焊接夹具设计准则
装焊夹具设计规范
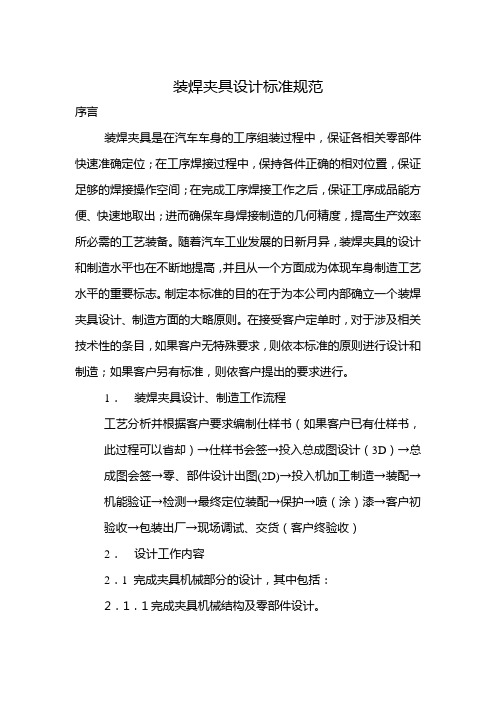
装焊夹具设计标准规范序言装焊夹具是在汽车车身的工序组装过程中,保证各相关零部件快速准确定位;在工序焊接过程中,保持各件正确的相对位置,保证足够的焊接操作空间;在完成工序焊接工作之后,保证工序成品能方便、快速地取出;进而确保车身焊接制造的几何精度,提高生产效率所必需的工艺装备。
随着汽车工业发展的日新月异,装焊夹具的设计和制造水平也在不断地提高,并且从一个方面成为体现车身制造工艺水平的重要标志。
制定本标准的目的在于为本公司内部确立一个装焊夹具设计、制造方面的大略原则。
在接受客户定单时,对于涉及相关技术性的条目,如果客户无特殊要求,则依本标准的原则进行设计和制造;如果客户另有标准,则依客户提出的要求进行。
1.装焊夹具设计、制造工作流程工艺分析并根据客户要求编制仕样书(如果客户已有仕样书,此过程可以省却)→仕样书会签→投入总成图设计(3D)→总成图会签→零、部件设计出图(2D)→投入机加工制造→装配→机能验证→检测→最终定位装配→保护→喷(涂)漆→客户初验收→包装出厂→现场调试、交货(客户终验收)2.设计工作内容2.1 完成夹具机械部分的设计,其中包括:2.1.1完成夹具机械结构及零部件设计。
2.1.2根据工序焊点位置和焊钳样式,在夹具图中进行焊钳动作模拟,并且对干涉部位进行避让修正。
2.2完成气动部分设计,其中包括:2.2.1完成气动原理图设计,列出动作程序时间表。
2.2.2在原理图的明细表中,列出所需气动元件的名称、规格型号、数量及制造或代理厂商。
2.3编制明细表,其中包括:2.3.1自制或外协加工件明细表2.3.2标准件、外购件明细表2.4图纸格式及表述内容2.4.1图纸格式(另附图说明)2.4.2总成图和分总成图均采用总成图标题栏的格式,零件图采用零件图的格式,气动原理图采用总成图的格式。
2.4.3需要在总成图中表述的内容为:工装的总体布局;工装的总体功能及各分总成之间动作配合关系;工装的总体轮廓尺寸及大致装配要求;工装总体的包装、起重、运输要求;对于左右对称制造的工装,需要在总成图中予以说明。
焊装夹具定位设计技术标准
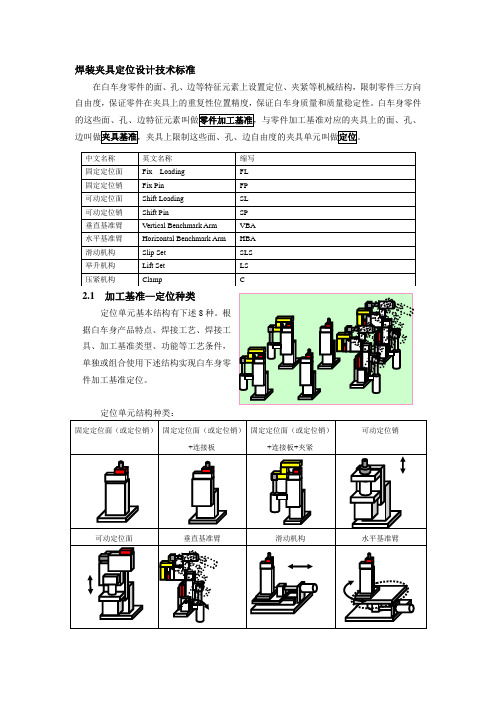
焊装夹具定位设计技术标准在白车身零件的面、孔、边等特征元素上设置定位、夹紧等机械结构,限制零件三方向自由度,保证零件在夹具上的重复性位置精度,保证白车身质量和质量稳定性。
白车身零件2.1 加工基准—定位种类定位单元基本结构有下述8种。
根据白车身产品特点、焊接工艺、焊接工具、加工基准类型、功能等工艺条件,单独或组合使用下述结构实现白车身零件加工基准定位。
定位单元结构种类:2.2定位单元构成定位单元通常由定位块(定位销)、连接板、支座、夹紧块、夹紧臂、铰链、气缸、导向8种基本功能件组成,复杂定位单元需要增加限位块、导轨、二层支座等功能件(如下图所示)。
2.3(白车身零件)加工基准加工基准需要同时满足四大工艺(冲压、焊装、涂装、总装)使用,具有一致性。
加工基准在产品设计时通过工艺评审,最终确定,是完整产品组成的一部分。
按零件面、孔、边的几何特征,加工基准可以划分为:面基准—S(s)、孔基准—H(h)、边基准—E(e);按零件上几何元素功能,加工基准可以划分为:正基准、辅助基准、变换基准等;结合上述两种划分方法,加工基准划分为以下13种,便于使用和管理。
2.4加工基准—定位单元位置精度不同加工基准的定位精度要求不同。
分为三类:孔基准—定位销、面(边)基准—定位块、特殊辅助面基准—定位块。
(1)孔基准—定位销◆孔基准类型:◆定位销、连接板孔配合公差:h7/H7◆ 定位销位置公差:±0.1mm◆ 定位销连接处直径公差:h7◆ 连接板孔直径公差:H7(2) 面基准—定位块◆ 面基准类型:◆ 定位块位置公差:±0.1mm(3) 特殊辅助面基准—定位块◆ 特殊辅助面基准类型:◆定位块位置精度:+0/-0.5㎜e2.5 加工基准—定位单元刚性为保证制造质量的稳定性,要求定位单元的定位件(块、销)装配后其工作方向位置变化<0.1mm 。
既要保证夹具骨架(平台)的结构刚性,还需要保证定位单元的结构刚性。
焊装夹具设计

焊装夹具设计、制造标准1、目的规范焊装夹具的设计、制造及管理,保持合格产品的质量状态。
2、范围本标准规定了公司内部设计与制作或委外设计与制作的夹具应遵守的基本规则。
本标准适用于本公司车辆产品的焊装夹具。
3、夹具制造精度标准3.1焊接夹具精度规格——焊接夹具精度规格值见表1表1 焊接夹具精度规格3.2 底板及槽钢规格底座板、厚度规格值见表2表2 底座板、厚度规格单位:mm底座板、槽钢规格值见表3表3 底座板、槽钢规格值单位:mm3.3 通用支座规格3.3.1 夹具所采用的支承座(即三角架)须满足系列化要求,一般高度为150 mm、200 mm、250mm、300mm、350mm、400mm,且能满足互换性要求,最高不能超过600mm。
3.3.2 通用支座的主要面板厚为19 mm,加强筋板厚为16 mm 。
备注:1. 焊缝应为连续焊缝,并要求牢固、光滑平整、无缺陷。
2. 支座焊后应作退火处理,消除应力。
3. 通用支座板厚为加工后的最小设定尺寸.3.4 定位块厚度规格为16mm.4、夹具设计规范4.1 设计基准:提供图面资料内容:1)AD DATA(3D扫描) 2)成品图或数模图 3)单件图 4)焊接工艺流程 5)焊枪型式图面。
样件需求别纸另议。
4.2设计方式:4.2.1设计通则:2.1.1 装焊夹具设计采用模块化方式,要求满足焊接工艺。
2.1.2 夹具操作方便,设计完成后的工装系统必须符合人机工程学的要求。
2.1.3 夹具应有足够的装配、焊接空间,焊点在布置时应易接近。
2.1.4 夹具本身应有良好的制造工艺性和较高的机械效率。
2.1.5 所有工装夹具,控制面板及面板显示器的标签要求使用中文,如果使用英语应得到业主的批准。
2.1.6 所有图纸和文件中的尺寸、工程单位要求为公制,所有的紧固件都必须是公制的。
设计中使用非公制前都应得到公司的书面批准。
2.1.7 紧固件:采用国标内六角螺栓及定位销,所有的紧固的地方要进行防松处理。
焊接夹具设计规范

焊接夹具设计规范预览说明:预览图片所展示的格式为文档的源格式展示,下载源文件没有水印,内容可编辑和复制第1页焊接夹具设计规范一、目的:规范工程师设计工作,标准化焊接夹具制造工艺。
二、适用范围:适用于本公司所有焊接夹具设计。
三、资料要求:首件打样需提供详细资料。
对于焊接夹具需提供GERBER 、实板及要求。
对于外厂加工而本厂返修则需提供Gerber 及具体数据要求。
四,设计要求:1.焊接工装夹具的设计原则:实用性原则、经济性原则、可靠性原则、艺术性原则。
总之针对PCB 焊接夹具要求:操作方便,定位准确,简单实用。
2.焊接工装夹具的设计步骤与内容。
A 、焊接工装夹具的设计步骤:①根据生产要求,确定实际要焊接元件的数量和位置。
②根据要焊接原件的插装方式初步确定焊接夹具的组装结构。
③根据每一个需要焊接的元件的实际情况,设计夹具的详细结构,如元件避位,元件定位等问题。
B 、焊接结构装配方案的确定:总的要求是能够快速实现定位,拿取方便。
焊接夹具的结构大致分为以下两种:①翻转结构。
翻转结构一般用在被焊接元件是在PCB 板在正面插装,然后翻转180°焊接的情况。
翻转结构的治具一般都带压盖。
②非翻转结构。
非翻转结构按样式的不同又可分为有压盖结构和无压盖结构。
有压盖结构是指被焊接元件在PCB 板的正面插装,然后也在正面焊接,但是需要施加外力把被焊接元件固定在PCB 板上的结构。
对被焊接元件施加力的作用的结构一般被称为压盖。
无压盖结构是指被焊接穿孔元件先安装在焊接夹具上,然后再把PCB 板定位在焊接夹具上的结构。
此时PCB 上的穿孔刚好被穿孔元件的元件脚穿过。
C 、夹具体设计1.夹具设计的时候要注意,由于电路板上元件较多,不允许压到元件,所以要根据PCB 板的实际情况避开元件,包括定位和压紧均是如此。
2.PCB 板要放置平整,否则容易造成焊接元件不良,翘起等问题。
焊装夹具的设计基本原则
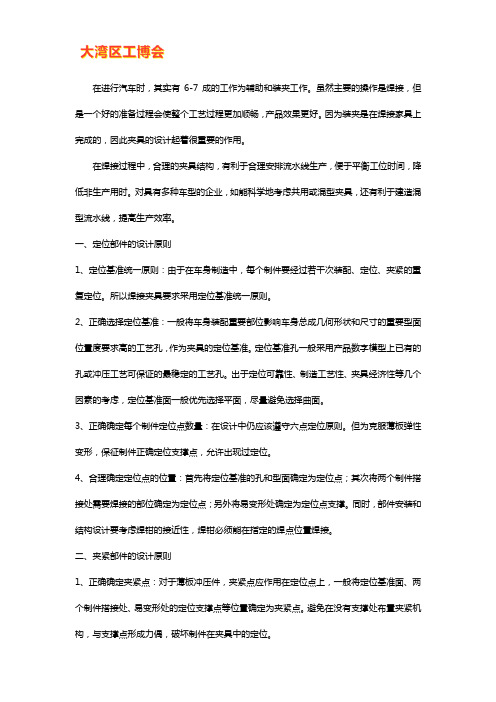
在进行汽车时,其实有6-7成的工作为辅助和装夹工作。
虽然主要的操作是焊接,但是一个好的准备过程会使整个工艺过程更加顺畅,产品效果更好。
因为装夹是在焊接家具上完成的,因此夹具的设计起着很重要的作用。
在焊接过程中,合理的夹具结构,有利于合理安排流水线生产,便于平衡工位时间,降低非生产用时。
对具有多种车型的企业,如能科学地考虑共用或混型夹具,还有利于建造混型流水线,提高生产效率。
一、定位部件的设计原则1、定位基准统一原则:由于在车身制造中,每个制件要经过若干次装配、定位、夹紧的重复定位。
所以焊接夹具要求采用定位基准统一原则。
2、正确选择定位基准:一般将车身装配重要部位影响车身总成几何形状和尺寸的重要型面位置度要求高的工艺孔,作为夹具的定位基准。
定位基准孔一般采用产品数字模型上已有的孔或冲压工艺可保证的最稳定的工艺孔。
出于定位可靠性、制造工艺性、夹具经济性等几个因素的考虑,定位基准面一般优先选择平面,尽量避免选择曲面。
3、正确确定每个制件定位点数量:在设计中仍应该遵守六点定位原则。
但为克服薄板弹性变形,保征制件正确定位支撑点,允许出现过定位。
4、合理确定定位点的位置:首先将定位基准的孔和型面确定为定位点;其次将两个制件搭接处需要焊接的部位确定为定位点;另外将易变形处确定为定位点支撑。
同时,部件安装和结构设计要考虑焊钳的接近性,焊钳必须能在指定的焊点位置焊接。
二、夹紧部件的设计原则1、正确确定夹紧点:对于薄板冲压件,夹紧点应作用在定位点上,一般将定位基准面、两个制件搭接处、易变形处的定位支撑点等位置确定为夹紧点。
避免在没有支撑处布置夹紧机构,与支撑点形成力偶,破坏制件在夹具中的定位。
2、正确确定夹紧力的作用方向:制件在夹具中的夹紧和定位是密切相关的。
夹紧力的作用方向就是向着定位支撑块。
通过定位支撑块的反作用力,使制件与定位块紧密接触。
3、正确决定夹紧力的大小:夹紧力大小应以能克服制件的弹性变形保证定位准确可靠为宜。
焊接制作标准及夹具设计

焊接夹具设计及制造标准总体技术要求:1、所有的夹具均采用气动控制压紧及车型转换方式(特殊规定可采用手动压紧器压紧或不用压紧)。
2、夹具应保证可靠的定位,防止变形,确保装配焊接质量和精度达到产品质量要求。
3、夹具工艺性能优良:各部件装配调整方便、人工焊接易于操作、产品取放方便、有足够的操作空间、操作方便快捷。
4、夹具上产品的高度应在700~800mm之间,对于四周焊接作业困难的应增加360°旋转转盘装置(特殊情况要求还需增加旋转定位锁紧装置)。
5、所有夹具须满足生产纲领的要求。
一、焊接件技术要求:1、焊缝高度不得<5mm、不允许有虚焊脱焊现象、重要部位须采用连续焊缝。
2、焊后清理焊渣、焊缝磨平。
所有部件在焊接后须退火消除应力再进行机加工。
-二、夹具底板1、夹具底板台面全部加工完成后厚度≮20mm,底板与槽钢等加强板料焊接前应校平,留有吊运点或叉车搬运位置,焊后应经退火处理和校平后再进行机加工等后续作业,加工完成后应对台面涂油处理。
2、加强筋规格选用标准(长方形的取最大值):(1)当夹具台面≤1400mm×1400mm时,底板的加强筋应采用10#以上槽钢;(2)当夹具台面>1400mm×1400mm时,底板的加强筋应采用16#以上槽钢;(3)当夹具台面>2000mm×2000mm时,底板的加强筋应采用20#以上槽钢;(4)底座周边的槽钢开口向外,中间加强筋用槽钢的间距不得>700mm.。
3、夹具台面的基准孔及网格坐标线:(1)基准孔:夹具台面上应留有两个坐标系的检测用基准孔,每个方向为两组,每组两个孔,孔径为φ10mm,孔距100mm.(在基准孔附近安装标牌或刻上钢字码,注明坐标数值)(2)网格坐标线:网格坐标线应与产品设计的坐标线对应。
深度及宽度均为0.5mm,间距为200mm.4、夹具台面的周边轮廓尽量与产品零件的轮廓相似,不得有突出的锐角,并尽量往里收,方便操作。
汽车焊装夹具设计、制造规范

汽车焊装夹具设计、制造规范1. 焊装夹具的设计依据:以业主提供的产品数模、国家通用件及标准件为设计依据。
2. 焊装夹具设计通则:2.1焊装夹具设计采取模块化设计方式,要求能满足焊接工艺要求,夹具设计图画法应贯彻国家机械制图标准。
2.2夹具操作方便,设计完成后的工装系统必须符合人机工程学的要求。
2.3夹具应有足够的装配、焊接空间,焊点在布置时应易接近。
2.4夹具本身必须有良好的制造工艺性和较高的机械效率。
2.5 所有工装夹具,控制面板及面板显示器的标签要求使用中文。
如果使用英语应得到业主的认可。
2.6所有图纸和文件中的尺寸、工程单位要求采用公制,所有的紧固件都必须是公制的。
设计中使用非公制前都应得到业主书面认可。
2.7紧固件:采用国标内六角螺钉及圆柱形内螺纹定位销,所有紧固的地方要采取防松措施。
2.8必须尽量选用已通用化、标准化的夹紧机构以及标准零部件,并做到零配件易互换,易维修。
2.9回转夹具要求从回转中心进气(使用特殊的进气机构,可以任意角度转动),回转夹具高度可调节。
2.10手动夹具的夹紧器选用一般推荐选用GOOD HAND牌标准产品。
2.11夹紧气缸一般采用带缓冲机构,以防快速夹紧工件时损坏工件。
3.焊装夹具设计规范及要求:3.1 总图及部件图设计3.1.1 总图设计原则上以左件为基础,图中说明图示为左件,右件与左件对称。
总图上应标注:夹具轮廓尺寸、连接尺寸、安装尺寸、定位尺寸、操作高度、产品件编号及名称、坐标线(与汽车产品数模坐标线统一)、坐标基准、坐标基准孔、各部件的安装位置。
所有定位尺寸、坐标基准孔应相对于坐标线标注,在图中按汽车产品件在汽车中的实际位置建立夹具设计坐标。
在夹具上有产品的摆放位置,并用细双点划线绘出。
焊点位置用表示.设计时应注意焊点的坐标位置,必须留有充分的焊钳工作空间位置,便于施焊。
用双点划线表示焊钳的外形。
总图上还应绘出夹具的操作步骤顺序图,特殊步骤必须详细说明。
焊接夹具设计

制造
1.底板与支座间的定位销孔采用数控镗床或铣床直接加工到位;
2.定位夹紧块的定位夹紧型面采用先切割或数控铣削;
3.支承座、过渡板、定位块的数控定位销孔;
其余非标零件尽可能采用普通加工;
底板的基面加工及刻线采用数控铣床加工。
NOKE标准制
造控制程序
装配
1.紧固螺栓采用内六角螺栓,公制标准件,2.在钢板厚度允许条件下,内六角头应沉入钢板表面。紧固需带弹簧垫圈;尽量从上方和侧面安装螺栓;
3.配有平衡块,转动轻松、灵活。
采用NOKE
标准
夹具
回转
1.采用人工转动;
2.配有分度定位机构和限位挡块;
3.采用标准转台
NOKE
标准
移动
单元
1.带有轴承及防尘装置;
2.设有限位块;
3.大型移动机构(重量大于40kg)采用直线轴承;
4.小型移动机构采用无油润滑轴承;
通用
结构
定位夹紧单元
1.定位销在位置度方向的二维调节;
2、尽可能水平、垂直排管。
3、使用标准汇流板。
4、采用快插接头和软管联接。
5、各类气管快换接头装有防撞盖板,进出气口采用不同颜色区分。
6、对CO2焊接区附近的气管采用硬管或软管加保护。
安全
1.有互锁要求的运动组之间设有气动逻辑互锁,以保护工人安全和工件不受到损坏。
ü典型结构:
焊接夹具标准夹紧单元:
焊接夹具标准定位单元
8.气缸:
焊接夹具设计时,气缸在压紧点处留有5~8mm运动行程余量,防止运动到端点。
9.其它部件:
其余部件设计要求结构简单可靠、维修方便,夹紧件,元器件的选择按选定标准设计。
- 1、下载文档前请自行甄别文档内容的完整性,平台不提供额外的编辑、内容补充、找答案等附加服务。
- 2、"仅部分预览"的文档,不可在线预览部分如存在完整性等问题,可反馈申请退款(可完整预览的文档不适用该条件!)。
- 3、如文档侵犯您的权益,请联系客服反馈,我们会尽快为您处理(人工客服工作时间:9:00-18:30)。
精心整理焊装夹具通用技术标准设计标准编制: 审核: 2010目录一、夹具基本结构夹具示意图 (3)1、平台结构1.1夹具平台技术要求 (4)1.2夹具基准点J B P (4)1.3坐标线 (6)1.4起吊设置 (6)1.5水平调整脚 (7)1.6其它 (8)2、定位夹紧2.1102.2 (10)2.3102.4112.5132.6132.7142.8182.9192.10202.11222.12262.13272.14302.1533 3、4.1 (49)4.254 4、5.1575.2575.3585.4595.5605.660二、铭牌 (61)一、夹具的基本结构夹具示意图1平台结构夹具平台是焊接夹具的骨架,是准确安装定位夹紧单元、旋转、举升等其他功能单元的平台,是整台夹具精度检查测量建系的基准。
(≤。
夹具平台上表面需设有测量建系的基准点—JBP。
具体要求如下:(1)JBP位置、数量要求:为了便于测量,平台上JBP位置不应与其它装置干涉或被覆盖,距离夹具平台边缘≥200㎜,且应保证JBP所在点刻有坐标线网格;平台JBP数量≥5处,间距≤1200mm,特殊的小型夹具平台JBP数量可以设定为3个或4个。
夹具设计会签时,需确定夹具JBP具体位置、数量,并记入《设计会签记录》。
(▽(4) JBP 标识要求:在JBP 的周围打印JBP 坐标值或安装JBP 标识牌(如下图所示),字迹要求清晰整齐,大小适当,耐磨。
JBP 标识不允许被其保护盖覆盖。
1.3 坐标线为便于目测检查,平台上表面需刻印坐标线和坐标线值(如下图所示)。
1.4 起吊装置通常使用吊环螺栓、起吊孔两种形式。
当夹具尺寸较小,使用叉车可以完成安装和运输时,可以根据叉车吨位、叉板宽度、叉板间距调整范围等设备参数,在夹具上设定(或不设定)叉车槽。
夹具设计会签时,需确定夹具起吊装置的具体形式、数量、位置,并记入《设计会签记录》。
吊孔设置示例:吊环螺栓和起吊孔位置需考虑整台夹具的重心位置,保证稳定起吊;需保证起吊时,钢丝绳当夹具与其它设备的相对位置有要求时,水平调整脚需增加地脚支架将其连接于地面,地脚支架用地脚螺栓固定于地面(结构如下图所示)。
对于手工夹具,地脚支架的安装方向不可以影响操作者作业,设置在操作者无作业侧或设置在夹具内侧(如下图所示)。
设置在夹具内侧时需考虑地脚螺栓的转配方法。
其2定位在白车身零件的面、孔、边等特征元素上设置定位、夹紧等机械结构,限制零件三方向自由度,保证零件在夹具上的重复性位置精度,保证白车身质量和质量稳定性。
白车身零件的这些面、孔、2.12.2座、件组成,复杂定位单元需要增加限位块、导轨、二层支座等功能件(如下图所示)。
2.3(白车身零件)加工基准、边基准—2.4 (1)◆ 定位销位置公差:±0.1mm◆ 定位销连接处直径公差:h7 ◆ 连接板孔直径公差:H7 (2) 面基准—定位块◆ 面基准类型:se◆定位块位置公差:±0.1mm(3)特殊辅助面基准—定位块2.6孔基准—定位销基本要求◆定位销型号:使用MISUMI标准规格型号定位销(推荐TLATAN型、TLNTAN型),特殊情况由工艺人员确认;为减少定位销备件,设计尽可能从一汽h◆定位销的工作直径公差:h7◆定位销的有效工作长度:5~7mm;螺母孔—进入2扣螺纹。
◆定位销材料:SCM415(15CrMo)、SCM435(35CrMo)◆定位销热处理方法:淬火◆定位销的表面硬度:≥HRC50◆定位销表面粗糙度:Ra1.6(3)定位销与定位块共点:即孔基准与面基准共点。
◆可以选择下图所示两种定位销紧固方法。
◆拔销作业孔≥Ф20mm,推荐Ф25mm。
◆定位销工作直径根部端面低于定位面,躲避高度≥1㎜,推荐2㎜。
◆定位块从定位面向下≈10㎜宽,加工基准面(边)标识—红色油漆。
◆工作状态(伸缩式定位销伸出)时,需保证定位销工作直径根部端面低于定位块本体,躲避间距≥2㎜。
◆需保证定位销单元刚度,导向杆与气缸活塞杆的连接不可以使用浮动连接。
◆根据《技术协议》要求,在外购件供应商清单选择气缸。
(6)伸缩式定位销—气缸自带单导向杆/夹紧销气缸◆定位销紧固需满足(1)、(2)、(3)要求。
◆需保证定位销径向的两个定位方向刚性(10㎏力作用,位置变动≤0.1㎜)。
◆根据《技术协议》要求,在外购件供应商清单选择气缸。
时,不可以将两个方向长圆孔设定在同一个零件上。
◆调整量=3㎜,长圆孔中心位置对称调整量>3㎜。
◆使用长圆孔调整,量产前需由一汽轿车确认位置,并用焊接、销将位置固定。
◆调整位置尽可能设在定位销附近,以保证定位销单元刚度。
◆ 摆动、滑动的限位以及连接板不调整。
(5) 定位块油漆要求:定位块单件加工检查结束后,按下表要求进行定位块标识油漆、车型标识油漆、防锈油漆,需保证油漆颜色统一。
(6)定位块打号要求:在定位块端面上打印零件号,要求字迹大小一致,清晰。
(7)定位块倒角要求:外表面车身零件定位块定位面周边棱线1㎜×45°◆定位块与连接板之间使用2个连接销+1个螺栓连接。
但当定位块定位面最大尺寸方向>30㎜或定位块高度>60㎜时,需使用2个连接销+2个螺栓连接。
◆活动定位块尽可能使用2个连接销+2个螺栓连接。
◆两种连接方式连接销与螺栓间隔布置。
◆因焊接飞溅,螺栓选用外六角螺栓,规格M8,强度等级10.9级。
◆连接销选用GB120型号、规格Φ6×长度(除主焊线),并用外六角螺丝保护。
◆ 垫片调整方式,使用一组M 型垫片用于PCF 车身匹配。
交货时需保证垫片厚度1㎜×2+0.5㎜×2=3㎜±0.04。
为便于夹具制造精度调整,供应商可以适当增加垫片整体厚度,允许厚度增加1~2㎜。
出厂前需(4) 矫正/暂定面基准—定位块: ◆ 矫正、暂定面基准类型:◆ 使用长圆孔调整,根据移动件移动方向长度设定1个或2个理论基准销(与移动件间隙=3㎜)和防转基准销2个(与移动件间隙=0)。
◆调整量=3㎜,长圆孔中心位置对称调整量>3㎜。
◆长圆孔调整,量产前需由一汽轿车确认后,并用焊接、连接销将位置固定。
◆调整位置尽可能设在定位块定位点附近,保证定位销单元刚度。
◆摆动、滑动的限位以及连接板不调整。
(2)夹紧方向:◆夹紧方向应为定位面的法向(即垂直方向),不能垂直夹紧时,角度≤5°。
◆夹紧时,夹紧臂的横向摆动≤0.5mm。
◆夹紧角度>5°、横向摆动>0.5mm时,需设置夹紧限位机构,以防≈30㎜。
(5)夹紧力要求:30~35㎏f夹紧力。
通常选用活塞直径=50㎜的气缸可以满足夹紧力要求,但当夹紧点与铰链点的距离>2/3夹紧点与气缸铰链点的距离时,需选用活塞直径=63㎜的气缸。
2.11 夹紧单元结构(1) 基本夹紧结构:由夹紧臂、夹紧块、铰链合件(单回转轴)、气缸、气缸铰链5部分组成。
◆ 为确保打开角度最大,铰链回转点应为1/2气缸使用行程。
◆ 为确保夹紧翻入定位销不与零件孔干涉,铰链回转点应在基准孔所在面的延长线上,并设置导向限位机构<使用方法见以下(6)所述>。
◆ 限位、连接板不调整。
◆ 连杆的限位高度≥1/2连杆高度。
(4) 1个夹紧臂同时夹紧2个以上夹紧点:◆多个点同时夹紧,先接触的点能够有效夹紧。
为了让所有的点都能有效夹紧需要将夹紧器设计为摆动式或可调整式。
◆因摆动式不易控制,易损坏零件,通常使用调整式。
(6)限位机构安装方法:◆为防止积尘,限位机构需垂直安装。
不得已必须水平安装时,凸部(7)夹紧单元回转点结构:◆夹紧单元回转点使用铰链销。
◆并用平垫圈、开口销、键板、U型锁紧螺母、开口环等防止铰链轴的轴向松动。
◆推荐使用开口销形式,开口销掰开角度≥60°,铰链轴长度≈(平垫圈厚度+A+4)。
◆使用键板时,键板需用2个螺栓紧固。
◆使用U型锁紧螺母时,U型螺母不能将铰链板轴向紧死。
◆因为开口环需要专用工具拆装,所以尽量不使用开口环。
◆铰链回转点连接板孔设置衬套,孔径=衬套外径H7;铰链板孔不设置衬套,孔径=铰链销直径H7。
◆其他回转支撑点连接板与铰链板均不设置衬套。
孔径=铰链销直径H8。
◆结构复杂的大型夹紧单元,根据需要设计成基准臂结构。
(会签时确(8)外板夹紧保护要求:◆夹紧车身外表面零件外表面时,夹紧块根据防止磕碰需要使聚氨脂材料,邵氏硬度60~80。
(会签时确定)◆由于有耐油性的问题,不允许使用橡胶材料。
◆MC尼龙硬度高,易导致磕碰伤,没有特殊指定,不允许使用。
◆聚氨酯夹紧块结构要求:需设置限位机构,其他参考聚氨酯定位块2.13垂直基准臂可动加工基准的定位可以使用基准臂,基准臂以铰链轴为中心转动。
(1)基准臂的基本结构、刚性要求:◆要确保夹具加工基准处定位刚性(施加10Kg力,定位变形量<0.1mm)。
(2)铰链点结构要求:◆基准臂支点部位的铰链轴的直径要大于驱动用气缸支点铰链销的直径。
(但是,对横向摆动等,基准臂重量,使用小径气缸时,根据基准臂的负荷决定。
)◆铰链轴支撑使用轴承。
(相当于直径系列2,3的轴承,密封型)◆需考虑负荷方向(轴向/径向/复合)的强度、刚性、精度。
◆无润滑轴承参考:开放型、密封型(ZZ)、非接触密封型(LLB、LLF)、低扭矩密封型(LLH)、接触密封型(LLU)。
变形量<0.1mm负荷10Kg带导向的限位铰链驱动部分(气缸)变形量<0.1mm负荷10Kg变形量<0.1mm负荷10Kg◆铰链合件参考图。
(3)带导向的限位的结构:◆为防止积尘,垂直安装。
◆不得已必须水平安装时,凸部向上。
◆定位时为不积留异物(灰尘、焊接飞溅等),下部开放。
◆大型摆臂结构排气时,会因自重而产生下垂,为了防止下垂,应该采用返回侧锁紧的气缸(会签时确定)。
◆车身下部的支撑等,以及负重比较大的摆臂,设计时要考虑零件重量对气缸的作用(会签时确定)。
2.14滑动装置块)。
◆直销固定:轨道长≤300㎜时,可用2个直销定位导轨;当导轨长度>300㎜时需使用多个直销定位,直销之间的间距≤300㎜;滑块依靠和2个直销定位,LM导轨B按LM导轨A找正中心后固定。
LM导轨A◆键板固定:导轨使用2块键板定位后,滑块依靠LM导轨A和2个直销定位,另一导轨B按LM导轨A找正中心位置后固定。
◆机械加工台阶固定:导轨A靠机械加工台阶定位后,滑块靠导轨A和台阶定位,导轨B按导轨A找正中心位置后固定。
导轨。
b)使用线性锁型:轨道和滑块分别使用2个平行销定位,再用线性锁锁紧。
滑块靠放安装数控加工孔的直销定位,进而定位A、B导轨。
(3)直线导轨固定件结构:线性锁参考图。
(4)滑动装置限位结构要求:在滑动装置动作侧和动作返回侧均需设置限位结构。
限位块固定安装:可以用直销直接固定限位块支座、用直销作为限位块支座基准、用机械加工台阶作为限位块支座基准、用键板作为限位2.15水平基准臂——旋转机构加工基准定位夹紧可以通过旋转机构实现,加工基准的定位夹紧单元在旋转台面上随转动平台转动。