装载机轮边减速器的多目标模糊可靠性优化设计
装载机变速箱的模糊可靠性优化
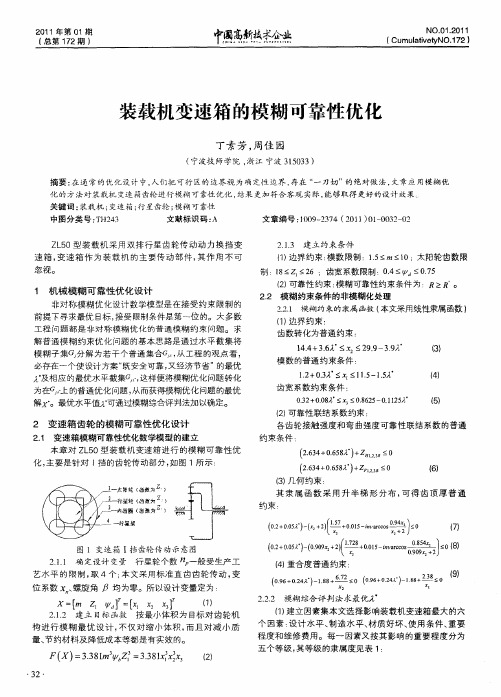
模 数的普通 约束条 件 :
12 2 . +O3 ’ ≤l . —15 15 .2’ () 4
. 的最优 水平截集 - 及相应 , 这样便将模糊 优化 问题 转化
为在 , 的普 通优 化问题 , 而获得模糊 优化 问题 的最优 上 从 解 ’ 。最优 水平值五可通过模糊综合评 判法加 以确定 。
0
(6 +.8’ l 0 2 3 05,) 1 4 6 2 + 2
() 6
其 隶 属 函 数 采 用 升 半 梯 形 分布 , 得齿 顶 厚 普 通 可
约束 :
( 齿数
、 )
(o" ) +5…等) o ) 0- s o “1 .i 25 ( 0n +4 1v . 5 7 。
211 确 定设 计 变量 ..
行星轮 个数 一 般受生产 工
艺水 平 的 限 制 , 4个 ; 文采用 标准 直 齿齿 轮传 动 , 取 本 变
(9 o ) s32 0 +- o6 s s+. .+ 6_ _ o o( : 9
222 模糊 综合 评判 法求最优 ’ ..
s s +
32 .
( 2 )
表 1影 响 因素 、 因素等级 及 隶属 度
1 1
因 素 等级 等级 隶 属度
/ 1 I
量 响 因素 ;
∑ / j> 0 1 ∑b = =.8 =五 6
jt = / , =
() 1 6Biblioteka l l设计 水 平
高
较 高
较低
低
223 模 糊 约 柬转 化为 普通 约束 ..
个 因素 : 计 水平 、 设 制造 水 平 、 质好 坏 、 用 条件 、 材 使 重要 程 度和 维修 费用 。每一 因素 又按 其影 响的重 要程 度分 为
机械系统优化设计中的多目标优化方法

机械系统优化设计中的多目标优化方法引言:机械系统是现代工业中不可或缺的一部分,它们的设计和优化对于提高生产效率和降低成本至关重要。
在机械系统的设计中,多目标优化方法被广泛应用,以实现各种设计指标的最优化。
本文将介绍机械系统优化设计中的多目标优化方法,并探讨其在实际应用中的优势和挑战。
一、多目标优化方法的概述多目标优化方法是一种通过考虑多个设计指标来实现最优解的方法。
在机械系统优化设计中,常见的设计指标包括性能、成本、可靠性、安全性等。
传统的单目标优化方法只考虑一个设计指标,而多目标优化方法则能够在多个指标之间找到一种平衡。
二、多目标优化方法的应用1. 遗传算法遗传算法是一种模拟生物进化过程的优化方法。
它通过模拟自然选择、交叉和变异等过程,逐步搜索最优解。
在机械系统优化设计中,遗传算法能够同时考虑多个设计指标,找到一组最优解,以满足不同的需求。
2. 粒子群算法粒子群算法是一种模拟鸟群觅食行为的优化方法。
它通过模拟粒子在解空间中的移动和信息交流,逐步搜索最优解。
在机械系统优化设计中,粒子群算法能够在多个设计指标之间找到一种平衡,以达到最优化设计。
3. 支持向量机支持向量机是一种基于统计学习理论的优化方法。
它通过构建超平面来划分不同类别的数据,以实现分类和回归的最优化。
在机械系统优化设计中,支持向量机能够通过分析历史数据和建立模型,预测不同设计参数对多个指标的影响,从而实现最优化设计。
三、多目标优化方法的优势和挑战多目标优化方法在机械系统优化设计中具有以下优势:1. 考虑多个设计指标,能够找到一种平衡,满足不同需求。
2. 能够通过模拟自然进化或群体行为的方式进行搜索,提高搜索效率。
3. 能够通过建立模型和分析数据,预测不同设计参数对多个指标的影响,指导设计过程。
然而,多目标优化方法也面临一些挑战:1. 设计指标之间可能存在冲突,需要找到一种平衡的解决方案。
2. 多目标优化问题的解空间通常非常大,搜索过程可能非常复杂和耗时。
JS40矿用减速器的优化及可靠性分析
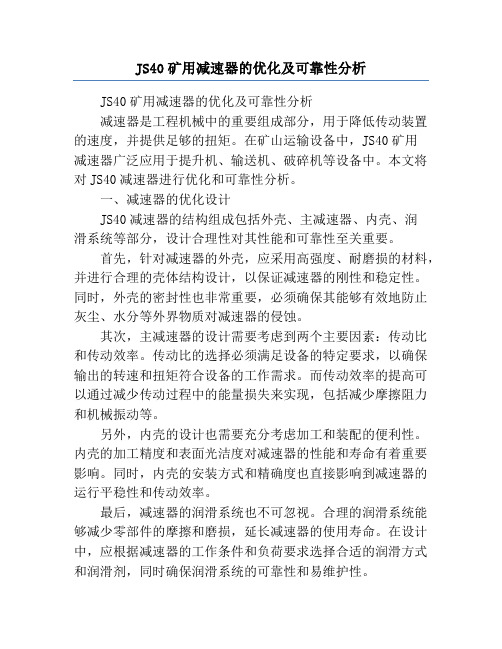
JS40矿用减速器的优化及可靠性分析JS40矿用减速器的优化及可靠性分析减速器是工程机械中的重要组成部分,用于降低传动装置的速度,并提供足够的扭矩。
在矿山运输设备中,JS40矿用减速器广泛应用于提升机、输送机、破碎机等设备中。
本文将对JS40减速器进行优化和可靠性分析。
一、减速器的优化设计JS40减速器的结构组成包括外壳、主减速器、内壳、润滑系统等部分,设计合理性对其性能和可靠性至关重要。
首先,针对减速器的外壳,应采用高强度、耐磨损的材料,并进行合理的壳体结构设计,以保证减速器的刚性和稳定性。
同时,外壳的密封性也非常重要,必须确保其能够有效地防止灰尘、水分等外界物质对减速器的侵蚀。
其次,主减速器的设计需要考虑到两个主要因素:传动比和传动效率。
传动比的选择必须满足设备的特定要求,以确保输出的转速和扭矩符合设备的工作需求。
而传动效率的提高可以通过减少传动过程中的能量损失来实现,包括减少摩擦阻力和机械振动等。
另外,内壳的设计也需要充分考虑加工和装配的便利性。
内壳的加工精度和表面光洁度对减速器的性能和寿命有着重要影响。
同时,内壳的安装方式和精确度也直接影响到减速器的运行平稳性和传动效率。
最后,减速器的润滑系统也不可忽视。
合理的润滑系统能够减少零部件的摩擦和磨损,延长减速器的使用寿命。
在设计中,应根据减速器的工作条件和负荷要求选择合适的润滑方式和润滑剂,同时确保润滑系统的可靠性和易维护性。
二、减速器的可靠性分析减速器的可靠性是指其在预定的时间内保持正常工作的能力。
通过可靠性分析,可以评估和提高减速器的工作稳定性和寿命。
可靠性分析应包括以下内容:1. 故障模式和影响分析(FMEA):对减速器的关键部件和工作环境进行分析,确定可能出现的故障模式,并评估故障对减速器性能和运行的影响。
2. 寿命预测:通过实验和数据分析,估计减速器的寿命,并根据寿命预测结果进行故障预警和维护计划制定。
3. 可靠性指标评估:通过计算减速器的可靠性指标,如平均无故障时间(MTTF)、平均故障时间(MTBF)等,评估减速器的可靠性水平。
XDE400矿用电动轮自卸车轮边减速器传动系统优化设计

XDE400矿用电动轮自卸车轮边减速器传动系统优化设计随着矿用电动车辆在矿山工作中的广泛应用,其轮边减速器传动系统的设计变得尤为重要。
XDE400矿用电动轮自卸车是一种性能卓越的矿用自卸车,其轮边减速器传动系统设计的性能直接影响了车辆的工作效率和可靠性。
本文将对XDE400矿用电动轮自卸车的轮边减速器传动系统进行优化设计,以提高其性能和可靠性。
1.现有轮边减速器传动系统存在的问题在XDE400矿用电动轮自卸车的现有轮边减速器传动系统中,存在一些问题需要优化。
首先,传动效率较低,造成能源的浪费。
其次,传动系统的结构设计不够合理,导致使用寿命较短,易出现故障。
另外,传动系统的噪音和振动较大,影响了车辆的舒适性和稳定性。
2.优化设计方案为解决上述问题,我们提出了以下优化设计方案:(1)优化传动结构针对现有传动系统结构设计不合理的问题,我们采用了新型的轮边减速器传动系统结构。
通过对齿轮、轴承和油封等关键部件的优化设计,提高了传动系统的使用寿命和可靠性。
此外,采用新型减震器和减振装置,有效降低了传动系统的噪音和振动。
(2)提高传动效率为提高传动效率,我们选用了高效率的传动部件和润滑系统。
优化齿轮的设计,减小齿轮传动时的能量损失;采用高质量的轴承和密封件,减少摩擦力和能量损失;优化油路系统,确保润滑油的充分循环和冷却。
这些措施有效提高了传动效率,减少了能源的浪费。
(3)增加智能化控制系统为提高矿用电动轮自卸车的自动化程度,我们增加了智能化控制系统。
通过传感器和控制器的精确监测和控制,实现了传动系统的智能化调节和优化。
例如,根据车速和工况自动调整传动比;实时监测传动系统的运行状态,提醒维护和保养。
3.结果与展望经过优化设计,XDE400矿用电动轮自卸车的轮边减速器传动系统性能得到了显著提升。
传动效率和可靠性大幅提高,传动系统的噪音和振动也得到了有效控制。
智能化控制系统的引入,使车辆的操作更加简便和安全。
未来,我们将继续研究和改进,不断提升矿用电动车辆的性能和可靠性,为矿山工作提供更好的技术支持。
机械减速器齿轮传动的优化设计解读

机械减速器齿轮传动的优化设计内容摘要:单级的,是一个多目标优化问题。
事实上把所有的优化原则作为优化目标,很难同时达到最优,只能在综合考虑各个目标的情况下,应用模糊可靠性理论将设计过程中大量的模糊数据进行科学的处理,定量的分析和研究,通过综合评价来求得一合适的优化方案。
关键词:;;;具有传递功率大,冲击小,维修方便,使用寿命长等许多优点,在工业上得到了广泛应用。
因此,对该种进行,具有可观的经济效益。
单级模糊可靠性方法:应用模糊可靠性理论能够将设计中的模糊因素和模糊主观信息定量化,通过合理给定约束函数、目标函数的容许值、期望值及其模糊分布(隶属函数)来求得一合适的优化方案。
例如:某大型机械采用单级圆柱齿轮,传动参数为:z1=33,z2=105,m n=3.5,ß=14º59′,b1=b2=100mm;小齿轮材料为38siMnMo、调质,硬度为220~240HB。
高速轴许用功率P1为80kW,高速轴转速730r/min,单向运转,长期连续工作。
要求以常用定型的有关参数和设计规范为基础,传动比允许误差±5%,在满足各约束的条件下,使具有最紧凑的结构。
一、数学模型的建立1、确定设计变量由原始条件可知,中齿轮传动需确定的参数值为:齿轮法向模数m n,小齿轮齿数z1,分度圆螺旋角ß,齿宽b(取两轮齿宽相等)。
则设计变量为X=[x1,x2,x3,x4]T=[m n,z1,ß,b]T。
2、建立目标函数根据设计要求,以最小体积为追求的目标,既可减轻重量,又可节约材料,降低成本。
为简化计算,用齿轮分度圆圆柱体积来近似代替齿轮的体积,则目标函数可表示为:3、建立模糊约束条件约束条件有性能约束和几何变量约束两部分,对于应力等性能约束,必须考虑其从完全许用到完全不许用的中间过渡过程,对于几何变量约束,必须考虑其边界实际存在的模糊性。
这些约束均为设计空间的模糊子集,建立约束条件如下:(1)接触应力约束 根据公式有:由齿轮材料可知,小齿轮优于大齿轮,取大齿轮硬度为220HB ,查得бHlim2=570Mpa ,推荐取[бH ]=0.96бHlim ,则有[бH2]=513Mpa ,于是有:(2)弯曲应力约束 根据公式有:由原始条件取小齿轮HB=260,大齿轮HB=220,查得бFlim1=600Mpa ,бFlim2=490Mpa 。
小议机械系统的可靠性模糊优化设计

小议机械系统的可靠性模糊优化设计系统可靠性模糊优化设计既考虑了随机性因素对系统的影响,又考虑了模糊性因素对系统的影响,其优化的结果往往比普通优化设计、可靠性设计、模糊优设计的结果要好。
标签:可靠性模糊优化系统优化最优解系统可靠性的优化设计是指在满足费用、体积、重量、尺寸性能等条件的约束下,使统可靠性达到最高,或是在满足一定可靠性指标要求的条件下使投资最少,以取得最大经济效益的设计方法。
在实际工程设计问题中,一般都要求兼顾多个目标,即要求多个目标同时达到最优。
针对实际情况,应用模糊理论进行研究。
在机械设计领域中存在着许多不确定性现象,它的主要表现之一就是模糊性。
所谓模糊就是边界不清楚,如设计工作中遇到的许用应用力,就是模糊概念。
众所周知,当许应用力[σ]=980MPa时,对于应力σ=980.098MPa便为强度不足,但实际上两者并无差别。
也就是说事物从可用到完全不可用之间存在一个过渡阶段,这个阶段就是模糊区。
在优化设计时考虑影响设计的各种因素的模糊性,就是模糊优化设计,进行模糊优化设计,不仅优化效果台大大提高,而且,由于考虑了很多不确定因素的主观信息,使优化结果更具实际意义。
一、多目标模糊优化设计的理论基础和普通优化相似,模糊优化的数学模型也是从设计变量、目标函数、约束条件三个方面给出的。
模糊优化的设计变量,仍是决定设计方案的、可由设计人员调整的、独立变化的参数。
这些参数在过去常被视为是确定性的,但严格说来,大多具有不同程度的模糊性。
模糊优化的目标函数,仍是衡量设计方案优劣的某一个或某几个指标。
“优”和“劣”本身,都是模糊概念,没有确定的界限和标淮。
通常说,要使某指标达到某个值附近,或达到某一范围内,或越小越好等等,这些说法实际上反映了目标函数的模糊性。
面且,由于目标函数是设计变量的函数,当考虑设计变量的模糊性时,目标函数也必然是模糊的。
模糊优化的约束条件,仍是限制设计变量取值的条件。
这些约束条件大体上有三个方面:一是几何约束;二是性能约束;三是人文因素约束。
基于MATLAB的多级齿轮传动多目标可靠性优化设计研究

基于MATLAB的多级齿轮传动多目标可靠性优化设计研究I. 内容概述随着工业自动化的发展,多级齿轮传动系统在各个领域得到了广泛的应用。
然而由于其复杂的结构和工作条件,齿轮传动系统的可靠性一直是设计者关注的重点。
为了提高齿轮传动系统的可靠性,本文提出了一种基于MATLAB的多级齿轮传动多目标可靠性优化设计方法。
首先本文对多级齿轮传动系统的工作原理进行了详细的阐述,包括齿轮啮合、齿面接触、磨损和疲劳等方面的问题。
在此基础上,分析了齿轮传动系统的可靠性评价指标体系,包括寿命、失效率、维修性等关键性能指标。
其次针对多级齿轮传动系统的可靠性优化设计问题,本文提出了一种基于遗传算法和粒子群优化算法的多目标优化设计方法。
通过对比分析不同优化算法的优缺点,最终确定了基于MATLAB的遗传算法作为本研究的主要优化方法。
本文以某型号齿轮传动系统为例,运用所提方法对其进行了多目标可靠性优化设计。
实验结果表明,所提方法能够有效地提高齿轮传动系统的可靠性指标,为实际工程应用提供了有力的理论支持。
A. 研究背景和意义随着科学技术的不断发展,齿轮传动技术在各个领域的应用越来越广泛。
齿轮传动具有传动效率高、承载能力大、传动精度高等优点,因此在工业生产中得到了广泛的应用。
然而齿轮传动系统的可靠性一直是制约其性能的重要因素,为了提高齿轮传动系统的可靠性,降低故障率,保证设备的正常运行,需要对齿轮传动系统进行多目标可靠性优化设计。
目前基于数值计算的可靠性优化设计方法已经成为齿轮传动系统研究的主要手段。
MATLAB作为一种广泛应用于工程领域的数值计算软件,具有强大的数学运算能力和图形化编程功能,为齿轮传动系统的可靠性优化设计提供了有力的支持。
因此基于MATLAB的多级齿轮传动多目标可靠性优化设计研究具有重要的理论和实际意义。
首先研究基于MATLAB的多级齿轮传动多目标可靠性优化设计方法有助于提高齿轮传动系统的可靠性。
通过合理的参数设置和优化策略选择,可以有效地提高齿轮传动系统的可靠性指标,降低故障率,延长设备使用寿命。
机械优化设计中的多目标优化问题
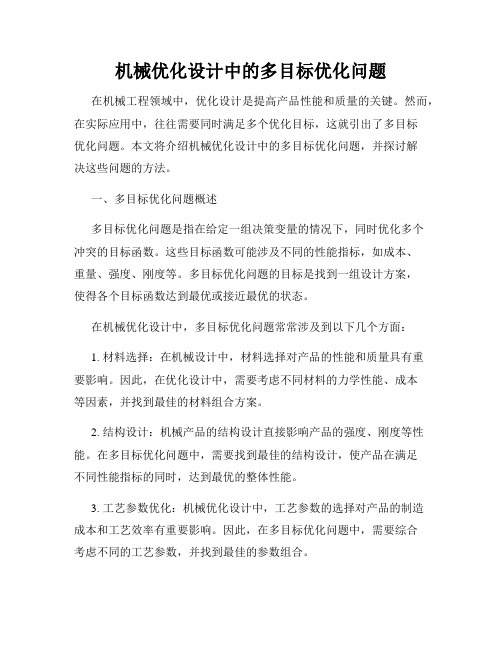
机械优化设计中的多目标优化问题在机械工程领域中,优化设计是提高产品性能和质量的关键。
然而,在实际应用中,往往需要同时满足多个优化目标,这就引出了多目标优化问题。
本文将介绍机械优化设计中的多目标优化问题,并探讨解决这些问题的方法。
一、多目标优化问题概述多目标优化问题是指在给定一组决策变量的情况下,同时优化多个冲突的目标函数。
这些目标函数可能涉及不同的性能指标,如成本、重量、强度、刚度等。
多目标优化问题的目标是找到一组设计方案,使得各个目标函数达到最优或接近最优的状态。
在机械优化设计中,多目标优化问题常常涉及到以下几个方面:1. 材料选择:在机械设计中,材料选择对产品的性能和质量具有重要影响。
因此,在优化设计中,需要考虑不同材料的力学性能、成本等因素,并找到最佳的材料组合方案。
2. 结构设计:机械产品的结构设计直接影响产品的强度、刚度等性能。
在多目标优化问题中,需要找到最佳的结构设计,使产品在满足不同性能指标的同时,达到最优的整体性能。
3. 工艺参数优化:机械优化设计中,工艺参数的选择对产品的制造成本和工艺效率有重要影响。
因此,在多目标优化问题中,需要综合考虑不同的工艺参数,并找到最佳的参数组合。
二、解决多目标优化问题的方法对于机械优化设计中的多目标优化问题,存在多种解决方法。
下面将介绍几种常用的方法:1. 基于加权求和法(Weighted Sum Method)的目标权重法:该方法将多个目标函数加权求和,通过调整权重的比例,将多目标优化问题转化为单目标优化问题。
然后可以使用传统的单目标优化方法求解。
2. 基于约束法的目标优化法:该方法将多目标优化问题转化为一个约束优化问题,通过设置适当的约束条件,将多个目标函数的值限定在一定的范围内。
3. 基于遗传算法的多目标优化法:遗传算法是一种模拟自然选择和遗传机制的优化算法。
通过模拟个体的遗传、交叉和变异过程,逐步优化设计变量,找到最优的设计方案。
三、案例分析以飞机机翼结构设计为例,介绍多目标优化问题在机械优化设计中的应用。
- 1、下载文档前请自行甄别文档内容的完整性,平台不提供额外的编辑、内容补充、找答案等附加服务。
- 2、"仅部分预览"的文档,不可在线预览部分如存在完整性等问题,可反馈申请退款(可完整预览的文档不适用该条件!)。
- 3、如文档侵犯您的权益,请联系客服反馈,我们会尽快为您处理(人工客服工作时间:9:00-18:30)。
C∀H lim=
2 CZ
X
[
C 2H lim +
]
1 2
! !!! !! !! !! !! !! !! ! ( 13) !! ! ( 14)
~
通常 ∀= 1 05~ 1 30, ∀= 0 70~ 0 95, ∀, ∀ 的具体 取值大小可根据实际情况确定。
式中各系数取值参见文献 [ 1] 。 同理得约束条件 : Z R H - [ Z R H ] #0
Multi objective fuzzy reliability optimum design of wheel side reducer for loader
Wen Fang, Huang Hualiang Ma Xintan
Abstract The mathematic model of the fuzzy reliability optimum design having double objective gear volume and width was established and explained on ex ample while the randomness and fuzziness of all parameter was considered. Key words: Loader Wheel side reducer Fuzzy reliability Optimum design
i = 1, 2 !I ; s . . s . t.
二、 模糊约束的隶属函数的确定
以上各模糊约束的边界从完全许用到完全不许用 的中间过渡过程 , 具有一定的隶属函数。应根据约束 的性质和设计要求来确定隶属函数 , 为计算方便, 此处 均采用线性隶属函数。 1 接触强度的模糊可靠性约束、 弯曲强度的模糊 可靠度约束、 邻接条件及孔径约束的隶属函数均选用 升半梯形分布, 如图 2 所示。 2 设计变量约束隶属函数选梯形分布, 见图 3。
2 F lim + 2 2 2 2
!!
!! !! !! !! !! !! !! !! !! ! ( 6) C
1 ∀ Fl im=
[C
C YST + C YNT + C Y∃rel + Y YRrel +
C2 YX ] 2 ! !! !! !! !! !! !! !! !! ! ( 7) 式中, K 1 、 K 2、 K 3 为装载机的影响系数 , 取值参见 文献 [ 2] 。 再由应力、 强度均为对数正态分布时的联立方程, 可求得弯曲强度的可靠度系数 : Z RF = ln
表1 模糊可靠性优化设计结果
基 设计方法 z1 普通优化设计 模糊可靠性 优化设计 16 16 z2 23 23 z3 62 62 m 6 6
d
由上式求得 的 X * 便 是多目 标优化 问题的 最优 解。 这样, 多目标优化问题即可转化为如下的单目标 优化问题求解: 求% , X 。max % ; s. t . gj ( X ) % 0 j = 1, 2, !; &f i ( X ) #% i = 1, 2; 0 % %% 1。
2 2 2 2 变异系数 C F = [ C 2 FM + C T 1 + C KA + C K V + C K F!+ 2 2 C2 K F∀ + C YF + C YS ] 2 1
太阳轮 内齿圈
一、 模糊可靠性优化设计的数学模型建立
1 设计变量 轮边减速 器的 设计参 数有模 数 m, 太 阳轮 齿数 z 1, 行星轮齿数 z 2 , 内齿圈齿数 z 3 , 齿宽系数
3 2 dz 1 [ z 1 + 2 z 2+ 2 z 3] d T d] T
! !! !! !! !! !! ! ( 5)
式中各符号均表示为其下角标变量的变异系数, 取值参见文献[ 1] 。 齿根弯曲疲劳极限均值和变异系数为:
∀ F lim =
= [ x 1 , x 2 , x3 ]
T
K 1 K 2K 3 F lim YST YNT Y∃ relT YRrelT YX
装载机轮边减速器普遍采用直 齿圆柱齿轮行星传动 ( 见图 1) 。目 前在 设计这 种传动 时, 常 规设 计和 普通优化设 计均 采用安 全系数 法, 即将应力和强度等变量视为确定性 变量 , 忽略 了这些 参数的 随机 性和 模糊性。本文 研究运 用模 糊理 论, 结合 可靠性 设计和 最优化 技术 , 使 该设计更为合理。
T
% 0 75 ~
4 确定性约束条件 1) 装配条件 : ( z 1 + z 3 ) / np = ∀ ! !! !! ! ( 18) 式中 , ∀ 为正整数。 2) 传动比条件: z 3 = ( i - 1) z 1 ! !! !! ! ( 19) 3) 同心条件 : z 1 + z 2 = z 3 - z 2 ! !! !! ! ( 20)
设备设计与维修
装载机轮边减速器的多目标模糊可靠性优化设计
温
摘要
芳
黄华梁
马心坦
在充分考虑轮边减速器各设计参数的随机性和模糊性的 基础上 , 建立以体 积和齿宽 最小为双目 标的模 糊可靠 性 轮边减速器 模糊可靠性 优 化设计 0086 03
优化数学模型 ; 给出求解此模型的方法 , 并对实例进行模糊可靠性优化设计 。 关键词 : 装载机 中图分类号 :T B11 文献标识码 : A 文章编号 : 1671 3133( 2004) 05
2) 接触强度的模糊可靠性约束 同理 , 齿轮接触应力 H 和接触强度 [ ] H 也是一 服从对数正态分布的随机变量 , 其均值为:
H= 1 2
ZEZH Z# 2000 T 1 K A K V KH ! KH ∀ 1+ i mz
mz d
∃
i
! !! !! !!! !( 10) 式中 , Z E 为弹性影响系数均值; ZH 为区域系数。
) Xj + % ( X j - X j ) % X % X j - % ( Xj - Xj ) ( j = 1, 2 !
L * u L u * u L *
3) 邻接条件 : m( z 1+ z 2 ) sin
np
- m( z 2 + 2) # l
式中 , l 为相邻星轮间隙下限。 4) 孔径约束条件 mz 1 - ( d + 2 h 1 ) #~ ∃ 1 mz 2 - ( d + 2 h 2 ) #~ ∃ 1 !! !! !! !! ! ( 16)
1 轮边减速器行 星齿 轮传动
2 行星轮 4 行星架
由文献 [ 1] 可知, 一般认为齿轮弯曲应力 曲强度[ ] F 均服从对数正态分布, 其均值为: 齿根弯曲应力均值:
F=
F
和弯
2000 T 1 KA K V K F ! K F∀ YF YS Y# 3 2 m z1 d
!! ! ( 3)
T 1 = ( T !/ np ) K p ! !! !! !! !! !! ! ( 4) 式中, T ! 为轮边减速器的输入转矩, 计算方法参 见文献 [ 2] ; K p 为行星轮间载荷分配不均匀系数, K p = 1 15; K A 、 K V、 K F!、 K F ∀、 YF 、 YS 、 Y# 分别为 使用情况系 数均值、 动载系数均值、 齿间载荷分配系数均值、 齿向 载荷分布系数均值、 齿形系数均值、 尺寸系数均值和重 合度系数 , 取值参见文献 [ 1] 。
q
q=
1 1 , , ! 2 3
3 构造模糊判决 D = i= & fi 1 87
设备设计与维修
其隶属函数为: & D(X)= ∋ & fi ( X ) i= 1 4 求最优解 & D ( X ) = max & D ( X ) = max ∋ & fi ( X ) i= 1
*
I I
将模糊可靠性优化设 计方案与普通 优化方案比 较, 轮边减速器的体积和齿宽分别减小了 21 88% , 且 具有较高的可靠性。由此可见, 在模糊可靠性优化设 计中由于考虑了设计参数的随机性和模糊性 , 使设计 更符合实际、 更科学、 更合理, 具有一定的实用价值。
现代制造工程 2004( 5)
X = [ x 1, x 2 , x 3] T ; maxf ( X ) i = 1, 2 !I ; gj (X ) % 0 j = 1, 2, !。 设求得其最大值和最小值分别为 M i , m i 。 2 各子目标函数模糊化 & fi( X ) =
I
Mi- f i( X ) Mi - m i
∀ F lim F
式中 , f 1 ( X ) = V1 + 3 V 2 + V3 = f 2 ( X ) = b = mz 1 3 模糊约束条件 1) 弯曲强度的模糊可靠性约束 86
b[
d2 1+
3d 2 2+
d2 3]
/
/ 4 !! !! !! !! ! ( 1) !! !! !! !! !! ! ( 2)
采用扩增系数法确定。扩增系数法是在充分考虑了以 往普通设计规范和设计经验的基础上, 引入增扩系数 ∀ 来确定过渡区间上、 下界的一种方法。 u 如 Xj % X j % X j , 取 X L j = X j , X j = ∀Xj