外文参考文献翻译-中文
外文参考文献翻译-中文
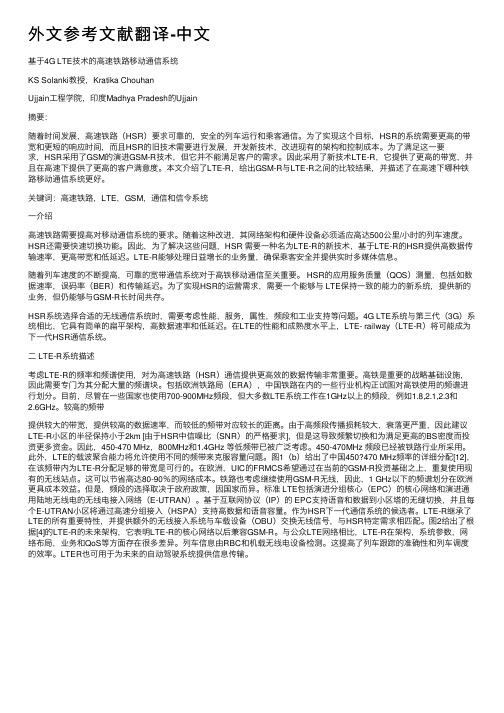
外⽂参考⽂献翻译-中⽂基于4G LTE技术的⾼速铁路移动通信系统KS Solanki教授,Kratika ChouhanUjjain⼯程学院,印度Madhya Pradesh的Ujjain摘要:随着时间发展,⾼速铁路(HSR)要求可靠的,安全的列车运⾏和乘客通信。
为了实现这个⽬标,HSR的系统需要更⾼的带宽和更短的响应时间,⽽且HSR的旧技术需要进⾏发展,开发新技术,改进现有的架构和控制成本。
为了满⾜这⼀要求,HSR采⽤了GSM的演进GSM-R技术,但它并不能满⾜客户的需求。
因此采⽤了新技术LTE-R,它提供了更⾼的带宽,并且在⾼速下提供了更⾼的客户满意度。
本⽂介绍了LTE-R,给出GSM-R与LTE-R之间的⽐较结果,并描述了在⾼速下哪种铁路移动通信系统更好。
关键词:⾼速铁路,LTE,GSM,通信和信令系统⼀介绍⾼速铁路需要提⾼对移动通信系统的要求。
随着这种改进,其⽹络架构和硬件设备必须适应⾼达500公⾥/⼩时的列车速度。
HSR还需要快速切换功能。
因此,为了解决这些问题,HSR 需要⼀种名为LTE-R的新技术,基于LTE-R的HSR提供⾼数据传输速率,更⾼带宽和低延迟。
LTE-R能够处理⽇益增长的业务量,确保乘客安全并提供实时多媒体信息。
随着列车速度的不断提⾼,可靠的宽带通信系统对于⾼铁移动通信⾄关重要。
HSR的应⽤服务质量(QOS)测量,包括如数据速率,误码率(BER)和传输延迟。
为了实现HSR的运营需求,需要⼀个能够与 LTE保持⼀致的能⼒的新系统,提供新的业务,但仍能够与GSM-R长时间共存。
HSR系统选择合适的⽆线通信系统时,需要考虑性能,服务,属性,频段和⼯业⽀持等问题。
4G LTE系统与第三代(3G)系统相⽐,它具有简单的扁平架构,⾼数据速率和低延迟。
在LTE的性能和成熟度⽔平上,LTE- railway(LTE-R)将可能成为下⼀代HSR通信系统。
⼆ LTE-R系统描述考虑LTE-R的频率和频谱使⽤,对为⾼速铁路(HSR)通信提供更⾼效的数据传输⾮常重要。
毕业论文(设计)外文文献翻译及原文
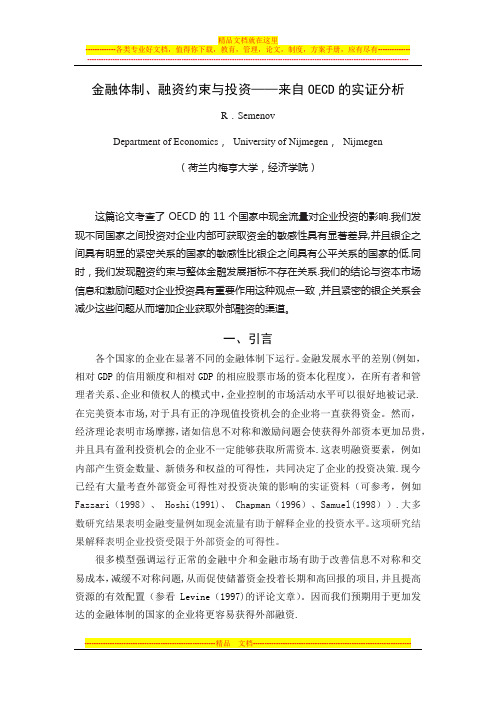
金融体制、融资约束与投资——来自OECD的实证分析R.SemenovDepartment of Economics,University of Nijmegen,Nijmegen(荷兰内梅亨大学,经济学院)这篇论文考查了OECD的11个国家中现金流量对企业投资的影响.我们发现不同国家之间投资对企业内部可获取资金的敏感性具有显著差异,并且银企之间具有明显的紧密关系的国家的敏感性比银企之间具有公平关系的国家的低.同时,我们发现融资约束与整体金融发展指标不存在关系.我们的结论与资本市场信息和激励问题对企业投资具有重要作用这种观点一致,并且紧密的银企关系会减少这些问题从而增加企业获取外部融资的渠道。
一、引言各个国家的企业在显著不同的金融体制下运行。
金融发展水平的差别(例如,相对GDP的信用额度和相对GDP的相应股票市场的资本化程度),在所有者和管理者关系、企业和债权人的模式中,企业控制的市场活动水平可以很好地被记录.在完美资本市场,对于具有正的净现值投资机会的企业将一直获得资金。
然而,经济理论表明市场摩擦,诸如信息不对称和激励问题会使获得外部资本更加昂贵,并且具有盈利投资机会的企业不一定能够获取所需资本.这表明融资要素,例如内部产生资金数量、新债务和权益的可得性,共同决定了企业的投资决策.现今已经有大量考查外部资金可得性对投资决策的影响的实证资料(可参考,例如Fazzari(1998)、 Hoshi(1991)、 Chapman(1996)、Samuel(1998)).大多数研究结果表明金融变量例如现金流量有助于解释企业的投资水平。
这项研究结果解释表明企业投资受限于外部资金的可得性。
很多模型强调运行正常的金融中介和金融市场有助于改善信息不对称和交易成本,减缓不对称问题,从而促使储蓄资金投着长期和高回报的项目,并且提高资源的有效配置(参看Levine(1997)的评论文章)。
因而我们预期用于更加发达的金融体制的国家的企业将更容易获得外部融资.几位学者已经指出建立企业和金融中介机构可进一步缓解金融市场摩擦。
毕业论文英文参考文献与译文
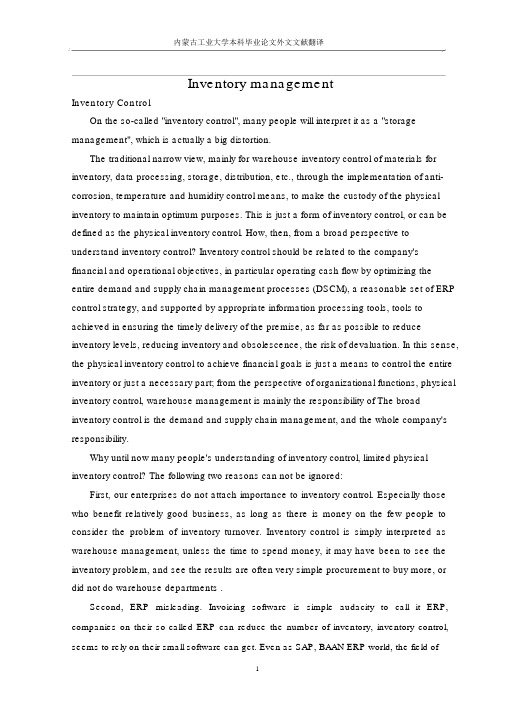
Inventory managementInventory ControlOn the so-called "inventory control", many people will interpret it as a "storage management", which is actually a big distortion.The traditional narrow view, mainly for warehouse inventory control of materials for inventory, data processing, storage, distribution, etc., through the implementation of anti-corrosion, temperature and humidity control means, to make the custody of the physical inventory to maintain optimum purposes. This is just a form of inventory control, or can be defined as the physical inventory control. How, then, from a broad perspective to understand inventory control? Inventory control should be related to the company's financial and operational objectives, in particular operating cash flow by optimizing the entire demand and supply chain management processes (DSCM), a reasonable set of ERP control strategy, and supported by appropriate information processing tools, tools to achieved in ensuring the timely delivery of the premise, as far as possible to reduce inventory levels, reducing inventory and obsolescence, the risk of devaluation. In this sense, the physical inventory control to achieve financial goals is just a means to control the entire inventory or just a necessary part; from the perspective of organizational functions, physical inventory control, warehouse management is mainly the responsibility of The broad inventory control is the demand and supply chain management, and the whole company's responsibility.Why until now many people's understanding of inventory control, limited physical inventory control? The following two reasons can not be ignored:First, our enterprises do not attach importance to inventory control. Especially those who benefit relatively good business, as long as there is money on the few people to consider the problem of inventory turnover. Inventory control is simply interpreted as warehouse management, unless the time to spend money, it may have been to see the inventory problem, and see the results are often very simple procurement to buy more, or did not do warehouse departments .Second, ERP misleading. Invoicing software is simple audacity to call it ERP, companies on their so-called ERP can reduce the number of inventory, inventory control, seems to rely on their small software can get. Even as SAP, BAAN ERP world, the field ofthese big boys, but also their simple modules inside the warehouse management functionality is defined as "inventory management" or "inventory control." This makes the already not quite understand what our inventory control, but not sure what is inventory control.In fact, from the perspective of broadly understood, inventory control, shouldinclude the following:First, the fundamental purpose of inventory control. We know that the so-called world-class manufacturing, two key assessment indicators (KPI) is, customer satisfaction and inventory turns, inventory turns and this is actually the fundamental objective of inventory control.Second, inventory control means. Increase inventory turns, relying solely on the so-called physical inventory control is not enough, it should be the demand and supply chain management process flow of this large output, and this big warehouse management processes in addition to including this link, the more important The section also includes: forecasting and order processing, production planning and control, materials planning and purchasing control, inventory planning and forecasting in itself, as well as finished products, raw materials, distribution and delivery of the strategy, and even customs management processes.And with the demand and supply chain management processes throughout the process, it is the information flow and capital flow management. In other words, inventory itself is across the entire demand and supply management processes in all aspects of inventory control in order to achieve the fundamental purpose, it must control all aspects of inventory, rather than just manage the physical inventory at hand.Third, inventory control, organizational structure and assessment.Since inventory control is the demand and supply chain management processes, output, inventory control to achieve the fundamental purpose of this process must be compatible with a rational organizational structure. Until now, we can see that many companies have only one purchasing department, purchasing department following pipe warehouse. This is far short of inventory control requirements. From the demand and supply chain management process analysis, we know that purchasing and warehouse management is the executive arm of the typical, and inventory control should focus on prevention, the executive branch is very difficult to "prevent inventory" for the simple reason that they assessment indicatorsin large part to ensure supply (production, customer). How the actual situation, a reasonable demand and supply chain management processes, and thus set the corresponding rational organizational structure and is a question many of our enterprisesto exploreThe role of inventory controlInventory management is an important part of business management. In the production and operation activities, inventory management must ensure that both the production plant for raw materials, spare parts demand, but also directly affect the purchasing, sales of share, sales activities. To make an inventory of corporate liquidity, accelerate cash flow, the security of supply under the premise of minimizing Yaku funds, directly affects the operational efficiency. Ensure the production and operation needs of the premise, so keep inventories at a reasonable level; dynamic inventory control, timely, appropriate proposed order to avoid over storage or out of stock; reduce inventory footprint, lower total cost of inventory; control stock funds used to accelerate cash flow.Problems arising from excessive inventory: increased warehouse space andinventory storage costs, thereby increasing product costs; take a lot of liquidity, resultingin sluggish capital, not only increased the burden of payment of interest, etc., would affect the time value of money and opportunity income; finished products and raw materials caused by physical loss and intangible losses; a large number of enterprise resource idle, affecting their rational allocation and optimization; cover the production, operation of the whole process of the various contradictions and problems, is not conducive to improve the management level.Inventory is too small the resulting problems: service levels caused a decline in the profit impact of marketing and corporate reputation; production system caused by inadequate supply of raw materials or other materials, affecting the normal production process; to shorten lead times, increase the number of orders, so order (production) costs; affect the balance of production and assembly of complete sets.NotesInventory management should particularly consider the following two questions:First, according to sales plans, according to the planned production of the goods circulated in the market, we should consider where, how much storage.Second, starting from the level of service and economic benefits to determine howto ensure inventories and supplementary questions.The two problems with the inventory in the logistics process functions.In general, the inventory function:(1)to prevent interrupted. Received orders to shorten the delivery of goods fromthe time in order to ensure quality service, at the same time to prevent out of stock.(2)to ensure proper inventory levels, saving inventory costs.(3)to reduce logistics costs. Supplement with the appropriate time interval compatible with the reasonable demand of the cargo in order to reduce logistics costs, eliminate or avoid sales fluctuations.(4)ensure the production planning, smooth to eliminate or avoid sales fluctuations.(5)display function.(6)reserve. Mass storage when the price falls, reduce losses, to respond to disasters and other contingencies.About the warehouse (inventory) on what the question, we must consider the number and location. If the distribution center, it should be possible according to customer needs, set at an appropriate place; if it is stored in central places to minimize the complementary principle to the distribution centers, there is no place certain requirements. When the stock base is established, will have to take into account are stored in various locations in what commodities.库存管理库存控制在谈到所谓“库存控制”的时候,很多人将其理解为“仓储管理”,这实际上是个很大的曲解。
外文文献翻译(图片版)
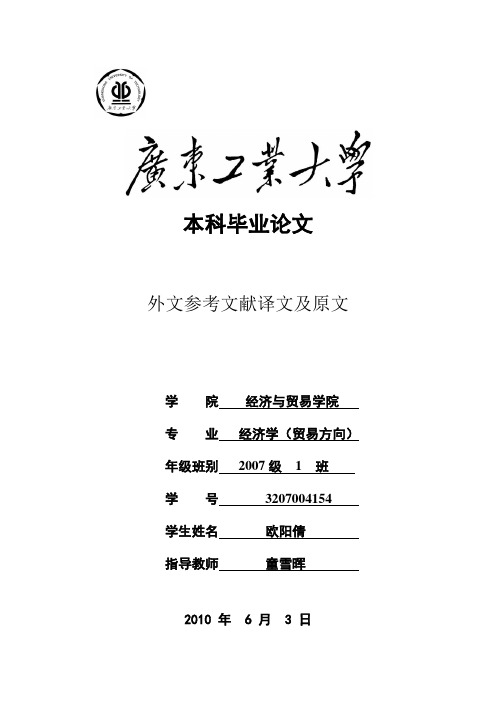
本科毕业论文外文参考文献译文及原文学院经济与贸易学院专业经济学(贸易方向)年级班别2007级 1 班学号3207004154学生姓名欧阳倩指导教师童雪晖2010 年 6 月 3 日目录1 外文文献译文(一)中国银行业的改革和盈利能力(第1、2、4部分) (1)2 外文文献原文(一)CHINA’S BANKING REFORM AND PROFITABILITY(Part 1、2、4) (9)1概述世界银行(1997年)曾声称,中国的金融业是其经济的软肋。
当一国的经济增长的可持续性岌岌可危的时候,金融业的改革一直被认为是提高资金使用效率和消费型经济增长重新走向平衡的必要(Lardy,1998年,Prasad,2007年)。
事实上,不久前,中国的国有银行被视为“技术上破产”,它们的生存需要依靠充裕的国家流动资金。
但是,在银行改革开展以来,最近,强劲的盈利能力已恢复到国有商业银行的水平。
但自从中国的国有银行在不久之前已经走上了改革的道路,它可能过早宣布银行业的改革尚未取得完全的胜利。
此外,其坚实的财务表现虽然强劲,但不可持续增长。
随着经济增长在2008年全球经济衰退得带动下已经开始软化,银行预计将在一个比以前更加困难的经济形势下探索。
本文的目的不是要评价银行业改革对银行业绩的影响,这在一个完整的信贷周期后更好解决。
相反,我们的目标是通过审查改革的进展和银行改革战略,并分析其近期改革后的强劲的财务表现,但是这不能完全从迄今所进行的改革努力分离。
本文有三个部分。
在第二节中,我们回顾了中国的大型国有银行改革的战略,以及其执行情况,这是中国银行业改革的主要目标。
第三节中分析了2007年的财务表现集中在那些在市场上拥有浮动股份的四大国有商业银行:中国工商银行(工商银行),中国建设银行(建行),对中国银行(中银)和交通银行(交通银行)。
引人注目的是中国农业银行,它仍然处于重组上市过程中得适当时候的后期。
第四节总结一个对银行绩效评估。
最新3000字英文参考文献及其翻译范例
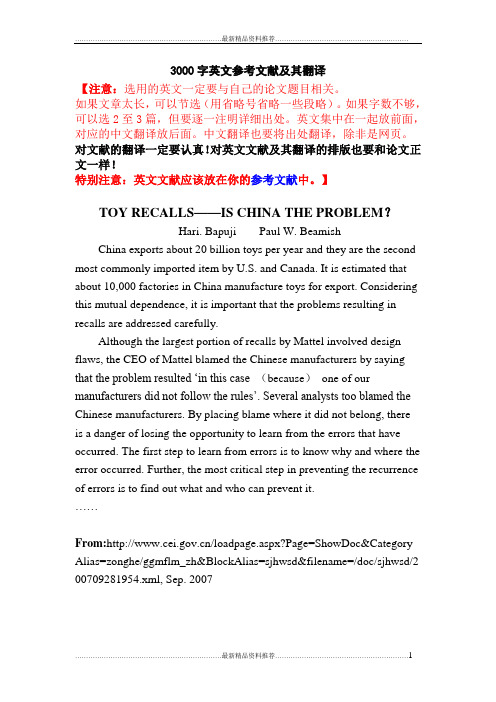
3000字英文参考文献及其翻译【注意:选用的英文一定要与自己的论文题目相关。
如果文章太长,可以节选(用省略号省略一些段略)。
如果字数不够,可以选2至3篇,但要逐一注明详细出处。
英文集中在一起放前面,对应的中文翻译放后面。
中文翻译也要将出处翻译,除非是网页。
对文献的翻译一定要认真!对英文文献及其翻译的排版也要和论文正文一样!特别注意:英文文献应该放在你的参考文献中。
】TOY RECALLS——IS CHINA THE PROBLEM?Hari. Bapuji Paul W. BeamishChina exports about 20 billion toys per year and they are the second most commonly imported item by U.S. and Canada. It is estimated that about 10,000 factories in China manufacture toys for export. Considering this mutual dependence, it is important that the problems resulting in recalls are addressed carefully.Although the largest portion of recalls by Mattel involved design flaws, the CEO of Mattel blamed the Chinese manufacturers by saying that the problem resulted ‘in this case (because)one of our manufacturers did not follow the rules’. Several analysts too blamed the Chinese manufacturers. By placing blame where it did not belong, thereis a danger of losing the opportunity to learn from the errors that have occurred. The first step to learn from errors is to know why and where the error occurred. Further, the most critical step in preventing the recurrence of errors is to find out what and who can prevent it.……From:/loadpage.aspx?Page=ShowDoc&Category Alias=zonghe/ggmflm_zh&BlockAlias=sjhwsd&filename=/doc/sjhwsd/2 00709281954.xml, Sep. 2007玩具召回——是中国的问题吗?哈里·巴普基保罗·比密什中国每年大约出口20亿美元的玩具,最常见是从美国和加拿大进口项目。
冲压模具成型外文翻译参考文献
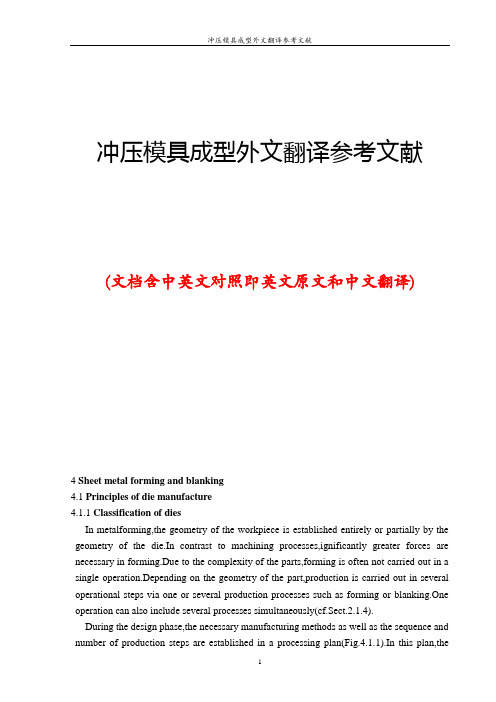
冲压模具成型外文翻译参考文献(文档含中英文对照即英文原文和中文翻译)4 Sheet metal forming and blanking4.1 Principles of die manufacture4.1.1 Classification of diesIn metalforming,the geometry of the workpiece is established entirely or partially by the geometry of the die.In contrast to machining processes,ignificantly greater forces are necessary in forming.Due to the complexity of the parts,forming is often not carried out in a single operation.Depending on the geometry of the part,production is carried out in several operational steps via one or several production processes such as forming or blanking.One operation can also include several processes simultaneously(cf.Sect.2.1.4).During the design phase,the necessary manufacturing methods as well as the sequence and number of production steps are established in a processing plan(Fig.4.1.1).In this plan,theavailability of machines,the planned production volumes of the part and other boundary conditions are taken into account.The aim is to minimize the number of dies to be used while keeping up a high level of operational reliability.The parts are greatly simplified right from their design stage by close collaboration between the Part Design and Production Departments in order to enable several forming and related blanking processes to be carried out in one forming station.Obviously,the more operations which are integrated into a single die,the more complex the structure of the die becomes.The consequences are higher costs,a decrease in output and a lower reliability.Fig.4.1.1 Production steps for the manufacture of an oil sumpTypes of diesThe type of die and the closely related transportation of the part between dies is determined in accordance with the forming procedure,the size of the part in question and the production volume of parts to be produced.The production of large sheet metal parts is carried out almost exclusively using single sets of dies.Typical parts can be found in automotive manufacture,the domestic appliance industry and radiator production.Suitable transfer systems,for example vacuum suction systems,allow the installation of double-action dies in a sufficiently large mounting area.In this way,for example,the right and left doors of a car can be formed jointly in one working stroke(cf.Fig.4.4.34).Large size single dies are installed in large presses.The transportation of the parts from oneforming station to another is carried out mechanically.In a press line with single presses installed one behind the other,feeders or robots can be used(cf.Fig.4.4.20 to 4.4.22),whilst in large-panel transfer presses,systems equipped with gripper rails(cf.Fig.4.4.29)or crossbar suction systems(cf.Fig.4.4.34)are used to transfer the parts.Transfer dies are used for the production of high volumes of smaller and medium size parts(Fig.4.1.2).They consist of several single dies,which are mounted on a common base plate.The sheet metal is fed through mostly in blank form and also transported individually from die to die.If this part transportation is automated,the press is called a transfer press.The largest transfer dies are used together with single dies in large-panel transfer presses(cf.Fig.4.4.32).In progressive dies,also known as progressive blanking dies,sheet metal parts are blanked in several stages;generally speaking no actual forming operation takes place.The sheet metal is fed from a coil or in the form of metal ing an appropriate arrangement of the blanks within the available width of the sheet metal,an optimal material usage is ensured(cf.Fig.4.5.2 to 4.5.5). The workpiece remains fixed to the strip skeleton up until the laFig.4.1.2 Transfer die set for the production of an automatic transmission for an automotive application-st operation.The parts are transferred when the entire strip is shifted further in the work flow direction after the blanking operation.The length of the shift is equal to the center line spacing of the dies and it is also called the step width.Side shears,very precise feeding devices or pilot pins ensure feed-related part accuracy.In the final production operation,the finished part,i.e.the last part in the sequence,is disconnected from the skeleton.A field of application for progressive blanking tools is,for example,in the production of metal rotors or stator blanks for electric motors(cf.Fig.4.6.11 and 4.6.20).In progressive compound dies smaller formed parts are produced in several sequential operations.In contrast to progressive dies,not only blanking but also forming operations areperformed.However, the workpiece also remains in the skeleton up to the last operation(Fig.4.1.3 and cf.Fig.4.7.2).Due to the height of the parts,the metal strip must be raised up,generally using lifting edges or similar lifting devices in order to allow the strip metal to be transported mechanically.Pressed metal parts which cannot be produced within a metal strip because of their geometrical dimensions are alternatively produced on transfer sets.Fig.4.1.3 Reinforcing part of a car produced in a strip by a compound die setNext to the dies already mentioned,a series of special dies are available for special individual applications.These dies are,as a rule,used separately.Special operations make it possible,however,for special dies to be integrated into an operational Sequence.Thus,for example,in flanging dies several metal parts can be joined together positively through the bending of certain metal sections(Fig.4.1.4and cf.Fig.2.1.34).During this operation reinforcing parts,glue or other components can be introduced.Other special dies locate special connecting elements directly into the press.Sorting and positioning elements,for example,bring stamping nuts synchronised with the press cycles into the correct position so that the punch heads can join them with the sheet metal part(Fig.4.1.5).If there is sufficient space available,forming and blanking operations can be carried out on the same die.Further examples include bending,collar-forming,stamping,fine blanking,wobble blanking and welding operations(cf.Fig.4.7.14 and4.7.15).Fig.4.1.4 A hemming dieFig.4.1.5 A pressed part with an integrated punched nut4.1.2 Die developmentTraditionally the business of die engineering has been influenced by the automotive industry.The following observations about the die development are mostly related to body panel die construction.Essential statements are,however,made in a fundamental context,so that they are applicable to all areas involved with the production of sheet-metal forming and blanking dies.Timing cycle for a mass produced car body panelUntil the end of the 1980s some car models were still being produced for six to eight years more or less unchanged or in slightly modified form.Today,however,production time cycles are set for only five years or less(Fig.4.1.6).Following the new different model policy,the demands ondie makers have also changed prehensive contracts of much greater scope such as Simultaneous Engineering(SE)contracts are becoming increasingly common.As a result,the die maker is often involved at the initial development phase of the metal part as well as in the planning phase for the production process.Therefore,a muchbroader involvement is established well before the actual die development is initiated.Fig.4.1.6 Time schedule for a mass produced car body panelThe timetable of an SE projectWithin the context of the production process for car body panels,only a minimal amount of time is allocated to allow for the manufacture of the dies.With large scale dies there is a run-up period of about 10 months in which design and die try-out are included.In complex SE projects,which have to be completed in 1.5 to 2 years,parallel tasks must be carried out.Furthermore,additional resources must be provided before and after delivery of the dies.These short periods call for pre-cise planning,specific know-how,available capacity and the use of the latest technological and communications systems.The timetable shows the individual activities during the manufacturing of the dies for the production of the sheet metal parts(Fig.4.1.7).The time phases for large scale dies are more or less similar so that this timetable can be considered to be valid in general.Data record and part drawingThe data record and the part drawing serve as the basis for all subsequent processing steps.They describe all the details of the parts to be produced. The information given in theFig.4.1.7 Timetable for an SE projectpart drawing includes: part identification,part numbering,sheet metal thickness,sheet metal quality,tolerances of the finished part etc.(cf.Fig.4.7.17).To avoid the production of physical models(master patterns),the CAD data should describe the geometry of the part completely by means of line,surface or volume models.As a general rule,high quality surface data with a completely filleted and closed surface geometry must be made available to all the participants in a project as early as possible.Process plan and draw developmentThe process plan,which means the operational sequence to be followed in the production of the sheet metal component,is developed from the data record of the finished part(cf.Fig.4.1.1).Already at this point in time,various boundary conditions must be taken into account:the sheet metal material,the press to be used,transfer of the parts into the press,the transportation of scrap materials,the undercuts as well as thesliding pin installations and their adjustment.The draw development,i.e.the computer aided design and layout of the blank holder area of the part in the first forming stage–if need bealso the second stage–,requires a process planner with considerable experience(Fig.4.1.8).In order to recognize and avoid problems in areas which are difficult to draw,it is necessary to manufacture a physical analysis model of the draw development.With this model,theforming conditions of the drawn part can be reviewed and final modifications introduced,which are eventually incorporated into the data record(Fig.4.1.9).This process is being replaced to some extent by intelligent simulation methods,through which the potential defects of the formed component can be predicted and analysed interactively on the computer display.Die designAfter release of the process plan and draw development and the press,the design of the die can be started.As a rule,at this stage,the standards and manufacturing specifications required by the client must be considered.Thus,it is possible to obtain a unified die design and to consider the particular requests of the customer related to warehousing of standard,replacement and wear parts.Many dies need to be designed so that they can be installed in different types of presses.Dies are frequently installed both in a production press as well as in two different separate back-up presses.In this context,the layout of the die clamping elements,pressure pins and scrap disposal channels on different presses must be taken into account.Furthermore,it must be noted that drawing dies working in a single-action press may be installed in a double-action press(cf.Sect.3.1.3 and Fig.4.1.16).Fig.4.1.8 CAD data record for a draw developmentIn the design and sizing of the die,it is particularly important to consider the freedom of movement of the gripper rail and the crossbar transfer elements(cf.Sect.4.1.6).These describe the relative movements between the components of the press transfer system and the die components during a complete press working stroke.The lifting movement of the press slide,the opening and closing movements of the gripper rails and the lengthwise movement of the whole transfer are all superimposed.The dies are designed so that collisions are avoided and a minimum clearance of about 20 mm is set between all the moving parts.4 金属板料的成形及冲裁4. 模具制造原理4.1.1模具的分类在金属成形的过程中,工件的几何形状完全或部分建立在模具几何形状的基础上的。
外文文献翻译(英文+中文对照)
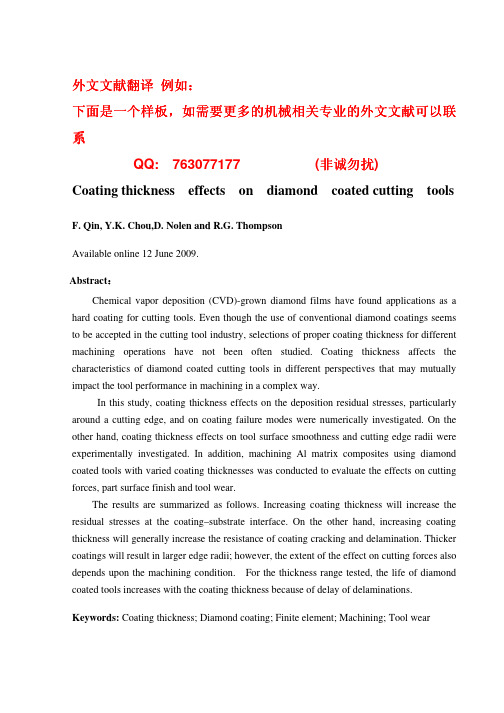
外文文献翻译 例如例如::下面是一个样板下面是一个样板,,如需要更多的机械相关专业的外文文献可以联系QQ: 763077177 (非诚勿扰) Coating thickness effects on diamond coated cutting tools F. Qin, Y.K. Chou,D. Nolen and R.G. ThompsonAvailable online 12 June 2009. Abstract :Chemical vapor deposition (CVD)-grown diamond films have found applications as a hard coating for cutting tools. Even though the use of conventional diamond coatings seems to be accepted in the cutting tool industry, selections of proper coating thickness for different machining operations have not been often studied. Coating thickness affects the characteristics of diamond coated cutting tools in different perspectives that may mutually impact the tool performance in machining in a complex way.In this study, coating thickness effects on the deposition residual stresses, particularly around a cutting edge, and on coating failure modes were numerically investigated. On the other hand, coating thickness effects on tool surface smoothness and cutting edge radii were experimentally investigated. In addition, machining Al matrix composites using diamond coated tools with varied coating thicknesses was conducted to evaluate the effects on cutting forces, part surface finish and tool wear.The results are summarized as follows. Increasing coating thickness will increase the residual stresses at the coating–substrate interface. On the other hand, increasing coating thickness will generally increase the resistance of coating cracking and delamination. Thicker coatings will result in larger edge radii; however, the extent of the effect on cutting forces also depends upon the machining condition. For the thickness range tested, the life of diamond coated tools increases with the coating thickness because of delay of delaminations. Keywords: Coating thickness; Diamond coating; Finite element; Machining; Tool wear1. IntroductionDiamond coatings produced by chemical vapor deposition (CVD) technologies have been increasingly explored for cutting tool applications. Diamond coated tools have great potential in various machining applications and an advantage in fabrications of cutting tools with complex geometry such as drills. Increased usages of lightweight high-strength components have also resulted in significant interests in diamond coating tools. Hot-filament CVD is one of common processes of diamond coatings and diamond films as thick as 50 µm have been deposited on various materials including cobalt-cemented tungsten carbide (WC-Co) . There have also been different CVD technologies, e.g., microwave plasma assisted CVD , developed to enhance the deposition process as well as the film quality too. However, despite the superior tribological and mechanical properties, the practical applications of diamond coated tools are still limited.Coating thickness is one of the most important attributes to the coating system performance. Coating thickness effects on tribological performance have been widely studied. In general, thicker coatings exhibited better scratch/wear resistance performance than thinner ones due to their better load-carrying capacity. However, there are also reports that claim otherwise and . For example, Dorner et al. discovered, that the thickness of diamond-like-coating (DLC), in a range of 0.7–3.5 µm, does not influence the wear resistance of the DLC–Ti6Al4V . For cutting tool applications, however, coating thickness may have a more complicated role since its effects may be augmented around the cutting edge. Coating thickness effects on diamond coated tools are not frequently reported. Kanda et al. conducted cutting tests using diamond-coated tooling . The author claimed that the increased film thickness is generally favorable to tool life. However, thicker films will result in the decrease in the transverse rupture strength that greatly impacts the performance in high speed or interrupted machining. In addition, higher cutting forces were observed for the tools with increased diamond coating thickness due to the increased cutting edge radius. Quadrini et al. studied diamond coated small mills for dental applications . The authors tested different coating thickness and noted that thick coatings induce high cutting forces due to increased coating surface roughness and enlarged edge rounding. Such effects may contribute to the tool failure in milling ceramic materials. The authors further indicated tools with thin coatings results in optimal cutting of polymer matrix composite . Further, Torres et al. studied diamondcoated micro-endmills with two levels of coating thickness . The authors also indicated that the thinner coating can further reduce cutting forces which are attributed to the decrease in the frictional force and adhesion.Coating thickness effects of different coating-material tools have also been studied. For single layer systems, an optimal coating thickness may exist for machining performance. For example, Tuffy et al. reported that an optimal coating thickness of TiN by PVD technology exists for specific machining conditions . Based on testing results, for a range from 1.75 to 7.5 µm TiN coating, thickness of 3.5 µm exhibit the best turning performance. In a separate study, Malik et al. also suggested that there is an optimal thickness of TiN coating on HSS cutting tools when machining free cutting steels . However, for multilayer coating systems, no such an optimum coating thickness exists for machining performance .The objective of this study was to experimentally investigate coating thickness effects of diamond coated tools on machining performance — tool wear and cutting forces. Diamond coated tools were fabricated, by microwave plasma assisted CVD, with different coating thicknesses. The diamond coated tools were examined in morphology and edge radii by white-light interferometry. The diamond coated tools were then evaluated by machining aluminum matrix composite in dry. In addition, deposition thermal residual stresses and critical load for coating failures that affect the performance of diamond coated tools were analytically examined.2. Experimental investigationThe substrates used for diamond coating experiments, square-shaped inserts (SPG422), were fine-grain WC with 6 wt.% cobalt. The edge radius and surface textures of cutting inserts prior to coating was measured by a white-light interferometer, NT1100 from Veeco Metrology.Prior to the deposition, chemical etching treatment was conducted on inserts to remove the surface cobalt and roughen substrate surface. Moreover, all tool inserts were ultrasonically vibrated in diamond/water slurry to increase the nucleation density. For the coating process, diamond films were deposited using a high-power microwave plasma-assisted CVD process.A gas mixture of methane in hydrogen, 750–1000 sccm with 4.4–7.3% of methane/hydrogen ratio, was used as the feedstock gas. Nitrogen gas, 2.75–5.5 sccm, was inserted to obtain nanostructures by preventing columnar growth. The pressure was about 30–55 Torr and the substrate temperature was about 685–830 °C. A forward power of 4.5–5.0 kW with a low deposition rate obtained a thin coating; a greater forward power of 8.0–8.5 kW with a highdeposition rate obtained thick coatings, two thicknesses by varying deposition time. The coated inserts were further inspected by the interferometer.A computer numerical control lathe, Hardinge Cobra 42, was used to perform machining experiments, outer diameter turning, to evaluate the tool wear of diamond coated tools. With the tool holder used, the diamond coated cutting inserts formed a 0° rake angle, 11° relief angle, and 75° lead angle. The workpieces were round bars made of A359/SiC-20p composite. The machining conditions used were 4 m/s cutting speed, 0.15 mm/rev feed, 1 mm depth of cut and no coolant was applied. The selection of machining parameters was based upon previous experiences. For each coating thickness, two tests were repeated. During machining testing, the cutting inserts were periodically inspected by optical microscopy to measure the flank wear-land size. Worn tools after testing were also examined by scanning electron microscopy (SEM). In addition, cutting forces were monitored during machining using a Kistler dynamometer.5. ConclusionsIn this study, the coating thickness effects on diamond coated cutting tools were studied from different perspectives. Deposition residual stresses in the tool due to thermal mismatch were investigated by FE simulations and coating thickness effects on the interface stresses were quantified. In addition, indentation simulations of a diamond coated WC substrate with the interface modeled by the cohesive zone were applied to analyze the coating system failures. Moreover, diamond coated tools with different thicknesses were fabricated and experimentally investigated on surface morphology, edge rounding, as well as tool wear and cutting forces in machining. The major results are summarized as follows.(1) Increase of coating thickness significantly increases the interface residual stresses, though little change in bulk surface stresses.(2) For thick coatings, the critical load for coating failure decreases with increasing coating thickness. However, such a trend is opposite for thin coatings, for which radial cracking is the coating failure mode. Moreover, thicker coatings have greater delamination resistance.(3) In addition, increasing the coating thickness will increase the edge radius. However, for the coating thickness range studied, 4–29 µm, and with the large feed used, cutting forces were affected only marginally.(4) Despite of greater interface residual stresses, increasing the diamond coating thickness, for the range studied, seem to increase tool life by delay of coating delaminations.AcknowledgementsThis research is supported by National Science Foundation, Grant No.: CMMI 0728228. P. Lu provided assistance in some analyses.金刚石涂层刀具的涂层厚度的影响作者:F. Qin, Y.K. Chou,D. Nolen and R.G. Thompson发表日期:2009摘要:化学气相沉积法(CVD),金刚石薄膜的发现,作为涂层刀具的应用。
参考文献中文的英文对照
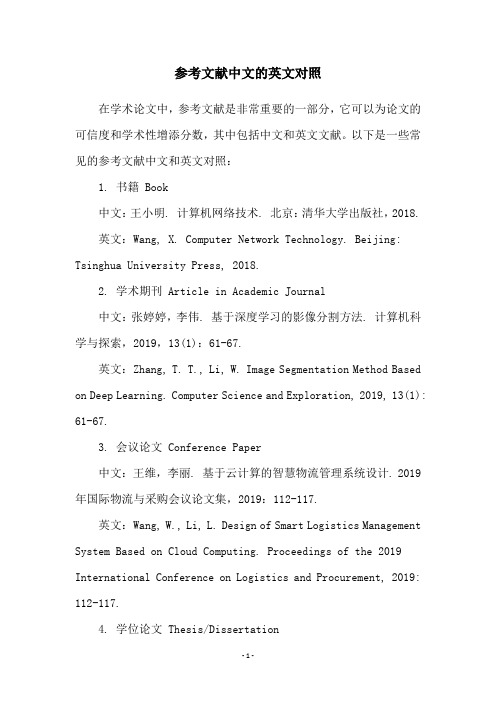
参考文献中文的英文对照在学术论文中,参考文献是非常重要的一部分,它可以为论文的可信度和学术性增添分数,其中包括中文和英文文献。
以下是一些常见的参考文献中文和英文对照:1. 书籍 Book中文:王小明. 计算机网络技术. 北京:清华大学出版社,2018.英文:Wang, X. Computer Network Technology. Beijing: Tsinghua University Press, 2018.2. 学术期刊 Article in Academic Journal中文:张婷婷,李伟. 基于深度学习的影像分割方法. 计算机科学与探索,2019,13(1):61-67.英文:Zhang, T. T., Li, W. Image Segmentation Method Based on Deep Learning. Computer Science and Exploration, 2019, 13(1): 61-67.3. 会议论文 Conference Paper中文:王维,李丽. 基于云计算的智慧物流管理系统设计. 2019年国际物流与采购会议论文集,2019:112-117.英文:Wang, W., Li, L. Design of Smart Logistics Management System Based on Cloud Computing. Proceedings of the 2019 International Conference on Logistics and Procurement, 2019: 112-117.4. 学位论文 Thesis/Dissertation中文:李晓华. 基于模糊神经网络的水质评价模型研究. 博士学位论文,长春:吉林大学,2018.英文:Li, X. H. Research on Water Quality Evaluation Model Based on Fuzzy Neural Network. Doctoral Dissertation, Changchun: Jilin University, 2018.5. 报告 Report中文:国家统计局. 2019年国民经济和社会发展统计公报. 北京:中国统计出版社,2019.英文:National Bureau of Statistics. Statistical Communique of the People's Republic of China on the 2019 National Economic and Social Development. Beijing: China Statistics Press, 2019.以上是一些常见的参考文献中文和英文对照,希望对大家写作有所帮助。
- 1、下载文档前请自行甄别文档内容的完整性,平台不提供额外的编辑、内容补充、找答案等附加服务。
- 2、"仅部分预览"的文档,不可在线预览部分如存在完整性等问题,可反馈申请退款(可完整预览的文档不适用该条件!)。
- 3、如文档侵犯您的权益,请联系客服反馈,我们会尽快为您处理(人工客服工作时间:9:00-18:30)。
基于4G LTE技术的高速铁路移动通信系统KS Solanki教授,Kratika ChouhanUjjain工程学院,印度Madhya Pradesh的Ujjain摘要:随着时间发展,高速铁路(HSR)要求可靠的,安全的列车运行和乘客通信。
为了实现这个目标,HSR的系统需要更高的带宽和更短的响应时间,而且HSR的旧技术需要进行发展,开发新技术,改进现有的架构和控制成本。
为了满足这一要求,HSR采用了GSM的演进GSM-R技术,但它并不能满足客户的需求。
因此采用了新技术LTE-R,它提供了更高的带宽,并且在高速下提供了更高的客户满意度。
本文介绍了LTE-R,给出GSM-R与LTE-R之间的比较结果,并描述了在高速下哪种铁路移动通信系统更好。
关键词:高速铁路,LTE,GSM,通信和信令系统一介绍高速铁路需要提高对移动通信系统的要求。
随着这种改进,其网络架构和硬件设备必须适应高达500公里/小时的列车速度。
HSR还需要快速切换功能。
因此,为了解决这些问题,H SR需要一种名为LTE-R的新技术,基于LTE-R的HSR提供高数据传输速率,更高带宽和低延迟。
LTE-R能够处理日益增长的业务量,确保乘客安全并提供实时多媒体信息。
随着列车速度的不断提高,可靠的宽带通信系统对于高铁移动通信至关重要。
HSR的应用服务质量(QO S)测量,包括如数据速率,误码率(BER)和传输延迟。
为了实现HSR的运营需求,需要一个能够与LTE保持一致的能力的新系统,提供新的业务,但仍能够与GSM-R长时间共存。
HSR系统选择合适的无线通信系统时,需要考虑性能,服务,属性,频段和工业支持等问题。
4G LTE系统与第三代(3G)系统相比,它具有简单的扁平架构, 高数据速率和低延迟。
在LTE的性能和成熟度水平上,LTE- railway(LTE-R)将可能成为下一代H SR通信系统。
二LTE-R系统描述考虑LTE-R的频率和频谱使用,对为高速铁路(HSR)通信提供更高效的数据传输非常重要。
高铁是重要的战略基础设施,因此需要专门为其分配大量的频谱块。
包括欧洲铁路局(ERA),中国铁路在内的一些行业机构正试图对高铁使用的频谱进行划分。
目前,尽管在一些国家也使用700-900MHz频段,但大多数LTE系统工作在1GHz以上的频段,例如 1.8,2.1,2.3和2.6GHz。
较高的频带提供较大的带宽,提供较高的数据速率,而较低的频带对应较长的距离。
由于高频段传播损耗较大,衰落更严重,因此建议LTE-R小区的半径保持小于2km[由于HSR中信噪比(SNR)的严格要求],但是这导致频繁切换和为满足更高的BS密度而投资更多资金。
因此,450-470 MHz,800MHz和1.4GHz等低频带已被广泛考虑。
450-470MHz频段已经被铁路行业所采用。
此外,LTE的载波聚合能力将允许使用不同的频带来克服容量问题。
图1(b)给出了中国450〜470 MHz频率的详细分配[12],在该频带内为LTE-R分配足够的带宽是可行的。
在欧洲,UIC的FRMCS 希望通过在当前的GSM-R投资基础之上,重复使用现有的无线站点。
这可以节省高达80-90%的网络成本。
铁路也考虑继续使用GSM-R无线,因此,1 GHz以下的频谱划分在欧洲更具成本效益。
但是,频段的选择取决于政府政策,因国家而异。
标准LTE包括演进分组核心(EPC)的核心网络和演进通用陆地无线电的无线电接入网络(E-UTRAN)。
基于互联网协议(IP)的EPC支持语音和数据到小区塔的无缝切换,并且每个E-UTRAN小区将通过高速分组接入(HSPA)支持高数据和语音容量。
作为HSR下一代通信系统的候选者。
LTE-R继承了LTE的所有重要特性,并提供额外的无线接入系统与车载设备(OBU)交换无线信号,与HSR特定需求相匹配。
图2给出了根据[4]的LTE-R的未来架构,它表明LTE-R的核心网络以后兼容GSM-R。
与公众LTE网络相比,LTE-R在架构,系统参数,网络布局,业务和QoS 等方面存在很多差异。
列车信息由RB C和机载无线电设备检测。
这提高了列车跟踪的准确性和列车调度的效率。
LTER也可用于为未来的自动驾驶系统提供信息传输。
基于未来HSR通信的QoS要求,LTE-R的优选参数总结在表1中。
请注意,LTE-R的可靠性将超过容量。
该网络必须能够在复杂的铁路环境中以500km/h的速度运行。
因此,正交相移键控(QPSK)调制是优选的,并且必须尽可能减少重传的分组数量。
三LTE-R服务HSR通信打算使用一个完善的/现成的系统,这些系统需要对某些特定需求的服务级别定义进行。
正如E-Train项目[6]所建议的, LTE-R应提供一系列服务来提高安全性,服务质量和效率。
与GSM-R的传统业务相比,描述了LTE-R的一些特性。
1)控制系统的信息传输:为了与ETCS-3或中国列车控制系统第4级(CTCS-4)兼容,LTE-R通过无线通信实现控制信息的实时信息传输,延迟时间<50 毫秒.当ETCS-2 / CTCS-3中的轨道电路检测到列车的位置信息时,在ETCS-3 / CTCS-4和LTE -R中,火车的位置信息被RBC和机载无线电设备检测到。
这提高了列车跟踪的准确性和列车调度的效率。
LTE-R也可用于为未来的自动驾驶系统提供信息传输。
2) 实时监控:LTE-R提供前轨道,驾驶室和汽车连接器状态的视频监控;轨道状况的实时信息监测(如温度和探伤);对铁路基础设施(如桥梁和隧道)视频监控以避免自然灾害;和对交叉轨道的视频监控以检测低温下的冻结。
监控信息将与控制中心和高速列车实时共享,延时小于300毫秒。
尽管上述一些监视可以通过有线通信进行,但基于无线的LTER系统对部署和维护而言更具成本效益。
3) 培训多媒体调度:LTE-R为调度员提供驾驶员和车场的全部调度信息(包括文本,数据,语音,图像,视频等),提高调度效率。
它支持丰富的功能,如语音中继,动态分组,临时组呼,短消息和多媒体消息。
4) 铁路应急通信:当发生自然灾害,事故或其他紧急情况时,需要在事故现场和救援中心之间建立即时通信,以提供语音,视频,数据和图像传输。
铁路应急通信系统使用铁路专用网络,以确保与GSM-R相比快速部署和更快的响应速度(延迟<100ms)。
5) 铁路物联网(IOT):LTE-R提供铁路物联网服务,例如实时查询和跟踪火车和货物。
它有助于提高运输效率并延长服务范围。
此外,铁路物联网还可以提高列车的安全性。
今天的大多数列车依靠位于偏远地区的轨道交换机。
借助IOT和远程监控,可以将交换机的轨道基础设施重新转换为电力线,可以自动执行许多常规安全检查并降低维护成本。
除了之前列出的功能之外,还应包括LTE-R的其他一些服务,例如动态座位预留,移动电子票务和乘客信息的无线互动。
基于UIC,中国铁路和ERA的技术报告,图3总结了LTE-R未来可能提供的服务。
值得注意的是,高速列车内的乘客的宽带无线接入不由LTE-R提供因为其带宽有限。
一些针对火车乘客的宽带无线接入的候选者已经被探讨过,例如Wi-Fi,全球微波接入互操作性(WiMAX), 3G / 4G / 5G,卫星通信以及光纤无线电(RoF) 技术[13]。
四LTE-R挑战与LTE-R相关的挑战有以下几个。
1) 特定于HSR的场景:在的LTE 标准中,提出了HSR的信道模型,其仅包括两种场景,即开放空间和隧道,并且在两种场景中都使用非衰落信道模型。
但是,如[15]所示,HSR的严格要求(高速,铁轨平坦度等)导致许多特定于HSR的环境,例如高架桥,岩屑和隧道。
这些情景中的传播特性是不同于传统的蜂窝通信,可能会明显影响GSM-R 和LTE-R的系统性能。
过去,为了描述GSM-R频带的HSR信道,进行了一些测量,并且已经提出了基于情景的路径损耗和阴影衰落模型,用于930MHz的GSM-R。
然而,这项工作仍在进行中,许多科学问题尚未在LTE-R频段得到解决,例如传播损耗,多径分量(MPC)的几何分布以及这些HSR特有的二维/三维角度估计环境。
有必要LTE-R的链路预算和网络设计开发一系列信道模型,并且需要广泛的信道测量。
2) 高机动性:高速列车通常以350公里/小时的速度运行,而LTE-R 则支持500公里/小时。
高速度导致一系列问题。
首先,高速度导致信道的不平稳,因为在短时间段内,列车通过MPC发生显著变化的大区域。
非平稳性的表征特别重要,因为它影响单载波和多载波系统的BER(误码率)。
其次,高速度导致接收频率的偏移,称为多普勒频移。
例如,如果频率为2.6 GHz,则350km/h的最大多普勒频移为843Hz,而10km/h的行人移动速度仅为24 Hz。
严重的多普勒频移会导致信号的相移,并可能损害角度调制信号的接收。
然而,由于高速列车大多以已知速度沿着预定线路移动,因此可以通过使用实时记录的速度和位置信息来跟踪和补偿多普勒频移。
第三,由于高速,HSR环境中会出现大的多普勒扩展。
对于LTE-R(宽带系统),多普勒扩展通常会导致信号与干扰加噪声比的损失,并会妨碍载波恢复和同步。
多普勒扩展也是正交频分复用(OFDM)系统特别关心的问题,因为它会破坏OFDM子载波的正交性。
应考虑几种方法,如频域均衡和载波间干扰自消除方案[18]。
3) 延迟扩展:延迟扩散会导致OF DM子载波之间的正交性的丢失,并且应该使用称为循环前缀(CP)的特殊类型的保护间隔。
延迟弥散决定了所需的CP长度。
LTE支持短(4.76毫秒)和长(16.67毫秒)CP方案。
对于短CP方案,两个MPC之间相应的最大路径长度差为1.4公里。
由于铁路通信的目标是提供线性覆盖,因此广泛使用沿轨道具有主瓣的定向BS天线,因此发射功率集中在窄条形区域。
直观地说,我们预计短CP方案对于LTE-R是足够的。
这主要是因为高速列车主要在(半)郊区/郊区环境中行驶,而在这些环境中,散射点很少。
但是,在一些具有丰富多次反射的特殊环境中,如岩屑,预计会出现较大的延迟差异(注意这是需要基于测量的验证),并应使用较长的CP方案。
另一个大型延误传播的例子发生在沿着铁轨[19]的山区,特别是在火车进入和离开隧道前后。
需要进行更多测量来解决HSR环境中延迟传播的现象,并且需要像使用通用LTE一样根据环境调整CP。
4) 线性覆盖:在HSR中,使用沿轨道定向天线的线性覆盖,其中定向BS 天线将它们的主瓣沿着轨道定位,以使其功率效率更高。
线性覆盖带来一些好处,例如,与火车的已知位置相比,可以设计具有良好性能的基于距离/时间的波束形成算法。
然而,值得注意的是,线性覆盖的链路预算和性能分析与蜂窝系统的环形小区不同,例如用于确定覆盖区域的百分比。