有限元分析系统的发展现状与展望外文翻译演示教学
有限元分析系统的发展现状与展望外文翻译
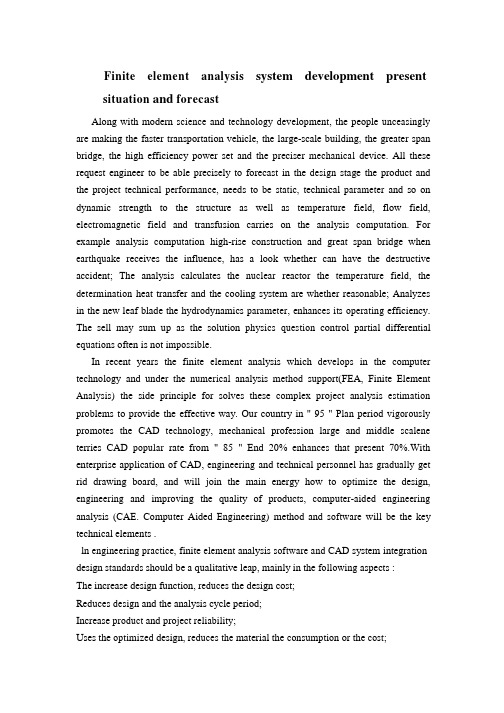
Finite element analysis system development present situation and forecastAlong with modern science and technology development, the people unceasingly are making the faster transportation vehicle, the large-scale building, the greater span bridge, the high efficiency power set and the preciser mechanical device. All these request engineer to be able precisely to forecast in the design stage the product and the project technical performance,needs to be static,technical parameter and so on dynamic strength to the structure as well as temperature field,flow field, electromagnetic field and transfusion carries on the analysis computation.For example analysis computation high-rise construction and great span bridge when earthquake receives the influence, has a look whether can have the destructive accident; The analysis calculates the nuclear reactor the temperature field,the determination heat transfer and the cooling system are whether reasonable; Analyzes in the new leaf blade the hydrodynamics parameter,enhances its operating efficiency. The sell may sum up as the solution physics question control partial differential equations often is not impossible.In recent years the finite element analysis which develops in the computer technology and under the numerical analysis method support(FEA, Finite Element Analysis)the side principle for solves these complex project analysis estimation problems to provide the effective way. Our country in " 95 " Plan period vigorously promotes the CAD technology,mechanical profession large and middle scalene terries CAD popular rate from " 85 " End 20% enhances that present 70%.With enterprise application of CAD, engineering and technical personnel has gradually get rid drawing board, and will join the main energy how to optimize the design, engineering and improving the quality of products, computer-aided engineering analysis (puter Aided Engineering)method and software will be the key technical elements.ln engineering practice, finite element analysis software and CAD system integration design standards should be a qualitative leap, mainly in the following aspects :The increase design function,reduces the design cost;Reduces design and the analysis cycle period;Increase product and project reliability;Uses the optimized design,reduces the material the consumption or the cost;Discovers the latent question in advance before the product facture or the project construction;Simulates each kind of experimental plan, reduces the experimental time and the funds;Carries on the machine accident to analyze, search accident cause factor.In vigorously promotes the CAD technology today, from the bicycle to the aerospace craft, all designs manufacture all will not be able to leave the finite element analysis computation,FEA obtains the more and more widespread value in the engineering design and the analysis. The next chart is the American San Francisco bay bridge earthquake responds the computation the finite element analysis model. The development direction and on significant progress international early20th century in the end of the 50's, at the beginning of the 60's has the formidable function on the investment massive manpower and the physical resource development the finite element analysis procedure.What is most famous was (NASA) entrusts US by American country Space Agency in 1965 to calculate the NASTRAN finite element analysis system which the scientific company and the Bell aerospace system company developed.This system development until now had several dozens editions, is in the present world the scale is biggest, the function strongest finite element analysis system. From at that time to the present, the world each place development facility and the university also developed one batch of scales smaller but to use nimble, the price is lower special-purpose or general finite element analysis software, mainly had German ASKA,England's PAFEC, France's company's the and so on SYSTUS, US'S ABQUS, ADINA, ANSYS, BERSAFE,BOSOR, COSMOS, ELAS, MARC and STARDYNE product. Now on the international FEA method and the software development presents below some tendency characteristics:1. develops from the pure structure mechanics computation to solves many physicalfields question finite element analysis method most early is comes from the structure matrix analysis development,gradually promotes to the board, the shell and the entity and so on the continual body solid mechanics analysis, the practice proved this is one extremely effective numerical analysis method. Moreover the or etically also already proved, so long as uses in to be separated solution object theunit enough to be small, the obtained solution may enough approach to the precise value.Therefore the recent years finite element method has developed question the and so on hydromechanics,temperature field,electricity conduction,magnetic field, transfusion and sound field solution computation,recently developed solves several inter disciplinary studies. the questions.For example when the air current flows a very high iron tower to have the distortion, but the tower distortion in turn affects to the air current flows. This needs to use the solid mechanics and the hydrodynamics finite element analysis finally overlapping iteration solves, namely so-called " Flows solid coupling " Question.2 Progresses from the solution linear project question to the analysis non-linear problem along with the science and technology development, the linear theory already by far could not satisfy the design there quest. For example in construction profession high-rise construction and great span hanging bridge appearance,request consideration geometry non-linear problem and so on structure big displacement and big strain; Astronautics and power engineering high temperature part existence thermal deformation and thermal load, also must consider the material the non-linear problem;Such as the plastic,the rubber and the compound material and so on each kind of new material appearance,only depends on the question which the linear computation theory is insufficient to solve meets, only has uses the non-linear finite element algorithm to be able to solve. It is well known, the non-linear value computation is very complex,it involves to the very many special mathematics question and the operation skill, thanks the general engineering technical personnel to grasp very much. Has spent massive specialty and so on manpower and investment development such as MARC, ABQUS and ADINA for this recent years overseas some companies to solution non-linear problem finite element analysis software, and widely applies to the project practice. These software common characteristics are have the highly effective non-linear solution as well as rich and the practical non-linear material.Definitely.3The enhancement visible pretag e modelling and the post positioned data processing function early time finite element analysis software research key lies in infers new high efficiency solution method and the high accuracy unit. Along with the numerical analysis method gradually consummation,the computer operating speed rapid development,the entire computing system uses in to solve the operation inparticular the time more and more few, but the data preparation and the operation result performance question day by day is actually prominent. On the present project workstation, solves to contain100,000 equations the finite lement models only to need to use several dozens minutes.But if establishes this model with the manual way, then the rehandling massive computed result must use several week-long time. May not exaggerate said, engineer calculates a project question when the analysis has 80% above the energy all to spend in the data preparation and the result analysis. Therefore the present nearly all shangye finite element software all has the function very strong pretage modeling and the post positioned data processing module.Is emphasizing" Visible " Today,very many procedures have all established to user extremely friendly GUI (Graphics User Interface), enables the user direct-viewing fast to carry on the grid automatic division by the visible graphic mode, the production finite element analysis needs the data, and the massive computed result will reorganize the distortion chart, the equivalentd is tribution cloud chart according to the request, will be advantageous for the extreme value search and needs the data to tabulate the output.4 With the CAD software seamless integration now the finite element analysis system another characteristic is and the general CAD software integrated use namely, after uses CAD software to complete the part and the components modeling design, automatically produces the finite element grid and carries on the computation,if analyzes the result does not conform to the design requirement then recarries on themodeling and the computation,until satisfaction, thus enormously raised the design level and the efficiency.The complex project analysis question today, which engineer may quickly solves in integrated CAD and in the FEA software environment in before is unable to deal with. Therefore now all shangye finite element system business all has developed and famous CAD software (for example Pro/ENGINEER,Unigraphics,SolidEdge, SolidWorks, IDEAS, Bentley and AutoCAD and so on) connection.5 Basically in Wintel platform development early time finite element analysis software all is in the large and middle scale computers(mainly is Mainframe) on the development and the movement,after wards also developed take the project workstation(EWS, Engineering WorkStation)as the platform, their common characteristic all uses the UNIX operating system.. The PC machine appearance caused the computer the application to have he fundamental change,engineer hadlonged for completed the complex project analysis on the desk the dream to become the reality. But early PC machine uses 16 CPU and the DOS operating system, in the memory public block data is restricted, at that time there fore calculated the model the scale not to be able to surpass 10,000 steps equations. Microsoft the Windows operating system and 32 Intel Pentium processor promoting for used in the finite element analysis PC machine to provide essential software and the hardware supports the platform. Therefore on the current international famous finite element procedure research and the development organization all in abundance move theirs software the value to the Wintel platform in. Next cava logged version environment and the SGI workstation simultaneously calculates the solution time with ADINA the V7.3 in PC machine Windows on the NT which 4 projects examples needed. May see the newest upscale PC machine solution ability already and center low-grade EWS is equally matched.In order to will develop on the large and middle scale computers and EWS the finite element procedure will move the value to PE machine on, frequently will need to use Hummingbird Corporation simulation software Exceed.Does this the result quite is troublesome,moreover cannot fully use the PC machine software and hardware resources. Therefore recently some companies,for example IDEAS, ADINA and R&D starts in the Windows platform to develop the finite element procedure,is called as " Native Windows" The edition, meanwhile has the finite element routine package which in on Linux operating system environment develops in PC machine.The domestic development situation and the prospect in 1979 US'S SAP5linear structure was static, the mechanical analysis procedure transplants successfully to the domestic introduction, raised the application general finite element procedure to analyze the computation project question the high tide. This high tide continuously continued to 1981 the ADINA non-linear structure analysis procedure introduction, many continuously was unable the project difficult problem which solved all to be easily solved for a while. Everybody also starts to realize indeed is engineer carries on then is computation to the finite element analysis procedure using the computer the important tool。
外文翻译--有限元分析软件的发展
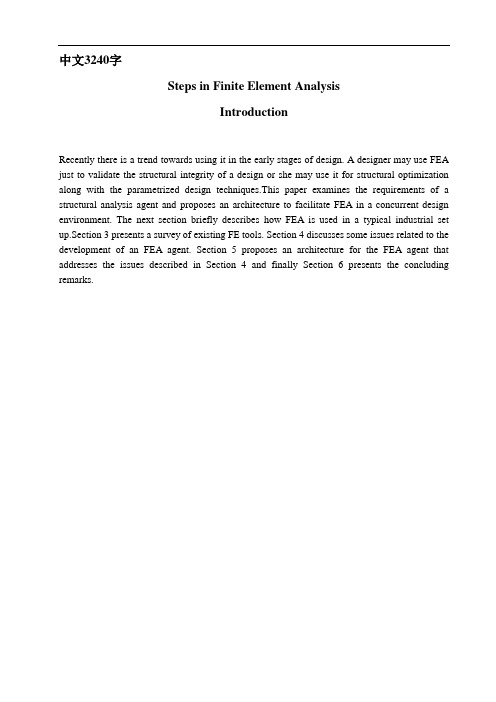
中文3240字Steps in Finite Element AnalysisIntroductionRecently there is a trend towards using it in the early stages of design. A designer may use FEA just to validate the structural integrity of a design or she may use it for structural optimization along with the parametrized design techniques.This paper examines the requirements of a structural analysis agent and proposes an architecture to facilitate FEA in a concurrent design environment. The next section briefly describes how FEA is used in a typical industrial set up.Section 3 presents a survey of existing FE tools. Section 4 discusses some issues related to the development of an FEA agent. Section 5 proposes an architecture for the FEA agent that addresses the issues described in Section 4 and finally Section 6 presents the concluding remarks.Steps in Finite Element AnalysisThe process of FEA starts with identification of the region of interest and the formulation of the physical problem。
有限元分析英文文献

The Basics of FEA Procedure有限元分析程序的基本知识2.1IntroductionThis chapter discusses the spring element,especially for the purpose of introducing various concepts involved in use of the FEA technique.本章讨论了弹簧元件,特别是用于引入使用的有限元分析技术的各种概念的目的A spring element is not very useful in the analysis of real engineering structures;however,it represents a structure in an ideal form for an FEA analysis.Spring element doesn’t require discretization(division into smaller elements)and follows the basic equation F=ku.在分析实际工程结构时弹簧元件不是很有用的;然而,它代表了一个有限元分析结构在一个理想的形式分析。
弹簧元件不需要离散化(分裂成更小的元素)只遵循的基本方程F=ku We will use it solely for the purpose of developing an understanding of FEA concepts and procedure.我们将使用它的目的仅仅是为了对开发有限元分析的概念和过程的理解。
2.2Overview概述Finite Element Analysis(FEA),also known as finite element method(FEM)is based on the concept that a structure can be simulated by the mechanical behavior of a spring in which the applied force is proportional to the displacement of the spring and the relationship F=ku is satisfied.有限元分析(FEA),也称为有限元法(FEM),是基于一个结构可以由一个弹簧的力学行为模拟的应用力弹簧的位移成正比,F=ku切合的关系。
有限元分析系统的发展现状与展望

有限元分析系统的发展现状与展望作者:谢小丽来源:《电脑知识与技术》2016年第18期摘要:随着我国科技的飞速发展,人们更是在不断的创建更快速,更简便,规模更大的建筑物以及更加精密的设备。
但创建这些东西的时候,都需要工程师在设计的时候要精确的预测出产品的技术性能,动力强度,流场,磁场等等的技术参数进行分析和计算。
随着以计算机技术为基础不断发展起来的有限元分析方法,不仅逐渐的解决了一些工程计算上的一些复杂的分析计算,而且相关的研究人员更是研究了许多新技术来不断的为我国做出了不可估量的贡献。
关键词:有限元分析;现状;发展局势中图分类号:TP311 文献标识码:A 文章编号:1009-3044(2016)18-0242-011 有限元分析系统的发展现状1)如今,在我们的生活中,从自行车到飞机,所有的设计都离不开有限元的系统分析计算。
随着科技的不断发展,以往的线性理论已经逐渐的不能满足现在的社会发展要求。
比如在建筑行业中,高层建筑的出现,工作人员就必须要考虑结构的大位移等等的几个非线性问题。
航天工程出现的高温部件存在的热应力问题,工作人员也必要考虑到材料的非线性问题。
所以现在我国的发展状况如果只是采用线性理论来解决问题,是远远不够的。
我们只能不断的发展更好的技术来解决现在的困境。
众所周知,非线性的计算的过程是非常复杂的,它一般会涉及许多复杂的数学问题以及一些运用技巧,相关的工作人员也很难在很短的时间掌握要点。
2)随着数值分析系统的不断改进和完善,尤其是计算机的运算速度上表现得尤其突出。
在现在的工程站上,想要求解一个包含10方程的模型时间只需要10分钟,而如果用手工的方式,则需要几周的时间才可以得出结果。
所以,我们在这方面做出的成绩还是比较优秀的。
3)现如今,CAD软件的无缝集成工艺已经成为我国有限元分析的另一个特点,也就是CAD软件的集成使用。
也就是说,在CAD软件造成零件的设计以后,再自动的生成有限元网络,然后进行分析计算。
ANSYS有限元分析外文文献翻译、中英文翻译

附录1:外文翻译CAE的技术种类有很多,其中包括有限元法,边界元法,有限差法等。
每一种方法各有其应用的领域,而其中有限元法应用的领域越来越广,现已应用于结构力学、结构动力学、热力学、流体力学、电路学、电磁学等。
ANSYS软件是融结构、流体、电场、磁场、声场分析于一体的大型通用有限元分析软件。
由世界上最大的有限元分析软件公司之一的美国ANSYS开发,它能与多数CAD软件接口,实现数据的共享和交换,如Pro/Engineer, NASTRAN, Alogor, I-DEAS, AutoCAD等,是现代产品设计中的高级CAE工具之一。
ANSYS有限元软件包是一个多用途的有限元法计算机设计程序,可以用来求解结构、流体、电力、电磁场及碰撞等问题。
因此它可应用于以下工业领域:航空航天、汽车工业、生物医学、桥梁、建筑、电子产品、重型机械、微机电系统、运动器械等。
有限元分析(FEA,Finite Element Analysis)的基本概念是用较简单的问题代替复杂问题后再求解。
它将求解域看成是由许多称为有限元的小的互连子域组成,对每一单元假定一个合适的(较简单的)近似解,然后推导求解这个域总的满足条件(如结构的平衡条件),从而得到问题的解。
这个解不是准确解,而是近似解,因为实际问题被较简单的问题所代替。
由于大多数实际问题难以得到准确解,而有限元不仅计算精度高,而且能适应各种复杂形状,因而成为行之有效的工程分析手段。
有限元是那些集合在一起能够表示实际连续域的离散单元。
有限元的概念早在几个世纪前就已产生并得到了应用,例如用多边形(有限个直线单元)逼近圆来求得圆的周长,但作为一种方法而被提出,则是最近的事。
有限元法最初被称为矩阵近似方法,应用于航空器的结构强度计算,并由于其方便性、实用性和有效性而引起从事力学研究的科学家的浓厚兴趣。
经过短短数十年的努力,随着计算机技术的快速发展和普及,有限元方法迅速从结构工程强度分析计算扩展到几乎所有的科学技术领域,成为一种丰富多彩、应用广泛并且实用高效的数值分析方法。
有限元分析 ppt课件
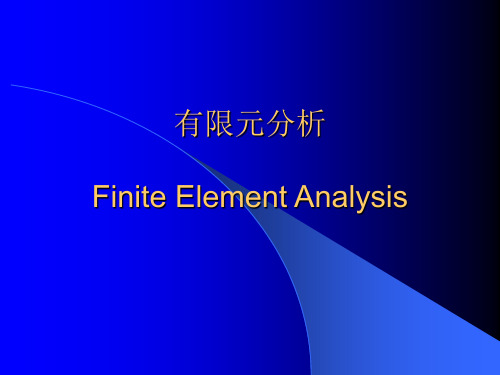
课程目标
1) 了解什么是有限单元法、有限单元法的基本 思想。
2) 学习有限单元法的原理,主要结合弹性力学 问题来介绍有限单元法的基本方法,包括单 元分析、整体分析、载荷与约束处理、等参 单元等概念。
3) 初步学会使用商用有限元软件分析简单工程 问题。
4. O.C. Zienkiewicz, R.L. Taylor. The finite element method( 5th ed). Oxford ; Boston : Butterworth-Heinemann, 2000
5. 郭和德编. 有限单元法概论,清华大学, 1998
1 有限单元法简介
自重作用下等截面直杆的材料力学解答
N(x)q(Lx)
d(L x)N(x)d xq(Lx)dx EA EA
u(x)xN(x)d xq(L xx2)
0 EA EA 2
x
du q (Lx) dx EA
x
Ex
q(Lx) A
自重作用下等截面直杆的有限单元法 解答
1)离散化 如图所示,将直杆划分 成n个有限段,有限段之 间通过一个铰接点连接。 称两段之间的连接点为 结点,称每个有限段为 单元。 第 i 个 单 元 的 长 度 为 Li , 包含第i,i+1个结点。
1.3.1网格划分
对弹性体进行必要的简化,再将弹性体 划分为有限个单元组成的离散体。 单元之间通过单元节点相连接。 由单元、结点、结点连线构成的集合称 为网格。
1.3.1网格划分
通常把三维实体划分成四面体(Tetrahedron) 或六面体(Hexahedron)单元的网格
四面体4结点单元
六面体8结点单元
外文翻译 对于有限元分析的介绍
本科生毕业设计 (论文)
外文翻译
原文标题INTRODUCTION TO THE FINITE ELEMENT
METHOD
译文标题对于有限元分析的介绍
作者所在系别机械工程系
作者所在专业机械设计制造及其自动化
作者所在班级
作者姓名
作者学号
指导教师姓名
指导教师职称
完成时间
注:1. 指导教师对译文进行评阅时应注意以下几个方面:①翻译的外文文献与毕业设计(论文)的主题是否高度相关,并作为外文参考文献列入毕业设计(论文)的参考文献;②翻译的外文文献字数是否达到规定数量(3 000字以上);③译文语言是否准确、通顺、具有参考价值。
2. 外文原文应以附件的方式置于译文之后。
共 5 页第11 页。
《有限元分析概述》课件
PART 05
有限元分析的未来发展与 挑战
新技术与新方法的探索
人工智能与机器学
习
利用人工智能和机器学习技术, 自动构建有限元模型、优化求解 过程和提高分值算法和 求解技术,提高有限元分析的稳 定性和精度。
多物理场耦合
探索多物理场耦合的有限元分析 方法,以解决复杂工程问题中的 多物理场耦合问题。
边界条件的处理
在有限元分析中,边界条件的处理是重要的环节。边界条件通常通过在边界节点上施加约束或加载来实现,以模拟实际系统 的边界条件。
边界条件的处理方式需要根据具体问题进行分析和设定,以确保求解结果的准确性和可靠性。
求解与后处理
求解是有限元分析的核心步骤,涉及到建立方程组、求解方程组并得到离散化模型的结果。常用的求 解方法包括直接法、迭代法和优化算法等。
优化设计
03
根据计算结果,对结构进行优化设计,提高其性能或降低成本
。
PART 04
有限元分析的优缺点
有限元分析的优缺点
• 有限元分析(FEA)是一种数值 分析方法,用于解决各种工程问 题,如结构分析、热传导、流体 动力学等。它通过将复杂的物理 系统离散化为有限数量的简单单 元(或称为“有限元”)来模拟 系统的行为。这些单元通过节点 相互连接,形成一个离散化的模 型,可以用来预测系统的性能和 行为。
2023-2026
ONE
KEEP VIEW
有限元分析概述
REPORTING
CATALOGUE
目 录
• 有限元分析简介 • 有限元分析的基本原理 • 有限元分析的实现过程 • 有限元分析的优缺点 • 有限元分析的未来发展与挑战
PART 01
有限元分析简介
定义与背景
有限元的发展历史现状及应用前景
有限元分析的发展趋势“有限元”这个名词第一次出现,到今天有限元在工程上得到广泛应用,经历了三十多年的发展历史,理论和算法都已经日趋完善。
有限元的核心思想是结构的离散化,就是将实际结构假想地离散为有限数目的规则单元组合体,实际结构的物理性能可以通过对离散体进行分析,得出满足工程精度的近似结果来替代对实际结构的分析,这样可以解决很多实际工程需要解决而理论分析又无法解决的复杂问题。
<br> 近年来随着计算机技术的普及和计算速度的不断提高,有限元分析在工程设计和分析中得到了越来越广泛的重视,已经成为解决复杂的工程分析计算问题的有效途径,现在从汽车到航天飞机几乎所有的设计制造都已离不开有限元分析计算,其在机械制造、材料加工、航空航天、汽车、土木建筑、电子电器,国防军工,船舶,铁道,石化,能源,科学研究等各个领域的广泛使用已使设计水平发生了质的飞跃,主要表现在以下几个方面:<br> 增加产品和工程的可靠性;<br> 在产品的设计阶段发现潜在的问题<br> 经过分析计算,采用优化设计方案,降低原材料成本<br> 缩短产品投向市场的时间<br> 模拟试验方案,减少试验次数,从而减少试验经费<br><br> 国际上早在60年代初就开始投入大量的人力和物力开发有限元分析程序,但真正的CAE软件是诞生于70年代初期,而近15年则是CAE软件商品化的发展阶段,CAE开发商为满足市场需求和适应计算机硬、软件技术的迅速发展,在大力推销其软件产品的同时,对软件的功能、性能,用户界面和前、后处理能力,都进行了大幅度的改进与扩充。
这就使得目前市场上知名的CAE软件,在功能、性能、易用性、可靠性以及对运行环境的适应性方面,基本上满足了用户的当前需求,从而帮助用户解决了成千上万个工程实际问题,同时也为科学技术的发展和工程应用做出了不可磨灭的贡献。
利用CiteSpace分析有限元技术在法医学中的应用现状
利用CiteSpace分析有限元技术在法医学中的应用现状王婷;孟运乐;魏智彬;肉孜·巴依斯;杨超朋【期刊名称】《刑事技术》【年(卷),期】2024(49)1【摘要】本文利用CiteSpace可视化软件对CNKI和ISI Web of Science数据库所收录的有限元技术在法医学中应用的研究文献进行统计和可视化对比分析,得出国内外法医领域有限元应用研究文献的关键词、机构合作、作者合作的可视化知识图谱。
在此基础上,作者对文献内容进行深入研究,发现有限元技术在法医学中的研究及应用主要集中在损伤机制分析方面,以车祸损伤、高坠损伤、钝器损伤、锐器损伤、枪弹损伤等为重点,研究方法主要是通过对人体、致伤物等建立高仿真模型,利用有限元技术,以数字化、可视化、可量化的方式研究各类损伤的生物力学机制。
目前,国内外法医学者主要借助Mimics等软件将人体影像数据转换为分割化的三维模型,依托较为成熟的THUMS、ANSYS等有限元系统构建多种损伤模型,有效揭示了各类损伤的发生机制,在一定程度上推动了法医病理损伤专业的发展,为法医学者开展相关研究提供了参考和借鉴。
同时,有限元技术在法医学中的应用属于学科交叉,但目前的研究人员多以法医为主,缺少相关学科专业技术人员的深度介入,在某种程度上限制了该技术在法医学中的应用发展,有必要加强与从事有限元等相关研究的专业技术人员之间的交流合作。
【总页数】7页(P57-63)【作者】王婷;孟运乐;魏智彬;肉孜·巴依斯;杨超朋【作者单位】首都医科大学;公安部鉴定中心;喀什市公安局【正文语种】中文【中图分类】DF795.1【相关文献】1.有限元方法在法医学颅脑损伤分析中的应用2.基于VOSviewer和CiteSpace分析功能性磁共振成像技术在针灸脑成像研究中的应用现状和趋势3.BIM技术在工程管理中的应用研究现状及热点——基于CiteSpace的知识图谱分析4.基于CiteSpace探讨有限元分析法在股骨中的应用研究5.基于CiteSpace技术的公路隧道领域智能技术应用现状及发展方向分析因版权原因,仅展示原文概要,查看原文内容请购买。
- 1、下载文档前请自行甄别文档内容的完整性,平台不提供额外的编辑、内容补充、找答案等附加服务。
- 2、"仅部分预览"的文档,不可在线预览部分如存在完整性等问题,可反馈申请退款(可完整预览的文档不适用该条件!)。
- 3、如文档侵犯您的权益,请联系客服反馈,我们会尽快为您处理(人工客服工作时间:9:00-18:30)。
Finite element analysis system development present situation and forecastAlong with modern science and technology development, the people unceasingly are making the faster transportation vehicle, the large-scale building, the greater span bridge, the high efficiency power set and the preciser mechanical device. All these request engineer to be able precisely to forecast in the design stage the product and the project technical performance, needs to be static, technical parameter and so on dynamic strength to the structure as well as temperature field, flow field, electromagnetic field and transfusion carries on the analysis computation. For example analysis computation high-rise construction and great span bridge when earthquake receives the influence, has a look whether can have the destructive accident; The analysis calculates the nuclear reactor the temperature field, the determination heat transfer and the cooling system are whether reasonable; Analyzes in the new leaf blade the hydrodynamics parameter, enhances its operating efficiency. The sell may sum up as the solution physics question control partial differential equations often is not impossible.In recent years the finite element analysis which develops in the computer technology and under the numerical analysis method support(FEA, Finite Element Analysis) the side principle for solves these complex project analysis estimation problems to provide the effective way. Our country in " 95 " Plan period vigorously promotes the CAD technology, mechanical profession large and middle scalene terries CAD popular rate from " 85 " End 20% enhances that present 70%.With enterprise application of CAD, engineering and technical personnel has gradually get rid drawing board, and will join the main energy how to optimize the design, engineering and improving the quality of products, computer-aided engineering analysis (CAE. Computer Aided Engineering) method and software will be the key technical elements .ln engineering practice, finite element analysis software and CAD system integration design standards should be a qualitative leap, mainly in the following aspects :The increase design function, reduces the design cost;Reduces design and the analysis cycle period;Increase product and project reliability;Uses the optimized design, reduces the material the consumption or the cost;Discovers the latent question in advance before the product facture or the project construction;Simulates each kind of experimental plan, reduces the experimental time and the funds;Carries on the machine accident to analyze, search accident cause factor.In vigorously promotes the CAD technology today, from the bicycle to the aerospace craft, all designs manufacture all will not be able to leave the finite element analysis computation, FEA obtains the more and more widespread value in the engineering design and the analysis. The next chart is the American San Francisco bay bridge earthquake responds the computation the finite element analysis model. The development direction and on significant progress international early20th century in the end of the 50's, at the beginning of the 60's has the formidable function on the investment massive manpower and the physical resource development the finite element analysis procedure. What is most famous was (NASA) entrusts US by American country Space Agency in 1965 to calculate the NASTRAN finite element analysis system which the scientific company and the Bell aerospace system company developed.This system development until now had several dozens editions, is in the present world the scale is biggest, the function strongest finite element analysis system. From at that time to the present, the world each place development facility and the university also developed one batch of scales smaller but to use nimble, the price is lower special-purpose or general finite element analysis software, mainly had German ASKA, England's PAFEC, France's company's the and so on SYSTUS, US'S ABQUS, ADINA, ANSYS, BERSAFE, BOSOR, COSMOS, ELAS, MARC and STARDYNE product. Now on the international FEA method and the software development presents below some tendency characteristics:1.develops from the pure structure mechanics computation to solves many physicalfields question finite element analysis method most early is comes from the structure matrix analysis development, gradually promotes to the board, the shell and the entity and so on the continual body solid mechanics analysis, the practice proved this is one extremely effective numerical analysis method. Moreover the or etically also already proved, so long as uses in to be separated solution object theunit enough to be small, the obtained solution may enough approach to the precise value.Therefore the recent years finite element method has developed question the and so on hydromechanics, temperature field, electricity conduction, magnetic field, transfusion and sound field solution computation, recently developed solves several inter disciplinary studies. the questions. For example when the air current flows a very high iron tower to have the distortion, but the tower distortion in turn affects to the air current flows. This needs to use the solid mechanics and the hydrodynamics finite element analysis finally overlapping iteration solves, namely so-called " Flows solid coupling " Question.2 Progresses from the solution linear project question to the analysis non-linear problem along with the science and technology development, the linear theory already by far could not satisfy the design there quest. For example in construction profession high-rise construction and great span hanging bridge appearance, request consideration geometry non-linear problem and so on structure big displacement and big strain; Astronautics and power engineering high temperature part existence thermal deformation and thermal load, also must consider the material the non-linear problem; Such as the plastic, the rubber and the compound material and so on each kind of new material appearance ,only depends on the question which the linear computation theory is insufficient to solve meets, only has uses the non-linear finite element algorithm to be able to solve. It is well known, the non-linear value computation is very complex, it involves to the very many special mathematics question and the operation skill, thanks the general engineering technical personnel to grasp very much. Has spent massive specialty and so on manpower and investment development such as MARC, ABQUS and ADINA for this recent years overseas some companies to solution non-linear problem finite element analysis software, and widely applies to the project practice. These software common characteristics are have the highly effective non-linear solution as well as rich and the practical non-linear material. Definitely.3 The enhancement visible pretag e modelling and the post positioned data processing function early time finite element analysis software research key lies in infers new high efficiency solution method and the high accuracy unit. Along with the numerical analysis method gradually consummation, the computer operating speed rapid development, the entire computing system uses in to solve the operation inparticular the time more and more few, but the data preparation and the operation result performance question day by day is actually prominent. On the present project workstation, solves to contain 100,000 equations the finite lement models only to need to use several dozens minutes. But if establishes this model with the manual way, then the rehandling massive computed result must use several week-long time. May not exaggerate said, engineer calculates a project question when the analysis has 80% above the energy all to spend in the data preparation and the result analysis. Therefore the present nearly all shangye finite element software all has the function very strong pretage modeling and the post positioned data processing module. Is emphasizing " Visible " Today ,very many procedures have all established to user extremely friendly GUI (Graphics User Interface), enables the user direct-viewing fast to carry on the grid automatic division by the visible graphic mode, the production finite element analysis needs the data, and the massive computed result will reorganize the distortion chart, the equivalentd is tribution cloud chart according to the request, will be advantageous for the extreme value search and needs the data to tabulate the output.4 With the CAD software seamless integration now the finite element analysis system another characteristic is and the general CAD software integrated use namely, after uses CAD software to complete the part and the components modeling design, automatically produces the finite element grid and carries on the computation, if analyzes the result does not conform to the design requirement then recarries on the modeling and the computation, until satisfaction, thus enormously raised the design level and the efficiency.The complex project analysis question today, which engineer may quickly solves in integrated CAD and in the FEA software environment in before is unable to deal with. Therefore now all shangye finite element system business all has developed and famous CAD software (for example Pro/ENGINEER, Unigraphics, SolidEdge, SolidWorks, IDEAS, Bentley and AutoCAD and so on) connection.5 Basically in Wintel platform development early time finite element analysis software all is in the large and middle scale computers(mainly is Mainframe) on the development and the movement, after wards also developed take the project workstation (EWS, Engineering WorkStation) as the platform, their common characteristic all uses the UNIX operating system.. The PC machine appearance caused the computer the application to have he fundamental change, engineer hadlonged for completed the complex project analysis on the desk the dream to become the reality. But early PC machine uses 16 CPU and the DOS operating system, in the memory public block data is restricted, at that time there fore calculated the model the scale not to be able to surpass 10,000 steps equations. Microsoft the Windows operating system and 32 Intel Pentium processor promoting for used in the finite element analysis PC machine to provide essential software and the hardware supports the platform. Therefore on the current international famous finite element procedure research and the development organization all in abundance move theirs software the value to the Wintel platform in. Next cava logged version environment and the SGI workstation simultaneously calculates the solution time with ADINA the V7.3 in PC machine Windows on the NT which 4 projects examples needed. May see the newest upscale PC machine solution ability already and center low-grade EWS is equally matched.In order to will develop on the large and middle scale computers and EWS the finite element procedure will move the value to PE machine on, frequently will need to use Hummingbird Corporation simulation software Exceed. Does this the result quite is troublesome, moreover cannot fully use the PC machine software and hardware resources. Therefore recently some companies, for example IDEAS, ADINA and R&D starts in the Windows platform to develop the finite element procedure, is called as " Native Windows" The edition, meanwhile has the finite element routine package which in on Linux operating system environment develops in PC machine.The domestic development situation and the prospect in 1979 US'S SAP5linear structure was static, the mechanical analysis procedure transplants successfully to the domestic introduction, raised the application general finite element procedure to analyze the computation project question the high tide. This high tide continuously continued to 1981 the ADINA non-linear structure analysis procedure introduction, many continuously was unable the project difficult problem which solved all to be easily solved for a while. Everybody also starts to realize indeed is engineer carries on then is computation to the finite element analysis procedure using the computer the important tool。