[复合材料模压工艺]复合材料模压成型工艺
复合材料模压成型的工艺特性和影响因素分析

复合材料模压成型的工艺特性和影响因素分析摘要:本文简述了聚合物基复合材料模压成型工艺特性,对模压成型的设备、预浸料、工装模具、工作环境条件等提出相应要求,着重对成型工艺过程中模压成型温度、压力、保温时间等工艺参数对复合材料制品性能影响做了分析,且简要介绍了复合材料模压制品可能出现的质量问题、产生原因、预防措施等内容。
关键词:复合材料;模压成型;工艺特性;影响因素现今社会复合材料越来越受到重视,并不断朝着更高比刚度、耐更苛刻工作环境等超高性能方向发展。
因此复合材料在材料科学中占据着重要地位,它的发展大大丰富了材料科学的内容。
复合材料成型工艺方法主要有手糊、注射、缠绕、真空导流、模压、热压罐、软模、树脂传递模塑等。
复合材料成型工艺是其重要环节,通常包括两个阶段,首先是使原材料在一定温度和压力下产生变形或流动,获取所需的形状,然后设法保持其形状。
本文着重对复合材料模压成型工艺特性、成型过程、影响制品质量因素及制品缺陷的产生原因及预防措施等内容作了简单叙述。
一、模压成型工艺特性模压成型工艺是将一定量预浸料放入到金属模具的对模腔中,利用带热源的压机产生一定的温度和压力,合模后在一定的温度和压力作用下使预浸料在模腔内受热软化、受压流动、充满流动、充满模腔成型和固化,从而获得复合材料制品的一种工艺方法。
模压成型工艺的特点是在成型过程中需要加热,加热的目的是使预浸料中树脂软化流动,充满模腔,并加速树脂基体材料的固化反应。
预浸料充满模腔过程中,不仅树脂基体流动,增强材料也随之流动,树脂基体和增强纤维同时填满模腔的各个部位。
只有树脂基体粘度很大、粘结力很强才能与增强纤维一起流动,因此模压工艺所需的成型压力较大,这就要求金属模具具有高强度、高精度和耐腐蚀,并要求用专用的热压机来控制固化成型的温度、压力、保温时间等工艺参数。
模压成型方法生产效率较高,制品尺寸准确,表面光洁,尤其对结构复杂的复合材料制品一般可一次成型,不会损坏复合材料制品性能。
复合材料模压成型工艺与应用技术

复合材料模压成型工艺与应用技术【摘要】随着复合材料生产水平和成型效率的提高,在各行各业已经取得了广泛的应用。
通过分析SMC、WCM、PCM三种模压成型工艺的工艺特点和关键技术,对三种高效率成型工艺的应用场景进行了对比。
总结而言,通过结构统型扩大单件产量需求,采用高效率模压成型工艺实现自动化生产,将进一步降低复合材料部件的制造成本。
【关键词】复合材料;高效率;低成本;模压成型1.引言以碳纤维、玻璃纤维、芳纶纤维等为代表的纤维增强复合材料,具备高比强度、高比模量、高耐候的优异特性,是目前最理想、应用最广泛的轻量化材料之一。
随着国内复合材料生产水平的提高以及成型效率的提升,复合材料越来越广泛地被各行各业接受。
在很多应用场景下,复合材料结构全生命周期的应用成本或低于金属结构。
面对汽车、风电、轨道交通等大批量应用场景,生产效率对成本的影响尤为关键。
复合材料的成型工艺为重要环节,高效低成本成型工艺的应用将直接降低部件的生产制造成本。
复合材料模压成型工艺是典型的高效成型工艺之一,具备以下优势:1.生产效率高,便于实现专业化和自动化生产;2.产品尺寸精度高,可重复性好;3.制品的内应力很低,且翘曲变形也很小,机械性能较稳定;4.表面光洁度高,无需二次加工;5.可在一给定的模板上放置模腔数量较多的模具,生产率高;6.原材料的损失小,不会造成过多的损失(通常为制品质量的2%-5%);7.能一次成型结构复杂的制品;8.模腔的磨损很小,模具的维护费用较低。
同时模压成型也存在一定的不足:1.不适用于存在凹陷、侧面倾斜等的复杂制品;2.在制作过程中,完全充模存在一定的难度;3.模具制造较为复杂,投资较大;4.产品尺寸受压机限制,一般只适合制造中小型复合材料制品。
复合材料模压成型工艺类型很多,本文主要对三种高效率复合材料模压成型工艺技术及其应用场景进行分析。
1.复合材料高效率模压成型工艺复合材料模压成型工艺在各种成型方法中占有十分重要的地位,其优势在于成型异形制品的高效率、高可重复性制造。
LFT-D复合材料模压成型工艺研究

—133—《装备维修技术》2021年第13期LFT-D 复合材料模压成型工艺研究梁绍吉(珠海格力电器股份有限公司,广东 珠海 519070)摘 要:针对LFT-D 复合材料模压成型,介绍生产线构成、生产工艺流程,结合超大型LFT-D 客车空调底盘的开发研究,分析相关因素的影响,验证确定工艺参数。
关键词:LFT -D 复合材料;模压成型;生产线设备;空调底盘引言玻璃纤维增强塑料俗称玻璃钢,它以价格低廉,固化后综合性能好,尤其在小批量生产中可降低成本和缩短生产周期,因此玻璃钢在客车行业应用广泛。
我司客车空调底盘用玻璃钢制作,随着产量增大,玻璃钢的缺点也日益呈现,如产品成型一致性差,漏水问题严重,绝缘性能差,生产不环保,材料不可回收利用,因此需要研究质量稳定、环保的产品制作工艺。
LFT-D 是以热塑性树脂为基体(PP 、PA 、PET 等),以长玻纤为增强材料的复合材料直接模压成型工艺。
目前在欧美、日本等发达国家,轻质、高强度,可回收的LFT -D 技术正广泛应用于汽车零部件生产,尤其是在机械强度要求较高的零部件如前端框架、吸能防撞保险杠、座椅骨架等。
本文主要讲述LFT-D 复合材料模压成型工艺及其应用于客车空调底盘的研究,用PP 和玻璃纤维作为主要材料来制作。
1 LFT -D 模压成型生产线构成LFT -D 模压成型生产线主要由三个部分构成,挤出、输送、成型。
挤出部分装置由真空上料机、连续称重计量混合装置、双螺杆挤出机构成,输送部分装置由玻纤切割计量装置、立式双刃双向加热切断机组、不锈钢保温输送机组构成,成型装置是液压压力机。
2 LFT -D 模压成型生产工艺流程模压成型主要工艺流程为在第一段螺杆中加入PP 并加热熔融,PP 和玻璃纤维加入到第二段螺杆中加热熔融并混合,再通过挤出机挤出,然后根据成型产品所需的质量定额将熔体切断,再将熔体保温输送到模具中进行模压成型,最后冷却定型和后处理。
3 产品分析根据空调系统和结构设计,底盘尺寸确定为3297mm*1803mm*238mm ,产品和模具是目前模压成型中最大的,没有现成的经验可以参考,如何制造出合格的产品,需要不断摸索和试验,并保证强度足够,能长期抵抗客车运行振动。
复合材料的预浸料模压成型工艺
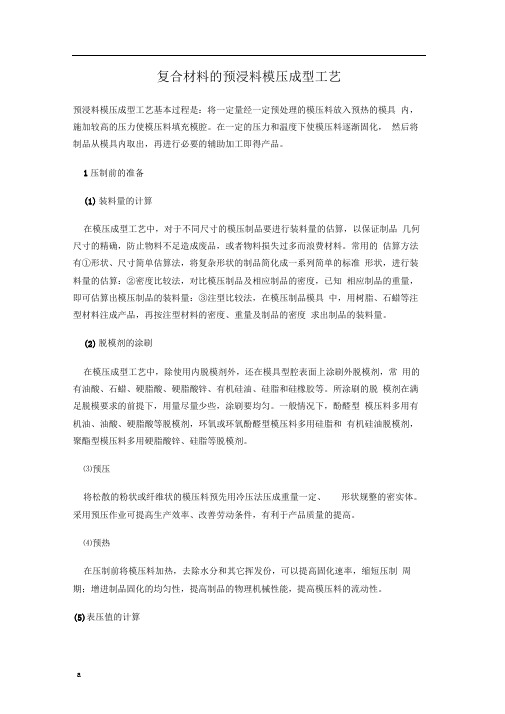
复合材料的预浸料模压成型工艺预浸料模压成型工艺基本过程是:将一定量经一定预处理的模压料放入预热的模具内,施加较高的压力使模压料填充模腔。
在一定的压力和温度下使模压料逐渐固化,然后将制品从模具内取出,再进行必要的辅助加工即得产品。
1压制前的准备(1)装料量的计算在模压成型工艺中,对于不同尺寸的模压制品要进行装料量的估算,以保证制品几何尺寸的精确,防止物料不足造成废品,或者物料损失过多而浪费材料。
常用的估算方法有①形状、尺寸简单估算法,将复杂形状的制品简化成一系列简单的标准形状,进行装料量的估算:②密度比较法,对比模压制品及相应制品的密度,已知相应制品的重量,即可估算出模压制品的装料量:③注型比较法,在模压制品模具中,用树脂、石蜡等注型材料注成产品,再按注型材料的密度、重量及制品的密度求出制品的装料量。
(2)脱模剂的涂刷在模压成型工艺中,除使用内脱模剂外,还在模具型腔表面上涂刷外脱模剂,常用的有油酸、石蜡、硬脂酸、硬脂酸锌、有机硅油、硅脂和硅橡胶等。
所涂刷的脱模剂在满足脱模要求的前提下,用量尽量少些,涂刷要均匀。
一般情况下,酚醛型模压料多用有机油、油酸、硬脂酸等脱模剂,环氧或环氧酚醛型模压料多用硅脂和有机硅油脱模剂,聚酯型模压料多用硬脂酸锌、硅脂等脱模剂。
⑶预压将松散的粉状或纤维状的模压料预先用冷压法压成重量一定、形状规整的密实体。
采用预压作业可提高生产效率、改善劳动条件,有利于产品质量的提高。
⑷预热在压制前将模压料加热,去除水分和其它挥发份,可以提高固化速率,缩短压制周期;增进制品固化的均匀性,提高制品的物理机械性能,提高模压料的流动性。
(5)表压值的计算在模压工艺中,首先要根据制品所要求的成型压力,计算出压机的表压值。
成型压力是指制品水平投影面上单位面积所承受的压力。
它和表压值之间存在的函数关系:j成型压力,即表压T MPa;仁——制品婴求的单位压力■念J\—压机额定表压,MPa:5 一制品水平投影面积T CT3;T——压机吨位,g复合材料的预浸料模压成型工艺在模压成型工艺中,成型压力的大小决定于模压料的品种和制品结构的复杂程度,成型压力是选择压机吨位的依据。
复合材料模压成型工艺的优缺点

复合材料模压成型工艺的优缺点在现代工业制造领域中,复合材料模压成型工艺是一种常用的生产技术,其在航空航天、汽车、船舶、建筑等领域具有广泛的应用。
本文将探讨复合材料模压成型工艺的优缺点,以帮助读者更好地理解这一制造工艺。
优点1. 良好的成型质量复合材料模压成型工艺可以实现高精度、高稳定性的产品成型,能够生产出表面平整、尺寸精准的制品,有利于保证产品的质量和性能稳定性。
2. 高效率生产相比手工复合工艺,模压成型工艺具有生产效率高、周期短的优势,能够满足大规模生产的需求,提高生产效率,降低生产成本。
3. 环保节能制造过程中,复合材料模压成型工艺可以有效减少废料产生,降低能源消耗,具有较好的环保节能效果,符合现代工业可持续发展的要求。
4. 设计灵活性通过合理设计模具,复合材料模压成型工艺可以生产各种复杂形状的产品,具有良好的设计灵活性和可塑性,能够满足不同客户的需求。
缺点1. 初期投资高复合材料模压成型工艺需要大量的设备投资和技术支持,特别是生产模具的制造成本较高,会增加企业的初期投资压力。
2. 模具制造周期长复合材料模压成型工艺中的模具制造周期相对较长,制造成本高,需要较长的制造周期,并且模具使用寿命有限,需要定期更换。
3. 需要专业技术人才复合材料模压成型工艺需要专业的操作技术和工艺经验支持,操作者需要接受相关的培训和指导,增加了生产管理的难度。
4. 模具设计复杂复合材料模压成型工艺的成功与否与模具设计密切相关,复杂的产品结构需要复杂的模具设计,增加了工艺的难度和成本。
综合来看,复合材料模压成型工艺具有诸多优点,如良好的成型质量、高效率生产、环保节能和设计灵活性,但也存在一些缺点,如初期投资高、模具制造周期长、需要专业技术人才和模具设计复杂。
在实际生产中,企业需要综合考虑这些因素,选择合适的生产工艺,以实现生产效率与产品质量的最佳平衡。
复合材料的成型工艺ppt课件
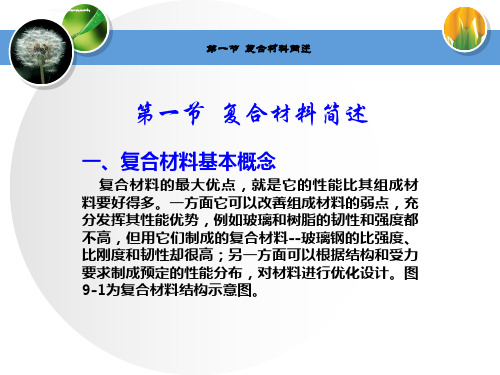
第二节 金属基复合材料(MMC)成形工艺
一、固态法
1.扩散黏结法(Diffusion Bonding) 如图9-2所示,扩散黏结是一种在较长时间、
较高温度和压力下,通过固态焊接工艺,使同类 或不同类金属在高温下互扩散而黏结在一起的工 艺方法。
2.形变法(Plastic Forming) 形变法就是利用金属具有塑性成型的工艺特点
2.复合材料的特点
(1)比强度和比刚度高 (2)抗疲劳性好 (3)高温性能好 (4)减振性能好 (5)断裂安全性高 (6)可设计性好
为 了 规 范 事 业单位 聘用关 系,建 立和完 善适应 社会主 义市场 经济体 制的事 业单位 工作人 员聘用 制度, 保障用 人单位 和职工 的合法 权益
第一节 复合材料简述
四 、 复 合 材 料 的 失 效 (Failure of Composite)
复合材料的失效一般是指其疲劳破坏过程。
1.制造加工损伤
此种损伤产生初始缺陷。,它包括:纤维铺设不 均,扭结、死扣等,树脂不均;纤维切断、错排; 固化不足;有孔隙、气泡;材质污染等。
2.使用引起的损伤
此种损伤导致缺陷发展。它包括:树脂裂纹或老 化;分层;纤维断裂;振动较大导致的纤维断裂; 温度变化较大;机加工产生内应力;碰撞等。
二、复合材料用原料
1.增强材料
(1)碳纤维(Carbon Fiber) (2)硼纤维(Boron Filament) (3)芳纶(Aramid Ring) (4)玻璃纤维(Glass Fiber) (5)碳化硅纤维(Silicon Carbide Fiber) (6)晶须(Whisker)
2.基体材料
3)基体能够很好地保护纤维表面,不产生表面 损伤、不产生裂纹。
复合材料的成型工艺
复合材料的成型工艺图1:热固性复合材料最基本的制备方法是手糊,通常包括将干层或半固化片层用手铺设到模具上,形成一个积层。
图中展示的是自由宇航公司的技术员(佛罗里达州墨尔本)正在通过手糊工艺加工一个碳/环氧预浸料,将用于制造通用航空飞机部件。
资料来源:自由宇航公司在复合材料的加工成型过程中会使用一系列模具,用来给未成形的树脂及其纤维增强材料提供一个成型的平台。
手糊(hand layup)成型是热固性复合材料最基本的制备方法,即通过人工将干层或半固化片层铺设到模具上,形成一个积层。
铺层方式分为两种:一种称为干法铺层,是先铺层后将树脂浸润(例如,通过树脂渗透方式)到干铺层上的方式,另一种方式是湿法铺层,即先浸润树脂后铺层的顺序。
现在普遍使用的固化方式可以分为以下几种:最基本的是室温固化。
不过,如果提高固化温度的话,固化进程也会相应加快。
比如通过烤箱固化,或使用真空袋(vacuum ba g)通过高压釜固化。
如果采用高压釜固化的话,真空袋内通常会包含透气膜,被放置在经手糊的半成型制品上,再连接到高压釜上,等最终固化完成后再将真空袋撤去。
在固化过程中,真空袋的作用是将产品密封在模具和真空袋之间,通过抽真空对产品均匀加压,将产品中汇总的气体排出,从而使产品更加密实、力学性能更好。
图2:热压釜独有的高温和高压条件使其成为完成热固性树脂零部件的固化的重要工具。
控制软件的改进则能够帮助经营者提高35-40%的生产量。
同时,一些新的树脂配方正在开发当中,将通过低压固化处理。
图中是Helicomb国际公司(俄克拉荷马州塔尔萨)的一名操作人员正在使用高压釜进行固化处理。
来源:Helicomb国际公司许多高性能热固性零件都需要在高热高压的条件下完成固化。
但是高压釜(Autocl aves)的设备成本和操作成本都较昂贵。
采购高压釜设备的制造商通常会一次性固化一定数量的部件。
对于高压釜的温度,压力,真空和惰性气体(inert atmosphere)等一系列参数,计算机系统能帮助实现远程甚至无人监控和检测,并最大限度地提高该技术的利用效率。
PP复合材料模压成型工艺及其性能研究的开题报告
木质纤维/PP复合材料模压成型工艺及其性能研究的开题报告一、题目木质纤维/PP复合材料模压成型工艺及其性能研究二、研究背景木质纤维/PP复合材料是一种具有优异性能的新型环保材料,具有优异力学性能、耐腐蚀性和可加工性能。
随着人们环保意识的增强和对新型材料越来越多的应用需求,该复合材料在汽车、建筑、轻工、船舶、家具等领域的使用越来越广泛。
本研究旨在探究木质纤维/PP复合材料的制备工艺及性能,为其应用提供技术支持。
三、研究内容1.制备木质纤维/PP复合材料:选取适当的木质纤维原料和PP树脂,在一定比例下进行混合,并加入适量的助剂,制成复合材料片。
2.优化模具设计:根据不同应用领域和产品要求设计不同的模具,优化产品的成型质量和尺寸精度。
3.模压成型工艺探究:研究模压成型工艺的参数,如温度、压力和时间等,探究其对复合材料成型的影响。
4.性能测试及分析:对模具成型的复合材料进行拉伸、弯曲、冲击等性能测试,分析其强度、硬度、韧性等性能指标。
同时,利用扫描电镜对材料的微观结构和界面结合情况进行观测。
四、研究意义1.探究木质纤维/PP复合材料的制备工艺及性能,为其更好地应用提供技术支持。
2.优化模具设计和模压成型工艺参数,提高产品的制备效率和质量。
3.为木质纤维/PP复合材料在汽车、建筑、轻工、船舶、家具等领域的应用提供技术支持和科学依据。
五、研究方法1.文献研究法:系统研究国内外相关文献,了解木质纤维/PP复合材料的制备工艺和性能测试方法,为研究提供理论支持。
2.实验研究法:制备木质纤维/PP复合材料,进行模具设计和模压成型工艺的实验研究。
对样品进行拉伸、弯曲、冲击等性能测试,并利用扫描电镜观察其微观结构和界面结合情况。
六、预期成果1.掌握木质纤维/PP复合材料的制备工艺和模具设计要点。
2.优化模压成型工艺的参数,提高产品制备质量。
3.分析木质纤维/PP复合材料的力学性能和微观结构,为其应用提供科学依据。
复合材料模压工艺-概述说明以及解释
复合材料模压工艺-概述说明以及解释1.引言1.1 概述概述:复合材料是一种由两种或两种以上的不同材料经过合理组合而成的新型材料,具有优异的性能和特点,如高强度、轻质、耐腐蚀等。
在各个行业中得到广泛应用,特别是在航空航天、汽车、建筑等领域。
模压工艺是一种常用的制造方法,通过将预先加工好的复合材料放入模具中,在高温高压下进行加工成型,从而得到符合要求的产品。
模压工艺具有成本低、生产效率高、产品质量稳定等优点,被广泛应用于复合材料制造中。
本文将着重介绍复合材料模压工艺的基本原理、应用领域等方面,以帮助读者深入了解这一重要的制造工艺,并展望未来的发展趋势。
1.2文章结构文章结构部分的内容如下:文章结构部分将会介绍本文的总体结构安排,包括引言、正文和结论三个主要部分。
在引言部分,我们会概述复合材料模压工艺的重要性和应用领域,以及本文的主要目的和结构安排。
在正文部分,将详细介绍复合材料的定义和特点、模压工艺的基本原理,以及模压工艺在复合材料制造中的实际应用情况。
最后,在结论部分,我们将总结复合材料模压工艺的优势,展望未来该工艺的发展方向,并得出本文的最终结论。
通过这样的结构安排,读者可以清晰地了解本文的主要内容和逻辑发展。
1.3 目的本文旨在探讨复合材料模压工艺在制造业中的重要性和应用。
通过对复合材料的定义和特点以及模压工艺的基本原理进行深入分析,以展现该工艺在提高复合材料制造效率、降低成本、增强材料性能等方面的优势。
同时,本文还将总结当前复合材料模压工艺的发展现状,展望未来的发展趋势,为相关领域的研究和生产提供参考和借鉴。
通过本文的研究和讨论,旨在促进复合材料模压工艺在工业应用中的进一步推广和应用,为制造业的发展做出贡献。
2.正文2.1 复合材料的定义和特点复合材料是由两种或两种以上不同的材料经过一定的工艺方法组合而成的一种新型材料,具有独特的性能和特点。
其主要特点包括以下几个方面:1. 高强度:由于复合材料是由不同材料组合而成的,在强度方面往往具有比单一材料更高的强度,可以满足各种工程结构对强度的要求。
复合材料的模压成型技术
复合材料的模压成型技术复合材料是由两种或两种以上的不同材料组成的材料,具有比单一材料更优越的性能。
模压成型是一种常用的复合材料制备技术,通过在模具中对复合材料进行加热和压力处理,使其固化成特定形状的产品。
下面将详细介绍复合材料的模压成型技术。
模压成型技术是一种传统且成熟的复合材料制备方法,适用于各种复材的生产。
其基本工艺包括:制备模具、预热模具、预切制复材、层堆压、模热固化、冷却脱模、再加工等步骤。
下面将分别介绍每个步骤的具体操作方法。
首先是制备模具。
模具是模压成型技术中非常重要的一部分,其质量和精度会直接影响最终产品的质量。
制备模具时,需要根据产品的要求设计和制造成型模具,通常采用金属材料制作,如铝合金、钢材等。
接下来是预热模具。
模具在使用前需要对其进行预热处理,以提高产品成型效果和减少模具损耗。
预热温度一般根据复合材料的热固化温度来确定,通常在50-100摄氏度之间。
然后是预切制复材。
复合材料通常是由纤维增强材料和树脂基体组成的,为了方便模压成型,需要将复材事先切成与产品形状相近的形状。
预切制复材时要注意保持纤维的方向和层间粘接质量,以确保最终产品的强度和性能。
层堆压是模压成型的核心步骤,也是影响成型质量的关键环节。
层堆压时,将预切制好的复材层叠放在模具中,注意纤维方向和树脂基体的均匀分布。
并在每一层复材之间涂上树脂胶水,以增强层间粘接力。
接着是模热固化。
层堆压好的复材在模具中进行加热和压力处理,以使树脂基体固化成型。
模具的温度和压力要根据树脂基体的热固化曲线和产品要求来确定。
一般情况下,模具温度在120-180摄氏度之间,压力在0.5-2.0MPa之间。
冷却脱模是使产品从模具中取出的最后一个步骤。
脱模时要注意避免产品变形和破损,可以采用自然冷却或水冷却的方法。
同时,也可以根据产品的要求进行一些后续处理,如修磨、修边、打孔等工艺。
最后是再加工。
模压成型的产品可能会因为形状和尺寸的要求不完全符合而需要进行一些再加工。
- 1、下载文档前请自行甄别文档内容的完整性,平台不提供额外的编辑、内容补充、找答案等附加服务。
- 2、"仅部分预览"的文档,不可在线预览部分如存在完整性等问题,可反馈申请退款(可完整预览的文档不适用该条件!)。
- 3、如文档侵犯您的权益,请联系客服反馈,我们会尽快为您处理(人工客服工作时间:9:00-18:30)。
[复合材料模压工艺]复合材料模压成型工艺
复合材料模压工艺
复合材料由于其众所周知的优异性能及各种工艺的日益成熟、原材料来源丰富、成本下降、可靠性提高,使其受到用户与生产者双方的青睐,越来越多地取代传统金属材料,我们的时代已进入了复合材
料时代。
据美国塑料工业协会复合材料所(SocietyofthePlasticsIndustry"sInstitute)1997年元月27日发表的年度统计报告表明:1996年美国复合材料的销售量为161万吨,比1995年的158.5万吨增长约1.6%,是复合材料的销售量连续第五年增长。
据预测,1997年以及以后五年内复合材料销售量仍会连续
增长。
聚合物基复合材料模压成形工艺在各种成形工艺方法中占有重要地位,主要用于异型制品的成形,因而所用的成形压力高于其它工艺
方法。
由于模压成形工艺所需设备简单,又能对纤维料、碎布、毡料、层压制品、缠绕制品、编织物进行模压成形,因而被各种规模的复合材料生产企业所普遍采用,复合材料模压工艺也几乎为各生产单位家喻户晓。
因此,本文并不打算对模压复合材料制品工艺进行系统介绍,仅就影响复合材料制品质量的一些重要环节谈谈体会,因为就复合材料复杂结构异型件而言,保证质量、提高合格率比一般制件更为重要,难度也更大。
一、对复合材料模压制品质量产生影响的因素
模压成形工艺的基本过程是将一定量的经过一定预处理的模压料放入预热的压模内,施加较高的压力使模压料充满模腔。
在预定的温度条件下,模压料在模腔内逐渐固化,然后将制品从压模内取出,再进行必要的辅助加工即得到最终制品。
从上述过程看,完成最终制品涉及的因素有模压料本身、压模模具、加压加温的热压机等;最重要的当是压制工艺,本文将单列一节
予以重点讲述;还有工作环境和辅助加工等。
1.模压料
任何形式的模压料(碎布料、毡料、长、短纤维),在装模前均应
使其按预定比例与树脂均匀浸渍。
对经溶剂稀释的树脂溶液,在浸渍纤维后应充分晾置使溶剂挥发。
晾置时间与环境温度湿度有关。
2.压制模具
制品用的模具除应保证在工作压力下的强度、刚度条件以外,主
要应考虑能给制品的各部位、各方向较均匀地加上压力。
一定的拔
模斜度既能保证制品顺利出模,又能起到侧向加压的作用。
模具设计
尽量使制品整体成形,既可保证制品的强度、刚度,又可减少辅助加
工工序和工装模具数量。
在模具上应开有流胶槽使多余的胶料顺利
排出。
压模的成型表面应至少进行抛光或镀铬,使光洁度在Δ9以上,以保证顺利脱模。
应在模具靠近型腔部位开设测温孔。
模具本身,必要时考虑设计一定的附件以保证较方便地实现脱模。
3.压机
压机的尺寸和吨位应能满足制品及所选材料、模具结构的要求。
压机的温度、压力最好能有手控和自动控制两种模式。
压机的工作台或上下加热板应尽量使工件保持水平以避免树脂向一侧流聚。
加热板在有效工作范围内温度差控制在±5℃左右。
4.工作场地
工作场地应光线充足、通风良好,温度、湿度满足要求,吊升降叉车、真空泵、压缩机、工作台等配套设备齐全、工作安全可靠。
环
境清洁、整齐。
二、复合材料模压制品的压制工艺
复合材料模压制品的压制工艺(以环氧树脂基体复合材料为例)是指模压料装模后在固化剂存在或加热的条件下在模腔内固化成制品的过程。
它是温度、压力、时间综合作用的结果,压制工艺条件的选择及可靠控制是决定制品质量的关键。
虽然原则上讲某一种牌号的树脂有一定的固化特性,但由于同牌号树脂的分子量、软化点,环氧值等都有一定的变化范围,因而固化特性也会有所差异。
为保证复合材料制品的质量,最好对每一批次树脂的固化特性进行测定,以确定最佳的压制工艺。
这一工作我们是通过DDA(动态介电分析)和DMA(动态力学性能分析)来完成的。
环氧树脂的固化过程从DDA曲线来看可分为软化流动、凝胶、固化、熟化(后固化)四个阶段。
如将后两个阶段合并为固化阶段也可视为三个阶段。
根据制品材料制作的试片所测的DDA曲线,再根据制件的厚度和模具结构情况,确定在一定的加热速度下每个阶段所需保温时间和加压时机。
在对不同加热速率、不同保温时间和加压时机的试片进行DMA测试后,选择动态力学性能最好的试片的温度、压力与时间关系的固化特性确定压制工艺。
图1、2、3分别为
F46+BF3·MEA树脂体系试片的DDA、DMA测试曲线及该体系为基体的结构制品的固化曲线。
由于该复合材料制品尺寸大、厚度厚、结构复杂,为保证接头部位的强度和刚度又采用了难度很大的整体成形工艺,因而固化压制工序成了特别关键的工序。
考虑产品大而厚的因素及压机中心位置与边缘温度的差异,为保证整个产品均匀固化,我们在80℃的软化流动峰前增加了在(45±5)℃时0.5小时的低温保温过程。
另外,在固化后的自然降温阶段,考虑到钢模与碳复合材料热物理性能的差异,为避免钢模收缩造成复合材料制品的翘曲变形,在工艺文件中规定在产品温度降至70℃左右时松开模具四周的顶模螺钉,使产品自由降至室温再卸模。
在上述压制工艺条件下压制的制品合格率达到90%以上。
三、聚合物基复合材料模压制品的缺陷、产生的原因及预防措施
四、复合材料模压制品工艺新进展
据1997年4月23日至25日在法国巴黎召开的第32届“欧洲复合材料”和“先进材料与加工工程科学”大会报导,德国凯瑟斯劳腾的复合材料研究所
(InstitutfurVerbundwerkstoffe,Kaiserslautern,简称IVW)从1993年起研制了一种双面传送压机,可以压制聚合物基复合材料连续薄板。
该研究所用纤维布和热塑性树脂膜作原料,采用连续等压工艺制出浸渍质量良好的宽度达600mm的预制板(带)。
压机的主要工作参数为:温度高达410℃,压力可达到5.5MPa。
预制板在加热条件下可在不到一分钟的时间内模压或冲压成最终制品,形成了预处理、塑化、模压和后加工一条龙生产线。
双面传送压机可用各种纤维增强各种树脂制成预制板,再压制成各种形状复杂的结构件,比RTM法、热压罐成形法等生产操作简单,生产周期短,是一种很有前途的工业复合材料制品模压工艺。