隧道内盾构机刀盘主驱动齿圈的修复技术
盾构机刀盘磨损的修复工艺探讨

盾构机刀盘磨损的修复工艺探讨摘要:在我国经济建设飞速发展的现阶段,基建工程在数量与规模方面均有所增长,所以不可避免的会用到机械化盾构机来开展相关建设活动。
在机械化盾构机当中,刀盘作为掘削机构在其中有着重要作用,例如,开挖地层、保持开挖面的稳定等,同时也因此需要承载较大的载荷与力矩,所以也因此容易出现磨损情况,导致工程建设的施工效率受到影响。
所以,本文重点分析盾构机刀盘磨损的修复工艺。
关键词:盾构机;刀盘;磨损;修复工艺引言:在隧道施工期间,需要使用盾构机来完成土体的开挖以及渣土的排运等工作,确保隧道施工可以快速的完成。
现阶段,随着现代科学技术的不断进步,机械化盾构机在相关隧道工程中得到了广泛的应用,并且应用效果十分显著。
在机械化盾构机工作期间,当中的刀盘由于长期要在较为恶劣的环境下工作,所以会因此导致刀盘出现不同程度的磨损,对工程的开展造成影响,所以要求施工单位可以尽快的完成磨损刀盘的修复,确保工程可以顺利开展。
一、工程实例在某工程中,盾构机的刀具与刀盘在施工过程中出现严重的磨损,具体为:对于刀盘来讲,在其中心区域以及辐条均出现显著的磨损,同时,刀箱与四把双联中心滚到均出现了掉落,还有8把正面滚刀以及6把切刀也同样出现了程度不等的磨损。
所以为了保证工程可以的开展,需要对竖井中的刀盘予以及时修复。
二、刀盘修复工艺胃由于刀盘磨损较为严重,修复工作量较大,且刀盘修复后仍需穿过长30m的上软下硬地层掘进施工,对刀盘修复质量要求较高,因此在刀盘修复前应认真熟悉图纸和施工现场,根据施工方案做好施工准备,并制定刀盘修复方案。
刀盘修复过程如下所述。
1、准备修复材料刀盘材料的材质为Q345B,所以为了确保刀盘在修复之后可以继续稳定使用,所以在修复过程中所选择的材质与之前保持一致。
此外,测量刀盘主梁厚度为80mm,所以需要根据测量后的规格尺寸来现场实施切割,刀座与刀箱均为原厂提供。
2、磨损区域的处理滚刀刀箱、加强筋板以及中心刀盘等磨损区域均要刨除干净,随后用打磨或者火焰切割等方式进一步修整磨损后的刀梁,并要将刀梁焊接表面的金属光泽打磨出来。
211110632_隧道掘进机主驱动密封系统洞内修复技术

专题研究SPECIAL RESEARCH隧道掘进机主驱动密封系统洞内修复技术陈良武1,王一博2,陈亚南1,王付利1,钟庆丰1(1. 中铁工程装备集团技术服务有限公司,河南 郑州 450016;2. 中铁工程装备集团有限公司,河南 郑州 450016)[摘要]通过对某工程应用的隧道掘进机主驱动密封系统洞内修复过程进行总结,形成了一套安全、高效、简便的隧道掘进机主驱动密封系统洞内修复技术。
该技术的运用极大节省了检修时间,保障了主驱动密封系统的修复质量,有效规避了由于密封系统失效导致的长时间停机现象,对提高隧道掘进机施工效率具有重要意义。
[关键词]隧道掘进机;主驱动;密封系统;检修[中图分类号]U455.43 [文献标识码]B [文章编号]1001-554X (2023)04-0102-06In -hole repair technology for main drive sealing system of tunnel boring machineCHEN Liang -wu ,WANG Yi -bo ,CHEN Ya -nan ,WANG Fu -li ,ZHONG Qing -feng隧道掘进机目前已广泛应用于地下空间建设及隧道施工领域[1,2]。
应用过程中,由于主驱动密封失效导致的停机事件常有发生,严重时将直接威胁主驱动使用寿命,造成长达数月甚至数年时间的工程停滞,严重影响施工效率[3-6]。
因此,当盾构设备在使用过程中主驱动密封系统出现问题时,对其及时进行修复显得尤为重要。
本文通过对某工程应用的隧道掘进机主驱动密封系统洞内修复过程进行总结,形成了一套安全、高效、简便的隧道掘进机主驱动密封系统洞内修复技术,在流程上大致可分为前期准备、密封系统拆卸、密封系统检修、密封系统回装4个步骤。
该技术的运用极大节省了修复时间,保障了主驱动密封系统的修复质量,有效规避了由于密封系统失效导致的长时间停机现象,对提高隧道掘进机施工效率具有重要意义。
盾构机主驱动和刀盘管路优化技术
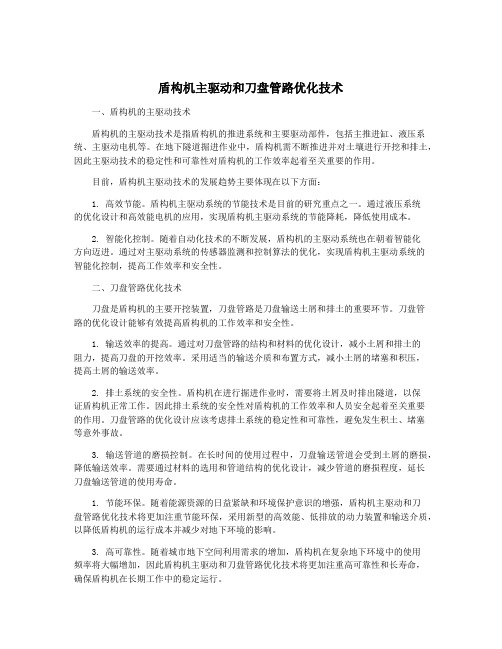
盾构机主驱动和刀盘管路优化技术一、盾构机的主驱动技术盾构机的主驱动技术是指盾构机的推进系统和主要驱动部件,包括主推进缸、液压系统、主驱动电机等。
在地下隧道掘进作业中,盾构机需不断推进并对土壤进行开挖和排土,因此主驱动技术的稳定性和可靠性对盾构机的工作效率起着至关重要的作用。
目前,盾构机主驱动技术的发展趋势主要体现在以下方面:1. 高效节能。
盾构机主驱动系统的节能技术是目前的研究重点之一。
通过液压系统的优化设计和高效能电机的应用,实现盾构机主驱动系统的节能降耗,降低使用成本。
2. 智能化控制。
随着自动化技术的不断发展,盾构机的主驱动系统也在朝着智能化方向迈进。
通过对主驱动系统的传感器监测和控制算法的优化,实现盾构机主驱动系统的智能化控制,提高工作效率和安全性。
二、刀盘管路优化技术刀盘是盾构机的主要开挖装置,刀盘管路是刀盘输送土屑和排土的重要环节。
刀盘管路的优化设计能够有效提高盾构机的工作效率和安全性。
1. 输送效率的提高。
通过对刀盘管路的结构和材料的优化设计,减小土屑和排土的阻力,提高刀盘的开挖效率。
采用适当的输送介质和布置方式,减小土屑的堵塞和积压,提高土屑的输送效率。
2. 排土系统的安全性。
盾构机在进行掘进作业时,需要将土屑及时排出隧道,以保证盾构机正常工作。
因此排土系统的安全性对盾构机的工作效率和人员安全起着至关重要的作用。
刀盘管路的优化设计应该考虑排土系统的稳定性和可靠性,避免发生积土、堵塞等意外事故。
3. 输送管道的磨损控制。
在长时间的使用过程中,刀盘输送管道会受到土屑的磨损,降低输送效率。
需要通过材料的选用和管道结构的优化设计,减少管道的磨损程度,延长刀盘输送管道的使用寿命。
1. 节能环保。
随着能源资源的日益紧缺和环境保护意识的增强,盾构机主驱动和刀盘管路优化技术将更加注重节能环保,采用新型的高效能、低排放的动力装置和输送介质,以降低盾构机的运行成本并减少对地下环境的影响。
3. 高可靠性。
盾构机主驱动和刀盘管路优化技术

盾构机主驱动和刀盘管路优化技术盾构机是一种用于地下隧道开挖的专业设备,其主要由主驱动和刀盘管路组成。
主驱动是盾构机的核心部件,它提供了足够的动力和转动力以驱动刀盘进行开挖工作。
而刀盘管路则是将主驱动提供的能量传递给刀盘,使其能够在地下隧道中进行开挖作业。
对于盾构机的主驱动和刀盘管路进行优化设计,可以极大提高盾构机的工作效率和稳定性,减少能源消耗和维护成本,从而实现更高效,更安全,更经济的地下隧道工程施工。
一、主驱动的优化技术1.电动主驱动:传统盾构机的主驱动一般采用液压驱动或者油压驱动。
随着科技的进步,电动主驱动技术已经成熟,并且在一些盾构机项目中得到了应用。
相比传统液压驱动,电动主驱动具有更高的效率和更稳定的性能,而且可以减少液压系统对机器的影响,使得盾构机在恶劣的地下工作环境下能够更加可靠。
2.智能控制系统:随着自动化技术的发展,盾构机的主驱动也可以配备智能控制系统,实现对主驱动的精准控制和监测。
智能控制系统能够根据地质情况和施工进度自动调整主驱动的工作参数,从而提高施工效率和降低能源消耗。
而且智能控制系统还可以及时发现主驱动的故障并提供预警,避免因故障引起的损失。
3.能量回收技术:盾构机在开挖过程中会产生大量的机械能,而在传统的设计中这部分能量通常被浪费掉了。
采用能量回收技术可以将这部分能量进行回收再利用,减少了对外部能源的依赖,降低了能源消耗和施工成本。
二、刀盘管路的优化技术1.优化刀盘设计:刀盘是盾构机的犁头,直接参与地下隧道的开挖工作,因此其设计对盾构机的整体性能有着重要影响。
通过优化刀盘的形状和材料,可以提高刀盘的耐磨性和耐腐蚀性,延长刀盘的使用寿命。
优化刀盘的结构和布置,可以减小刀盘对土壤的扰动,降低了施工过程中产生的土壤沉降,提高了施工安全性。
2.改善刀盘管路传动系统:刀盘管路是将主驱动提供的动力传递给刀盘的关键部件,其传动系统的优劣直接关系到刀盘的开挖效率和稳定性。
改善刀盘管路传动系统可以采用新型的轴承和传动元件,减少了传动损耗和振动,提高了传动效率和稳定性。
盾构机主驱动和刀盘管路优化技术

盾构机主驱动和刀盘管路优化技术盾构机是现代隧道建筑中的一种重要设备,广泛应用于交通、市政、水利、能源等领域的地下隧道、地下管廊等工程中。
主驱动和刀盘管路是盾构机中最核心的部分,其优化技术的应用可以大大提高盾构机的工作效率、降低运行成本、延长设备寿命。
主驱动系统是盾构机的核心部件,其可靠性直接关系到盾构机的工作效率和能够处理的隧道地质环境。
为了提高主驱动系统的稳定性和可靠性,优化技术可采用以下措施:1. 采用新型液压系统。
传统的液压系统由于存在压力和流量等方面的限制,其响应速度和控制精度有限。
而采用新型液压系统,如可控比例阀液压系统及电液伺服液压系统,其响应速度较快,控制更为精确,对于细微的地质环境变化能够做出更快速、更准确的响应。
2. 引入集成电路技术。
使用集成电路技术可以提高主驱动系统的处理能力和系统响应速度,从而提高盾构机的工作效率和控制精度。
3. 引入故障预测技术。
通过对主驱动系统进行故障分析和预判,预防系统的故障,提高盾构机的安全性和可靠性。
4. 加入智能化元素。
采用智能化控制系统和人工智能技术,使主驱动系统具备更好的自诊断和自我修复能力。
刀盘管路则是盾构机中负责切削和输送土方的重要系统。
刀盘管路的优化主要针对刀盘的材质、结构和刀具布置等方面,旨在提高盾构机的切削效率和土方输送能力。
具体措施包括:1. 优化刀盘设计。
根据不同地质环境的特点,合理设计刀盘的刀具布置、刀头形状和刀杆选用等参数,提高切削效率和耐磨性。
2. 优化刀盘材质。
采用高强度、耐磨性好的材料,延长刀盘的使用寿命和降低更换频率。
3. 引入集成控制技术。
采用集成控制技术,将刀盘、输送系统和土方处理系统进行无缝连接,实现更精确的控制和更高效的土方输送。
4. 采用节能技术。
针对刀盘管路中的能量损失问题,推广节能型刀盘和输送系统,减少能源浪费。
盾构机刀盘修复

盾构机刀盘修复盾构机拆解后发现:1、刀盘外圆面磨损。
2、部分主切刀座及原有耐磨钢板已经完全磨耗。
3、刀盘空腔外露没有蒙板覆盖。
4、刀盘面网格耐磨带稀少。
5、原有耐磨板失效。
6、泡沫孔裸露没有保护。
7、原有边刮刀没有固定在刀座上,而是直接与刀盘主体筋板焊接。
8、刀盘里面筋板需要堆焊网格耐磨带。
分析主要原因为隧道穿越的地层主要为粘土沙,其中夹杂中粗砂、砾砂、卵石,砂性土摩擦阻力大,渗透性强,在盾构的推进挤压下水分很快排出,土体强度提高,故不仅盾构推进摩擦阻力大,而且开挖面土压力也较大,对刀盘的磨损会比较严重。
3.1 焊工管理3.1.1 所有焊工须持有有效证件,并且模拟现场焊接符合要求。
3.1.2 焊工精神饱满上岗作业,技能娴熟,操作手法全面。
3.1.3 焊前对焊工进行工艺交底,使焊工掌握具体焊接工艺,熟悉焊材和焊机性能,工艺确定后,焊工要严格执行。
3.1.4 开工前带焊工熟悉施工现场,进行详细的安全教育和管理,使焊工树立安全观念,进行安全操作。
3.2 焊材管理3.2.1焊材入库焊材有齐全的材质证明,并经检查确认合格后入库。
3.2.2 焊材发放焊材由专人发放,并做好发放记录,包括生产批号,施焊焊缝部位。
3.2.3耐磨焊丝检查固本耐磨焊丝只有在烘烤时拆包,拆包时核对焊丝牌号、规格、批号等。
拆包后检查焊丝是否生锈、药皮是否脱落,目测检验不合格的焊条不得进入烘箱,烘干后,对同一生产批号的焊丝进行检查,看药皮韧性及内部焊心是否生锈,如有不合格,这扩大检查,如仍有不合格报告技术负责人处理。
3.3环境管理3.3.1 手工电弧焊现场风速大于8m/s时,采取有效的防风措施后方可施焊。
3.3.2 雨雪天气或相对湿度大于90%时,采取有效防护措施后施焊。
3.3.3 现场需要搭设围挡(施工场地待定)3.3.4 刀盘面向上水平放置,安放支点应牢固可靠。
1、设计尺寸:主视图外径Ф6260mm,剖视图B-B显示:环带直径6230mm,刀盘厚度为450mm,耐磨环带宽度160 mm厚度50mm,耐磨块原有数量56块均匀分布。
盾构机主轴承的轴承故障与修复技术

盾构机主轴承的轴承故障与修复技术盾构机主轴承是盾构机中重要的部件之一,起着支撑和转动刀盘的关键作用。
然而,由于长时间高负荷运转,主轴承可能会发生故障,影响盾构机的正常工作。
本文将探讨盾构机主轴承的常见故障原因以及相应的修复技术。
首先,了解主轴承的构造及工作原理对于故障的分析和修复非常重要。
主轴承通常由内圈、外圈、滚动体以及保持架等组成。
主轴承承受来自刀盘的扭矩和轴向力,并在高速运转的同时保持较小的振动。
然而,由于工作环境的恶劣条件和长时间的运转,主轴承可能会出现以下故障。
一、疲劳断裂疲劳断裂是主轴承常见的故障形式之一。
长时间高速运转会导致主轴承内圈和外圈的疲劳裂纹逐渐扩展,最终导致轴承的断裂。
造成疲劳断裂的原因主要有以下几点:1.负荷过大:盾构机工作时所受的负荷过大会导致主轴承在运转过程中产生较大的应力,从而加速轴承的疲劳断裂。
2.润滑不良:不良的润滑导致主轴承表面的润滑膜被破坏,使得轴承表面出现划痕,进而加速疲劳断裂的发生。
修复技术:针对主轴承的疲劳断裂问题,一般采取以下修复技术:1.更换轴承:当主轴承发生疲劳断裂时,常规的修复方法是将断裂的轴承更换为新的轴承。
更换轴承时,需要注意选择合适的轴承型号和品牌,确保其质量可靠。
2.强化润滑系统:改善润滑条件可以有效减少疲劳断裂的发生。
通过增加润滑剂的供给,维持良好的润滑膜,减少轴承表面的磨损,从而延长轴承的使用寿命。
二、磨损除了疲劳断裂外,主轴承还容易发生磨损。
磨损可能是由于长时间工作导致轴承表面的润滑膜破坏,也可能是因为入侵物质(如尘土、水分等)导致轴承表面磨损。
造成磨损的原因主要有以下几点:1.润滑不良:不良的润滑条件会导致轴承表面的润滑膜被破坏,使得轴承表面出现磨损,甚至裸露金属表面。
2.入侵物质:盾构机作业环境中存在大量的尘土、水分等入侵物质,这些物质进入轴承内部后会与润滑剂发生化学反应,导致轴承表面磨损。
修复技术:针对主轴承的磨损问题,常见的修复技术如下:1.轴承研磨:对于表面轻微磨损的主轴承,可以采用轴承研磨技术进行修复。
盾构机主驱动和刀盘管路优化技术

盾构机主驱动和刀盘管路优化技术盾构机是一种在土壤或岩石中进行隧道开挖和建设的专用设备,是现代城市地下工程建设和地下管线铺设的重要工具。
而盾构机的主驱动和刀盘管路优化技术是盾构机性能提升和工程质量保障的关键之一。
一、盾构机主驱动技术主驱动是盾构机的核心部件,其作用是通过动力装置将动力传递给刀盘,驱动刀盘进行钻进。
盾构机主驱动采用的传动方式主要有液压驱动、电动驱动和内燃机驱动等多种形式。
1.液压驱动液压驱动是目前盾构机主要的驱动方式之一,其优点是传动平稳、能量转换效率高、响应速度快,具有适应性强等特点。
液压系统还可以实现多轴同步控制,有利于盾构机的精确掏土和定位。
2.电动驱动电动驱动是另一种常见的盾构机主驱动方式,通常采用交直流电机作为动力源,通过齿轮传动将动力传递给刀盘。
电动驱动具有动力大、速度可调、响应灵敏等特点,适用于地铁隧道、城市管线等工程。
3.内燃机驱动内燃机驱动是盾构机主驱动的传统形式,通过内燃机将燃油燃烧产生的能量传递给刀盘,驱动刀盘进行开挖。
内燃机驱动具有功率大、适应范围广等特点,适用于硬岩、长距离等特殊工况。
盾构机主驱动技术的发展趋势是高效化、智能化和环保化。
未来,盾构机主驱动将更加注重能源利用效率,提高动力装置的精度和可靠性,实现更高的工作效率和更低的排放。
随着自动化技术和智能控制技术的发展,盾构机主驱动系统将实现自动化协调、智能调节和远程监控,为地下工程建设提供更便捷、高效的解决方案。
二、刀盘管路优化技术刀盘是盾构机的开挖工具,其运行状态直接影响着开挖效率和质量。
为了提高刀盘的工作性能,刀盘管路的优化设计显得尤为重要。
刀盘管路优化技术主要包括刀盘结构设计、刀具选择、刀具布置以及刀盘动力传递等方面。
1.刀盘结构设计刀盘结构设计是刀盘管路优化的关键内容。
刀盘应具有足够的刚度和强度,以承受切削力和冲击力,并保证开挖的稳定性和安全性。
刀盘还应具有良好的自清洁性和降阻减振性能,以减少切削阻力和延长刀具使用寿命。
- 1、下载文档前请自行甄别文档内容的完整性,平台不提供额外的编辑、内容补充、找答案等附加服务。
- 2、"仅部分预览"的文档,不可在线预览部分如存在完整性等问题,可反馈申请退款(可完整预览的文档不适用该条件!)。
- 3、如文档侵犯您的权益,请联系客服反馈,我们会尽快为您处理(人工客服工作时间:9:00-18:30)。
隧道内盾构机刀盘主驱动齿圈的修复技术
摘要:该文介绍了海瑞克盾构机刀盘主驱动齿圈的修复。
详细说明了齿圈轮齿在不拆除和狭小施工空间的情况下,对焊接材料选取、焊接工艺、检测方法等的方案制定,成功的修复了大齿圈轮齿的过程。
关键词:盾构机,齿圈,修理
Abstract: this paper introduces the Shanghai g shield construction machine cutter tooth the restoration of the Lord drive circle. Detailed description of the gear tooth circle in the preservation and narrow space construction of welding material selection, the welding process, the detection method of decision-making, the success of the big circle gear tooth repair process.
Keywords: shield construction machine, tooth circle, repair
1、产生的现象
盾构正在掘进,在盾体部位隐约能听见咯噔的声响,马上进行了全面检查,发现声音出现在前盾位置,仔细观察发现,中心回转体方位指针在出现声响的时候有滑移现象,初步判定可能为刀盘主驱动问题,后经确诊为刀盘驱动轴承齿圈损坏。
2、问题产生的原因
此处为437环,处在小转弯半径(200M)的施工段,正值全断面地层,微风化花岗岩,纹理结合紧密。
掘进过程中刀盘扭矩一直处在180bar以上,渣土温度很高,最高达到68℃,齿轮油温度也徘徊在60℃~70℃之间,另外由于此盾构机为德国海瑞克早期型号,工作有7年多,推进里程为9公里以上,已接近使用寿命,部分机械零件老化严重。
在广州这种复合层地层中掘进,长期的满负荷工作,轴承的疲劳磨损比较严重,鉴于以上因素,使得盾构机刀盘主驱动部位(含8个减速箱和驱动马达)发生了故障,8号减速箱内轴承损坏,导致轴承滚珠掉入齿圈中,从而导致大齿圈的轮齿和其他减速箱内的轮齿断裂。
图1 大齿圈轮齿损伤照片
3、处理措施
8个减速箱可以拆卸出来维修和更换,其维修难度较小,而在盾构机上的大齿圈由于机械本身设计和空间限制无法取出来更换,因此只能在现场进行维
修,由于现场条件的限制对于大齿圈的修复带来了很大的困难(比如轮齿的加温和焊接的操作空间)。
图2 大齿圈和减速箱马达位置示意图
4、修复前准备工作
4.1 主要材料选择
本工程的施工机械为德国海瑞克生产,齿圈为SKF公司制造,材质为:42CrMo4v,相当于国内的42CrMo,日本的SCM440,美国的4140。
对于焊条的选择,需满足以下条件:
(1)主材和焊材的主要成分必须相近,由于现场内无法进行高温加热(只能采取氧气-乙炔焰加热),因此要求焊材必须能在低温焊接;
(2)具有很高的伸长率和抗裂性能,由于要采取多次的堆焊,因此焊材在不断地热循环中必须不能疲劳破坏或产生裂痕;
(3)具有优良的耐热性,抗氧化性及耐蚀性;
参考国内的一些大型齿轮的修复,多数采用2222XHD焊条,但是由于第二条的限制,此种焊条不太适合,根据国外的一些经验,最终我们确定了卡斯特林公司生产的Xuper NucleoTec 2222 焊条,此种焊条完全符合上述条件。
4.2 现场准备工作
采取24小时工作制的连续作业方式,确保按时修复完成,严格按照既定技术修复方案进行修复,秉着严谨而周密的原则详细安排材料和修复的技术人员。
表1刀盘驱动轴承齿圈修复主要材料及设备统计表
5、修复工艺
5.1焊条除潮:由于焊条在存放过程中会吸取部分潮气,为了保证焊接的质量,我们首先把焊条在烤箱内,先加温至200℃保温3分钟后,再加温至300℃继续保温15分钟时间,使用前用牛皮纸包好拿到现场使用,在暂时不用时再包好存放。
5.2坏齿处理:用打磨机将损坏齿轮坏齿部位全部打掉,有裂纹部位打磨直到裂纹消失,焊接坡口采用“U” 型或“V”型,尽量减少母材金属熔入焊缝金属中的比例。
如果裂纹太深超过整个齿厚的一半将全部齿打掉,然后用气动小打磨机修整。
5.3堆焊补全:为了保护大齿圈的其它地方,烧焊前,焊点两侧尽量用石棉盖住,先将齿面用氧气-乙炔焰进行预热,坡口处先前打磨光的部位用焊条线拉式的层层敷焊起来。
在焊接过程中用对母材进行加热保温,每焊完一层对焊缝焊渣进行彻底清除,并用榔头轻击焊层尽量消除焊缝处内应力。
5.4回火保温:焊接完成后用氧气-乙炔焰对母材轮齿进行回火,用石棉布进行覆盖保温使母材温度缓慢降低冷却,尽量避免因为冷却过快应力集中产生裂纹。
5.5齿形修复:齿形修复采用钳工手工修复。
用气动打磨机打磨修复粗略齿形,用三菱尺涂色修复齿面直线度,用齿形卡尺保证齿形尺寸。
5.6检测方法
为检测轮齿的损伤程度,需要对其进行探伤,探伤比较常用的有渗透探伤、磁粉探伤、超声波探伤、UT探伤等,但是由于直接在机械上进行探伤,上面有好多电器元件,因此我们只采用了渗透探伤和超声波探伤2种。
首先给轮齿进行编号,再使用探伤剂进行渗透探伤,然后把有裂纹的轮齿的裂缝情况和编号记录下来,第一遍修复好轮齿后,统一进行了超声波探伤,并把有问题的部位再次修复,直至全部探伤通过为止。
5.7修理后的效果
盾构机刀盘主驱动轴承齿圈全部修复完成后,装配好8个减速箱内轴承及主驱动马达。
为满足下一步的施工,对盾构机的掘进参数进行了调整,刀盘扭矩不超过150bar,推进速度不超过30mm/min,推力控制在800t~1000t,控制齿轮油及刀盘温度。
现在已经完成剩余1470m掘进,隧道贯通,此次修复的盾构机刀盘主驱动轴承齿圈强度等技术参数完全满足了施工需求。
6、经济分析
如果主轴承大齿圈不采取隧道内修复而是采用吊出盾构机后更换的话成本会很高。
根据厂家报价,运输至厂家和更换新的大齿圈约需人民币400万元,再加上打竖井和吊出盾构机的费用,会超出700万,耽误最少2个月的工期。
而在隧道内维修大齿圈只用了人民币约3万元(含机械费和人工费),不到1个月就恢复了掘进。
通过两个数据比较来看,采取了隧道内修复的做法是完全正确的,并验证了其可行性,大大节约了施工成本。
7、总结
在国内维修盾构机大齿圈的案例很少,并且在隧道内成功维修海瑞克盾构机尚属首例,通过这次的大齿圈维修,为今后类似问题的处理有一定借鉴参考意义。
注:文章内所有公式及图表请以PDF形式查看。