汽车用新型罩光涂料UV 和热双固化清漆
UV汽车涂料 树脂
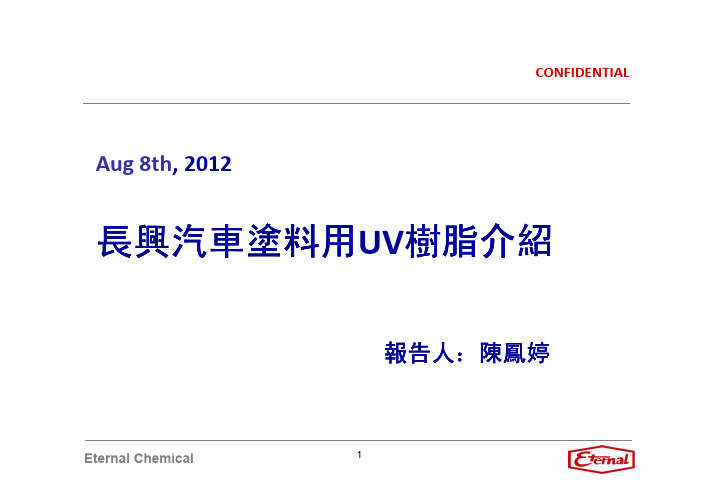
8/7/2012
25°C 10 22,00032,000cps
25°C 11,000-16,000cps
25°C 27,00030,000cps P.10
基本測試(高官系列)
CONFIDENTIAL
測試配方
Oligomer 60
EM223 (TMPTA)
35
PI 1173
5
TOTAL 100
固化能量 柔韌性 硬度 初始黃變及耐候性
佳 耐候性
DR-A845 6106
611B-85 6151
Eternal Chemical
8/7/2012
硬度
16
佳
P.16
樹脂選用
高耐候性PC車燈
CONFIDENTIAL
硬度&耐候性
DR-U076 6103 6145-100 DR-U025
柔韌性&耐候性
6151 611B-85 6106 DR-A845
耐候性佳 柔韌性佳 極佳的耐候性
P.9
物理性能
CONFIDENTIAL
DR-U076
6103
6145-100
DR-U025
外觀(25°C)
澄清&透明
澄清&透明
澄清&透明
澄清&透明
官能度 色數/Gardner
6 1max
6 1max
6 1max
4 1max
黏度
25°C 60,000-80,000cps
Tota8l/7/2012
20.0 20.0 20.0 201.2
耐熱(130℃,2h) QUV 1500h(△b)
18
通過 2.99(1級)
P.18
結論
CONFIDENTIAL
罩面清漆执行标准

罩面清漆执行标准
罩面清漆是一种高级涂料,在很多社会领域都有广泛应用,如汽车、机车、电子、家具等等。
罩面清漆不仅可以美化物品的表面,还
可以保护它们不受外界干扰,因此,其质量必须有严格的执行标准。
罩面清漆的执行标准通常由制造商、行业协会和相关政府机构制定。
在中国,国家质量监督检验检疫总局和中国标准化协会等主要制
定和负责罩面清漆的标准制定和执行工作。
罩面清漆的主要执行标准包括以下几个方面:
1.外观质量。
所有罩面清漆产品都应该具有良好的外观质量,包
括涂层均匀、光泽度高、颜色均匀等等。
2.涂层厚度。
涂层厚度直接关系到罩面清漆的保护性能和美观度,所以其厚度必须要达到标准要求,一般而言,其厚度应该在10~30微
米之间。
3.附着力。
涂层与基材间的附着力是罩面清漆的关键要素之一。
在标准测试中,一般常常使用横向剥离、交叉切割等方法来评测附着力,其评分应在标准范围内。
4.耐化学性。
罩面清漆在使用时会受到各种化学物质的侵袭,因
此其耐化学性能实际上也是关键的。
按照标准规定,其应对酸碱、水、油、溶剂等物质都有相应的抵御能力。
5.耐热性。
罩面清漆在使用过程中必须要具备一定的耐热性能,
在标准测试中,150℃烘烤24h后其外观和物理性质都应该保持稳定。
综上所述,罩面清漆的执行标准涉及到外观、涂层厚度、附着力、耐化学性和耐热性等多个方面。
因此,在选择和使用罩面清漆时,必
须要选择符合标准的产品,以确保物品的保护和美观度。
罩光漆标准

罩光漆标准
罩光漆标准是指对罩光漆的一系列要求和规范,以确保其质量和性能。
1.外观要求:罩光漆应具备良好的光亮度和光泽,并且要求均匀、平滑,无明显的划痕、气泡、污渍等缺陷。
2.色彩要求:罩光漆应按照客户要求的色彩进行配制,并且要求色彩均匀、饱满,无明显的色差。
3.干燥时间:罩光漆在涂覆后应具备合理的干燥时间,快速干燥可以提高生产效率,但同时要求干燥后不产生粘黏或易受损的薄膜。
4.耐磨性:罩光漆应具备较高的耐磨性,能够抵抗日常使用中的摩擦、刮擦等损伤,并保持较长时间的光泽。
5.环保要求:罩光漆应符合国家相关的环保标准,不包含有害物质,如重金属、挥发性有机物等,以确保对人体和环境的安全。
6.附着力:罩光漆应具备良好的附着力,能够牢固地粘附在基材上,不易剥落或脱落。
7.耐化学品性:罩光漆应具备较好的耐化学品性能,能够抵抗一些常见的化学物质、溶剂、酸碱等的腐蚀,以增强其使用寿命和稳定性。
以上是一些常见的罩光漆标准,具体标准和要求还需根据不同的应用领域和具体需求来制定。
uv光固化涂料安全技术说明书(3篇)
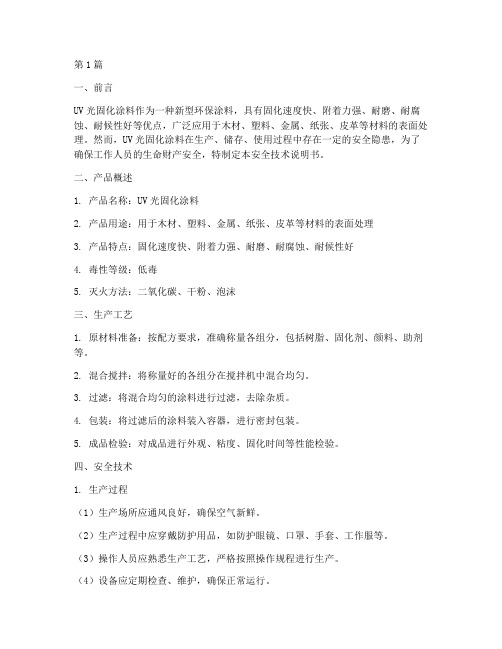
第1篇一、前言UV光固化涂料作为一种新型环保涂料,具有固化速度快、附着力强、耐磨、耐腐蚀、耐候性好等优点,广泛应用于木材、塑料、金属、纸张、皮革等材料的表面处理。
然而,UV光固化涂料在生产、储存、使用过程中存在一定的安全隐患,为了确保工作人员的生命财产安全,特制定本安全技术说明书。
二、产品概述1. 产品名称:UV光固化涂料2. 产品用途:用于木材、塑料、金属、纸张、皮革等材料的表面处理3. 产品特点:固化速度快、附着力强、耐磨、耐腐蚀、耐候性好4. 毒性等级:低毒5. 灭火方法:二氧化碳、干粉、泡沫三、生产工艺1. 原材料准备:按配方要求,准确称量各组分,包括树脂、固化剂、颜料、助剂等。
2. 混合搅拌:将称量好的各组分在搅拌机中混合均匀。
3. 过滤:将混合均匀的涂料进行过滤,去除杂质。
4. 包装:将过滤后的涂料装入容器,进行密封包装。
5. 成品检验:对成品进行外观、粘度、固化时间等性能检验。
四、安全技术1. 生产过程(1)生产场所应通风良好,确保空气新鲜。
(2)生产过程中应穿戴防护用品,如防护眼镜、口罩、手套、工作服等。
(3)操作人员应熟悉生产工艺,严格按照操作规程进行生产。
(4)设备应定期检查、维护,确保正常运行。
2. 储存过程(1)储存场所应通风干燥,避免阳光直射。
(2)储存容器应密封良好,防止涂料挥发、变质。
(3)储存环境温度宜控制在5-30℃之间,相对湿度控制在40%-80%之间。
(4)储存期间应定期检查,确保涂料质量。
3. 使用过程(1)施工场所应通风良好,确保空气新鲜。
(2)施工人员应穿戴防护用品,如防护眼镜、口罩、手套、工作服等。
(3)施工过程中应严格按照操作规程进行,避免涂料接触皮肤、眼睛等部位。
(4)施工完成后,应清洗施工工具,防止涂料残留。
4. 污染处理(1)施工过程中产生的废弃物应按照国家相关法规进行处理。
(2)若涂料不慎溅入眼睛,应立即用清水冲洗,并寻求医生帮助。
(3)若涂料不慎接触皮肤,应立即用大量清水冲洗,并寻求医生帮助。
QJD 1080—2004汽车涂装用罩光清漆

序
号
材料名称
牌号
标准编号
品种规格
有关规定
标记示例
5
汽车涂装用罩光清漆
Q/JD 1080—2004
原漆技术要求
ቤተ መጻሕፍቲ ባይዱ应用:
汽车涂装用罩光清漆主要用于汽车车身多层涂装中的表面涂层。
罩光清漆Q/JD 1080—2004
项目
质量指标
一般清漆
中高固体份清漆
不挥发物,%
≥50
≥56
金属闪光漆+罩光清漆:
试验时间1500h
中涂漆+金属闪光漆+罩光清漆:试验时间2000h
漆膜涂层老化单项等级评定:0~1级
中涂漆+本色面漆+罩光清漆:试验时间2000h
中涂漆+金属闪光漆+罩光清漆:试验时间2000h
漆膜涂层老化单项等级评定:0~1级
耐候性
在广州、海南岛地区暴晒两年或使用四年,涂层仍完好,即不起泡,不粉化、无锈点、不开裂。允许失光率不大于30%。
耐碱性[c(NaOH)=0.1mol/L,20℃,24h]
不起泡、允许轻微变化
续表
序
号
材料名称
牌号
标准编号
品种规格
有关规定
标记示例
漆膜技术要求(续)
项目
质量指标
微车
轿车
耐汽油性(93号汽油,24h)
不起泡、允许轻微变化
人工气候老化
本色面漆:试验时间1000h
中涂漆+本色面漆+罩光清漆:试验时间2000h
金属闪光漆+罩光清漆:
深色系≥75
浅色系≥70
中涂漆+本色面漆(金属闪光漆)+罩光清漆:
涂装工艺论文

汽车涂装工艺与环保背景随着汽车市场竞争的日趋激烈以及环保呼声的日渐增高,汽车涂装在保证高装饰性、高防腐蚀性能的同时,对于环境保护的效果、涂装材料和涂装生产成本以及设备投资也越来越为重视。
在涂装工艺体系中,电泳漆的主要作用是防腐蚀,色漆的主要作用是满足用户对不同颜色的需求,清漆的主要作用是耐候、耐紫外线以及提高光亮度,上述三个涂层均是必不可少的。
涂装工艺可分为:一、前表面处理的作用(1)提高涂层对材料表面的附着力,材料表面有油脂、污垢、锈蚀产物等时,直接涂漆会造成漆膜对基材的附着力很弱,漆膜易整片剥落或产生各种外观缺陷。
(2)提高涂层对金属基体的防护保护能力,钢铁生锈后会产生不稳定的铁酸,它在涂层下锈蚀扩张,很快就使涂层丧失了保护功能。
如果除去铁锈在涂漆,涂层的保护作用就大大提高了(见表)。
各除锈方法对涂层防护的影响作者:一汽车集团 王锡春进入21世纪以来,汽车用涂料和涂装领域的世界性的重要课题是适应时代要求:环境保护、节能省资源和在高质量的基础上降低涂装成本。
从防止大气污染观点,要求削减VOC(挥发性有机化合物)排出量;从防止地球温暖化观点,要求削减CO2排出量;从防止水污染和克服全球缺水状况观点,要求节省用水量,提高水的循环利用率,实现零排放;同时为持续发展,必须提高资源利用率;为了实现清洁生产和随着国内外汽车市场竞争越来越激烈,利润空间大幅度变小,必须在保证高质量的基础上优化工艺降低成本。
轿车车身的三涂层涂装体系(3C3B):漆前磷化处理→阴极电泳底漆→溶剂型中涂→溶剂型面漆(和后期的底色漆+罩光清漆的面漆涂装工艺变成4C3B涂装体系),已有30年的历史。
为实现上述环保、节能省资源、降成本的时代要求,汽车涂装又一次进入了更新换代,革命性地大变革时代;依靠技术进步,更新观念,对现4C3B工艺开始动“大手术”的创新局面已经到来。
国外的经验是汽车厂、涂装材料公司和涂装设备及涂装机具公司紧密协作,联合攻关,立题分工负责。
论文摘要1

双固化:硅氧烷型光-潮气双固化保形涂料的合成及光固化行为摘要:合成了一种以异氰酸酯为"桥"的硅氧烷-丙烯酸酯型光-潮气双固化保形涂料.探讨了引发剂、稀释剂等对其光固化行为的影响,结果表明,所合成的保形涂料存在较明显的氧阻聚现象,加入三丁胺可以抑制部分氧阻聚的影响.聚己内酯三元醇型双固化聚氨酯丙烯酸酯的合成及其固化膜性能研究摘要:以聚己内酯三元醇、异佛尔酮二异氰酸酯和羟基丙烯酸酯为原料,合成了一种新型聚氨酯丙烯酸酯.该树脂含有CC双键和未封闭的-NCO基团,可同时进行光固化和热固化反应.研究了不同双键含量对体系成膜性能的影响.结果表明,随着双键含量的上升,体系光固化后的摆杆硬度变大,耐溶剂性、玻璃化转变温度、铅笔硬度提高,但是柔韧性下降.同时发现,后期的热固化对体系的硬度和热性能有补强的作用,但是会在一定程度上导致涂膜的柔韧性下降.双固化聚氨酯丙烯酸酯的性能研究摘要:将三种双固化聚氨酯丙烯酸酯低聚物与环氧丙烯酸酯组成不同的双固化体系,利用实时红外(FT-IR)的方法研究了不同固化顺序(先光固化后热固化和先热固化后光固化)对体系中-NCO反应基团和C=C双键转化率的影响,结果显示先光固化后热固化的固化顺序更有利于体系达到高转化率.通过测试不同体系固化后的硬度和柔韧性,证明后期的热固化能大幅度提高涂膜的硬度.硅氧烷改性环氧丙烯酸酯及其紫外-湿气双固化涂层的性能摘要:以环氧树脂和丙烯酸合成环氧丙烯酸酯,再与正硅酸乙酯反应,合成硅氧烷改性的环氧丙烯酸酯.以FT- IR分析合成产物的结构和UV-湿气固化过程;研究UV-湿气双重固化硅氧烷改性环氧丙烯酸酯涂膜的性能.以正硅酸乙酯封闭环氧丙烯酸酯的羟基,使环氧丙烯酸酯的黏度降低82%;经紫外-湿气双重固化,改性环氧丙烯酸酯涂层的摆杆硬度、耐磨性、水接触角均比未改性样品大幅提升,起始热失质量温度比未改性环氧丙烯酸酯高约63℃.汽车用新型罩光涂料--UV和热双固化清漆摘要:轿车车身面漆涂装采用两涂层涂装工艺(即底色+罩光)已逐步成为面漆的典型涂装工艺,罩光涂料已成为关键的汽车涂料.介绍UV固化涂料的固化机理及其特征,新型双固化汽车用罩光涂料,双固化工艺及涂膜的优异性能以及新工艺的节能、环保效益及发展前景.有机硅改性聚氨酯丙烯酸酯光-潮气双固化体系摘要:由甲基丙烯酸羟乙酯、异佛尔酮二异氰酸酯和二-(γ-三乙氧基硅烷基丙基)胺为原料,合成了有机硅改性聚氨酯丙烯酸酯(Si-PUA)预聚物,预聚物属于宾汉流体. 用GPC凝胶渗透色谱方法测得预聚物的分子量分散度为1.12,用FTIR和光DSC示差扫描量热法(DPC)方法研究了预聚物的固化行为,光聚合反应的转化率为56.3%,用TG(热重分析)等方法研究了光、潮气固化膜的膜性能,发现光固化膜的电性能、热性能均好于潮气固化膜的膜性能.紫外光/湿气双固化聚哇氧烷树脂的制备及其固化机理的研究聚硅氧烷树脂可以通过硅羟基缩合及硅氢加成反应进行交联固化,同时固化产物具有优良的耐高低温性能和弹性的可调节性,在电子灌封以及建筑门窗密封等行业受到广泛应用,并且在诸多领域已经成为不可或缺的材料。
UV和EB固化技术在汽车制造领域的应用

•UV/EB固化技术特点与应用背景•UV/EB固化技术在汽车原厂制造中的应用•车灯制造应用•汽车轮毂应用•汽车转向架轴及其它机械部件UV涂装保护•汽车保险杠与车体部件制造•汽车仪表盘与中控面板制造•汽车轮胎加工应用•车窗贴膜•汽车紧固件应用•汽车内饰应用•汽车内部、外部塑料仿金属件•UV固化汽车修补漆UV/EB 固化技术特点适应性广E nabling5 E featurers辐射固化技术特征不含溶剂快速固化,快速加工经济E conomical高效性E fficient环境友好E nvironmental Friendly 节能E nergy Saving固化能耗不足溶剂型烤漆的10%不足水性烤漆3%与溶剂型涂料固含成本相当高附着、耐磨,软硬皆可几秒钟固化UV/EB 固化技术特点与应用背景UV/EB 固化技术可以做什么?辐射固化技术—并非无所不能,但却无所不在辐射固化胶粘剂辐射固化油墨包装印刷油墨功能性油墨辐射固化涂料装饰保护涂料功能性涂料辐射固化技术与材料辐射固化复合材料FRPUV/EB 固化技术应用产业领域竹木家具辐射固化涂料油墨胶粘剂FRP复合材料包装印刷电器/电子涂装管道安装与修复LCD平板显示器核心制造OLED制造广泛粘接加工印刷电子PCB 卫生健康产品制造医疗器械与医药农林保水汽车/舰船/飞机制造风电/光伏/光热产业高铁涂装室内防污涂装装修建材涂装光纤制造UV/EB固化技术在汽车原厂制造中的应用2001巴塞尔(第一辆UV赛车)UV/EB固化技术应用于汽车制造,很多公司一直在努力。
2002年,福特汽车公司的UV固化汽车零件制造技术获得RadTech Award.●汽车构造复杂,零件众多●小汽车发展趋势:轻量化、电动化●主要材料:钢铁、铝合金、聚烯烃塑料、FRP(BMC 、SMC 等)、合成革、橡胶、化纤织物、玻璃等。
●辅材:涂料、胶粘剂、贴膜、油墨等。
车灯制造应用UV保护面漆金属镀层UV底漆灯罩基体PVDVacuum Metallization Coating (VMC)BMC材质车灯杯金属化涂装-反光主流汽车反光灯杯金属化涂装几乎100%采用UV底涂+UV面涂,甚至三涂。
- 1、下载文档前请自行甄别文档内容的完整性,平台不提供额外的编辑、内容补充、找答案等附加服务。
- 2、"仅部分预览"的文档,不可在线预览部分如存在完整性等问题,可反馈申请退款(可完整预览的文档不适用该条件!)。
- 3、如文档侵犯您的权益,请联系客服反馈,我们会尽快为您处理(人工客服工作时间:9:00-18:30)。
汽车用新型罩光涂料UV和热双固化清漆王锡春 ( 中国第一汽车集团公司,长春 130011)摘要:轿车车身面漆涂装采用两涂层涂装工艺 ( 即底色 + 罩光 ) 已逐步成为面漆的典型涂装工艺,罩光涂料已成为关键的汽车涂料。
介绍 UV 固化涂料的固化机理及其特征,新型双固化汽车用罩光涂料,双固化工艺及涂膜的优异性能以及新工艺的节能、环保效益及发展前景。
关键词:罩光涂料;汽车涂料; UV 固化;热固化汽车用金属闪光色面漆涂装都采用两涂层面漆涂装工艺 ( 即底色 + 罩光工艺 ) ;为提高面漆涂膜的装饰性,本色面漆和水性面漆也采用两涂层面漆涂装工艺。
为适应环保法规的要求,环保型的汽车车身涂装工艺中采用水性底色漆已成为主流;而罩光涂料虽然有粉末罩光涂料 ( 含浆状粉末罩光涂料 ) ,而水性清漆、高固体分和超高固体分清漆已商品化,获得工业应用;但全世界的汽车制造厂还在进一步探索中,全世界的汽车涂料制造厂还在开发新的环保型罩光涂料。
如 BASF 公司在 2003 年南昌汽车涂装交流会上介绍的 TwinGloss 紫外线 (uv) 和热双固化清漆就是一例。
早在 1993 年,德国汽车界从环保和成本角度对选择什么样的罩光涂装体系,采用生命周期评估法LCA(Life Cycle Assessment) 对粉末罩光涂料 (PDCC 、 NV=97 % ) 、浆状粉末罩光涂料 (NV=38% ) 、溶剂型罩光涂料 (NV=48 % ) 、超高固体分罩光涂料 (SHSCC 、 NV=80 % ) 和水性罩光涂料(NV=43 % ) ,假设在日产 500 台轿车车身涂装线条件下的选用施工进行了剖析J 。
当时的评价意见是:在新建涂装线 ( 设备投资 ) 的前提下,溶剂型清漆和粉末清漆的成本指数相同。
在采用粉末清漆场合节省污水处理费用,降低了运营成本,但为保持涂膜外观,粉末清漆涂膜要厚 60 ~80 µ m ,其材料费用约为溶剂型清漆的 2 倍。
选用粉末清漆、浆状粉末清漆和水性清漆时,存在设备不能适用的难题,必须购置新设备。
相比之下,超高固体分清漆可使用原有设备进行涂装,这对降低面漆的总成本有利。
从环保 (VOC 排出污物 ) 、节能的角度,粉末罩光涂料最优。
烘干能量消耗,各种罩光涂料间差别不大。
另外可使用现有设备的超高固体分罩光涂料是今后不可忽视的环保型涂料之一。
近 l0 年来,世界环保法规不仅对挥发性有机化合物 (voc) 的排放量有限制,对 CO2 的排放量也要限制,对面漆涂膜的功能性 ( 耐酸雨,抗划伤性 ) 和外观装饰性提出了更高的要求。
近年开发的 UV 和热双固化罩光涂料,用于汽车外表面涂装在环保、节能、涂膜性能 ( 外观装饰性,耐酸雨和抗划伤性 ) 和涂装成本等方面都有较强的竞争力。
国内已有几条摩托车零部件生产线采用 UV 固化涂料。
本文对 UV 固化型涂料的特征及固化机理、优缺点、双固化法、应用实例等作一知识介绍。
1 Uv 固化型涂料的特征UV(Ultra Violet 紫外线 ) 是波长在可见光外的 200 ~ 400 nm 范围的短波长不可见光。
UV 固化型涂料是籍助照射 UV 光,引起交联反应,形成干涂膜的涂料。
UV 固化形式有基团聚合和阳离子聚合。
而阳离子聚合其优点不需使用光引发剂,但固化时制约条件太严。
实用化的 UV 固化型涂料仅是基团聚合,基团聚合固化形式如下式所示:I :光引发剂 (Photo Initiater) ;I *:已活性化的光引发剂I* +M → I+M *M :含有不饱和基团 ( 双键 ) 的成分;M* +M → MM *M* :已活性化的含有不饱和基团的成分光引发剂受 Uv 照射被活性化,发生基团。
这种基团使 Uv 固化成分 ( 含有不饱和基的单体,聚合物 ) 中的不饱和基活性化,引起聚合反应,进行交联。
Uv 照射时间以秒单位计,与原来的热固化型涂料的固化形式 ( 附加聚合,缩聚合 ) 相比较,可以大幅度地缩短固化时间。
UV 固化型涂料的长处和短处列于表 1 中。
表 1 uv 固化型涂料的长处和短处从表 1 中可知: Uv 固化型涂料的长处很明显,但其短处要用于汽车、摩托车的外表面涂装,会存在 3 个致命缺点。
一是形状复杂的被涂物会发生 Uv 照射不到的阴影部位,产生固化不足,凸出部位可能产生 Uv 照射能量过剩而发生变黄现象。
而要所有的部位照射同量的 Uv 光 ( 照射能量 ) 是不可能的。
二是 Uv 固化时的黄变性。
变黄是由光引发剂所引起,一般理论是光引发剂在 Uv 照射时产生的副产物为发色团。
浅色 ( 白珍珠色、金属感的银灰色 ) 的汽车涂膜无法采用有黄变性的光固化型涂料。
三是耐候性不足。
Uv 固化形式自身基团聚合,交联密度高,不易受光、热、水的影响产生老化、分解。
可是, Uv 照射时不能理想地消耗全部光引发剂, Uv 照射后,还有较多的光引发剂受自然界 Uv 光的激励,产生基团,它是涂膜变黄和劣化的原因。
涂膜开裂是由涂膜中的残留应力引起的。
Uv 固化速度快( 固化时间以秒计 ) ,可大幅度缩短固化时间,但其反面是固化时产生的涂膜的残留应力要比热固化型涂料大数十倍。
新开发的 Uv 和热双固化的罩光涂料已能克服上述 3 个致命的缺点。
2 Uv 和热双固化型涂料的基础技术以上介绍的是一般 Uv 固化型涂料和涂膜的特征。
双固化法(Twin Cure System) 系指 Uv 固化和热目化并用 ( 混合使用 ) 的涂膜固化方法。
Uv 固化成分是靠 Uv 照射形成的基团聚合的网状结构物。
在同一涂膜中的热固化成分是靠热能形成附加聚合 ( 聚氨酯结合 ) 的网状结构物,成为内渗透网状 (IPN — Inter Penetrating Network) 构造,固化机理见图 1 。
图 1 中所示的热固化法的代表例为丙烯酸聚氨酯固化体系,选用丙烯酸三聚氰胺固化体系和酸一环氧固化体系等也无任何问题。
图 1 固化机理双固化法使克服 Uv 固化型涂料及 Uv 固化法的阴影部涂膜固化不足、涂膜黄变性和耐候性不足等作为汽车外涂装的罩光涂料时的致命缺点成为可能。
首先,关于复杂形状被涂物的阴影部的 Uv 照射量( 能量 ) 不足,由热固化成分的交联来弥补 Uv 成分的固化不足,使涂膜性能达标。
关于 Uv 固化时变黄性、变黄量受 Uv 成分及所加光引发剂量的支配,籍助于 Uv 固化和热固化并用,来减少 Uv 成分量及所加光引发剂量,也就抑制了黄变性。
同样籍助减少光引发剂用量,来抑制 uv 照射后干涂膜中残留光引发剂的量解决了耐候性不足的问题。
还有产生开裂问题,靠 uV 固化与热固化并用的方法可使 Uv 固化时基团聚合产生的涂膜中的残留应力得到缓和。
双固化法的固化工艺如图 2 所示。
图 2 双固化法的固化工艺工序 1 ,蒸发涂膜中所含溶剂的预加热工序。
它在双固化法固化工艺中起着非常重要的作用。
因涂膜中残存溶剂在 uV 照射场合,仅涂膜表面层 uv 固化,内部未固化。
严重的场合,涂膜起皱,用手指抓压涂膜有凹陷、柔软的感觉,表明固化不足,而在轻微蒸发不足的场合,看不出表面上的涂膜缺陷。
但在长期的耐湿性、耐候性试验场合下,与溶剂完全挥发后 uV 照射的涂膜相比,有着显著的涂膜物性差异。
第一道工序必须要充分蒸发掉涂膜中所含有的溶剂。
工序 2 ,照射 UV 光使涂膜中 UV 固化成分形成基团聚合的网状结构。
不言而喻,是充分给予推算UV 固化所需的 UV 能量。
工序 3 ,使热固化成分靠热能形成附加聚合 ( 聚氨酯结合 ) 的网状结构的后加热工序。
如图 2 所示的那样,先使 uv 成分固化,再在 uv 固化的网状结构间使热固化成分附加聚合 ( 聚氨酯结合 ) ,形成 IPN 构造。
总之,工序不能倒置布置,在热固化— UV 固化场合,将产生以下两个问题:第一,是 UV 成分的固化受阻碍。
热固化成分的网状结构形成后,再 uV 照射,由于涂膜高分子比,迁移性下降,使 uV 成分达不到所规定的聚合率。
第二,外观装饰性差。
选用 UV 固化型罩光涂料原有的目的之一是改善外观,按图 2 的固化工艺执行, UV 照射后能形成镜面那样的平滑外观。
可是,热固化—UV 固化场合,受热固化成分对外观装饰性的支配,易生成桔皮。
3 应用实例 b 0( 摩托车汽油箱罩光涂装工艺设计 )图 3 所示的是 UV 罩光涂装生产线的布置设计。
其特征是被涂物 ( 摩托车汽油箱 ) 在涂装、固化过程中旋转。
“旋转”是使油箱各部位照射的 uv 光 ( 照射能量 ) 均一,无阴影部位。
涂装时也“旋转”是防止产生垂流,涂装不均,溜痕等涂装缺陷,另外可厚膜涂装,改善外观装饰性,不需熟练的喷漆工,采用机械手实现自动涂装。
在一条涂装线上可生产大小不同、形状复杂的摩托车汽油箱 50 种以上。
图 3 摩托车 UV 固化型罩光涂装线布置与热固化型罩光涂装线的比较列于表 2 中。
表 2 与热固化型罩光涂装线的比较UV 涂装线的全长、工程时间约为原有的热固化型涂装线的 1 / 3 ,非常紧凑。
测定涂膜的映像性,以 PGD 值评价涂膜的外观装饰性, uv 罩光涂膜外观呈镜面状态, PGD 值为 1 . 0 。
喷涂实现了无人涂装 ( 机械手自动喷涂 ) ,其他 3 项指数都以热固化型罩光为 100 计。
从表 2 的结果来看,单位被涂物 ( 油箱 ) 的加工成本 ( 含涂料成本 ) 可降低 50 %以上。
日本油脂· BASF 涂料公司的辐射罩光涂层在冲绳曝晒了 3 年的试验结果列于表 3 中。
表 3 辐射罩光涂层的耐候性试验结果由表 3 可见, 3 种底色漆的光泽保持率结果良好,都在 9O %以上。
uV 固化涂料的问题点是白色的变黄性,结果保色性良好,曝晒前后的色差仅为 AE=1 . 5 。
目测检查外观, 3 种底色漆未发生开裂缺陷。
这证明该罩光涂料的耐候性已具有适用于汽车、摩托车外涂装用途的高耐久的水平。
4 汽车用罩光涂料 ( 涂膜 ) 的技术要求轿车车身的涂层配套工艺一般为:漆前处理 ( 磷化处理 ) →阴极电泳底漆 (CED) →烘干→中涂→烘干→底色涂层 (Basecoat 简称 BC) →晾干 (Flash — off) →罩光涂层 (Clearcoat 简称 CC) →烘干。
底色罩光采用“湿碰湿” (Wet on Wet) 工艺。
罩光涂层的干膜厚度一般为 35 ~40 µ m ( 有个别厂家为提高外观装饰性控制到 50 µ m 左右 ) 。
罩光是轿车车身涂装的最后一道工序,它直接影响涂层的外观装饰性,耐久性 ( 耐候性,保光保色性,耐酸雨性等 ) ,抗划伤性,抗污耐油和耐化学药品性等,因此对罩光涂料及涂层的技术要求较高,通常的要求有以下几方面。