印制电路板化学沉铜详解3
化学沉铜介绍(章节优讲)

• 目的:将残留于孔壁的MnO4-、MnO42-、
•
MnO2还原
• 工艺控制:温度40-50°C
•
时间4-8 min
优质教学
7
化学沉铜
• 工艺流程: • 调整 微蚀 预浸 催化 加速
沉铜
优质教学
8
调整(Conditioner)
• 目的:调整孔壁电性,利于对胶体钯的
•
吸附
• 工艺控制:温度45-55°C
优质教学
17
化学沉铜工艺分类
• 催化剂分类:1.胶体钯Pd(SnCL3)-
•
2.离子钯Pd2+
• 沉铜厚度分类:1.沉薄铜(0.3-0.5um)
•
2.沉厚铜(1.2-2.5um)
优质教学
18
化学沉铜存在的缺点
• 1.溶液中含有EDTA,废水处理难. • 2.使用甲醛作还原剂,甲醛是致癌物 • 质不利于健康. • 3.氧化还原反应,过程控制难.
优质教学
19
直接电镀
• 特点:1.不含EDTA、HCHO等
•
2.反应为物理吸附过程,易控制。
•
3.工艺流程简化
•
4.适用于水平或垂直
• 分类:1.Pd导电金属薄层
•
2.导电高分子材料
•
3.炭或石墨导电层
优质教学
20
钯系列
• 常见工艺流程: • (去钻污处理) 整孔 预浸 催化
加速 硫化 后处理 微蚀 • 供应商:Shipley、Atotech、Blasberg等 • 适用设备:水平线及垂直线
优质教学
12
加速(Accelerator)
• 目的:将钯Pd周围的Sn沉积物除去
pcb沉铜工艺
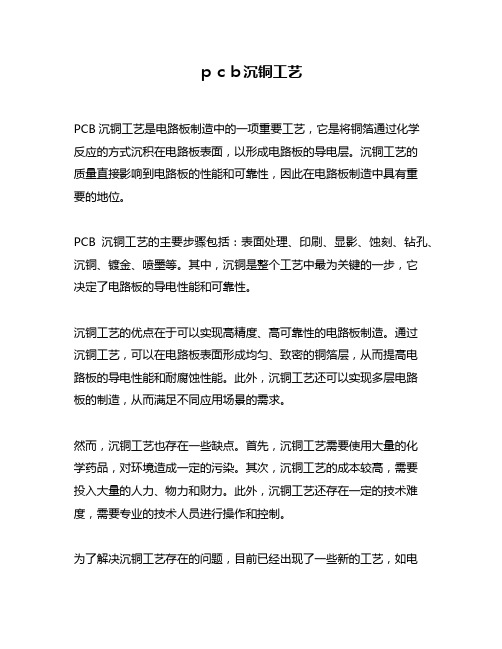
pcb沉铜工艺
PCB沉铜工艺是电路板制造中的一项重要工艺,它是将铜箔通过化学
反应的方式沉积在电路板表面,以形成电路板的导电层。
沉铜工艺的
质量直接影响到电路板的性能和可靠性,因此在电路板制造中具有重
要的地位。
PCB沉铜工艺的主要步骤包括:表面处理、印刷、显影、蚀刻、钻孔、沉铜、镀金、喷墨等。
其中,沉铜是整个工艺中最为关键的一步,它
决定了电路板的导电性能和可靠性。
沉铜工艺的优点在于可以实现高精度、高可靠性的电路板制造。
通过
沉铜工艺,可以在电路板表面形成均匀、致密的铜箔层,从而提高电
路板的导电性能和耐腐蚀性能。
此外,沉铜工艺还可以实现多层电路
板的制造,从而满足不同应用场景的需求。
然而,沉铜工艺也存在一些缺点。
首先,沉铜工艺需要使用大量的化
学药品,对环境造成一定的污染。
其次,沉铜工艺的成本较高,需要
投入大量的人力、物力和财力。
此外,沉铜工艺还存在一定的技术难度,需要专业的技术人员进行操作和控制。
为了解决沉铜工艺存在的问题,目前已经出现了一些新的工艺,如电
镀铜工艺、化学镀铜工艺等。
这些新工艺具有成本低、环保、高效等
优点,逐渐成为电路板制造的主流工艺。
总之,PCB沉铜工艺是电路板制造中不可或缺的一环,它对电路板的
性能和可靠性具有重要的影响。
随着科技的不断发展,电路板制造工
艺也在不断创新和改进,未来将会出现更加高效、环保、可靠的工艺,为电路板制造带来更大的发展空间。
pcb化学沉铜工艺流程
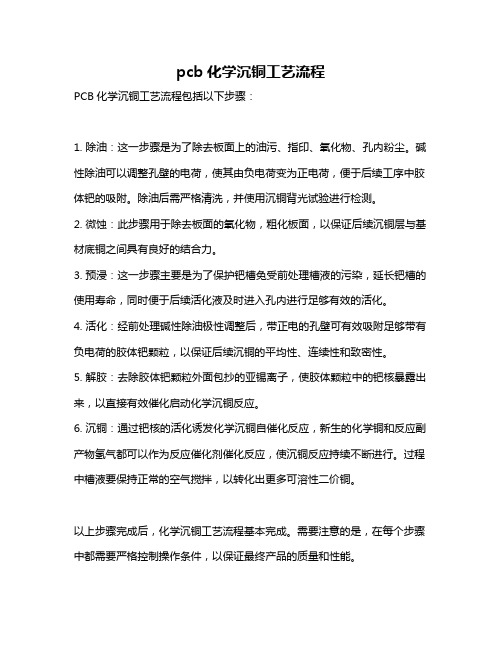
pcb化学沉铜工艺流程
PCB化学沉铜工艺流程包括以下步骤:
1. 除油:这一步骤是为了除去板面上的油污、指印、氧化物、孔内粉尘。
碱性除油可以调整孔壁的电荷,使其由负电荷变为正电荷,便于后续工序中胶体钯的吸附。
除油后需严格清洗,并使用沉铜背光试验进行检测。
2. 微蚀:此步骤用于除去板面的氧化物,粗化板面,以保证后续沉铜层与基材底铜之间具有良好的结合力。
3. 预浸:这一步骤主要是为了保护钯槽免受前处理槽液的污染,延长钯槽的使用寿命,同时便于后续活化液及时进入孔内进行足够有效的活化。
4. 活化:经前处理碱性除油极性调整后,带正电的孔壁可有效吸附足够带有负电荷的胶体钯颗粒,以保证后续沉铜的平均性、连续性和致密性。
5. 解胶:去除胶体钯颗粒外面包抄的亚锡离子,使胶体颗粒中的钯核暴露出来,以直接有效催化启动化学沉铜反应。
6. 沉铜:通过钯核的活化诱发化学沉铜自催化反应,新生的化学铜和反应副产物氢气都可以作为反应催化剂催化反应,使沉铜反应持续不断进行。
过程中槽液要保持正常的空气搅拌,以转化出更多可溶性二价铜。
以上步骤完成后,化学沉铜工艺流程基本完成。
需要注意的是,在每个步骤中都需要严格控制操作条件,以保证最终产品的质量和性能。
化学沉铜原理及异常

化学沉铜原理介绍
流程简介
膨松→除胶渣→中和 Desmear
调整→清洁→调整剂→微蚀→ 预 浸→活化→加速→化铜 PTH
膨松
成分及操作条件:
NaOH 已二醇乙醚 已二醇 水 温度 时间
20g/l 30/l 2g/l 其余 60-80℃ 5min
膨松
• 功能:利用溶剂膨松软化树脂胶渣 • 原理:环氧树脂是高聚形化合物,具有优良的耐
加速反应
注意点: 解胶液主要是控制槽液浓度,时间控制在5分钟左右,
冬天应注意温度控制; 解胶液的更换一般也按生产板的平米数添加更换,
除此之外,解胶液的铜含量也作为一个参考监测项 目,铜含量一般控制在0.7克/升以下; 板件从水洗进入解胶槽或从解胶槽取出时应注意滴 水充分,保证槽液和生产的稳定性;板面水洗后, 颜色应均匀,无明显孔口流液痕迹;
粗化效果不良,板面发花或粗化深度不够,沉铜电镀后,铜层结合力不足, 易产生起泡脱皮现象;粗化过度,孔口铜基材很容易被蚀掉,形成孔口露 基材,造成不必要的报废;另外槽液的温度特别是夏天,一定要注意,温 度太高,粗化太快或温度太低,粗化太慢或不足都会产生上述质量缺陷; 微蚀槽如使用过硫酸盐体系时,铜含量一般控制在25克/升以下,铜含量 太高,会影响粗化效果和微蚀速率;另外过硫酸盐的含量应控制在80— 120克/升; 微蚀槽在开缸时,应留约1/4的旧槽液,以保证槽液中有适量的铜离子, 避免新开缸槽液粗化速率太快,过硫酸盐补充应按50平米/3—6公斤来及 时补充;另外微蚀槽负载不宜过大,亦即开缸时应尽量开大些,防止槽液 因负载过大而造成槽液温度升高过快,影响板面粗化效果; 板面经微蚀处理后,颜色应为均匀粉红色;否则说明除油不足或除油后水 洗不良或粗化不良(可能是时间不足,微蚀剂浓度太低,槽液铜含量太高 等原因造成),应及时检查反馈并处理; 板件从水洗槽进入微蚀槽应注意滴水,尽量减少滴水带入,造成槽液稀释 和温度变化过大,同时板件从微蚀槽取出时,也应注意滴液时间充分;
pcb沉铜原理
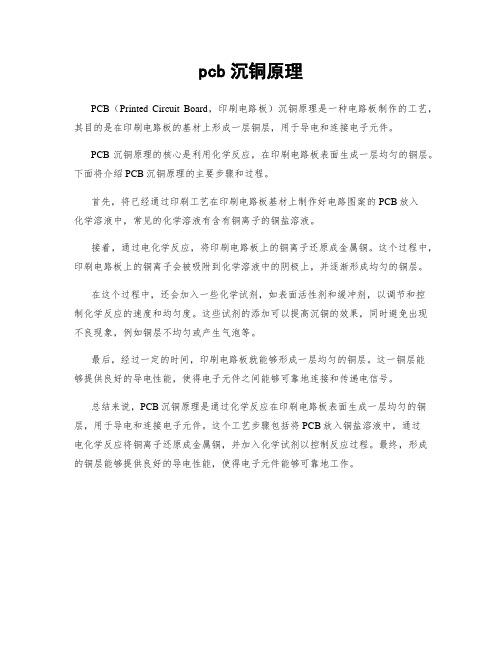
pcb沉铜原理
PCB(Printed Circuit Board,印刷电路板)沉铜原理是一种电路板制作的工艺,其目的是在印刷电路板的基材上形成一层铜层,用于导电和连接电子元件。
PCB沉铜原理的核心是利用化学反应,在印刷电路板表面生成一层均匀的铜层。
下面将介绍PCB沉铜原理的主要步骤和过程。
首先,将已经通过印刷工艺在印刷电路板基材上制作好电路图案的PCB放入
化学溶液中,常见的化学溶液有含有铜离子的铜盐溶液。
接着,通过电化学反应,将印刷电路板上的铜离子还原成金属铜。
这个过程中,印刷电路板上的铜离子会被吸附到化学溶液中的阴极上,并逐渐形成均匀的铜层。
在这个过程中,还会加入一些化学试剂,如表面活性剂和缓冲剂,以调节和控
制化学反应的速度和均匀度。
这些试剂的添加可以提高沉铜的效果,同时避免出现不良现象,例如铜层不均匀或产生气泡等。
最后,经过一定的时间,印刷电路板就能够形成一层均匀的铜层。
这一铜层能
够提供良好的导电性能,使得电子元件之间能够可靠地连接和传递电信号。
总结来说,PCB沉铜原理是通过化学反应在印刷电路板表面生成一层均匀的铜层,用于导电和连接电子元件。
这个工艺步骤包括将PCB放入铜盐溶液中,通过
电化学反应将铜离子还原成金属铜,并加入化学试剂以控制反应过程。
最终,形成的铜层能够提供良好的导电性能,使得电子元件能够可靠地工作。
化学沉铜工艺知识讲解-PPT
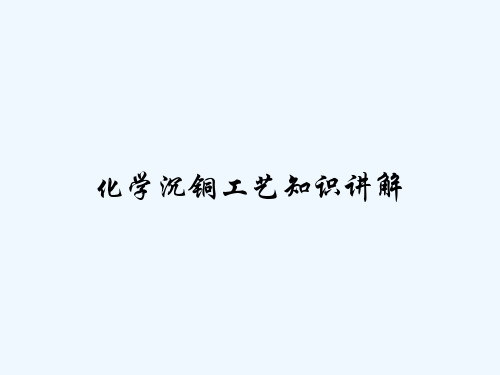
三、工艺流程简介- Plasma
2、1、2 去钻污(针对特殊板材)
去钻污主要针对得是Desmear难以去除得板材类型,包括含碳氢化合物板材、HTg板材等。
2、1、3 电镀夹膜得处理
从图可以清晰得看 出,等离子处理后得 板材可以做出三面 包夹得效果,更好得 增强了可靠性。
2、1、4 去除激光钻孔后得碳膜
三、工艺流程简介-Desmear
3、3、2 MLB 除钻污剂 214(主要成分高锰酸钾+液碱)
作用:
高锰酸钾具有强氧化性,在高温及强碱得条件下,与树脂发生化学反应 使其分解溶去。
反应原理:
4MnO4- + 有机树脂 + 4OH-
4 MnO42- + CO2 + 2H2O
附产物得生成:
KMnO4 + OH - K2MnO4 + H2O + O2
After Plating
二、工艺流程
plamsa
等离子处理
磨板
Desmear 除胶渣
Deburr 去毛刺
MLB 211膨松 Promoter 214除胶渣 Neutralizer 216 中和 Conditioner1175除油
Conditioner233调整
Electroless Copper 化学沉铜
作用:除去板子铜面上得氧化物及其它杂质。粗化铜表面,增强铜面与电解铜得齿结 能力
微蚀前
微蚀后
反应式: Cu+ S2O82- Cu2+ + 2SO42-
微蚀后铜面状况
三、工艺流程简介-沉铜工艺
微蚀中可能出现得问题: 微蚀不足:微蚀不足将导致基铜与铜镀层附着力不良、 微蚀过度:微蚀过度将导致在通孔出现反常形状(见图点A和点B)、这种情况将导致化 学铜得额外沉积并出现角裂(负凹蚀)。 槽液污染 :氯化物和有机物残渣得带入会降低蚀铜量、清洁--调整剂后需保证良好得
水平沉铜工艺原理
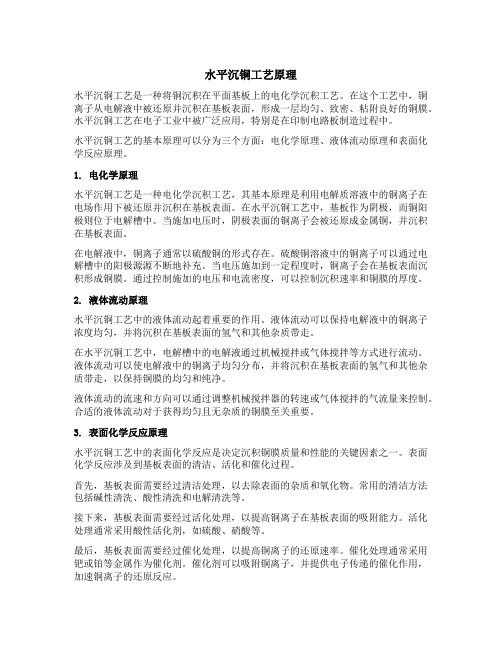
水平沉铜工艺原理水平沉铜工艺是一种将铜沉积在平面基板上的电化学沉积工艺。
在这个工艺中,铜离子从电解液中被还原并沉积在基板表面,形成一层均匀、致密、粘附良好的铜膜。
水平沉铜工艺在电子工业中被广泛应用,特别是在印制电路板制造过程中。
水平沉铜工艺的基本原理可以分为三个方面:电化学原理、液体流动原理和表面化学反应原理。
1. 电化学原理水平沉铜工艺是一种电化学沉积工艺,其基本原理是利用电解质溶液中的铜离子在电场作用下被还原并沉积在基板表面。
在水平沉铜工艺中,基板作为阴极,而铜阳极则位于电解槽中。
当施加电压时,阴极表面的铜离子会被还原成金属铜,并沉积在基板表面。
在电解液中,铜离子通常以硫酸铜的形式存在。
硫酸铜溶液中的铜离子可以通过电解槽中的阳极源源不断地补充。
当电压施加到一定程度时,铜离子会在基板表面沉积形成铜膜。
通过控制施加的电压和电流密度,可以控制沉积速率和铜膜的厚度。
2. 液体流动原理水平沉铜工艺中的液体流动起着重要的作用。
液体流动可以保持电解液中的铜离子浓度均匀,并将沉积在基板表面的氢气和其他杂质带走。
在水平沉铜工艺中,电解槽中的电解液通过机械搅拌或气体搅拌等方式进行流动。
液体流动可以使电解液中的铜离子均匀分布,并将沉积在基板表面的氢气和其他杂质带走,以保持铜膜的均匀和纯净。
液体流动的流速和方向可以通过调整机械搅拌器的转速或气体搅拌的气流量来控制。
合适的液体流动对于获得均匀且无杂质的铜膜至关重要。
3. 表面化学反应原理水平沉铜工艺中的表面化学反应是决定沉积铜膜质量和性能的关键因素之一。
表面化学反应涉及到基板表面的清洁、活化和催化过程。
首先,基板表面需要经过清洁处理,以去除表面的杂质和氧化物。
常用的清洁方法包括碱性清洗、酸性清洗和电解清洗等。
接下来,基板表面需要经过活化处理,以提高铜离子在基板表面的吸附能力。
活化处理通常采用酸性活化剂,如硫酸、硝酸等。
最后,基板表面需要经过催化处理,以提高铜离子的还原速率。
印制电路板化学沉铜详解3

印制电路板化学沉铜详解(三)3. 为后续活化剂的吸附提供一个良好的锚点,使后续的活化胶体耙可以很好的吸附在基材铜的表面:4. 后续的无电铜层可以通过粗化良好的表面与基材铜紧密地结合在一起;5. 其实此处的微蚀还有一个作用:除去板面铜箔上和内层铜箔面上的吸附的作为调整剂的表面活性剂分子,因为在基材铜和化学铜之间存在有机分子层会影响二者之间的结合力)为了达到理想的效果,微蚀要达到一定的深度。
通常情况至少要微蚀到1微米以上,一般在1-2o 5微米左右,微蚀厚度不足即使在后续条件理想条件下,也不一定会有一个满意的结果。
单纯的从基材铜箔上蚀去铜不是我们的真正目的,微蚀剂微蚀后产生的鲜艳粉红色的活性铜面才是我们的真正的所要求的,由此可以得到一个微粗化的活性表面。
微蚀剂作用的好坏会受到槽液里铜含量的高低的影响。
温度也是微蚀液的一个重要参数。
温度太低,微蚀不足甚至铜面依然光亮;温度太高,槽液失控分解报废,板件孔I I露基材,多层板内层铜箔的反回蚀等;多层板的内层铜箔会因为微蚀过度造成回缩,这种现象称为反回蚀,这样会降低无电铜和内层铜箔之间的结合面枳及结合力(因为反回蚀后的部分树脂表面没有经过除油调整而会造成此处的沉铜的连续和沉积性问题,影响板子的连接可靠性信赖度等问题)这是我们不希望看到的。
无电铜和基材铜箔之间的结合力不良一般都是由于微蚀不足和表面清洁度问题造成的。
沉铜后的结合力的拉力试验可以每天一到两次作为沉铜质量控制的手段之一,可以帮助我们及时地发现问题,但是很多工厂只是在问题发生后才去做此检验,这样拉力试验只是作为人们对担心的问题的验证方法而已!拉力试验一般使用约6英寸长宽约0» 5-1英寸的胶带紧紧压贴在铜面上,用力快速的拉起, 胶带应贴在有部分孔的地方,用拇指或硬币按压结实,撕后观察胶带板面有无铜箔被拉起撕掉。
孔I I铜皮翻起的口J能原仄I :板子孔内残留的清洗剂流出而清洗未净;过活化;无电铜沉积不良:孔I I铜皮翻起町能会因为过微蚀和上述的原因:微蚀前的水洗很重要,水洗充分可以确保残留除油剂不带入微蚀槽内或污染铜面。
- 1、下载文档前请自行甄别文档内容的完整性,平台不提供额外的编辑、内容补充、找答案等附加服务。
- 2、"仅部分预览"的文档,不可在线预览部分如存在完整性等问题,可反馈申请退款(可完整预览的文档不适用该条件!)。
- 3、如文档侵犯您的权益,请联系客服反馈,我们会尽快为您处理(人工客服工作时间:9:00-18:30)。
一般情况保证活化时间在4-6分钟即可;
定期的更换预浸液;
避免工件提出槽液后再重新浸入槽液;
活化后的水洗
应该避免太长水洗时间;
充分的清洗水流量;
避免空气搅拌或尽量使用很小的空气搅拌;
清洗水水质要好;
太长的水洗时间会造成活化剂的缓慢破坏,导致活性的降低;同时也会导致表面铜的氧化。
温度也是微蚀液的一个重要参数。温度太低,微蚀不足甚至铜面依然光亮;温度太高,槽液失控分解报废,板件孔口露基材,多层板内层铜箔的反回蚀等;多层板的内层铜箔会因为微蚀过度造成回缩,这种现象称为反回蚀,这样会降低无电铜和内层铜箔之间的结合面积及结合力(因为反回蚀后的部分树脂表面没有经过除油调整而会造成此处的沉铜的连续和沉积性问题,影响板子的连接可靠性信赖度等问题)这是我们不希望看到的。无电铜和基材铜箔之间的结合力不良一般都是由于微蚀不足和表面清洁度问题造成的。沉铜后的结合力的拉力试验可以每天一到两次作为沉铜质量控制的手段之一,可以帮助我们及时地发现问题,但是很多工厂只是在问题发生后才去做此检验,这样拉力试验只是作为人们对担心的问题的验证方法而已!
因为活化剂是一层介于化铜层和基材铜箔或非导电基材上的物质,它可有效的增强铜-铜之间的结合力和化学铜与非导电基材之间的结合力。一般情况下,活化液的活化强度不宜太高,避免在活化槽处理时间过长,活化液中钯含量一般是微量的,但是作用效果却很明显!
活化不良,结果可能会造成铜-铜之间的结合力变差,当然钯的消耗和由此产生的成本也会很高!
采用过硫酸盐体系微蚀剂,微蚀槽一般使用1-3%的稀硫酸溶液来除去微蚀残留物并伴有一个良好的水洗槽。因为无电铜生产线主要是酸性槽液,需要特别注意重金属离子对槽液的污染,这可能会影响化铜的结合力。
活化前处理液/预浸液/预活化液
除去表面氧化物,减少铜离子对活化液的污染;
避免其他粒子的带入和对活化槽液PH值的冲击;
印制电路板化学沉铜详解(三)
3.为后续活化剂的吸附提供一个良好的锚点,使后续的活化胶体钯可以很好的吸附在基材铜的表面;
4.后续的无电铜层可以通过粗化良好的表面与基材铜紧密地结合在一起;
5.其实此处的微蚀还有一个作用:除去板面铜箔上和内层铜箔面上的吸附的作为调整剂的表面活性剂分子,因为在基材铜和化学铜之间存在有机分子层会影响二者之间的结合力)
拉力试验一般使用约6英寸长宽约0。5-1英寸的胶带紧紧压贴在铜面上,用力快速的拉起,胶带应贴在有部分孔的地方,用拇指或硬币按压结实,撕后观察胶带板面有无铜箔被拉起撕掉。
孔口铜皮翻起的可能原因:
板子孔内残留的清洗剂流出而清洗未净;
过活化;
无电铜沉积不良;
孔口铜皮翻起可能会因为过微蚀和上述的原因;
微蚀前的水洗很重要,水洗充分可以确保残留除油剂不带入微蚀槽内或污染铜面。对所有的微蚀剂来讲,碱性有机物是一种毒化剂,会严重破坏微蚀剂的功能;
水洗槽中的水呈黄色和有泡沫产生意味着活化可能出了问题。这种情况下,应该立即关掉水阀,完全放掉水槽内的水,换成新鲜的市水(自来水)方可。
一些良好清洗方法应该做到,详情请参阅《Rinsing,recycle and recovery of plating effluents》作者D.A.Swalheim.这个专题中的建议对所有水洗制程都有好处!
一般情况下,胶体微粒内亚锡离子的数目是钯原子数目的50-100倍左右,胶体颗粒在配制过程当然是越小越好。没有亚锡离子的存在,钯原子会失去活性被氧化为没有活性的钯离子。槽液的活化能力不仅取决于活化液中钯的含量,同时也取决于胶体微粒的复合物结构。活化液在一般情况下是典型的深棕黑色。可以通过分析控制槽液中的亚锡离子含量来保证槽液中有足够的亚锡离子以防止槽液失去活性,维护槽液的稳定性。活化槽本身不可进行空气搅拌,因为会氧化亚锡离子和活化钯颗粒而使之失去活性。
为了达到理想的效果,微蚀要达到一定的深度。通常情况至少要微蚀到1微米以上,一般在1--2。5微米左右,微蚀厚度不足即使在后续条件理想条件下,也不一定会有一个满意的结果。单纯的从基材铜箔上蚀去铜不是我们的真正目的,微蚀剂微蚀后产生的鲜艳粉红色的活性铜面才是我们的真正的所要求的,由此可以得到一个微粗化的活性表面。微蚀剂作用的好坏会受到槽液里铜含量的高低的影响。
活化/催化
良好的活化在化学铜制程中甚至比化学铜本身还要重要。尽管如此,之前的槽液处理也必须良好的处理状态。
活化的胶体钯微粒主要是通过粒子的布朗运动和异性电荷的相互吸附作用分别吸附在微蚀后产生的活性铜面上和经清洗调整处理后的孔壁的非导电基材上。
活化液/催化液主要是有二价的亚锡离子包围钯原子核组成的胶体的溶液。该溶液中含有较高浓度的氯离子和适量的酸,比五到十年前的酸含量已大大降低,以尽量避免或减少多层板反回蚀和粉红圈现象的发生。这种活化性的胶体颗粒会吸附在所有的工件上,包括铜箔表面,非导电基材等,经活化处理后一般情况下非导电基材呈现褐色。
生产板从活化液中提出时应该充分的滴液时间。在很多工厂,钯的消耗主要不是生产板件的消耗,而是板件的带出消耗。锡钯胶体溶液对于外来污染中的一些金属离子特别是铜离子和锑离子很敏感。一般情况下,10-20ppm的锑离子存在可以造成化学沉积层微空洞的产生。但对于铜离子来说,活化液的敏感性稍有不同:对多层板来说,当活化液内的铜含量达到800ppm左右,经过Desmear除胶渣处理后的非导电基材可能会出现一些孔内空洞的问题,;相对于双面板来说,同样的情况只有在活化液的铜含量达到1500-2000ppm甚至更高才会出现。
采用硫酸双氧水作为微蚀剂,需要在一个较高的操作温度下,一般经常在微蚀槽前除油后增加一个硫酸浸洗液主要是为减少碱性材料特别是一些表面活性剂的带入,因为对于硫酸双氧水体系的稳定剂来讲,除油和调整的一些表面活性剂是毒性剂。若采用其他的微蚀剂体系,则要求在微蚀后增加一硫酸浸洗液,以除去微蚀残留物,,但这并不是必需的,特别是对过硫酸盐体系微蚀剂来讲。
预浸液需要经常性更换(与活化液相比价格相对低廉的)。随着时间而带入预浸液的铜离子的不断升高,一般铜含量在超过1克/升前即要更换。
因为强酸性预浸液会攻击多层板内层的黑氧化层甚至残留在内层铜箔的盐酸会加大反回蚀的发生,因此近年来,预浸趋向于降低酸强度(1-2%的盐酸),同样活化液液是如此!(现在的胶体钯多数是盐基的,少数是酸基的,高盐酸型的目前已经被淘汰出线路板行业)
活化后的第一个水洗槽一般会变得很浑浊,是因为锡的氢氧化物的生成。水洗不充分,可能会造成大量的锡的氢氧化物污染活化的表面。(可能会造成化学铜粗糙甚至镀层的结合力)
空气搅拌虽有利于生产板件的清洗效果,但是也可能氧化活化颗粒,使之降低甚至失去活性,这主要看空气搅拌的大小。
此处的清洗水如果采用再生循环水清洗可能会在此处以及还原/加速后的水洗中产生一些问题。这要看是采用何种循环系统再生和哪些清洗水用于循环再生的,可能会产生一些偶然的问题:因为再生循环水可能会含有一些润湿剂或者络合剂或者氧化剂等,这些物质可能会降低活化剂的活性甚至使之完全失去活性,继而造成化学铜的孔内空洞。一旦活化颗粒在处理过程中吸附于生产工件之上后,所有的预防措施都是围绕着如何保证持化颗粒的活性状态而展开的。
过硫酸铵,过硫酸钠,其他如硫酸双氧水氧化剂(一般双氧水1---1。5磅/加仑1%硫酸)以及其他的过硫酸盐微蚀剂,氯化铜不可用做微蚀剂,因为微蚀铜面会残留氯化亚铜,难于清洗去除。
微蚀剂
过硫酸盐型硫酸双氧水型
1.除油剂/调整除油/调整
2.水洗水洗
3浸硫酸溶液微蚀
6.水洗水洗
微蚀的维护预防措施:
用单独的槽子用于无电铜挂具/篮的铜褪镀;
水洗充分---避免铜的带出
化学铜用的挂篮应该用一个单独的槽子去褪镀,不能放在微蚀槽中,因为微蚀剂对金属的带入特别是钯的存在敏感性特别明显,可能会导致槽液的分解;微蚀后良好的水洗也是为了不带入铜离子污染其他化铜前处理液。常见的可作为微蚀剂的化学品主要有以下几种:
就是作为一个牺牲奉献槽;
位于活化液前的预浸液在标准制程SOP上很常见,主要为了减少污染粒子对活化液污染,预浸后生产板件不经水洗直接进入活化槽。因为大部分活化液是氯基的,所以预浸液液是氯基的。在这种情况下,工件带入到活化槽的残留物对活化液来讲都是一种离子污染!
每一次覆铜板进入水槽中浸洗,表面都会发生轻微的氧化,特别是在酸性浸洗后,浸入到一些弱酸液中可以将表面的轻微的氧化物除去,因而减少铜离子对槽液的污染。活化液都有一定程度酸性,弱酸性的预浸液将铜离子溶解在自身溶液内在某种程度上也延长了活化液的寿命。许多活化剂对铜离子污染很敏感。
加速(有时也称为后活化/解胶等)
目的主要是提高或增强活化颗粒的活性。
我们可以设想一下胶体钯颗粒的结构:像一个花蕾,中间是钯原子,周围被层层的亚锡离子包围,最外围是氯离子和氢氧根离子。加速的目的就好像拨开花蕾,除去亚锡离子(也可能会有一些钯颗粒)从而使内部的钯颗粒可以暴露在后续的化铜液中并在后续的沉铜槽液中可以更好的发挥催化活性。