工业锅炉烟气脱硫技术.
烟气锅炉脱硫脱硝 工艺

烟气锅炉脱硫脱硝工艺
烟气锅炉脱硫脱硝工艺主要包括以下步骤:
1.烟气预处理:将烟气通过除尘器去除固体颗粒物和粉尘,以减少后续处理的干扰和防止设备堵塞。
2.烟气脱硫:将石灰石或氨水等脱硫剂喷入烟气中。
与烟气中的二氧化硫反应生成硫酸钙或硫酸铵,从而达到脱除烟气中二氧化硫的目的。
常用的脱硫工艺包括湿法脱硫和干法脱硫。
其中。
干法脱硫如SDS 干法脱硫则利用粉末的活性高的钙基或者钠基脱硫剂,吸收烟气中的二氧化硫。
3.烟气脱硝:将氨水或尿素等脱硝剂喷入烟气中,在催化剂的作用下与烟气中的氮氧化物反应生成氮和水,从而达到脱除烟气中氮氧化物的目的。
脱硝工艺用于去除烟气中的氮氧化物。
4.烟气后处理:将处理后的烟气通过除臭器等设备去除异味等杂质,使烟气达到排放标准。
其中。
烟气脱硫脱硝技术有多种,包括scr脱硝+半干法脱硫+布袋除尘(+升温热备)、半干法脱硫+布袋除尘+升温+低温scr脱硝、升温+scr 脱硝+ (余热回收+ )湿法脱硫+湿式电除尘+加热空气热备、干法脱硫脱硝一体化技术等。
这些技术各有特点,可以根据实际情况选择适合的工艺。
烟气脱硫脱硝技术是应用于多氮氧化物、硫氧化物生成化工工业的一项锅炉烟气净化技术。
氮氧化物、硫氧化物是空气污染的主要来源之一,因此,应用此项技术对环境空气净化益处颇多。
请注意,烟气锅炉脱硫脱硝工艺的具体实施可能因设备、环境、排放标准等因素而有所不同。
因此,在实际操作中,应根据具体情况进行选择和调整。
脱硫的常见方式
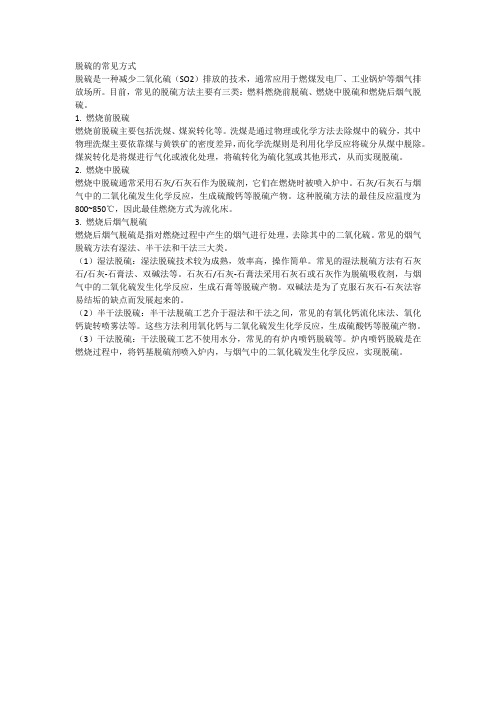
脱硫的常见方式脱硫是一种减少二氧化硫(SO2)排放的技术,通常应用于燃煤发电厂、工业锅炉等烟气排放场所。
目前,常见的脱硫方法主要有三类:燃料燃烧前脱硫、燃烧中脱硫和燃烧后烟气脱硫。
1. 燃烧前脱硫燃烧前脱硫主要包括洗煤、煤炭转化等。
洗煤是通过物理或化学方法去除煤中的硫分,其中物理洗煤主要依靠煤与黄铁矿的密度差异,而化学洗煤则是利用化学反应将硫分从煤中脱除。
煤炭转化是将煤进行气化或液化处理,将硫转化为硫化氢或其他形式,从而实现脱硫。
2. 燃烧中脱硫燃烧中脱硫通常采用石灰/石灰石作为脱硫剂,它们在燃烧时被喷入炉中。
石灰/石灰石与烟气中的二氧化硫发生化学反应,生成硫酸钙等脱硫产物。
这种脱硫方法的最佳反应温度为800~850℃,因此最佳燃烧方式为流化床。
3. 燃烧后烟气脱硫燃烧后烟气脱硫是指对燃烧过程中产生的烟气进行处理,去除其中的二氧化硫。
常见的烟气脱硫方法有湿法、半干法和干法三大类。
(1)湿法脱硫:湿法脱硫技术较为成熟,效率高,操作简单。
常见的湿法脱硫方法有石灰石/石灰-石膏法、双碱法等。
石灰石/石灰-石膏法采用石灰石或石灰作为脱硫吸收剂,与烟气中的二氧化硫发生化学反应,生成石膏等脱硫产物。
双碱法是为了克服石灰石-石灰法容易结垢的缺点而发展起来的。
(2)半干法脱硫:半干法脱硫工艺介于湿法和干法之间,常见的有氧化钙流化床法、氧化钙旋转喷雾法等。
这些方法利用氧化钙与二氧化硫发生化学反应,生成硫酸钙等脱硫产物。
(3)干法脱硫:干法脱硫工艺不使用水分,常见的有炉内喷钙脱硫等。
炉内喷钙脱硫是在燃烧过程中,将钙基脱硫剂喷入炉内,与烟气中的二氧化硫发生化学反应,实现脱硫。
循环流化床锅炉烟气脱硫技术
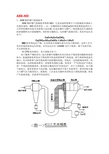
ABB-NID1、ABB锅炉烟气脱硫技术ABB锅炉烟气脱硫技术简称NID,它是由旋转喷雾半干法脱硫技术基础上发展而来的。
NID的原理是:以一定细度的石灰粉(CaO)经消化增湿处理后与大倍率的循环灰混合直接喷入反应器,在反应器中与烟气二氧化硫反应生成固态的亚硫酸钙及少量硫酸钙,再经除尘器除尘,达到烟气脱硫目的。
其化学反应式如下:CaO+H2O=Ca(OH)2Ca(OH)2+SO2=CaSO3·1/2H2O+1/2H2ONID技术将反应产物,石灰和水在容器中混合在加入吸收塔。
这种工艺只有很有限的商业运行经验,并且仅运行在100MW及以下机组,属于发展中的,不完善的技术。
和CFB技术相比,其主要缺点如下:由于黏性产物的存在,混合容器中频繁的有灰沉积由于吸收塔内颗粒的表面积小,造成脱硫效率低由于吸收塔中较高的固体和气体流速,使气体固体流速差减小,而且固体和气体在吸收塔中的滞留时间短,导致在一定的脱硫效率时,钙硫比较高,总的脱硫效果差。
需要配布袋除尘器,使其有一个”后续反应”才能达到一个稍高的脱硫效率,配电除尘器则没有”后续反应”。
对于大型机组,由于烟气量较大,通常需要多个反应器,反应器的增多不便于负荷调节,调节时除尘器入口烟气压力偏差较大。
脱硫剂、工艺水以及循环灰同时进入增湿消化器,容易产生粘接现象,负荷调节比较滞后。
Wulff-RCFBWulFF的CFB技术来源于80年代后期转到Wulff 去的鲁奇公司的雇员。
而LEE 近年来开发的新技术,Wulff公司没有,因此其技术有许多弱点:电除尘器的水平进口,直接积灰和气流与灰的分布不均。
没有要求再循环系统,对锅炉负荷的变化差,并直接导致在满负荷时烟气压头损失大。
消石灰和再循环产物的加入点靠近喷水点,使脱硫产物的黏性增加。
喷嘴上部引入再循环灰将对流化动态有负面影响,导致流化床中灰分布不均,在低负荷时,流化速度降低,循环灰容易从流化床掉入进口烟道中,严重时,大量的循环灰可将喷嘴堵塞。
湿法脱硫的工作原理是

湿法脱硫的工作原理是
湿法脱硫是一种常用的烟气脱硫技术,其工作原理是通过将烟气与含有氧化剂的吸收剂接触,使烟气中的二氧化硫(SO2)被吸收剂吸收并转化为硫酸盐。
这种技术主要适用于燃煤电厂、工业锅炉等燃烧过程中产生大量二氧化硫的场合。
具体来说,湿法脱硫的工作原理包括以下几个步骤:
1. 烟气接触:烟气从燃烧设备中排出后,进入脱硫塔或吸收器。
在脱硫塔中,烟气与喷射进来的吸收剂进行接触,形成气液两相的接触界面。
2. 吸收剂循环:吸收剂通常是一种碱性溶液,如石灰石浆液(石灰石和水的混合物)。
吸收剂通过喷淋或喷射的方式,与烟气进行充分接触。
在接触过程中,二氧化硫会被吸收剂吸收。
3. 反应转化:二氧化硫与吸收剂中的氧化剂(如氧气或空气)发生反应,生成硫酸盐。
这个反应通常是一个氧化还原反应,将二氧化硫氧化为硫酸。
4. 产物处理:生成的硫酸盐会与吸收剂中的其他成分一起形成溶液。
这个溶液需要进行处理,以便回收或处理其中的有害物质,同时将吸收剂重新循环使用。
总的来说,湿法脱硫通过将烟气与吸收剂接触和反应,将二氧化硫转化为硫酸盐,从而实现脱硫的目的。
这种技术在减少燃煤电厂和工业锅炉等燃烧过程中产生的
二氧化硫排放方面具有重要的应用价值。
锅炉及炉窑湿法烟气脱硫工程技术规范.pdf
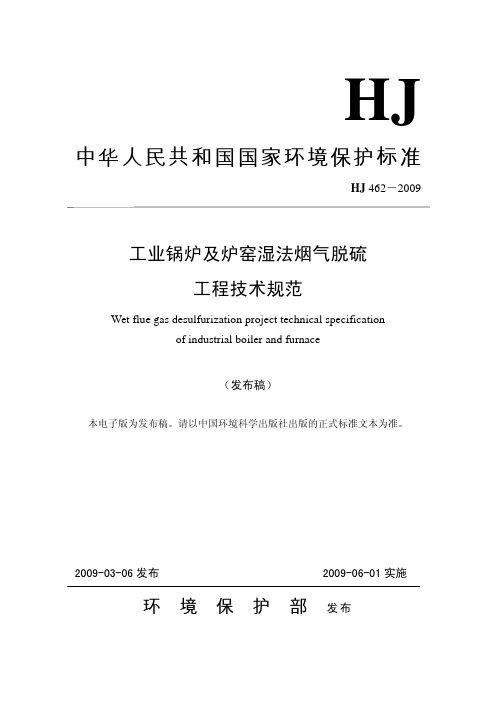
HJ 中华人民共和国国家环境保护标准HJ 462-2009工业锅炉及炉窑湿法烟气脱硫工程技术规范Wet flue gas desulfurization project technical specificationof industrial boiler and furnace(发布稿)本电子版为发布稿。
请以中国环境科学出版社出版的正式标准文本为准。
2009-03-06发布 2009-06-01实施环 境 保 护 部发布目 次前 言 (II)1 适用范围 (1)2 规范性引用文件 (1)3 术语和定义 (2)4 总体设计 (3)5 脱硫工艺系统 (4)6 材料、设备选择 (9)7 施工与验收 (10)8 运行与维护 (11)前 言为贯彻《中华人民共和国环境保护法》和《中华人民共和国大气污染防治法》,执行国家《锅炉大气污染物排放标准》、《工业炉窑大气污染物排放标准》,防治工业锅炉及炉窑大气污染,改善环境质量,制定本标准。
本标准对工业锅炉及炉窑湿法烟气脱硫工程的术语和定义、总体设计、脱硫工艺系统、材料和设备选择、施工与验收、运行与维护提出了技术要求。
本标准为首次发布。
本标准由环境保护部科技标准司组织制订。
本标准主要起草单位:浙江天蓝脱硫除尘有限公司、中国环境保护产业协会、北京市环境保护科学研究院、浙江大学环境工程研究所、杭州天蓝环保设备有限公司、北京西山新干线脱硫有限公司、六合天融(北京)集团公司、北京利德衡环保工程有限公司。
本标准环境保护部2009年3月6日批准。
本标准自2009年6月1日起实施。
本标准由环境保护部解释。
工业锅炉及炉窑湿法烟气脱硫工程技术规范1适用范围本标准对工业锅炉及炉窑湿法烟气脱硫工程的术语和定义、总体设计、脱硫工艺系统、材料和设备选择、施工与验收、运行与维护提出了技术要求。
本标准适用于采用石灰法、钠钙双碱法、氧化镁法、石灰石法工艺,配用在蒸发量≥20 t/h (14MW)的燃煤工业锅炉或蒸发量<400 t/h的燃煤热电锅炉以及相当烟气量炉窑的新建、改建和扩建湿法烟气脱硫工程,可作为环境影响评价、设计、施工、环境保护验收及建成后运行与管理的技术依据。
电厂锅炉脱硫脱硝及烟气除尘技术

电厂锅炉脱硫脱硝及烟气除尘技术摘要:随着国内工业的快速发展,工业生产的污染问题越来越严重。
在火电企业的发展中,大量的电力是以破坏周围环境为代价的。
因此,电力企业需要严格控制发电过程中产生的各种污染物的排放,以保持火电企业的可持续发展,增强其市场竞争力。
关键词:电厂锅炉;脱硫脱硝;烟气除尘技术引言火电厂燃煤过程中产生的氮氧化物和硫氧化物对环境构成了极大的威胁,这些有害物质容易形成酸雨等灾害。
因此,有必要对火电厂的燃烧过程进行有效的改造。
在生产过程中,锅炉的脱硫脱硝处理主要依靠反应塔内的对流交换和物理化学吸附,但不同的生产结构在处理方式的选择上会有一定的差异。
因此,需要相关技术人员根据实际需要进行优化调整,使锅炉整体吸附率达到合格排放的标准。
1电厂锅炉脱硫脱硝技术分析就锅炉脱硫脱硝技术的实际应用而言,目前很多企业相关技术试验方案落实不到位,达不到脱硫脱硝的基本要求。
有些技术应用甚至处于迷茫甚至混乱的阶段。
其中一些企业还借鉴国外先进的脱硫脱硝经验和技术,与中国传统技术相结合,希望达到技术创新的目的。
1.1湿法脱硫脱硝技术第一种是利用吸收剂吸收火力发电过程中的气体污染物,从而达到脱硫脱硝的效果。
由硫和氮与氧反应形成的氧化物通常能够与碱性物质发生化学反应。
因此,为了增加脱硫脱硝的效果,往往选择碱性物质作为吸收剂;第二种采用的是传统的石灰石—石膏湿法技术,由于其应用时间长,应用效果也比较理想,基本能够达到百分之九十以上的脱除率。
与此同时,石灰石—石膏湿法技术应用中得到产物还能进行回收并进行二次利用,从而有效避免由于脱硫脱硝后所产生的物质对于环境产生的二次污染以及产物难以处理的难题。
1.2炉后半干法脱硫技术炉后半干法脱硫最常用的工艺是旋转喷雾半干法工艺,旋转喷雾反应系统由喷雾反应塔和石灰浆制备系统组成。
石灰制备系统将生石灰(CaO)制备成一定浓浆液,通过旋转雾化器喷入半干式反应塔内形成微小液滴。
与石灰度的Ca(OH)2浆液滴充分接触和反应,去除SO2气体。
科技成果——工业锅炉、炉窑烟气脱硫脱硝技术开发与应用
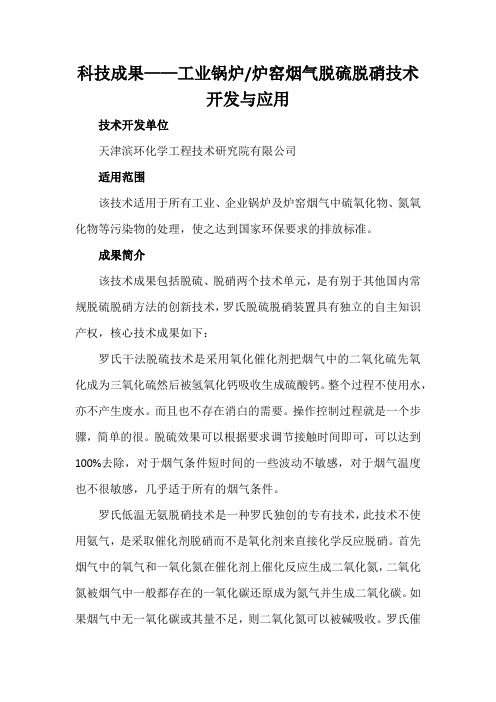
科技成果——工业锅炉/炉窑烟气脱硫脱硝技术开发与应用技术开发单位天津滨环化学工程技术研究院有限公司适用范围该技术适用于所有工业、企业锅炉及炉窑烟气中硫氧化物、氮氧化物等污染物的处理,使之达到国家环保要求的排放标准。
成果简介该技术成果包括脱硫、脱硝两个技术单元,是有别于其他国内常规脱硫脱硝方法的创新技术,罗氏脱硫脱硝装置具有独立的自主知识产权,核心技术成果如下:罗氏干法脱硫技术是采用氧化催化剂把烟气中的二氧化硫先氧化成为三氧化硫然后被氢氧化钙吸收生成硫酸钙。
整个过程不使用水,亦不产生废水。
而且也不存在消白的需要。
操作控制过程就是一个步骤,简单的很。
脱硫效果可以根据要求调节接触时间即可,可以达到100%去除,对于烟气条件短时间的一些波动不敏感,对于烟气温度也不很敏感,几乎适于所有的烟气条件。
罗氏低温无氨脱硝技术是一种罗氏独创的专有技术,此技术不使用氨气,是采取催化剂脱硝而不是氧化剂来直接化学反应脱硝。
首先烟气中的氧气和一氧化氮在催化剂上催化反应生成二氧化氮,二氧化氮被烟气中一般都存在的一氧化碳还原成为氮气并生成二氧化碳。
如果烟气中无一氧化碳或其量不足,则二氧化氮可以被碱吸收。
罗氏催化剂系列为高效复合催化剂,无毒无二次污染,可以在较宽和较低温度范围内(室温至300℃以下)将NO去除,去除效果可以很方便地调节,其去除率可达到60%或更高。
过程简单操作方便,投资运行成本均较低。
由于不使用氨气,无安全隐患。
技术效果工业锅炉/窑炉领域的脱硝脱硫,主要体现在技术先进性有效性以及成本竞争。
本技术在先进适用有效以及投资/操作成本上均有无可匹敌的优势,而且不产生二次污染。
我们的工艺,对于脱硫脱硝的效率可以灵活调节,可以从百分之几十直到大于99%。
可以满足并超越国家/敏感地区如北京市最新环保要求。
在许多情况下实现脱硫近100%,脱硝根据需要设计成优于当地环保部门要求的排放标准。
应用情况1、河北廊坊耀邦热力35+20t/h燃煤锅炉脱尘脱硫脱硝一体化处理项目;2、兖矿科技有限公司杨村煤矿20t/h链条排炉尾部烟气脱硫脱硝深度处理项目;3、湖南巨强再生资源科技发展有限公司烟气脱硫脱硝项目;4、唐钢高强板35t/h焦炉煤气发电烟气脱硫脱硝除尘超低排放项目;5、唐山荣程特钢动力厂15MW高炉煤气发电锅炉脱硫处理项目。
工业锅炉烟气治理中几种脱硫工艺流程及对比
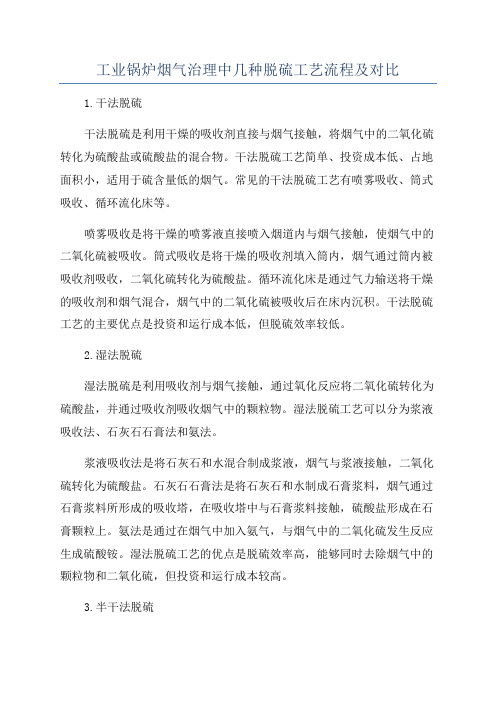
工业锅炉烟气治理中几种脱硫工艺流程及对比1.干法脱硫干法脱硫是利用干燥的吸收剂直接与烟气接触,将烟气中的二氧化硫转化为硫酸盐或硫酸盐的混合物。
干法脱硫工艺简单、投资成本低、占地面积小,适用于硫含量低的烟气。
常见的干法脱硫工艺有喷雾吸收、筒式吸收、循环流化床等。
喷雾吸收是将干燥的喷雾液直接喷入烟道内与烟气接触,使烟气中的二氧化硫被吸收。
筒式吸收是将干燥的吸收剂填入筒内,烟气通过筒内被吸收剂吸收,二氧化硫转化为硫酸盐。
循环流化床是通过气力输送将干燥的吸收剂和烟气混合,烟气中的二氧化硫被吸收后在床内沉积。
干法脱硫工艺的主要优点是投资和运行成本低,但脱硫效率较低。
2.湿法脱硫湿法脱硫是利用吸收剂与烟气接触,通过氧化反应将二氧化硫转化为硫酸盐,并通过吸收剂吸收烟气中的颗粒物。
湿法脱硫工艺可以分为浆液吸收法、石灰石石膏法和氨法。
浆液吸收法是将石灰石和水混合制成浆液,烟气与浆液接触,二氧化硫转化为硫酸盐。
石灰石石膏法是将石灰石和水制成石膏浆料,烟气通过石膏浆料所形成的吸收塔,在吸收塔中与石膏浆料接触,硫酸盐形成在石膏颗粒上。
氨法是通过在烟气中加入氨气,与烟气中的二氧化硫发生反应生成硫酸铵。
湿法脱硫工艺的优点是脱硫效率高,能够同时去除烟气中的颗粒物和二氧化硫,但投资和运行成本较高。
3.半干法脱硫半干法脱硫是将湿法脱硫和干法脱硫两种技术相结合的一种工艺。
半干法脱硫的主要原理是在湿法脱硫工艺中加入干式脱硫的环节,通过干式脱硫可以提高脱硫效率和降低湿法脱硫工艺中的吸收剂消耗量。
常见的半干法脱硫工艺有旋风式湿法脱硫和浆液喷雾干式脱硫。
旋风式湿法脱硫是在湿法脱硫系统的前段设置旋风除尘器,通过旋风分离颗粒物,将大部分颗粒物分离并回收,然后再进入湿法脱硫系统进行吸收。
浆液喷雾干式脱硫是在干燥塔内喷雾吸收剂直接与烟气接触,在干燥塔内将烟气中的二氧化硫转化为硫酸盐。
半干法脱硫工艺的优点是脱硫效率高,投资和运行成本相对较低,但操作复杂度较高。
- 1、下载文档前请自行甄别文档内容的完整性,平台不提供额外的编辑、内容补充、找答案等附加服务。
- 2、"仅部分预览"的文档,不可在线预览部分如存在完整性等问题,可反馈申请退款(可完整预览的文档不适用该条件!)。
- 3、如文档侵犯您的权益,请联系客服反馈,我们会尽快为您处理(人工客服工作时间:9:00-18:30)。
工业锅炉烟气脱硫技术主要介绍:烟气脱硫技术——湿法、半干法、干法等1.1 湿法已商业化或完成中试的湿法脱硫工艺包括石灰(石灰石)法、双碱法、氨吸收法、磷铵复肥法、稀硫酸吸收法、海水脱硫、氧化镁法等10多种。
其中,又以湿式钙法占绝对统治地位,其优点是技术成熟、脱硫率高,Ca/S比低,操作简便,吸收剂价廉易得,副产物便于利用。
1.1.1石灰石-石膏法:石灰石/石灰湿法脱硫最早由英国皇家化学工业公司在20世纪30年代提出,目前是应用最广泛的脱硫技术。
该工艺是利用石灰石/石灰石浆液洗涤烟道气,使之与SO2反应,生成亚硫酸钙(CaSO3),脱硫产物亚硫酸钙可直接抛弃,也可以通入空气强制氧化和加入一些添加剂,以石膏形式进行回收,脱硫率达到95%以上。
为了减轻SO2洗涤设备的负荷,先要将烟道气除尘,然后再进入洗涤设备与吸收液发生反应。
吸收过程的主要反应为:CaCO3+SO2+1/2 H2O→CaSO3·1/2H2O+CO2↑Ca(OH)2+SO2→CaSO3·1/2 H2O+1/2H2OCaSO3·1/2 H2O+SO2+1/2H2O→Ca(HSO3)2废气中的氧或送入氧化塔内的空气可将亚硫酸钙和亚硫酸氢钙氧化成石膏:2CaSO3·1/2 H2O+O2+3H2O→2CaSO4·2 H2OCa(HSO3)2+1/2O2+H2O→CaSO4·2 H2O+SO2通常石灰/石灰石法由三个单元组成:① SO2吸收;②固液分离;③固体处理。
图12.2 石灰石/石灰法烟气脱硫示意流程图吸收塔内的吸收液与除尘后进入的烟气反应后,被送入氧化塔内制取石膏。
烟道气脱硫常用的吸收塔有:湍球塔、板式塔、喷淋塔和文丘里/喷雾洗涤塔等。
石灰或石灰石的吸收效率与浆液的pH值、钙硫比、液气比、温度、石灰石粒度、浆液固体浓度、气体中S02浓度、洗涤器结构等众多因素有关,主要因素有:(a)浆液pH值。
研究表明,硫酸钙的溶解度随pH值的变化比较小,而亚硫酸钙的溶解度随pH值降低则增大。
当浆液的pH值低时,溶液中存在较多的亚硫酸钙,在CaCO3颗粒表面液膜中,溶解的CaCO3使液膜的pH值上升,使得亚硫酸钙在液膜中析出,沉积在CaCO3颗粒表面,抑制其与SO2的传质过程。
因此,石灰的传质阻力比石灰石要小,若采用石灰石,则需要延长接触时间,增加持液量和减少石灰石粒径,以便获得相应的脱硫率。
一般石灰石系统的最佳操作pH =6,石灰系统pH=8。
;(b)液气比。
由于反应中Ca2+持续地被消耗,这就需要吸收器有较大的持液量,即保证较高的液气比。
显然,脱硫率随液气比增大而主要 反应SO2(g)+H2O →H2SO3 H2SO3→H ++HSO -3H ++CaCO3→Ca2++HCO -3 Ca2++HCO -3+2H2O →CaSO3·2H2O +H + H ++HCO -3→H2CO3SO2(g)+H2O →H2SO3 H2SO3→H ++HSO -3 CaO +H2O →Ca(OH)2 Ca(OH)2→Ca2++2OH - Ca2++HSO -3+2H2O →CaSO3·2H2O +H + 由于湿法脱硫的特点,有多种因素影响到吸收洗涤塔的长期可靠运行。
这些技术问题目前已得到妥善解决,但在20世纪70年代和80年代,湿法烟气脱硫技术的发展都是围绕解决这些问题而开展的。
①设备腐蚀:化石燃料燃烧的排烟中含有多种微量的化学成分,如氯化物。
在酸性环境中,它们对金属(包括不锈钢)的腐蚀性相当强。
目前广泛应用的吸收塔材料是合金C -276(55%Ni ,17%Mo ,16%Cr ,6%Fe ,4%W ),其价格是常规不锈钢的15倍。
为延长设备的使用寿命,溶液中氯离子的浓度不能太高。
为保证氯离子不发生浓缩,有效的方法是在脱硫系统中根据物料平衡排出适量的废水,并以清水补充。
②结垢和堵塞:固体沉积主要以三种方式出现,湿干结垢,即因溶液或料浆中的水分蒸发而使固体沉积;Ca(OH)2或CaCO3沉积或结晶析出;CaSO3或CaSO4从溶液中结晶析出。
其中后者是导致脱硫塔发生结垢的主要原因,特别是硫酸钙结垢坚硬、板结,一旦结垢难以去除,影响到所有与脱硫液接触的阀门、水泵、控制仪器和管道等。
硫酸钙结垢的原因是SO2-4和Ca2+的离子积在局部达到过饱和。
为此,在吸收塔中要保持亚硫酸盐的氧化率在20%以下。
亚硫酸盐的氧化需要在脱硫液循环池中完成,可通过鼓氧或空气等方式进行,形成的硫酸钙发生沉淀。
从循环池返回吸收塔的脱硫液中,还因为含有足量的硫酸钙晶体,起到了晶种的作用,因此在后续的吸收过程中,可防止固体直接沉积在吸收塔设备表面。
③除雾器堵塞:在吸收塔中,雾化喷嘴并不能产生尺寸完全均一的雾滴,雾滴的大小存在尺寸分布。
较小的雾滴会被气流所夹带,如果不进行除雾,雾滴将进入烟道,造成烟道腐蚀和堵塞。
早期的除雾器通常用的是金属编织网,容易因雾滴中的固体颗粒沉积而堵塞。
因此,除雾器必须易于保持清洁。
目前使用的除雾器有多种形式(如折流板型等),通常用高速喷嘴每小时数次喷清水进行冲洗。
④脱硫剂的利用率:脱硫产物亚硫酸盐和硫酸盐可沉积在脱硫剂颗粒表面,从而堵塞了这些颗粒的溶解通道。
这会造成石灰石或石灰脱硫剂来不及溶解和反应就随产物排除,增加了脱硫剂和脱硫产物的处理费用。
因此,脱硫液在循环池中的停留时间一般要达到5~10min。
实际的停留时间设计与石灰石的反应性能有关,反应性能越差,为使之完全溶解,要求它在池内的停留时间越长。
⑤液固分离:半水亚硫酸钙通常是较细的片状晶体,这种固体产物难以分离,也不符合填埋要求。
而二水硫酸钙是大的圆形晶体,易于析出和过滤。
因此,从分离的角度看,在循环池中鼓氧或空气将亚硫酸盐氧化为硫酸盐也是十分必要的,通常要保证95%的脱硫产物转化为硫酸钙。
石灰/石灰石-石膏法技术比较成熟,吸收剂价廉易得,运行可靠,应用最广,脱硫效率可达90%以上,通过添加有机酸可使脱硫率提高到95%以上。
重庆路璜电厂已引进的这种烟气脱硫设备。
但该工艺流程较复杂,投资为与运行费用高,占地面积大。
1.1.2双碱法:用碱性化合物作吸收剂,是脱除SO2最主要的方法。
由于Na2SO3- NaHSO3溶解能适应吸收与再生的循环操作。
因此,大烟气量的脱硫系统以采用再生型更为适宜。
双碱法是针对石灰或石灰石法易结垢和堵塞的问题发展的一种脱硫工艺,又称钠碱法。
首先采用钠化合物(NaOH、Na2CO3或Na2SO3)溶液吸收烟气中的SO2,生成Na2SO3和NaHSO3,接着用石灰或石灰石使吸收液再生为钠溶液,并生成亚硫酸钙或硫酸钙沉淀。
由于吸收塔内用的是溶于水的钠化合物作为吸收剂,不会结垢。
然后将离开吸收塔的溶液导入一开口反应器,加入石灰或石灰石进行再生反应,再生后的钠溶液返回吸收塔重新作为吸收剂使用。
该法可避免钙盐结垢堵塞的问题,脱硫效率可达90%以上。
吸收反应为:Na2CO3+SO2→Na2SO3+CO2↑2NaOH+SO2→Na2SO3+H2ONa2SO3+SO2+H2O→2NaHSO3反应器中的再生反应为:Na2SO3+Ca(OH)2+1/2H2O→2NaOH+CaSO3·1/2H2O↓2NaHSO3+Ca(OH)2→CaSO3·1/2H2O↓+3/2H2O+Na2SO32NaHSO3+CaCO3→CaSO3·1/2H2O↓+Na2SO3+CO2↑+1/2H2O如果将亚硫酸钙进一步氧化,才能回收石膏。
此法的脱硫率也很高,可达95%以上。
缺点是吸收过程中,生成的部分Na2SO3会被烟气中残余O2氧化成不易清除的Na2SO4,使得吸收剂损耗增加和石膏质量降低。
电站锅炉烟气中,大约有5%~10%的Na2SO3被氧化为Na2SO4。
如果溶液中的OH-和SO2-保持足够高的浓度:Na2SO4+Ca(OH)2+2H2O→2NaOH+CaSO4·2H2O则可除去Na2SO4。
若吸收塔采用稀硫酸来除去硫酸钠,这也要增加硫酸消耗:Na2SO4+H2SO4+2CaSO3+4H2O→2CaSO4·2H2O+2NaHSO3钠钙双碱法所得的亚硫酸钙滤饼(约60%的水)重新浆化为含10%固体的料浆,加入硫酸降低pH值后,在氧化器内用空气进行氧化可制得石膏。
亚硫酸钙滤饼也可直接抛弃。
双碱法在国外有较广泛的应用,国内有关单位在国家“十五”863计划的支持下,双碱法脱硫技术研究和应用都进展很好,目前已成为我国工业锅炉烟气脱硫的主要技术之一。
1.1.3 亚硫酸钠循环吸收法亚硫酸钠循环吸收法由于双碱法生成的石膏产品质量较差,而且往往滞销,因此,为了寻求副产品的出路,在双碱法的基础上,又开发了一种亚硫酸钠循环吸收工艺。
亚硫酸钠溶液循环吸收SO2产生NaHSO3,NaHSO3的再生是通过热分解NaHSO3来实现的,在热分解过程中。
释放出高浓度SO2气体,可以将其制成液体SO2,也可以制成硫酸或元素硫。
1.1.4稀硫酸吸收法稀硫酸吸收法烟气经预除尘和降温后,进入吸收塔,在50℃-80℃时被2%-4%的稀硫酸吸收,由于在吸收剂中加入了Fe3+作为氧化剂,并同时向吸收塔内鼓入空气以促进氧化作用,因此,增强了吸收效果。
氧化了的SO2生成硫酸,如加入CaCO3则生成石膏。
该方法操作简单,二次污染少,无结垢和堵塞问题,脱硫效率可达90%以上。
1.1.5海水脱硫天然海水含有大量的可溶性盐,其中主要成分是氯化钠和硫酸盐及一定量的可溶性碳酸卤。
海水通常呈碱性,自然碱度约为1.2~2.5mmol/L。
这使得海水具有天然的酸碱缓冲能力及吸收SO2的能力,其脱硫效率为90%以上。
用于燃煤电厂的海水烟气脱硫工艺是近几年发展起来的新型烟气脱硫工艺。
根据是否添加其分化学吸收剂,海水脱硫工艺可分为两类:①用纯海水作为吸收剂的工艺,以挪威ABB公司开发的Flakt-Hydro工艺为代表,有较多的工业应用。
②在海水中添加一定量石灰以调节吸收液的碱度,以美国Bechtel公司的脱硫工艺为代表,在美国已建成示范工程,但未推广应用。
世界上第一座用海水进行火电厂排烟脱硫的装置是1988年在印度孟买建成的,采用的是ABB的海水脱硫技术。
中国第一座海水脱硫工程应用在深圳西部电电力有限公司2号300MW机组,1999年投产运行。
1.1.6磷铵复肥法磷铵复肥法该法是利用天然磷矿石和氨为原料,在烟气脱硫过程中副产品为磷铵复合肥料,工艺流程主要包括四个过程,即:活性炭一级脱硫并制得稀硫酸;稀硫酸萃取磷矿制得稀磷酸溶液;磷酸和氨的中和液[(NH4)2HPO4]二级脱硫;料浆浓缩干燥制磷铵复肥。
其法脱硫效率为95%以上。
此法四川豆坝电厂应用成功。