塑性成形中的CAE应用
板料成形CAE分析

板料成形CAE分析实验报告班级:学号:姓名:板料成形CAE分析一、实验目的和要求:通过本实验的教学,使学生基本掌握有限元技术在板料塑性成形领域的应用情况,拓宽学生的知识面,开阔视野,使学生对塑性成形过程的数值模拟技术有深刻的理解,预测板料弯曲成形的性能。
二、教学基本要求:学会使用Dynaform数值模拟软件进行板料弯曲成形过程的仿真模拟,对模拟结果具有一定的分析和处理能力。
三、实验内容提要:掌握前处理的关键参数设置,如零件定义、网格划分、模型检查、工具定义、坯料定义、工具定位和移动、工具动画、运行分析。
了解后处理模块对模拟结果的分析,如读入d3plot 文件、动画显示变形和生成动画文件、成形极限图分析、坯料厚度变化分析等。
四、实验步骤1、导入零件模型,保存文件打开下拉菜单File->Import,如图2所示,在F:\dynaform\BLANK_CAE目录下分别导入文件punch.igs,binder.igs,die.igs和blank.igs。
图1 导入文件窗口3、更改零件层名打开下拉菜单Parts->Edit,对应不同的零件更改层名,改好层名后保存文件。
图2 修改层名窗口4、进行网格划分以blinder为例进行说明。
(1)、点击,只选择binder1(红色),点击OK退出。
图3(2)、选择Preprocess—>Element进入如图3界面。
选择,在surf mesh中将max size 改为5.图4 图5(3)、依次选select surfaces—>displayed surf-->0k-->apply,然后依次退出各个页面。
网格化后的零件如图6所示。
图6网格化后的零件4、检查工具。
仍然以binder为例。
(1)、点击preprocess—>model check,出现如图7界面。
图7(2)、点击,选择cursor pick part,点击工具的小格单元,出现如图8界面。
模流分析CAE在塑料成型模具设计中的应用

以不 同颜色显示塑件 脱模 后冷却至
室温常压下在三个 坐标方 向的总尺寸变 化 ( 位移 ) 。总 位移 :图 7 代表总位移的分 布情 形 ,此分 布综合 了成型
过程中的所有效应 ,此分布值乃相对 于网格模型原点 。
值 ,由流道至充填末端渐减 ,最大压力值可提供 射出机 之锁模力值 。压力分 布是否 均匀 ,显示 压力传 递效果 。 评估模具中厚度及温度对于压力分布及损耗的影响 。 ()温度分布 2 以不 同颜色显示充填结束 瞬间,塑
件流动波前分析 ,并 了解流道与浇 口所需 要的压力 ,以
流动应力是否过高 ,以作为是否使塑料产生裂解及 过度
残余应力 (ciu t s) 的参 考 。如 其值过 大 ( 于 rs ases d r 大 1 P) M a ,则造成产品 日后可能产生断裂 。
评估流道引起的压力降是否过大 ,同时判断流道设计 与
测试 的翘 曲分析——总位移
( )设计验证 结论分析 7
利用 M le3 odxD进行流道
模穴各处剪切应力分布情形 。剪切应力代 表塑料在加工
过程中由于剪切流动造成 的应力大小 。可 由图判别 塑料
设计系统与浇 口 位置的评估 :流道系统与浇 口设计是成 型品品质好坏 的第一要素,观察 流动波前模 拟 了解熔融 塑料 自 射嘴注入模穴的行 为,例如 图 3 所展 示的产品制
形 ,可预测缝合线及包封位置 ,且可 判断是 否会有短射
问题焦点 :本产品采用两穴 两点直接 中间连浇 。要
求对模具流道设计系统与浇 1位 置评估 ,了解 穴 内充 填 2 1 平顺性 ,防止短射与过度充填 。对 保压是否 充分传 递及 预 防零件翘 曲行为及产品厚度 进行分析 。产 品模型 参数 如表 l 所示 。针对该塑料 料制件 的模 拟成型条 件如 图 2
模具CAE的应用基础知识概述
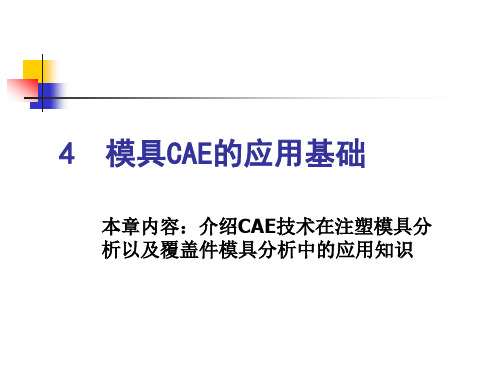
•
9、
。上 午7时51 分25秒 上午7 时51分0 7:51:25 20.11.1 1
• 10、一个人的梦想也许不值钱,但一个人的努力很值 钱。11/11/2020 7:51:25 AM07:51:252020/11/11
• 11、在真实的生命里,每桩伟业都由信心开始,并由 信心跨出第一步。11/11/2020 7:51 AM11/11/2020 7:51
成功源于不懈的努力,人生最大的敌人是自己怯懦
•
2、
。0 7:51:25 07:51:2 507:511 1/11/2 020 7:51:25 AM
每天只看目标,别老想障碍
•
3、
。20.1 1.1107: 51:250 7:51Nov -2011-Nov-20
宁愿辛苦一阵子,不要辛苦一辈子
•
4、
。07:5 1:2507: 51:250 7:51We dnesda y, November 11, 2020
4 模具CAE的应用基础
本章内容:介绍CAE技术在注塑模具分 析以及覆盖件模具分析中的应用知识
塑料成型分析的优点
对注塑流动、保压、冷却等注塑成型过程进行 数值模拟、可视化动态显示以及统计计算。
使得模具制造之前,预测模具设计和成型条件 对产品地影响,发现可能出现的缺陷,为判断 模具设计条件是否合理提供科学的依据。
一个应用例子
FASTFORM的应用实例
选择FASTBLANK菜单,选择所有面。
选择材料,这里内置数据库可以自定 义。
选择材料厚度
选择压力方向,系统默认为Z轴。
点击OK按钮
则网格划分的对话框出现,输入网格的尺寸。或者 由系统自动生成。
关闭渲染,观察网格,选择YES或NO。
注塑成型填充工艺的CAE分析及应用实施

注塑成型填充工艺的CAE分析及应用实施注塑成型技术一直以来都是塑料加工技术中最常用的一种方法,但是在注塑成型过程中,如何保证填充效果和产品品质一直是工程师们所关注和研究的重点。
为了解决这些问题,CAE技术的应用越来越广泛。
下面,我们将深入探讨注塑成型填充CAE分析及应用实施。
首先,注塑成型的填充过程是非常复杂的,需要考虑到非常多的因素。
如果我们只是采用试错的方式来完善产品,不仅会耗费大量的物料和时间,而且效率非常低。
因此,将CAE技术应用于注塑成型填充的分析中,可以减少试验次数,提高生产效率,更加有效地规避制造过程中的困难。
其次,注塑成型填充CAE分析需要进行以下几个方面的分析:1.塑料材料的分析:塑料材料和熔体的流动性能和熔指数值非常重要,这对于填充和制品的品质有着非常重要的影响。
2.模具结构分析:模具的结构特点会影响注塑成型成本和生产周期。
例如,模具腔的数量和大小、针阀的位置、冷却方式等因素都需要考虑到。
3.填充过程分析:注塑成型过程中的力学运动和热学特征也是需要考虑的关键因素。
例如,熔胶的流速、温度、压力、流动路径和填充时间等都会影响填充效果。
通过CAE仿真软件的应用,可以更加精确地模拟注塑成型过程,进而确定最佳的产品结构,提高生产效率和质量。
最后,注塑成型填充CAE分析的应用实施需要注意以下几点:1.选择合适的CAE仿真软件:在选择CAE仿真软件时,需要考虑成本、易用性、功能等因素。
2.收集准确数据:进行仿真分析必须透彻了解塑料材料、模具结构和注塑成型过程中的各种参数,所以必须收集到尽可能准确的数据。
3.与现实结果对比:在分析过程中,需要对分析结果与实际结果进行对比,以验证分析的准确性。
总之,注塑成型填充CAE分析是一种非常有效的方法,可以帮助企业降低成本,提高生产效率和维持产品品质。
相关数据分析是在各个领域中进行有效决策的重要工具。
以下是一个样本数据集的分析。
数据集:一家企业去年的销售额(单位:美元)。
第1章塑性成形CAE技术分析
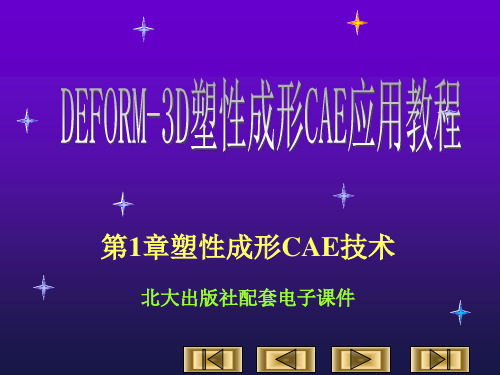
1.3.2DEFORM 的特点
• DEFORM-3D模型来自CAD系统的面或 实体造型(STL/SLA)格式。 • 集成有成形设备模型,如:液压压力机、 锤锻机、螺旋压力机、机械压力机等。 • 表面压力边界条件处理功能适用于解决 胀形工艺模拟。 • 单步模具应力分析方便快捷,适用于多 个变形体、组合模具、带有预应力环时 的成形过程分析。
1.3.1DEFORM的发展
• 20世纪70年代后期,位于美国加州伯克 利的加利福尼亚大学小林研究室在美国 军方的支持下开发出有限元软件ALPID (Analysis of Large Plastic Incremental Deformation)。 • 1990年在此基础上开发出DEFORM-2D软 件。该软件的开发者独立出来成立SFTC 公司(Scientific Forming Technologies Co.)
• 但是,这些研究和应用的领域以及分布 的行业和地区还很有限,现在还主要局 限于少数具有较强经济实力的大型企业、 部分大学和研究机构。
• 我国的计算机分析软件开发是一个薄弱 环节,严重地制约了CAE技术的发展。
金属塑性成形技术
• 金属塑性成形技术是现代制造业中 金属加工的重要方法之一,它是金属坯 料在模具的外力作用下发生塑性变形, 并被加工成棒材、板材、管材以及各种 机器零件、构建或日用器具等技术。
• DEFORM-3D图形界面既强大又灵活,为 用户准备输入数据和观察结果数据提供 了有效工具,DEFORM-3D还提供了3D 几何操纵修正工具,这对于3D过程模拟 极为重要。 • 在最近的国际范围复杂零件成形模拟招 标演算中,DEFORM-3D的计算精度和结 果可靠性,被国际成形模拟领域公认为 第一。
CAE的应用,(在塑胶模具中)

CAE技术在注射模具设计及制造中的应用一、引言模具是生产各种工业产品的重要工艺装备,随着塑料工业的迅速发展,以及塑料制品在航空、航天、电子、机械、船舶和汽车等工业部门的推广应用,产品对模具的要求也越来越高,传统的模具设计方法已无法适应当今的要求。
与传统的模具设计相比,计算机辅助工程(CAE)技术无论是在提高生产率、保证产品质量方面,还是在降低成本、减轻劳动强度方面,都具有极大的优越性。
美国MOLDFLOW 上市公司是专业从事注塑成型CAE软件和咨询公司,自1976年发行了世界上第一套流动分析软件以来,一直主导塑料成型CAE软件市场。
MOLDFLOW一直致力于帮助注塑厂商提高其产品设计和生产质量,MOLDFLOW的技术和服务提高了注塑产品的质量,缩短了开发周期,也降低了生产成本,MOLDFLOW已成为世界注塑CAE的技术领袖。
二、CAE技术的作用利用CAE技术,可以在模具加工前,在计算机上对整个注塑成型过程进行模拟分析,准确预测熔体的填充、保压和冷却情况,以及制品中的应力分布、分子和纤维取向分布、制品的收缩和翘曲变形等情况,以便设计者能尽早发现问题并及时进行修改,而不是等到试模后再返修模具。
这不仅是对传统模具设计方法的一次突破,而且在减少甚至避免模具返修报废、提高制品质量和降低成本等方面,都有着重大的技术、经济意义。
塑料模具的设计不但要采用CAD技术,而且还要采用CAE技术,这是发展的必然趋势。
三、CAE技术应用实例制件为电脑面板,一模一腔,材料为CHIMEI ABS‘POLYLAC PA707’。
采用MPI的流动、保压、冷却和变形分析模块检查塑件的质量,并得到优化的流道设计。
1.建模可在其他CAD软件中建模,MOLDFLOW通过图形接口,直接读入CAD模型,或在MOLDFLOW建模模块中直接建模。
模型及浇注系统,浇注系统初始设计使用两个侧浇口,如图1所示。
图1 模型及其浇注系统2.工艺参数型腔温度为60.0deg.C,熔体温度为240.0deg.C,注射流动速率172cu.cm/sec,注射时间为2.22sec,保压时间为8.0sec,冷却时间为15.0sec,开模时间为10.0sec。
塑料模具设计中CAE技术的应用
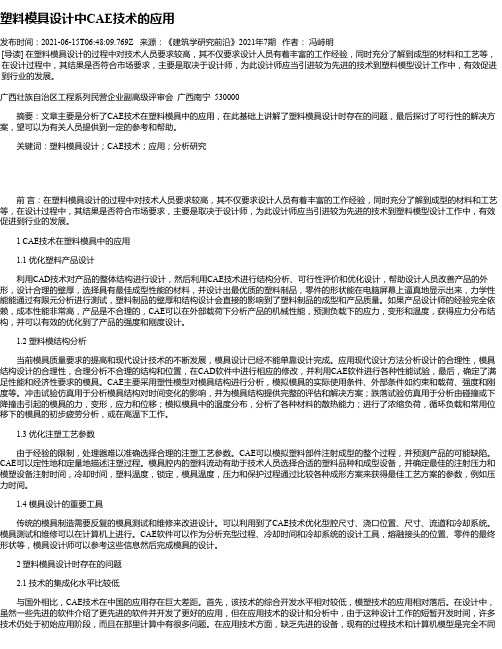
塑料模具设计中CAE技术的应用发布时间:2021-06-15T06:48:09.769Z 来源:《建筑学研究前沿》2021年7期作者:冯峙明[导读] 在塑料模具设计的过程中对技术人员要求较高,其不仅要求设计人员有着丰富的工作经验,同时充分了解到成型的材料和工艺等,在设计过程中,其结果是否符合市场要求,主要是取决于设计师,为此设计师应当引进较为先进的技术到塑料模型设计工作中,有效促进到行业的发展。
广西壮族自治区工程系列民营企业副高级评审会广西南宁 530000摘要:文章主要是分析了CAE技术在塑料模具中的应用,在此基础上讲解了塑料模具设计时存在的问题,最后探讨了可行性的解决方案,望可以为有关人员提供到一定的参考和帮助。
关键词:塑料模具设计;CAE技术;应用;分析研究前言:在塑料模具设计的过程中对技术人员要求较高,其不仅要求设计人员有着丰富的工作经验,同时充分了解到成型的材料和工艺等,在设计过程中,其结果是否符合市场要求,主要是取决于设计师,为此设计师应当引进较为先进的技术到塑料模型设计工作中,有效促进到行业的发展。
1 CAE技术在塑料模具中的应用1.1 优化塑料产品设计利用CAD技术对产品的整体结构进行设计,然后利用CAE技术进行结构分析、可行性评价和优化设计,帮助设计人员改善产品的外形,设计合理的壁厚,选择具有最佳成型性能的材料,并设计出最优质的塑料制品,零件的形状能在电脑屏幕上逼真地显示出来,力学性能能通过有限元分析进行测试,塑料制品的壁厚和结构设计会直接的影响到了塑料制品的成型和产品质量。
如果产品设计师的经验完全依赖,成本性能非常高,产品是不合理的,CAE可以在外部载荷下分析产品的机械性能,预测负载下的应力,变形和温度,获得应力分布结构,并可以有效的优化到了产品的强度和刚度设计。
1.2 塑料模结构分析当前模具质量要求的提高和现代设计技术的不断发展,模具设计已经不能单靠设计完成。
应用现代设计方法分析设计的合理性,模具结构设计的合理性,合理分析不合理的结构和位置,在CAD软件中进行相应的修改,并利用CAE软件进行各种性能试验,最后,确定了满足性能和经济性要求的模具。
塑性成型中CAE的应用
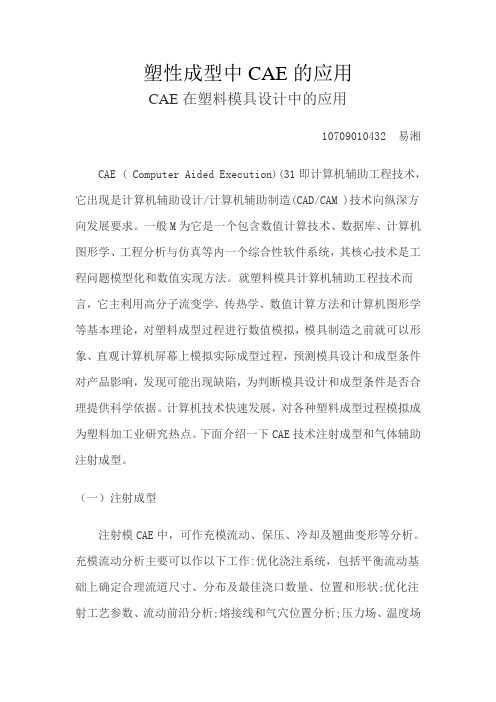
塑性成型中CAE的应用CAE在塑料模具设计中的应用10709010432 易湘CAE ( Computer Aided Execution)(31即计算机辅助工程技术,它出现是计算机辅助设计/计算机辅助制造(CAD/CAM )技术向纵深方向发展要求。
一般M为它是一个包含数值计算技术、数据库、计算机图形学、工程分析与仿真等内一个综合性软件系统,其核心技术是工程问题模型化和数值实现方法。
就塑料模具计算机辅助工程技术而言,它主利用高分子流变学、传热学、数值计算方法和计算机图形学等基本理论,对塑料成型过程进行数值模拟,模具制造之前就可以形象、直观计算机屏幕上模拟实际成型过程,预测模具设计和成型条件对产品影响,发现可能出现缺陷,为判断模具设计和成型条件是否合理提供科学依据。
计算机技术快速发展,对各种塑料成型过程模拟成为塑料加工业研究热点。
下面介绍一下CAE技术注射成型和气体辅助注射成型。
(一)注射成型注射模CAE中,可作充模流动、保压、冷却及翘曲变形等分析。
充模流动分析主要可以作以下工作:优化浇注系统,包括平衡流动基础上确定合理流道尺寸、分布及最佳浇口数量、位置和形状;优化注射工艺参数、流动前沿分析;熔接线和气穴位置分析;压力场、温度场和速度场分析。
保压过程是指到满意制品,充模结束时仍需较高保压压力作用下向型腔内继续注料,以弥补温度、压力变化造成体积收缩。
保压过程实质是补料,主要用于预测熔体型腔补料与压实过程压力场、温度场,计算体积收缩和型腔剪切应力及密度变化情况。
冷却过程中熔融塑料发生固化,固化过程中放出热量模具由冷却介质带走。
该过程中模具型腔温度高低及均匀性直接影响到注塑件生产效率和质量。
苌主要设计参数包括:冷却,管道尺寸、位置及各冷tp管道连接关系等几何参数和冷却介质流量、进口温度等物理参数。
一个好冷却系统应该使模具达到快速、均衡冷却,以减少冷却时间,提高成型效率,并减少或避免塑件翘曲变形、残余应力及表面质量缺陷等,提高产品质量。
- 1、下载文档前请自行甄别文档内容的完整性,平台不提供额外的编辑、内容补充、找答案等附加服务。
- 2、"仅部分预览"的文档,不可在线预览部分如存在完整性等问题,可反馈申请退款(可完整预览的文档不适用该条件!)。
- 3、如文档侵犯您的权益,请联系客服反馈,我们会尽快为您处理(人工客服工作时间:9:00-18:30)。
塑性成形中的CAE应用
——CAE 在汽车冲压件生产工艺中的优化应用
摘要:汽车冲压件在设计过程中采用快速冲压可行性分析,结合有限元软件和CAD 软件的造型功能,通过合理地分析、排样, 达到节省材料、降低生产成本的目的, 采用一步成形法有限元技术与增量有限元技术相结合的方法,分析设计出合理的工艺方案,并在生产实际中得到有效应用。
关键词:排样;冲压可行性;生成成本;CAE 技术
汽车是国民经济和现代生活中不可缺少的一种交通工具,汽车工业是一个国家工业化水平的代表性产业,它的兴衰成败又决定和影响着一大批工业产业的发展。
以CAD和CAE为代表的计算机技术的出现使汽车的设计过程和设计理念也有了革命性的变化。
钣金冲压件在卡车中总重量超过1/ 2 ,在轿车中达到3/ 4。
随着经济全球化和一体化的不断发展, 汽车制造企业之间的竞争日趋激烈, 汽车冲压件更新换代的步伐不断加快。
汽车冲压件设计制造中焦点问题是如何在保证质量的前提下达到成本最低; 同时进一步缩短冲压件的开发周期,也是汽车冲压件成为竞争取胜的决定因素。
随着计算机技术的不断发展, CAE(计算机辅助工程) 技术目前已经在各大汽车模具厂广泛用于产品模拟分析、冲压件成形过程分析。
通过提前对产品可能出现的成形缺陷进行研究, 预示汽车冲压件成形的可行性。
通过计算机数值模拟技术, 达到在设计阶段对冲压件质量进行预测, 控制成本, 提高产品工艺设计的合理性, 减少因为
设计的错误而造成返修。
应用于汽车冲压件分析的主流软件是增量求解软件, 由于增量求解软件在前处理阶段花费大量的时间,计算速度相对较长,它非常适合冲压工艺最后验证阶段使用。
一步成形技术可以在冲压件设计和早期工艺设计阶段发挥设置简单、求解速度快的优势,如果把一步成形法和增量求解法相结合,就能达到兼顾精度、提高效率的目的,目前这类方法在汽车工业界被广泛地采用。
2 降低成本措施及可行性分析
2. 1 降低成本
降低汽车冲压件生产制造成本包括降低材料成本、生产成本、人力成本等, 其中降低生产成本和降低人力成本的空间已经很小, 现在对于材料成本的控制显得更为迫切。
冲压件在最初设计阶段采用CAD 和CAE 相结合技术, 根据CAE 的成本计算结果,调整几何形状,使冲压件展开后的外轮廓面积最小, 结合FormingSuite 软件的Costoptimizer 优化软件包,对汽车冲压件的仿真工艺设计过程进行分析,通过降低材料等级、厚度和增大冲压件设计的圆角半径及修剪冲压件的边缘各项措施, 达到降低材料成本的目的。
2. 2 冲压可行性分析
在钣金冲压件和工艺设计阶段, 对于已有的冲压件, 并不能预先知道坯料的几何形状。
不同的冲压件形状和工艺条件会生成不同的坯料形状和尺寸。
采用不成熟的技术时, 会造成冲压件不合格甚至报废。
为了缩短设计过程和降低整个成本, 快速分析技术显得非常重要。
有限元方法提供一个工具, 能够把试验和不成熟的方法从昂贵的
现场搬到相对便宜的计算机模拟。
现结合拉延件产生起皱的状况, 通过快速冲压CAE 分析, 找到合理的拉延成形条件,加速冲压件开发进度。
2 冲压件成形工艺分析
2.1 冲压件产品特征分析
图1为一款液晶电视的底板,它
将要支撑20kg以上的整机重
量,四周通过螺丝孔固定橡胶
垫支撑底座,中心的圆盘为支
撑整机接触面,其上面装配旋
转立柱。
本文结合发散式的设计思想和钣金塑性成形原理,设计了此
款产品,其零件的机械性能、
整机的机械强度和稳定性得到
了很好的改善。
2.2 冲压件成形有限元模型
如图2所示为冲压件有限元模
型图,根据实际冲压成形工艺及材料拉伸试验得到相关参数,如表1
所示。
其中,模具间隙取0.1倍的壁
厚,即0.15mm,工件接触摩
擦系数取0.1。
2.3 经验法设计结果及对比分析
图3、图4分别为依据经验法
设计得到的试冲样件和有限
元仿真得到的成形极限图
-FLD。
从图3和图4对比分析,
产品破裂的区域和产品翘曲
的区域几乎是一致的,可以
得出仿真的结果和实际冲压
结果非常接近,换句话说,如
果能在设计之初引进有限元
仿真成形质量结果分析,就可
以大大提高设计开发的效率,
使得产品设计更科学、更高
效。
3.产品结构设计优化
根据图4结果分析,产品结构设计优化有以下几点:
(1)加大破裂区域的圆角。
(2)圆角采用变倒圆角的方式,拉伸高度高的地方增加圆角半径。
(3)降低顶面到底面过渡区域坡度,使拉伸深度一致,并均匀过渡。
(4)翘曲部分区域可通过压边加拉延筋等途径改善。
图4为优化设计后得到产品实际冲压结果,产品的成形质量较高,通过CAE分析辅助产品结构设计大大提高了产品设计开发的效率。
图
图4 结构设计优化后实冲零件
4 结束语
结合有限元软件,通过计算机模拟、分析冲压件的冲压可行性,
设计阶段利用各种降低成本的措施,达到了大大降低生产成本的目的, 分析结果指导制定合理的冲压工艺。
对于汽车零件, 若表面质量要求不高, 起皱部位无需严格控制; 若冲压件对表面质量要求较高时,则
可通过适当增大压边力、添加拉延筋等工艺措施消除起皱,满足控制
冲压件外观质量的要求。
以有限元法为基础的冲压成形过程中计算机仿真技术或数值模拟技术,为模具设计、冲压过程设计与工艺参数优
化提供了科学的新途径, 将是解决复杂冲压过程设计和模具设计的
最有效手段。
参考文献:
[ 1]胡世光,成鹤鸣. 板料冷冲压成形的工程解析. 北京:北京航空航天大学出
版社,2004.
[ 2]周军,马闯,钟志华. 基于计算机技术的薄板冲压成形毛坯形状和尺寸反算. 计算机仿真,2002(1) :86-89.
[ 3]吴诗. 冲压工艺学. 西安:西北工业大学出版社,1987.
[ 4]徐国艳,高峰,施法中. 面向对象的冲压成形一步法有限元分析系统研究和
开发. 高技术通讯,2004(9) :86-89。