硫酸锌溶液的净化工艺技术
硫酸锌的生产工艺
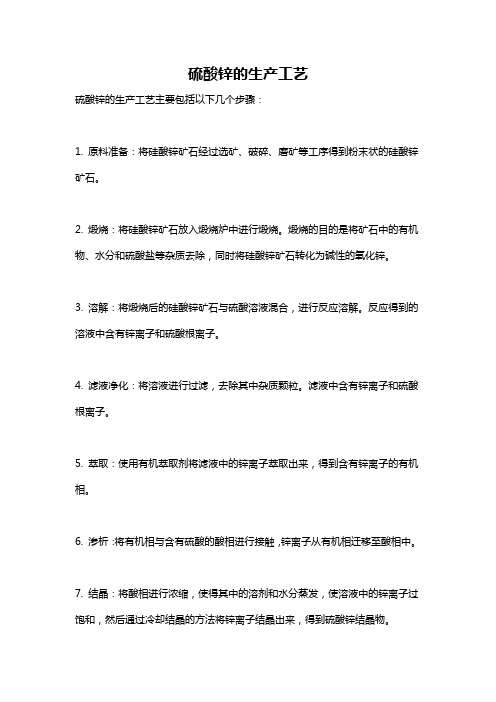
硫酸锌的生产工艺
硫酸锌的生产工艺主要包括以下几个步骤:
1. 原料准备:将硅酸锌矿石经过选矿、破碎、磨矿等工序得到粉末状的硅酸锌矿石。
2. 煅烧:将硅酸锌矿石放入煅烧炉中进行煅烧。
煅烧的目的是将矿石中的有机物、水分和硫酸盐等杂质去除,同时将硅酸锌矿石转化为碱性的氧化锌。
3. 溶解:将煅烧后的硅酸锌矿石与硫酸溶液混合,进行反应溶解。
反应得到的溶液中含有锌离子和硫酸根离子。
4. 滤液净化:将溶液进行过滤,去除其中杂质颗粒。
滤液中含有锌离子和硫酸根离子。
5. 萃取:使用有机萃取剂将滤液中的锌离子萃取出来,得到含有锌离子的有机相。
6. 渗析:将有机相与含有硫酸的酸相进行接触,锌离子从有机相迁移至酸相中。
7. 结晶:将酸相进行浓缩,使得其中的溶剂和水分蒸发,使溶液中的锌离子过饱和,然后通过冷却结晶的方法将锌离子结晶出来,得到硫酸锌结晶物。
8. 产品处理:对得到的硫酸锌结晶物进行烘干、筛分和包装等工序,得到最终的硫酸锌产品。
需要注意的是,硫酸锌的生产工艺可以根据不同的生产条件和需求进行调整和改进,上述工艺仅为常见的一种。
硫酸锌溶液锑盐净化工艺改造实践

Ab t a t I h r d c i n s s e o t lu g c lp a t i h i p rt s c n e t a i n i n ta n O4 s r c :n t e p o u to y t m fa me a l r ia l n ,h g m u ii o c n r t n i i l S e o i Z
炼 厂 , 中黄钾 铁矾 法 沉 铁 连续 浸 出 炼锌 生 产 线 于 其 20 0 3年建成 投产 , 设计 能力 为 年产 电 锌 5万 吨 。锌
应 过剩 的 0奈 酚对 电 解 的 电流 效 率不 利 , 须 用 活 一 必 性炭 吸 附残余试 剂 , 试剂 价格 昂贵 , 且 故采用 这两种 方法 的厂 家不 多 。砷盐 净 化 法 虽具 有 效 果好 、 本 成
摘 要 : 厂锌 系统 投 产 初 期 由于 新 液 中 A 、 b C 某 s S 、 o等 主 要 杂 质 含 量 偏 高 , 响 锌 电 解 生 产 , 过 对 净 化 影 通
工 艺 流 程 的 改 造 , 降 低 锌 粉 单 耗 的 同 时 , 化 了新 液 质 量 , 在 优 使锌 电解 生 产 步 入 正 轨 。 关 键 词 : 法 炼 锌 ; 液 净 化 ; 盐 法 湿 溶 锑 中图 分 类 号 : F 1 T 83 文献标识码 : A 文 章 编 号 :0 7 7 4 (0 0 0 —0 2 —0 1 0 — 5 5 2 1 )4 0 2 3
低 的 特 点 , 因 其 在 净 化 过 程 中 产 生 剧 毒 气 体 但 H。 , 在 国内较少 采用 。锑盐 净化 法具有 工 艺成 As故
一水硫酸锌的生产工艺流程

一水硫酸锌的生产工艺流程原料制备
锌粉:采用球磨机将粗锌粉研磨成细锌粉,粒度小于45μm。
硫酸:一般采用工业级硫酸,浓度为98%。
溶解
将锌粉加入硫酸中,在搅拌下缓慢加热至80℃左右,保持温度恒定,使锌粉完全溶解生成硫酸锌溶液。
净化
为了去除溶液中的杂质,如铁、铜等,可加入少量过氧化氢或高锰酸钾进行氧化处理。
反应后,加入活性炭吸附杂质。
过滤除去杂质。
结晶
将净化后的溶液冷却至40~60℃,并在搅拌下逐渐加入硫酸钠溶液,促进硫酸锌结晶析出。
结晶完成后,静置一段时间,使晶体生长至一定大小。
过滤与洗涤
将晶体浆液过滤,用冷水洗涤去除杂质。
为了获得更高纯度的产品,可重复多次过滤和洗涤步骤。
干燥
将洗涤后的晶体放入干燥箱中,在50~80℃下干燥至恒重。
粉碎
将干燥后的晶体粉碎成需要的粒度。
包装
将粉碎后的硫酸锌包装在干燥、密封的容器中。
工艺特点
该工艺简单易行,成本较低。
产品纯度高,符合工业标准。
生产过程中产生的废水和废渣较少,环境友好。
注意事项
反应过程中,应严格控制温度,避免生成亚硫酸锌。
净化过程中,氧化剂的用量应适中,过量会生成过氧化物。
结晶过程中,搅拌速度不宜过快,否则会导致晶体破碎。
干燥过程中,温度不宜过高,否则会导致晶体分解。
硫酸锌溶液置换沉淀法除铜镉钴镍.

用多倍于当量的锌粉。在许多场合下,用置换沉淀法有可能完全除去溶液中被置换的金属离
子。
表 2-4
在平衡状态下被置换金属与置换金属离子活度的比值( aMe1x ) aMe2y
置换金属
被置换金属
Zn
Cu
Fe
Cu
Ni
Cu
金属的标准电位,V
置换金属
-0.763 -0.440 -0.241
被置换金属
+0.337 +0.337 +0.337
+0.536 +0.798
Ag+,Ag
Ag++e→Ag
+0.799
Hg2+,Hg
Hg2++2e→Hg
Hale Waihona Puke +0.854Br(l),BrCl2(g),Cl-
1/2Br2+e→Br1/2Cl2+e→Cl-
+1.066 +1.358
Au+,Au
Au++e→Au
+1.50
F2(g),F-
1/2F2++e→F-
+2.85
2.1.1.2 置换沉淀的应用
(1) 用主体金属除去浸出液中的较正电性金属 如硫酸锌中性浸出液用锌粉置换脱铜、镉、钴和镍;镍钴溶液中用镍粉或钴粉置换脱铜。 在锌湿法冶金中,广泛使用锌粉置换除去中性浸出液中的铜、镉、钴和镍。该法除铜比
较容易,当使用量为铜量的 1.2~1.5 倍的锌粉时,就能将铜彻底除尽。但除镉较困难,除 钴和镍更困难。
离子的析出电位随离子活度和温度而变,表 2-5 是锌和钴的离子析出电位随温度和离子 活度变化的情况。
硫酸锌生产工艺操作规程范文(二篇)
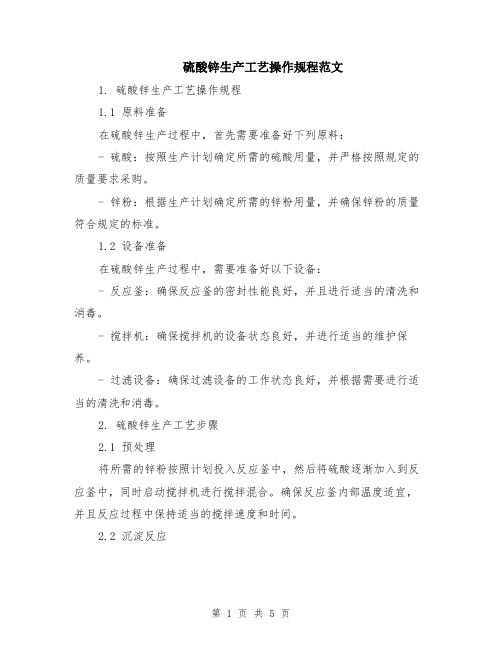
硫酸锌生产工艺操作规程范文1. 硫酸锌生产工艺操作规程1.1 原料准备在硫酸锌生产过程中,首先需要准备好下列原料:- 硫酸:按照生产计划确定所需的硫酸用量,并严格按照规定的质量要求采购。
- 锌粉:根据生产计划确定所需的锌粉用量,并确保锌粉的质量符合规定的标准。
1.2 设备准备在硫酸锌生产过程中,需要准备好以下设备:- 反应釜:确保反应釜的密封性能良好,并且进行适当的清洗和消毒。
- 搅拌机:确保搅拌机的设备状态良好,并进行适当的维护保养。
- 过滤设备:确保过滤设备的工作状态良好,并根据需要进行适当的清洗和消毒。
2. 硫酸锌生产工艺步骤2.1 预处理将所需的锌粉按照计划投入反应釜中,然后将硫酸逐渐加入到反应釜中,同时启动搅拌机进行搅拌混合。
确保反应釜内部温度适宜,并且反应过程中保持适当的搅拌速度和时间。
2.2 沉淀反应在反应釜内加热的同时,继续搅拌混合,使锌粉与硫酸充分反应。
在反应过程中,控制反应温度、时间和pH值,确保反应达到预期的目标。
2.3 过滤将反应釜中的混合物通过过滤设备进行过滤,将产生的硫酸锌溶液与废液分离。
确保过滤设备的工作稳定,并定期清洗和消毒以保持设备的正常工作状态。
2.4 淘洗将过滤得到的硫酸锌固体进行淘洗,以去除杂质的残留。
控制淘洗时间和水的用量,确保淘洗效果达到要求。
2.5 干燥将淘洗后的硫酸锌固体放置在适当的干燥器中,进行干燥处理。
确保干燥器的工作温度和时间符合要求,并进行定期的清洗和消毒。
2.6 包装完成硫酸锌固体干燥后,将其进行包装,并按照规定的要求进行标识和质量检测。
确保包装过程中的卫生和安全,以及包装的质量符合标准。
3. 安全注意事项3.1 生产操作时应戴好防护用品,如手套、安全镜等,确保操作人员的安全。
3.2 在硫酸锌生产过程中,应根据相关规定正确使用化学品,并妥善保管高浓度的硫酸,避免事故发生。
3.3 在反应过程中应注意控制反应温度,避免发生过热或爆炸的危险。
3.4 搅拌机的使用应注意安全保护措施,避免意外伤害。
硫酸锌的生产工艺原理
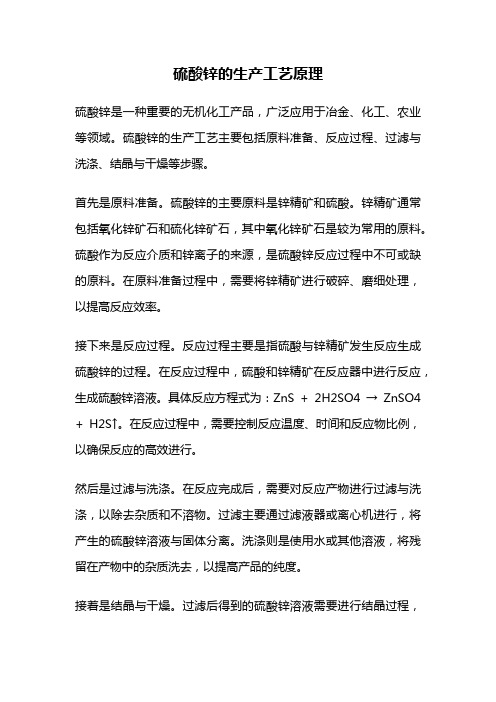
硫酸锌的生产工艺原理硫酸锌是一种重要的无机化工产品,广泛应用于冶金、化工、农业等领域。
硫酸锌的生产工艺主要包括原料准备、反应过程、过滤与洗涤、结晶与干燥等步骤。
首先是原料准备。
硫酸锌的主要原料是锌精矿和硫酸。
锌精矿通常包括氧化锌矿石和硫化锌矿石,其中氧化锌矿石是较为常用的原料。
硫酸作为反应介质和锌离子的来源,是硫酸锌反应过程中不可或缺的原料。
在原料准备过程中,需要将锌精矿进行破碎、磨细处理,以提高反应效率。
接下来是反应过程。
反应过程主要是指硫酸与锌精矿发生反应生成硫酸锌的过程。
在反应过程中,硫酸和锌精矿在反应器中进行反应,生成硫酸锌溶液。
具体反应方程式为:ZnS + 2H2SO4 → ZnSO4 + H2S↑。
在反应过程中,需要控制反应温度、时间和反应物比例,以确保反应的高效进行。
然后是过滤与洗涤。
在反应完成后,需要对反应产物进行过滤与洗涤,以除去杂质和不溶物。
过滤主要通过滤液器或离心机进行,将产生的硫酸锌溶液与固体分离。
洗涤则是使用水或其他溶液,将残留在产物中的杂质洗去,以提高产品的纯度。
接着是结晶与干燥。
过滤后得到的硫酸锌溶液需要进行结晶过程,使溶液中的硫酸锌逐渐结晶出来。
结晶通常通过控制温度和浓度来进行。
在结晶过程中,硫酸锌晶体逐渐生长并沉淀,最终形成结晶体。
结晶后的硫酸锌需要进行干燥处理,以去除结晶中的水分,提高产品的稳定性和储存性。
在硫酸锌的生产过程中,还需要注意一些关键因素。
首先是反应条件的控制,包括反应温度、反应时间和反应物比例等。
合理的反应条件可以提高反应效率和产品质量。
其次是原料的质量和纯度,高质量的原料可以提高产品质量和产量。
此外,还需要注意生产过程中的安全和环保措施,确保生产过程安全可靠,并减少对环境的污染。
硫酸锌的生产工艺原理包括原料准备、反应过程、过滤与洗涤、结晶与干燥等步骤。
通过合理控制反应条件和原料质量,可以获得高质量的硫酸锌产品。
在生产过程中,还需要注意安全和环保措施,以确保生产的安全可靠性和环境友好性。
湿法锌工艺流程

湿法锌工艺流程
湿法锌工艺流程
湿法锌工艺是一种将锌从锌矿石中分离出来的方法,主要通过化学反应来实现。
下面是湿法锌工艺的一般流程:
1. 破碎与磨矿:先将锌矿石进行破碎,使其颗粒大小合适,然后进行磨矿,即用磨矿设备对矿石进行细磨。
这一步的目的是将矿石颗粒破碎并提高浸出效果。
2. 酸溶浸出:将磨矿后的锌矿与稀硫酸进行混合,然后加热反应。
这个步骤的主要目的是将锌矿石中的锌溶解出来,形成硫酸锌溶液。
3. 澄清过滤:将溶液经过澄清处理,去除其中的杂质和固体颗粒。
这一步的目的是提高后续步骤的反应效果。
4. 电积杂质去除:通过将硫酸锌溶液进行电解,使溶液中的其他金属离子在阳极处析出,从而去除杂质。
这一步的目的是提高锌的纯度。
5. 电积锌:将经过除杂的硫酸锌溶液电解,使锌在阴极处析出。
这样就可以将锌从溶液中沉积出来,得到纯净的锌产品。
6. 锌收集与干燥:将电积出来的锌收集起来,并加以干燥处理。
这一步的目的是得到锌的成品。
7. 浸出液处理:将溶液中的杂质进行处理,使其变为无害物质。
这样可以减少环境污染。
总的来说,湿法锌工艺是一种通过溶解、电解和沉积等步骤将锌从锌矿石中分离的方法。
经过多个步骤的反应、过滤和处理,最终可以得到纯净的锌产品。
这种工艺具有高效、环保的优点,被广泛应用于各种锌矿石的处理中。
但是,由于涉及到一系列的化学反应和设备操作,工艺过程中还需要严格控制各参数和操作条件,以确保工艺的稳定性和产品质量。
硫酸锌工艺知识培训

的把反应终点PH 值控制到5o 具体硫酸锌工艺知识培训一、硫酸锌工艺操作流程生产硫酸锌分为五步:浸锌、浸渣、净化、浓缩、结晶包装入库1、浆化浸出反应机理:ZnO (固)+ H 2SO 4 (液)=ZnSO4 (液)+HQ (液)为了保证浸出液的质量和提高锌的回收率,采用中性(或弱酸性)浸出, 即先将锌矿料和二次浸出液加入浆化池稀释成浆状,然后慢慢加入 硫酸。
把浸渣液打入运转的调浆池中,加入氧化锌,调成糊状,打开排风扇,加 入硫酸反应,反应过程PH 值控制在2左右。
反应1个小 时后,把浸好作要点:渣回收母①中浸液比重约为1 -36g/L具体操作是: 将先是氧化除铁,在除铁过程中,是用双氧水作为氧化增大消耗量。
反应若合格进行压滤, 若不② 温度约为85°C③ 用试纸检测浸出终点的PH 为5o2、酸性浸出(即二段浸出)浸锌压滤后的滤饼去二次酸浸,即浸渣。
把物料中残余的锌再次加酸浸出,PH 值控制在0.5以下,反应4个小 时,压滤。
压滤的酸液返回浸锌,循环使用。
二次渣装袋堆存,要求二次 渣含锌不大于 7% o滤 渣投入二次酸浸池,加入适量的硫酸进行搅拌反应。
① 使酸浸渣中含硫酸在1—5g/L,即PH 值0.5② 反应时间约4小时 ③温度应保持在80°C 以上④酸浸时,液固比为5:1 o3、浸出液中含有其他的金属杂质,一般有铁、镉、铜、铅等微 量 元素,所以需要加入氧化剂进行除杂。
一、除铁,二、净化。
剂,在中性 介质将二价铁氧化成三价铁,继而水解形成氢氧化铁沉 淀,通过固液分离而把铁除去。
反应过程中用氧化锌调PH,使溶液 PH 值控制在5,以利于铁的氧化水解而形成沉淀,反应温度在约为55度。
加入双氧 水的管必须伸到反应液面以下,以免双氧水分解而合格继续加双氧水反 应,直到铁元素合格为止。
(1)除(2)净化检测镉是否合格,检测合格后及时停止搅拌立锌粉送化二¥孟小于(一)一次净化:除完铁合格后的硫酸锌溶液进入净化工序;净化工序的原理是用锌粉将硫酸锌溶液中镉、铜等杂质置换除去。
- 1、下载文档前请自行甄别文档内容的完整性,平台不提供额外的编辑、内容补充、找答案等附加服务。
- 2、"仅部分预览"的文档,不可在线预览部分如存在完整性等问题,可反馈申请退款(可完整预览的文档不适用该条件!)。
- 3、如文档侵犯您的权益,请联系客服反馈,我们会尽快为您处理(人工客服工作时间:9:00-18:30)。
硫酸锌溶液的净化工艺技术一、硫酸锌溶液成分及其净化方法锌焙砂或其他的含锌物料(如氧化锌烟尘、氧化锌原矿等)经过浸出后,产出中性浸出液,虽然在浸出过程中通过控制终点酸度使Fe3+完全水解沉淀的同时,除去了砷、锑等部分杂质,但是残存的许多杂质(如Cu,Cd,CO,Ni,AS,Sb,Ge等)对锌电解沉积过程有极大危害,会使电解电流效率降低、增加电能消耗、影响阴极锌质量、腐蚀阴极和造成剥锌困难等。
因此,必须通过溶液净化,将危害锌电积的所有杂质除去,产出合格净化液才能送至锌电解槽。
中彭化工环保技术生产。
表1 中性浸出液的成分范围及平均含量(g/L)净化的目的是将中性浸出液中的铜、镉、钴、镍、砷、锑等杂质除至电积过程的允许含量范围之内,确保电积过程的正常进行并生产出较高等级的锌片。
同时,通过净化过程的富集作用,使原料中的有价伴生元素,如铜、镉、钴、铟、铊等得到富集,便于从净化渣中进一步回收有价金属成分。
净化方法按其净化原理可分为两类:①加锌粉置换除铜、镉,或在有其他添加剂存在时,加锌粉置换除铜、镉的同时除镍、钴。
根据添加剂成分的不同该类方法又可分为锌粉-砷盐法、锌粉-锑盐法、合金锌粉法等净化方法;②加有机试剂形成难溶化合物除钴,如黄药净化法和亚硝基β-萘酚净化法。
各种净化方法的工艺过程概要列于表2。
表2 各种硫酸锌溶液净化方法的几种典型流程从表2可以看出,由于各厂中性浸出液的杂质成分与新液成分控制标准不同,故各厂的净化方法亦有所差别,且净化段的设置亦不同。
按净化段的设置不同,净化流程有二段、三段、四段之分。
按净化的作业方式不同有间断、连续作业两种。
间断作业由于操作与控制相对较易,可根据溶液成分的变化及时调整组织生产,为中、小型湿法炼锌厂广泛应用。
连续作业的生产率较高、占地面积少、设备易于实现大型化、自动化,故近年来发展较快,但该法操作与控制要求较高。
由于铜、镉的电位相对较正,其净化除杂相对容易,故各工厂都在第一段优先将铜、镉首先除去。
利用锌粉置换除铜、镉时,由于铜的电位较镉正,更易优先沉淀,而锌粉置换除镉则相对困难些,需加入过量的锌粉才能达到净化的要求。
由于钴、镍是浸出液中最难除去的杂质,各工厂净化工艺方法的差异(表2)实质上就在于除钴方法的不同。
采用置换法除钴、镍时除需加添加剂外,还要在较高的温度下,并加入过量的锌粉才能达到净化要求。
或者使用价格昂贵的有机试剂,合理选择除钴净化工艺可降低净化成本。
二、锌粉置换除铜、镉(一)置换法除铜、镉的基本反应由于锌的标准电位较负,即锌的金属活性较强,它能够从硫酸锌溶液中置换除去大部分较正电性的金属杂质,且由于置换反应的产物Zn2+进入溶液而不会造成二次污染,故所有湿法炼锌工厂都选择锌粉作为置换剂。
金属锌粉被加入到硫酸锌溶液中便会与较正电性的金属离子如Cu2+,Cd2+等发生置换反应。
因Cu,Cd,Co,Ni四种金属的标准电极电位都较锌为正,但由于铜的电位较锌的电位正得多,所以Cu2+能比Cd2+,Co2+,Ni2+更容易被置换出来。
在生产实践中,如果净化液中其他杂质成分能满足电积要求,那么Cu2+则完全能够达到新液质量标准。
湿法炼锌厂浸出液含锌一般在150g/L左右,锌电极反应平衡电位为-0.752V。
那么上述置换反应就可以一直进行到Cu,Cd,Co,Ni等杂质离子的平衡电位达到-0.752V时为止,即从理论上讲这些杂质金属离子都能被置换得很完全。
但这仅仅是从热力学角度通过计算得到的结果,与实际情况有很大偏差。
例如,从热力学数据比较,钴的平衡电位比镉的平衡电位相对较正,应当优先于镉被置换沉淀,但由于Co2+还原析出的超电压较高的缘故,实际上Co难以被锌粉置换除去,甚至几百倍理论量的锌粉也难以将Co除去至锌电积的要求。
结果刚好相反,因此在生产上需要通过采取其他的措施才能将钴从溶液中置换沉淀出来。
(二)置换过程的影响因素由于铜、镉较易除去,故大多数工厂都选择在同一段将铜、镉同时除去,该置换过程受以下几个方面的影响:1、锌粉质量置换除Cu,Cd应当选用较为纯净的锌粉,除了可避免带入新的杂质外,同时减少锌粉的用量。
由于置换反应是液相与固相之间的反应,故反应速度主要取决于锌粉的比表面积,因此,锌粉的表面积越大,溶液中杂质成分与金属锌粉接触的机会就越多,反应速度越快。
但是,过细的锌粉容易漂浮在溶液表面,也不利于置换反应的进行。
由于净化用锌粉在制备、贮藏等过程中均不可避免地有部分表面氧化,使锌粉的置换能力大大降低,故有的工厂在净化时首先用废液将净化前液酸化,使锌粉表面的ZnO与硫酸发生反应,使锌粉呈现新鲜的金属表面,以提高锌粉的置换反应能力。
应当指出,溶液酸化必须适当,酸度过低则难以达到目的,酸度过高则会增加锌粉耗量,一般工厂控制酸化PH值为3.5~4.0。
如果采用一次加锌粉同时除Cu和Cd,一般要求锌粉的粒度为-0.149~-0.125mm。
但有的工厂由于浸出液含铜较高,故采用两段分别除铜和镉。
例如比利时巴伦电锌厂,当溶液含铜超过400mg/L时,首先加粗锌粉沉铜。
飞龙实业有限责任公司当溶液含铜超过500mg/L时,加入粗锌粉将铜首先沉积下来,产出海绵铜后再将溶液送至除镉工段。
在单设的除镉工序则可选用粒度相对较粗的锌粉。
2、搅拌速度由于置换反应是液相与固相之间的反应,提高搅拌速度有利于增加溶液中Cu2+和Cd2+与锌粉相互接触的机会,另外,搅拌还能促使已沉积在锌粉表面的沉积物脱落,暴露出锌粉的新鲜表面,有利于反应的进行。
同时,加强搅拌更有利于被置换离子向锌粉表面扩散,从而达到降低锌粉单耗的目的。
但搅拌强度过高对反应速度的提高并无明显改善,反而增加了能耗,造成净化成本上升,因此选择适宜的搅拌强度是很重要的。
为了强化生产,有的工厂在净化除铜、镉时采用流态化净液槽。
锌粉置换除铜、镉时的搅拌方式应该采用机械搅拌,若采用空气搅拌则会使锌粉表面氧化而出现钝化现象,另外,空气中的氧会使已置换析出的铜、镉发生复溶。
3、温度提高温度可以提高置换过程的反应速度与反应进行的完全程度,但提高温度也会增加锌粉的溶解以及已沉淀析出的镉的复溶。
所以加锌粉置换除Cu,Cd应控制适当的反应温度,一般为60℃左右。
研究表明,镉在40~45℃之间存在同素异形体的转变点,温度过高会促使镉复溶。
4、浸出液的成分浸出液含锌浓度、酸度与杂质含量及固体悬浮物等,均影响置换反应的进行。
浸出液含锌浓度较低则有利于置换过程中锌粉表面Zn2+向外扩散,但浓度过低则有利于氢气的析出,从而增大锌粉消耗量。
故生产实践一般控制浸出液含锌量在150~180g/L为宜。
溶液酸度越高则越有利于氢气的析出,从而产生无益的锌粉损耗,并促使镉的复溶。
生产实践中,为使净化溶液残余的Cu,Cd达到净化要求,须维持溶液的PH 值在3.5以上。
5、副反应的发生尽管在浸出过程中已将大部分的AS,Sb通过共沉淀的方法除去,但仍有一定量的AS,Sb存在于浸出液中,置换过程中尤其在酸度较高的情况下,在实际溶液PH值条件下,不可避免地产生剧毒的AsH3和SbH3气体(后者很不稳定,在锌电积条件下SbH3容易分解),因此,应在浸出段尽可能将砷、锑完全除去。
另外,在生产中应加强工作场地的通风换气,确保生产安全。
(三)镉复溶及避免镉复溶的措施前已述及,镉的复溶与温度有很大的关系,故须控制适宜的操作温度。
另外,生产实践表明镉的复溶还与时间、渣量以及溶液成分等因素有关。
其中铜、镉渣与溶液的接触时间长短对镉的复溶影响较大。
由于置换析出的铜、镉渣与溶液接触的时间越长则置后液含镉越高,故净化作业结束后应快速进行固液分离。
生产实践表明,溶液中铜、镉渣的渣量也对镉复溶有很大影响,渣量越多则镉复溶越厉害,故在生产过程中应定期清理槽罐,采用流态化净化时应尽量缩短放渣周期。
溶液中的杂质AS,Sb的存在,不仅增加锌粉的单耗,也促使镉的复溶。
因此中性浸出时应尽可能将这些杂质完全除去。
此外,还需要控制好中性浸出液中Cu2+的浓度,铜离子的浓度控制在0.2~0.3g/L为宜。
为尽量避免除铜、镉净化过程中镉的复溶,生产实践中除控制好操作技术条件外,还须控制好适宜的锌粉过量倍数,有的工厂在除铜、镉中将锌粉分批次投入,并在净化压滤前投入少量锌粉压槽,并通过增加铜、镉渣中的金属锌粉量来减少镉的复溶。
(四)置换法除铜、镉的主要技术条件控制湿法冶金工厂由于原料差异原因,有的工厂浸出液含铜高,采用二段净化分别沉积铜、镉,但大部分工厂都在同一净化段同时除铜、镉。
其主要技术条件列于表3。
由于各厂溶液成分有差异,故置换铜镉后液成分亦有不同,且产出的铜镉渣的化学成分也不同,一般来说,铜镉渣含锌38%~42%,含铜4%~6%,含镉8%~16%。
产出的铜镉渣送综合回收铜、镉和其他有价伴生金属。
表3 置换除铜镉的主要技术条件三、有机试剂法除钴、镍有机试剂沉淀法除钴是通过试剂与溶液中钴、镍等杂质形成难溶的化合物被除去的方法。
目前在生产上应用的有机试剂除钴法有黄药除钴和α亚硝基-β萘酚除钴法。
四、除去氟氯及其他杂质的净化方法中性浸出液中的氟、氯、钾、钠、钙、镁等离子含量如超过允许范围,也会对电解过程造成不利影响,可采用不同的净化方法降低它们的含量。
(一)除氯一般情况下,氯的主要来源是锌烟尘中的氯化物及自来水中的氯离子。
溶液中氯离子的存在会腐蚀锌电解过程的阳极,使电解液中铅含量升高而降低析出锌品级率,当溶液含氯离子高于100mg/L时应净化除氯。
常用的除氯方法有硫酸银沉淀法、铜渣除氯法、离子交换法等。
1、硫酸银沉淀除氯是往溶液中添加硫酸银与氯离子作用,生成难溶的氯化银沉淀。
该方法操作简单,除氯效果好,但银盐价格昂贵,银的再生回收率低。
2、铜渣除氯是基于铜及铜离子与溶液中的氯离子相互作用,形成难溶的氯化亚铜沉淀。
用处理铜镉渣生产镉过程中所产的海绵铜渣(25%~30%Cu、17%Zn、0.5%Cd)作沉氯剂。
过程温度45~60℃,酸度5~10g/L,经5~6h搅拌后可将溶液中氯离子从500~1000mg/L降至100mg/L以下。
3、离子交换法除氯是利用离子交换树脂的可交换离子与电解液中待除去的离子发生交互反应,使溶液中待除去的离子吸附在树脂上,而树脂上相应的可交换离子进入溶液。
国内某厂采用国产717强碱性阴离子树脂,除氯效率达50%。