加工中心镗孔圆度超差故障分析与排除
加工中心精度不高原因分析及解决办法

加工中心因其在制造工业中保证了机械产品零件加工精度和产品质量稳定,所以在现代工业发展,机械制造中得到越来越广泛的应用。
但加工中心精度也时刻影响着机床加工工件的质量问题。
加工中心精度不高是什么原因引起?这种情况下在不考虑是机床的问题,加工中产生的误差造成加工工件的精度不高,如:1、计算失误造成的精度误差,人为因素,所以在加工工件前可以通过验算,试加工来排除。
2、材料变形引起的精度误差,需要加工前期采取相应的措施,加工时要采取相应的办法避免这种错误。
提升加工中心加工零件时精度加工精度就是零件加工后的几何参数,其与原图纸的理想几何参数差异越小,它的符合程度也就越高,加工精度也就越高。
在加工实践中,受到各种因素的影响,零件加工与理想几何参数存在较大的差异,这种偏差就是加工误差。
因此合理控制加工误差,就是提升加工精度的最佳方法。
而合理范围内的加工误差就是不超出零件设计要求的公差,只要在这个范围内,就能够进行零件加工精度的保证。
加工精度及加工误差都可以进行零件几何参数的评定。
加工误差的大小都能够影响加工精度的高低,通过对加工精度的有效控制,可以实现加工误差的减少,从而满足实际工作的要求。
在工作过程中,很多因素都影响到零件的加工精度。
即使使用同一种加工方法,在不同的工作环境下,它的精度也是不同的。
如果我们片面的追求零件的加工精度,就会导致生产效率的降低,从而导致工程成本的增加,为了满足实际工作的要求,我们必须要进行加工质量强化体系的应用,保证工作效率的有效提升,实现生产成本的有效控制。
在工作过程中,加工精度具体分为形状精度、位置精度、尺寸精度等,加工精度的高低变化,需要以形状公差、位置公差等来判断。
通过对试切法可以进行加工表面的试切,通过对试切所得尺寸的测量,可以满足零件的加工精度的要求。
过程中需要进行适当刀具的使用,做好不同数量的试切及测量工作,最终达到加工一个精度标准。
最后,就是对材料变形的问题处理,通过对零件变形问题的解决,可以有效提高零件的加工精度,在实际操作中不同的工作场景,对应不同的零件变形处理措施,需要辩证分析,因地制宜的进行工作,提升零件加工系统的整体工作效率。
T68镗床的故障原因分析:

一、镗杆镗孔与零件底面的平行度超差:此项误差产生是镗杆、主轴箱、立柱导轨与床身、纵向机床工作台各部件间之间的精度综合反映。
1、机床工作台移动在垂直平面内的直线度超差。
2、机床工作台移动时倾斜由于导轨磨损或机床安装水平不对。
3、机床工作台台面不平。
4、主轴箱垂直移动与机床工作台面的垂直度超差。
5、主轴旋转中心对前立柱导轨的垂直度超差。
6、机床工作台纵横向移动与床身导轨不平行。
7、镗杆轴心线对机床工作台面不平行。
8、主轴箱锁紧装置失灵。
9、镗杆与轴瓦间隙过大。
10、主轴箱上立柱间斜铁松动,间隙过大。
二、引起镗床用平旋刀架铣削平面与零件底面的垂直度超差的原因:1、机床安装水平精度不够。
2、主轴箱垂直移动对机床工作台面不垂直。
3、平旋盘旋转中心线与立柱导轨垂直度超差。
三、引起镗床工作台横向移动铣削平面及镗孔的垂直度超差的原因:1、横向工作台斜铁间隙过大。
2、平旋盘与镗轴中心线同轴度超差。
四、用长镗杆镗孔时出现斜孔现象的原因:两立柱安装精度不够。
五、铣削时工件表面产生波纹的原因如下:1、电动机振动,电动机前后轴承支架不同轴,电动机轴承外环配合过松或轴承损坏。
2、机床振动,引起振动的主要原因:a、电动机支架松动b、主轴箱内传动齿轮有缺陷,齿轮表面碰伤,有毛刺或缺牙现象。
c、因主轴箱内驱动油泵磨损面引起振动。
d、传动三角皮带过紧或长短不一致。
e、主轴上圆锥滚子轴承松动。
f、主轴后支撑点与支座孔不同轴。
六、用平旋盘刀座加工端面与用主轴镗孔的垂直度超差的原因如下:1、平旋盘轴各轴承点不同轴2、滚套和主轴配合间隙过大3、平旋盘定位锥孔与平旋盘轴锥体配合不良(新结构为圆柱体).4、主轴弯曲。
七、镗孔时出现均匀螺旋线的原因:1、送刀蜗杆副咬合不良。
2、主轴上两条键配合间隙大或歪斜。
八、主轴实际转速与速度盘所指速度不相符的原因:1、速度盘装配时位置不对。
2、双速电动机互相转换时电极变换不正确。
九、转速盘的走刀量与实际走刀量不符的原因:在机床维修中,由于送刀变速机构各相关位置安装的不正确以及相关的刻度没有对准所致。
数控机床孔加工常见问题解决方案

数控机床孔加工常见问题解决方案数控机床在工业生产中扮演着重要的角色,它的高精度和高效率使其成为现代制造业不可或缺的工具。
然而,数控机床在孔加工过程中,常常会遇到一些问题。
本文将针对数控机床孔加工中常见的问题进行解决方案的讨论,以帮助工程师和操作人员提高加工效率。
1. 孔径误差过大孔径误差过大是数控机床孔加工中常见的问题之一。
造成孔径误差的原因可能有多种,例如机床参数设置错误、刀具磨损、夹具不稳定等。
解决方案:1.1 检查并优化机床参数设置,确保正确设置进给速度和转速等相关参数。
1.2 定期检查和更换刀具,保持刀具的锋利度,避免磨损引起的误差。
1.3 确保夹具的稳定性,避免夹具松动引起孔径误差。
2. 表面质量不佳表面质量不佳是另一个常见的孔加工问题,特别是在高速切削和深孔加工中。
表面质量不佳可能导致工件精度降低、表面粗糙度增加等问题。
解决方案:2.1 优化切削参数,确保适当的进给速度和切削速度。
2.2 使用合适的刀具和切削液,选择适当的刀具材料和涂层技术,以及使用切削液来降低摩擦和热量。
2.3 定期清洁和维护切削工具,包括清理切片和刀尖,并确保它们保持锋利。
3. 孔面度问题在孔加工过程中,孔面度问题是常见的挑战之一。
孔面度问题包括圆度误差、垂直度误差等。
解决方案:3.1 使用高精度的加工工具和设备,例如精密刀具、夹具等。
3.2 检查和校准机床的几何精度,确保机床的精度和稳定性。
3.3 在加工过程中使用合适的切削液和冷却系统,避免因热变形导致的孔面度问题。
4. 加工效率低加工效率低是数控机床孔加工中常见的问题之一。
低效率可能导致生产周期延长、成本增加等问题。
解决方案:4.1 优化切削参数,例如有效减少孔深和切削时间,提高进给速度和切削速度等。
4.2 使用高效的刀具和切削液,选择合适的刀具和涂层技术,以及使用切削液来降低摩擦和热量。
4.3 自动化和智能化,利用数控机床的自动化功能和智能化控制系统,提高加工效率和生产能力。
镗削加工误差及孔系镗削质量分析 1~11
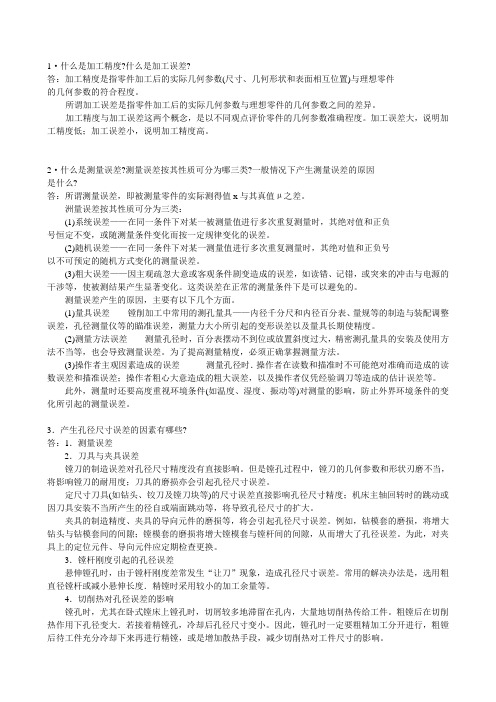
1·什么是加工精度?什么是加工误差?答:加工精度是指零件加工后的实际几何参数(尺寸、几何形状和表面相互位置)与理想零件的几何参数的符合程度。
所谓加工误差是指零件加工后的实际几何参数与理想零件的几何参数之间的差异。
加工精度与加工误差这两个概念,是以不同观点评价零件的几何参数准确程度。
加工误差大,说明加工精度低;加工误差小,说明加工精度高。
2·什么是测量误差?测量误差按其性质可分为哪三类?一般情况下产生测量误差的原因是什么?答:所谓测量误差,即被测量零件的实际测得值x与其真值µ之差。
洲量误差按其性质可分为三类:(1)系统误差——在同一条件下对某一被测量值进行多次重复测量时,其绝对值和正负号恒定不变,或随测量条件变化而按一定规律变化的误差。
(2)随机误差——在同一条件下对某一测量值进行多次重复测量时,其绝对值和正负号以不可预定的随机方式变化的测量误差。
(3)粗大误差——因主观疏忽大意或客观条件剧变造成的误差,如读错、记错,或突来的冲击与电源的干涉等,使被测结果产生显著变化。
这类误差在正常的测量条件下是可以避免的。
测量误差产生的原因,主要有以下几个方面。
(1)量具误差镗削加工中常用的测孔量具——内径千分尺和内径百分表、量规等的制造与装配调整误差,孔径测量仪等的瞄准误差,测量力大小所引起的变形误差以及量具长期使精度。
(2)测量方法误差测量孔径时,百分表摆动不到位或放置斜度过大,精密测孔量具的安装及使用方法不当等,也会导致测量误差。
为了提高测量精度,必须正确掌握测量方法。
(3)操作者主观因素造成的误差测量孔径时.操作者在读数和描准时不可能绝对准确而造成的读数误差和描准误差;操作者粗心大意造成的粗大误差,以及操作者仅凭经验调刀等造成的估计误差等。
此外,测量时还要高度重视环境条件(如温度、湿度、振动等)对测量的影响,防止外界环境条件的变化所引起的测量误差。
3.产生孔径尺寸误差的因素有哪些?答:1.测量误差2.刀具与夹具误差镗刀的制造误差对孔径尺寸精度没有直接影响。
加工中心圆度出现误差的原因是什么?怎么调整?
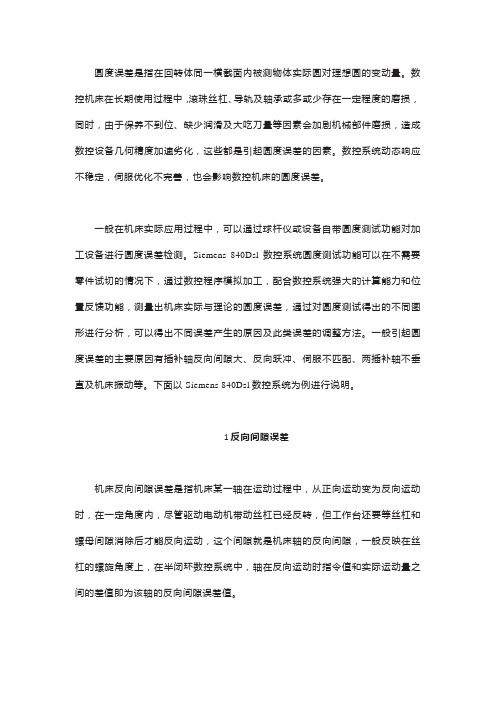
圆度误差是指在回转体同一横截面内被测物体实际圆对理想圆的变动量。
数控机床在长期使用过程中,滚珠丝杠、导轨及轴承或多或少存在一定程度的磨损,同时,由于保养不到位、缺少润滑及大吃刀量等因素会加剧机械部件磨损,造成数控设备几何精度加速劣化,这些都是引起圆度误差的因素。
数控系统动态响应不稳定,伺服优化不完善,也会影响数控机床的圆度误差。
一般在机床实际应用过程中,可以通过球杆仪或设备自带圆度测试功能对加工设备进行圆度误差检测。
Siemens 840Dsl数控系统圆度测试功能可以在不需要零件试切的情况下,通过数控程序模拟加工,配合数控系统强大的计算能力和位置反馈功能,测量出机床实际与理论的圆度误差,通过对圆度测试得出的不同图形进行分析,可以得出不同误差产生的原因及此类误差的调整方法。
一般引起圆度误差的主要原因有插补轴反向间隙大、反向跃冲、伺服不匹配、两插补轴不垂直及机床振动等。
下面以Siemens 840Dsl数控系统为例进行说明。
1反向间隙误差机床反向间隙误差是指机床某一轴在运动过程中,从正向运动变为反向运动时,在一定角度内,尽管驱动电动机带动丝杠已经反转,但工作台还要等丝杠和螺母间隙消除后才能反向运动,这个间隙就是机床轴的反向间隙,一般反映在丝杠的螺旋角度上,在半闭环数控系统中,轴在反向运动时指令值和实际运动量之间的差值即为该轴的反向间隙误差值。
(1)反向间隙对圆度误差的影响反向间隙的存在会影响机床的定位精度和重复定位精度,降低数控机床加工精度,在加工中心铣圆过程中会造成圆度误差。
当Y轴在反向运动过程中,由于反向间隙的存在,会造成Y轴反向后滞后于X 轴进行插补运动,铣圆加工会出现如图1所示结果。
图1反向间隙造成的圆度误差(2 )反向间隙测量与调整影响机床轴反向间隙误差的因素多种多样,从驱动电动机到运动部件之间所有的机械联接件都会存在间隙,电动机对丝杠的联轴结是否松动、滚珠丝杠制造误差、丝杠预紧是否过紧或过松、丝母与运动部件联接是否紧固,都是造成机床轴反向间隙的原因。
加工中心机械故障诊断方法及常见故障维修
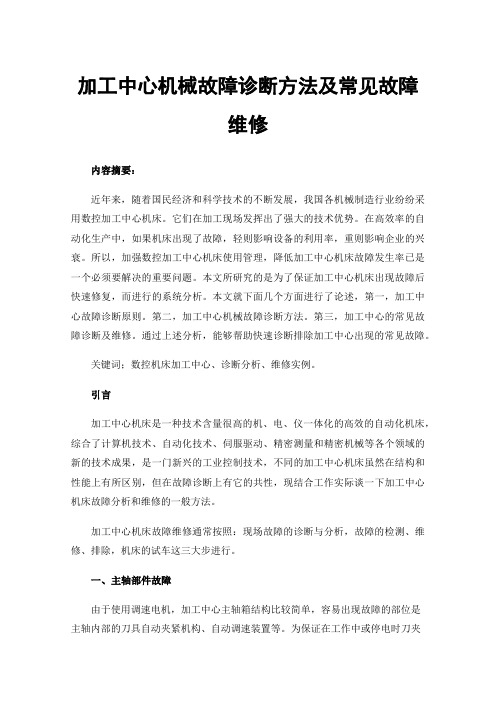
加工中心机械故障诊断方法及常见故障维修内容摘要:近年来,随着国民经济和科学技术的不断发展,我国各机械制造行业纷纷采用数控加工中心机床。
它们在加工现场发挥出了强大的技术优势。
在高效率的自动化生产中,如果机床出现了故障,轻则影响设备的利用率,重则影响企业的兴衰。
所以,加强数控加工中心机床使用管理,降低加工中心机床故障发生率已是一个必须要解决的重要问题。
本文所研究的是为了保证加工中心机床出现故障后快速修复,而进行的系统分析。
本文就下面几个方面进行了论述,第一,加工中心故障诊断原则。
第二,加工中心机械故障诊断方法。
第三,加工中心的常见故障诊断及维修。
通过上述分析,能够帮助快速诊断排除加工中心出现的常见故障。
关键词;数控机床加工中心、诊断分析、维修实例。
引言加工中心机床是一种技术含量很高的机、电、仪一体化的高效的自动化机床,综合了计算机技术、自动化技术、伺服驱动、精密测量和精密机械等各个领域的新的技术成果,是一门新兴的工业控制技术,不同的加工中心机床虽然在结构和性能上有所区别,但在故障诊断上有它的共性,现结合工作实际谈一下加工中心机床故障分析和维修的一般方法。
加工中心机床故障维修通常按照:现场故障的诊断与分析,故障的检测、维修、排除,机床的试车这三大步进行。
一、主轴部件故障由于使用调速电机,加工中心主轴箱结构比较简单,容易出现故障的部位是主轴内部的刀具自动夹紧机构、自动调速装置等。
为保证在工作中或停电时刀夹不会自行松脱,刀具自动夹紧机构采用弹簧夹紧,并配行程开关发出夹紧或放松信号。
若刀具夹紧后不能松开,则考虑调整松刀液压缸压力和行程开关装置或调整碟形弹簧上的螺母,减小弹簧压合量。
维修实例1、故障现象:HTM4228G龙门式加工中心加工过程中出现镗孔精度下降,圆度超差,故障分析:首先检查主轴定心锥孔位置和镗刀杆结合部,发现主轴定心锥孔表面有轻微研伤,用千分表检查主轴锥孔直线度超差0.08mm,根部圆跳动0.06mm,远端圆跳动0.10mm。
解决镗孔表面粗糙度质量差小妙招

解决镗孔表面粗糙度质量差小妙招通过多年来操作各类镗床,以及对加工中心镗削各种矿用零部件的研究,分析总结了多种导致工件镗孔表面粗糙度质量差的原因,现介绍如下。
1.问题产生的原因及分析(1)进给量较大或太小。
在镗孔过程中,当刀具每转进给量大于刀尖修光刃的有效修光长度时,必然造成加工过程中的加工面存在“螺纹”的现象,使孔壁的已加工面出现“山”形的加工痕迹,导致所镗孔的表面粗糙度值较高。
若其进给量太小,使刀尖的修光刃在切削过程中存在着与孔壁已加工表面的重复性摩擦,亦会降低孔壁的表面质量;如果是利用镗床主轴安装刀杆镗孔,进给量过小,还会存在刀具因切削阻力降低而发生微量的轴向窜动现象,进一步降低镗孔的表面粗糙度质量。
(2)刀头的刀尖角圆弧过渡刃较小。
当工艺系统刚性较好时,可尽量选择较大的刀尖圆弧角。
如果刀头的刀尖角圆弧过渡刃的修光长度小于镗孔过程中的每转进给量,必然导致镗削过程中已加工面出现修光不彻底的现象,同样会使孔壁的已加工面在加工过程中,出现“螺纹”状态的“山”形,造成所镗孔的表面粗糙度质量差。
(3)刀杆或镗轴伸出超长。
在悬伸镗孔过程中,当刀杆长度大于其五倍直径或镗轴伸出超长时,镗削过程中容易引起刀杆出现“发颤”的现象,使刀具产生微量的高频径向跳动,从而降低了镗孔表面质量,且还会影响镗孔的尺寸精度。
(4)刀头的切削刃高于镗孔的中心线。
刀头的切削刃高于镗孔的中心线,即刀头的前刀面高于镗轴的回转中心时,刀头在镗孔过程中会因受到切削阻力而发生反向弯曲的现象,加大了刀头的副后面与孔壁的接触面积,增大了摩擦力,有时还会引起刀头在切削过程中发生“颤动”,使孔壁的表面粗糙度值增大,严重时将会使切削刃挤坏。
(5)镗床主轴系统间隙较大。
在镗孔过程中,特别是在精镗孔的过程中,由于镗削余量很小,刀具的切削阻力较低,当镗床主轴系统存在较大间隙时,主轴会发生轴向窜动或径向跳动,导致安装在其上的切削刀具随之发生轴向窜动或径向跳动,造成镗孔质量的下滑。
论降低数控镗铣加工中心几何精度超差几率的方法

论降低数控镗铣加工中心几何精度超差几率的方法摘要:在数控加工中心机床普及应用的背景下,针对工程实践中存在数控镗铣加工中心几何精度超差的情况,有针对性地分别从消除自激振动、改善工件加工方法和工装夹具、加固机床垫铁和规范机床保养等角度出发,全面解决了的数控镗铣加工中心中存在的问题。
关键词:数控镗铣加工,几何精度,超差问题,对策1 引言在新时代的背景下,随着数控加工中心机床的普及应用,对于全面推动精密加工技术的快速发展具有重要意义,但人们也往往对于数控加工中心机床的加工精度要求也越来越高。
在数控双面镗铣加工中心的应用实践中,部分产品精度通过三坐标检测表明存在着不合格的情况。
结合同轴度和垂直度的超差情况来看,其具有比较高的频率。
相应检查加工工艺和工装的符合性方面并没有存在异常情况。
在设备的几何精度检测中,存在着机床的同轴度和主机 w 轴与 x轴的垂直度两项精度超差的情况,从这个角度来看,往往是存在着机床几何精度的超差从而引发了产品精度超差的情况。
针对数控双面镗铣加工中心机床几何精度超差的问题进一步深入分析,原因主要是由于存在着机床产生震动引发机床垫铁的变化情况;存在着不牢固机床垫铁,容易遭自身震动或外力作用下存在着细微变化;操作不当、设备保养不力等情况。
这里重点结合实际情况,提出了降低数控镗铣加工中心几何精度超差几率有效措施。
2降低数控镗铣加工中心几何精度超差几率的方案2.1消除自激振动第一,考虑到形成自激振动和切削加工具有直接关联,在进行抑制方面,可以考虑到实践中的合理优化切削刀具几何角度、工件材料等方式。
比如,在进行切削速度范围满足20 m/min~60 m/min的情况,则会造成相应的自激振动增长很快。
如果超过其范围,其呈现出逐步减弱的特点。
实践中,切削速度范围为50 m/min~60 m/min的情况下,稳定性最差而容易出现自激振动,所以应合理化控制相应的切削速度。
在进行给进量的优化过程中,其数值比较小的情况下则会造成较大的振幅问题,在其不断增大的情况下,振幅呈现出减小的趋势。
- 1、下载文档前请自行甄别文档内容的完整性,平台不提供额外的编辑、内容补充、找答案等附加服务。
- 2、"仅部分预览"的文档,不可在线预览部分如存在完整性等问题,可反馈申请退款(可完整预览的文档不适用该条件!)。
- 3、如文档侵犯您的权益,请联系客服反馈,我们会尽快为您处理(人工客服工作时间:9:00-18:30)。
加工中心镗孔圆度超差故障分析与排除
摘要:NC800卧式加工中心、XH715和ARROW1000立式加工中心,加工的箱体上轴承孔圆度超差,主要是主轴刀具松紧机构、滚珠丝杠间隙、主轴轴承预紧不够题目所致。
关键词:NC800 圆度镗孔
镗孔圆度超差故障涉及到工艺系统的很多方面,机床自身机械方面的原因,是首先应检查的主要因素。
一、主轴刀具拉紧力不够
各种加工中心主轴刀具锁紧机构基本上大同小异,大多采用液压或气压松开,靠碟形弹簧回复力拉紧刀具,碟形弹簧长期使用会产生疲惫和损坏,导致对刀具的拉紧力下降。
在镗孔过程中由于切削力的作用会使刀具产生松动,从而出现孔尺寸不稳定以及孔圆度超差的故障。
假如不能确认镗孔圆度超差是否由于主轴碟形弹簧引起,可以先采用压力调整法进行试验,再结合其他
检验来判定,避免盲目拆卸主轴松刀机构。
一台NC800卧式加工中心加工的箱体上轴承孔圆度误差0.045mm,在排除了其他因素的影响之后,对松刀机构进行检验,先调整液压系统压力,由系统设置的6.3MPa逐渐往下降,每降低0.5MPa,对松刀情况进行检验,看松刀是否到位。
当压力降到
4MPa时,松刀机构卡爪的位移出现题目,刀具不能松开。
正常情况下假如系统压力低于5.8MPa时,就不能正常装卸刀具了。
假若松刀机构位移即松刀行程不变,而弹簧的回复力与压缩弹簧液压缸的压力成正比,松刀所需要的液压压力降低,证实弹簧的刚度降低了,这实际上说明碟形弹簧有题目。
拆卸主轴刀具松紧机构,发现部分碟形弹簧损坏,对其进行全部更换,将锁母压紧到松开前的位置。
安装后,松刀所需的压力恢复到正常的5.8MPa左右,再次进行镗孔测试,圆度误差减至0.01mm以内,恢复到正常水平。
还有一种可能的情况是碟形弹簧并未损坏,但由于疲惫而刚度下降,通过调紧碟形弹簧的压紧锁母也可以增加刀具拉紧力,但留意不要影响松刀机构爪子的松开及锁紧位置,否则会造成刀具无法正常装卸,造成新的故障隐患。
假如确是这种情况,仍然建议更换全部碟形弹簧,以确保刀具锁紧可靠。
二、主轴轴承未有效预紧
加工中心镗孔圆度超差,一般最直接的原因与主轴旋转精度有关,主轴旋转精度主要是靠主轴轴承来保证的,加工中心的
主轴组件有多种结构形式,由于需要满足高速、重载、精密的现代加工要求,加工中心主轴前轴承多采用三个角接触球轴承组合,并承受双向的轴向载荷,对于这种配置的轴承的预紧,存在是否有效的题目。
一台ARROW1000立式加工中心在加工壳体零件的轴承孔时,圆度误差0.03mm,几乎接近孔径公差,所以操纵工很难保证该孔的尺寸要求,经过对主轴径跳的静态检验,均符合该机床的精度指标要求,证实主轴轴承精度保持正常水平,同时也排除了刀具、夹紧力的影响。
模拟主轴加工受力状况,将百分表压在镗刀杆的端部外圆面上,距主轴端面300mm左右,通过对镗刀杆人为推动施加外力,力的方向朝着表头压下的方向,可以看到百分表针有0.05mm左右的摆动。
所以以为是主轴轴承预紧不够,在零件的加工过程中,由于受切削力的作用造成主轴径跳加大,从而影响镗孔圆度。
主轴结构如图1所示。
主轴轴承为三套角接触球轴承,通过内外两个隔环组合在一起。
但是,在对预紧锁母施加预紧力之后,仍不能得到应有的预紧效果。
由于轴承经过长时期磨损之后,轴向间隙加大,无论在轴承1的内环上施加力有多大,都无法使轴承2、3的内环随主轴产生位移来消除间隙,因此也就无法对主轴有效预紧。
根据力平衡原理,轴承1的轴向力应即是轴承2、3的轴向力之和,当轴
向施加外载荷后,轴承2、3的轴向载荷增加,轴承1的载荷则减小,三个轴承的载荷分配趋向均匀。
成套供给的新轴承有很高的精度,基本可以保证轴承2和3有大体相同的预紧量,即受力比较均匀。
在长期使用后,轴承2和3也基本有大体相同的磨损量,实在只需对轴承1和2之间的内隔环进行配磨,就可补偿轴承的轴向间隙,使得在轴承1和2与外隔环相互接触时,而内隔环与轴承内圈之间留有一定间隙,压紧后即可得到要求的预紧力。
因此,解决的方法有两个:一是更换轴承;二是通过修配隔环使主轴预紧。
考虑到轴承的精度还没有丧失,还是采取修配隔环使主轴预紧较好。
由于在实际操纵中面临丈量方面的困难,将内隔环的长度由121.35mm修磨到121.25mm。
安装后,以120N·m左右的力矩旋紧锁母来压紧轴承,留意预紧力不要太大,可根据机床要求的力矩,由于轴承1、2和内隔环之间可能压紧后仍存有间隙,预紧力过大会造成轴承发热,若无丈量力矩的装置,盘动主轴略有阻尼感觉即可。
此后,经过测试及现场切削加工证实,此方法可行,同样镗Ф80mm的孔,圆度误差由0.03mm减小到0.005mm,完全满足零件的加工要求。
三、坐标轴间隙导致的镗孔圆度超差
加工中心坐标轴的间隙,在很大程度上影响机床运行的稳定性,是引起机床运行抖动的重要原因。
在半闭环控制系统中,系统只检测电机输出真个位置,对坐标轴的实际位置并不检测,即使加进间隙补偿,也只是保证反向运行的精度,并不能纠正坐标轴停止后的位置变化。
尤其是轻系列的加工中心,大都采用直线导轨,具有运动轻便灵活、负载轻的特点,但这类机床坐标轴
抗振性较差,对间隙的反应很敏感,极易受到切削力的影响,在镗孔过程中也会引起圆度超差现象。
一台XH715立式加工中心,采用直线导轨,半闭环控制系统,在加工行星架的三个齿轮轴的安装孔时,同一把镗刀,加工圆周方向均布的三个相同尺寸的孔大小不一样。
进一步精测发现,三个孔的圆度都有不同程度的超差,误差大的0.03mm,小的0.02mm,但总是呈一定规律分布,圆度超差的方向上一致,都是在Y轴方向上尺寸小,X方向上尺寸基本没有变化,通过对Y轴监测,发现在镗孔过程中Y轴有稍微抖动,且抖动的频率与主轴转速一致,对Y轴进行检验,发现Y轴反向间隙超过0.07mm,X轴反向间隙为零。
间隙的存在,使工作台在切削力的作用下,Y方向产生让刀现象,是造成镗孔圆度超差的主要因素。
检查Y轴滚珠丝杠正负方向运动的窜动量基本为零,支撑的预紧没有题目,确认0.07mm的间隙是由丝杠的螺母产生,该螺母为双螺母垫片调隙结构,如图2。
可通过加厚垫片厚度,使两螺母向撑开的方向产生轴向位移,达到消除间隙的目的。
根据丈量的结果,先取出两个螺母之间的连接键块,将两螺母旋开一点,参照垫片的圆环尺寸,将0.07mm厚的铜皮剪成合适的半圆环,紧贴着垫片装进,随即旋紧两螺母,用键块压紧。
完成安装之后,验其反向间隙在0.01mm以内,达到了消除间隙的目的。
再次进行零件的加工试验,Y轴抖动现象消失。
四、结论
加工中心镗孔圆度超差题目,在机械维修中固然不是很复杂的题目,但与类似传动部件失效、零件损坏、卡死等故障不同。
镗孔圆度超差可以是机床的原因,也可以是刀具、夹具以及零件材料的原因,还可能是几种因素共同影响所致。
以上列举的导致镗孔圆度超差的几个原因及解决途径,只是个例,实际中碰到的情况可能不尽相同,但只要针对具体故障,密切关注不同机床的特征与故障现象之间的联系,具体题目具体分析,通过试验、丈量及现实的一些手段,找出影响圆度题目最主要的因素,故障的解决就只是个过程题目。