我国铝土矿资源特点及溶出技术发展趋势
铝土矿溶出技术装备大型化发展现状和趋势分析

1
C 封面报道 over Report
出 NEUI600 ~ 1000kt/a 管道化加停留罐溶出技术 [2]。 随着 NEUI 大型管道化加停留罐溶出技术的持续开发,为进
一步优化氧化铝厂核心技术,NEUI 相继开发出 600 ~ 1000kt/a 全管道化溶出技术及装备,2014 年,NEUI800kt/a 在山西复晟铝 业率先投入产业化应用,成功完成了氧化铝大型化核心技术的 再创新 [3-5] ;
关键词 :拜耳法 ;一水硬铝石型铝土矿 ;溶出 ;大型化装备 ;节能降耗
中图分类号 :TQ133.1
文献标识码 :A
文章编号 :11-5004(2019)02-0001-3
拜耳法是处理铝土矿流程简单、作业方便、产品质量高的一 种氧化铝生产工艺,目前世界上 95% 以上的氧化铝企业均采用 拜耳法工艺处理铝土矿。拜耳法生产工艺的核心是铝土矿矿浆 的溶出工序,其目的是使铝土矿和循环母液在一定温度下反应, 生成铝酸钠溶液,反应式为 :
C 封面报道 over Report
铝土矿溶出技术装备大型化发展现状和趋势分析
许文强,董 菲,王 宁
(东北大学设计研究院(有限公司)介绍了铝土矿溶出技术和装备的发展历程和主要现状,同时在分析影响一水硬铝石铝土矿溶出的因素及技术
进步的基础上,重点论述了一水硬铝石的传统压煮溶出技术装备、大型管道化加停留罐溶出技术装备和全管道化溶出技术装备,
2023年铝土矿行业发展概况分析及未来五年行业数据趋势预测
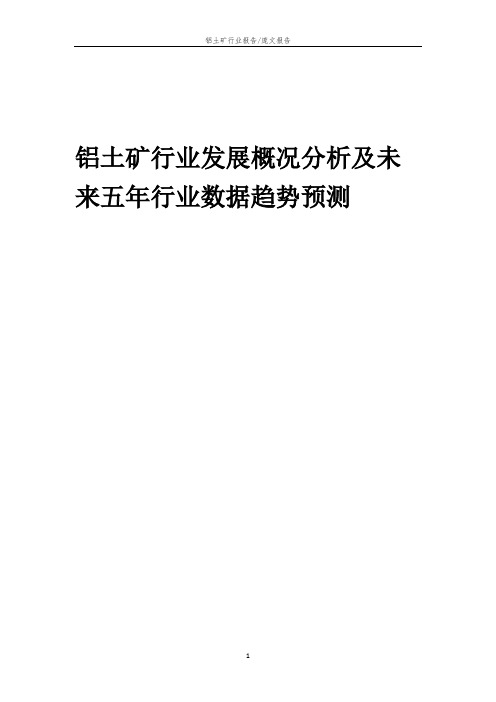
铝土矿行业发展概况分析及未来五年行业数据趋势预测目录申明 (4)一、铝土矿企业战略选择 (4)(一)、铝土矿行业SWOT分析 (4)(二)、铝土矿企业战略确定 (5)(三)、铝土矿行业PEST分析 (5)1、政策因素 (5)2、经济因素 (6)3、社会因素 (7)4、技术因素 (7)二、铝土矿行业发展状况及市场分析 (7)(一)、中国铝土矿市场行业驱动因素分析 (7)(二)、铝土矿行业结构分析 (8)(三)、铝土矿行业各因素(PEST)分析 (9)1、政策因素 (9)2、经济因素 (10)3、社会因素 (10)4、技术因素 (11)(四)、铝土矿行业市场规模分析 (11)(五)、铝土矿行业特征分析 (11)(六)、铝土矿行业相关政策体系不健全 (12)三、铝土矿行业(2023-2028)发展趋势预测 (13)(一)、铝土矿行业当下面临的机会和挑战 (13)(二)、铝土矿行业经营理念快速转变的意义 (13)(三)、整合铝土矿行业的技术服务 (14)(四)、迅速转变铝土矿企业的增长动力 (14)四、铝土矿业数据预测与分析 (15)(一)、铝土矿业时间序列预测与分析 (15)(二)、铝土矿业时间曲线预测模型分析 (16)(三)、铝土矿行业差分方程预测模型分析 (17)(四)、未来5-10年铝土矿业预测结论 (17)五、铝土矿业发展模式分析 (18)(一)、铝土矿地域有明显差异 (18)六、铝土矿企业战略实施要点 (18)(一)、打造自主品牌 (18)(二)、重塑企业价值链 (19)1、规范研发设计流程 (19)2、优化生产制造 (19)(三)、重视市场营销 (20)(四)、整合线上线下平台 (22)(五)、宏观环境下铝土矿行业的定位 (22)(六)、铝土矿行业发展趋势 (22)七、铝土矿行业竞争分析 (23)(一)、铝土矿行业国内外对比分析 (23)(二)、中国铝土矿行业品牌竞争格局分析 (24)(三)、中国铝土矿行业竞争强度分析 (25)1、中国铝土矿行业现有企业的竞争 (25)2、中国铝土矿行业上游议价能力分析 (25)3、中国铝土矿行业下游议价能力分析 (25)4、中国铝土矿行业新进入者威胁分析 (26)5、中国铝土矿行业替代品威胁分析 (26)八、铝土矿行业风险控制解析 (26)(一)、铝土矿行业系统风险分析 (26)(二)、铝土矿业第二产业的经营风险 (26)九、关于未来5-10年铝土矿业发展机遇与挑战的建议 (27)(一)、2023-2028年铝土矿业发展趋势展望 (27)(二)、2023-2028年铝土矿业宏观政策指导的机遇 (27)(三)、2023-2028年铝土矿业产业结构调整的机遇 (27)(四)、2023-2028年铝土矿业面临的挑战与对策 (28)十、未来铝土矿企业发展的战略保障措施 (29)(一)、根据公司发展阶段及时调整组织结构 (29)(二)、加强人才培养和引进 (30)1、制定总体人才引进计划 (30)2、渠道人才引进 (31)3、内部员工竞聘 (31)(三)、加速信息化建设步伐 (31)申明中国的铝土矿业在当前复杂的商业环境下逐步发展,呈现出一个积极整合资源以提高粘连性的耐寒时代。
2024年铝矿市场规模分析
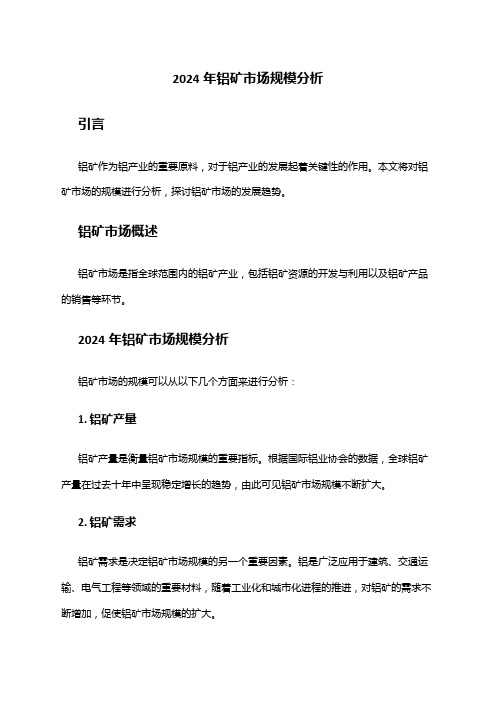
2024年铝矿市场规模分析引言铝矿作为铝产业的重要原料,对于铝产业的发展起着关键性的作用。
本文将对铝矿市场的规模进行分析,探讨铝矿市场的发展趋势。
铝矿市场概述铝矿市场是指全球范围内的铝矿产业,包括铝矿资源的开发与利用以及铝矿产品的销售等环节。
2024年铝矿市场规模分析铝矿市场的规模可以从以下几个方面来进行分析:1. 铝矿产量铝矿产量是衡量铝矿市场规模的重要指标。
根据国际铝业协会的数据,全球铝矿产量在过去十年中呈现稳定增长的趋势,由此可见铝矿市场规模不断扩大。
2. 铝矿需求铝矿需求是决定铝矿市场规模的另一个重要因素。
铝是广泛应用于建筑、交通运输、电气工程等领域的重要材料,随着工业化和城市化进程的推进,对铝矿的需求不断增加,促使铝矿市场规模的扩大。
3. 铝矿价格铝矿价格是影响铝矿市场规模的重要因素之一。
铝矿价格的上涨会吸引更多的企业投资于铝矿开发领域,从而推动铝矿市场的发展。
4. 铝矿市场竞争格局铝矿市场的竞争格局也会对市场规模产生影响。
目前,全球范围内铝矿市场呈现出供需失衡的情况,少数大型铝矿企业垄断了市场,这种竞争格局限制了市场规模的扩大。
铝矿市场的发展趋势铝矿市场在未来有以下几个发展趋势值得关注:1. 铝矿资源的开发和利用技术不断提升随着科技进步和环保意识的增强,铝矿资源的开采技术将得到改进,对环境的影响将减少,从而推动铝矿市场规模的扩大。
2. 新兴市场的需求增长在发展中国家经济快速增长的背景下,对铝矿的需求将不断增加,这将为铝矿市场的发展提供新的机遇。
3. 产业结构调整随着全球化进程的推进,铝矿市场将面临着产业结构调整的挑战和机遇,需要加强合作,加大创新力度,推动铝矿市场规模的进一步扩大。
结论综上所述,铝矿市场作为铝产业的重要组成部分,其规模在全球范围内呈现扩大的趋势。
未来,铝矿市场将面临着技术进步、市场需求增长和产业结构调整等挑战和机遇。
为了确保铝矿市场的健康发展,相关企业和政府应加强合作,加大投入,共同推动铝矿市场规模的扩大。
铝土矿行业现状分析报告

供应地区分布
澳大利亚将继续是全球最 大的铝土矿供应国,中国 和印度尼西亚也将保持重 要地位。
供应结构变化
低品位、高杂质铝土矿的 供应将逐渐减少,高品位 、低杂质铝土矿的供应将 增加。
铝土矿行业技术发展趋势
采矿技术
采矿技术将不断进步,提高采矿 效率和安全性,降低采矿成本。
选矿技术
选矿技术将向高效、环保、节能方 向发展,提高铝土矿的选矿回收率 和产品质量。
价格波动
铝土矿市场价格受多种因素影响,如供求关系、 政策变化、国际政治经济形势等,价格波动较大 。
需求变化
铝土矿主要应用于氧化铝、电解铝等行业,需求 受国内外经济形势、政策调整等因素影响,需争日趋激烈,企 业面临市场份额下降、盈利能力减弱等风险。
铝土矿的密度通常在2.4到2.7 克/立方厘米之间,具有较高的 熔点和良好的耐腐蚀性。
铝土矿的用途与价值
铝土矿是生产铝的主要原料,通 过电解铝过程可以得到纯度较高
的铝。
铝是一种广泛应用于航空、建筑 、汽车、包装等领域的重要金属 材料,对国家经济发展具有重要
意义。
随着全球经济的快速发展,铝土 矿的需求量逐年增加,市场前景
地企业合作等方式,提高自身在全球市场的地位。
环保与安全标准成为重要考量因素
03
在兼并与收购过程中,环保与安全标准成为双方考量的重要因
素,对交易的成功与否产生影响。
05
行业政策与法规
国际铝土矿政策与法规
国际铝土矿政策
国际上对铝土矿资源的开发利用有着严格的政策规定。这些 政策主要涉及资源保护、开采许可、环境保护、税收等方面 ,目的是确保铝土矿资源的可持续利用和生态环境的保护。
冶炼技术
冶炼技术将向高效、环保、节能方 向发展,提高铝土矿的冶炼效率和 产品质量。
2023年铝土矿行业市场调研报告

2023年铝土矿行业市场调研报告铝土矿是指以铝矾土、高岭土、膨润土等为主要成分的矿石,是重要的非金属矿产资源之一。
在现代工业生产中,铝土矿是制取铝、陶瓷、建筑材料、造纸、化学品等的重要原材料。
本文主要对铝土矿行业市场进行调研和分析。
一、行业概况铝土矿产业主要有三个环节:采矿、选矿和加工。
中国的铝土矿主要分布在江西、贵州、广东和云南等地,其中江西占全国铝土矿总储量的60%以上。
铝土矿矿山数量多,小规模分散,生产能力相对较弱,而且采用落后的采选技术,导致资源浪费和环境污染严重。
二、市场需求铝土矿是重要的铝工业原材料,随着全球铝工业的不断发展,铝土矿的市场需求也在逐年增长。
中国作为世界主要的铝生产国,铝土矿的市场需求也非常旺盛。
另外,建筑材料、陶瓷、造纸、化学品等行业也对铝土矿有着很高的需求。
三、市场价格铝土矿的市场价格受到多种因素的影响,其中最主要的是铝土矿矿山的生产能力和采矿成本。
目前,铝土矿市场价格相对稳定,但由于资源的分散和采选技术的滞后,导致成本较高,影响市场竞争力。
四、市场竞争目前,中国铝土矿行业市场较为分散,主要企业包括中铝、明义铝业、江西铝业、白云山等。
这些企业在发展过程中积极引进国际先进技术和管理经验,提高产品品质和降低生产成本,取得了一定的市场份额。
但整体来看,中国铝土矿行业在技术、管理和品质等方面还有很大的提升空间。
五、发展趋势未来,中国铝土矿行业将面临良好的发展机遇。
随着国家环保政策的不断加强和矿产资源的日益枯竭,铝土矿行业将迎来新的发展机遇,发展方向主要包括以下几个方面:1. 引进先进技术和管理经验,提高产品品质和生产效率。
2. 提高铝土矿的回收利用率,减少资源浪费和环境污染。
3. 积极拓展多元化市场,如向新兴市场、高端市场等倾斜。
4. 加强产学研合作,实现科技创新和创新能力的提升。
总之,铝土矿行业市场前景广阔,但也面临着很多挑战,需要进一步完善管理和采选技术,提高产品品质和生产效率。
铝土矿行业分析报告

铝土矿行业分析报告铝土矿是指含有铝的矿物和土状物质。
铝土矿是一种重要的非金属矿物资源,其主要用途是制造铝及其合金、耐火材料和水泥等。
铝土矿产业是一种高附加值和高技术含量的产业,具有广泛的市场前景和经济价值。
本文将对铝土矿行业进行深入分析,并对其未来发展趋势和前景进行预测。
定义铝土矿是指含有铝的矿物和土状物质,是铝的主要原材料之一。
铝土矿分为高氧化铝矾土、膨润土和堆积灰土三种类型。
高氧化铝矾土主要用于制造铝及其合金,膨润土主要用于制造耐火材料,堆积灰土主要用于制造水泥。
分类特点铝土矿根据含铝量的不同,可以分为高铝矾土、混合铝矾土、低氧化铝矾土三类。
其中,高铝矾土铝含量较高,适用于铝的冶炼。
混合铝矾土铝硅比较低,远远达不到铝的冶炼要求,但可以用于制造水泥等。
低氧化铝矾土铝含量较低,主要用于制造耐火材料。
产业链铝土矿产业链主要包括矿山开采、选矿、冶炼、加工和销售等环节。
矿山开采包括地质勘查、开发和采矿,选矿包括铝土矿的分类、测定和分离;冶炼包括炼铝和其他铝合金产品的制造;加工包括铝制品的加工和铝合金的成型加工;销售包括铝土矿、铝锭和其他铝制品的销售。
发展历程20世纪80年代,中国铝土矿产业处于起步阶段。
当时国内铝土矿储量已经是全球第一,但是生产技术十分落后,生产能力低下,且无法满足铝工业的需求。
随着改革开放的逐渐深入,铝土矿产业得到了快速的发展。
经过不断的技术创新和产业链的延伸,铝土矿产业的生产能力得到了大幅提升,产业规模逐渐扩大。
近年来,中国的铝土矿开采技术和铝制品加工技术也逐步成熟,产业链板块化趋势明显。
行业政策文件及其主要内容我国铝土矿行业政策文件主要有《铝工业发展规划》、《非金属矿物资源保护与综合利用规划》等。
其中,《铝工业发展规划》提出到2020年,我国整个铝工业乃至铝土矿行业要实现三个目标:一是铝土矿年采矿能力达到4000万吨,二是铝的年产量达到500万吨,三是全球的铝工业原铝和铝制品市场份额均达到20%以上。
我国铝土矿选矿发展现状

我国铝土矿选矿发展现状1.引言1.1 概述我国铝土矿是一种重要的非金属矿产资源,广泛应用于铝冶炼、建筑材料、化工等行业。
近年来,在我国经济持续快速发展的背景下,铝土矿选矿工业也取得了显著的进展。
在我国,铝土矿选矿主要是通过将矿石进行粉碎、磨矿、矿浆浸出、浮选等工艺步骤,从而分离出铝的有效成分。
选矿过程中的各个环节都需要高效的工艺设备和先进的技术手段来保证矿石的高效处理。
目前,我国铝土矿选矿发展取得了一定的成就。
在选矿工艺上,采用了一系列先进技术,包括湿式粉碎和干式粉碎工艺、湿式和干式矿浆浸出工艺、浮选工艺等。
这些技术的引入和应用使得选矿效率得到了显著提高,矿石中的有用成分得以更好地被分离和提取出来。
此外,我国在选矿设备的生产和研发方面也取得了重要的突破。
各种高效、智能化的选矿设备不断涌现,并逐渐取代了传统的选矿设备,提高了选矿生产线的自动化程度和生产效率。
然而,与发达国家相比,我国铝土矿选矿产业仍存在一些问题和不足之处。
首先,选矿工艺仍需要进一步进行改进和创新,以提高选矿效率和降低生产成本。
其次,选矿设备的性能和质量还有待提高,特别是在环保、节能方面的需求上,还存在一定的差距。
进一步推动我国铝土矿选矿发展需要多方共同努力。
政府应加大对选矿技术研发和设备生产的支持力度,鼓励企业增加研发投入,加强国际合作与交流。
同时,选矿企业也要积极引进和吸收国内外先进技术和管理经验,不断提升自身的创新能力和竞争力。
总之,我国铝土矿选矿发展现状已经取得了一定的成就,但与发达国家相比仍存在一定差距。
只有通过加强技术创新、提升设备质量和完善管理,我国铝土矿选矿业才能实现更加可持续的发展。
1.2 文章结构文章结构部分的内容可以描述本文的整体框架和各个章节的内容概要。
具体地,可以对文章的各个章节进行简要介绍,以便读者了解整篇文章的组织结构和内容安排。
以下是针对本文的文章结构部分的一种可能的编写方式:文章结构:本文分为引言、正文和结论三个部分。
2024年铝土矿市场分析现状

2024年铝土矿市场分析现状1. 引言铝土矿是一种重要的铝原料,广泛应用于铝冶炼、建筑材料、航空航天、汽车制造等行业。
铝土矿市场受到全球经济发展、政策环境和供需关系等因素的影响。
本文将对铝土矿市场的现状进行分析,以期为相关行业提供决策参考。
2. 全球铝土矿资源储量及分布情况铝土矿是铝的重要原料之一,其资源储量和分布情况对全球铝工业具有重要意义。
根据研究数据,在全球范围内,主要的铝土矿资源储量集中在澳大利亚、巴西、中国和印度等国家。
其中,澳大利亚的铝土矿资源储量最为丰富,占全球总储量的34%。
3. 全球铝土矿市场供需关系铝土矿的市场供需关系对全球铝工业的发展具有重要意义。
目前,全球铝土矿市场供需情况总体平衡,但供需关系存在一定的波动。
随着全球经济的不断发展,对铝土矿的需求呈现出增长趋势。
同时,铝土矿产能的不断提升也推动了市场供给的增加。
4. 铝土矿市场价格波动分析铝土矿市场价格的波动对相关行业的生产成本和利润率具有重要影响。
铝土矿的价格波动主要受到供需关系、宏观经济因素和政策环境等影响。
近年来,铝土矿价格呈现出波动上升的趋势。
这一波动主要受到中国等国家的铝工业发展和市场需求的增加影响。
5. 铝土矿市场的发展趋势随着全球经济的快速发展和工业化进程的推进,铝土矿市场将继续保持良好的发展态势。
未来,铝土矿市场的发展趋势主要包括以下几个方面:•需求增长:铝土矿作为铝工业的重要原料,其需求将随着相关行业的发展持续增加。
•国际竞争格局:由于铝土矿资源的垄断性质,全球铝土矿市场将呈现出一定的竞争格局。
•技术创新:随着科技进步和绿色环保意识的提高,铝土矿的提取和利用技术将得到进一步创新和改进。
6. 结论综上所述,铝土矿市场处于供需平衡状态,价格波动较为明显。
随着全球经济的发展和工业化程度的提高,铝土矿市场将继续保持良好的发展趋势。
各相关行业应关注市场供需关系的变化,并加强技术创新,以适应市场发展的需求。
- 1、下载文档前请自行甄别文档内容的完整性,平台不提供额外的编辑、内容补充、找答案等附加服务。
- 2、"仅部分预览"的文档,不可在线预览部分如存在完整性等问题,可反馈申请退款(可完整预览的文档不适用该条件!)。
- 3、如文档侵犯您的权益,请联系客服反馈,我们会尽快为您处理(人工客服工作时间:9:00-18:30)。
我国铝土矿资源特点及溶出技术发展趋势王一雍、张廷安、陈霞、王艳利(东北大学材料与冶金学院沈阳 110004 )摘要:我国铝土矿多为一水硬铝石矿,资源丰富,且高硅高铝,但铝硅比低,氧化铝溶出性能差,碱耗、能耗高,生产成本高。
我国现行的氧化铝生产方法已愈益不适应目前的资源状况及日益竞争的国际环境。
本文对不同的强化溶出方法进行了技术上的分析,并针对我国一水硬铝石矿的特点,重点阐明了采用后加矿增溶溶出技术、微波加热技术、生物浸出技术进行强化溶出的优势所在及技术上的可行性了。
关键词:铝土矿;一水硬铝石;强化溶出;增溶溶出技术1.我国铝土矿资源特点及存在的问题我国铝土矿资源储量丰富,截止到2001年底,我国铝土矿储量5.06亿t,基础储量6.74亿t。
资源量18亿t,居世界第五位,其中广西、贵州、河南、广西、山东五省区占全国总储量的85.5%。
但我国铝土矿类型以一水硬铝石型为主,约占总储量的98%以上,而三水铝石型铝土矿仅在海南、广西、福建、台湾等省区有分布。
表1 中国主要铝土矿产地的矿石特征省份Al2O3含量(%)SiO2含量(%)Fe2O3含量(%)平均铝硅比(%)占全国总储量(%)广西58~60 5~6 15~17 9.9 12.8 贵州67~68 8.8~11.1 2.2~3.0 6.1~7.8 18.1 河南64~71 7.5~13.7 3.0~5.1 4.7~9.4 26.0 广东54~61 15~22 5~9 3.7~3.9 3.8 广西63~65 11~13 2~3 5.0~6.0 26.0由表1可以看出我国的铝土矿具有高硅、高铝、低铁的特点,铝硅比偏低,约在4~6之间,其中的主要含铝矿物为一水硬铝石,这是一种难浸出的矿物,用传统的拜耳法处理这类矿石时,要求溶出温度高,使用的碱液浓度也高,因而生产上采用的工艺条件比用三水铝石或一水软铝石为原料时苛刻。
这给拜耳法系统的溶出,分解、蒸发等重要工序的技术和装备带来了一系列困难。
随着氧化铝工业和其他需用铝土矿工业的快速发展,我国铝土矿资源,特别是优质资源的短缺,已充分显现出来。
按目前的生产需求估算,我国每年需消耗的铝土矿多达1000多万t,其中大多是优质矿或次优质矿。
目前优质铝土矿供需矛盾十分突出,矿山均不同程度出现了贫化趋势,特别是河南等地的高铝矿已濒临枯渴,众多用户争先采购有限的优质资源。
我国铝土矿资源基础储量中80%以上为中低品位矿,目前高品位优质铝土矿平均服务年限少于10年。
如果没有新的大规模的高品位铝土矿发现、探明并开发,我国北方地区氧化铝厂的拜耳法系统将在数年之后面临高铝矿资源严重短缺的局面。
这不但将增加单位产品耗矿量,而且将使生产成本大大增加。
面对国内供不应求的市场和国际氧化铝低成本的冲击,我国氧化铝生产显现出危机四伏、回天无力的局面。
中国加入世贸组织以后,受国外氧化铝工业的影响,我的氧化铝工业面临的形势更加严峻。
因此,根据我国铝土矿的特点,开发生产成本低的氧化铝生产工艺,发展我国氧化铝工业,提高我国氧化铝工业的国际竞争力,已迫在眉睫。
2.我国铝土矿的溶出技术的发展目前,管道化高温加热强化溶出技术、铝酸钠溶液高浓度分解技术、新型搅拌分解槽、间接加热的连续脱硅等技术正在推广使用,从国外引进的先进技术与设备已在发挥巨大的作用。
管道化溶出技术管道化溶出是拜耳法溶出工艺及装置的一种,该工艺又分为单管管道化和多管管道化两种,均采用管道进行矿浆的预热及溶出[1]。
前西德V AW于1960年即开始对管道化溶出的技术进行研究,于1966年在纳勃氧化铝厂建成世界上第一套年产60万t氧化铝的管道化溶出装置。
上世纪九十年代初,中铝从V AW引进一套Ra6管道化溶出装置,至九十年代末期成功的应用于氧化铝生产中,开创了管道化溶出用于处理一水硬铝石型铝土矿之先河。
中国长城铝业公司的侯用兴,李旺兴,吕子剑[2]在研制一水硬铝石管道化溶出技术方案时,针对河南一水硬铝石铝土矿可磨性差、硅矿物结构形态复杂、难溶等特点,设置了磨矿、化灰、原矿浆预脱硅、管道化溶出、熔盐加热、和酸洗等工序,使之成为了一个适合我国一水硬铝石的管道化溶出系统。
我国针对一水硬铝石矿物形态复杂、难溶、可磨性差的特性,通过研究一水硬铝石矿的溶出、硅矿物结疤及腐蚀等规律,并对引进的国外设备消化、吸收和创新,首次实现了国际上管道化溶出一水硬铝石的工业实践。
开发研制成功了处理一水硬铝石矿的管道化溶出成套工艺技术和装备。
此项技术在处理一水硬铝石矿技术方面,达到世界领先水平。
但一水硬铝石型铝土矿因其硬度高,对溶出装置的进料泵、管道、管件、阀的磨蚀严重,且其中硅矿物含量较高,还含有少量钛矿物,它们在溶出过程中易形成较多的硅、钛矿物的结疤。
为使管道化溶出装置更好地适应于溶出我国一水硬铝石型铝土矿,不宜采用单纯的管道化溶出装置。
管道预热+保温罐溶出技术我国第一套管道预热+保温停留罐溶出装置是1983年贵阳铝镁设计研究院为郑州轻金属研究院氧化铝中试厂设计的,1988年投产试车成功[3]。
上世纪90年代先后投产的山西铝厂和平果铝厂引进了法国彼施涅铝业公司的“管道预热-压煮器加热溶出”的间接加热溶出技术。
中国长城铝业公司的赵清杰等人[4]通过对目前世界上拜尔法强化溶出工艺的技术分析和对河南封登铝土矿的半工业试验研究,提出了适宜于河南登封铝土矿特点的改良管道预热—停留罐溶出新工艺,它既具有管道预热—停留罐溶出工艺的优点,即保证有良好的溶出效果和较低的能耗,又可避免在管道预热面产生结疤、使强化溶出工艺能长周期运转。
此项技术令矿浆在单管预热器中快速加热到溶出温度,再在停留罐中充分溶出。
它利用了管式反应器容易实现高温溶出及高压釜能保证较长溶出时间的特点,又克服了纯管道化溶出时间管道过长,使泵头压力升高,电耗大且结疤清洗困难的缺点,以及纯高压釜溶出时溶出温度不能超过260℃,机械搅拌密封和结疤清洗困难的缺点,适合于处理需要较长溶出时间的一水硬铝石型铝土矿。
停留罐中无搅拌和加热装置,结构简单,加工制造容易,维修方便,容易清洗结疤。
采用此项技术需要较长的溶出时间以及稍高的碱液浓度(N k150~160g/L)但溶出的热耗较低(约4.0GJ/t.Al2O3以下)与管道化溶出相当,但由于我国一水硬铝石矿含有较高的硅矿物, 为了避免在管道预热面产生结疤,因此要认真研究其在不同温度下的反应行为,以选择适宜的脱硅钛装置才能使此技术得到很好的应用。
单管预热——高压釜溶出技术我国已经引进该项技术并投入生产,其技术特点是器中预热到150℃左右,再在间接加热机械搅拌高压釜中加热、溶出。
溶出温度高260℃,溶出时间充分,达45~60min,矿浆流量450m3/h,相当于年产氧化铝330kt,是当前处理一水硬铝石型铝土矿的最大溶出器组。
此项技术的最大缺点是机械搅拌的高压、高温、高浓度碱的恶劣条件下工作,器内加热管束常被矿浆磨穿造成事故,设备维修频繁,同时还须采用高压蒸汽锅作为热源,热效率不高,这是它的不足之处。
虽然上述技术在一水硬铝石的强化溶出方面都有其显著的优势,但都存在流程长,能耗大的缺点。
只有从我国资源特点出发、开发流程短、能耗低、经济合理的新工艺,才是我们努力的根本方法。
下面分别对几种新兴技术进行介绍。
后加矿增溶溶出技术该技术在本世纪50年代美国首次使用,溶出液的αk为1.48。
随后该技术也在日本得到了应用,溶出液的αk为1 39。
澳大利亚的昆士兰氧化铝厂于1988年开始利用该技术以提高产出率,溶出温度255℃,在此条件下充分溶出Comalco公司的三水铝石——水软铝石矿,然后在180℃的自蒸发器内加入三水铝石矿使氧化铝浓度提高,溶出液的αk 为1.34。
昆士兰氧化铝厂利用此技术将年产量提高10%以上。
郑州轻金属研究所的吕子剑和尹中林[5]等对增溶溶出技术处理我国一水硬铝石矿的可行性进行了分析。
认为到目前为止,我国可用于氧化铝生产的铝土矿几乎全部为一水硬铝石矿,拜耳法溶出需要较高的碱浓度和溶出温度,如在N k200~220g/l,溶出温度为250~260℃的条件下需要60~90分钟才能获得较好的溶出指标,而三水铝石-一水软铝石矿在230℃的温度下只需5分钟即可达到溶出要求,三水铝石矿的溶出则更为容易。
因此,在我国开发利用该项技术具有明显优势。
此技术在无需在大量投资和现场改造的情况下,就可用于我国各拜耳法及联合法氧化铝厂实现增溶溶出,降低溶液出液的分子比。
而且此技术可用于我国氧化铝生产技术的任一发展阶段。
尹中林,周海龙等[6]通过实验证明有目的的提高河南铝土矿溶出配料αk,降低了河南矿的溶出温度,缩短河南矿的溶出时间。
而在溶出料浆自蒸发器中加入适当比例的韦帕矿来进行溶出,可以达到较低溶出液αk,较高溶出率的综合溶出效果,以达到降低能耗,增加产能以及降低赤泥铝硅比的目的。
近年来国内的学者还对采用一水硬铝石矿进行活化焙烧后作为后加矿进行增溶溶出技术以及增浓机理等作了大量研究。
中南工业大学的李小斌等[7~8]对活化焙烧一水硬铝石矿增溶溶出过程动力学作了研究,通过实验验证了当温度在230~240℃之间变化时,焙烧矿在增浓溶出过程中和苛性碱反应为一级反应,遵循推导的反应方程。
山西铝厂的梁春来和中南工业大学的李小斌、彭志宏[9,10,11]对增溶溶出的工艺进行了研究,在拜耳法溶出末期,温度在230℃以上添加焙烧矿相当于拜耳法溶出总配矿量的10~20%,焙烧矿部分氧化铝溶出率可以达到70%以上。
长城铝业公司的张瑜[12]等人利用氢氧化铝生产过程中产生的氢氧化铝结疤料作为后加矿进行增溶溶出实验。
发现拜尔法系统添加氢氧化铝结疤料进行增溶溶出,在技术上可行,流程简单,设备投资少,操作方便,与现有生产工艺流程衔接合理,对现有生产技术条件影响较小。
目前,国内对于采用国外的三水铝石矿和国内的焙烧精矿作为后加矿的增溶溶出工艺的研究比较多。
东北大学的张廷安,王艳利[13,14]等人以三水铝石矿作为后加矿,通过单因素实验推荐增溶溶出条件为:一段配料分子比范围在 1.55~1.60,增溶温度为195~200℃,增溶时间为15~20分钟,后加矿的加矿量为一段溶出时加入一水硬铝石矿的20%左右。
在此条件下,铝土矿的溶出率可以达到88.5%,溶出液的分子比可以降至1.38。
且增溶溶出后矿浆的沉降性能得到很大的改善。
国内的铝土矿中三水铝石只占1%多,而作为后加矿的加入量应占矿石量的10%左右,所以采用三水铝石矿作为后加矿的话,势必要大量进口国外的三水铝石矿,但是国外优质的三水铝石矿价格昂贵并且受多种因素影响。
采用焙烧精矿作为后加矿进行增溶溶出在技术上和工艺上是可行的,但是高温焙烧精矿要增加能耗。
还可以将目前我国联合法工艺中的烧结法粗液直接进行深度碳酸化分解所得到的粗氢氧化铝作为后加矿进行增溶溶出,但关于这方面的研究成果未见更多文字报导。