的直径。
2. V带传动的皮带轮速比计算公式:N1/N2 = (D2/D1) * (cosα1/cosα2)其中,N1和N2分别为驱动轮和从动轮的转速,D1和D2分别为驱动轮和从动轮的直径,α1和α2分别为驱动轮和从动轮的包角。
3. 偏心轴带传动的皮带轮速比计算公式:N1/N2 = (D2/D1) * (1 + e * sinθ)其中,N1和N2分别为驱动轮和从动轮的转速,D1和D2分别为驱动轮和从动轮的直径,e为偏心率,θ为偏心角。
三、皮带轮速比的应用皮带轮速比的计算结果可以用于传动装置的设计和优化。
通过合理选择皮带轮的直径和转速,可以实现传动装置的速度调节和输出扭矩的控制。
此外,皮带轮速比还可以用于计算传动装置的传动比,为其他工程计算提供依据。
四、注意事项在计算皮带轮速比时,需要注意以下几点:1. 确保输入的参数准确无误,包括驱动轮和从动轮的直径、转速、包角等。
2. 根据具体的传动装置类型选择合适的计算公式。
3. 考虑传动装置的实际工作环境和条件,对速比进行合理的调整和优化。
4. 在计算过程中,可以借助计算机软件或在线计算工具来提高计算的准确性和效率。
五、结论皮带轮速比是传动装置设计中的重要参数,它对传动装置的工作效率和性能有着直接影响。
本文介绍了几种常见的皮带轮速比计算公式,并指出了其在传动装置设计和优化中的应用。
在实际应用中,我们应该根据具体情况选择合适的计算公式,并注意参数的准确性和实用性。
【温故而知新】V带传动的设计计算步骤
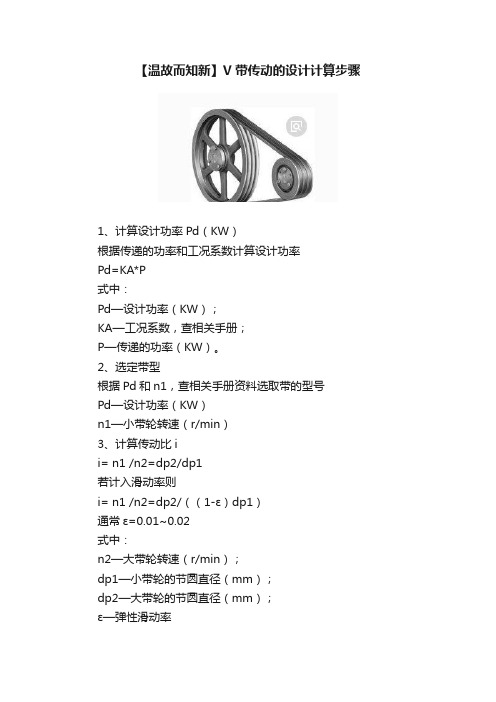
【温故而知新】V带传动的设计计算步骤1、计算设计功率Pd(KW)根据传递的功率和工况系数计算设计功率Pd=KA*P式中:Pd—设计功率(KW);KA—工况系数,查相关手册;P—传递的功率(KW)。
2、选定带型根据Pd和n1,查相关手册资料选取带的型号Pd—设计功率(KW)n1—小带轮转速(r/min)3、计算传动比ii= n1 /n2=dp2/dp1若计入滑动率则i= n1 /n2=dp2/((1-ε)dp1)通常ε=0.01~0.02式中:n2—大带轮转速(r/min);dp1—小带轮的节圆直径(mm);dp2—大带轮的节圆直径(mm);ε—弹性滑动率通常带轮的节圆直径(符号:dp)可视为基准直径(符号:dd)4、选取小带轮的基准直径:查相关手册选定dd1的大小。
为提高V带的寿命,宜选取较大的直径。
5、计算大带轮的基准直径:Dd2=i*(1-ε)*dd1计算出dd2的数值后,应根据相关手册选取标准值6、计算带速v(m/s)(带速:5~25m/s)V=ㄫ* dp1* n1/60/1000≤Vmax普通V带 Vmax=25~30窄V带 Vmax=35~40注:一般v不得低于5m/s,为充分发挥V带的传动能力,应使v≈20m/s。
7、初定轴间距a0(mm)0.7(dd1+ dd2)≤a0<2(dd1+ dd2)注:或根据结构要求选定。
8、所需基准长度Ld0(mm)Ld0=2 *a0+ㄫ*(dd1+ dd2)/2+(dd2- dd1)2/4/ a0计算出带基准长度Ld0后,根据供应商样本,选择最接近Ld对有效宽度值V带,按有效直径计算所需带长度由相关样本选相近带长。
9、计算实际中心距a(mm)a≈a0+(Ld- Ld0)/2安装时所需最小轴间距:amin=a-0.015Ld张紧或补偿伸长所需最大轴间距:amax=a+0.03 Ld10、计算小带轮包角ɑ1(°)ɑ1=180°-(dd2- dd1)/a*57.3°注:带轮包角要大于120°,如ɑ1较小,应增大a、减小传动比或用张紧轮11、单根V带传递的额定功率P1(kw)根据带型、dd1和n1查相关样本选取。
(完整版)V带轮设计计算公式

工况系数KA= 1.3传递功率P=75kw
设计功率Pd=
97.5kw 1480r/min 925r/min
传动比 i =
n1/n2= 1.6小轮直径
d1=250mm
滑动率ε=0.01大轮直径
d2=
396mm 大带轮转速 n2=925
r/min
带速v=试选dP2=d2=400mm 求出
v=19.4
m/s
455≤a0﹤
1300选择a0=
900mm V带基准长度Ld0=2826.8mm 选取基准长度Ld=2800mm 实际轴间距a=886.6mm 最小轴间距: a min=844.6mm 最大轴间距: aman=886.7mm
小带轮包角a1=170.3根据d1和n1查得V带 P1=15.07kw 额定功率的增量△P1=0.00kw
小轮包角修正系数Ka=0.98带长修正系数KL=0.96根数z= 6.9根选取z=7根V带质量m=0.2kg/m 单根V带的预紧力F0=632.8N 作用在轴上的力
F r =8106.8
N
注意:绿色部分为手工输入或
查表输入或选值输入
πd P1n 1/60×1000≤νmax 普通V带νmax=25~30,窄V带νmax=35~40V带轮设计计算公式
一,求设计功率 P d 二.传动比 i 小带轮转速 n 1=大带轮转速 n 2=三.选定小轮基准直径 d 1:四,计算大轮基准直径d 2:五, n 2实际转速六, 带速ν十三, 单根V带的预紧力: F 0十四, 作用在轴上的力: F r
七, 初定轴间距: a 0
八, 所需V带的基准长度: L d0九,实际轴间距: a 十, 小带轮包角: α1十一, 单根V带的基本额定功率:P1十二, V带的根数:。
V带传动的设计计算

V带传动的设计计算序 号计算项目符 号单 位计算公式和参数选定说明P—传递的功率(kW);KA —工况系数,见表V 带传动的工况系数KA2选定带型根据P d 和n 1由图a 或图b 选取n 1—小带轮转速(r/min)n 2—大带轮转速(r/min);d p1—小带轮的节圆直径(mm);d p2—大带轮的节圆直径(mm);若计入滑动率ε—弹性滑动率通常带轮的节圆直径可视为基准直径通常ε=0.01~0.024小带轮的基准直径d d1mm 按表V 带轮的基准直径系列和表最小带轮直径选定为提高V 带的寿命,宜选取较大的直径5大带轮的基准直径d d2mmd d2=id d1(1-ε)dd2应按表V 带轮的基准直径系列选取标准值普通V带 υmax =25~30窄V带 υmax =35~40m/s6带速υP d =K A P1设计功率P dkW一般υ不得低于5m/s 为充分发挥V带的传动能力,应使υ≈20m/s3传动比i7初定轴间距a 0mm 0.7(d d1+d d2) ≤a 0<2(d d1+d d2)或根据结构要求定a min —安装时所需最小轴间距;a max —张紧或补偿伸长所需最大轴间距;a min =a -(2b d +0.09L d )b d —基准宽度a max =a +0.02L d11单根V 带传递的基本额定功率P 1kW根据带型、dd1和n1查表Y 、Z 、A 、B 、C 、D 、E 、型V 带的额定功率和SPZ 、SPA 、SPB 、SPC 型窄V带的额定功率P 1是α=180°、载荷平稳时,特定基准长度的单根V 带基本额定功率(GBT 13575.1-2008普通和窄V 带传动第1部分:基准宽度制)12传动比i≠1的额定功率增量△P 1kW根据带型、n1和i 查表Y 、Z 、A 、B 、C 、D 、E 、型V 带的额定功率和SPZ 、SPA 、SPB 、SPC 型窄V 带的额定功率Ka —小带轮包角修正系数,见表小带轮包角修正系数Ka KL —带长修正系数,见表带长修正系数KL16带轮的结构和尺寸14单根V带的预紧力15作用在轴上的力F rNF 0N 如a 1较小,应增大a 或用张紧轮m —V 带每米长的重量(kg/m),见表V 带每米长的重量13V带的根数z小带轮包角a 1(°)9实际轴间距a mm10由表普通V 带的基准长度系列和表窄V 带基准长度选取相近的L d 8所需基准长度L d0mm。
普通V带设计计算说明书

机械设计课程——普通V带设计计算说明书目录一、V带传动的设计计算 (1)1)已知条件和设计容 (1)2)设计步骤和方法 (1)①确定计算功率 (1)②选择V带的带型 (1)③确定带基准直径dd并验算带速v (1)④确定中心距a,并选择V带的基准长度Ld (2)⑤验算小带轮上的包角 (3)⑥确定带的根数z (3)⑦计算单根V带的初拉力的最小值(F0)min (4)⑧计算压轴力Fp (4)二、V带轮的设计 (4)1).V带轮的设计容 (4)2).V带轮的材料 (4)3).V带轮的结构形式 (5)三、各零件及装配图 (5)小带轮零件图 (5)大带轮零件图 (6)机架零件图 (6)轴零件图 (7)装配图 (7)设计容和要求:一、V带传动的设计计算1)已知条件和设计容设计V带传动时的已知条件包括:带传动的工作条件(载荷变动微小);传动位置与总体尺寸限制;所需传递的额定功率P=3kw;小带轮转速n1=960r/min;大带轮转速n2或传动比i=2。
设计容包括选择带的型号、确定基准长度、根数、中心距、带轮的材料、基准直径以及结构尺寸、初拉力和压轴力、紧装置等。
2)设计步骤和方法①确定计算功率计算功率Pca是根据传递的功率P和带的工件条件而确定的Pca =KAP=1.1×3=3.3KW式中:Pca——计算功率,KW;KA ——工作情况系数,查表得KA=1.1P——所需传递的额定功率,如电动机的额定功率或名义的负载功率,kw。
②选择V带的带型根据计算功率Pca 和小带轮转速n1,从图8-11选取普通V带的带型。
选择V带的带型是:A型③确定带基准直径dd并验算带速v1. 初选小带基准直径dd1根据V带的带型,参考表8-6和表8-8确定小带轮的基准直径dd1,应使min1)(d d d d ≥。
d d1=112mm2. 验算带速v 根据式sm n d v d /6.5100060960112100060111=⨯⨯⨯=⨯⋅⋅=ππ带速不宜过低或过高,一般应使v=5~25m/s,最高不超过30m/s 。
V带传动的设计计算

V带传动的设计计算设计计算是指根据给定的参数和条件,计算出V带传动所需的各种尺寸和性能指标。
V带传动是一种常见的传动方式,广泛应用于各种机械设备中,如风机、水泵、发电机等。
下面将详细介绍V带传动的设计计算内容。
1.功率计算首先需要根据传动装置的输入和输出功率来计算V带传动所能传输的功率。
功率计算公式为:P=(T₁-T₂)×ω,其中P为功率,T₁和T₂为传动装置的转矩,ω为角速度。
根据输入和输出轴的转速、转矩以及效率,可以计算出传动装置的输入和输出功率。
2.带速计算带速是指带传动时带的线速度,常用单位为m/s。
带速计算公式为:V=π×D×n,其中V为带速,D为驱动轮的直径,n为驱动轮的转速。
根据传动装置的转速和直径,可以计算出V带传动的带速。
3.力计算对于V带传动来说,力是计算中的重要指标,既要满足传动所需的驱动力,又要确保带的正常工作。
力的计算公式为:F=T×K,其中F为力,T为带的拉紧力,K为带的侧压系数。
根据带的拉紧力和侧压系数,可以计算出V带传动所需的力。
4.弯曲应力计算弯曲应力是指带在受力时产生的弯曲应力,对带的弯曲疲劳寿命和使用寿命有重要影响。
弯曲应力计算公式为:σ=f×z×y,其中σ为弯曲应力,f为受力系数,z为带的截面形状系数,y为受力位置系数。
根据受力系数、带的截面形状系数和受力位置系数,可以计算出V带传动所产生的弯曲应力。
5.带长计算带长是指带传动时带的周长,常用单位为mm。
带长计算公式为:L = 2 × (C + π × (D₁ + D₂) / 2) ,其中L为带长,C为中心距,D₁和D₂为驱动轮和从动轮的直径。
根据中心距和驱动轮和从动轮的直径,可以计算出V带传动所需的带长。
除了以上的计算内容,还需要注意V带传动的自动对中和拼接长度等问题,并根据实际应用情况选择合适的带型、带宽和驱动轮和从动轮的材料,以及进行带的张紧和对中调整。
机械设计V带传动设计及其计算

机械设计V带传动设计及其计算V带传动是一种常见的机械传动方式,广泛应用于各种机械设备中。
其主要优点是结构简单,传动效率高,能够传递较大的功率,并且具有噪音小、寿命长等优点。
下面将详细介绍V带传动的设计及计算方法。
首先需要确定V带传动的工作条件,包括传动比、传动功率以及工作速度等。
根据这些工作条件,可以选择合适的V带型号和尺寸。
目前市场上常见的V带型号有Z、A、B、C、D等,它们的截面形状不同,也适用于不同的传动功率范围。
根据工作条件,选择合适的V带型号和尺寸是设计的第一步。
黏着力=功率/带速其中,黏着力的单位是牛顿(N),功率的单位是瓦特(W),带速的单位是米/秒(m/s)。
根据黏着力的计算结果,可以选择合适的V带张紧力。
一般情况下,V带的张紧力为传动黏着力的1.7倍。
然后需要计算V带的张紧力。
张紧力是指保持V带传动紧密连接的力,用来防止滑动和跳齿。
张紧力的计算公式如下:张紧力=动力传递功率/带速其中,张紧力的单位是牛顿(N),传递功率的单位是瓦特(W),带速的单位是米/秒(m/s)。
根据张紧力的计算结果,可以选择合适的张紧轮直径和张紧力调整装置。
最后需要计算V带的寿命,并根据寿命选择合适的V带材料和质量。
V带的寿命可以根据以下公式计算:寿命=(C×10^6)/(P×v)其中,寿命的单位是小时(h),C是V带的寿命系数(一般为1000-4000),P是传动功率的单位(kW),v是带速的单位(m/s)。
根据寿命的计算结果,可以选择合适的V带材料和质量。
综上所述,V带传动的设计及计算包括选择合适的V带型号和尺寸、计算黏着力和张紧力、选择合适的张紧轮直径和张紧力调整装置,以及计算V带的寿命并选择合适的材料和质量。
这些步骤可以确保V带传动在工作过程中能够稳定可靠地传递功率,延长传动寿命。
普通V带轮结构和尺寸设计

V带轮结构和尺寸设计一、带轮的材料带轮材料多采用灰铸铁,牌号一般选用HT150或HT200,也可选用钢、铝或非金属材料(塑料、木材)。
铸铁带轮允许的最大圆周速度为25m/s,速度更高时,可采用铸钢或钢板冲压而成。
二、V带轮槽的截面尺寸普通V带轮的轮槽截面如图所示,其各部分尺寸见表3。
轮槽角φ的极限偏差:Y、Z、A、B型为±1°;C、D、E型为±30′。
槽间距e的极限偏差适用于任何两个轮槽对称中心面的距离。
(表1)普通V带轮槽截面尺寸三、V带轮的基本结构型式及尺寸带轮由轮缘、轮毂和轮辐组成。
按轮辐结构的不同分为以下四种基本型式:S型——实心带轮:d d≤ (2.5~3) d0时选用;P型——辐板带轮:d d ≤ 300mm时选用;H型——孔板带轮:d d ≤ 300mm但轮毂和轮缘之间的距离超过100mm时选用;E型——椭圆轮辐带轮:d d>300mm选用。
S-I型S-II型P-I型P-II型P-III型P-IV型d d为基准直径;d a为外径;d0为毂孔直径;d1为轮毂直径。
注:H型带轮轮毂结构参照P型带轮。
各型带轮工作表面的粗糙度Ra的极限值参照本图。
E-I型E-II型E-III型E-IV型S型(实心带轮)P型(辐板带轮)H型(孔板带轮)E型(椭圆轮辐带轮)(表4)V带轮的结构形式和辐板厚度四、带轮的技术要求1、轮毂孔直径d0公差多取H7或H8;2、轮毂长度L的上偏差为IT14,下偏差为零;3、带轮几何公差见有关标准;4、轮槽工作表面不应有砂眼、气孔;5、轮辐及轮毂不应有缩孔和较大的凹陷;6、带轮外缘棱角要倒圆和倒钝。
- 1、下载文档前请自行甄别文档内容的完整性,平台不提供额外的编辑、内容补充、找答案等附加服务。
- 2、"仅部分预览"的文档,不可在线预览部分如存在完整性等问题,可反馈申请退款(可完整预览的文档不适用该条件!)。
- 3、如文档侵犯您的权益,请联系客服反馈,我们会尽快为您处理(人工客服工作时间:9:00-18:30)。
V带基准长度
Ld0=
2826.8
选取基准长度
Ld=
2800
九,实际轴间距: a
实际轴间距
a=
886.6
最小轴间距: amin=
844.6
最大轴间距: aman=
十, 小带轮包角: α1
小带轮包角
a1=
886.7 170.3
十一, 单根V带的基本额定功率:P1
根据d1和n1查得V带 P1=
15.07
额定功率的增量△P1=
mm
mm r/min
mm m/s
mm mm mm mm mm mm
kw kw
根 根 kg/m N N
大轮直径
d2=
396
五, n2实际转速
大带轮转速 n2=
925
六, 带速ν 带速v= 选
πdP1n1/60×1000≤νmax
dP2=d2=
400
求出
v=
19.4
普通V带νmax=25~30,
窄V带νmax=35~40
七, 初定轴间距: a0
455 ≤a0﹤
1300
选择a0=
900
八, 所需V带的基准长度: Ld0
0.00
十二, V带的根数:
小轮包角修正系数
Ka=
0.98
带长修正系数
KL=
0.96
根数
z=
6.9
选取
z=
7
十三, 单根V带的预紧力: F0
V带质量
m=
0.2
单根V带的预紧力
F0=
632.8
十四, 作用在轴上的力: Fr
作用在轴上的力
Fr=
8106.8
注意:绿色部分为手工输入或 查表输入或选值输入
kw kw r/min r/min
V带轮设计计算公式
一,求设计功率 Pd
工况系数
KA=
1.3
传递功率
P=
75
设计功率
Pd=
97.5
二.传动比 i 小带轮转速 n1= 大带轮转速 n2=
传动比 i = 三.选定小轮基准直径 d1:
小轮直径 四,计算大轮基准直径d2:
滑动率
n1/n2= d1= ε=
1480 925 1.6
250
0.01