切削用量对切削力的影响比较分析
切削用量三要素对切削力的影响规律
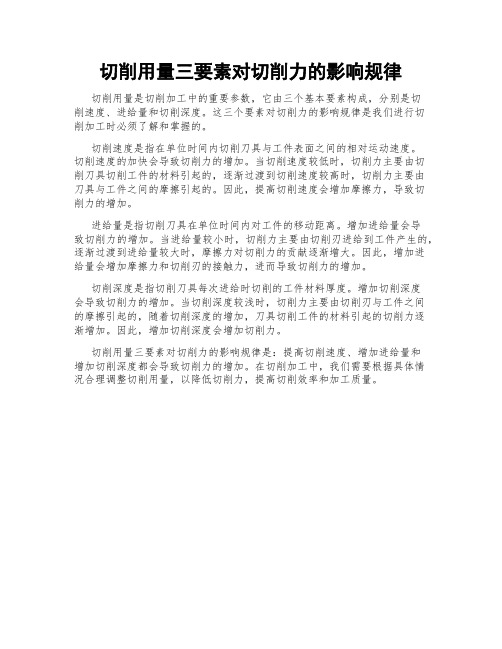
切削用量三要素对切削力的影响规律
切削用量是切削加工中的重要参数,它由三个基本要素构成,分别是切
削速度、进给量和切削深度。
这三个要素对切削力的影响规律是我们进行切
削加工时必须了解和掌握的。
切削速度是指在单位时间内切削刀具与工件表面之间的相对运动速度。
切削速度的加快会导致切削力的增加。
当切削速度较低时,切削力主要由切
削刀具切削工件的材料引起的,逐渐过渡到切削速度较高时,切削力主要由
刀具与工件之间的摩擦引起的。
因此,提高切削速度会增加摩擦力,导致切
削力的增加。
进给量是指切削刀具在单位时间内对工件的移动距离。
增加进给量会导
致切削力的增加。
当进给量较小时,切削力主要由切削刃进给到工件产生的,逐渐过渡到进给量较大时,摩擦力对切削力的贡献逐渐增大。
因此,增加进
给量会增加摩擦力和切削刃的接触力,进而导致切削力的增加。
切削深度是指切削刀具每次进给时切削的工件材料厚度。
增加切削深度
会导致切削力的增加。
当切削深度较浅时,切削力主要由切削刃与工件之间
的摩擦引起的,随着切削深度的增加,刀具切削工件的材料引起的切削力逐
渐增加。
因此,增加切削深度会增加切削力。
切削用量三要素对切削力的影响规律是:提高切削速度、增加进给量和
增加切削深度都会导致切削力的增加。
在切削加工中,我们需要根据具体情
况合理调整切削用量,以降低切削力,提高切削效率和加工质量。
切削用量对切削力的影响比较讲解

]3[切削用量对切削力的影响比较(陕西理工学院 机械工程学院 )摘 要:通过分析切削力单因素实验,探讨切削用量对切削力的影响规律;同时讨论刀具几何参数对切削力的影响,得出一般结论;进而对比说明精密切削切削力的特殊规律。
关键词:切削变形;切削力;刀具;精密切削;规律1.引言金属机械加工过程中,产生的切削力直接影响工件的粗糙度和加工精度,同时也是确定切削用量的基本参数。
所以掌握切削用量对切削力的影响规律也显得重要。
本文从一般切削和精密切削两个方面对切削用量对切削力的影响规律做初步探讨。
2.金属切削加工机理金属切削加工是机械制造业中最基本的加工方法之一。
金属切削加工是指在金属切削机床上使用金属切削刀具从工件表面上切除多余金属,从而获得在形状、尺寸精度及表面质量等方面都符合预定要求的加工。
2.1切削加工原理利用刀具与工件之间的相对运动,在材料表面产生剪切变形、摩擦挤压和滑移变形,进而形成切屑。
2.2切削变形根据金属切削实验中切削层的变形,如图1-2,可以将切削刃作用部位的切削层划分为3个变形区。
第Ⅰ变形区:剪切滑移区。
该变 形区包括三个过程,分别是切削层弹 性变形、塑性变形、成为切屑。
第Ⅱ变形区:前刀面挤压摩擦区。
该变形区的金属层受到高温高压作用, 使靠近刀具前面处的金属纤维化。
第Ⅲ变形区:后刀面挤压摩擦区。
该变形区造成工件表层金属纤维化与图1-2 切削层的变形区 加工硬化,并产生残余应力。
F xF y F z F xy F Z F22222++=+=]1[3.切削力切削力是指切削过程中作用在刀具或工件上的力,它是工件材料抵抗刀具切削所产生的阻力。
3.1切削力来源根据切削变形的不同,切削过程中刀具会受到三种力的作用,即: (1)克服切削层弹性变形的抗力 (2)克服切削层塑性变形的抗力(3)克服切屑对刀具前面、工件对刀具后面的摩擦力3.2切削力的合成与分解图2 - 2 切削力合力和分力 图2-2为车削外圆时切削力的合力与分力示意图。
试论切削用量对车削加工的影响

试论切削用量对车削加工的影响作者:苏利晓来源:《科技风》2017年第21期摘要:在机械加工中,切削用量对切削中所出现的物理现象有着非常重要的影响。
本文主要对切削量变化在车削加工中的影响进行了仔细的分析和研究,以帮助工作人员对切削量做到真确的判断。
选择适当的切削量,可以提升零件的加工质量,对其起到很好的保护作用。
关键词:切削用量;车削;加工;影响作为一个合格的车工人员,它必须要对切削用量的三要素烂熟于心。
比如切削力、切削热、积屑瘤、加工阶段的划分等相关内容,然后进行仔细分析。
工作人员需要在长期的工作中才能对三要素做到很好的总结和掌握。
通过这项技术能力的掌握,可以提高车工人员的工作质量。
一、切削用量的三要素二、切削用量对车削加工的影响在对工件进行切削工作时,工件会发生弹性变形和塑性变形,这种变形会产生抗力、而且在切削加工中,还会产生摩擦力,这些力的统称为切削阻力。
切削用量对切削力主要的影响有如下几点:(一)切削加工时的进给量在一般车削时,当进给量f确定时,切削力会随着切削深度的增加而增加;当切削深度一定时,切削力会随着进给量的增加而增加,相关的比例大约是1:8。
切削速度。
在车床刀具切削塑性金属时,无论车床是运行的速度如何,切削力都是会因为其运转速度的增加而增加。
这主要是因为当车床的运转速度变快,切削速度加快,在这样的做功中,会产生大量的热量,而在这其中摩擦力会不断的减小,最终切削力也会因此而降低。
在进行切削工作中,切削材质不同,切削力受到的影响也会存在差异。
比如在切削脆性金属时,切削速度就不会对其造成严重的影响。
通过这样的分析,可以总结中对切削力影响从小到大的因素是切削速度、进给量和切削深度。
在实际的零件加工中,可以根据零件的实际情况和具体因素,适当的调整切削用量。
(二)切削加工时温度的影响在对两件进行切削加工时,会出现切削热量,这主要是因为车床在运转时,切削金属和工件之间摩擦变形而形成的一种热量。
车削加工切削用量选择分析

车削加工切削用量选择分析在长期车削加工实践中,有经验的车工老师会在开车切削前,对照着零件图样先考虑开几转车速,吃刀多少深,选择多少走刀量。
这不仅体现了切削用量的重要性,更直接关系到如何充分发挥车刀、机床的潜力来提高实际的生产效率。
因此在车削加工前一定要合理的选择切削用量。
一、切削用量对切削的影响在车削加工中,始终存在着切削速度、吃刀深度和走刀量这三个切削要素,在有条件增大切削用量时,增加切削速度、吃刀深度和走刀量,都能达到提高生产效率的目的,但它们对切削的影响却各有不同。
1. 切削速度对切削的影响所谓切削速度,实质上是指切屑变形的速度,其高低决定着切削温度的高低,影响着切削变形的大小,而且直接决定着切削热的多少。
当车削碳钢、不锈钢以及铝和铝合金等塑性金属材料达到一定的切削温度时,切削底层金属将粘附在车刀的刀刃上面形成积屑瘤。
由于积屑瘤的存在,将会增大车刀的实际前角,对切削力、车刀的磨损以及工件加工质量会产生较大影响。
(1)切削速度对切削力的影响。
一般来说,提高切削速度,切屑变形小,切削力也就相应降低。
对于碳钢等塑性金属材料,在用硬质合金车刀车削碳钢工件时(前角γ=0°),开始切削速度小,切削力大,但随着切削速度的提高,形成积屑瘤后会增大车刀的实际前角,使切屑变形减小,导致切削力下降。
积屑瘤在刀刃上的堆积高度越高,即车刀实际前角增加得越多,切削变形与切削力也就越小。
但当切削速度超过一定范围时(≥20m/min),随着切削速度的提高,积屑瘤高度将会逐渐减小,直至完全消失,车刀的实际前角也随之逐渐减小,直至回复原来大小,这时切削变形与切削力又将逐渐增大。
当切削速度再继续提高时(≥50m/min),由于切削温度甚高,切屑与车刀前面接触的一层表皮开始微熔,起了一种特殊的润滑作用,减少了摩擦,而且因被切层变形不够充分,使切屑变形减小,切削力得到了再次降低。
此后切削力的变化逐渐趋于稳定。
对于不同的工件材料以及不同的车刀前角值,切削速度与切削力之间的变化规律大致如此,但各个变化阶段的速度范围则会不尽相同。
切削力及其影响因素

yF f nF f
f
Ff p
c
Ff
(2)切削层单位面积切削力经验公式
切削层单位面积切削力p是指切除单位切削 层面积所产生的主切削力,其计算公式为:
p Fc Fc Fc AD ap f hDbD
由上式可得,主切削力Fc的计算公式:
Fc pap f phDbD
上页式中,p是指f=0.3mm/r时的单位切削力, 硬质合金外圆车刀车削常用金属的单位切削力如 下表所示。
2.切削用量
(1)背吃刀量ap和进给量f
背吃刀量ap和进给量f通过对切削宽度bD和切 削厚度hD的影响而影响切削力Fr,如下图所示。
如上页左图所示,背吃刀量ap增大,切削宽 度bD增大,切削面积AD和切屑与前刀面的接触面 积按比例增大。由于进给量f不变,所以单位切削
力p不变。因此,当背吃刀量ap增大一倍时,主切 削力Fc成比例增大,背向力Fp和进给力Ff也近似 成比例增大。
机械制造技术
切削力及其影响因素
一、切削力
切削力是指金属切削时,刀具切入工件使被 加工材料发生变形并成为切屑所需的力。
1.切削力的来源
切削力的来源主要有以下两方面: ① 克服被加工材料对弹性变形和塑性变形的抗 力。 ② 克服刀具与切屑、工件表面间的摩擦阻力所 需的力。 这些力的合力形成了作用在刀具上的切削力Fr。
Pc Fcvc 10 3
三、影响切削力的因素
1.工件材料
工件材料的硬度、强度越高,剪切屈服强度越 大,切削力Fr越大。
硬度、强度相近的材料,塑性或韧性越好,切 屑越不易折断,切屑与前刀面的摩擦越加,切削力 Fr越大。
切削铸铁等脆性材料时,由于塑性变形小,崩 碎切屑与前刀面摩擦小,切削力Fr较小。
铣削加工中切削参数对切削力的影响
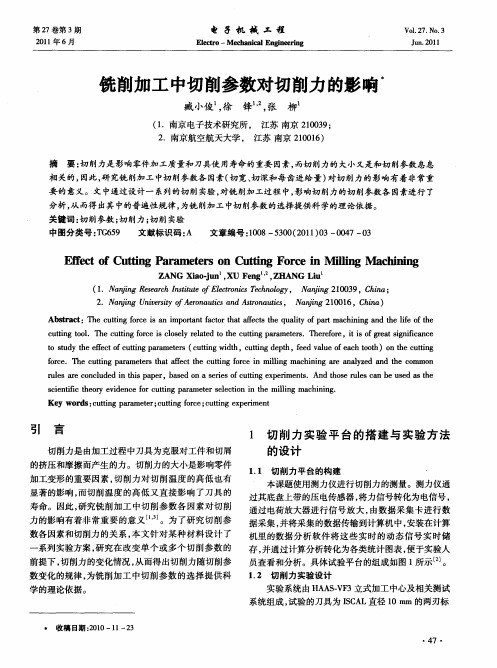
宽增 大 而增 大 。
,一~
。
在单因素试验过程 中, 主要考虑影响切削力 的 3 个主要 因素 : 切宽 a, 。切深 口 和每齿进给量 。首先 。 进行了 3 组单因素对切削力 的影 响的实验 , 即只改变 切宽 口 , 。切深 0 和每齿进给量 中的一个 因素 , 。 研究 切削力随这个因素的变化规律。 12 2 双 因素 实验 设 计 .. 金属去除率是衡量切削效率的重要指标 , 为了研 究在金属去除率不变 的情况下 , 切削参数各因数对切 削力的影响 , 设计了如下的实验 : 在保持金属去除率不 变的前提下 , 研究只改变切宽 凸 , 切深 口 和每齿进给 。 量 中的两个因素 , 研究切削力随这两个 因素的变化
规律 。
霹 / l // 囝 } 厂 /
6 0
,
. .
/ /
2 } . P — — — —。—一 0 ’
切宽 , m m
2 切 削 参数 各 因数 对切 削 力 的影 响 实 验 结果 分 析
2 1 单 因素 实验 结 果分 析 .
2 1 1 切 削力 随切 深 的变化规 律 分析 ..
实验结果如 图 3 所示 , 切削力随切宽 口 增大的变 。
化不是很明显。当切削宽度达 到一定大小后 , 切削力 趋于一个稳定值。切削宽度的增大使变形 系数减少 , 摩擦系数也减少 , 相应 的切削力也随之减少 , 但由于切 宽的增大有可能使 同时工作的齿数增多, 相应的铣 刀 切削力增大 , 正反两方面的作用使切削力不一定随切
切削用量_切削用量三要素

切削用量_切削用量三要素切削用量是指在进行机械切削加工过程中,所使用的切削刀具所需要的切削用油液、气体或冷却液等的量。
在切削加工过程中,切削用量的大小直接影响着切削刀具的稳定性、加工质量和寿命等因素。
切削用量的三要素是切削速度、切削深度和进给量。
切削速度是指切削面上单位时间内被剪切掉的金属的长度,也是切削加工中最重要的参数之一、切削速度的大小主要取决于切削材料的硬度、切削刀具的材料、刀具的热处理状态和润滑条件等。
通常情况下,切削速度越高,切削加工的效率越高,但是过高的切削速度对刀具的负荷也会增大,容易引起刀具的磨损和断裂。
切削深度是指刀具在切削过程中每次进给时切削面上被去除的金属层的厚度。
切削深度的大小直接影响着刀具的负荷和切削过程中的金属去除率。
通常情况下,切削深度越大,切削加工的效率越高,但是刀具的负荷也会相应增大,容易引起刀具的振动和断裂。
进给量是指在单位时间内给进工件的移动量。
进给量的大小直接影响着切削加工过程中的切削速度和切削深度。
进给量过大会导致切削过程中切削力的增大,刀具负荷加大,加工表面质量变差;而进给量过小会降低切削加工的效率。
因此,选择合适的进给量对于保证切削加工的效率和加工质量是非常重要的。
在选择切削用量时,需要综合考虑以上三个要素的关系,根据具体的加工要求和切削刀具的特性来确定。
一般而言,切削速度可以根据切削刀具的材料和润滑条件等来确定,切削深度可以根据加工方案和工件的要求来确定,而进给量可以根据切削力和加工表面质量等因素来确定。
另外,切削用量的选择还需要考虑切削刀具的冷却和润滑效果。
切削加工过程中,由于切削热的产生,切削刀具和工件表面温度会升高,如果不能及时散热降温,将会影响刀具的寿命和加工质量。
因此,选择合适的冷却液和润滑液以及合适的切削用量对于保证切削加工的稳定性和质量也是非常重要的。
总之,切削用量的选择是机械切削加工中非常重要的一环,直接影响着切削刀具的稳定性、加工质量和寿命等因素。
影响刀具切削力的因素
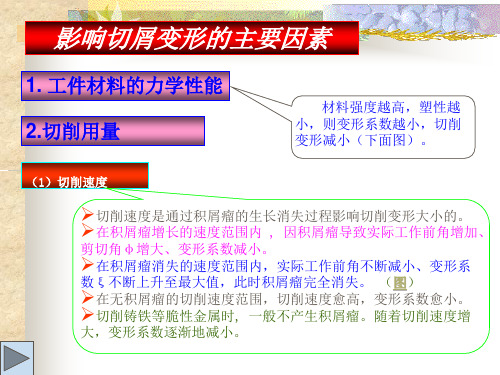
1. 工件材料的力学性能 2.切削用量
(1)切削速度
材料强度越高,塑性越 小,则变形系数越小,切削 变形减小(下面图)。
切削速度是通过积屑瘤的生长消失过程影响切削变形大小的。 在积屑瘤增长的速度范围内 , 因积屑瘤导致实际工作前角增加、
剪切角φ 增大、变形系数减小。 在积屑瘤消失的速度范围内,实际工作前角不断减小、变形系 数ξ 不断上升至最大值,此时积屑瘤完全消失。 (图) 在无积屑瘤的切削速度范围,切削速度愈高,变形系数愈小。 切削铸铁等脆性金属时, 一般不产生积屑瘤。随着切削速度增 大,变形系数逐渐地减小。
b. 切削速度 加工塑性材料时,如下图所示 加工脆性材料时,因塑性变形小,摩擦小,所以影响小.
(三)刀具几何参数对切削力的影响(具体分析见后面的 各页PPT)
1、 前角: γο↑ → Fz↓
2、负倒棱: (负倒棱/进给量) bγ/f ↑ → F↑ 3、主偏角 : κγ↑→Fy/Fz↓,Fx/Fz↑ 4 、刃倾角 :λs变化→合力F的方向,λs↓→Fy↑,Fx↓,Fz基本不变
• 1)主偏角kr对切削力Fc的影响较小,影响程度 不超过10%。主偏角kr在60°~75°之间时,切 削力Fc最小。因为还要考虑刀尖圆弧的影响 • 2)主偏角kr对背向力Fp和进给力Ff的影响较大。
• 式中:FD--切削合力F在基面内的分力。 • 可见Fp随kr的增大而减小,Ff则随kr的增大而 增大。
高的强度和硬度,所以切削这种类型的材料时,切削温度比切削其他材料要高得多。
(4)脆性金属的抗拉强度和延伸率都较小,切削过程中切削区的塑性变形很小,切屑 呈崩碎状或脆性带状,与前刀面的摩擦也较小,所以产生的切削热较少,切削温度一
般比切削钢料时低,同切削45钢相比较,切削灰铸铁HT20-40时的切削温度大约低
- 1、下载文档前请自行甄别文档内容的完整性,平台不提供额外的编辑、内容补充、找答案等附加服务。
- 2、"仅部分预览"的文档,不可在线预览部分如存在完整性等问题,可反馈申请退款(可完整预览的文档不适用该条件!)。
- 3、如文档侵犯您的权益,请联系客服反馈,我们会尽快为您处理(人工客服工作时间:9:00-18:30)。
]3[切削用量对切削力的影响比较(陕西理工学院 机械工程学院 )摘 要:通过分析切削力单因素实验,探讨切削用量对切削力的影响规律;同时讨论刀具几何参数对切削力的影响,得出一般结论;进而对比说明精密切削切削力的特殊规律。
关键词:切削变形;切削力;刀具;精密切削;规律1.引言金属机械加工过程中,产生的切削力直接影响工件的粗糙度和加工精度,同时也是确定切削用量的基本参数。
所以掌握切削用量对切削力的影响规律也显得重要。
本文从一般切削和精密切削两个方面对切削用量对切削力的影响规律做初步探讨。
2.金属切削加工机理金属切削加工是机械制造业中最基本的加工方法之一。
金属切削加工是指在金属切削机床上使用金属切削刀具从工件表面上切除多余金属,从而获得在形状、尺寸精度及表面质量等方面都符合预定要求的加工。
2.1切削加工原理利用刀具与工件之间的相对运动,在材料表面产生剪切变形、摩擦挤压和滑移变形,进而形成切屑。
2.2切削变形根据金属切削实验中切削层的变形,如图1-2,可以将切削刃作用部位的切削层划分为3个变形区。
第Ⅰ变形区:剪切滑移区。
该变 形区包括三个过程,分别是切削层弹 性变形、塑性变形、成为切屑。
第Ⅱ变形区:前刀面挤压摩擦区。
该变形区的金属层受到高温高压作用, 使靠近刀具前面处的金属纤维化。
第Ⅲ变形区:后刀面挤压摩擦区。
该变形区造成工件表层金属纤维化与图1-2 切削层的变形区 加工硬化,并产生残余应力。
F xF y F z F xy F Z F22222++=+=]1[3.切削力切削力是指切削过程中作用在刀具或工件上的力,它是工件材料抵抗刀具切削所产生的阻力。
3.1切削力来源根据切削变形的不同,切削过程中刀具会受到三种力的作用,即: (1)克服切削层弹性变形的抗力 (2)克服切削层塑性变形的抗力(3)克服切屑对刀具前面、工件对刀具后面的摩擦力3.2切削力的合成与分解图2 - 2 切削力合力和分力 图2-2为车削外圆时切削力的合力与分力示意图。
图中字母分别表示: N 1、F 1——作用在车刀前刀面的正压力、摩擦力 N 2、F 2——作用在车刀后刀面的正压力、摩擦力 Q 1、Q 2——N1与F 1、N 2与F 2的合力 F ——Q 1与Q 2的合力,即总切削力一般地,为了研究方便,将总切削力F 按实际运动效果分为以下三个分力:切削力F z ——垂直于水平面,与切削速度的方向一致,且该分力最大。
径向切削力F y ——在基面内,与进给方向垂直,沿切削深度方向,不做功,但能使工件变形或造成振动。
轴向切削力F x ——在基面内,与进给方向平行。
由图2-2可知,合力与各分力之间的关系为: 其中: k r F xy F x sin =。
式中:F xy ——合力在基面上的分力。
k r F xy F y cos=]6[3.3切削力的测定实验——单因素实验法在切削过程中,影响切削力的因素很多,主要有工件材料、切削用量、刀具几何参数等。
单因素实验法就是只改变一个因素,固定其它因素不变,进行试验;如此测得多组数据。
最后综合考虑实验数据,得出包含多个可变因素的切削力实验公式。
以下是我搜集的部分实验数据处理后的关系曲线,如图2-3-1。
从曲线中,可以得出结论:(1)背吃刀量a p 增大,切削力F z 增大(2)进给量f 增大,切削力F z 增大(3)不同的切削速度范围,切削力变化不同 (4)a p 与F z 和f 与F z 成某种函数关系图2-3-1 切削三要素对切削力的影响曲线为了了解a p 、f 、v 与F z可能成的函数关系,我们搜集了切削力单因素实验]4[]4[]4[的部分原始数据,如下表所示。
根据表中数据,利用MATLAB 编程可作出对应的散点图和曲线图,如图2-3-2所示。
观察曲线图,猜测a p 、f 、v 与F z 可能成指数函数关系或一次函数关系。
表1-1 f=0.2mm ,v=100m/min 实验 f(mm) v(m/min)a p (mm)F z (kN)10.2100 0.5 0.023 2 1.0 0.043 3 1.5 0.063 4 2.0 0.082 5 2.5 0.101 6 3.0 0.119 73.50.137表1-2 a p =1mm ,v=100m/min 实验 a p (mm)v(m/min)f(mm) F z (kN)111000.1 0.346 2 0.2 0.562 3 0.3 0.746 4 0.4 0.912 5 0.5 1.067 6 0.6 1.212 70.71.351表1-3 a p =1mm ,f=100mm 实验 a p (mm)f(mm) V(m/min) F z (kN)110.225 0.061 2 50 0.055 3 75 0.052 4 100 0.049 5 125 0.048 6 150 0.046 71750.045图3-2-2 实验散点图和曲线图数据分析:(以a p 与F z 为例)假设a p 与F z 成指数函数关系,即:a x p k F z 11= 为了便于计算,对上式两边同时取对数,可得:k a p x F z 1lg lg 1lg +=对比一次函数y=kx+b ,lg F z 与lg a p 成一次函数关系。
同理: f x k F z 22= k f x F z 2lg lg 2lg += v x k F z 33= k v x F z 3lg lg 3lg +=为了验证假设,依据②式,我先对原始数据取对数,再在对数坐标系中分别作出a p 、f 、v 与F z 的散点图和曲线图;为了验证该曲线为一次函数,分别在曲线上各取四点,两两求斜率,若对应斜率之差的绝对值近似为0(在误差允许范围内),则可认为该曲线为一次函数;然后取斜率的平均值为最终斜率,再代值求出截距,写出表达式;最后求反函数分别写出a p 、f 、v 与F z 的关系式。
按照上述思路,编写MATLAB 语言程序(附1),运行结果如下:图3-3-3 实验对数坐标图K =0.9353 0.9236 0.9149 0.9246 0.6987 0.7015 0.7052 0.7018 -0.1150 -0.1927 -0.1152 -0.1410 h =[ -3.1408 0.5512 -2.3426] H =[0.0432 1.7353 0.0961]其中,K ——矩阵元素表示斜率,行分别表示x 1、x 2和x 3的值,最后一列为斜率的平均值。
h ——矩阵元素分别表示截距k 1lg 、k 2lg 和k 3lg 的值。
H ——矩阵元素分别表示系数k 1、k 2和k 3的值。
根据运行结果代值,分别写出函数关系表达式如下: 14.3lg 92.0lg -=a p F z a p F z 92.00432.0= ③ 55.0lg 70.0lg +=f F z f F z 70.07353.1= ④ 34.2lg 14.0lg --=v F zv F z 14.00961.0-= ⑤式③④⑤表明,在a p 、f 和v 只有一个因素改变时,切削力Fz 都与该可变因素成指数函数关系。
当综合考虑三个可变因素时,可得出:v x cf x a x p K F z 321=。
式中,K 为综合系数。
]2[类似的,可分别求出a p、f、v和Fy、Fx的关系表达式。
4.切削用量对切削力的影响一般性结论:(1)背吃刀量与切削力近似成正比;(2)进给量增加,切削力增加,但不成正比;(3)切削速度对切削力影响较复杂(与切削温度的变化和积屑瘤的产生和消失有关)。
在无积屑瘤的切削速度范围内,随着切削速度的增大,切削力减小。
5.刀具几何参数对切削力的影响图4-1 刀具几何参数与切削力的关系曲线一般性结论:(1)前角对切削力的影响最大。
加工塑性材料时,增大前角,切削力降低;加工脆性材料时,由于切屑变形很小,前角对切削力影响的显著。
(2)主偏角对切削力影响较小,但对径向力和轴向力影响较大。
径向力随着主偏角的增大而减小,轴向力随着主偏角的增大而增大。
(3)刃倾角在很大范围内变化时对切削力影响不大,但对径向力和轴向力影响较大,随着刃倾角的增大,径向力减小,轴向力增大。
6.精密切削加工切削用量对切削力的影响精密切削过程中,就本质而言,切屑的变形与一般切削相同,所以其切削力的来源也相同。
但是,由于精密切削采用的是微量切屑方法,与一般切削不同,所以可变因素对二者的影响就不同,,也就是说可变因素对精密切削切削力的影响具有独特规律。
6.1进给量和背吃刀量的影响为了探讨精密切削切削力的独有规律,搜集部分实验数据,如下表:]1[]1[]1[]1[表6-1进给量对切削力的影响(HSS 刀)切削力(N )进给量f/(mm/r)0.01 0.02 0.04 0.10 0.20 F z60 100 350 570 900 F y240280410580700表6-2进给量对切削力的影响(金刚石刀)切削力 (N )进给量f/(mm/r)0.01 0.02 0.04 0.10 0.20 F z200 260 480 900 1030 F y4050120170200表6-3切削深度对切削力的影响(HSS 刀)切削力 (N )切削深度a p (mm )0.002 0.004 0.008 0.016 0.032 F z80 150 370 520 670 F y250270330370390表6-4切削深度对切削力的影响(金刚石刀)切削力 (N )切削深度a p (mm )0.003 0.006 0.01 0.02 0.03 F z100 170 260 450 500 F y 20305070 90以上数据的曲线图如图5-1所示。
从曲线中可以清楚地看出,①精密切削采用HSS 车刀(或硬质合金车刀)时,当进给量或背吃刀量小于一定值时,均有F z F y >成立。
而采用金刚石刀时,F z F y <。
这和一般切削F z 总是大于F y 是不同的。
②另外,在精密切削时,进给量对切削力的影响大于切削深度的影响。
这和一般切削恰恰相反。
为了解释以上两条特殊规律,我查阅了相关资料文献,得知:a.规律①取决]1[于切削用量(f 、a p )同刀具刃口半径的比值。
b.规律②与精密切削通常采用f 大于a p 的切削方式有关。
图5-1精密切削切削用量与切削力的关系曲线6.2切削速度的影响如图5-2所示(考虑积屑瘤的影响), 低速时切削力随切削速度增加而急剧下降。
到200~300m/min 后,切削力基本保持不变,这规律和积屑瘤高度随切削速度的变化规律 一致。
即积屑瘤高时切削力大,积屑瘤小时切削力也小,这和一般切削规律正好相反。