锅炉结焦解决方法
锅炉结焦现场处置方案
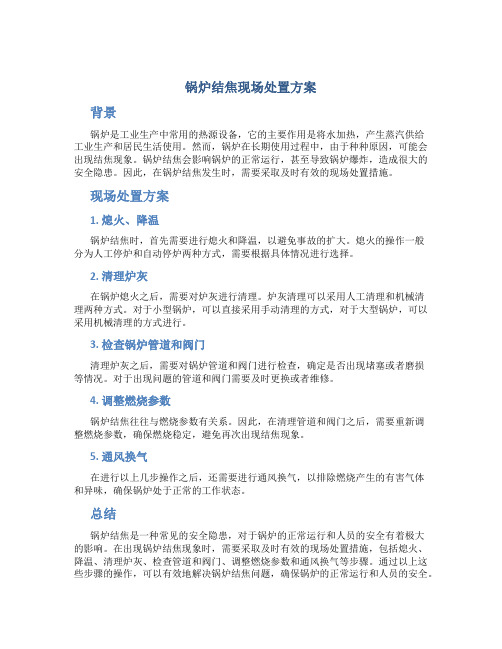
锅炉结焦现场处置方案背景锅炉是工业生产中常用的热源设备,它的主要作用是将水加热,产生蒸汽供给工业生产和居民生活使用。
然而,锅炉在长期使用过程中,由于种种原因,可能会出现结焦现象。
锅炉结焦会影响锅炉的正常运行,甚至导致锅炉爆炸,造成很大的安全隐患。
因此,在锅炉结焦发生时,需要采取及时有效的现场处置措施。
现场处置方案1. 熄火、降温锅炉结焦时,首先需要进行熄火和降温,以避免事故的扩大。
熄火的操作一般分为人工停炉和自动停炉两种方式,需要根据具体情况进行选择。
2. 清理炉灰在锅炉熄火之后,需要对炉灰进行清理。
炉灰清理可以采用人工清理和机械清理两种方式。
对于小型锅炉,可以直接采用手动清理的方式,对于大型锅炉,可以采用机械清理的方式进行。
3. 检查锅炉管道和阀门清理炉灰之后,需要对锅炉管道和阀门进行检查,确定是否出现堵塞或者磨损等情况。
对于出现问题的管道和阀门需要及时更换或者维修。
4. 调整燃烧参数锅炉结焦往往与燃烧参数有关系。
因此,在清理管道和阀门之后,需要重新调整燃烧参数,确保燃烧稳定,避免再次出现结焦现象。
5. 通风换气在进行以上几步操作之后,还需要进行通风换气,以排除燃烧产生的有害气体和异味,确保锅炉处于正常的工作状态。
总结锅炉结焦是一种常见的安全隐患,对于锅炉的正常运行和人员的安全有着极大的影响。
在出现锅炉结焦现象时,需要采取及时有效的现场处置措施,包括熄火、降温、清理炉灰、检查管道和阀门、调整燃烧参数和通风换气等步骤。
通过以上这些步骤的操作,可以有效地解决锅炉结焦问题,确保锅炉的正常运行和人员的安全。
锅炉大面积结焦处置方案

锅炉大面积结焦处置方案一、研究结焦原因和特点,定位问题区域1.1分析燃烧情况、燃料特性和供氧条件,找出造成结焦的主要原因。
1.2通过锅炉内外视察、红外线热像仪等手段,确定结焦区域、范围和程度。
可以分为严重和轻微两个等级,以便分别采取不同的处置措施。
二、采取机械清扫措施2.1使用清扫器具,定期清除结焦区域的积碳物质。
可以选择刷子、铲刀、高压水枪等清扫工具,根据结焦程度和材料特性来选择具体工具。
2.2清扫时要注意保护锅炉受热面和管壁,避免造成机械损伤,尽量采用无损伤的清扫措施。
三、采取化学清洗措施3.1选用适当的化学清洗剂,将其稀释到合适的浓度后喷洒在结焦区域。
清洗剂的选择要根据结焦物质的成分和特性来确定。
3.2在清洗剂作用下,经过一定时间的浸泡和反应,结焦物质会逐渐溶解和脱落。
可以使用软化水和其他辅助措施来提高清洗效果。
3.3清洗过程中需要注意保护操作人员的安全,戴好防护手套和眼镜,避免化学品对人体的伤害。
四、加强监测和预防措施4.1建立完善的监测体系,对锅炉的温度、压力、烟气成分等进行实时监测。
及时发现结焦问题,进行处置和预防。
4.2加强锅炉的日常维护和保养工作,定期检查和清洗受热面,及时清理沉积物和结焦物质。
4.3合理调整燃烧工艺,改善供氧条件,降低结焦的可能性。
可以通过优化燃烧系统、调整燃烧器和喷嘴等措施来实现。
五、定期评估和改进5.1结焦处置方案实施后,需要进行效果评估,分析和总结处置效果和存在的问题,针对性地进行改进。
5.2定期召开经验交流会议,邀请专家进行技术指导,提高处置效果和防范能力。
通过以上方案,并结合实际情况,应该能够有效处理锅炉大面积结焦问题,提高锅炉的运行效率和安全性。
需要强调的是,在处置过程中,要确保操作人员的安全,遵守相关操作规程和安全规范,防止发生意外事故。
锅炉结焦原因分析及解决方案

锅炉结焦原因分析及解决方案一、引言锅炉是工业生产中常见的热能转换设备,广泛应用于电力、化工、纺织、食品等行业。
然而,在锅炉运行过程中,经常会出现结焦问题,给生产带来不利影响。
为了解决这一问题,本文将对锅炉结焦原因进行分析,并提出相应的解决方案。
二、锅炉结焦原因分析1. 燃料问题燃料是锅炉运行的重要组成部分,不合适的燃料会导致结焦问题。
例如,燃料中硫含量过高,燃烧时会产生硫酸,进而形成结焦物质。
此外,燃料中灰分含量过高也会增加结焦的可能性。
2. 锅炉设计问题锅炉的设计也是影响结焦的重要因素之一。
例如,过小的燃烧室容积会导致燃烧不完全,产生大量的未燃烧物质,增加结焦的风险。
此外,过小的换热面积也会导致烟气温度过高,进而促使结焦的发生。
3. 操作问题不正确的操作也是导致锅炉结焦的原因之一。
例如,燃烧调节不当,燃烧过程中产生的高温烟气无法充分利用,增加了烟气中未燃烧物质的含量,从而导致结焦。
此外,不定期清理锅炉内部的积灰也会增加结焦的可能性。
4. 水质问题锅炉水质的好坏直接影响着结焦问题。
水中的杂质和硬度物质会在锅炉内部沉积,形成结焦物质。
此外,水中的氧气和二氧化碳也会加速结焦的发生。
三、锅炉结焦解决方案1. 优化燃料选择选择低硫、低灰分的燃料,可以有效降低结焦的风险。
此外,对燃料进行预处理,如除尘、除硫等,也可以减少结焦物质的生成。
2. 改善锅炉设计合理设计锅炉的燃烧室容积和换热面积,确保燃烧充分和烟气温度适宜,可以降低结焦的可能性。
此外,增加锅炉内部的清洁设备,如烟气脱硫装置、除尘器等,也可以有效减少结焦问题。
3. 规范操作流程加强对操作人员的培训,确保燃烧调节的准确性和及时性。
定期检查和清理锅炉内部的积灰,保持锅炉的清洁状态,也是减少结焦的重要措施。
4. 改善水质管理加强对锅炉水质的监测和管理,定期进行水质测试,及时清除水中的杂质和硬度物质。
在需要的情况下,可以使用水处理剂来控制水质,减少结焦问题的发生。
锅炉结焦原因分析及解决方案

锅炉结焦原因分析及解决方案一、问题描述:锅炉结焦是指在锅炉内部烟道、燃烧室或者烟气侧管道上形成的燃烧产物积聚物,会导致锅炉热交换效率下降、烟气温度升高、燃料消耗增加等问题。
本文将对锅炉结焦的原因进行分析,并提出相应的解决方案。
二、原因分析:1. 燃料质量问题:燃料中的灰分和硫分含量高,容易产生结焦物质。
灰分中的无机物质在高温下会形成结焦物质,硫分则会与金属表面发生化学反应,形成硫酸盐结焦物质。
2. 燃烧过程问题:燃烧过程中,燃料燃烧不彻底会产生大量的烟气,其中含有大量的颗粒物和有机物质,这些物质在烟道中会逐渐沉积形成结焦物质。
3. 锅炉设计问题:锅炉内部的烟道设计不合理,烟气流动不畅,容易导致结焦物质的积聚。
此外,锅炉的受热面积不足、传热效果差等问题也会增加结焦的风险。
三、解决方案:1. 燃料选择和处理:选择低灰分、低硫分的燃料,减少结焦物质的生成。
对于高灰分、高硫分的燃料,可以采取预处理措施,如煤粉的洗选、脱硫等,降低结焦物质的含量。
2. 燃烧调整和优化:通过优化燃烧系统,提高燃烧效率,减少燃烧产物的生成。
可以采用先进的燃烧器技术,改善燃烧过程中的混合和燃烧效果,减少燃料残留和烟气中的颗粒物。
3. 清洁和维护:定期对锅炉进行清洗和维护,清除烟道和燃烧室中的结焦物质。
可以采用物理清洗、化学清洗等方法,彻底清除结焦物质,恢复锅炉的正常工作状态。
4. 锅炉设计和改进:对于现有的锅炉,可以通过改进锅炉内部的烟道设计,增加受热面积,改善烟气流动情况,减少结焦物质的积聚。
对于新建的锅炉,应根据实际情况,合理设计燃烧系统和烟道结构,降低结焦的风险。
5. 监测和控制:建立完善的监测和控制系统,及时发现和处理锅炉结焦问题。
可以采用温度、压力、烟气成份等参数的在线监测,实时掌握锅炉的运行情况,及时采取措施防止结焦的发生。
四、总结:锅炉结焦问题对于锅炉的正常运行和热能利用效率有着重要影响。
通过燃料选择和处理、燃烧调整和优化、清洁和维护、锅炉设计和改进以及监测和控制等方面的综合措施,可以有效地解决锅炉结焦问题,提高锅炉的运行效率和可靠性,降低能源消耗。
300MW循环流化床锅炉结焦原因及处理

300MW循环流化床锅炉结焦原因及处理
循环流化床锅炉是一种高效节能的锅炉,广泛应用于电厂、化工厂和制纸厂等工业领域。
在使用过程中,循环流化床锅炉会出现结焦问题,给生产运行带来一定影响。
本文将分析300MW循环流化床锅炉结焦的原因及处理方法。
一、结焦原因
1. 燃料成分不均匀
循环流化床锅炉燃烧的燃料种类繁多,包括煤、煤矸石、生物质颗粒等。
而这些燃料的成分和质量并不一致,导致在燃烧过程中形成不同的灰渣,有些灰渣容易结焦。
2. 燃烧温度不均匀
循环流化床锅炉的燃烧过程中,温度不均匀也是导致结焦的重要原因。
部分区域温度过高或者过低都会导致燃烧产生的灰渣结焦。
3. 燃烧控制不当
在循环流化床锅炉的燃烧过程中,如果燃料投放、空气供给等参数控制不当,容易造成燃烧不完全的情况,导致灰渣结焦。
4. 锅炉运行方式不当
循环流化床锅炉在长时间高负荷运行后,如果未能及时进行清灰和维护保养,也容易导致结焦问题的发生。
二、处理方法
1. 燃料选择
对于循环流化床锅炉来说,选择合适的燃料是预防结焦问题的重要一环。
合理的燃料混合和调节,可以减少结焦的可能性。
2. 控制燃烧温度
在锅炉运行过程中,需要采取控制燃烧温度的措施,确保燃烧温度均匀,防止局部温度过高导致结焦问题。
3. 燃烧控制
加强对锅炉燃烧过程中的参数控制,确保燃料充分燃烧,减少未燃烧残留物产生。
5. 使用解结剂
循环流化床锅炉结焦后,可使用一定的解结剂进行处理,帮助清除结焦物质,恢复锅炉正常燃烧。
火电厂锅炉结焦原因分析及解决方法
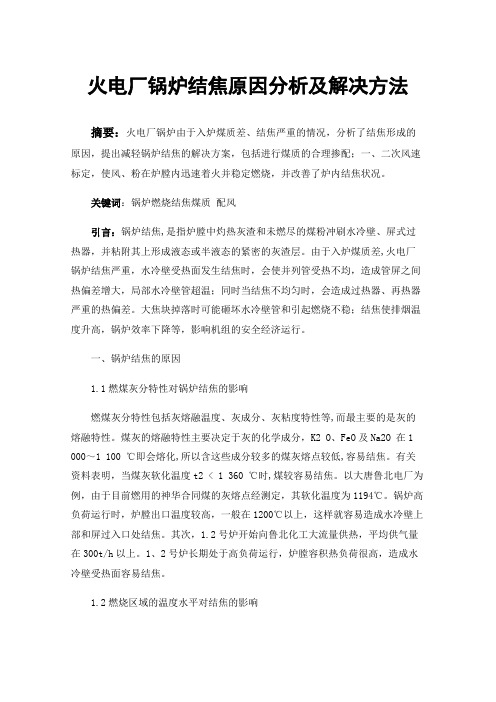
火电厂锅炉结焦原因分析及解决方法摘要:火电厂锅炉由于入炉煤质差、结焦严重的情况,分析了结焦形成的原因,提出减轻锅炉结焦的解决方案,包括进行煤质的合理掺配;一、二次风速标定,使风、粉在炉膛内迅速着火并稳定燃烧,并改善了炉内结焦状况。
关键词:锅炉燃烧结焦煤质配风引言:锅炉结焦,是指炉膛中灼热灰渣和未燃尽的煤粉冲刷水冷壁、屏式过热器,并粘附其上形成液态或半液态的紧密的灰渣层。
由于入炉煤质差,火电厂锅炉结焦严重,水冷壁受热面发生结焦时,会使并列管受热不均,造成管屏之间热偏差增大,局部水冷壁管超温;同时当结焦不均匀时,会造成过热器、再热器严重的热偏差。
大焦块掉落时可能砸坏水冷壁管和引起燃烧不稳;结焦使排烟温度升高,锅炉效率下降等,影响机组的安全经济运行。
一、锅炉结焦的原因1.1燃煤灰分特性对锅炉结焦的影响燃煤灰分特性包括灰熔融温度、灰成分、灰粘度特性等,而最主要的是灰的熔融特性。
煤灰的熔融特性主要决定于灰的化学成分,K2 O、FeO及Na2O 在1 000~1 100 ℃即会熔化,所以含这些成分较多的煤灰熔点较低,容易结焦。
有关资料表明,当煤灰软化温度t2 < 1 360 ℃时,煤较容易结焦。
以大唐鲁北电厂为例,由于目前燃用的神华合同煤的灰熔点经测定,其软化温度为1194℃。
锅炉高负荷运行时,炉膛出口温度较高,一般在1200℃以上,这样就容易造成水冷壁上部和屏过入口处结焦。
其次,1.2号炉开始向鲁北化工大流量供热,平均供气量在300t/h以上。
1、2号炉长期处于高负荷运行,炉膛容积热负荷很高,造成水冷壁受热面容易结焦。
1.2燃烧区域的温度水平对结焦的影响炉膛容积热强度、断面热强度及燃烧器区域热强度数值的大小都会对结焦产生一定的影响。
炉膛容积热强度过大时,由于炉膛容积小,燃烧器区域热强度负荷过高,会使煤粉在燃烧区域释放出来的热量没有足够的受热面来吸收,因此炉膛内温度较高而容易结焦。
若断面热强度过低,则炉膛断面大而高度却不足,烟气到达炉膛出口还未能得到足够冷却,炉膛出口部位受热面就会结焦。
锅炉结焦原因分析及解决方案

锅炉结焦原因分析及解决方案引言概述:锅炉结焦是指在燃烧过程中,锅炉内壁和管道表面积聚了燃烧产物,形成焦炭层,导致热传递效率降低,影响锅炉运行稳定性和安全性。
为了解决锅炉结焦问题,需要深入分析结焦原因,并采取相应的解决方案。
一、燃料质量问题1.1 燃料含灰量高燃料中灰分含量高会导致燃烧后生成的灰渣增多,易形成结焦物质。
1.2 燃料含硫量高燃料中硫含量高容易生成硫酸盐,加剧结焦的程度。
1.3 燃料粒度不均匀燃料粒度不均匀会导致燃烧不充分,产生大量未燃烧残渣,易形成结焦。
二、锅炉操作问题2.1 燃烧调节不当燃烧过程中,燃烧调节不当会导致燃烧不充分,产生过多的未燃烧残渣,加剧结焦。
2.2 进料速度过快进料速度过快会导致燃料在炉膛内停留时间不足,燃烧不充分,易形成结焦。
2.3 管道清洁不及时管道长期未清洁会积聚大量灰渣,形成结焦,影响热传递效率。
三、锅炉设计问题3.1 燃烧系统设计不合理燃烧系统设计不合理会导致燃烧不充分,产生大量未燃烧残渣,易形成结焦。
3.2 管道布局不合理管道布局不合理会导致燃料在管道内停留时间过长,易形成结焦。
3.3 烟气排放不畅烟气排放不畅会导致烟气在锅炉内停留时间过长,易形成结焦。
四、清洁维护问题4.1 清灰不及时清灰不及时会导致灰渣在锅炉内积聚,形成结焦。
4.2 管道清洁不彻底管道清洁不彻底会留下一定量的灰渣,易形成结焦。
4.3 管道维护不到位管道维护不到位会导致管道内积聚大量灰渣,易形成结焦。
五、解决方案5.1 选择优质燃料选择含灰量低、硫含量低的优质燃料,减少结焦的可能性。
5.2 加强操作管理加强燃烧调节,控制进料速度,定期清洁管道,确保锅炉正常运行。
5.3 定期维护清洁定期清理灰渣,彻底清洁管道,保持锅炉清洁,防止结焦的发生。
结语:通过对锅炉结焦原因分析及解决方案的详细探讨,可以有效避免锅炉结焦问题的发生,保障锅炉的正常运行,提高锅炉的热效率和安全性。
在实际操作中,应根据具体情况采取相应的措施,及时解决问题,确保锅炉长期稳定运行。
锅炉结焦处理方案
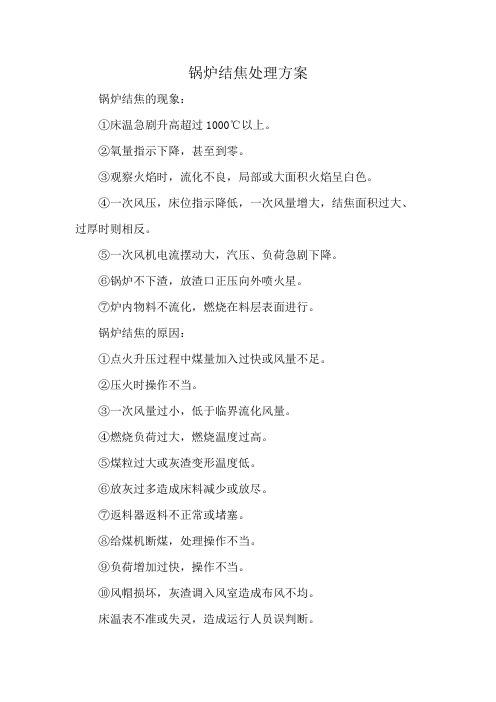
锅炉结焦处理方案锅炉结焦的现象:①床温急剧升高超过1000℃以上。
②氧量指示下降,甚至到零。
③观察火焰时,流化不良,局部或大面积火焰呈白色。
④一次风压,床位指示降低,一次风量增大,结焦面积过大、过厚时则相反。
⑤一次风机电流摆动大,汽压、负荷急剧下降。
⑥锅炉不下渣,放渣口正压向外喷火星。
⑦炉内物料不流化,燃烧在料层表面进行。
锅炉结焦的原因:①点火升压过程中煤量加入过快或风量不足。
②压火时操作不当。
③一次风量过小,低于临界流化风量。
④燃烧负荷过大,燃烧温度过高。
⑤煤粒过大或灰渣变形温度低。
⑥放灰过多造成床料减少或放尽。
⑦返料器返料不正常或堵塞。
⑧给煤机断煤,处理操作不当。
⑨负荷增加过快,操作不当。
⑩风帽损坏,灰渣调入风室造成布风不均。
床温表不准或失灵,造成运行人员误判断。
床料太厚,没有及时排渣。
除铁器分离不好,铁件进入炉内造成沸腾不好。
锅炉结焦的处理:①发现锅炉有局部结焦现象,放渣口不下渣时,可适当提高一次风压,并及时连续捅渣,直到下渣正常为止。
②如煤质配比不当,应汇报值长,并在上煤时改变煤配比,可适当降低负荷运行。
③大面积结焦时应请示值长,尽快停炉,继续保持一次风机、引风机运行,冷却料层与焦块。
请示值长尽快启动备用炉。
④在事故处理过程中应严格监视锅炉循环水量、供水温度和压力正常。
结焦预防:①控制入炉煤粒度在8mm以下。
②升降负荷时,严格做到升负荷先加风后加煤,减负荷先减煤后减风。
③燃烧调节时要做到少量多次的调节方法,避免床温大起大落。
④经常检查给煤情况,观察炉床火焰颜色,返料器是否正常。
⑤排渣时根据料层压差及时少放勤放。
⑥排渣结束后认真检查,确认排渣门关闭严密后,方可离开现场。
- 1、下载文档前请自行甄别文档内容的完整性,平台不提供额外的编辑、内容补充、找答案等附加服务。
- 2、"仅部分预览"的文档,不可在线预览部分如存在完整性等问题,可反馈申请退款(可完整预览的文档不适用该条件!)。
- 3、如文档侵犯您的权益,请联系客服反馈,我们会尽快为您处理(人工客服工作时间:9:00-18:30)。
锅炉结焦解决方法
锅炉结焦的情况分析
一熔渣
水冷壁及其它辐射受热面上的积灰主要是熔渣。
燃料灰中含有易熔的碱性金属氧化物和硫酸盐,在高温下发生升华或形成易熔的共晶体,遇到较冷的受热面管壁即冷凝下来形成内灰层。
其外表温度随灰厚度的增加而不断增加,使灰层达到熔化状态,覆盖在管壁且具有粘性,进一步捕捉飞灰而不断加厚,这种熔渣的一个重要特点是它能够随时间无限增长。
二高温积灰
在高温烟气环境中飞灰沉积在管束外表面的现象叫高温积灰。
过热器与在热器管外的积灰既属于高温积灰。
煤灰根据其易熔程度可分为三部分。
底熔灰主要是金属氯化物和硫化物(NACL,NA2SO4,MGCL2,AL(SO4)3)等他们的熔点大都在700--800ºC。
中熔灰的主要成分是FES,NA2SIO3,K2SO4等,熔点900-1100 ºC。
高熔灰是由纯氧化物(SIO2,AL2O3,CAO,MGO,FE2O3)等组成,熔点1600-2800 ºC
高熔灰的熔点超过了炉膛火焰区的温度,当它通过燃烧区时不发生状态变化。
高温过热器与再热器布置在烟温高于700--800 ºC的烟道里,管子的外表面积灰由两部分组成,内层灰紧密,与管子黏结牢固,不容易清除,外灰层松散,容易清除。
低熔灰在炉膛内高温烟气区已成为气态,随烟气流向烟道。
由于高温过热器和再热器区域的烟温较高,低熔灰若不接触温度较低的受热面则不会凝固,若接触到温度较低的受热面就回凝固在受热面上,形成黏性灰层。
灰层形成后,表面温度随灰层厚度的增加而增加。
此后,一些中熔,高熔灰粒也被黏附在黏性灰层中。
这种积灰在高温烟气中的氧化硫气体的长期作用下形成白色的硫酸盐密实灰层,这个过程称为烧结。
随的灰层厚度的增加,起外表面温度继续升高,低熔灰的黏结结束。
但是中熔灰和高熔灰在密实灰层表面还进行着动态沉积,形成松散而且多孔的外层灰。
三松散灰
松散灰是物理沉积,灰粒之间呈松散状态。
在烟气温度低于600-700ºC的烟道内,低温受热面管子表面形成的积会为松散灰。
四粘结灰
由于燃料中含有燃料硫,燃料燃烧后总有一部分会形成SO3,并和烟气中的水蒸气形成
硫酸蒸气。
硫酸蒸气能在较高温度下冷凝,使烟气露点温度升高。
当硫酸蒸气流经受热面时,如果金属壁温低于烟气露点,则硫酸蒸气就在管壁冷凝下来,当烟气流过时,硫酸溶液就吸附灰粒子与灰中钙的氧化物进行化学反应生成CASO4粘在管壁上,形成了一硫酸钙为基质的低温粘结灰。
低温粘结灰呈硬结状,不易清除,也会无限增长,甚至会产生堵灰,电站锅炉中常在空气预热器中发生,而工业锅炉中常发生在省煤器中,尤其是铸铁式省煤器中。
(注:烟气露点温度指硫酸蒸气冷凝时的温度。
)尾部受热面的积灰包括松散灰和低温粘结灰两种。
影响结焦的因素
一煤粉灰分的特性
目前判断燃煤锅炉燃烧过程中是否发生结渣的一个重要依据是灰的熔融性,通常将灰的软化温度ST做为衡量是否发生结渣的主要指标。
不同的燃料的灰分具有不同的成分和熔融性,灰熔点较低的煤(ST<1200ºC)易结渣。
评价灰的结渣性能除用灰的熔融性说明外,还必须引用其他一些指标。
1 SIO2比简称硅比硅比=SIO2/(SIO2+FE2O3+CAO+MGO)×100
式中的几种氧化物是指它们在灰中的重量百分比。
硅比反映燃煤结渣趋势和对不同煤种进行比较的一个简单的指标。
硅比越大灰渣黏度越高,越不易结渣,一般硅比大于72时灰渣不易发生结渣,当硅比小于65就严重结渣。
通常把SIO2含量高的渣称为酸性渣,含量低的称为碱性渣,酸性渣的灰熔点和黏度都是比较高的,因而不发生结渣。
2灰分中的碱性和酸性氧化物含量比叫灰的酸碱比
酸碱比=(FE2O3+CAO+MGO+NA2O+K2O)/(SIO2+AL2O3+TIO2)
式中分子的碱性氧化物都是提高灰的流动性的,而分母中的酸性氧化物都是增加灰的黏滞性的,由此可知酸碱比越小的煤越不易发生结渣,对固态排渣煤粉炉使用的煤,为防止结渣,灰的酸碱比应尽可能低于0。
5。
燃煤灰分特点对结渣的影响是一个十分复杂的问题,目前还没有一个世界公认的评价结渣性能的方法。
它不仅与灰中各组分的含量有关,还与各组分的物理化学性质、相互之间的作用和锅炉的运行工况(如炉内的介质的气氛)等因素有关。
二炉内空气动力特性
炉膛内的烟气温度以及水冷壁附近的温度工况和介质气氛等都与炉内动力特性密切相关。
正常运行工况下,高温的火焰中心应位于炉膛断面的几何中心,实际运行中,一次风速偏低,气流刚性差,燃烧器周围容易结渣;一次风管风量分布不均容易造成炉膛火焰偏斜,炉膛火焰中心向风量小的一角倾斜,使其周围结渣。
另外二次风速低,刚性弱对一次风的保护能力降低,一次风容易贴壁,使一次风在着火早期得不到足够的氧气而产生还原性气氛,造成炉内结渣。
(例如,用FE2O3较高的煤时,在没有充分氧气的情况下,C不完全燃烧生成CO,而CO有还原性,则高熔点的FE2O3被CO还原成FEO,而FEO与SIO2等进一步形成
熔点更低的共晶体,有时候会使灰的熔点下降150-300ºC)。
或是当四角燃烧器喷口喷气的角度调试不当时也造成结渣。
当采用摆动式燃烧器向下摆动调节气温时,如下排燃烧器距冷灰斗转弯处较近,易造成冷灰斗结渣。
(注:一次风为含煤粉和空气的风叫一次风。
二次风则就是空气,作用是为了提供氧气,使煤充分燃烧。
)
三炉膛的设计特性
炉膛容积热负荷QV,断面热负荷QA和让燃烧区域热负荷QR数值的大小都会对结渣产生一定的影响。
当锅炉设计时炉膛热负荷取得过大,或实际运行时炉膛热负荷过高,都会提高炉膛或局部区域的温度水平,使结渣的可能性增大。
四锅炉运行负荷
锅炉负荷升高时,炉内温度也相应升高,结渣的可能性增大。
结渣的危害
1受热面结渣以后,会使传热热阻增加,传热减弱,工质吸收热量减少,锅炉排烟温度升高,排烟热损失增加,锅炉效率下降。
为保持锅炉的正常运行,在增加燃料量的同时必须相应的加大风量,这就使送、引风机负荷增加,厂用电增加,因此,结渣使锅炉运行的经济性明显降低。
2受热面结渣时,问保持锅炉的正常运行,必须增大风量。
若通风设备容量有限,加上结渣容易使烟气通道局部堵塞,烟气阻力增加,风机风量难于加大,锅炉只好被迫降负荷运行。
3锅炉受热面结渣后,炉膛出口烟温升高,导致过热气温升高,加之结渣造成的热偏差,易引起过热器超温损坏。
这时为了维持过热气温和保护再热器,运动中也需要限制锅炉负荷。
4燃烧器喷口结渣,改变了燃烧器出口气流结构,从而使炉内空气动力工况受到破坏,影响燃烧过程的进行。
喷口结渣严重而被堵塞时,锅炉只好降负荷运行,或是被迫停炉。
5水冷壁结渣,会使其个部分受热不均,对自然循环锅炉的水循环安全性和控制流动锅炉水冷壁的热偏差带来不利影响,可能导致水冷壁管破坏。
6炉膛上部结的焦块掉落时可能会砸坏冷灰斗的冷壁管。
7冷灰斗处结渣严重时,会使冷会斗出口居间堵塞,无法排渣,锅炉无法继续运行。
总之,结渣不但增加了锅炉运行维护和检修的工作量,严重危及锅炉安全经济运行,还可能迫使锅炉降低负荷运行甚至被迫停炉,结渣本身是一个复杂的物理化学过程同时还有自动加剧的特点,一旦发生,由于渣层的热阻使传热恶化,炉内咽气温度和渣层表面温度都将升高,加之渣层表面粗糙,渣粒更容易黏附上去,结果结渣过程会愈演愈烈,所以应尽最大努力来减轻或防止锅炉结渣。
锅炉结焦解决方法
3U高效液态锅炉除焦技术可有效解决锅炉因结焦带来的安全问题!
1、改变焦渣特性,使焦块变的疏松,焦渣呈粉末状,避免因掉大焦块造成的非正
常停车次数;
2、显着改善捞渣系统工作强度,降低维护保养要求;
3、可快速清除锅炉各受热面焦渣,防止因管壁结焦造成的爆管现象;
4、减缓SO3和硫酸腐蚀,延长设备使用寿命,降低生产成本;
5、免除人工打焦,减少员工工作强度;便于集控人员调整锅炉运行参数。
6、在燃煤供应日趋严峻的情况下,可以拓展电站锅炉燃用煤种范围,增加燃料的
灵活性,额外节约生产成本。
7、电站锅炉可掺烧低价、廉价劣质煤,节约生产成本;
8、电站锅炉还可掺烧高热量优质煤种提高锅炉负荷,增加发电量;
9、有效提升锅炉效率,加强热交换,降低发电煤耗,节约燃煤;
10、减少锅炉吹灰次数,降低排烟温度和减温水使用量。
11、可减少S、N氧化物的大气排放量;
12、促进燃料完全燃烧,降低灰渣中含碳量,减少废渣排放量;
13、降低烟气林克曼黑度;
14、降低烟尘排放量。
本产品为弱酸性淡蓝色液体,是目前市场上技术最为领先的高节能、环保产品,对锅炉受热面无任何腐蚀。
本产品使用量仅为燃料之1~3ppm,而市场上粉状
除焦产品的用量为燃料的0.01%~0.02%,相比之下本剂使用量仅为固态除焦剂的
十二分之一,费用仅为固态除焦剂的60%,且3U液态锅炉除焦剂的效果远非固态
除焦剂可比。