轴承计算公式
滑动轴承间隙计算

滑动轴承间隙计算
滑动轴承的间隙计算方法可以根据轴承的类型和使用要求而有所不同。
以下是一种常见的间隙计算方法:
1. 确定滑动轴承类型:常见的滑动轴承类型有径向滑动轴承和推力滑动轴承。
根据具体的使用要求选择相应的轴承类型。
2. 确定负荷条件:根据实际应用中的负荷条件,包括径向负荷和推力负荷,确定轴承的工作负荷。
3. 计算轴承间隙:根据轴承的类型和工作负荷,使用滑动轴承间隙计算公式计算轴承的间隙。
- 对于径向滑动轴承,一般采用以下公式计算轴承间隙:间隙= ε × √(负荷/ (π × d × L × μ))
其中,ε为系数(一般为0.2-1.0),d为轴承内径,L为轴承长度,μ为润滑油的黏度。
- 对于推力滑动轴承,一般采用以下公式计算轴承间隙:间隙= ε × √(负荷/ (π × d × L × μ))
其中,ε为系数(一般为0.2-1.0),d为轴承内径,L为轴承长度,μ为润滑油的黏度。
4. 根据实际要求调整间隙:根据实际应用要求,对计算得到的间隙进行调整。
一般来说,间隙过小会导致润滑不良,间隙过大则会导致轴承的振动和松动。
需要注意的是,以上的计算方法只是一种常见的方法,实际应用中还需要考虑其他因素,如温度、工作速度等。
最好咨询专业的轴承制造商或工程师来进行具体的间隙计算。
角接触球轴承轴向力计算公式
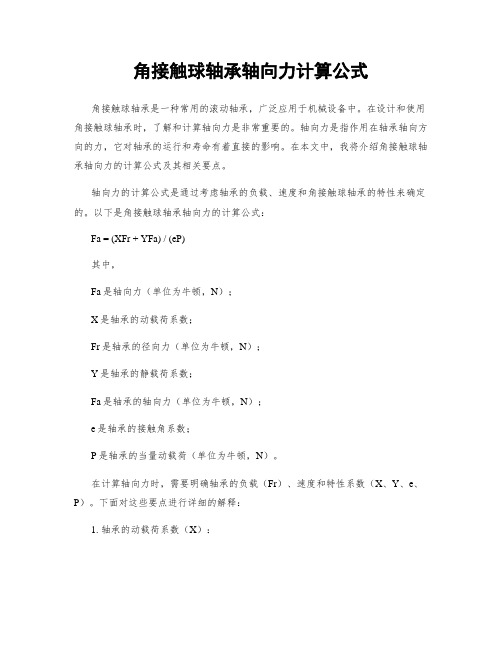
角接触球轴承轴向力计算公式角接触球轴承是一种常用的滚动轴承,广泛应用于机械设备中。
在设计和使用角接触球轴承时,了解和计算轴向力是非常重要的。
轴向力是指作用在轴承轴向方向的力,它对轴承的运行和寿命有着直接的影响。
在本文中,我将介绍角接触球轴承轴向力的计算公式及其相关要点。
轴向力的计算公式是通过考虑轴承的负载、速度和角接触球轴承的特性来确定的。
以下是角接触球轴承轴向力的计算公式:Fa = (XFr + YFa) / (eP)其中,Fa是轴向力(单位为牛顿,N);X是轴承的动载荷系数;Fr是轴承的径向力(单位为牛顿,N);Y是轴承的静载荷系数;Fa是轴承的轴向力(单位为牛顿,N);e是轴承的接触角系数;P是轴承的当量动载荷(单位为牛顿,N)。
在计算轴向力时,需要明确轴承的负载(Fr)、速度和特性系数(X、Y、e、P)。
下面对这些要点进行详细的解释:1. 轴承的动载荷系数(X):动载荷系数(X)是考虑到轴承在动载荷作用下的变形和变位情况的。
X的取值范围通常为0.56-0.98,具体取值需要根据轴承的类型、尺寸和应用情况进行确定。
2. 轴承的静载荷系数(Y):静载荷系数(Y)是考虑到轴承在静载荷作用下的变形和变位情况的。
Y的取值范围通常为0.56-0.98,具体取值需要根据轴承的类型、尺寸和应用情况进行确定。
3. 轴承的接触角系数(e):接触角系数(e)是轴承接触角的函数,接触角是指球和滚道的接触角度。
e的取值范围通常为0.6-0.8,具体取值需要根据轴承的类型和设计要求进行确定。
4. 轴承的当量动载荷(P):当量动载荷(P)是指在轴承承受的径向力和轴向力同时作用下,所能承受的相当于纯径向载荷的动载荷。
P的计算公式通常为P = Fr + 1.2Fa,其中Fr为径向力,Fa为轴向力。
轴向力的计算公式的目的是为了确定角接触球轴承在实际工作中所承受的轴向力,以便进行轴承的选择和设计。
通过合理的计算和选择,可以保证轴承在工作过程中的可靠性和寿命。
轴承的计算公式.
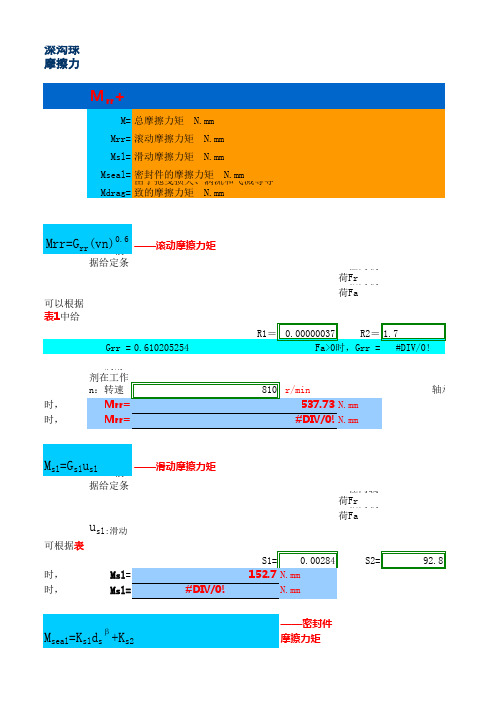
NR=
242.19713 W
Fa=0时
NR=
如果冷却系数(指轴承与环境温度之间每一度温差所带走的热量)是已知数,则可用以下公式粗略估算轴
∆T=N_R/W_s
∆T:温升 ℃
N_R:功率损耗 W
W_S:冷却系数
20
Δ T=
12.10986 ℃ Fa=0时
Δ T=
管方向,只取正值
10000 N 0N
117.5 mm
深沟球摩擦力矩的准确计算,要考虑四个不同导致摩擦的因素:
M=Mrr+Msl+Mseal+Mdrag
M= 总摩擦力矩 N.mm Mrr= 滚动摩擦力矩 N.mm Msl= 滑动摩擦力矩 N.mm Mseal= 密封件的摩擦力矩 N.mm Mdrag= 由于拖曳损失、涡流和飞溅等导致的摩擦力矩 N.mm
轴承额定动载荷C0=
100 mm2/s 76500 N
10000 N 0N
油);0.1(以传动液润滑)
摩擦系数Usl:
0.04
2.25 2
0.00017
1
列球轴承常数:
3.1
75
160
滚动摩擦的切入发热和贫油回填效应的
.28 v^0.64 )
油回填常数,脂润滑为: 0.00000006
2847.70 N.mm #DIV/0! N.mm
轴向载荷Fa
usl:滑动摩擦系数,当润滑条件良好,可取以下值:0.05(矿物油);0.04(合成油);0.1(以传动液润滑)
Gsl的值可根据表1中给出的公式计算,几何常数S则可从表2中找到
当Fa=0时, Msl=
S1= 0.00284
S2=
152.7 N.mm
轴承的计算公式
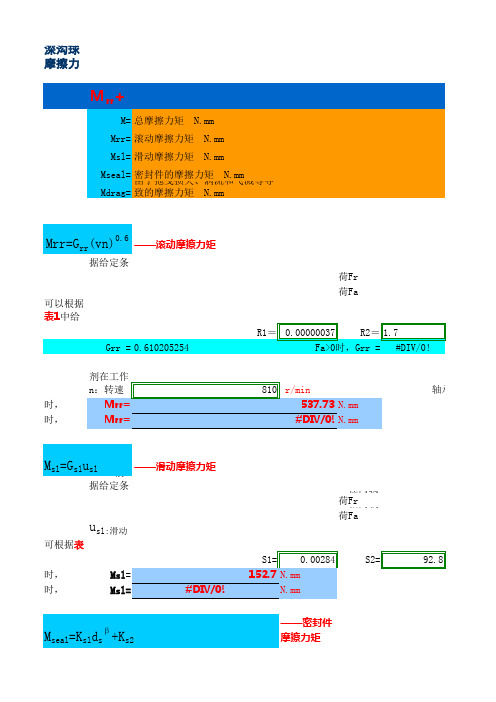
M= Mrr+
M= 总摩擦力矩 N.mm
Mrr= 滚动摩擦力矩 N.mm
Msl= 滑动摩擦力矩 N.mm
Mseal= 密由封于件拖的曳摩损擦失力、矩 涡流和N.飞mm溅等导 Mdrag= 致的摩擦力矩 N.mm
Mrr=Grr(Grvrn:)根0.6 ——滚动摩擦力矩
据给定条
Grr的值 可以根据 表1中给
10000 N 0N
摩擦系数Usl:
0.04
2.25 2
0.00017
1 3.1
75 160
滚动摩擦的切入发热和贫油回填效应的
.28 v^0.64 )
0.00000006
2847.70 N.mm #DIV/0! N.mm
Fa=0时 Fa>0时
W Fa〉0
#DIV/0! 时
111
#DIV/0!
℃ Fa〉0 时
21.41 N.mm
iKzr=w=单球列
和d=双轴列承球 内D=径轴尺承 外径尺
在新的摩擦模型中引入了减少系数 和 ,分别用来考虑滚动摩擦的切入发
切影入响发:热
∅_ish ∅_rs
减少系
数:——
∅_ish=1/(1+1.84×〖10〗^(-9) 〖(n d_m )〗^1.28 v^0.64 )
0.923646
贫油回填 减少系 数:——
∅_rs=1/(e^(K_rs vn(d+D)) √(K_z/(2(D-d))))
3.663692474
贫油回填常
Krs= 数,脂润滑
将以上的 其它效应
=
功率 损M耗=∅_ish ∅_rs
因轴承的 摩擦而造
如果冷却 系数(指
轴承游隙计算

轴承游隙的计算公式:(1): 配合的影响1、轴承内圈与钢质实心轴:△j = △dy * d/h2、轴承内圈与钢质空心轴:△j = △dy * F(d)F(d) = d/h * [(d/d1)2 -1]/[(d/d1)2 - (d/h)2]3、轴承外圈与钢质实体外壳:△A = △Dy * H/D4、轴承外圈与钢质薄壁外壳:△A = △Dy * F(D)F(D) = H/D * [(F/D)2 - 1]/[(F/D)2 - (H/D)2]5、轴承外圈与灰铸铁外壳:△A = △Dy * [F(D) –0.15 ]6、轴承外圈与轻金属外壳:△A = △Dy * [F(D) –0.25 ]注:△j -- 内圈滚道挡边直径的扩张量(um)。
△dy —轴颈有效过盈量(um)。
d -- 轴承内径公称尺寸(mm)。
h -- 内圈滚道挡边直径(mm)。
B -- 轴承宽度(mm)。
d1 -- 空心轴内径(mm)。
△A -- 外圈滚道挡边直径的收缩量(mm)。
△Dy -- 外壳孔直径实际有效过盈量(um)。
H -- 外圈滚道挡边直径(mm)。
D -- 轴承外圈和外壳孔的公称直径(mm)。
F -- 轴承座外壳外径(mm)。
(2): 温度的影响△T = Гb * [De * ( T0 – Ta ) – di * ( Ti – Ta)] 其中Гb 为线膨胀系数,轴承钢为11.7 *10-6 mm/mm/ 0CDe 为轴承外圈滚道直径,di 为轴承内圈滚道直径。
Ta 为环境温度。
T0 为轴承外圈温度,Ti 轴承内圈温度。
四、轴向游隙与径向游隙的关系:Ua = [4(fe + fi – 1) * Dw * Ur – Ur2 ] 1/2因径向游隙Ur很小、故Ur2 很小,忽略不记。
故 Ua = 2 * [(fe + fi –1) * Dw * Ur ] 1/2其中 fe 为外圈沟曲率系数,fi 为内圈沟曲率系数,Dw 为钢球直径。
轴承设计寿命计算公式汇总
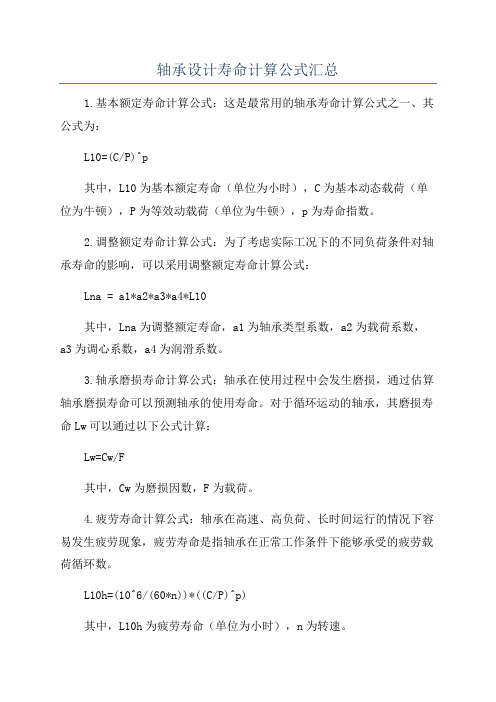
轴承设计寿命计算公式汇总
1.基本额定寿命计算公式:这是最常用的轴承寿命计算公式之一、其公式为:
L10=(C/P)^p
其中,L10为基本额定寿命(单位为小时),C为基本动态载荷(单位为牛顿),P为等效动载荷(单位为牛顿),p为寿命指数。
2.调整额定寿命计算公式:为了考虑实际工况下的不同负荷条件对轴承寿命的影响,可以采用调整额定寿命计算公式:
Lna = a1*a2*a3*a4*L10
其中,Lna为调整额定寿命,a1为轴承类型系数,a2为载荷系数,a3为调心系数,a4为润滑系数。
3.轴承磨损寿命计算公式:轴承在使用过程中会发生磨损,通过估算轴承磨损寿命可以预测轴承的使用寿命。
对于循环运动的轴承,其磨损寿命Lw可以通过以下公式计算:
Lw=Cw/F
其中,Cw为磨损因数,F为载荷。
4.疲劳寿命计算公式:轴承在高速、高负荷、长时间运行的情况下容易发生疲劳现象,疲劳寿命是指轴承在正常工作条件下能够承受的疲劳载荷循环数。
L10h=(10^6/(60*n))*((C/P)^p)
其中,L10h为疲劳寿命(单位为小时),n为转速。
5.温度因子计算公式:轴承在工作时会产生热量,可以通过计算温度因子来估算轴承的使用寿命。
温度因子aISO可以通过以下公式计算:aISO=a*〖10(ΔT/10)〗^b
其中,a、b为轴承类型参数,ΔT为温度变化。
以上是一些常用的轴承设计寿命计算公式汇总。
需要注意的是,不同类型的轴承有不同的设计寿命计算公式,具体应根据实际情况选择合适的计算方法。
此外,在进行寿命计算时还需要考虑轴承材料、润滑方式、工作温度等因素对轴承寿命的影响。
轴承轴向载荷计算公式

轴承轴向载荷计算公式
轴承是一种用于支撑机械旋转部件的重要元件。
在实际应用中,轴承通常承受着来自旋转部件的各种载荷,其中包括轴向载荷。
轴向载荷是指垂直于轴心线方向的力或压力,其作用方向与轴的轴向相同或相反。
轴向载荷的计算对于正确选择合适的轴承和确保轴承工作正常非常重要。
以下是常用的轴向载荷计算公式:
1. 线性轴承的轴向载荷计算公式:
轴向载荷 = 1/2 * (F1 + F2)
其中,F1和F2分别为轴承所受外力的大小,取正负号表示方向。
2. 圆柱滚子轴承的轴向载荷计算公式:
轴向载荷 = (F1 + F2) / 2
其中,F1和F2分别为轴承所受外力的大小,取正负号表示方向。
3. 锥形滚子轴承的轴向载荷计算公式:
轴向载荷= (F1 + F2) / 2 * cosα
其中,F1和F2分别为轴承所受外力的大小,取正负号表示方向;α为锥面与轴线的夹角。
4. 推力球轴承的轴向载荷计算公式:
轴向载荷 = F
其中,F为轴承所受外力的大小,取正负号表示方向。
需要注意的是,在实际应用中,轴向载荷不仅仅是由外力引起的,还可能由于转子离心力、温度变化等因素而产生。
因此,需要综合考虑这些因素对轴向载荷的影响,进行准确的计算。
在进行轴向载荷计算时,还需要考虑其他一些因素,如轴承的额定载荷、轴承的径向载荷等。
同时,还要根据具体的工况条件和设计要求,选择合适的轴承类型和规格。
轴向载荷的计算是轴承设计中非常重要的一部分。
通过合理计算和选择,可以确保轴承工作正常,并提高设备的安全性和可靠性。
轴承设计寿命计算公式
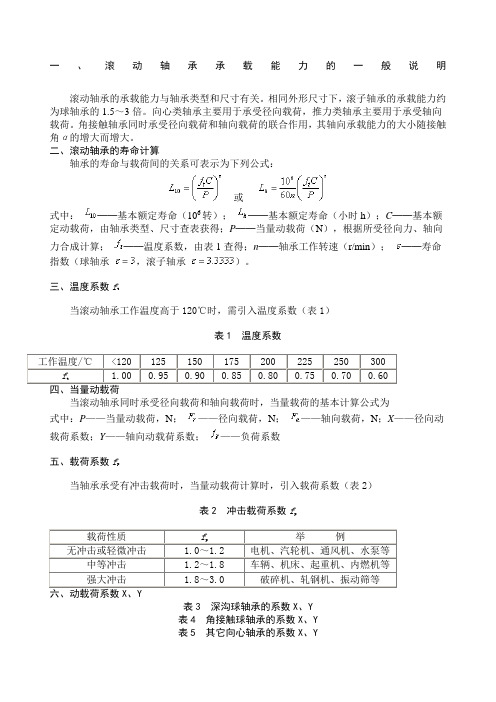
一、滚动轴承承载能力的一般说明滚动轴承的承载能力与轴承类型和尺寸有关。
相同外形尺寸下,滚子轴承的承载能力约为球轴承的1.5~3倍。
向心类轴承主要用于承受径向载荷,推力类轴承主要用于承受轴向载荷。
角接触轴承同时承受径向载荷和轴向载荷的联合作用,其轴向承载能力的大小随接触角α的增大而增大。
二、滚动轴承的寿命计算轴承的寿命与载荷间的关系可表示为下列公式:或式中:──基本额定寿命(106转);──基本额定寿命(小时h);C──基本额定动载荷,由轴承类型、尺寸查表获得;P──当量动载荷(N),根据所受径向力、轴向力合成计算;──温度系数,由表1查得;n──轴承工作转速(r/min);──寿命指数(球轴承,滚子轴承)。
三、温度系数f t当滚动轴承工作温度高于120℃时,需引入温度系数(表1)表1 温度系数工作温度/℃<120 125 150 175 200 225 250 300 f1.00 0.95 0.90 0.85 0.80 0.75 0.70 0.60t四、当量动载荷当滚动轴承同时承受径向载荷和轴向载荷时,当量载荷的基本计算公式为式中:P——当量动载荷,N;——径向载荷,N;——轴向载荷,N;X——径向动载荷系数;Y——轴向动载荷系数;——负荷系数五、载荷系数f p当轴承承受有冲击载荷时,当量动载荷计算时,引入载荷系数(表2)表2 冲击载荷系数f p载荷性质f p举例无冲击或轻微冲击 1.0~1.2 电机、汽轮机、通风机、水泵等中等冲击 1.2~1.8 车辆、机床、起重机、内燃机等强大冲击 1.8~3.0 破碎机、轧钢机、振动筛等表3 深沟球轴承的系数X、Y表4 角接触球轴承的系数X、Y表5 其它向心轴承的系数X、Y表6 推力轴承的系数X、Y七、成对轴承所受轴向力计算公式:角接触球轴承:圆锥滚子轴承:式中e为判断系数,可由表4查出;Y应取表5中的数值。
●正排列:若则???若?则●反排列:若则若??? ?则八、成对轴承当量动载荷根据基本公式:式中:P——当量动载荷,N;——径向载荷,N;——轴向载荷,N;X——径向动载荷系数;Y——轴向动载荷系数;——负荷系数。
- 1、下载文档前请自行甄别文档内容的完整性,平台不提供额外的编辑、内容补充、找答案等附加服务。
- 2、"仅部分预览"的文档,不可在线预览部分如存在完整性等问题,可反馈申请退款(可完整预览的文档不适用该条件!)。
- 3、如文档侵犯您的权益,请联系客服反馈,我们会尽快为您处理(人工客服工作时间:9:00-18:30)。
轴承毛坯锻造模具计算公式
一外圈;
外圈;套切冲头¢=【芯料重量/7.85/3.14/(锻件高+压平量)】开根号×2
成型压边器孔¢=冲头¢+2
凹模H=锻件高+压平量-3
凹模¢1=【下料重量/7.85/3.14/(锻件高+压平量)】开根号×2
减去
Ta n凹模°×(锻件高+压平量)×1.0125
凹模¢2=tan凹模°×H×2+¢1
凹模°=锻件度数+1.5°左右
二内圈;
内圈;挤压冲头¢=【眼子铁重量/7.85/3.14/厚度】开根号×2
凹模大档边¢1=【(圈大档边¢/2)平方+(冲头¢/2)平方-(圈内径¢/2)平方】开根号×2×1.0125
凹模小内孔¢3=【(圈小档边¢/2)平方+(冲头¢/2)平方-(圈内径¢/2)平方】开根号×2×1.0125
凹模度数=圈度数+30′
凹模滚道高度=圈高×1.0125-大档边高度+0.5-小档边-0.5
凹模滚道¢2=tan凹模度数×凹模滚道高度×2+凹模小孔¢3
凹模h=圈大档边高度+0.5-3。