对超塑性成型的认识汇总
非合金钢板的超塑性成形技术研究及其应用潜力

非合金钢板的超塑性成形技术研究及其应用潜力超塑性成形是一种通过在高温条件下对材料应力施加的加工方法,可以使非合金钢板也能够实现高度塑性变形。
本文将探讨非合金钢板超塑性成形技术的研究现状以及其在实际应用中的潜力。
首先,我们将介绍非合金钢板超塑性成形技术的研究现状。
非合金钢板由于其较低的碳含量以及少量的合金元素,通常具有较低的塑性,限制了其在成形过程中的应用。
然而,通过对非合金钢板进行超塑性成形的研究,可以改善其塑性特性,使其具备更广阔的应用前景。
目前,非合金钢板超塑性成形技术的研究主要集中在以下几个方面。
首先,研究人员通过调整非合金钢板的化学成分,改变晶体结构,提高材料的塑性。
其次,采用热处理方法,通过控制加热温度和时间,使非合金钢板获得更高的塑性。
此外,研究人员还探索了不同的成形方法,如等温拉伸、等温压缩、等温缩径等,以实现非合金钢板的超塑性变形。
在实际应用中,非合金钢板超塑性成形技术具有广阔的潜力。
首先,超塑性成形可以极大地提高材料的成形能力,使非合金钢板能够制造出更复杂的形状和结构。
这对于一些应用场景,如汽车、航空航天以及能源领域的零部件制造具有重要意义。
其次,超塑性成形技术可以减少材料在成形过程中的应力和变形,降低材料的变形硬化率,从而改善零部件的成形质量和机械性能。
此外,超塑性成形还可以降低材料的成形温度,减少能源消耗,降低生产成本。
然而,在实际应用中,非合金钢板超塑性成形技术还面临一些挑战。
首先,超塑性成形需要非常严格的加工条件和设备配置,包括高温环境、复杂的工艺参数控制等。
这增加了生产成本和困难。
其次,非合金钢板超塑性成形技术的研究还相对较少,需要进一步的实验研究和理论探索。
此外,超塑性成形后的材料往往会出现晶界滑移和晶界扩散现象,可能会影响材料的综合性能和寿命。
为了克服这些挑战,进一步开展非合金钢板超塑性成形技术的研究是非常必要的。
首先,可以通过优化材料的化学成分,改善非合金钢板的塑性特性。
塑性成形原理知识点总结
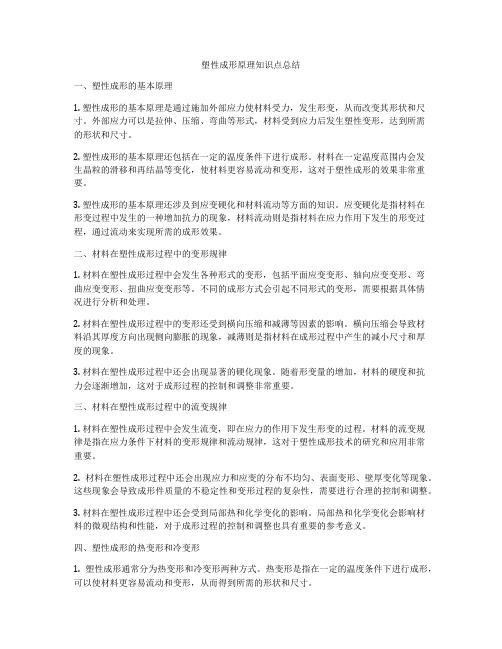
塑性成形原理知识点总结一、塑性成形的基本原理1. 塑性成形的基本原理是通过施加外部应力使材料受力,发生形变,从而改变其形状和尺寸。
外部应力可以是拉伸、压缩、弯曲等形式,材料受到应力后发生塑性变形,达到所需的形状和尺寸。
2. 塑性成形的基本原理还包括在一定的温度条件下进行成形。
材料在一定温度范围内会发生晶粒的滑移和再结晶等变化,使材料更容易流动和变形,这对于塑性成形的效果非常重要。
3. 塑性成形的基本原理还涉及到应变硬化和材料流动等方面的知识。
应变硬化是指材料在形变过程中发生的一种增加抗力的现象,材料流动则是指材料在应力作用下发生的形变过程,通过流动来实现所需的成形效果。
二、材料在塑性成形过程中的变形规律1. 材料在塑性成形过程中会发生各种形式的变形,包括平面应变变形、轴向应变变形、弯曲应变变形、扭曲应变变形等。
不同的成形方式会引起不同形式的变形,需要根据具体情况进行分析和处理。
2. 材料在塑性成形过程中的变形还受到横向压缩和减薄等因素的影响。
横向压缩会导致材料沿其厚度方向出现侧向膨胀的现象,减薄则是指材料在成形过程中产生的减小尺寸和厚度的现象。
3. 材料在塑性成形过程中还会出现显著的硬化现象。
随着形变量的增加,材料的硬度和抗力会逐渐增加,这对于成形过程的控制和调整非常重要。
三、材料在塑性成形过程中的流变规律1. 材料在塑性成形过程中会发生流变,即在应力的作用下发生形变的过程。
材料的流变规律是指在应力条件下材料的变形规律和流动规律,这对于塑性成形技术的研究和应用非常重要。
2. 材料在塑性成形过程中还会出现应力和应变的分布不均匀、表面变形、壁厚变化等现象。
这些现象会导致成形件质量的不稳定性和变形过程的复杂性,需要进行合理的控制和调整。
3. 材料在塑性成形过程中还会受到局部热和化学变化的影响。
局部热和化学变化会影响材料的微观结构和性能,对于成形过程的控制和调整也具有重要的参考意义。
四、塑性成形的热变形和冷变形1. 塑性成形通常分为热变形和冷变形两种方式。
超塑性与超塑成形
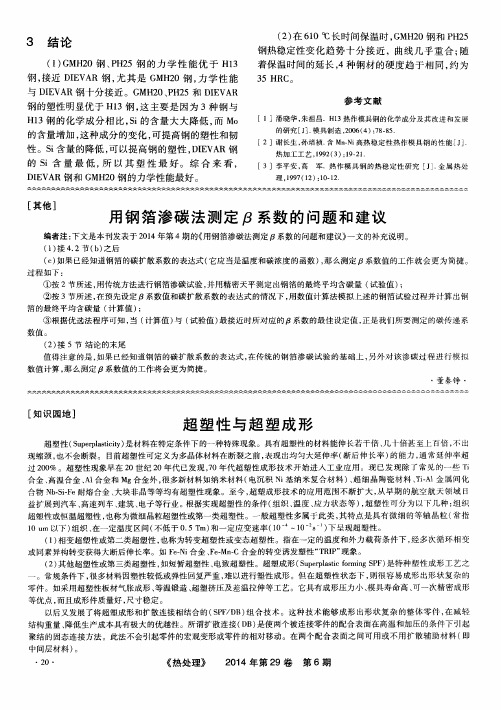
超塑性或恒温超塑性 , 也称为微细晶粒 超塑性或第一类超塑性 。一般 超塑性多属于此类 , 其特点是具有微 细的等轴 晶粒( 常指
1 0 u m 以下 ) 组织 、 在一 定 温 度 区 间 ( 不低于 0 . 5 T m) 和 一 定 应 变 速率 ( 1 0一 ~1 0~s ) 下呈现超塑性。
( 1 ) 接4 . 2节 ( b ) 之 后
( c ) 如果 已经知道钢箔 的碳扩散系数的表达式( 它应当是 温度 和碳浓度 的函数 ) , 那 么测定 系数值 的工作就会更 为简捷。
过程 如下 :
①按 2节所述 , 用传统方法进行钢箔渗碳试验 , 并用精密 天平测定 出钢箔的最终平 均含碳量 ( 试验值 ) ; ②按 3节所述 , 在预先设定 系数值和碳 扩散 系数 的表达式的情况下 , 用数值计算法模 拟上述 的钢箔试验过程并计 算出钢 箔的最终平均含碳量 ( 计算值 ) ; ③根 据优选法程序可知 , 当 ( 计算值 ) 与 ( 试验值 ) 最接近时所对应的 系数 的最佳设定值 , 正是我们所要测定 的碳传递 系
超塑性( S u p e r p l a s t i c i t y ) 是材料在特定条件下的一种特殊现象。具有超塑性 的材料能伸长若 干倍 、 几十倍甚 至上 百倍 , 不出
现缩颈 , 也不会断裂 。目前超 塑性 可定义为多晶体材料在断裂之前 , 表现出均匀大延伸率 ( 断后伸 长率) 的能力 , 通 常延 伸率超 过2 0 0 % 。超塑性现象早在 2 0世纪 2 0年代 已发现 , 7 0年代超塑性成 形技术开始进人工业应 用。现 已发现除 了常见的一些 合金 、 高温合金 、 A l 合金和 Mg 合金外 , 很 多新材料如纳米材料 ( 电沉积 N i 基纳 米复合材料 ) 、 超细 晶陶瓷材料 、 — A 1金属问化 合物 N b . s i — F e耐熔合金 、 大块 非晶等等均有超塑性现象。至今 , 超塑成形技术 的应用 范围不断扩大 , 从 早期 的航空航 天领域 日 益扩展到汽车 、 高速列车 、 建筑、 电子等行业 。根据实现超塑性 的条件 ( 组织 、 温度 、 应 力状 态等 ) , 超塑性 可分为 以下几种 : 组织
超塑性成形与扩散连接技术
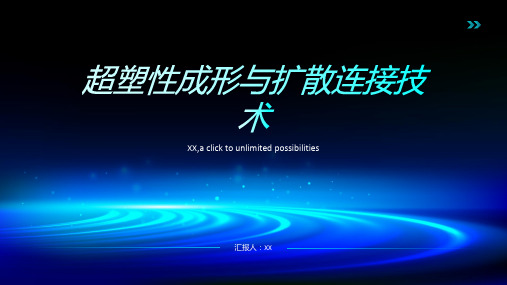
提高产品质量和可靠性 降低生产成本和能耗 促进新产品的开发和上市 增强企业竞争力和市场地位
汇报人:XX
添加标题
添加标题
添加标题
添加标题
智能化:通过引入人工智能、机器学 习等技术,实现超塑性成形与扩散连 接技术的智能化控制,提高生产效率 和产品质量。
绿色化:在环保意识日益增强的背景 下,超塑性成形与扩散连接技术将向 更加环保、绿色的方向发展,减少对 环境的负面影响。
航空航天领域:超塑性成形与扩散连接技术将进一步提高航空航天器的性能和可靠性。
比较:超塑性成形对材料的要求更为严 格,需要材料具备较好的塑性变形能力, 而扩散连接对材料的要求相对较为宽松。
应用范围:超塑性成形适用于轻质、薄 壁、复杂结构件的制作,而扩散连接适 用于金属、陶瓷、玻璃等材料的连接。
优点:超塑性成形与扩散连接技术能够提高材料成形极限,减少成形缺陷,提高产品质量。
缺点:超塑性成形与扩散连接技术需要较高的温度和压力,对设备要求较高,同时需要严格控制工艺参数,否则 容易造成成形失败或产品质量问题。
材料的热膨胀系数、弹性模量、 热导率等物理性能也是扩散连 接的重要考虑因素。
扩散连接对材料的要求包括材 料的纯净度、晶粒度、表面光 洁度等。
材料的厚度、形状、尺寸等 也会影响扩散连接的效果。
材料的可加工性、可焊性、可 连接性等也是扩散连接需要考
虑的因素。
航空航天领域:连接不同材料,提 高结构强度和疲劳性能
比较:超塑性成形与扩散连接技术在不同应用场景下各有优缺点,需要根据具体情况进行选择。
应用:超塑性成形与扩散连接技术在航空航天、汽车、精密机械等领域有广泛应用。
轻量化:超塑性成形与扩散连接技 术将向更轻、更薄的方向发展,以 满足现代工业对节能减排的需求。
超塑性成形与扩散连接技术
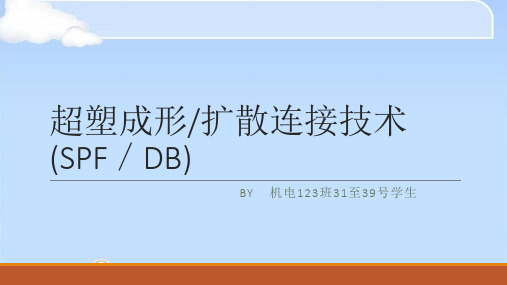
具有异常高的延伸率并提出超塑性”这一名词。 超塑成形/扩散连接工艺SPF/DB
的结构,进一步提高结构承载效率,减轻结构件质量;
·1964年 的Backofen提出了应变速率敏感性 图3所示力F-15型飞机机身背部2块大型壁板,长3048mm,宽1143mm。 指数m值,为超塑性研究奠定了基础。20世纪60 现改用sPF/DB结构,只需4块sPF/DB壁板,减少了9个隔框、10根桁条、150个零件和5000个铆钉,总质量减轻38.4%,总成本降低53.4%。
超塑成形/扩散连接技术 (SPF/DB)
BY 机电123班31至39号学生
&1.超塑成型SPF
超塑性通常是指材料在拉伸条件下 表现出异常高的延伸率也不产生缩 颈与断裂现象。
·1920年,Rosenhain等发现Zn-4Cu-7A1合金在低 速弯曲时可以弯曲近180。而不出现裂纹 ·1934年英国的Pearson发现Pb-Sn共晶合金在室 2温0世纪低60 速拉伸时可以得到2000%的延伸率。 ·1945年前苏联的Bochvar等发现Zn-Al共析合金 年代后期及70年代,世界上形成了超塑性研究的来自&2.扩散连接DB
扩散连接是在一定的温度和压力下, 经过一定时间,连接 界面原子间相互扩散,实现的可靠连接。
扩散连接的特点:
①可以进行内部及多点、大面积构件的连接,以及 电弧可达性不好或用熔焊方法根本不能实现的连接。 ②可成功连接用熔化焊和其他连接方法难以连接的 材料,如弥散强化型合金、活性金属、耐热合金、 陶瓷和复合材科等,特别适用于不同种类的金属、 非金属及异种材料的连接。 ③是一种高精密的连接方法,用这种方法连接后, 工件不变形,可以实现机械加工后的精密装配连接。
超塑性定义和性质

相变超塑性不要求微细等轴晶粒,这是有利 的,但要求变形温度反复变化,给实际生产带来 困难,故使用上受到加工条件下产生较大弯曲、拉伸等变 形,二次大战后由前苏联科学家通过锌铝 合金拉伸试验提出超塑性的概念。
超塑性成形实例
Bi-44Sn挤压材料在慢速拉伸下出现异常大的延伸率现象 (δ=1950%),左为拉伸前的试样。
我国已成功开发应用了以铝合金、钛合金、 铜合金为代表的结构合金超塑性材料。 (1)、研究获得超塑性的途径; (2)、探索成型工艺规范; (3)、解决成型工艺关键
1.2、超塑性成形的基本特点 金属材料在受到拉伸应力时,显示出很大的延伸率
而不产生缩颈与断裂现象,把延伸率能超过100% 的材料统称为“超塑性材料”,相应地把延伸率 超过100%的现象叫做“超塑性”。
但实际的变形程度要更大。也可用应变速率敏感性 指数m来定义超塑性。 宏观上,可用大变形、无缩颈、小应力、
易成形来描述超塑性特点。
(1)、大变形 金属材料的最高伸长率铝青铜可达8000﹪,
材料成型性能好,可成形复杂程度高、变形 量大的成型件。 (2)、无缩颈
超塑性成形类似于粘性物质的流动,对 应变速率较敏感,既有应变速率硬化效应。 (3)、小应力
超塑性成形的流动应力是常规成型的十 几到几十分之一,设备吨位小。 (4)、易成形
m:0.6, σ:2MPa,δ:1000~2000﹪, غ:1.6×10‾³s‾¹,t:200~300 ℃
第二讲:超塑性成形

超塑性成形的应用
SPF构件用料情通开式模锻比较,模具结构基本相同,但需
增加加热和保温装置。同时,由于应变速率要求在较低范围内, 不能采用锤和热模锻压力机,只能用液压机。具有充模好、变 形力低、组织性能好、变形道次少、弹复小的特点。用于铝、 镁、钛合金的叶片、翼板等薄腹板带肋件或类似形状复杂零件 的模锻。
超塑性变形机理
溶解—沉淀理论 亚稳态理论 扩散蠕变机制 扩散流动机制--Ashby-Verral模型 位错蠕变机制
超塑性成形的应用
利用气压胀形/扩散连接复合工艺(SPF/DB)工艺制造的发动 机整流叶片形
超塑性成形的应用
军用飞机采用的超塑成形零件
超塑性成形的应用
铝合金超塑成形构件的市场分布
(2)实现超塑性的条件
微细晶粒超塑性的实现有赖于晶粒细化、适当的温度和低应变速率三个 基本条件。
冶金方法:主要是添加一些能够促使早期形核,使组织弥散,并在变形 过程中稳定晶粒的微量元素。此外,还可采取快速凝固方法。 压力加工方法:采用冷、温、热三种不同温度下的轧制或锻造。 热处理方法:包括反复淬火、形变热处理、球化退火等方法。
1、超塑性

(1)、大变形 金属材料的最高伸长率铝青铜可达8000﹪, 材料成型性能好,可成形复杂程度高、变形 量大的成型件。 (2)、无缩颈 超塑性成形类似于粘性物质的流动,对 应变速率较敏感,既有应变速率硬化效应。 (3)、小应力 超塑性成形的流动应力是常规成型的十 几到几十分之一,设备吨位小。 (4)、易成形 成形过程无硬化,流动性和填充性好,可用多 种方式成形。
②、钛合金 TC4(Ti-6Al-4V)和TC9:供货状态即为细晶组 织。 m:0.85, σ:,δ:1000﹪, ³‾01×0.1: غs‾¹,t:800~1000 ℃. Ti679:在900℃下锻造,800 ℃下退火1h后 空冷。 m:0.43, σ:25MPa,δ:734﹪, ⁴‾01×7.6: غs‾¹,t:800~850 ℃.
的2~4倍。 要求设备:可调速、可保压、有大的封闭高度与足 够的工作台面、有顶出装置、有温控系统。
(2)、超塑性气胀成形设备 要求: 除具有锻造设备的要求外,还有以下要求: 更长时间的保压; 更大的工作台面; 气源及控制系统。 典型设备:
1.4.3、超塑性成形的摩擦与润滑 特点: (1)、模具温度高 原子扩散加剧,提高摩擦系数,脱模困难; (2)、应变速率低 易于接触面咬合,挤出润滑剂,导致摩擦系数增大; (3)、变形时间长 对润滑剂要求: (1)、在整个成形过程中能在模具和坯料之间形成连续的润 滑剂薄膜,并具有较低的摩擦系数; (2)、对坯料表面具有防护作用,防止其氧化或吸收其他气 体; (3)、兼具脱模剂的作用; (4)、不与坯料和模具发生反应; (5)、易于涂覆和去除; (6)、应为无毒、非易燃、非稀缺物。
⑤ 、鎂、铜合金 MB8:供货状态即为细晶组织。 m:0.34σ:25MPa,δ:228﹪, ⁴‾01×8.2 : غs‾¹,t:400 ℃. ⁴ MB15:360℃保温1h,然后空冷。 m:0.51σ:23MPa,δ:574﹪, ⁴ ⁴‾01×0.1 : غs‾¹,t:290 ℃. HPb59-1:300 ℃温轧后,450 ℃保温1h。 m:0.5σ:23MPa,δ:550﹪, ⁴‾01×33.8 : غs‾¹,t:600 ℃. H62:250~300 ℃保温1h,然后空冷。
- 1、下载文档前请自行甄别文档内容的完整性,平台不提供额外的编辑、内容补充、找答案等附加服务。
- 2、"仅部分预览"的文档,不可在线预览部分如存在完整性等问题,可反馈申请退款(可完整预览的文档不适用该条件!)。
- 3、如文档侵犯您的权益,请联系客服反馈,我们会尽快为您处理(人工客服工作时间:9:00-18:30)。
对超塑性成型的认识
一. 超塑性的简介及发展历史
超塑性是指材料在一定的内部(组织)条件啊(如晶粒尺寸及形状、相变等)和外部(环境)条件下(如温度、应变速率等),呈现出异常低的流变抗力、异常高的流变性能(如大的延伸率)的现象。
超塑性的特点有大延伸率,无缩颈(小缩颈),小应力,易成形。
超塑性合金是指那些具有超塑性的金属材料。
超塑性是一种奇特的现象。
具有超塑性的合金能像饴糖一样伸长10倍、20倍甚至上百倍,既不出现缩颈,也不会断裂。
金属的超塑性现象,是英国物理学家森金斯在1982年发现的,他给这种现象做如下定义:凡金属在适当的温度下(大约相当于金属熔点温度的一半)变得像软糖一样柔软,而应变速度10毫米秒时产生本身长度三倍以上的延伸率,均属于超塑性。
最初发展的超塑性合金是一种简单的合金,如锡铅、铋锡等。
一根铋锡棒可以拉伸到原长的19.5倍,然而这些材料的强度太低,不能制造机器零件,所以并没有引起人们的重视。
60年代以后,研究者发现许多有实用价值的锌、铝、铜合金中也具有超塑性,于是前苏联、美国和西欧一些国家对超塑性理论和加工发生了兴趣。
特别在航空航天上,面对极难变形的钛合金和高温合金,普通的锻造和轧制等工艺很难成形,而利用超塑性加工却获得了
成功。
到了70年代,各种材料的超塑性成型已发展成流行的新工艺。
现在超塑性合金已有一个长长的清单,最常用的铝、镍、铜、铁、合金均有10~15个牌号,它们的延伸率在200~2000%之间。
如铝锌共晶合金为1000%,铝铜共晶合金为1150%,纯铝高达6000%,碳和不锈钢在150~800%之间,钛合金在450~1000%之间。
实现超塑性的主要条件是一定的变形温度和低的应变速率,这时合金本身还要具有极为细小的等轴晶粒(直径五微米以下),这种超塑性称为超细晶粒超塑性。
还有一些钢,在一定的温度下组织中的相发生转变,在相变点附近加工也能完成超塑性,称为相变超塑性。
超塑加工具有很大的实用价值,只要很小的压力就能获得形状非常复杂的制作。
试想一下,金属变成了饴糖状,从而具有了可吹塑和可挤压的柔软性能,因此过去只能用于玻璃和塑料的真空成型、吹塑成型等工艺被沿用过来,用以对付难变形的合金。
而这时所需的压力很小,只相当于正常压力加工时的几分之一到几十分之一,从而节省了能源和设备。
使用超塑性加工制造零件的另一优点是可以一次成型,省掉了机械加工、铆焊等工序,达到节约原材料和降低成本的目的。
在模压超塑性合金薄板时,只需要具备一种阴模或阳模即可,节省一半模具费用。
超塑性加工的缺点是加工时间较长,由普通热模锻的几秒增至几分钟。
超塑性的铝合金已经商品化,如英国的Supral 100
(Al—6Cu—0.4Zr)和加拿大的Alcan 08050(Al—5Ca—5Zn)。
铝板可在300~600℃时利用超塑性成型为复杂形状,所用模具费用降
低至普通压力加工模具费用的十分之一,因此它具有和薄钢板、铝压铸件及塑料模压件相竞争的能力。
据推测,最近超塑性成形工艺将在航天、汽车、车厢制造等部门中广泛采用,所用的超塑性合金包括铝、镁、钛、碳钢、不锈钢和高温合金等
二.超塑性的发展方向
近年来超塑性在我国和世界上主要的发展方向主要有如下三个方面:
1. 先进材料超塑性的研究,这主要是指金属基复合材料、金属
间化合物、陶瓷等材料超塑性的开发,因为这些材料具有若干优异的性能,在高技术领域具有广泛的应用前景。
然而这些材料一般加工性能较差,开发这些材料的超塑性对于其应用具有重要意义;
2. 高速超塑性的研究:提高超塑变形的速率,目的在于提高超
塑成形的生产率;
3. 研究非理想超塑材料(例如共货态工业合金)的超塑性变形
规律,探讨降低对超塑变形材料的苛刻要求,而提高成形件的质量,目的在于扩大超塑性技术的应用范围,使其发挥更大的效益。
三.超塑性的分类:
早期由于超塑性现象仅限于Bi-Sn和Ai-Cu共晶合金、Zn-Al共析合金等少数低熔点的有色金属,也曾有人认为超塑性现象只是一种特殊现象。
随着更多的金属及合金实现了超塑性,以及与金相组织及
结构联系起来研究以后,发现超塑性金属有着本身的一些特殊规律,这些规律带有普遍的性质。
而并不局限于少数金属中。
因此按照实现超塑性的条件(组织、温度、应力状态等)一般分为以下几种1. 恒温超塑性或第一类超塑性。
根据材料的组织形态特点也称之为微细晶粒超塑性。
1.一般所指超塑性多属这类超塑性,其特点是材料具有微细的等轴晶粒组织。
在一定的温度区间(Ts≥0.5Tm,Ts和Tm分别为超塑变形和材料熔点温度的绝对温度)和一定的变形速度条件下(应变速率在10-4~10-1/S之间)呈现超塑性。
这里指的微细晶粒尺寸,大都在微米级,其范围在0.5~5μ之间。
一般来说,晶粒越细越有利于塑性的发展,但对有些材料来说(例如Ti合金)晶粒尺寸达几十微米时仍有很好的超塑性能。
还应当指出,由于超塑性变形是在一定的温度区间进行的,因此即使初始组织具有微细晶粒尺寸,如果热稳定性差,在变形过程中晶粒迅速长大的话,仍不能获得良好的超塑性。
2. 相变超塑性或第二类超塑性,亦称转变超塑性或变态超塑性。
这类超塑性,并不要求材料有超细晶粒,而是在一定的温度和负荷条件下,经过多次的循环相变或同素异形转变获得大延伸。
例如碳素钢和低合金钢,加以一定的负荷,同时于A1,3温度上下施以反复的一定范围的加热和冷却,每一次循环发生(αγ)的两次转变,可以得到二次条约式的均匀延伸。
等用AISI1018、1045、1095、52100等钢种试验表明,延伸率可达到500%以上,这样变形的特点是,初期时每一次循环的
变形量(△ε∕N)比较小,而在一定次数之后,例如几十次之后,每一次循环可以得到逐步加大的变形,到断裂时,可以累积为大延伸。
有相变的金属材料,不但在扩散相变过程中具有很大的塑性,并且淬火过程中奥氏体向马氏体转变,即无扩散的脆性转变过程(γ→a)中,也具有相当程度的塑性。
同样,在淬火后有大量残余奥氏体的组织状态下,回火过程,残余奥氏体向马氏体单向转变过程,也可以获得异常高的塑性。
另外,如果在马氏体开始转变点(Ms)以上的一定温度区间加工变形,可以促使奥氏体向马氏体逐渐转变,在转变过程中也可以获得异常高的延伸,塑性大小与转变量的多少,变形温度及变形速度有关。
这种过程称为"转变诱发塑性"。
即所谓"TRIP"现象。
Fe-Ni 合金,Fe-Mn-C等合金都具有这种特性。
3. 其它超塑性(或第三类超塑性):在消除应力退火过程中在应力作用下可以得到超塑性。
Al-5%Si及Al-4%Cu合金在溶解度曲线上下施以循环加热可以得到超塑性,根据Johnson试验,在具有异向性热膨胀的材料如U,Zr等,加热时可有超塑性,称为异向超塑性。
有人把a-U在有负荷及照射下的变形也称为超塑性。
球墨铸铁及灰铸铁经特殊处理也可以得到超塑性。
1.1超塑性的概念
超塑性是指材料在特定条件下,表现出异常高的塑性而不产生缩颈与断裂的现象。
但至今还没有从物理本质上的确切定义。
有的以拉伸试验的延伸率来定义,认为即为超塑性;有的以应变速率敏感性指数m来定义,认为m>0.3,即为超塑性;还有的认为抗颈缩能力大,即为超塑性。
1.2超塑性的分类
根据目前世界上各国学者研究的成果,按照实现超塑性的条件(组织,温度,应力状态等)可将超塑性分为三类:
1.微晶组织超塑性(即恒温超塑性或结构超塑性)一般所指超塑性多属这类,它是国内外研究最多的一种。
当材料是微细的等轴晶粒组织,间距为0.5一5μm,温度大于该材料熔点温度的一半,应变速度为10-4一10-1/s之间时,材料拉伸断裂将呈现超塑性变形的能力。
2.相变超塑性(变温超塑性或动态超塑性)
将材料在相变温度附近进行热循环,利用相变过程,每一次热循环贡献一小的应变,从而在多次热循环过程中获得大的延伸率。
3.内应力超塑性
和相变超塑性一样进行热循环,利用材料的热膨胀系数的差异产生内
应力,内应将有助于基体的塑性流动,从而使材料获得超塑性。
1.3超塑性的特点
金属塑性成形时宏观变形有几个特点:大延伸、无缩颈、小应力、易成形。
(1)大变形:超塑性材料在单向时延伸率极高,有的可以到8000%表明超塑性材料在变形稳定性方面要比普通材料好很多。
这样使材料的成形性能大大改善,可以使许多形状复杂,一般难以成形的材料变形成为可能。
(2)无紧缩:超塑性材料的变形类似于粘性物质的流动,没有(或很小)应变硬化效应,但对应变速率敏感,当变形速度增大,材料会强化。
因此,超塑性材料变形时初期有紧缩形成,但由于紧缩部位变形速度增大而发生局部强化,而其余未强化部分继续变形,这样使紧缩传播出去,结果获得巨大的宏观均匀变形。
超塑性的无紧缩是指宏观上的变形结果,并非真的没有紧缩。
(3)小应力:超塑性材料在变形过程中,变形抗力可以很小,因为它具有粘性或半粘性流动的特点。
通常用流动应力来表示变形抗力的大小。
在最佳变形条件下,流动应力要比常规的变形的小到几分之一乃至几十分之一。
(4)易成形:超塑性材料在变形过程中没有或只有很小的应变硬化
现象,所以超塑性材料易于加工、流动性和填充性好,可以进行多种方式成形,而且产品质量可以大大提高。