铝合金的时效强化是如何进行和完成的
铝合金时效硬化现象
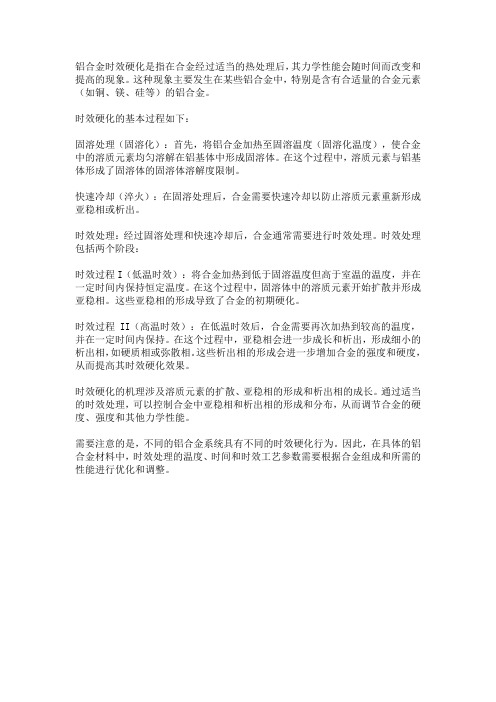
铝合金时效硬化是指在合金经过适当的热处理后,其力学性能会随时间而改变和提高的现象。
这种现象主要发生在某些铝合金中,特别是含有合适量的合金元素(如铜、镁、硅等)的铝合金。
时效硬化的基本过程如下:
固溶处理(固溶化):首先,将铝合金加热至固溶温度(固溶化温度),使合金中的溶质元素均匀溶解在铝基体中形成固溶体。
在这个过程中,溶质元素与铝基体形成了固溶体的固溶体溶解度限制。
快速冷却(淬火):在固溶处理后,合金需要快速冷却以防止溶质元素重新形成亚稳相或析出。
时效处理:经过固溶处理和快速冷却后,合金通常需要进行时效处理。
时效处理包括两个阶段:
时效过程I(低温时效):将合金加热到低于固溶温度但高于室温的温度,并在一定时间内保持恒定温度。
在这个过程中,固溶体中的溶质元素开始扩散并形成亚稳相。
这些亚稳相的形成导致了合金的初期硬化。
时效过程II(高温时效):在低温时效后,合金需要再次加热到较高的温度,并在一定时间内保持。
在这个过程中,亚稳相会进一步成长和析出,形成细小的析出相,如硬质相或弥散相。
这些析出相的形成会进一步增加合金的强度和硬度,从而提高其时效硬化效果。
时效硬化的机理涉及溶质元素的扩散、亚稳相的形成和析出相的成长。
通过适当的时效处理,可以控制合金中亚稳相和析出相的形成和分布,从而调节合金的硬度、强度和其他力学性能。
需要注意的是,不同的铝合金系统具有不同的时效硬化行为。
因此,在具体的铝合金材料中,时效处理的温度、时间和时效工艺参数需要根据合金组成和所需的性能进行优化和调整。
铝合金时效处理工艺
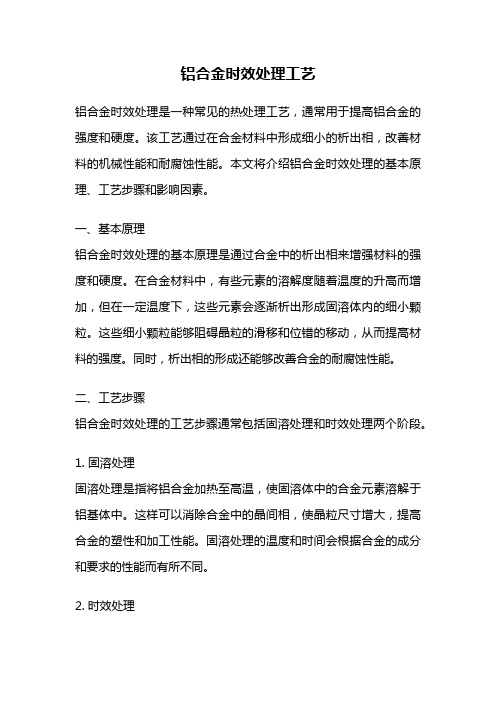
铝合金时效处理工艺铝合金时效处理是一种常见的热处理工艺,通常用于提高铝合金的强度和硬度。
该工艺通过在合金材料中形成细小的析出相,改善材料的机械性能和耐腐蚀性能。
本文将介绍铝合金时效处理的基本原理、工艺步骤和影响因素。
一、基本原理铝合金时效处理的基本原理是通过合金中的析出相来增强材料的强度和硬度。
在合金材料中,有些元素的溶解度随着温度的升高而增加,但在一定温度下,这些元素会逐渐析出形成固溶体内的细小颗粒。
这些细小颗粒能够阻碍晶粒的滑移和位错的移动,从而提高材料的强度。
同时,析出相的形成还能够改善合金的耐腐蚀性能。
二、工艺步骤铝合金时效处理的工艺步骤通常包括固溶处理和时效处理两个阶段。
1. 固溶处理固溶处理是指将铝合金加热至高温,使固溶体中的合金元素溶解于铝基体中。
这样可以消除合金中的晶间相,使晶粒尺寸增大,提高合金的塑性和加工性能。
固溶处理的温度和时间会根据合金的成分和要求的性能而有所不同。
2. 时效处理时效处理是指在固溶处理后,将合金材料冷却至室温,并在一定温度下保持一定时间。
在这个过程中,合金中的合金元素会逐渐析出形成细小的析出相。
这些析出相的形成不仅能够提高合金的强度和硬度,还能够改善合金的耐腐蚀性能。
时效处理的温度和时间也会根据合金的成分和要求的性能而有所不同。
三、影响因素铝合金时效处理的效果会受到多种因素的影响,包括合金成分、固溶处理温度、时效处理温度和时间等。
1. 合金成分不同的合金成分会影响合金中析出相的类型和数量,从而影响合金的强度和硬度。
一般来说,含有大量合金元素的合金,析出相的数量和尺寸会更多更大,因此强度和硬度会相应增加。
2. 固溶处理温度固溶处理温度的选择会影响合金中合金元素的溶解度和晶粒尺寸。
较高的固溶处理温度可以提高合金元素的溶解度,但也会导致晶粒尺寸增大,从而降低合金的强度。
3. 时效处理温度和时间时效处理温度和时间的选择会直接影响到析出相的形成和生长。
较高的时效处理温度和较长的时效处理时间可以促进析出相的形成和生长,从而提高合金的强度和硬度。
铝合金欠时效,过时效国标
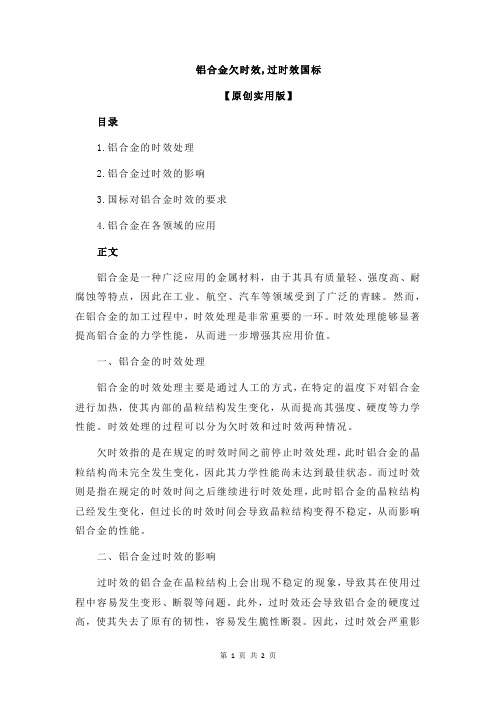
铝合金欠时效,过时效国标【原创实用版】目录1.铝合金的时效处理2.铝合金过时效的影响3.国标对铝合金时效的要求4.铝合金在各领域的应用正文铝合金是一种广泛应用的金属材料,由于其具有质量轻、强度高、耐腐蚀等特点,因此在工业、航空、汽车等领域受到了广泛的青睐。
然而,在铝合金的加工过程中,时效处理是非常重要的一环。
时效处理能够显著提高铝合金的力学性能,从而进一步增强其应用价值。
一、铝合金的时效处理铝合金的时效处理主要是通过人工的方式,在特定的温度下对铝合金进行加热,使其内部的晶粒结构发生变化,从而提高其强度、硬度等力学性能。
时效处理的过程可以分为欠时效和过时效两种情况。
欠时效指的是在规定的时效时间之前停止时效处理,此时铝合金的晶粒结构尚未完全发生变化,因此其力学性能尚未达到最佳状态。
而过时效则是指在规定的时效时间之后继续进行时效处理,此时铝合金的晶粒结构已经发生变化,但过长的时效时间会导致晶粒结构变得不稳定,从而影响铝合金的性能。
二、铝合金过时效的影响过时效的铝合金在晶粒结构上会出现不稳定的现象,导致其在使用过程中容易发生变形、断裂等问题。
此外,过时效还会导致铝合金的硬度过高,使其失去了原有的韧性,容易发生脆性断裂。
因此,过时效会严重影响铝合金的性能和使用寿命。
三、国标对铝合金时效的要求我国国家标准对铝合金的时效处理有严格的要求,规定了不同类型铝合金的时效温度、时效时间等参数。
在铝合金的生产加工过程中,必须按照国家标准的要求进行时效处理,以确保铝合金的性能和使用寿命。
四、铝合金在各领域的应用铝合金由于其优异的性能,被广泛应用于各个领域。
例如,在航空领域,铝合金被用于制造飞机机身、发动机等部件;在汽车领域,铝合金被用于制造发动机、轮毂等部件;在建筑领域,铝合金被用于制造门窗、幕墙等结构件。
随着铝合金加工技术的不断发展,其在各个领域的应用将更加广泛。
总之,铝合金的时效处理对其性能和使用寿命具有重要影响。
铝合金强化方法

铝合金强化方法入后通过以下几个方面对铝进行强化。
1.固溶强化合金元素加入纯铝中形成无限固溶体或有限固溶体,不仅能获得高的强度,而且还能获得优良的塑性与良好的压力加工性能。
在一般铝合金中固溶强化最常用的合金元素是铜、镁、锰、锌、硅、镍等元素。
一般铝的合金化都形成有限的固溶体,如Al-Cu,Al-Mg,Al-Zn,Al-Si,Al-Mn等二元合金均形成有限固溶体,并且都有较大的极限溶解度能起较大的固溶强化效果。
2.时效强化铝合金热处理后可以得到过饱和的铝基固溶体。
这种过饱和铝基固溶体在室温或加热到某一温度时,其强度和硬度随时间和延长而增高,但塑性降低。
这个过程就称时效。
时效过程中使合金的强度、硬度增高的现象称为时效强化或时效硬化。
3.过剩相强化当铝中加入的合金元素含水量超过其极限溶解度时,淬火加热时便有一部分不能溶入固溶体的第二相出现称之为过剩相。
在铝合金中过剩相多为硬而脆的金属间化合物。
它们在合金中起阻碍滑移和位错运动的作用,使强度、硬度提高,而塑性、韧性降低。
合金中过剩相的数量愈多,其强化效果愈好,但过剩相多时,由于合金变脆而导致强度、塑性降低。
4细化组织强化在铝合中添加微量元素细化组织是提高铝合金力学性能的另一种重要手段。
变形铝合金中添加微量钛、锆、铍、锶以及稀土元素,它们能形成难熔化合物,在合金结晶时作为非自发晶核,起细化晶粒作用,提高合金的强度和塑性。
铸造铝合金中常加入微量元素作变质处理来细化合金组织,提高强度和塑性。
变质处理对不能热处理强化或强化效果不大的铸造铝合金和变形铝合金具有特别重要的意义。
比如在铝硅铸造铝合金中加入微量钠或钠盐或锑作变质剂进行变质处理,细化组织可以显著提高塑性和强度。
同样在铸造铝合金中加入少量锰、铬、钴等元素能使杂质铁形成的板块状或针状化合物AlFeSi细化,提高塑性,加入微量锶可消除或减少初晶硅,并使共晶硅细化;粒子园整度提高。
5冷变形强化冷变形强化亦称冷作硬化,即金属材料在再结晶温度以下冷变形,冷变形时,金属内部位错密度增大,且相互缠结并形成胞状结构,阻碍位错运动。
铝合金强化挤压方法
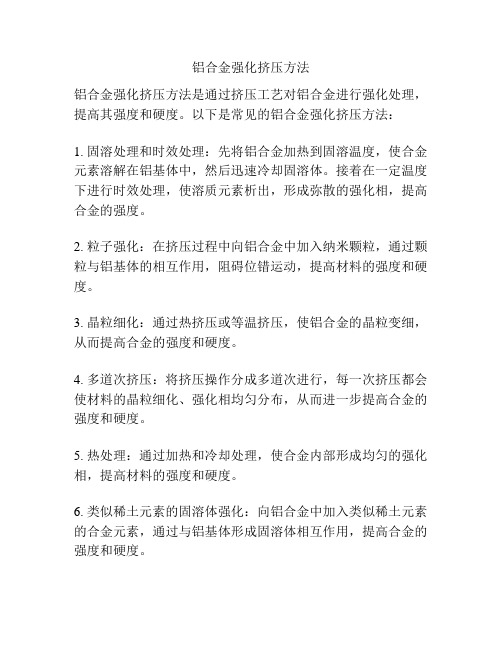
铝合金强化挤压方法
铝合金强化挤压方法是通过挤压工艺对铝合金进行强化处理,提高其强度和硬度。
以下是常见的铝合金强化挤压方法:
1. 固溶处理和时效处理:先将铝合金加热到固溶温度,使合金元素溶解在铝基体中,然后迅速冷却固溶体。
接着在一定温度下进行时效处理,使溶质元素析出,形成弥散的强化相,提高合金的强度。
2. 粒子强化:在挤压过程中向铝合金中加入纳米颗粒,通过颗粒与铝基体的相互作用,阻碍位错运动,提高材料的强度和硬度。
3. 晶粒细化:通过热挤压或等温挤压,使铝合金的晶粒变细,从而提高合金的强度和硬度。
4. 多道次挤压:将挤压操作分成多道次进行,每一次挤压都会使材料的晶粒细化、强化相均匀分布,从而进一步提高合金的强度和硬度。
5. 热处理:通过加热和冷却处理,使合金内部形成均匀的强化相,提高材料的强度和硬度。
6. 类似稀土元素的固溶体强化:向铝合金中加入类似稀土元素的合金元素,通过与铝基体形成固溶体相互作用,提高合金的强度和硬度。
这些方法可以单独或结合使用,根据不同的合金成分和要求进行选择。
铝合金强化挤压方法在航空航天、汽车、船舶等领域得到广泛应用。
铝合金固溶时效处理工艺
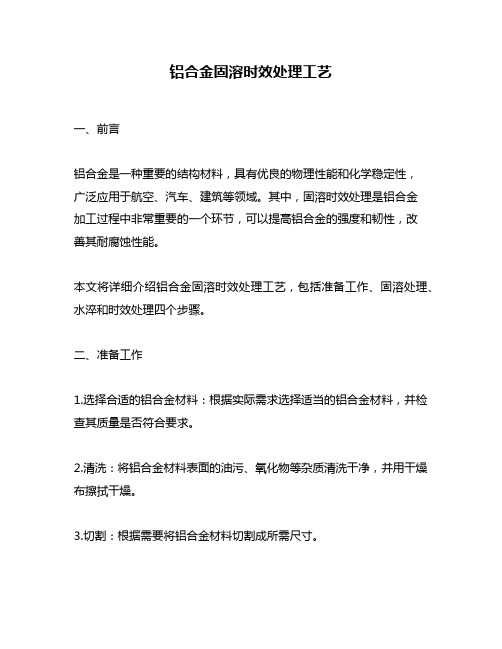
铝合金固溶时效处理工艺一、前言铝合金是一种重要的结构材料,具有优良的物理性能和化学稳定性,广泛应用于航空、汽车、建筑等领域。
其中,固溶时效处理是铝合金加工过程中非常重要的一个环节,可以提高铝合金的强度和韧性,改善其耐腐蚀性能。
本文将详细介绍铝合金固溶时效处理工艺,包括准备工作、固溶处理、水淬和时效处理四个步骤。
二、准备工作1.选择合适的铝合金材料:根据实际需求选择适当的铝合金材料,并检查其质量是否符合要求。
2.清洗:将铝合金材料表面的油污、氧化物等杂质清洗干净,并用干燥布擦拭干燥。
3.切割:根据需要将铝合金材料切割成所需尺寸。
4.标记:对切割好的铝合金材料进行标记,以便后续加工使用。
三、固溶处理1.装夹:将切割好并标记好的铝合金材料装夹在固溶炉内。
2.加热:将固溶炉加热至适当的温度,根据不同的铝合金材料选择不同的加热温度和时间。
一般来说,铝合金的固溶处理温度在500℃左右,时间为1-2小时。
3.保温:将铝合金材料保持在固溶处理温度下一定时间,使其达到均匀的固溶状态。
四、水淬1.取出:将经过固溶处理后的铝合金材料取出,并迅速放入水中进行淬火。
淬火时要注意水温不能太高,以免造成变形或开裂。
2.清洗:将淬火后的铝合金材料表面清洗干净,去除水中残留物。
五、时效处理1.装夹:将清洗干净的铝合金材料再次装夹在时效炉内。
2.加热:将时效炉加热至适当的温度,根据不同的铝合金材料选择不同的加热温度和时间。
一般来说,铝合金的时效处理温度在150-200℃左右,时间为4-6小时。
3.冷却:将经过时效处理的铝合金材料从炉内取出,并进行自然冷却。
4.清洗:将时效处理后的铝合金材料表面清洗干净,去除残留物。
六、总结铝合金固溶时效处理工艺是一项非常重要的加工工艺,可以使铝合金材料具有更好的强度和韧性。
在实际应用中,需要根据不同的铝合金材料选择适当的固溶处理和时效处理温度和时间,并严格按照操作规程进行操作,以保证加工质量。
铝合金的时效强化是如何进行和完成的

铝合金的时效强化是如何进行和完成的经淬火后的铝合金强度、硬度随时间延长而发生显著提高的现象称之为时效,也称铝合金的时效硬化。
这是铝合金强化的重要方法之一。
由定义可知,铝合金时效强化的前提,首先是进行淬火,获得饱和单相组织。
在快冷淬火获得的固溶体,不仅溶质原子是过饱和的,而且空位(晶体点缺陷)也是过饱和的,即处于双重过饱和状态。
以Al -4%Cu 合金为例,固溶处理后,过饱和α固溶体的化学成分就是合金的化学成分,即固溶体中钢含量为4%。
由Al-Cu 相图可知,在室温平衡态下,α固溶体的含铜量仅为0.5%,故3.5%Cu过饱和固溶于α相中。
当温度接近纯铝熔点时,空位浓度接近10-3数量级,而在常温下,空位浓度为10-11数量级,二者相差10-8级。
经研究可知;铝合金固溶处理温度越高,处理后过饱和程度也越大,经时效后产生的时效强化效果也越大。
因此固溶处理温度选择原则是:在保证合金不过烧的前提下,固溶处理温度尽可能提高。
固溶处理后的铝铜合金,在室温或某一温度下放置时,发生时效过程。
此过程实质上是第二相Al2Cu 从过饱和固溶体中沉淀的过程。
这种过程是通过成型和长大进行的,是一种扩散型的固态相变。
它依下列顺序进行:a过→G.P区→θ’’相→θ’相→θ相G.P区就是指富溶质原子区,对Al-Cu合金而言,就是富铜区。
铝钢合金的G.P区是铜原子在(100)晶面上偏聚或从聚而成的,呈圆片状。
它没有完整的晶体结构,与母相共格。
200℃不再生成G.P 区。
室温时效的G.P区很小,直径约50A,密度为1014-1015/mm3,G.P区之间的距离为20-40 ?。
130℃时效15h后,G.P 区直径长大到90 ?,厚为4-6 ?。
温度再高,G.P区数目开始减少。
它可以在晶面处引起弹性应变。
θ’’相是随时效温度升高或时效时间延长,G.P区直径急剧长大,且铜、铝原子逐渐形成规则排列,即正方有序结构。
在θ’’过渡相附近造成的弹性共格应力场或点阵畸变区都大于G.P区产生的应力场,所以θ’’相产生的时效强化效果大于G.P区的强化作用。
铝合金的时效强化是如何进行和完成的
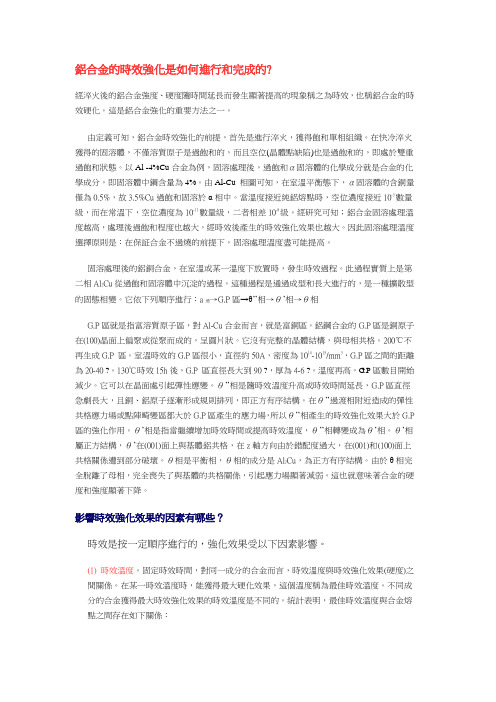
鋁合金的時效強化是如何進行和完成的?經淬火後的鋁合金強度、硬度隨時間延長而發生顯著提高的現象稱之為時效,也稱鋁合金的時效硬化。
這是鋁合金強化的重要方法之一。
由定義可知,鋁合金時效強化的前提,首先是進行淬火,獲得飽和單相組織。
在快冷淬火獲得的固溶體,不僅溶質原子是過飽和的,而且空位(晶體點缺陷)也是過飽和的,即處於雙重過飽和狀態。
以Al -4%Cu合金為例,固溶處理後,過飽和α固溶體的化學成分就是合金的化學成分,即固溶體中鋼含量為4%。
由Al-Cu 相圖可知,在室溫平衡態下,α固溶體的含銅量僅為0.5%,故3.5%Cu過飽和固溶於α相中。
當溫度接近純鋁熔點時,空位濃度接近10-3數量級,而在常溫下,空位濃度為10-11數量級,二者相差10-8級。
經研究可知;鋁合金固溶處理溫度越高,處理後過飽和程度也越大,經時效後產生的時效強化效果也越大。
因此固溶處理溫度選擇原則是:在保証合金不過燒的前提下,固溶處理溫度盡可能提高。
固溶處理後的鋁銅合金,在室溫或某一溫度下放置時,發生時效過程。
此過程實質上是第二相Al2Cu從過飽和固溶體中沉淀的過程。
這種過程是通過成型和長大進行的,是一種擴散型的固態相變。
它依下列順序進行:a過→G.P區→θ’’相→θ’相→θ相G.P區就是指富溶質原子區,對Al-Cu合金而言,就是富銅區。
鋁鋼合金的G.P區是銅原子在(100)晶面上偏聚或從聚而成的,呈圓片狀。
它沒有完整的晶體結構,與母相共格。
200℃不再生成G.P 區。
室溫時效的G.P區很小,直徑約50A,密度為1014-1015/mm3,G.P區之間的距離為20-40 ?。
130℃時效15h後,G.P 區直徑長大到90 ?,厚為4-6 ?。
溫度再高,G.P區數目開始減少。
它可以在晶面處引起彈性應變。
θ’’相是隨時效溫度升高或時效時間延長,G.P區直徑急劇長大,且銅、鋁原子逐漸形成規則排列,即正方有序結構。
在θ’’過渡相附近造成的彈性共格應力場或點陣畸變區都大於G.P區產生的應力場,所以θ’’相產生的時效強化效果大於G.P 區的強化作用。
- 1、下载文档前请自行甄别文档内容的完整性,平台不提供额外的编辑、内容补充、找答案等附加服务。
- 2、"仅部分预览"的文档,不可在线预览部分如存在完整性等问题,可反馈申请退款(可完整预览的文档不适用该条件!)。
- 3、如文档侵犯您的权益,请联系客服反馈,我们会尽快为您处理(人工客服工作时间:9:00-18:30)。
铝合金的时效强化是如何进行和完成的经淬火后的铝合金强度、硬度随时间延长而发生显著提高的现象称之为时效,也称铝合金的时效硬化。
这是铝合金强化的重要方法之一。
由定义可知,铝合金时效强化的前提,首先是进行淬火,获得饱和单相组织。
在快冷淬火获得的固溶体,不仅溶质原子是过饱和的,而且空位(晶体点缺陷)也是过饱和的,即处于双重过饱和状态。
以Al -4%Cu 合金为例,固溶处理后,过饱和α固溶体的化学成分就是合金的化学成分,即固溶体中钢含量为4%。
由Al-Cu 相图可知,在室温平衡态下,α固溶体的含铜量仅为0.5%,故3.5%Cu过饱和固溶于α相中。
当温度接近纯铝熔点时,空位浓度接近10-3数量级,而在常温下,空位浓度为10-11数量级,二者相差10-8级。
经研究可知;铝合金固溶处理温度越高,处理后过饱和程度也越大,经时效后产生的时效强化效果也越大。
因此固溶处理温度选择原则是:在保证合金不过烧的前提下,固溶处理温度尽可能提高。
固溶处理后的铝铜合金,在室温或某一温度下放置时,发生时效过程。
此过程实质上是第二相Al2Cu 从过饱和固溶体中沉淀的过程。
这种过程是通过成型和长大进行的,是一种扩散型的固态相变。
它依下列顺序进行:a过→G.P区→θ’’相→θ’相→θ相G.P区就是指富溶质原子区,对Al-Cu合金而言,就是富铜区。
铝钢合金的G.P区是铜原子在(100)晶面上偏聚或从聚而成的,呈圆片状。
它没有完整的晶体结构,与母相共格。
200℃不再生成G.P 区。
室温时效的G.P区很小,直径约50A,密度为1014-1015/mm3,G.P区之间的距离为20-40 ?。
130℃时效15h后,G.P 区直径长大到90 ?,厚为4-6 ?。
温度再高,G.P区数目开始减少。
它可以在晶面处引起弹性应变。
θ’’相是随时效温度升高或时效时间延长,G.P区直径急剧长大,且铜、铝原子逐渐形成规则排列,即正方有序结构。
在θ’’过渡相附近造成的弹性共格应力场或点阵畸变区都大于G.P区产生的应力场,所以θ’’相产生的时效强化效果大于G.P区的强化作用。
θ’相是指当继续增加时效时间或提高时效温度,θ’’相转变成为θ’相。
θ’相属正方结构,θ’在(001)面上与基体铝共格,在z轴方向由于错配度过大,在(001)和(100)面上共格关系遭到部分破坏。
θ相是平衡相,θ相的成分是Al2Cu,为正方有序结构。
由于θ相完全脱离了母相,完全丧失了与基体的共格关系,引起应力场显著减弱。
这也就意味着合金的硬度和强度显著下降。
影响时效强化效果的因素有哪些?时效是按一定顺序进行的,强化效果受以下因素影响:(1) 时效温度。
固定时效时间,对同一成分的合金而言,时效温度与时效强化效果(硬度)之间关系。
在某一时效温度时,能获得最大硬化效果,这个温度称为最佳时效温度。
不同成分的合金获得最大时效强化效果的时效温度是不同的。
统计表明,最佳时效温度与合金熔点之间存在如下关系:T0 = (0.5 – 0.6)T(2) 时效时间。
硬度与强度峰值出现在θ’’相的末期和θ’过渡相的初期,θ’后期已过时效,开始软化。
当大量出现θ相时,软化已非常严重。
故在一定的时效温度内,为获得最大时效强化效果,应有一最佳时效时间,即在θ’’产生并向θ’转变时所需的时间。
(3) 淬火温度、淬火冷却速度和淬火转移时间。
实践证明,淬火温度越高,淬火冷郄速度越快,淬火中间转移时间越短,所获得的固溶体过饱和程度越大,时效进行后强化效果越大。
(4) 时效工艺。
时效可选单级或分级时效。
单级时效指在室温或低于100℃温度下进行的时效过程。
它工艺简单,但组织均匀性差,抗拉强度、屈服强度、条件屈服强度、断裂性、应力腐蚀抗力性能很难得到良好的配合。
分级时效是在不同温度下进行两次时效或多次时效。
在较低温度进行预时效,目的在于在合金中获得高密度的G.P区,由于G.P区通常是均匀成核的,当其达到一定尺吋后,就可以成为随后沉淀相的核心,从而提高了组织的均匀性。
在稍高温度保持一定时间进行最终时效。
由于温度稍高,合金进入过时效区的可能性增大,故所获得合金的强度比单级时效略低,但是这样分级时效处理后的合金,其断裂性值高,并改善了合金的抗腐蚀性,提高了应力腐蚀抗力。
鋁合金的析出硬化處理陳克昌教授編撰一. 實驗目的1. 瞭解析出硬化的機制。
2. 學習鋁合金析出硬化處理之適當作業步驟。
3. 學習析出硬化效果之量測。
二. 實驗設備中溫加熱爐、低溫加熱爐、淬火槽、硬度試驗計及金相觀察設備。
三. 實驗原理1.析出硬化簡介【1~8】:二十世紀初德國人Alfred Wilm 把含有4%Cu及微量Mg和Mn之鋁合金,經高溫淬火後,室溫放置或於稍高溫下恆溫處理一段時間,發現此合金有時效硬化現象;即其硬度和強度會隨放置(或處理)時間之增長逐漸增加。
1930年代Guinier和Preston利用X-Ray繞射法量測出微細析出物的存在,1950年代TEM發明而可直接觀察析出粒子,使析出硬化之理論快速進展而逐漸建立。
目前已可使某些鋁、鈦、鎂和銅之合金、不銹鋼、超合金及麻時效鋼等結構材料,利用析出硬化處理大幅提高它們之強硬度。
析出硬化處理的最基本程序至少須包含三個步驟:溶體化處理(solution treatment)、快速淬火(quenching)及時效處理(aging treatment)。
溶體化處理是將材料加熱至固溶線以上之單相區,持溫一適當時間使合金元素全部溶入基地而形成單相固溶體。
快速淬火至低溫,則材料形成過飽和固溶體。
時效處理是要把過飽和固溶體放置於室溫或在稍高溫恆溫加熱,使超過溶解度的合金元素或金屬間化合物逐漸析出,來產生強硬化的效應。
因此,能析出硬化的材料必需具備兩項基本的特性:(1)主要合金元素的溶解度須隨溫度之升高而增加,亦即能在淬火後形成過飽和固溶體。
(2)能在室溫或稍高溫析出微細又密集的非平衡相析出物。
2.熱處理型鋁合金【3】鋁合金因所含的合金元素及產生的組成結構對熱處理的反應不同,一般可粗分成兩種類型,熱處理型與不能熱處理型鋁合金;前者是指鋁合金之強硬度主要可藉熱處理(析出硬化)來增大,後者之強硬度只有利用固溶硬化或加工硬化來增大。
屬於熱處理型之商用鋁合金有2000系之Al-Cu-(Mg),6000系之Al-Mg-Si及7000系之Al-Zn-Mg-(Cu);其他1000系之純鋁,3000系之Ai-Mn,4000系之Al-Si 及5000系之Al-Mg等合金雖亦具有析出硬化所需的第一項特性,但因析出物為粗大之平衡相,而不適合用為析出硬化型鋁合金。
3.鋁合金析出硬化的機制【3~6】茲以Al-Cu合金為例,圖1【3,6】顯示此合金平衡圖靠富鋁之部份。
在548℃以下Cu在Al內之溶解度由5.7%降至0.5%,因此,如把Al-5%Cu之鋁合金在545℃固溶體處理一星期後,合金元素Cu或金屬間化合物CuAl2粒子就完全溶入固溶體之內而成單相固溶體。
此時若緩慢冷卻,則降至525℃左右將開始析出AlCu2,隨溫度持續的緩慢下降至室溫,AlCu2會長成沒有析出硬化作用的粗大析出物,如圖2【6】所示。
如果固溶體處理後快速淬火至室溫水中,則高溫之析出被抑制而形成過飽和固溶體,如圖3【6】所示,大部份之溶質仍留在基地內。
把此過飽和固溶體放置在室溫下(自然時效)或在稍高溫度中(人工時效)保持一段適當時間,使合金中過量的合金原子或金屬間化合物粒子於低溫中析出,此種微細之析出物在溶體內會產生應力場,對差排之滑移產生阻力而達到使合金硬化的效果,材料最後的性質就依析出粒子的大小和粒子在晶粒內的分佈而定。
進行人工時效的溫度愈高,析出粒子的粒徑愈大、顆粒數愈少及分佈愈疏鬆,此種析出粒子對變形的阻力愈小,亦即對硬化之效益愈少;圖4【6】顯示出Al-4%Cu 鋁合金在不同時效溫度下的時效硬化曲線,可清楚的看出在每一特定的溫度時效,其硬度均隨時效時間之增加先逐漸上升至最大硬度再逐漸下降,而溫度在110℃~130℃之間可獲得最大之硬化效益,溫和度太高或太低,其最高硬度都較小。
鋁合金在固溶體處理及淬火後的質地為一相當軟、常溫時狀態不安定的過飽和固溶體。
欲安定,乃析出第二相,如G.P.一區和G.P.二區等中間相,這些相的晶粒和基地晶粒具有完全整合性(fully coherency),這種整合性使兩種晶粒間產生具有「鏈」與「鎖」的作用之應力場,在材料承受外力時阻止差排的滑移,如圖5【6】所示,亦即可阻止基材內部結構的滑動和變形,達到硬化鋁合金的目的。
由於析出需要時間,所以其硬度會隨時效時間的增加而增大。
在常溫下進行即可獲得所需硬度者稱為自然時效(natural aging),一般以T4表示其鍊度(temper)。
需要在稍高於室溫的條件下進行者稱為人工時效(artificial aging),一般以T6表示其鍊度。
人工時效主要是要使析出硬化作用能在合理的期間內完成,因為時效溫度愈高達到最大硬度的時間愈短,唯所穫得的硬度愈低,如圖4所示。
時效時間太長時,硬度會從最高點逐漸下降,即產生過時效(overaging)現象,這是因為析出粒子和基地間之整合性,將因析出粒子的成長而逐漸消失,先成為部份整合性(partially coherency),最後變成不整合性(noncoherency),亦即逐漸失去晶粒間的應力場,而失去硬化基地的功能,如圖6所示。
四. 實驗方法與步驟1. 材料及試片準備(1)材料:AA2024,AA6061或AA7075鋁合金之板材。
(2)試片尺寸:60㎜×30㎜×2㎜。
(3)試片之邊緣須去除毛邊並用砂紙研磨。
2. 析出硬化處理(1)把三組試片放入中溫爐內、加熱至固溶體化溫度;各種鋁合金的固溶溫度參考表一。
(2)在固溶溫度保持1小時後,急速從爐中取出試片淬火於室溫之水中;容許之淬火延遲時間參考表二。
(3a)第一組試片淬火後,放置於室溫自然時效;時效時間分別為0.5、1、2、5、10、20、50及100小時。
(3b)第二組試片淬火後,放入低溫爐內作人工時效;人工時效溫度參考表一,時效時間同第一組試片。
(3c)第三組試片淬火後,先室溫自然時效1天(24小時),再人工時效,時效溫度及時間同第二組試片。
(4)對不同的時效處理型式及時效時間的試片作硬度量測、拉伸試驗及衝擊試驗。
(5)觀察並攝取各試片的光學顯微鏡組織。
五. 實驗結果1. 分別繪製硬度、抗拉強度、伸長率和衝擊值與時效時間之變化曲線。
2.分析各試片金相組織的變化與時效溫度和時效時間的關係。
六. 問題與討論1. 如何計算淬火延遲時間?為什麼淬火時須注意淬火延遲?2. 為什麼2024鋁合金一般以自然時效進行硬化,而7075常以人工時效來進行硬化?3. 討論人工時效時、溫度與時間對顯微組織(析出物)及機械性質的影響。