聚合物加工基础学习知识原理复习资料题
聚合物成型加工基础练习题
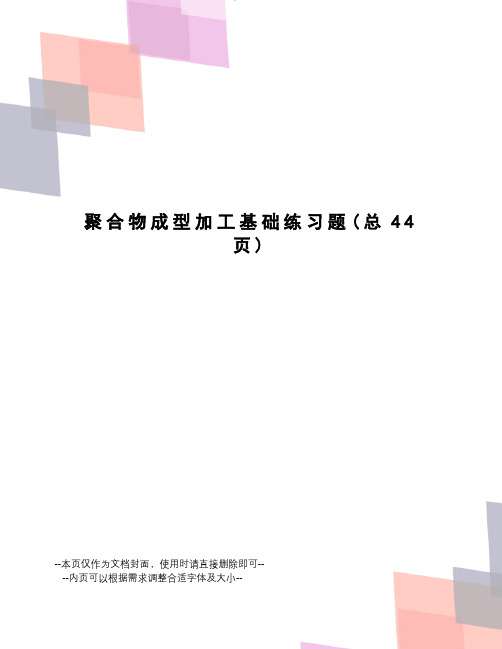
聚合物成型加工基础练习题(总44页)--本页仅作为文档封面,使用时请直接删除即可----内页可以根据需求调整合适字体及大小--基础部分1、简述引起熔体破碎的主要的原因。
熔体破裂是液体不稳定流动的一种现象。
产生熔体破裂的原因主要是熔体中的弹性回复所引起。
熔体在管道中流动时剪切速率分布的不均匀性使熔体中弹性能不均匀分布。
当熔体中产生的弹性应力一旦增加到与滞流动阻力相当时,粘滞阻力就不能再平衡弹性应力的作用,而弹性效应所致熔体流速在某一位置上的瞬时增大形成“弹性湍流”,即“应力破碎”现象。
在园管中,如果产生弹性湍流的不稳定点沿着管的周围移动,则挤出物将呈螺旋状,如果不稳定点在整个圆周上产生,就得到竹节状的粗糙挤出物。
产生不稳定流动和熔体破裂现象的另一个原因是熔体剪切历史的波动引起的。
即剪切应力不同,熔体所产生的弹性效应不同,从而使其弹性回复产生差异,形成熔体破裂。
2、将聚丙烯丝抽伸至相同伸长比,分别用冰水或90℃热水冷却后,再分别加热到90℃的二个聚丙烯丝试样,哪种丝的收缩率高,为什么用冰水的聚丙烯丝收缩率高,因为冰水冷却时,冰水的温度远远低于聚丙烯的最佳结晶温度,此时,聚丙烯丝的结构更多的保持了其纺丝过程中分子的取向状态,而用90℃热水冷却时,聚丙烯分子具有较为充分的解取向时间,当聚丙烯丝再次分别加热到90℃时,前者才进行较高程度的解取向,表现出较高的收缩率。
3、简述高聚物熔体流动的特点。
由于高聚物大分子的长链结构和缠绕,聚合物熔体、溶液和悬浮体的流动行为远比伤分子液体复杂。
在宽广的剪切速率范围内,这类液体流动时剪切力和剪切速率不再成比例关系,液体的粘度也不是一个常此因而聚合物液体的流变行为不服从牛顿流动定律。
即非牛顿型流动。
4、举例说明高聚物熔体粘弹性行为的表现。
聚合物流动过程最常见的弹性行为是端末效应和不稳定流动。
端末效应包括入口效应和模口膨化效应(离模膨胀)即巴拉斯效应。
不稳定流动即可由于熔体弹性回复的差异产生熔体破碎现象。
高分子 聚合物加工原理试题

高分子聚合物加工原理试题聚合物加工原理试题一、名词解释:1、高聚物的成型加工通常是在一定温度下使聚合物变形或熔融,经过模具或口模流道的压塑,形成所需的形状,通过定型得到能保持所取得形状的制品的工艺过程。
2、热塑性塑料塑料的一大类。
以热塑性树脂为基本成分的塑料,一般具有链状的线型结构,受热软化,在成型过程中是物理变化过程,成型冷却后便成为成品。
可反复塑制。
4、异型材的挤出成型通过挤出成型将聚合物材料制成横向截面非圆形、环形的各种异型形状的连续型材的工艺过程。
二、填空4、在粉料的制备过程中,首先要做好原料的准备工作,准备工作的第一项是原料的预处理,原料的预处理通常是指树脂过筛、吸磁、固体助剂粉碎、粉状助剂磨浆、母料的配制等工作。
6、挤出理论概括为固体输送理论、熔融理论、熔体输送理论三个理论,其意义在于寻求在聚合物加工中提高产量、提高塑化质量、降低能量消耗的有效途径。
10、常见双螺杆挤出机的类型:异向旋转平行啮合型双螺杆挤出机、同向旋转平行啮合型双螺杆挤出机、异向旋转锥型啮合双螺杆挤出机。
三(判断题: (每题1分)1.降低物料与螺杆的摩擦系数,有利于提高固体输送率。
( )3.如果有几种非牛顿流体,其中非牛顿指数n最小者,其流动行为必定与牛顿流体偏离最远。
()4.在评定固体物料的混合状态时,不仅要比较取样中各组分的比率与总体比率间的差异大小,而且还要考查混合料的分散程度。
( )5.拉伸后的薄膜或单丝,在重新加热时,将会延着分子定向方向发生较大的收缩。
()10.在塑料成型操作中,对一种表观粘度随温度变化不大的聚合物来说,可以仅凭增加温度来增加其流动性而成型。
( )四(计算题一台单螺杆挤出机,加料段螺杆的几何参数为:料筒内径D,90mm,螺距S,90mm,螺杆根部直径Ds,62mm,螺纹宽度e??,9mm,螺纹头数i,1;求:这台挤出机的最大挤出量。
已知:Db,90,Ds,62,h1,(Db-Ds)/2, ( 90-62)/2,14mm解:(φb,arctan(s/πDb),arctan(90/3.14×90),17.67?(φs,arctan(s/πDs),arctan(90/3.14×62),24.81?(φ,arctan(s/πD),arctan(90/3.14×76),20.66?sinφb,sin17.67?,0.30 cosφ,cos17.67?,0.95n Wb,s/i cosφb- e,=90× cos17.67?-9 = 90× 0.95-9=76.5 n Ws,s/icosφs-e,=90× cos24.81?-9= 90× 0.91-9=72.9 n W,s/i cosφ-e,=90×cos20.66?- 9= 90× 0.93-9=74.7 n Q=Qmax= π2??h1??Db(Db-h1) n (W/W, e,) sinφ??cosφn = 3.142×14×90(90-14)×1×(74.7/74.7,9)sin17.67?×cos17.67? n=9.86×14×90×76×0.89×0.30×0.95=239×103mm3/min 答:这台挤出机的最大挤出量239×103mm3/min.六、问答题2、为什么要对一些成型物料进行(干燥)预处理,举例说明,并列出工艺条件。
聚合物加工原理

《聚合物加工原理》复习题
1.聚合物的聚集态结构有哪些特点?
2.聚合物的结晶过程。
3.成型加工条件对结晶过程经过的影响。
4.单轴拉伸和双轴拉伸取向概念及对制品性能的影响。
5.成型加工中降解形式及产生的原因。
6.假塑性流体的流变性质。
7.影响聚合物流变行为的主要因素。
8.聚合物熔体弹性产生及影响因素。
9.聚合物流体流动过程中的末端效应。
10.物料混合的分类及混合设备。
11.单螺杆挤出机的基本结构及作用。
12.挤出螺杆的主要功能及各段的主要作用。
13.挤出成型的基本过程。
14.挤出成型的工艺过程。
15.熔体在螺杆中的流动形式。
16.PVC管材生产工艺流程。
17.聚乙烯单丝生产工艺流程、工艺及控制。
18.电线电缆包覆工艺流程。
19.注塑机的基本结构。
20.注塑成型周期分析。
21.注塑成型的塑化分析。
22.注塑成型的流动分析。
23.热固性塑料注塑成型特点。
24.双色注射成型、夹芯注射成型、发泡注射成型的基本过程。
25.柱塞式注塑机分流梭的作用。
26.双色注射为什么不适用热稳定性差塑料的生产主要原因。
27.说明注射长试样时熔体在模具型腔中流动取向分布曲线情况。
28.压制成型的基本原理。
29.压制成型工艺过程。
聚合物加工原理复习及作业

此时流体不再能充满所有的空隙,润滑作用因
而受到限制,表观粘度就随着剪切速率的增长 而增大。
2.时间依赖性液体
产生震凝性的原因,可以解释为液体中 的不对称粒子(椭球形线团)在剪切力场的
震 凝 性 液 体
速度作用下取向排列形成暂时次价交联点所 致,这种缔合使粘度不断增加而形成凝胶状, 一旦外力作用终止,暂时交联点也相应消失, 粘度重新降低。
1、影响聚合物流变行为的主要因素, 非牛顿液
体及其流变行为。 2、牛顿液体的流变学方程及非牛顿液体的流变 学方程。
第一节 聚合物熔体的流变行为
聚合物熔体在加工过程中的力学行为:
聚 合 物 受 力 的 三 种 类 型
剪切应力
简单的剪切
拉伸应力
简单的拉伸
流体静压力P
流体静压力的均 匀压缩
聚 合 物 受 力 的 相 应 形 变
一、牛顿流体及其流变方程
1.流动类型
层流和湍流 Re<2100 层流
低分子流体 Re>2100
湍流
Re=2100~4000 过渡态(介于层流与湍 流) 聚合物熔体,在成型过程中流动时,其雷诺准数一
般小于10,分散体也不会大于2100,因此其流动均为层
流。
原因:
粘度高,如低密度聚乙烯的熔体粘度约为 0.3×102 ~ 1×103Pa.s ,而且流速较低,在加工
剪切流动按其流动的边界条件可分为拖曳流动和压力 流动 由边界的运动而产生的流动,如运转滚筒表面
对流体的剪切摩擦而产生流动,即为拖曳流动。 而边界固定,由外压力作用于流体而产生的流 动,称为压力流动。
例如
聚合物熔体注射成型时,在流道内的流动 属于压力梯度引起的压力流动。 聚合物在挤出机螺槽中的流动为另一种剪
聚合物成型加工复习题-最终版

一、填空题:1.影响聚合物流变行为的主要因素有温度、压力、剪切速率、聚合物结构和组成。
2.对塑料制品进行热处理的主要目的是消除制品的内应力、提高尺寸稳定性。
热处理应该在高于玻璃态转化温度低于粘流温度的温度范围内进行。
此过程中聚合物的结晶度增高,取向度降低。
3.在处于粘流温度以上较小区域的温度范围,聚合物的粘度符合ln= lnA + E/RTη,其中Eη为聚合物的粘流活η化能(千卡/克分子)。
5.螺旋流动试验被广泛地用来判断聚合物的可模塑性。
7.在平均分子量相同时,随分子量分布变宽,聚合物熔体的粘度迅速下降,流体的非牛顿性更强。
8.混合过程一般是靠扩散、对流、剪切作用来完成的,在初混合过程中起主要作用的是对流作用,塑炼过程中起主要作用的是剪切作用。
9.固体物料的混合效果可以用分散程度和均匀程度来评定。
11.在聚合物成型加工中,流动和拉伸会使聚合物产生取向。
13.用于物料的塑炼的常用设备有开炼机、密炼机、螺杆挤出机等。
14.“五大合成树脂”是指聚乙烯(PE)、聚氯乙烯(PVC)、聚苯乙烯(PS)、聚丙烯(PP)和ABS树脂,其中,热15.某PP熔体的粘度为4000Pa·s,若其平均分子量增加一倍,在同样条件下,熔体的粘度约为42224Pa·s。
16.聚合物熔体在园管中流动,在管壁处所受的剪切应力最大。
17.某PVC配方为(以PVC为100份计):邻苯二甲酸二辛酯40,二盐基亚磷酸铅3,石蜡0.8,氯化石蜡5。
各组分的主要作用分别为:邻苯二甲酸二辛酯是增塑剂,二盐基亚磷酸铅是热稳定剂,石蜡是润滑剂,氯化石蜡是增塑剂。
19.注射成型时充模不满的可能原因有树脂塑化量不足、模温过低、流道部分堵塞、注射压力过低、注射速度太低等。
20.单螺杆挤出机的螺杆可分为加料段、压缩段、均化段等基本功能段。
其中,压缩段的螺槽容积逐渐变小,料筒中的压力在均化段提升最大。
21.为了提高物理机械性能和尺寸稳定性,初生纤维要进行后拉伸和热定型等后处理。
聚合物加工原理
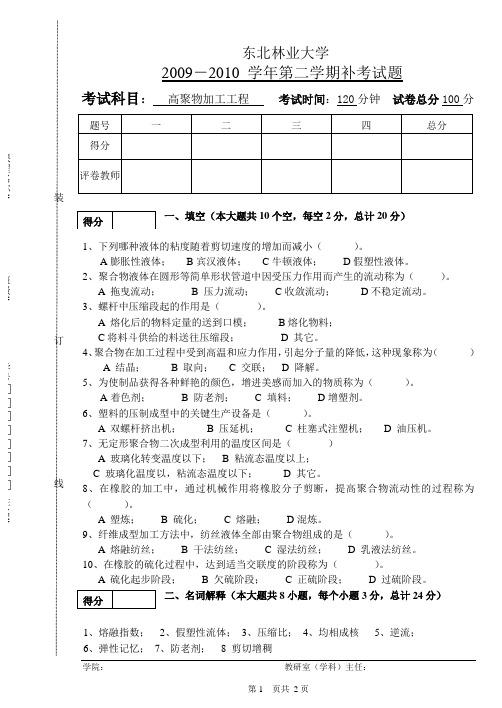
东北林业大学 2009-2010 学年第二学期补考试题 考试科目: 高聚物加工工程 考试时间:120分钟 试卷总分100分一、填空(本大题共10个空,每空2分,总计20分) 1、下列哪种液体的粘度随着剪切速度的增加而减小( )。
A 膨胀性液体; B 宾汉液体; C 牛顿液体; D 假塑性液体。
2、聚合物液体在圆形等简单形状管道中因受压力作用而产生的流动称为( )。
A 拖曳流动; B 压力流动; C 收敛流动; D 不稳定流动。
3、螺杆中压缩段起的作用是( )。
A 熔化后的物料定量的送到口模; B 熔化物料; C 将料斗供给的料送往压缩段; D 其它。
4、聚合物在加工过程中受到高温和应力作用,引起分子量的降低,这种现象称为( ) A 结晶; B 取向; C 交联; D 降解。
5、为使制品获得各种鲜艳的颜色,增进美感而加入的物质称为( )。
A 着色剂; B 防老剂; C 填料; D 增塑剂。
6、塑料的压制成型中的关键生产设备是( )。
A 双螺杆挤出机; B 压延机; C 柱塞式注塑机; D 油压机。
7、无定形聚合物二次成型利用的温度区间是( ) A 玻璃化转变温度以下; B 粘流态温度以上; C 玻璃化温度以,粘流态温度以下; D 其它。
8、在橡胶的加工中,通过机械作用将橡胶分子剪断,提高聚合物流动性的过程称为( )。
A 塑炼; B 硫化; C 熔融; D 混炼。
9、纤维成型加工方法中,纺丝液体全部由聚合物组成的是( )。
A 熔融纺丝;B 干法纺丝;C 湿法纺丝;D 乳液法纺丝。
10、在橡胶的硫化过程中,达到适当交联度的阶段称为()。
A 硫化起步阶段;B 欠硫阶段;C 正硫阶段;D 过硫阶段。
二、名词解释(本大题共8小题,每个小题3分,总计24分)1、熔融指数;2、假塑性流体;3、压缩比;4、均相成核5、逆流;6、弹性记忆;7、防老剂; 8 剪切增稠1、什么是聚合物的可模塑性,采用何种仪器测量,如何衡量聚烯烃的模塑性?(7分)2、试描述挤出成型过程中,一个螺槽内的塑料是如何熔融的。
聚合物成型加工复习题

在墙上刷一层 100 微米厚的涂料, 涂料的粘度为多大时, 才能保证涮涂后涂料在墙上向下流 淌的速度不超过 10 微米/秒?
2.1.3 聚合物普适流动曲线
三个区域: 1、第一牛顿区 零切粘度 (反映材料性质) 2、假塑性区(非牛顿区) 随切变速率增加,表观粘度ηa 值变小。 通常聚合物流体加工成型时的切变速率正在这一范围内。 3、第二牛顿区 无穷切粘度或极限粘度η∞。通常观察不到 聚合物流动曲线的微观解释 某个实验的结论 结论:随剪切速率升高,体系的取向程度提高 结论:在取向度相同的条件下,不同体系具有相同的约化粘度。 约化粘度:表观粘度与零切粘度的比值 聚合物流动曲线的解释 缠结理论解释:缠结破坏与形成的动态过程。 ⅰ第一牛顿区: 高分子处于高度缠结的拟网结构,流动阻力大;缠结结构的破坏速度等于 形成的速度,粘度保持不变,且最高。 ⅱ假塑性区:切变速率增大,缠结结构被破坏,破坏速度大于形成速度,粘度减小,表现出 假塑性流体行为。 ⅲ第二牛顿区:切变速率继续增大,高分子中缠结结构被完全破坏,来不及形成新的缠结, 体系粘度恒定,表现牛顿流动行为。
第二章 高聚物流变性能的一般特征 2.1 聚合物熔体的流变行为
(a)拉伸流动: 流体内质点速度沿着流动方向发生变化、垂直于流动方向是相等的。 存在纵向速度梯度 (b)剪切流动: 流体内质点速度仅沿着与流动方向垂直的方向发生变化。 存在横向速度梯度 2.1.1 流体的流变方程,牛顿流体 简单平行剪切流场
粘弹性-本课程最重要的概念! ! 1)剪切变稀 聚合物粘度随着剪切速率的增加而减小 大部分聚合物属于这种类型 剪切增稠 聚合物粘度随着剪切速率的增加而增加 高聚物悬浮液
(不是时间 t 的函数) 2)韦森堡效应。 又叫爬杆现象,是高分子液体法向应力差的反映。 3)挤出胀大 巴拉斯效应, 当高聚物熔体从小孔、 毛细管或狭缝中挤出时挤出物在挤出模口后膨 胀使其横截面大于模口横截面的现象。 定量上用胀大比来表示。 挤出物胀大在聚合 物熔体中是常见的, 这是由于聚合物熔体在模具内因流动而取向, 在流出模口时分 子重新蜷曲。挤出物胀大随切变速度增大而增大,在到达最大值后再下降。分子量 增大和其他能增加缠结的因素(如长支链的增加)都将使挤出物胀大增大。 4)无管虹吸 对牛顿型流体,当虹吸管提高到离开液面时,虹吸现象立即终止。 对高分子液体, 如聚异丁烯的汽油溶液或聚醣在水中的微凝胶体系, 当虹吸管升离 液面后,杯中的液体仍能源源不断地从虹吸管流出,这种现象称无管虹吸效应。 5)二次流 因流线弯曲、 水流分离等引起的除主流以外的各种次生流动的总称。 对于弹性等有 影响啊 6)触变性和震凝性 触变(摇溶)体:指恒温、恒γ下,粘度随受剪时间的增加而下降的流体。冻胶是最 常见的典型触变体。 震凝(摇凝)体:指恒温、恒γ下,粘度随受剪时间的增加而增大,一般受剪切 10~ 100 分钟后可达到一平衡值,当停止剪切后,可以回复到受剪切前的粘度。 1.3 流变学在聚合物加工中的应用 1)可指导聚合,以制得加工性能优良的聚合物。 2)对评定聚合物的加工性能、分析加工过程、正确选择加工工艺条件、指导配方设计均有 重要意义。 3)对设计机械和模具有指导作用。 1.4 聚合物流变学的研究方法、 1)宏观流变学(唯象流变学、加工流变学) 用宏观物理量:η、τ、 、T、t 等,采用连续介质力学理论建立物质的应力-应变关 系,建立本构方程。 2)微观流变学(结构流变学) 研究聚合物奇异的流变学性质与其微观结构-分子链结构、聚集态结构之间的联系。 3)流变测量学 通过各种仪器测定材料参数和物理函数, 通过可测量的物理量 (流量、 压力差、 转速、 扭矩)获得不可直接测量的流变量(剪切速率、剪切应力、粘度、法向应力差系数等) 。 小结 1. 流变学是一种世界观和方法论; 2. 聚合物流变学是随着高分子材料工业的大规模发展而成长起来的新兴学科 . 它是研究高 分子材料结构性能与加工工艺关系的理论基础; 3. 粘弹性是聚合物流变行为的基本特征。
聚合物加工工程

聚合物加工题库塑料部分第一章绪论2学时 1 道题第二章聚合物加工基本原理6学时28道题第三章成型用原料2学时22道题第四章混合与混炼4学时36道题第五章挤出成型10学时72道题第六章注射成型6学时38道题第七章压延成型4学时25道题第八章中空吹塑4学时9道题第九章模压成型4学时8道题第十章其他成型方法6学时16道题纤维十一~十五章橡胶十六~十九章第一章聚合物加工基本原理2学时1道题1、塑料工业包括哪三个生产系统?(简答题4分)塑料原料(树脂、助剂)的生产、塑料的配制和塑料制品的生产、塑料成型机械和模具的生产。
第二章聚合物加工基本原理6学时28道题1、可挤压性(概念题2 分)可挤压性是塑料通过挤压作用变形时,获得和保持其形状的能力。
利用可挤压性可进行“口模成形”。
2、可模塑性(概念题2 分)可模塑性是塑料在温度、压力作用下产生变形并在模具中模制成型的能力。
3、可纺性(概念题2 分)可纺性是塑料熔体通过成形而制成细长而连续的固态纤维的能力。
4、可压延性(概念题2 分)可压延性是指塑料在一个或两个方向上受到压延或拉伸力作用时发生变形的能力。
5、聚合物的可加工性有:、、、。
(填空题2分)6、哪些指标可以表征聚合物材料的加工性能(简答题5分)粘度、熔融指数MI(可挤出性)螺旋线长度(可模塑性) 熔体细流的稳定性(可纺性)细颈长度、自然拉伸比(可延性)7、什么是可挤压性能?什么指标可以表征聚合物材料的可挤压性能(简答题5分)可挤压性是指聚合物通过挤压作用形变时获得形状和保持形状的能力。
MI η8、什么是可模塑性能?什么指标可以表征聚合物材料的可模塑性能?(简答题5分)可模塑性是指材料在温度和压力作用下形变和在模具中模制成型的能力。
螺线长度(可模塑性)9、什么是可纺性能?什么指标可以表征聚合物材料的可纺性能(简答题5分)可纺性是指聚合物材料通过加工形成连续的固态纤维的能力。
熔体细流的稳定性(可纺性)10、什么是可延性能?什么指标可以表征聚合物材料的可延性能(简答题5分)可延性表示无定形或半结晶固体聚合物在一个方向或二个方向上受到压延或拉伸时变形的能力。
- 1、下载文档前请自行甄别文档内容的完整性,平台不提供额外的编辑、内容补充、找答案等附加服务。
- 2、"仅部分预览"的文档,不可在线预览部分如存在完整性等问题,可反馈申请退款(可完整预览的文档不适用该条件!)。
- 3、如文档侵犯您的权益,请联系客服反馈,我们会尽快为您处理(人工客服工作时间:9:00-18:30)。
1.单轴取向:取向单元沿着一个方向做平行排列而形成的取向状态2.双轴取向:取向单元沿着两个互相垂直的方向取向3.降解:聚合物分子主链断裂引起聚合度降低或发生分子内链转移反应的现象。
4.剪切变稀:聚合物流体表现为假塑性流动的区域。
随着剪切速率增大,其表观粘度降低。
5.机械降解:聚合物受到外力作用(如粉碎、塑炼、高速搅拌、塑化、挤出、注射等过程)引起聚合物的降解。
6.端末效应:聚合物在管道中进行剪切流动时,流体流经截面变化的部位时发生的弹性收敛和膨胀运动。
7.入口效应:由于流道截面变小,使流体压力降突然增大的现象。
8.离模膨胀效应:聚合物流体离开口模后产生体积膨胀的现象。
9.注塑成型周期:完成一次注塑所需的时间称为成型周期。
包括合模时间、注座前进时间、注射时间、保压时间、冷却时间、开模时间、制件顶出时间、以及下一成型周期的准备时间。
10.注塑成型塑化:塑料在料筒内受热达到流动状态并具有良好可塑性的过程。
11.层压成型:在一定温度和压力下,将多层浸有热塑性树脂或热固性树脂的薄片状材料黏结和熔合成为具有一定厚度的层压板材。
1.聚合物的结晶过程①结晶温度范围:Tg-Tm之间②结晶过程:晶核生成和晶体生长。
低温区为生成晶核,高温区为晶体生长。
2.物料混合的分类及混合设备分类:(1)按分散程度简单混合和分散混合;(2)按混合过程的特点间歇混合和连续混合;(3)按混合形式层流剪切混合和固定混合。
设备:转鼓式混合机、螺带式混合机、捏合机、高速混合机、密炼机、双辊混炼机、挤出机3.螺杆冷却与加料斗冷却作用螺杆冷却作用:控制物料温度;降低物料与螺杆的摩擦系数,提高物料输送效率;加料斗冷却作用:防止物料在料斗中架桥而影响加料进入机筒。
4. 注塑成型减少内应力措施(工艺上):①提高熔体温度和模具温度;②降低充模压力和充模速度;③缩短保压时间。
1.单轴拉伸和双轴拉伸取向概念及对制品性能的影响单轴取向是指取向单元沿着一个方向做平行排列而形成的取向状态双轴取向是指取向单元沿着两个互相垂直的方向取向单轴拉伸和双轴拉伸取向导致制品中在性能上表现出各向异性,以提高制品的力学强度;有的取向会给制品带来不利影响,如易使制品发生翘曲、变形、开裂等现象。
取向过程是分子链或链段有序排列过程,拉伸取向是在Tg-Tm(或T f)温度范围内发生,流动取向是在高于T f温度发生。
取向后使制品沿取向方向拉伸强度增大,断裂伸长率下降。
根据拉伸取向方式不同,取向可分为单轴取向和双轴取向(如塑料绳、纤维的生产为单轴取向,双向拉伸薄膜生产为双轴取向)。
注塑制品主要发生流动取向,使制品产生内应力,易发生翘曲变形现象。
无定形聚合物的流动取向2.假塑性流体的流变性质聚合物流体表现为假塑性流动的区域。
随着剪切速率增大,其表观粘度降低,称为“剪切变稀”。
3.影响聚合物流变行为(粘度)的主要因素(1)温度对粘度的影响(温度T↑,粘度↓)(2)压力对剪切粘度的影响(压力增大使粘度增大、分子间作用力↑粘度↑)(3)剪切速率或剪切应力对表观粘度的影响(速率增加,粘度减小)(4)聚合物结构因素的影响:①分子链柔韧性(柔性大的粘度大);②长支链(长支链的粘度大);③侧基大小(侧基大的粘度大);④分子量(分子量↑,粘度↑);⑤分子量分布(分子量分布窄的粘度大)。
(5)添加剂对剪切粘度的影响(一般添加无机填充剂、纤维状填充剂会增加聚合物熔体粘度;而润滑剂、增塑剂则会降低熔体粘度)。
4.成型加工中降解形式及产生的原因降解:指聚合物分子主链断裂引起聚合度降低或发生分子内链转移反应的现象。
降解原因:光、热、辐射、机械力等(物理因素);氧、水、醇、酸、碱(化学因素)。
(1)热降解:形式:无规热降解(如PE、PP等);链式降解(如PMMA);消除反应(PVC、聚醋酸乙烯酯等)。
原因:温度高于其分解温度或在分解温度下停留时间过长。
PVC、POM是典型的热敏性聚合物。
(2)机械降解指聚合物受到外力作用(如粉碎、塑炼、高速搅拌、塑化、挤出、注射等过程)引起聚合物的降解。
(3)氧化降解聚合物在氧存在下,同时伴随光、热、辐射作用易发生自由基降解,但也可能发生交联。
所以聚合物氧化机理比较复杂。
(4)水解对于极性聚合物,由于其吸水性大,其极性基团在高温情况下易发生水解反应,使聚合物发生水解。
5.注塑成型的塑化分析及主要工艺参数(1)注塑成型的塑化指塑料在料筒内受热达到流动状态并具有良好可塑性的过程。
塑料塑化受热包括料筒外加传导热和塑料的剪切生热。
a.塑化量:指单位时间内注塑机熔化塑料的重量。
螺杆式注射机的塑化量比柱塞式注射机高。
b.热均匀性螺杆式注射机的热均匀性比柱塞式注射机好。
(2)主要工艺参数:温度:注塑成型温度、模具温度;压力:注射压力、保压压力、预塑压力(背压)时间:注射时间、保压时间、冷却时间。
6.聚合物熔体弹性产生及影响因素聚合物弹性形变由链段运动引起的,链段运动的能力由松弛时间τ决定。
(1)分子量及分子量分布分子量大、分子间作用力强,熔体粘度高,松弛时间长,弹性效应大,熔体易破碎;分子量分布宽,高分子量级分松弛时间长,熔体弹性行为强。
(2)温度与剪切速率温度升高,松弛时间缩短熔体破碎的临界剪切速率提高;剪切速率增大,熔体弹性行为增强。
(3)流道的几何尺寸管径突变,熔体弹性效应增加;口模长径比(L/D)增大,熔体弹性形变可得到充分松弛,使熔体弹性恢复变小。
7.聚合物流体流动过程中的端末效应(1)端末效应指聚合物在管道中进行剪切流动时,流体流经截面变化的部位时发生的弹性收敛和膨胀运动。
(2)影响端末效应的因素:入口效应:由于流道截面变小,使流体压力降突然增大的现象;离模膨胀效应:聚合物流体离开口模后产生体积膨胀的现象。
①内因:分子量高、分子量分布窄和非牛顿性强的聚合物,出口膨胀现象越显著。
②外因:流道长度长、稳定流动时间长、增大流道直径或提高流道长径比(L/D)、提高流体温度,出口膨胀现象降低。
8.挤出成型工艺过程及主要工艺参数工艺参数:螺杆转速、挤出成型温度。
9.熔体在螺杆中的流动形式a.正流:物料沿螺槽向机头方向的流动,是螺杆旋转时螺棱的推力在螺槽z轴方向作用的结果。
b.逆流:逆流方向与正流相反,由机头、口模、过滤网等对物料反压引起的流动。
c.漏流:由口模、机头、过滤网等对物料的反压引起的,通过螺杆与机筒间隙δ沿螺杆轴向料斗方向的流动。
d横流:物料沿螺纹斜棱相垂直方向的流动。
10.单螺杆挤出机的基本结构及作用①挤出系统:由螺杆和机筒组成,其作用使塑料塑化均匀,建立压力,使物料被螺杆连续、定压、定温、定量挤出机头。
②传动系统:由电动机、调速装置及传动装置组成,其作用是驱动螺杆、保证螺杆在挤出过程所需的扭矩和转速。
③加热冷却系统:由温控(加热圈、冷却水或鼓风)设备组成,其作用是通过加热和冷却,保证挤出系统的成型在工艺要求的温控范围内进行。
④控制系统:由电器、仪表和执行机构组成,其作用是调节螺杆的转速、机筒温度和机头压力。
11.螺杆基本参数:a.螺杆直径D:是指螺杆外径,D越大,产量越高。
b.螺杆长径比L/D:是指螺杆工作部分的有效长度与直径之比。
L/D越大,物料塑化、混合效果越好,挤出产量越大,通常在15~40。
c.压缩比ε:指加料段第一个螺槽容积与均化段最后一个螺槽容积之比。
不同物料ε不同,只要起到压实物料作用。
12.挤出螺杆的主要功能及各段的主要作用挤出螺杆的主要功能:输送固体物料、压紧和熔化固体物料,均化、计量和产生足够压力以挤出熔融物料。
a加料段作用(固体输送区):此段螺槽为等深等距,随着螺杆转动,使物料受压、受热前移。
此段物料仍为固体,末端接近粘流温度,有些发粘。
b.压缩段作用(熔融区):此段螺杆螺槽容积逐渐变小,随着螺杆转动,物料被进一步剪切搅拌,压实,物料由固体转化为熔融体,并排除物料中的空气。
c.均化段作用(熔体输送区):使熔体进一步均化,将料流定量定压送入机头,使其在口模中成型。
13.PVC管材生产工艺流程14.在挤出成型理论中,根据固体输送理论,固体输送的必要条件及提高固体输送效率的措施必要条件:①只有当Fs<Fbz时,物料才能在机筒与螺杆间产生相对运动,并被迫沿螺槽移向前方;②固体与机筒的摩擦系数必须大于固体与螺杆的摩擦系数(Fb>Fs),才能保证物料沿着螺槽方向向前输送。
措施:提高螺杆固体输送效率,从挤出机结构和挤出工艺两方面采取措施。
a.挤出机结构:增加螺槽深度、降低物料与螺杆的摩擦系数fs,增大物料与料筒的摩擦系数可提高固体输送率;b.挤出工艺角度:螺杆通冷却水、增加料筒温度和降低螺杆温度都可提高固体输送率。
15.热固性层压板材成型的基本过程①成型工艺过程:叠料、进模、热压、脱模、加工和热处理。
叠料:将附胶材料进行剪裁和层叠,层叠厚度确定制品要求确定。
叠料要求:板坯两面加用2~4张表面专用附胶材料(含脱模剂),以改善板材表观质量;附胶材料叠放排列方向可互相垂直或同向。
叠好板坯压制单元顺序:金属板—衬纸—单面钢板—板坯—单面钢板—衬纸—金属板。
进模:将装好的压制单元分层推入多层压机的热板中,闭合压机,升温升压进行压制。
热压:压制温度和压力控制分五段:第一阶段为预热阶段:从室温到硬化反应开始的温度。
此段树脂熔化,浸透玻璃布,排除挥发份,压力为总压力的1/3~1/2。
第二阶段为保温阶段:树脂在低温下固化反应,直至板坯边缘的树脂不能被拉成丝,开始升温升压。
第三阶段为升温升压阶段:温度和压力升值工艺规定值。
第四阶段为热压保温阶段:树脂充分固化,制品达到最佳性能。
第五阶段为冷却阶段:板坯充分固化后冷却,便于脱模。
脱模:当压制好的板材温度降至60℃,卸压,依次推出板材。
加工:除去压制好的板材的毛边。
热处理:进一步固化树脂,消除内应力。
如环氧树脂和酚醛树脂层压板热处理温度120~130℃,时间120~150min。
16.聚乙烯单丝生产工艺流程、工艺及控制工艺流程:原料→挤出→喷丝板挤出→水冷→加热拉伸→定型热处理→卷取工艺及控制:①温度控制喷丝机头温度一般比挤出成型其他产品温度高,一般在220~240℃,聚合物分子量分布窄(如HDPE5000s)。
②冷却水温经喷丝板成型的丝坯立刻进入水箱冷却,主要是为了防止单丝粘连和降低聚乙烯结晶,有利于提高拉伸质量。
水温控制在25~35℃,水面距喷丝板距离15~30mm。
③拉伸温度和倍数拉伸时大分子链取向过程,为了便于快速分子链或链段取向,必须在接近其熔点温度附近进行。
HDPE单丝的拉伸温度接近100℃,一般采用热水加热,如高于100℃,可采用电热板加热。
拉伸温度越高,拉伸倍数越大,拉伸速度越快,力学强度越高,反之则相反。
拉伸倍数一般在6~10倍。
④热处理PE单丝拉伸后伸长率较大,受热容易热收缩。