铸造新技术
目前世界最先进的的铝铸造技术大全

目前世界最先进的的铝铸造技术大全本文由全球铝业网 () 编辑,转载请注明出处,十分感谢!美国Wagastaff(瓦格斯塔夫)公司是世界著名铝材铸造设备公司,以向全球铝工业提供DC铸造设备而闻名全世界,不但如此,而且它还拥有许多先进的铝材铸造技术。
1.AirSlip气滑铸造技术AirSlip气滑铸造技术是Wagastaff公司最重要工艺,于1982年开发并投入市场。
到目前为止,全球的铸造车间大约拥有800条气滑铸造生产线,由于采用该技术生产出的产品质量好,一直是铝材生产厂家的首选技术。
AirSlip还有壳区小的特点,与使用传统铸造技术生产的产品相比,铸造速度更快,生产成本更有竞争力,产品晶粒结构均匀,缩短了均质化周期时间,在环保方面的优势是油耗最小,降低了冷却水流速。
2.LHC铝板坯铸造技术LHC铝板坯铸造技术是Wagastaff公司研究开发的新技术,其质量可以和电磁铸造技术生产的板坯质量相比,但生产成本却比电磁铸造生产板坯低一些。
LHC铸造的板坯具有产品质量优异、成品率高、产生废料少、能耗低、性能可靠的特点,并且由于冷却水流速低,节省能源。
LHC铝板坯铸造技术的突出特点是在板坯模上采用了油保持系统(oilretentionsystem),在铸造过程中主要省去了到达冷却水系统的模润滑油。
油保持系统的连续润滑降低了处理冷却水的相关成本。
油保持系统在采用模台倾斜系统时停止了模润滑油的滴流,降低了铸造台周围的“油喷溅”,并使进入冷却水系统的油较少,从而使在铸造台周围的工作人员减少走路打滑的现象。
3.保证铸造安全的StopCast技术为保证在铸造过程中操作人员的安全,Wagastaff公司开发研制出铝水池漏探测系统一StopCast系统,该系统在挤压坯铸造过程中探测到有铝水泄漏时会自动断开连续铝水流,所需时间仅仅为几秒;没有安装StopCast系统,则关断连续铝水流则要几分钟,甚至更长时间。
对于采用AirSlip挤压铸造技术和StopCast技术生产线的进一步开发仍在进行中。
铸造技术的发展现状与前景探究

铸造技术的发展现状与前景探究铸造技术是一种广泛应用的金属加工工艺,其发展对于工业生产具有重要意义。
随着现代制造业的不断发展和需求的不断增加,铸造技术也得到了迅速的发展并取得了较大的成就。
本文将对铸造技术的发展现状进行探究,并展望其未来的发展前景。
一、铸造技术的发展现状1. 传统铸造技术传统铸造技术主要包括砂型铸造、金属型铸造、压力铸造等。
这些技术在工业生产中应用广泛,具有成本低、工艺简单等优点。
但是传统铸造技术也存在一些问题,如生产效率低、能源消耗大、材料利用率低等,不能完全满足现代工业对高质量、高效率、节能环保的需求。
随着科技的不断进步,先进铸造技术不断涌现,如精密铸造技术、数字化铸造技术、快速凝固铸造技术等。
这些新技术在提高铸造件的精度、降低能耗、改善材料利用率等方面具有明显优势。
先进铸造技术也在发展中遇到了一些挑战,例如技术成熟度不高、设备投资大等问题,需要不断进行技术改进和创新。
随着人工智能、大数据、云计算等技术的不断发展,智能化铸造技术也逐渐走进人们的视野。
智能化铸造技术通过智能装备、智能控制系统等手段,实现铸造过程的自动化、智能化,极大地提高了生产效率和产品质量,降低了生产成本。
智能化铸造技术的发展将有效推动铸造行业向数字化、智能化方向转变。
数字化铸造技术是近年来的热门发展方向,它通过数字化建模、仿真分析等手段,对铸造过程进行全面监控和优化。
数字化铸造技术的发展将引领铸造行业向数字化制造方向转变,实现生产智能化、灵活化、高效化。
2. 绿色铸造技术的推广随着环保意识的增强,绿色铸造技术也受到了越来越多的关注。
各种新型的绿色铸造材料和清洁生产技术不断涌现,有力地推动了铸造行业向绿色化转型。
绿色铸造技术的发展将有效解决传统铸造技术存在的环境污染和资源浪费等问题。
3. 智能化铸造技术的应用铸造技术发展现状良好,同时面临的挑战和机遇也在不断增加。
只有不断进行技术创新和提高,才能更好地满足现代制造业对高质量、高效率、节能环保的需求,铸造技术必将迎来更加美好的未来。
新型铸造技术的研究及应用

新型铸造技术的研究及应用随着工业化的不断发展,铸造技术作为制造行业的重要基石,在技术的持续改进和创新中也得到了长足的发展。
近年来,新型铸造技术的研究和应用,为铸造行业带来了新的发展机遇。
一、新型铸造技术的研究1.1 数字化铸造技术数字化铸造技术是一种集成了数字化设计、数字化模拟、数控加工等多种先进技术的铸造生产方式。
主要通过对铸造工艺进行数字化仿真,优化铸造参数设置,提高生产效率和产品质量。
其中,CAD/CAM技术和虚拟样机技术是数字化铸造技术的核心。
1.2 新材料铸造技术新材料铸造技术是指应用新材料和新工艺技术进行铸造。
这种技术能够满足特定材料的需求,如高性能合金、超导材料等,同时还可以降低能耗和环境污染。
1.3 先进成形技术先进成形技术是一种通过快速成形技术制造金属原型的铸造技术。
它采用了激光喷粉和激光熔化成形、电子束烧结和光敏树脂快速成型等多种技术手段,可以实现一次成形,并且工艺稳定可靠,能够有效改善金属成形的精度和质量。
二、新型铸造技术的应用2.1 轻量化汽车零部件铸造随着汽车工业和环保意识的不断提高,轻量化汽车零部件的需求也越来越大,而新型铸造技术的应用,则可以有效地解决这一问题。
比如,采用先进的高强度铝材料,或采用热成型、注压成型等先进技术生产部件,可以将汽车的重量减轻15%-20%。
2.2 航空航天领域铸造航空航天领域对铸造技术的要求尤为高。
而数字化铸造技术和新材料铸造技术则可以为航空航天领域带来更高的科技含量。
比如,使用高强度合金材料,采用虚拟样机技术进行设计和仿真,可以有效的提高飞机的安全性和性能。
2.3 家电产品铸造家电产品作为大众化产品,对铸造的要求较高。
而先进成型技术的应用,则可以大幅提高产品的生产效率和质量。
比如,使用激光喷粉和激光熔化成形技术代替传统的生产方式,可以有效地提高家电产品的质量和生产效率。
三、新型铸造技术未来的发展趋势随着科技的不断推进,新型铸造技术也在不断的发展和创新。
铸造技术未来的发展方向

铸造是现代机械制造工业的基础工艺之一。
铸造作为一种金属热加工工艺,在我国发展逐步成熟。
铸造机械就是利用这种技术将金属熔炼成符合一定要求的液体并浇进铸型里,经冷却凝固、清整处理后得到有预定形状、尺寸和性能的铸件的能用到的所有机械设备,又称铸造设备。
新的铸造技术,可举出下述七个方面:(1)向轻量化挑战,超微细化和超薄壁化。
很多采用砂型铸件,在于砂子有适当的耐火性、砂型有使瓦斯通过的通气性、价格便宜、可反复利用,砂型毕竟是原始的,但依然是铸造法的主流。
通常砂型的铸造技术,在砂粒空隙(0.1mm)以下是不行。
历来代表小型铸件是加牙齿的齿套。
中川公司等利用精铸技术试制成音盘,使声音可以再生。
野口公司制作出如蚂蚁大小的铸件,用0.7微米的铝氧粉造型用离心铸造,蚂蚁的义眼模样也可以再生出来。
这方面铸造的开展会引起新的需求。
薄壁化是以压铸为中心而发展起来的,是利用高压的压铸法。
例如平均为1.0mm以下音频箱壳就是用1200吨压铸机高速铸造法制造出来的。
这种薄壁化的进展会加速铸件取代板金件。
在压铸中有效地利用芯子,从而由于中空而达到轻量化的目的。
例如增压器的叶轮过去都用重力铸造法生产的,在压铸法上用可旋转的金属芯子的方法开发出中空的叶轮。
用压铸法代替重力铸造从而取近净型的产品提高了效益。
(2)复杂形状部件的整体化;铸件一般多用于单体物件,最近已开始向复杂形状的部件发展。
例如将蜗轮增压器和排气岐管两种铸件合成整体,用耐热高速钢的减压吸引铸造法而铸成的最薄壁厚只有2mm的整体铸件。
(3)铸件焊接:迄今可焊接的都是钢件,最近铸铁件在具表面经过脱碳处理等工艺后也可以焊接了。
汽车用的铸件排气歧管和高速钢管焊接在一起,从面解决了由于铸铁件耐热性不足而采用了高速钢管的焊接结构以适应燃烧温度。
今后为达到廉价,性能好的目的分别制造焊接到一起的工艺也会有发展。
(4)触变铸造(半熔融铸造)液体固体在共存的状态下用高压方法进行铸造的一种方法。
铸造技术有哪些及应用

铸造技术有哪些及应用铸造技术是制造业中非常重要的一项技术,它通过将熔化的金属或其他材料注入到模具中,然后冷却固化,最终得到所需的零件或产品。
铸造技术由于其灵活性、高效性和成本效益,在各行各业都得到了广泛的应用。
铸造技术根据其工艺和原理的不同,可以分为多种类型,下面将介绍几种常见的铸造技术及其应用。
1. 砂型铸造砂型铸造是最常见的铸造技术之一,也是历史最久远的铸造方法。
它的原理是利用湿砂模具将熔融金属注入,再通过冷却和固化得到所需的零件。
砂型铸造适用于生产大批量的零件,成本较低,适用于各种大小和形状的工件。
它广泛应用于汽车、航空航天、机械制造等领域。
2. 精密铸造精密铸造是一种高精度、高要求的铸造技术,通常适用于生产精密零件和复杂结构的产品。
与砂型铸造不同,精密铸造采用金属模具,可以实现更高的精度和表面质量。
精密铸造技术广泛应用于航空航天、国防、医疗器械等领域。
3. 压铸压铸是一种通过高压将金属或合金注入到模具中,以实现快速充填和高精度的铸造技术。
压铸适用于生产尺寸精度高、表面质量好的复杂结构零件,广泛应用于汽车零部件、电子设备、家用电器等领域。
4. 精密铸造精密铸造技术是一种高精度的铸造工艺,适用于生产精密的、复杂的零件。
精密铸造通常采用金属模具,具有高精度和表面质量的优势,广泛应用于航空航天、国防和医疗器械等领域。
5. 液态金属注射成型液态金属注射成型技术是一种先进的铸造技术,它通过将金属融化后注入到模具中,实现高精度、高表面质量的成型。
该技术适用于生产高精度的复杂结构零件,广泛应用于汽车、航空航天、电子设备等行业。
6. 冷室压铸冷室压铸是一种在金属液态温度较低的情况下进行压铸成型的铸造技术。
它适用于生产具有高强度和高硬度要求的零件,广泛应用于汽车、摩托车、航空航天、船舶等领域。
这些铸造技术各有特点,适用于不同的生产需求和行业。
铸造技术在制造业中起着举足轻重的作用,它可以实现从小型零件到大型零件的生产,满足了各种工业领域对于材料和零件的需求。
铸造技术创新及其应用实践总结
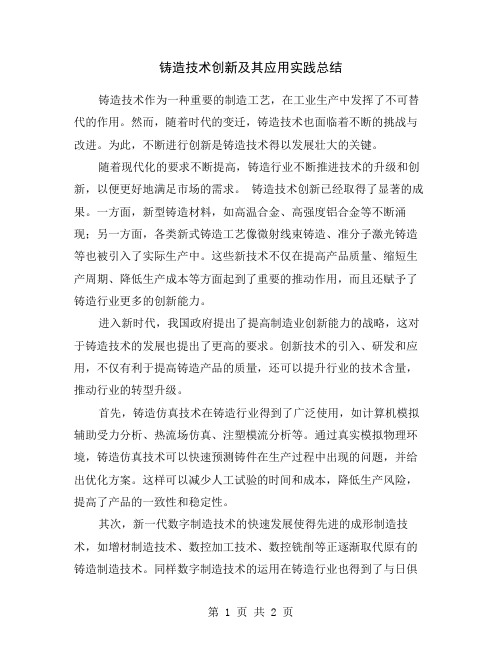
铸造技术创新及其应用实践总结铸造技术作为一种重要的制造工艺,在工业生产中发挥了不可替代的作用。
然而,随着时代的变迁,铸造技术也面临着不断的挑战与改进。
为此,不断进行创新是铸造技术得以发展壮大的关键。
随着现代化的要求不断提高,铸造行业不断推进技术的升级和创新,以便更好地满足市场的需求。
铸造技术创新已经取得了显著的成果。
一方面,新型铸造材料,如高温合金、高强度铝合金等不断涌现;另一方面,各类新式铸造工艺像微射线束铸造、准分子激光铸造等也被引入了实际生产中。
这些新技术不仅在提高产品质量、缩短生产周期、降低生产成本等方面起到了重要的推动作用,而且还赋予了铸造行业更多的创新能力。
进入新时代,我国政府提出了提高制造业创新能力的战略,这对于铸造技术的发展也提出了更高的要求。
创新技术的引入、研发和应用,不仅有利于提高铸造产品的质量,还可以提升行业的技术含量,推动行业的转型升级。
首先,铸造仿真技术在铸造行业得到了广泛使用,如计算机模拟辅助受力分析、热流场仿真、注塑模流分析等。
通过真实模拟物理环境,铸造仿真技术可以快速预测铸件在生产过程中出现的问题,并给出优化方案。
这样可以减少人工试验的时间和成本,降低生产风险,提高了产品的一致性和稳定性。
其次,新一代数字制造技术的快速发展使得先进的成形制造技术,如增材制造技术、数控加工技术、数控铣削等正逐渐取代原有的铸造制造技术。
同样数字制造技术的运用在铸造行业也得到了与日俱增的应用,打造了智能、高精度、自动化的铸造生产线,提高了生产效率和生产质量。
此外,新型的表面导向制造技术、高能密度表面制备技术、表面纳米处理等新技术也正带动着铸造生产的迈向高效化和高附加值的方向。
表面处理技术在提高产品表面性能、增大材料表面能、加速反应速率等方面具有广泛的应用。
在铸造加工中,表面处理技术特别适用于提高表面粗糙度、硬度和耐磨性,促进产品的耐用度。
总的来说,铸造行业在技术创新与升级过程中,应重视提高创新能力,加速科技创新的步伐,走向高品质产品制造。
新铸造工艺技术
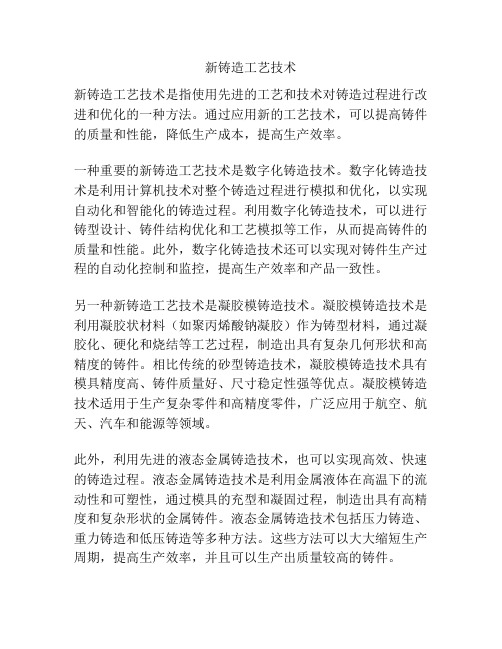
新铸造工艺技术
新铸造工艺技术是指使用先进的工艺和技术对铸造过程进行改进和优化的一种方法。
通过应用新的工艺技术,可以提高铸件的质量和性能,降低生产成本,提高生产效率。
一种重要的新铸造工艺技术是数字化铸造技术。
数字化铸造技术是利用计算机技术对整个铸造过程进行模拟和优化,以实现自动化和智能化的铸造过程。
利用数字化铸造技术,可以进行铸型设计、铸件结构优化和工艺模拟等工作,从而提高铸件的质量和性能。
此外,数字化铸造技术还可以实现对铸件生产过程的自动化控制和监控,提高生产效率和产品一致性。
另一种新铸造工艺技术是凝胶模铸造技术。
凝胶模铸造技术是利用凝胶状材料(如聚丙烯酸钠凝胶)作为铸型材料,通过凝胶化、硬化和烧结等工艺过程,制造出具有复杂几何形状和高精度的铸件。
相比传统的砂型铸造技术,凝胶模铸造技术具有模具精度高、铸件质量好、尺寸稳定性强等优点。
凝胶模铸造技术适用于生产复杂零件和高精度零件,广泛应用于航空、航天、汽车和能源等领域。
此外,利用先进的液态金属铸造技术,也可以实现高效、快速的铸造过程。
液态金属铸造技术是利用金属液体在高温下的流动性和可塑性,通过模具的充型和凝固过程,制造出具有高精度和复杂形状的金属铸件。
液态金属铸造技术包括压力铸造、重力铸造和低压铸造等多种方法。
这些方法可以大大缩短生产周期,提高生产效率,并且可以生产出质量较高的铸件。
总之,新铸造工艺技术的应用,不仅可以提高铸件的质量和性能,还可以降低生产成本,提高生产效率。
随着科技的不断发展和进步,新的铸造工艺技术将不断涌现,推动整个铸造行业向更加智能化、高效化的方向发展。
国外熔模铸造新材料和新工艺的发展概况

国外熔模铸造新材料和新工艺的发展概况一、熔模铸造技术概述熔模铸造是一种传统的金属铸造技术,它通过将金属加热到液态,然后倒入预先制作好的熔模中进行成型。
这种技术具有成型精度高、表面光洁度好等优点,广泛应用于汽车、航空航天、电子设备等领域。
二、国外熔模铸造新材料和新工艺的发展概况1. 新材料的应用在熔模铸造中,新材料的应用可以提高产品的性能和质量。
例如,在航空航天领域,采用高温合金材料可以提高部件的耐高温性能;在汽车领域,采用铝合金可以降低车身重量。
此外,还有一些新型材料如钛合金、镍基合金等也得到了广泛应用。
2. 新工艺的发展随着科技不断进步,新工艺也不断涌现。
其中最具代表性的是快速凝固技术和数控加工技术。
快速凝固技术是利用高速冷却来制备非晶态或细晶粒材料,提高材料的强度和硬度。
这种技术可以应用于熔模铸造中,制备出更加高性能的铸件。
数控加工技术则是通过计算机控制机床进行加工,可以实现高精度、高效率、低成本的生产方式。
这种技术可以应用于熔模铸造中,提高产品的加工精度和生产效率。
三、国外熔模铸造新材料和新工艺的应用案例1. 高温合金材料在航空领域的应用高温合金材料具有优异的耐腐蚀性和耐高温性能,在航空领域得到了广泛应用。
例如,美国通用电气公司采用了一种名为“单晶涡轮叶片”的部件,该部件采用了先进的熔模铸造技术,结合快速凝固技术制备出非晶态合金材料,从而实现了更好的性能。
2. 铝合金在汽车领域的应用铝合金具有轻质、强度高等特点,在汽车领域得到广泛应用。
例如,德国宝马公司采用了一种名为“i3”的电动车型,该车身采用了铝合金材料,从而实现了更轻量化的设计。
四、国外熔模铸造新材料和新工艺的未来发展趋势1. 绿色环保随着环保意识的不断提高,绿色环保已经成为了未来发展的重要趋势。
在熔模铸造中,采用可再生材料和节能减排技术将成为未来发展的方向。
2. 数字化制造数字化制造是将数字技术应用于制造业中,可以实现高效率、高精度、低成本的生产方式。
- 1、下载文档前请自行甄别文档内容的完整性,平台不提供额外的编辑、内容补充、找答案等附加服务。
- 2、"仅部分预览"的文档,不可在线预览部分如存在完整性等问题,可反馈申请退款(可完整预览的文档不适用该条件!)。
- 3、如文档侵犯您的权益,请联系客服反馈,我们会尽快为您处理(人工客服工作时间:9:00-18:30)。
53
2.半固态铸造生产过程
动画56 半固态成形工艺流程
54
表8 用于汽车前悬挂系统的SSM成形零件与铸铁零件的质量比较
零件名称 铸铁零件/kg SSM零件/kg 质量减少/kg 质量减少%
上控制臂:前端
上控制臂:后端 悬臂 驾驶控制杆 支撑 悬挂支架 减震器支架梁 驾驶控制杆支撑 架 万向节
0.73710
13.1 造型新方法
13.1.1 真空密封造型
真空密封造型又称真空薄膜造型、减压造型、负压造型或V法, 适用于生产薄壁、面积大、形状不太复杂的扁平铸件。 1.真空密封造型法的优点 (1)铸件尺寸精确, 能浇出2~3mm的薄壁部分。 (2)铸件缺陷少,废品率可控制到1.5%以下。 (3)砂型成本低,损耗少,回用率在95%以上。 (4)工作环境比较好,噪声小、粉尘少,劳动强度低。 2.真空密封造型法的缺点 (1)对形状复杂、高度较高的铸件覆膜成形困难。 (2)工艺装备复杂,造型生产率比较低。
件精度高、表面粗糙度低,工作安全、可靠、方便。
气冲造型的缺点是砂型最上部约 30mm的型砂达不到紧实要 求,因而不适用于高度小于150mm的矮砂箱造型。工装要求严格,
砂箱强度要求较高。
45
1.气冲紧实原理 气冲紧实过程可分成两个阶段,如动画52所示。 (1) 型砂自上而下加速并初步紧实阶段。在顶部气压迅速提高 的作用下,表面层型砂上下产生很大的气压差,使表面层型砂紧实 度迅速提高,形成一初实层。在气压的推动下,初实层如同一块高 速压板,以很大的速度向下移动,使下面的砂层加速并初步紧实。 (2) 运动的砂层自下而上冲击紧实 阶段。初实层继续向下移动和扩展,型 砂的紧实前锋很快到达模板,与模板发 生冲击;在冲击处,砂层运动突然滞止, 产生巨大的冲击力,使靠近模板的一层 型砂紧实度迅速提高;随后,冲击向上 发展,型砂由下而上逐层滞止,直到砂 层顶部为止。
轿车 载货汽车 造船业 管件 机床 一般工业 其他 总计
50
动画55 消失模铸造新发展示意图
13.2.3 快速原型制造技术
铸造模型的快速原型制造技术(RPM)是以分层合成工艺为基 础的计算机快速立体模型制造系统,包括分层合成工艺的计算机 智能铸造生产是最近几年机器制造业的一个重要发展方向。快速 原型制造技术集成了现代数控技术、CAD/CAM技术、激光技术 以及新型材料的成果与一体,突破了传统的加工模式,可以自动、 快速地将设计思想物化为具有一定结构和功能的原型或直接制造 零件,从而对产品设计进行快速评价、修改,以适应市场的快速 发展要求,提高企业的竞争力。 快速原型制造技术的工作原理是将零件的CAD三维几何模型, 输入到计算机上,再以分解算法将模型分解成一层层的横向薄层, 确定各层的平面轮廓,将这些模型数据信息按顺序一层接一层地 传递到分层合成系统。
58
2.特种铸造工艺的发展 随着现代工业对铸件的比强度、比模量要求的增加,以及 近净成形、净终成形的发展和特种铸造工艺向大型铸件方向发 展等,使铸造柔性加工系统得以推广,逐步适应多品种少批量 的产品升级换代需求。复合铸造技术(挤压铸造和真空吸铸) 和一些全新的工艺方法(快速凝固成形技术、半固态铸造、悬 浮铸造、定向凝固技术、压力下结晶技术、超级合金等离子滴 铸工艺等)逐步进入应用。
动画54 消失模铸造
48
2.消失模铸造特点和应用范围 消失模铸造主要用于形状结构复杂,难以起模或使用活块和外 型芯较多的铸件。与普通铸造相比,具有以下优点:工序简单、生 产周期短、效率高,铸件尺寸精度高 ( 造型后不起模、不分型,没 有铸造斜度和活块),精度达CT8级,可采用无黏结剂型砂,增大了 铸件设计的自由度,简化了铸造生产工序,降低了劳动强度。近年 来,消失模铸造技术在欧美发展很快(见表7)。 3.消失模铸造的新发展 消失模铸造用的泡沫塑料模与不断涌现的其他新材料、新设备、 新技术相结合,发展形成很多新的造型和铸造方法(如动画 55 所 示)。这些方法扩大了消失模铸造的应用范围,提高了铸造生产水 平。
49
表7 美国消失模铸造情况(生产和增长速度)
应 用 吨/年(1997年) 82.697 5.110 8.463 11.057 7.018 7.105 19.026 140.676 增长速度% (1994~1997年) 13 44 65 163 6 19 60 27 增长速度% (1997~2000年) 52 232 43 200 15 45 168 83
金属材料及工艺(第二版)
铸造篇之 铸造新技术
主讲:
铸造生产的机械化自动化程度在不断提高的同时,将更 多地向柔性生产方面发展,以扩大对不同批量和多品种生产 的适应性。节约能源和原材料的新技术将会得到优先发展, 少产生或不产生污染的新工艺新设备将首先受到重视。质量 控制技术在各道工序的检测和无损探伤、应力测定方面,将 有新的发展。 铸造产品发展的趋势是要求铸件有更好的综合性能,更 高的精度,更少的加工余量和更光洁的表面。此外,节能的 要求和社会对恢复自然环境的呼声也越来越高。为适应这些 要求,新的铸造合金将得到开发,冶炼新工艺和新设备将相 应出现。
在计算机的控制下,由激光器或紫外光发生器逐层扫描塑 料、复合材料、液态树脂等成形材料,在激光束或紫外光束作 用下,这些材料将会发生固化、烧结或粘结而制成立体模型。 用这种模型作为模样进行熔模铸造、实型铸造等,可以大大缩 短铸造生产周期。 目前,正在应用与开发的快速原型制造技术有以分层叠加 合成工艺为原理的激光立体光刻技术(SLA)、激光粉末选区烧结 成形技术(SLS)、熔丝沉积成形技术(FDM)、叠层轮廓制造技术 (LOM)等多种工艺方法。每种工艺方法原理相同,只是技术有所 差别。 (1) 激光立体光刻技术(SLA)。采用SLA成形方法生产金属零 件的最佳技术路线是:SLA原型(零件型)→熔模铸造(消失模铸 造)→铸件,主要用于生产中等复杂程度的中小型铸件。
铸造技术的发展趋势(续)
59
3.特殊性能合金进入应用 球墨铸铁、合金钢、铝合金、钛合金等高比强度、比模量 的材料逐步进入应用。新型铸造功能材料如铸造复合材料、阻 尼材料和具有特殊磁学、电学、热学性能和耐辐射材料进入铸 造成形领域。 4.微电子技术进入使用 铸造生产的各个环节已开始使用微电子技术。如铸造工艺 及模具的CAD及CAM,凝固过程数值模拟,铸造过程自动检测、 监测与控制,铸造工程 MIS ,各种数据库及专家系统,机器人 的应用等。
面上。 (2)放置砂箱,充填型砂,微振紧实。 (3)刮平,覆背膜,抽真空,使砂型保持一定的真空度。 (4)在负压状态下起模、下芯、合型浇注。铸件凝固后恢复常 压,型砂自行溃散,取出铸件。
43
动画51 真空密封造型
44
13.1.2 气流冲击造型
气流冲击造型简称气冲造型,是一种新的造型方法。其原理 是利用气流冲击,使预填在砂箱内的型砂在极短的时间内完成冲 击紧实过程。 气冲造型分低压气冲造型和高压气冲造型两种,低压气冲造 型应用较多。 气冲造型的优点是砂型紧实度高且分布合理,透气性好、铸
动画52 气冲造型紧实过程
46
2.气冲造型紧实度 (1)紧实度分布规律。气冲造型紧实度 如动画 53 所示,靠近模底板处紧实度最高, 随着与模底板的距离加大,紧实度逐步降 低。这样的分布即保证砂型分型面处及型 腔的高紧实度,又使型砂具有良好的透气 性。有利于得到表面粗糙度低、精度高的 铸件。气冲造型砂型紧实度分布最为合理。
65
61 62 47 43 55 29 稳,加工温度较低,模具寿命大幅提高,凝固时 间短,生产率高。 (2)铸件表面平整光滑,内部组织致密,气孔和偏析少;晶 粒细小,力学性能接近锻件。 (3)凝固收缩小,尺寸精度高,可实现近净成形、净终成形 加工。 (4)流动应力小,成形速度高,可成形十分复杂的零件。 (5)适宜于铸造铝、镁、锌、镍、铜合金和铁碳合金,尤其 适宜于铝、镁合金。
13.2 铸造新技术
13.2.1 半固态金属铸造
1.半固态金属铸造原理 半固态金属加工技术属21世纪前沿性金属加工技术(其生产过 程见动 画 56 ) 。 20 世 纪 70 年 代 麻省理 工 学院 ( MIT ) 弗 莱 明斯 (Flemings )教授发现金属在凝固过程中进行强烈搅拌或通过控制 凝固条件,抑制树枝晶的生成或破碎所生成的树枝晶,形成具有等 轴、均匀、细小的初生相均匀分布于液相中的悬浮半固态浆料。这 种浆料在外力作用下即使固相率达到 60%仍具有较好的流动性。可 利用压铸、挤压、模锻等常规工艺进行加工,这种工艺方法称为半 固态金属加工技术(简称 SSM )。表 8列出了用于汽车前悬挂系统 的SSM成形零件与铸铁零件的质量比较。
42
3.真空密封造型原理 真空密封造型是在特制砂箱内充填无水无黏结剂的型砂,用薄 而富有弹性的塑料薄膜将砂箱密封后抽成真空,借助铸型内外的压
力差(约40kPa)使型砂紧实和成形。
4.真空密封造型过程 真空密封造型过程如动画51所示,主要由以下几个步骤:
(1)通过抽气箱抽气,将预先加热好的塑料薄膜吸贴到模样表
动画53 气冲造型紧实度分布
(2) 影响紧实效果的主要因素。压力梯度是影响紧实度的主要 因素。所谓压力梯度是指作用在型砂上面先后的压力差dP与建压时 间dt之比。当dP/dt值愈大,铸型的紧实度愈高。
51
13.1.3 冷冻造型法
冷冻造型法又称低温硬化造型法,采用普通石英砂加入少量的 水,必要时还加入少量的黏土,按普通造型法制好铸型后送入冷冻 室,使铸型冷冻,借助于包覆在砂粒表面的冰冻水分而实现砂粒的 结合,使铸型具有很高的强度及硬度。浇注时,铸型温度升高,水 分蒸发,铸型逐步解冻,稍加振动立即溃散,可方便地取出铸件。 与其他造型方法相比,这种造型方法具有以下特点 (1)型砂成分简单,配置容易,铸件落砂清理方便,旧砂回用容 易,砂处理设备少。 (2)在造型、浇注、落砂过程中,产生的粉尘及有害气体少,符 合清洁生产的要求。 (3)铸型强度高、硬度大、透气性好,铸件表面光洁、缺陷少。