中深孔爆破的钻孔
中深孔爆破技术
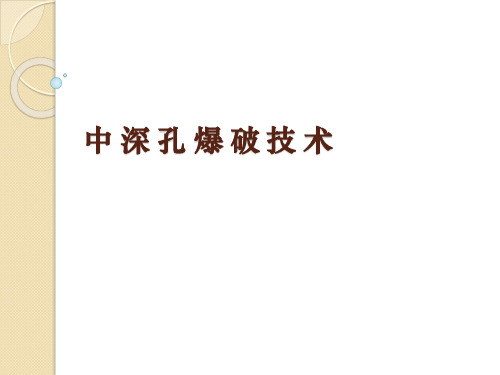
2、钻孔形式
露天深孔爆破的钻孔形式一般分为垂直钻孔和倾斜钻孔两 种,如下图所示:
垂直深孔和倾斜深孔的使用条件和优缺点:
深孔布置 形式
塑料导爆管是一种由高压聚乙烯材料做成的白色或彩色塑 料软管,外径3mm,内径1.5mm,管内涂有薄层奥克托金或 黑索金、泰安等猛炸药与铝粉等组成的混合炸药,常用导爆管 的爆速多数在1900~2000m/s之间。
导爆管的引爆可用击发抢、雷管和导爆索引爆。
使用导爆管毫秒爆破网络一般采用孔内毫秒起爆网络,所 谓的孔内毫秒起爆网络是指网路中各个炮孔内的起爆雷管采用 时间表(延时量)决定的。孔外传爆器件仅起传爆作用,不起 延时作用。
(2)钻孔作业
凿岩基本操作方法:“软岩慢打,硬岩快打”;在操作过 程中做到“一听、二看、三检查”。一听:听钻孔声音判断孔 内情况;二看:看风压表、电流表是否正常;三检查:检查机 械、检查风电、检查孔内故障。
(3)钻孔施工故障判断和排除
钻孔故障包括内故障和机械故障。一般判断方法:听冲击 岩石声音判断孔内情况,看风压电表、电流表的变化和钻孔排 碴情况,判断故障原因。
4、爆破参数的确定 露天深孔爆破参数包括:孔径、孔深、超深、底盘抵抗线、 孔距、排距、堵塞长度和单位炸药消耗量等。 (1)孔径 露天中深孔的孔径主要取决于钻机类型、台阶高度和岩石 性质; (2)孔深与超深
孔深是由台阶高度和超深确定的。 根据我地区的开采现状,如果8米台阶开采,则应取孔深 9米,12米台阶开采应取13米~14米。 (3)底盘抵抗线 底盘抵抗线受许多因素影响,变动范围较大。 根据钻孔作业的安全条件: W≤HCtga+B 式中w——底盘抵抗线,m; d——台阶坡面角,一般为60~75度 H——台阶高度,m; B——从钻孔中心至顶线的安全距离,m; (4)孔距和排距 孔距(a)是指同一排孔中相邻两钻孔中心线间的距离。 孔距按下式计算: a=mW 式中m——炮孔密集系数。
中深孔爆破作业规程范本(2篇)
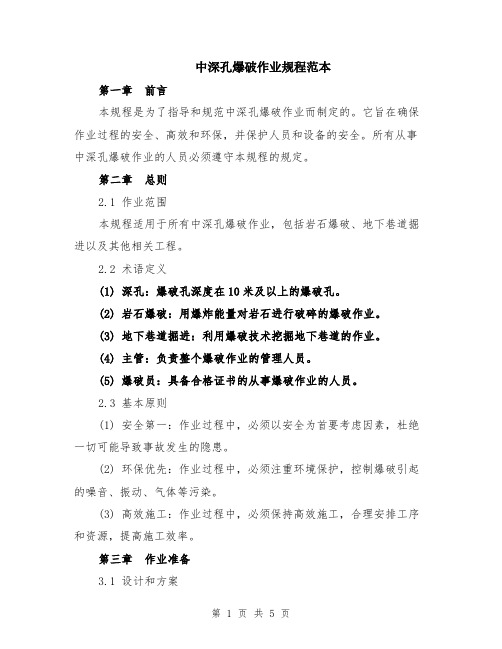
中深孔爆破作业规程范本第一章前言本规程是为了指导和规范中深孔爆破作业而制定的。
它旨在确保作业过程的安全、高效和环保,并保护人员和设备的安全。
所有从事中深孔爆破作业的人员必须遵守本规程的规定。
第二章总则2.1 作业范围本规程适用于所有中深孔爆破作业,包括岩石爆破、地下巷道掘进以及其他相关工程。
2.2 术语定义(1) 深孔:爆破孔深度在10米及以上的爆破孔。
(2) 岩石爆破:用爆炸能量对岩石进行破碎的爆破作业。
(3) 地下巷道掘进:利用爆破技术挖掘地下巷道的作业。
(4) 主管:负责整个爆破作业的管理人员。
(5) 爆破员:具备合格证书的从事爆破作业的人员。
2.3 基本原则(1) 安全第一:作业过程中,必须以安全为首要考虑因素,杜绝一切可能导致事故发生的隐患。
(2) 环保优先:作业过程中,必须注重环境保护,控制爆破引起的噪音、振动、气体等污染。
(3) 高效施工:作业过程中,必须保持高效施工,合理安排工序和资源,提高施工效率。
第三章作业准备3.1 设计和方案(1) 根据工程需要,确定爆破设计方案,包括孔径、孔距、孔深等参数。
(2) 编制爆破作业方案,明确作业流程和安全措施。
(3) 确定爆破者的数量和配置,保证作业过程的安全性。
3.2 安全措施(1) 负责人员必须制定详细的安全工作方案,并进行逐一检查,确保每项工作都有相应的安全措施。
(2) 爆破区域必须进行划定,并设置明显的警示标志,确保安全通道的畅通。
(3) 必须配备专业人员及时消除不安全因素,确保作业过程中的安全。
第四章爆破孔钻掘4.1 设备准备(1) 检查钻机设备,确保设备完好,安全可靠。
(2) 准备足够的钻杆、钻头等配件,并进行检查。
4.2 钻孔操作(1) 按照设计要求,进行合理的钻孔布局。
(2) 钻孔过程中,必须使用正确的钻具,掌握合适的转速和进给速度。
(3) 钻孔过程中,必须保持适当的冷却液,防止钻头过热。
中深孔爆破作业规程范本(二)一、引言中深孔爆破作业是一项涉及到工程建设和安全的关键工作,准确的操作方法和规范的作业流程是保证爆破作业顺利进行的重要保障。
中深孔爆破法
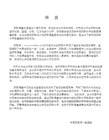
(4)符合矿山业主的实际要求。2005年,随着《安全生产许可证条例》的进一步落实,国务院、国家安全生产监督管理总局进一步加强安全生产工作,业主若要取得非煤矿矿山企业安全生产许可证,就必须投入较多的资金,对矿山进行较大程度的整改。但业主只要采用中深孔爆破方法,对凿岩设备进行更新、爆破作业人员进行重新培训,使他们掌握新的开采技术,就可以以较小的资金投入,改变现状,从而为顺利取得安全生产许可证奠定了坚实的基础。
炮孔装药量:影响其取值的因素较多,主要因素有:合理炸药单位消耗量取值、岩石性质和地质条件、炸药品种、装药结构、气候条件、爆破方法的选择。
炮孔装药量计算公式为:Q=q·V=q·aWH,(单位:kg);H为台阶高度。
以上计算为一般常用计算方法,在实际运用过程中应根据矿山实际情况作适当的调整,以达到理想的爆破效果。
(5)由于中深孔爆破的钻孔和爆破作业是在平缓的台阶上进行,具有机械化程度高,一次爆落矿量大,爆破成本低,生产效率高,施工进度快,工作环境好,爆破时对开采边坡的影响比大炮小、采矿作业安全等优点,从长期来看,可以降低开采成本,提高成为作业安全,因此,中深孔爆破应可以成为我省非煤露天矿山的主要爆破方法。
排距b:相邻两排炮孔间的距离。按炮孔的布置方式有不同的计算方式。排间炮孔交错呈等边三角形布置时,计算方式:b=a·Sin60o=0.866a (单位:米);排间炮孔平行布置时,计算方式:b=f·a,(单位:米);f为排间系数,根据矿岩性质,一般常取为0.45~0.75。
底盘最小抵抗线W的大小与炮孔直径、装药直径、炸药威力、装药密度、岩石可爆性、要求破碎程度和阶段高度有关。计算方式:W=(0.6~0.9)H;超钻深度h:h=(0.15~0.35)W,岩石松软、层理发育时,取小值,岩石坚硬时取大值。但应注意超深也不能太大,否则会将底板或下一台阶的顶部破坏;
2024年露天矿山中深孔爆破技术(3篇)
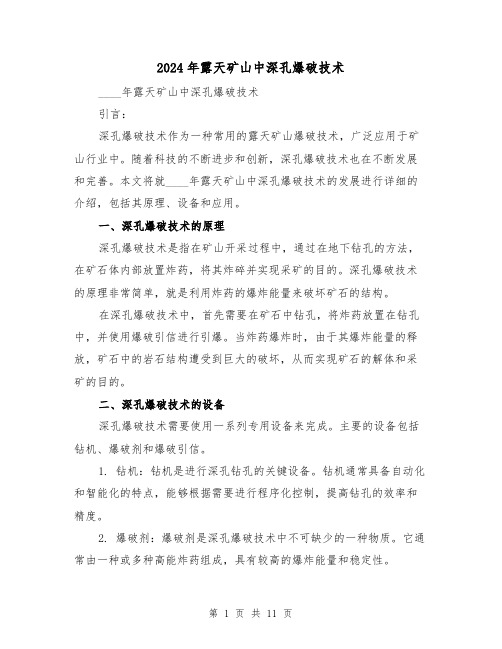
2024年露天矿山中深孔爆破技术____年露天矿山中深孔爆破技术引言:深孔爆破技术作为一种常用的露天矿山爆破技术,广泛应用于矿山行业中。
随着科技的不断进步和创新,深孔爆破技术也在不断发展和完善。
本文将就____年露天矿山中深孔爆破技术的发展进行详细的介绍,包括其原理、设备和应用。
一、深孔爆破技术的原理深孔爆破技术是指在矿山开采过程中,通过在地下钻孔的方法,在矿石体内部放置炸药,将其炸碎并实现采矿的目的。
深孔爆破技术的原理非常简单,就是利用炸药的爆炸能量来破坏矿石的结构。
在深孔爆破技术中,首先需要在矿石中钻孔,将炸药放置在钻孔中,并使用爆破引信进行引爆。
当炸药爆炸时,由于其爆炸能量的释放,矿石中的岩石结构遭受到巨大的破坏,从而实现矿石的解体和采矿的目的。
二、深孔爆破技术的设备深孔爆破技术需要使用一系列专用设备来完成。
主要的设备包括钻机、爆破剂和爆破引信。
1. 钻机:钻机是进行深孔钻孔的关键设备。
钻机通常具备自动化和智能化的特点,能够根据需要进行程序化控制,提高钻孔的效率和精度。
2. 爆破剂:爆破剂是深孔爆破技术中不可缺少的一种物质。
它通常由一种或多种高能炸药组成,具有较高的爆炸能量和稳定性。
3. 爆破引信:爆破引信是将炸药引爆的关键设备。
目前,已经出现了一种无线遥控引爆系统,可以远程操控爆破引信进行引爆操作,提高了爆破的安全性和可靠性。
三、深孔爆破技术的应用深孔爆破技术广泛应用于露天矿山中的矿石开采中。
它具有以下几个优势:1. 提高采矿效率:由于深孔爆破技术可以更好地破碎矿石,使其更易于提取和处理,从而大大提高了采矿的效率。
2. 减少采矿成本:深孔爆破技术可以减少挖掘和运输的工作量,降低了采矿的成本。
3. 保护环境:与传统的爆破技术相比,深孔爆破技术在挖掘过程中产生的噪音和颗粒物的排放较少,能够更好地保护环境。
4. 提高安全性:深孔爆破技术可以远程操控爆破引信进行引爆操作,减少了人员在爆破现场的风险。
露天矿山中深孔爆破技术
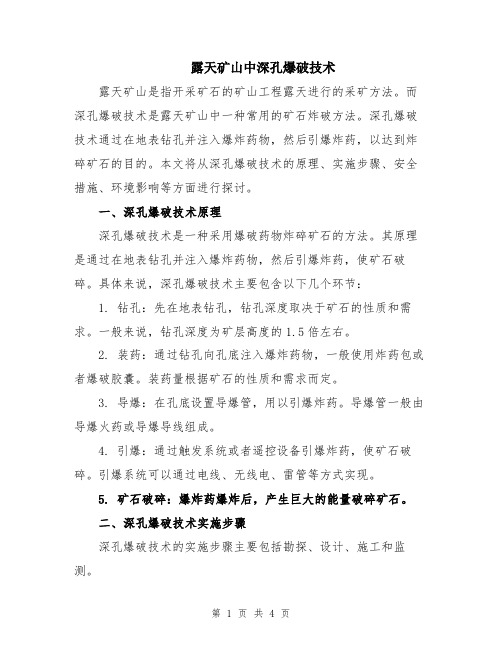
露天矿山中深孔爆破技术露天矿山是指开采矿石的矿山工程露天进行的采矿方法。
而深孔爆破技术是露天矿山中一种常用的矿石炸破方法。
深孔爆破技术通过在地表钻孔并注入爆炸药物,然后引爆炸药,以达到炸碎矿石的目的。
本文将从深孔爆破技术的原理、实施步骤、安全措施、环境影响等方面进行探讨。
一、深孔爆破技术原理深孔爆破技术是一种采用爆破药物炸碎矿石的方法。
其原理是通过在地表钻孔并注入爆炸药物,然后引爆炸药,使矿石破碎。
具体来说,深孔爆破技术主要包含以下几个环节:1. 钻孔:先在地表钻孔,钻孔深度取决于矿石的性质和需求。
一般来说,钻孔深度为矿层高度的1.5倍左右。
2. 装药:通过钻孔向孔底注入爆炸药物,一般使用炸药包或者爆破胶囊。
装药量根据矿石的性质和需求而定。
3. 导爆:在孔底设置导爆管,用以引爆炸药。
导爆管一般由导爆火药或导爆导线组成。
4. 引爆:通过触发系统或者遥控设备引爆炸药,使矿石破碎。
引爆系统可以通过电线、无线电、雷管等方式实现。
5. 矿石破碎:爆炸药爆炸后,产生巨大的能量破碎矿石。
二、深孔爆破技术实施步骤深孔爆破技术的实施步骤主要包括勘探、设计、施工和监测。
1. 勘探:在进行深孔爆破之前,需要进行勘探工作,了解矿石的性质、厚度、分布等信息,以确定最合适的爆破方案。
2. 设计:根据勘探结果,制定深孔爆破设计方案,包括爆破孔网、炸药量、装药方式、引爆方式等。
3. 施工:按照设计方案进行深孔爆破孔的钻孔和装药工作。
施工过程中需要严格控制钻孔的位置、角度和深度,确保炸药的合理分布。
4. 监测:在深孔爆破之前、之中和之后进行监测,包括地震监测、振动监测、颗粒物监测等。
监测结果用于评估爆破效果和安全性。
三、深孔爆破技术安全措施深孔爆破技术在实施过程中,需要采取一系列安全措施,以保障施工人员和周边环境的安全。
1. 施工人员安全:施工人员需要穿戴防护装备,包括安全帽、防护眼镜、防护服等,以防止破碎物和爆炸物对施工人员的伤害。
掘进工作面中深孔爆破技术研究
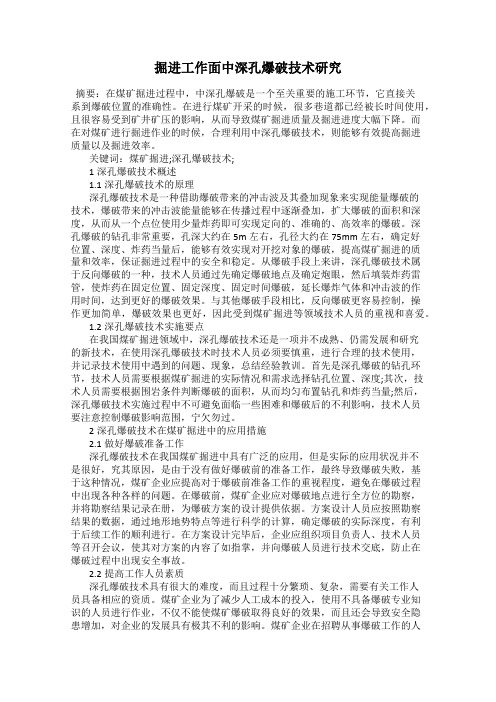
掘进工作面中深孔爆破技术研究摘要:在煤矿掘进过程中,中深孔爆破是一个至关重要的施工环节,它直接关系到爆破位置的准确性。
在进行煤矿开采的时候,很多巷道都已经被长时间使用,且很容易受到矿井矿压的影响,从而导致煤矿掘进质量及掘进进度大幅下降。
而在对煤矿进行掘进作业的时候,合理利用中深孔爆破技术,则能够有效提高掘进质量以及掘进效率。
关键词:煤矿掘进;深孔爆破技术;1深孔爆破技术概述1.1深孔爆破技术的原理深孔爆破技术是一种借助爆破带来的冲击波及其叠加现象来实现能量爆破的技术,爆破带来的冲击波能量能够在传播过程中逐渐叠加,扩大爆破的面积和深度,从而从一个点位使用少量炸药即可实现定向的、准确的、高效率的爆破。
深孔爆破的钻孔非常重要,孔深大约在5m左右,孔径大约在75mm左右,确定好位置、深度、炸药当量后,能够有效实现对开挖对象的爆破,提高煤矿掘进的质量和效率,保证掘进过程中的安全和稳定。
从爆破手段上来讲,深孔爆破技术属于反向爆破的一种,技术人员通过先确定爆破地点及确定炮眼,然后填装炸药雷管,使炸药在固定位置、固定深度、固定时间爆破,延长爆炸气体和冲击波的作用时间,达到更好的爆破效果。
与其他爆破手段相比,反向爆破更容易控制,操作更加简单,爆破效果也更好,因此受到煤矿掘进等领域技术人员的重视和喜爱。
1.2深孔爆破技术实施要点在我国煤矿掘进领域中,深孔爆破技术还是一项并不成熟、仍需发展和研究的新技术,在使用深孔爆破技术时技术人员必须要慎重,进行合理的技术使用,并记录技术使用中遇到的问题、现象,总结经验教训。
首先是深孔爆破的钻孔环节,技术人员需要根据煤矿掘进的实际情况和需求选择钻孔位置、深度;其次,技术人员需要根据围岩条件判断爆破的面积,从而均匀布置钻孔和炸药当量;然后,深孔爆破技术实施过程中不可避免面临一些困难和爆破后的不利影响,技术人员要注意控制爆破影响范围,宁欠勿过。
2深孔爆破技术在煤矿掘进中的应用措施2.1做好爆破准备工作深孔爆破技术在我国煤矿掘进中具有广泛的应用,但是实际的应用状况并不是很好,究其原因,是由于没有做好爆破前的准备工作,最终导致爆破失败,基于这种情况,煤矿企业应提高对于爆破前准备工作的重视程度,避免在爆破过程中出现各种各样的问题。
中深孔爆破安全操作规程

中深孔爆破安全操作规程中深孔爆破是一种常用于采矿、工程爆破和建筑拆除等行业的爆破方法,但随着深孔爆破规模的扩大和工作环境的复杂化,爆破作业存在着一定的安全风险。
为了确保爆破作业的安全进行,制定一套完善的中深孔爆破安全操作规程势在必行。
一、爆破前的准备工作1. 编制详细的爆破设计方案,并经专家审核。
2. 针对爆破地点进行现场勘查,确定爆破孔长度、直径、布孔方式等参数,并制定详细的布孔图。
3. 检查爆破设备和材料,确保其正常运行和良好状态。
4. 进行必要的安全培训,提高操作人员的安全意识和爆破技术水平。
二、爆破孔的钻探1. 钻孔作业前应在爆破地点设置明显的警示标志,确保周围人员远离钻孔区域。
2. 严格执行钻孔参数和技术要求,钻孔长度、直径、倾角等应符合设计方案要求。
3. 钻孔过程中应定期检查钻孔条件、孔深和孔壁稳定性,确保钻孔质量。
4. 钻孔完成后,应进行孔眼检查,确保没有破碎岩块和炸药泄漏。
三、装药与引爆1. 装药前,应对炸药进行仔细检查,确保其质量无问题。
2. 严格执行装药的数量和方式,确保炸药与包装物的接触面积充分,并保证装药密实度。
3. 在装药前,应将周围人员疏散到安全区域,并设置好警示标志。
4. 引爆前,应确保没有未炸药物和炸药泄漏,并远离爆破点。
5. 引爆操作应交由经验丰富的爆破工作人员执行,并确保操作正确、灵活和准确。
四、爆破后的处理1. 爆破后,应先检查爆破效果,并对爆破残留物进行处理和清理。
2. 检查爆破地点和周围环境,确认无安全隐患后,方可恢复正常的作业。
3. 对于可能造成环境污染的物质及时处理和处置,确保环境安全。
五、安全措施1. 操作人员应穿戴符合标准的个体防护用品,包括安全帽、眼镜、口罩、耳塞、手套等。
2. 参与爆破作业的人员必须经过专门的培训和考核,具备相关的工作经验和技能。
3. 周围区域应设置安全警戒线,确保没有人员进入爆破区域。
4. 定期对爆破设备和工具进行检修和维护,确保其正常运行。
中深孔爆破操作规程
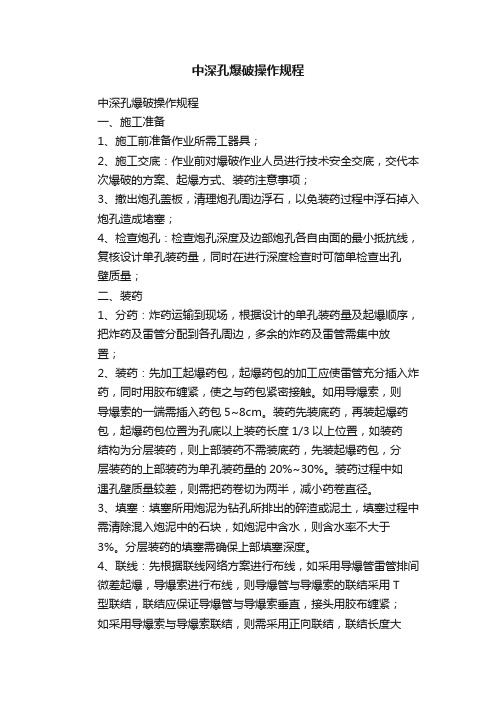
中深孔爆破操作规程中深孔爆破操作规程一、施工准备1、施工前准备作业所需工器具;2、施工交底:作业前对爆破作业人员进行技术安全交底,交代本次爆破的方案、起爆方式、装药注意事项;3、撤出炮孔盖板,清理炮孔周边浮石,以免装药过程中浮石掉入炮孔造成堵塞;4、检查炮孔:检查炮孔深度及边部炮孔各自由面的最小抵抗线,复核设计单孔装药量,同时在进行深度检查时可简单检查出孔壁质量;二、装药1、分药:炸药运输到现场,根据设计的单孔装药量及起爆顺序,把炸药及雷管分配到各孔周边,多余的炸药及雷管需集中放置;2、装药:先加工起爆药包,起爆药包的加工应使雷管充分插入炸药,同时用胶布缠紧,使之与药包紧密接触。
如用导爆索,则导爆索的一端需插入药包5~8cm。
装药先装底药,再装起爆药包,起爆药包位置为孔底以上装药长度1/3以上位置,如装药结构为分层装药,则上部装药不需装底药,先装起爆药包,分层装药的上部装药为单孔装药量的20%~30%。
装药过程中如遇孔壁质量较差,则需把药卷切为两半,减小药卷直径。
3、填塞:填塞所用炮泥为钻孔所排出的碎渣或泥土,填塞过程中需清除混入炮泥中的石块,如炮泥中含水,则含水率不大于3%。
分层装药的填塞需确保上部填塞深度。
4、联线:先根据联线网络方案进行布线,如采用导爆管雷管排间微差起爆,导爆索进行布线,则导爆管与导爆索的联结采用T 型联结,联结应保证导爆管与导爆索垂直,接头用胶布缠紧;如采用导爆索与导爆索联结,则需采用正向联结,联结长度大于10cm,联结夹角小于45度。
如采用电雷管起爆,则需根据设计的联线方案进行联结,接头应充分接触,尽力减小联结过程中接头增加的电阻值。
联线完后需进行检查,检查内容为是否有漏接及联结质量。
三、起爆1、警戒:装药完成后,撤出爆破影响范围内的人员及设备,按设计的安全距离及爆破安全规程要求的飞石距离设置警戒,发出爆破信号,只有起爆信号发出后方可起爆。
2、起爆后按安全规程要求的间隔时间到后进行检查及爆后爆破效果评估,检查内容为查看是否有盲炮,如遇盲炮则需设置警戒,进行处理。
- 1、下载文档前请自行甄别文档内容的完整性,平台不提供额外的编辑、内容补充、找答案等附加服务。
- 2、"仅部分预览"的文档,不可在线预览部分如存在完整性等问题,可反馈申请退款(可完整预览的文档不适用该条件!)。
- 3、如文档侵犯您的权益,请联系客服反馈,我们会尽快为您处理(人工客服工作时间:9:00-18:30)。
可变影响系数大小可估计如下:
最好情况 92% (55min/h) 好的情况 83% (50min/h) 一般情况 75% (45min/h) 差的情况 67% (40min/h)
电铲日能力
每勺斗的物料重量=----------------
工作周期数
每勺斗物料量×K8
勺斗规格=------------------
8-20
33050000003455000000-
岩石等级 f
金-80
4-8
27
8-12
20
12-16
12
16-18
YQ-150 KQ-170 KQ-200 KQ-250
32
32
35
37
25
25
38
30
20
20
22
24
15
45
18
20
钻进速度和孔径的平方成反比
钻机效率与岩石f系数有很大关系,但f 系数并不 是决定钻孔效率的唯一因素,有些岩石尽管f系数 较低,但由于韧性较大,钻孔效率低下,并且钻头,钻 杆消耗量很大。
2)运距 3)车铲利用率。 4)系统的组织管理水平。
车铲比的确定方法较多,但均不够完善。分析计算 法是较常用的方法,其匹配卡车数可按下式计算。
卡车作业周期时间
匹配卡车数=-------------------- 或
入换就位和装车时间
电铲小时能力
匹配卡车数=-------------------
电铲选型的最后一步是研究其它电铲机组的规格 和数量,从而选择最佳的电铲规格和机组规模方 案,以便把资本投资和作业成本降到最小值。
车铲比是电铲一卡车系统中最重要的匹配参数。 合理的铲车配合降低电铲欠车和卡车待装时间, 改善铲车利用,从而达到整个工艺系统不同的装载工作面和道路条件, 要求不同的卡车队规模,以达到铲车间的良好匹 配,并降低装载和运输成本。
中深孔爆破使用的钻机有牙轮钻,潜孔钻及各种 露天凿岩台车,在选择钻机时,首先要确定钻孔 直径,然后根据设计的每日矿岩总量,边坡处理 钻孔数量来选择钻机型号和数量。
钻机效率由以下诸因素决定:
1、牙轮钻设计台班效率 2、潜孔钻台班效率
钻机型号 KY-250
孔径(mm) 250
r×KH
式中 Ks-----松散系数
KH-----满斗系数,可如下选用:
容易挖掘的物料 0.95—1.0
中等挖掘条件 0.9 –0.95
困难挖掘条件 0.80-0.90
非常困难挖掘条件 0.70-0.80
r---实方容重,t/m3
求出勺斗规格后,为估计最大的悬持载荷,除每 次装的物料重量外还要加上估计的勺斗自重,并 据此选择电铲型号。
勺容比的最小值取决于技术条件。从装载矿岩块 度分析,V/E应大于或等于3-4;从卡车车体强 度考虑,V/E值应不小于2。
勺容比的最优值取决于车铲的最优利用。经验认 为,V/E的最佳值约为3-5。影响V/E值选择的 主要因素是运距和勺斗规格。
一般随运距增加,V/E值也相应增加。其原因是, 首先,随着运距增加,在卡车作业周期中装车时 间比重减小,增大V/E对电铲有利,对卡车也因 相应使入换、等装比重下降而产生有利影响。其 次,随卡车运距增大,采用大型卡车更为有利。
此外,破碎设备和选矿厂通常要求较高的供矿稳
定性。假如仅用一台电铲作业,而电铲的利用率 为80%时,那么将有20%的时间停产或者相当于 每年有73天停产,推知如果用5台电铲作业时, 全矿停产的概率几乎等于0。
3)矿岩块度
4)投资和经营费用。
在具有配矿要求和供矿稳定性的条件下,电铲规格可如下选择。
机手的熟练与否和钻孔效率、设备完好率关系很
大,现场工作环境条件、管理水平也对钻机效率 发挥有较大影响。
钻机选型
选择钻机应根据生产规模、岩石可钻性及可爆性、 大块标准、
管理水平,综合分析钻爆成本,在满足产量及质 量要求的前提下,选择综合钻爆成本最低的钻机 和钻孔直径。一个工地不宜选用多型号钻机,一 般是矿生产选用一种钻机,边坡处理选择一种钻 机, 离选用一种钻机,钻机数量不宜过少。
在单斗铲一卡车工艺系统中,铲车匹配的合理性 主要通过勺容比和车铲比体现。一般认为,在电 铲一卡车系统中,电铲的选型是基础,计算表明, 只要V/E值大于3,则卡车规格的大小对电铲生 产率的影响很小。共原因是卡车的入换时间不长, 且可通过采用合理采掘方法(如双侧折返入换)
把卡车的入换时间减到最低限度。经验也表明, 电铲和不同规格的卡车队匹配一般均可满足其需 要。
钻机数量的确定 钻机数量按下式计算
Q
L
N = ------ 或 N = -------
qp(1-e)
p1(1-e)
式中N---所需钻机数量,台;
Q—设计规模,t/a;
p—钻机年钻孔效率,m/a;
q—每米钻孔爆破量,t/m;
e—废孔率;
p1—钻机台班效率,m/台班; L—每班需钻孔米数,m。
岩石等级 (f)
162--1128
台班效率 (m)
2155--5305
台日效率 (m)
7500--115000
台年效率 (m)
2323550000000000000--
KY-310
310
162--1128
3255--7500
17000--125000
3405000000-
45R
250
8-20
60R
310
影响电铲规格选择的因素很多,主要考虑
露天矿矿岩生能力、工作线年推进度与工作台阶 上配铲数之间的合理匹配,
合理服务台数 应用规格较大的电铲,可简化系 统并降低装载费用,从而改善经济效果;另一方 面,服务台数将受制于配矿约束、供矿稳定性和 管理水平。
为了减小矿石品位波动,大部分开采作业需要某 种程度的矿内配矿。当需配矿时,一般用2-3台 电铲在指定工作面进行作业,通过储矿场的配矿 系统达到均匀混合,以满足规定的矿石品位。
年产量
所需日产量=--------------,t/d
实际生产日数
所需日产量
所需电铲能力=----------------------,t/d
供、配矿可靠性要求台数
日作业小时X3600
电铲每天工作周期数=-------------------,次/d
作业周期(s)
式中,日作业小时=(24-固定影响)×可变影响系数