基于CAN总线的多点温度采集系统设计
基于CAN总线的分布式多点实时红外测温系统
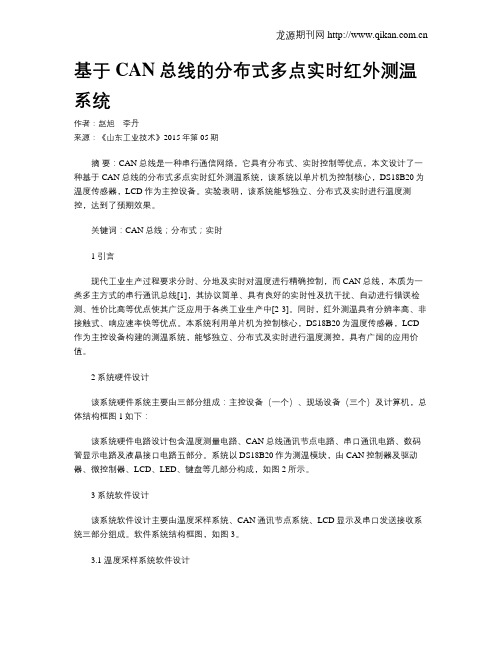
基于CAN总线的分布式多点实时红外测温系统作者:赵旭李丹来源:《山东工业技术》2015年第05期摘要:CAN总线是一种串行通信网络,它具有分布式、实时控制等优点,本文设计了一种基于CAN总线的分布式多点实时红外测温系统,该系统以单片机为控制核心,DS18B20为温度传感器,LCD作为主控设备。
实验表明,该系统能够独立、分布式及实时进行温度测控,达到了预期效果。
关键词:CAN总线;分布式;实时1 引言现代工业生产过程要求分时、分地及实时对温度进行精确控制,而CAN总线,本质为一类多主方式的串行通讯总线[1],其协议简单、具有良好的实时性及抗干扰、自动进行错误检测、性价比高等优点使其广泛应用于各类工业生产中[2-3]。
同时,红外测温具有分辨率高、非接触式、响应速率快等优点。
本系统利用单片机为控制核心,DS18B20为温度传感器,LCD 作为主控设备构建的测温系统,能够独立、分布式及实时进行温度测控,具有广阔的应用价值。
2 系统硬件设计该系统硬件系统主要由三部分组成:主控设备(一个)、现场设备(三个)及计算机,总体结构框图1如下:该系统硬件电路设计包含温度测量电路、CAN总线通讯节点电路、串口通讯电路、数码管显示电路及液晶接口电路五部分。
系统以DS18B20作为测温模块,由CAN控制器及驱动器、微控制器、LCD、LED、键盘等几部分构成,如图2所示。
3 系统软件设计该系统软件设计主要由温度采样系统、CAN通讯节点系统、LCD显示及串口发送接收系统三部分组成。
软件系统结构框图,如图3。
3.1 温度采样系统软件设计温度测量部分在系统软件设计的主程序中不断循环,具体操作包含读写温度预警数据,数据的处理及码制转换等。
这里需注意,在处理DS18B20时:每次读写数据之前需进行复位;在复位成功之后立马发送ROM指令,以发送RAM指令作为结束。
3.2 CAN通讯节点软件设计CAN接口通讯节点软件主要包括三个部分:CAN初始化,数据发送及接收。
基于CAN总线的多点温度监测系统

基于CAN总线的多点温度监测系统在经济高速发展的今天,温度的监测和控制已经成为一个重要的方面。
多点温度的检测也变的相当重要,并且应用于各个领域。
本论文设计了一种基于CAN总线的多点温度监测系统,能够对各个地方的温度进行监控并做出相应的处理。
而且CAN是控制器局域网络是一种国际上应用最广泛的现场总线,具有实时性强、传输距离较远、抗电磁干扰能力强、成本低、结构简单等优点。
标签:can总线;多点温度;监控系统;控制器局域网络1.研究背景1.1 研究背景及意义。
在快速发展的当今社会,不管在工业或是农业和日常的生活中,温度的监测和控制已经成为一个重要的方面。
多点温度的检测也变的相当重要,并且应用于各个领域;空调系统的温度检测和电讯设备过热故障的预知检测,各种交通运输工具内部工作温度的检测,医疗的温度测试,粮仓和楼寓温度的检测。
可见温度监测系统已经完全融入到我们的日常生活中了,并且有着十分广泛的应用。
本文中设计用一台上位机(由LabVIEW编写),下位机(单片机)多点温度数据采集,组成三点温度测量检测系统。
此系统采用CAN总线通讯,在比较各种总线的优缺点之后决定使用最广泛和可靠性最高的CAN总线进行数据的传送,将各个温度采集节点挂接在CAN总线上,经过CAN总线传送到主控节点,送回主控机进行数据处理,并显示出各个点的温度值,使管理人员做出相应的处理。
采用CAN通信,CAN总线具有极高的可靠性、独特灵活的设计和低廉的价格,CAN总线上的节点是网络上的数据接收和发送站,智能节点能够通过编程设置工作方式、ID地址、波特率等参数。
它主要是由STM32F103ZET6单片机和TJA105收发器构成。
CAN控制器工作于多主方式,网络中的各节点都可根据总线访问优先权(取决于报文标识符)采用无损结构的逐位仲裁的方式竞争向总线发送数据,且CAN协议废除了站地址编码,取而代之对通信数据进行编码,这可使不同的节点同时接收到相同的数据,这些特点使得CAN总线构成的网络各节点之间的数据通信实时性强,并且容易构成冗余结构,提高系统的可靠性和系统的灵活性。
基于can总线的温湿度采集系统的设计

理方法 3.1经过上述分析,得出电刷冒火原
因:压力不均和电刷不在电枢几何中心线 上
3.1.1压力不均的原因: 3.1.1.1施压元件结构 3.1.1.2施压元件长期运行已经部分失 去弹性功能; 3.1.1.3碳刷长短过于悬殊及一次更换 电刷过多。 3.1.2电刷不在电枢几何中心线上的 原因: 3.1.2.1电刷与刷窝不配套,研磨的间 隙过大t 3.1.2.2电刷过长(约5cm),而原电 刷(3.5cm)使施压后摆动过大。 3.2针对上述问题,采取了以下5个方 面措施: 3.2.1调整压力将几个比较短而且弹 簧比较小的用皮筋加压。 3.2.2擦拭整流子,用块布擦拭整流
5.吴文珍.韩玉祥.司光宇.董玉红.朴雪梅 基于CAN总线智能检测仪的设计[期刊论文]-大庆石油学院学报 2005(5)
6.SJA1000独立cAN控制器数据手册 7.TJA1050高速CAN收发器数据手册 8.Anon CAN interface 2004(6) 9.基于FT245BM的简易USB接口开发 2007
3.2.5在现场有专人盯住处理,发现 问题及时消除,并稳定一段时间。
经过上述措施处理,2#励磁机电刷火 花等级下降至一级以下,甚至达到无火花 程度,但是需要明确的是在运行中处理电 刷冒火必须是有实践运行维护经验的人员, 在有把握的前提卜实施运行中处理,否则 应安排停机处理。 4.结论及建议
4.1绪论 2#发电机励磁机电刷冒火原因:一 是施压弹簧压力不均,二是电刷不在几何 中心线上,造成整流子表面氧化亚铜薄膜 被破坏,使换向闲难。 经过采取卜.述措施,火花得以消除,在 运行中还必须注意监视和维护,发现小火 花立即消除,不能维持长期运行。 4.2建议: 4.2.1应定期检查恒压弹簧压力及转 轴。 4.2.2运行中电刷不能过短,注意监视 及时更换。如果磨过短造成了整流子表面 磨损时,在停机后应用机床处理。提高处理 精度(挠沟、例角、找正等)。 4.2.3电刷应错位安装,只要在刷窝与 刷臂同定之间加以不同厚度反坦崮即可, 此方法町以相对加宽电刷尺寸,改善换向 条件。 4.2.4如有可能在整流子表面,采用 涂铬丁艺,既ur以解决冒火问题,又大大减 少了整流子的磨损。 4.2.5如有条件最好把发电机组更换成 为无刷励磁方式。 5.效果检查 按照上述处理方法,我厂2#机励磁 机无火运行到2006年4月小修。小修中将 施压弹簧更新,整流子表面进行处理,机组 启动后,一直运行到目前,状态良好。
基于can总线的温度采集与显示系统
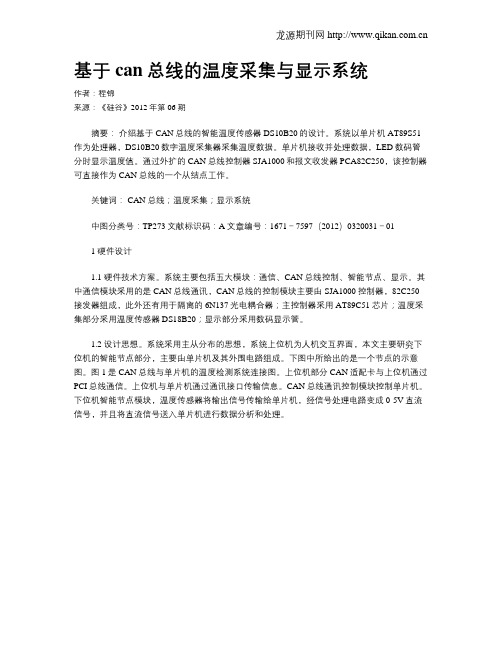
基于can总线的温度采集与显示系统作者:程锦来源:《硅谷》2012年第06期摘要:介绍基于CAN总线的智能温度传感器DS10B20的设计。
系统以单片机AT89S51作为处理器,DS10B20数字温度采集器采集温度数据。
单片机接收并处理数据,LED数码管分时显示温度值。
通过外扩的CAN总线控制器SJA1000和报文收发器PCA82C250,该控制器可直接作为CAN总线的一个从结点工作。
关键词: CAN总线;温度采集;显示系统中图分类号:TP273文献标识码:A文章编号:1671-7597(2012)0320031-011 硬件设计1.1 硬件技术方案。
系统主要包括五大模块:通信、CAN总线控制、智能节点、显示。
其中通信模块采用的是CAN总线通讯,CAN总线的控制模块主要由SJA1000控制器,82C250接发器组成,此外还有用于隔离的6N137光电耦合器;主控制器采用AT89C51芯片;温度采集部分采用温度传感器DS18B20;显示部分采用数码显示管。
1.2 设计思想。
系统采用主从分布的思想,系统上位机为人机交互界面,本文主要研究下位机的智能节点部分,主要由单片机及其外围电路组成。
下图中所给出的是一个节点的示意图。
图1是CAN总线与单片机的温度检测系统连接图。
上位机部分CAN适配卡与上位机通过PCI总线通信。
上位机与单片机通过通讯接口传输信息。
CAN总线通讯控制模块控制单片机。
下位机智能节点模块,温度传感器将输出信号传输给单片机,经信号处理电路变成0-5V直流信号,并且将直流信号送入单片机进行数据分析和处理。
图1系统结构图1.3 CAN总线通讯设计。
89C51作为CAN总线系统智能节点的微处理器,在CAN总线通信接口中采用的是PHILIPS公司的SJA1000和82C250芯片。
SJA1000是CAN通信控制器,82C250是CAN总线的收发器。
为了使总线上各个CAN节点之间实现隔离,SJA1000与P82C250之间要通过高速光电耦合器6N137相连。
CAN总线多点温度采集节点硬件设计

CAN总线多点温度采集节点硬件设计【摘要】随着科学技术的发展,温度监控系统的应用越来越广泛,本文阐述了一种基于CAN总线的多点温度采集系统,可以实现温度实时监测,该系统能应用于工农业生产的诸多场合。
系统以AT89C52单片机为微处理器,外接数字式温度传感器DS18B20获得现场环境的温度信号。
通过CAN总线控制器SJA1000和CAN总线驱动器PCA82C250将数据发送到CAN总线上,从而实现对温度的采集。
【关键词】CAN总线;节点;温度采集0 概述现场总线是安装在生产制造过程中的装置与控制室内的控制装置之间的一种数字式、串行、多点通信的数据线。
应用现场总线技术不仅可以降低系统的布线成本,还具有设计简单、调试方便等优点。
同时,由于现场总线本身还提供了灵活且功能强大的协议,这就使得用户对系统配置,设备选型具有强大的自主权,可以任意的将多种功能模块组合起来扩充系统的功能。
在众多的现场工业总线中。
随着温度控制技术在各个领域得到广泛地推广和应用,相关行业对温度控制技术的要求与日俱增。
目前市场上也有一些温度控制系统,但是这些系统在传送数据时实时性能实现的不是很好,而CAN总线的实时性强、成本低,而且还具备可靠性高、抗干扰强等特点。
综合多方面因素考虑,我们能够利用CAN总线的特点和优势设计温度控制系统。
1 设计方案1.1 系统功能要求系统能够接受数字式温度传感器DS18B20的温度信号,将温度信号传给单片机,完成单片机最小系统设计,并把此系统作为CAN的节点,节点的硬件包括AT89C52单片机、CAN总线驱动器PCA82C250、CAN总线控制器SJA1000、单片机的时钟和复位电路。
主要研究基于AT89C52单片机与DS18B20数字温度传感器的多点温度测量系统。
完成数字式温度传感器与CAN总线节点的接口设计及电路设计,实现具有数字式串行温度采集功能的CAN总线节点的硬件设计。
应用CAN总线控制器SJA1000及其总线收发器的工作原理,完成数字式温度传感器与CAN总线节点的接口设计。
基于PIC18F4580的CAN总线多点温度采集系统设计
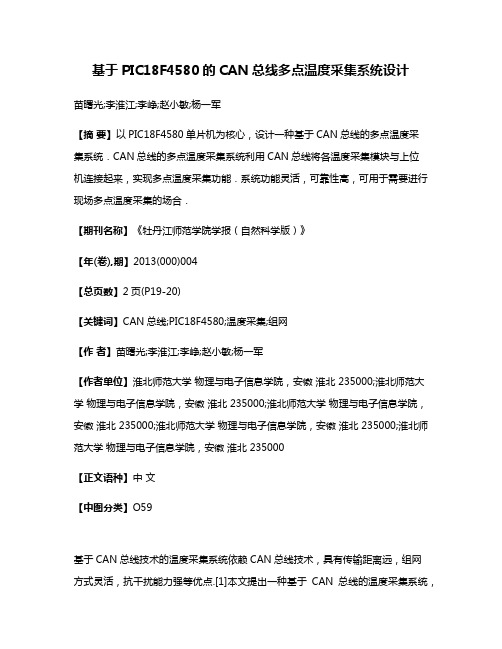
基于PIC18F4580的CAN总线多点温度采集系统设计苗曙光;李淮江;李峥;赵小敏;杨一军【摘要】以PIC18F4580单片机为核心,设计一种基于CAN总线的多点温度采集系统.CAN总线的多点温度采集系统利用CAN总线将各温度采集模块与上位机连接起来,实现多点温度采集功能.系统功能灵活,可靠性高,可用于需要进行现场多点温度采集的场合.【期刊名称】《牡丹江师范学院学报(自然科学版)》【年(卷),期】2013(000)004【总页数】2页(P19-20)【关键词】CAN总线;PIC18F4580;温度采集;组网【作者】苗曙光;李淮江;李峥;赵小敏;杨一军【作者单位】淮北师范大学物理与电子信息学院,安徽淮北 235000;淮北师范大学物理与电子信息学院,安徽淮北 235000;淮北师范大学物理与电子信息学院,安徽淮北 235000;淮北师范大学物理与电子信息学院,安徽淮北 235000;淮北师范大学物理与电子信息学院,安徽淮北 235000【正文语种】中文【中图分类】O59基于CAN总线技术的温度采集系统依赖CAN总线技术,具有传输距离远,组网方式灵活,抗干扰能力强等优点.[1]本文提出一种基于CAN总线的温度采集系统,利用现场总线CAN-Bus技术和数字温度传感器DS18B20,以总线方式进行组网,通过CAN232协议转换器和上位机PC进行通信.1 系统硬件设计1.1 总体设计思路CAN总线温度采集网络结构如图1所示.系统包括温度采集节点、CAN232节点和上位机软件.温度采集器负责采集温度数据,通过CAN总线,传输到CAN232协议转换器,通过RS232口和上位机软件进行通信,从而实现对温度的实时动态采集.温度采集节点由以下几个部分组成:带有CAN总线接口的单片机PIC18F4580、数字温度传感器DS18B20、显示模块、电源模块等.[2]图1 CAN总线温度采集网络结构1.2 微控制器和CAN通信单元设计系统采用内部集成CAN控制器单元的PIC18F4580系列作为控制核心单元,和其他单片机相比,该单片机集成度高,不需要外扩CAN控制器,性价比高;内置CAN总线模块,符合国际标准ISO CAN,高达1Mbps的通信速率,与CAN2.0B版本一致,有优越的错误处理性能.[3]CAN收发器单元采用高速的CAN收发器TJA1050.TJA1050是控制器区域网络(CAN)协议控制器和物理总线之间的接口.控制器和CAN通信单元电路如图2所示.图2 控制器和CAN单元电路图1.3 温度传感器模块设计温度传感器选择的是数字温度传感器DS18S20.电路连接仅需一条数据线,通过10K上拉电阻,接到PIC18F4580的RB4管脚,对于每一个DS18S20,在其内部ROM中具有唯一的64位序列号,因此多个传感器可以同时接于数据总线,构成分布式多点温度测控系统.1.4 CAN232协议转换器设计CAN232协议转换器是计算机和CAN总线的通信桥梁.本文通过RS232口实现和CAN数据的交换,CAN模块电路的设计和温度采集节点相同,只需要在温度节点基础上增加一个RS232单元电路即可,RS232电路主要通过MAX232芯片设计完成.[4]2 系统软件设计系统软件主要完成传感器温度数据的采集、处理、显示以及通过CAN总线模块传输,[5]程序流程如图3所示.图3 温度采集发送流程图3 系统测试图4是三个温度采集节点实时采集的温度数据,通过CAN232传输到上位机的测试界面.串口波特率是4 800,十六进制发送,十六进制接收,CAN总线的波特率设置为10kbps,系统具有温度实时显示和查询功能.图4 系统运行界面从系统运行界面中可以看到,1号、2号和3号节点采集节点的温度都是27℃,测试环境选择在实验室,温度节点之间的距离比较近,所以实测温度相同,作为对照,此时用标准温度计测量的温度为26.5℃,误差为0.5℃.实验结果表明,设计能够满足温度测量精度的要求.4 结语系统采用内部集成CAN控制器的单片机,结合数字温度传感器DS18B20设计的一款基于现场总线温度的采集网络,具有卓越的低功耗、集成度高、体积小、抗干扰能力强、传输距离远等特点.实验测试结果表明,该温度采集网络不仅能够更方便地获取通信数据,且能把数据通过CAN总线发送到PC机,具有实时显示温度和动态查询功能,在工农业温度监控,煤矿井下温度监控方面具有重要的应用价值.参考文献【相关文献】[1]邬宽明.现场总线技术应用选编[M].北京:北京航空航天大学出版社,2003:50-55.[2]孙培民,孙鑫.基于单片机的通信系统[J].牡丹江师范学院学报:自然科学版,2009(3):29-30.[3]刘和平.PIC18Fxxx单片机原理及接口程序设计[M].北京:北京航空航天大学出版社,2006:1-20.[4]饶运涛.现场总线CAN原理与应用技术[M].北京:北京航空航天大学出版社,2003:100-120.[5]李峥,苗曙光,陈得宝,等.单片机指令系统中绝对调用指令的地址范围分析[J].牡丹江师范学院学报:自然科学版,2013(1):16-17.。
基于CAN总线的多点温度采集系统设计

【摘要】随着科学技术的发展,为提供农作物生长的最佳环境,大棚种植也成为现代农业种植中必要可行的一种方式。
在温室大棚中的温度实时监测与控制却成为为一个难题。
因此基于CAN总线的主要优点,再从CAN总线的可靠性,它的优越性以及低成本出发,采用基于CAN总线多点温度采集系统的设计,该系统采用非破坏性总线仲裁技术具有实时性高,精度高,灵活性强能够及时信息的测控。
本课题是采用一种基于CAN总线的多点温度采集系统。
论文根据系统的要求完成了整体的方案设计和系统选型。
该方案是利用温度传感器PT100将温室大棚内温度的变化,经放大电路送入含A/D转换器的单片机的采集模块完成A/D转换,在通过CAN收发器将信号传至住监视器。
再经过液晶显示器进行数据显示。
CAN总线通信模块是本次设计中的核心技术,它负责系统中主控器和执行器之间的数据通信。
经过试验验证表明该系统可靠性好、精度高、结果简单、成本低在使用范围可代替传统的测温系统的不足。
【关键词】CAN总线微控制器传感器Pt100 液晶显示器。
Design of multi-spot temperature gathering system based on CANbus【Abstract】With the development of science and technology, to provide the best environment for crop growth, greenhouse cultivation has become an essential of modern farming viable way. The temperature in greenhouse real-time monitoring and control has become a problem. Therefore, the main advantages based on CAN bus, CAN bus, and from the reliability, technological superiority of the system operation and low cost starting point based on CAN bus multi-temperature collection system design, system technology using non-destructive real-time bus arbitration high, high precision, flexibility and timely information to the monitoring and control.This issue is based on CAN bus using a multi-point temperature acquisition system. System requirements thesis completed under the overall program design and system selection. The program is the use of the greenhouse temperature sensor PT100 temperature changes, the amplifier circuit into with A / D converter module to complete the acquisition of SCM A / D converter, CAN transceiver through the signal transmitted live monitor. Data for another LCD display. CAN bus communication module is the core of this design technique, which is responsible for the system and implementation of master data communication between devices.Tested to verify that the system reliability, high accuracy, the results of simple, low cost alternative to the use of conventional temperature measurement system deficiencies.【Keywords】The can bus MCU sensor Pt100 LCD monitors。
基于CAN总线和PID算法的多点水温控制系统
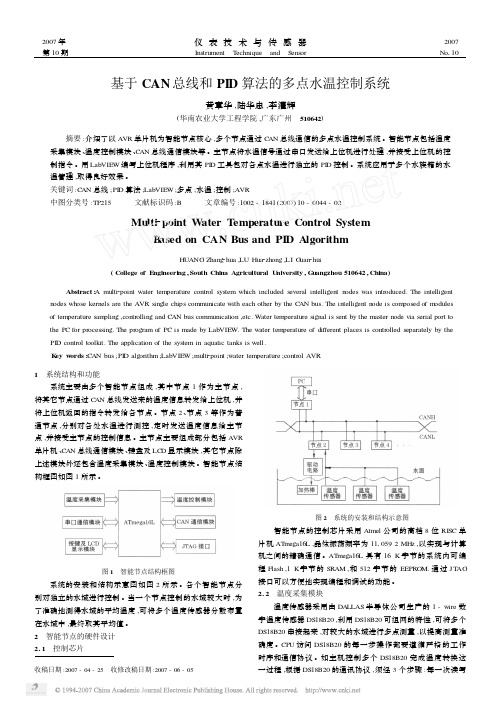
PWM 信号由 ATmega16L 的定时/ 计数器 1 的输出端口 OC1A 产
生 。如果当前温度值小于设定温度值 ,则由 PWM 信号控制加
热棒工作 ,随着温差值的减小 ,PWM 占空比也逐渐减小 ,使加热
定系统的研制. 仪表技术与传感器 ,2003 (7) :20 - 22. 作者简介 :赵又力 (1979 —) ,讲师 ,研究方向为机械设计及理论 。
(上接第 45 页) 模块 、参数设定和数据显示存储模块 、串口通信 模块等 。
4. 1 PID 控制模块 PID 控制模块的核心是 LabVIEW 软件的 PID 工具包[2] ,具
1 系统结构和功能 系统主要由多个智能节点组成 ,其中节点 1 作为主节点 ,
将其它节点通过 CAN 总线发送来的温度信息转发给上位机 ,并 将上位机返回的指令转发给各节点 。节点 2 、节点 3 等作为普 通节点 ,分别对各处水温进行测控 ,定时发送温度信息给主节 点 ,并接受主节点的控制信息 。主节点主要组成部分包括 AVR 单片机 、CAN 总线通信模块 、键盘及 LCD 显示模块 ,其它节点除 上述模块外还包含温度采集模块 、温度控制模块 。智能节点结 构框图如图 1 所示 。
第 10 期
黄章华等 :基于 CAN 总线和 PID 算法的多点水温控制系统
4 5
之前都要对 DS18B20 进行复位 ,复位成功后发送一条 MATCH ROM 指令 ,最后发送 RAM 指令 ,这样才能对各个 DS18B20 进行 预定的操作 。 2. 3 温度控制模块
温度控制电路主要由光电耦合器和可控硅组成 ,如图 3 所 示 。单片机发出控制信号 ( PWM) 经驱动器后控制光电耦合器 的状态 。当光电耦合器工作后 ,使双向可控硅的触发极处于高 电平 ,可控硅处于导通状态 ,进而控制加热棒的工作 。系统使 用双向可控硅 ,使交流的 220 V 电压在全周期内都能够加载在 加热棒上 。使用光电耦合器能够有效地降低外界对系统的影 响 ,增强了系统的稳定性 。其中光电耦合器采用 MOC3401 ,可 控硅采用 BT138 - 600 ,其耐压为 600 V. RL 为加热棒 。
- 1、下载文档前请自行甄别文档内容的完整性,平台不提供额外的编辑、内容补充、找答案等附加服务。
- 2、"仅部分预览"的文档,不可在线预览部分如存在完整性等问题,可反馈申请退款(可完整预览的文档不适用该条件!)。
- 3、如文档侵犯您的权益,请联系客服反馈,我们会尽快为您处理(人工客服工作时间:9:00-18:30)。
【摘要】随着科学技术的发展,为提供农作物生长的最佳环境,大棚种植也成为现代农业种植中必要可行的一种方式。
在温室大棚中的温度实时监测与控制却成为为一个难题。
因此基于CAN总线的主要优点,再从CAN总线的可靠性,它的优越性以及低成本出发,采用基于CAN总线多点温度采集系统的设计,该系统采用非破坏性总线仲裁技术具有实时性高,精度高,灵活性强能够及时信息的测控。
本课题是采用一种基于CAN总线的多点温度采集系统。
论文根据系统的要求完成了整体的方案设计和系统选型。
该方案是利用温度传感器PT100将温室大棚内温度的变化,经放大电路送入含A/D转换器的单片机的采集模块完成A/D转换,在通过CAN收发器将信号传至住监视器。
再经过液晶显示器进行数据显示。
CAN总线通信模块是本次设计中的核心技术,它负责系统中主控器和执行器之间的数据通信。
经过试验验证表明该系统可靠性好、精度高、结果简单、成本低在使用范围可代替传统的测温系统的不足。
【关键词】CAN总线微控制器传感器Pt100 液晶显示器。
Design of multi-spot temperature gathering system based on CANbus【Abstract】With the development of science and technology, to provide the best environment for crop growth, greenhouse cultivation has become an essential of modern farming viable way. The temperature in greenhouse real-time monitoring and control has become a problem. Therefore, the main advantages based on CAN bus, CAN bus, and from the reliability, technological superiority of the system operation and low cost starting point based on CAN bus multi-temperature collection system design, system technology using non-destructive real-time bus arbitration high, high precision, flexibility and timely information to the monitoring and control.This issue is based on CAN bus using a multi-point temperature acquisition system. System requirements thesis completed under the overall program design and system selection. The program is the use of the greenhouse temperature sensor PT100 temperature changes, the amplifier circuit into with A / D converter module to complete the acquisition of SCM A / D converter, CAN transceiver through the signal transmitted live monitor. Data for another LCD display. CAN bus communication module is the core of this design technique, which is responsible for the system and implementation of master data communication between devices.Tested to verify that the system reliability, high accuracy, the results of simple, low cost alternative to the use of conventional temperature measurement system deficiencies.【Keywords】The can bus MCU sensor Pt100 LCD monitors。
目录绪论 (1)1开发概述 (2)1.1背景 (2)1.2课题来源 (3)1.3国内外研究现状 (3)1.4论文主要工作 (3)1.5论文结构 (4)2.相关技术的概念 (4)2.1总线的概述 (4)2.2 CAN总线的特点 (4)2.3 CAN总线的分层结构 (5)2.4 CAN总线的发展应用 (6)3硬件系统的设计 (6)3.1硬件的设计任务 (6)3.2 硬件设计模块 (7)3.2.1 硬件电路 (7)3.2.2 PIC18F4580单片机 (7)3.2.3 电源电路 (9)3.2.4 传感器电桥和放大电路 (9)3.2.5 CAN收发器连接电路 (10)3.2.6 液晶显示器电路[13] (10)3.3综上所述 (11)4软件设计 (11)4.1监视器主程序 (11)4.2采集系统主程序 (11)4.3 CAN总线的接收和发送程序 (12)4.6按键子程序 (15)4.7 A/D转换流程图 (16)4.8 液晶显示模块程序 (17)总结及展望 (18)参考文献 (19)附录 (20)致谢........................................................ 错误!未定义书签。
绪论在人类生活的环境中,温度扮演找极其重要的角色,无论你生活在哪里,从事什么工作,无时无刻不在和温度打交道。
我国人多地少,人均占有更少,因此,要改变我国的这种局限,要靠增加耕地面积是不现实的,为此,我们只有另辟蹊径,在原本就不宽裕的土地上来想办法提高单位产量,而温室大棚种植就是一种行之有效的方法。
随着大棚种植的技术的大面积的推广和应用,大棚种植温度检测控制技术要求逐渐提高,基于市场提供的一些温度检测系统不能实时的传送数据,而且主要考虑到器件的繁杂和费用的高选择利用了CAN总线的优越性能,CAN总线采用多主竞争式结构,通信介质可以是双绞线,同轴电缆,或光导纤维。
通信率可达1Mbps,CAN总线通信接口中集成了CAN 协议的物理层和数据链路层功能,可完成对通信数据的成幀处理,包括位填充,数据块编码,循环冗余检码,优先级判别等[1]。
温室系统气候受影响的因数多样。
复杂而且众多,难以完全计算在内。
针对目前的温室系统的现状和特点,决定采用当前比较先进的现场总线技术进行控制。
设计了温室系统的总体框架,各种植区各由一个智能节点来控制,节点之间采用现场总线相连,实现分散控制,再接入一计算机作为人机接口,实行监督。
根据现代温室控制的要求,设计一套适合问世控制系统的应用现场总线技术。
本文经过查阅大量国内外参考文献的基础上,概述了温室在国内外的发展历史以及发展现状。
了解了国内外温室测控装置的发展动态和发展方向,并且根据温室内影响作物生长所需的基本条件,即温度、环境的条件、控制特点和控制方法,设计出了出了适合本系统的控制方案。
1开发概述在科学社会高速发展的今天,引发了自动化域的深刻变革,并使自动化领域逐渐形成了开放系统互联网通信,以大大深刻的改善了大棚种植温度采集和控制的优越性,形成了高集成化的自动控制系统。
CAN (Controller Area Network)即控制器局域网络,属于工业现场总线的范畴。
在与其他的通信总线相比较,CAN总线在数据通信方面具有突出的可靠性、实时性和灵活性。
由于CAN总线具有独特的设计及其良好的性能,CAN总线在人们的生活中的运用是越来越广泛。
它首先是在汽车领域上的应用最为突出,世界上一些著名的汽车制造厂商,都利用CAN总线来实现汽车内部控制系统与各检测和执行机构间的数据通信。
于此同时,由于CAN总线本身优越的特点,其应用范围目前已不再局限于汽车行业之中,而向自动控制、航海、航空航天、机械工业、纺织机械、农用机械、机器人、数控机床、医疗器械及传感器等领域发展的应用也比较突出。
CAN已经形成国际标准,并已被公认为最有前途的几种现场总线之一[2]。
本文将设计一种由CAN总线完成测控系统间数据通信、结构灵活、通用性强的温度测控系统,在该系统中,我们同时使用了单总线数字温度传感器Pt100,并能方便的实现系统互联。
将传感器的输出变换成标准电压或电流信号,通过A/D转换变成数字量。
将数字量信号传给单片机,最后单片机将采集到的数据送到CAN总线控制器,通过CAN总线收发器传到总线,完成数据采集工作任务。
1.1背景20世纪50年代以前,由于当时企业的生产规模较小,测控仪表处于发展的初级阶段,所采用的仅仅是安装在生产现场,只具备简单测控功能的基于20.67-103.35Pa启动信号标准的基地式气动仪表。
其信号仅在本以表内使用,不能传送给别的仪表或系统,即各测控仪表处于封闭的状态,无法与外界沟通信息,操作人员只能通过生产现场的巡视,才可以了解生产过程的状况[3]。
20世纪60年代,随着企业的生产规模的进一步扩大,操作人员需要综合掌握多点的运行参数和信息,需要同时按多点的信息实行操作控制,因此出现了气动、电动单元组合式仪表,形成了集中控制室。
生产现场中的各参数通过统一的模拟信号送往集中控制室。
操作人员可以在控制室内观察生产现场的状况,可以把各单元仪表的信号按需要组合成复杂测控系统[4]。
20世纪70年代,人们在测量、模拟和逻辑控制领域率先使用了数字计算机,从而产生了集中式控制。
数据采集系统是计算机应用于生产过程控制最早的一种类型。
把需要采集的过程参数经过采样、A/D转换变为数字信号送入计算机。
计算机对这些输入量进行计算处理(如数字滤波、标度变换、越限报警等),并按需要进行显示和打印输出[5]。
经过实践发展证明,这类系统虽然不直接参与生产过程的控制,但其作用还是较为明显。
由于计算机具有速度、运算方便等特点,在过程参数的测量和记录中可以代替大量的常规显示和记录仪表,对整个生产过程进行集中监视。
数据采集系统主要是对大量传输参数进行巡回检测、数据记录、、数据统计和处理、以及对大量数据进采集储存和实时分析。