陶瓷粉末的制备
陶瓷喷雾造粒方法

陶瓷喷雾造粒方法
陶瓷喷雾造粒方法是一种常见的制备微米级陶瓷粉末的方法。
该方法通过将陶瓷原料溶解或悬浮于溶剂中,然后将其喷雾成微小液滴,最终通过热处理将液滴转化为陶瓷粉末。
陶瓷喷雾造粒方法具有以下优点:
1. 粒径分布均匀:由于喷雾过程中液滴的大小可以控制,因此制备出的陶瓷粉末粒径分布均匀,可以满足不同应用的需求。
2. 纯度高:该方法可以制备出高纯度的陶瓷粉末,因为在喷雾过程中,原料与溶剂之间的相互作用力可以有效地去除杂质。
3. 生产效率高:陶瓷喷雾造粒方法可以实现大规模生产,因此可以满足工业化生产的需求。
陶瓷喷雾造粒方法的具体步骤如下:
1. 准备陶瓷原料和溶剂:将陶瓷原料和溶剂按照一定比例混合,制备成溶液或悬浮液。
2. 喷雾:将溶液或悬浮液通过喷雾器喷雾成微小液滴,液滴大小可以通过调整喷雾器的参数来控制。
3. 干燥:将喷雾得到的液滴在烘箱中进行干燥,使其转化为固体颗粒。
4. 热处理:将固体颗粒进行热处理,使其转化为陶瓷粉末。
需要注意的是,在陶瓷喷雾造粒方法中,喷雾器的参数对最终产品的质量有很大影响,因此需要进行充分的实验和优化。
此外,陶瓷喷雾造粒方法还可以与其他制备方法相结合,如球磨、热压等,以获得更好的制备效果。
陶瓷制备的化学方程式
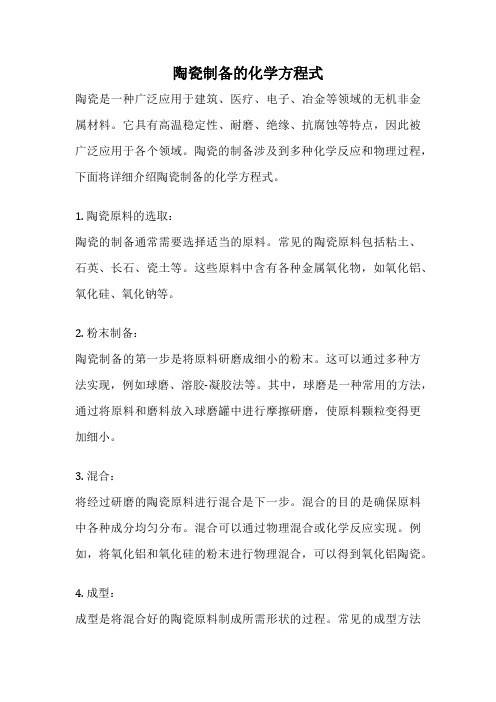
陶瓷制备的化学方程式陶瓷是一种广泛应用于建筑、医疗、电子、冶金等领域的无机非金属材料。
它具有高温稳定性、耐磨、绝缘、抗腐蚀等特点,因此被广泛应用于各个领域。
陶瓷的制备涉及到多种化学反应和物理过程,下面将详细介绍陶瓷制备的化学方程式。
1. 陶瓷原料的选取:陶瓷的制备通常需要选择适当的原料。
常见的陶瓷原料包括粘土、石英、长石、瓷土等。
这些原料中含有各种金属氧化物,如氧化铝、氧化硅、氧化钠等。
2. 粉末制备:陶瓷制备的第一步是将原料研磨成细小的粉末。
这可以通过多种方法实现,例如球磨、溶胶-凝胶法等。
其中,球磨是一种常用的方法,通过将原料和磨料放入球磨罐中进行摩擦研磨,使原料颗粒变得更加细小。
3. 混合:将经过研磨的陶瓷原料进行混合是下一步。
混合的目的是确保原料中各种成分均匀分布。
混合可以通过物理混合或化学反应实现。
例如,将氧化铝和氧化硅的粉末进行物理混合,可以得到氧化铝陶瓷。
4. 成型:成型是将混合好的陶瓷原料制成所需形状的过程。
常见的成型方法包括压制、注塑、挤出等。
以压制为例,将混合好的陶瓷粉末放入模具中,施加一定的压力使其成型。
5. 烧结:烧结是陶瓷制备的核心步骤之一。
经过成型的陶瓷坯体需要进行高温处理,使其颗粒之间发生结合,形成致密的陶瓷材料。
烧结的温度通常较高,可以达到原料的熔点以上。
烧结过程中,陶瓷原料中的金属氧化物发生氧化还原反应,形成金属氧化物之间的化学键。
6. 冷却:经过高温烧结后的陶瓷材料需要进行冷却,使其达到室温。
冷却过程中,陶瓷材料逐渐固化,形成坚硬的陶瓷。
7. 补充工艺:制备出的陶瓷材料还需要进行一些补充工艺,如抛光、涂层等。
这些工艺可以提高陶瓷的光洁度、表面硬度等性能。
陶瓷制备的化学方程式主要涉及原料的选取、粉末制备、混合、成型、烧结等步骤。
在这些过程中,陶瓷原料中的金属氧化物发生氧化还原反应,形成陶瓷材料的化学键。
通过这些化学反应和物理过程,我们可以制备出各种具有优异性能的陶瓷材料。
陶瓷粉末成型工艺
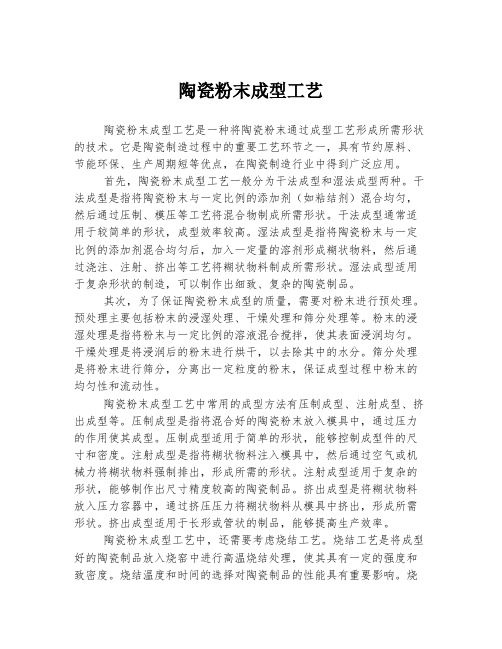
陶瓷粉末成型工艺陶瓷粉末成型工艺是一种将陶瓷粉末通过成型工艺形成所需形状的技术。
它是陶瓷制造过程中的重要工艺环节之一,具有节约原料、节能环保、生产周期短等优点,在陶瓷制造行业中得到广泛应用。
首先,陶瓷粉末成型工艺一般分为干法成型和湿法成型两种。
干法成型是指将陶瓷粉末与一定比例的添加剂(如粘结剂)混合均匀,然后通过压制、模压等工艺将混合物制成所需形状。
干法成型通常适用于较简单的形状,成型效率较高。
湿法成型是指将陶瓷粉末与一定比例的添加剂混合均匀后,加入一定量的溶剂形成糊状物料,然后通过浇注、注射、挤出等工艺将糊状物料制成所需形状。
湿法成型适用于复杂形状的制造,可以制作出细致、复杂的陶瓷制品。
其次,为了保证陶瓷粉末成型的质量,需要对粉末进行预处理。
预处理主要包括粉末的浸湿处理、干燥处理和筛分处理等。
粉末的浸湿处理是指将粉末与一定比例的溶液混合搅拌,使其表面浸润均匀。
干燥处理是将浸润后的粉末进行烘干,以去除其中的水分。
筛分处理是将粉末进行筛分,分离出一定粒度的粉末,保证成型过程中粉末的均匀性和流动性。
陶瓷粉末成型工艺中常用的成型方法有压制成型、注射成型、挤出成型等。
压制成型是指将混合好的陶瓷粉末放入模具中,通过压力的作用使其成型。
压制成型适用于简单的形状,能够控制成型件的尺寸和密度。
注射成型是指将糊状物料注入模具中,然后通过空气或机械力将糊状物料强制排出,形成所需的形状。
注射成型适用于复杂的形状,能够制作出尺寸精度较高的陶瓷制品。
挤出成型是将糊状物料放入压力容器中,通过挤压压力将糊状物料从模具中挤出,形成所需形状。
挤出成型适用于长形或管状的制品,能够提高生产效率。
陶瓷粉末成型工艺中,还需要考虑烧结工艺。
烧结工艺是将成型好的陶瓷制品放入烧窑中进行高温烧结处理,使其具有一定的强度和致密度。
烧结温度和时间的选择对陶瓷制品的性能具有重要影响。
烧结温度过高会使陶瓷制品变形或烧结不充分,烧结温度过低则会影响陶瓷制品的力学性能和致密度。
陶瓷粉体制备ppt课件.ppt
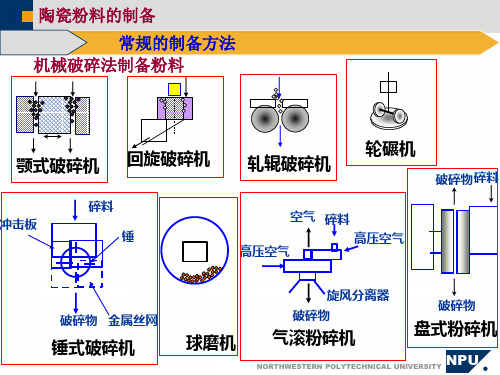
1100-1200℃
NbC
Nb+炭黑
H2,CO, CnHm
1400-1500℃
真空
1200-1300℃
Nb2O5+炭黑
H2,CO, CnHm
1900-2000℃
真空
1600-1700℃
TaC
Ta+炭黑
H2,CO, CnHm
1400-1600℃
真空
1200-300℃
Ta2O5+炭黑
为了克服直接沉淀的缺点,改变沉淀剂的加入方式,使得溶液本身缓慢反应产生沉淀剂,常用的有尿素: (NH2)2CO+3H2O→2NH4OH+CO2 (70℃) NH4OH在溶液中形成后立即被消耗,尿素继续分解平衡,可用来制备铁、铝、锡、镓、锆等的氧化物。
铝粉和B2O3粉料在刚玉罐中球磨混合1h,经真空干燥后,压坯,置入充满氩气的反应器中,进行燃烧合成。反应器内压力可在500Pa~0.1Mpa之间调节,用钨丝通电点火。热电偶插入试样心部测温。球磨后得到粉料。
Al2O3
AlB12
自蔓延法有以下优点: 1、工艺简单 2、消耗外部能量少 3、可在真空或者控制气氛下进行,得到高纯产品 4、材料烧成与合成可同时完成
900℃5h
1300℃2h
先进陶瓷粉料的制备
固相法制备粉料
可以获得高纯的Al2O3, 粒度小于1μm
用于碳化硅生产的阿奇逊电炉 (a)炉役开始前;(b)炉役结束后
分步反应: SiO2+C → SiO(气)+CO SiO+2C → SiC+CO SiO+C → Si(气)+CO Si+C → SiC
先进陶瓷粉料的制备
A(S)+B(S)→C(S)+D(g)
陶瓷粉贴生产工艺
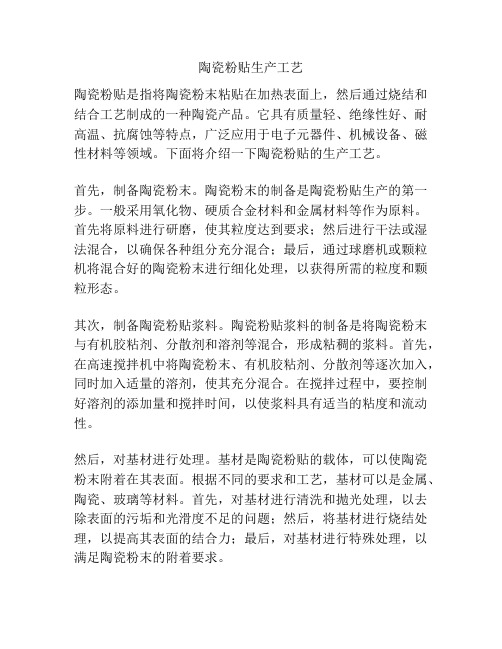
陶瓷粉贴生产工艺陶瓷粉贴是指将陶瓷粉末粘贴在加热表面上,然后通过烧结和结合工艺制成的一种陶瓷产品。
它具有质量轻、绝缘性好、耐高温、抗腐蚀等特点,广泛应用于电子元器件、机械设备、磁性材料等领域。
下面将介绍一下陶瓷粉贴的生产工艺。
首先,制备陶瓷粉末。
陶瓷粉末的制备是陶瓷粉贴生产的第一步。
一般采用氧化物、硬质合金材料和金属材料等作为原料。
首先将原料进行研磨,使其粒度达到要求;然后进行干法或湿法混合,以确保各种组分充分混合;最后,通过球磨机或颗粒机将混合好的陶瓷粉末进行细化处理,以获得所需的粒度和颗粒形态。
其次,制备陶瓷粉贴浆料。
陶瓷粉贴浆料的制备是将陶瓷粉末与有机胶粘剂、分散剂和溶剂等混合,形成粘稠的浆料。
首先,在高速搅拌机中将陶瓷粉末、有机胶粘剂、分散剂等逐次加入,同时加入适量的溶剂,使其充分混合。
在搅拌过程中,要控制好溶剂的添加量和搅拌时间,以使浆料具有适当的粘度和流动性。
然后,对基材进行处理。
基材是陶瓷粉贴的载体,可以使陶瓷粉末附着在其表面。
根据不同的要求和工艺,基材可以是金属、陶瓷、玻璃等材料。
首先,对基材进行清洗和抛光处理,以去除表面的污垢和光滑度不足的问题;然后,将基材进行烧结处理,以提高其表面的结合力;最后,对基材进行特殊处理,以满足陶瓷粉末的附着要求。
最后,进行粘贴和烧结。
将制备好的陶瓷粉贴浆料均匀地涂敷在经过处理的基材上,然后通过压贴或层积等方式将其粘贴在一起。
接下来,将粘贴好的陶瓷粉贴进行烧结。
烧结温度和时间根据不同的陶瓷粉末和工艺要求而定。
在烧结过程中,通过控制温度和气氛,使粘贴在基材上的陶瓷粉末烧结成为致密坚实的陶瓷体。
最后,对烧结好的陶瓷粉贴进行必要的后处理,如抛光、加工、检测等,以保证其质量和性能。
以上是一般陶瓷粉贴的生产工艺流程,具体生产过程中还可能涉及到一些特殊要求和工艺,需要根据具体的产品和工艺要求进行调整和改进。
同时,对于不同类型的陶瓷粉贴,其生产工艺也会有差异。
因此,在生产过程中要根据具体情况进行合理的控制和调整,以确保产品的质量和性能。
【精品文章】碳化锆(ZrC)陶瓷粉体的制备方法综述
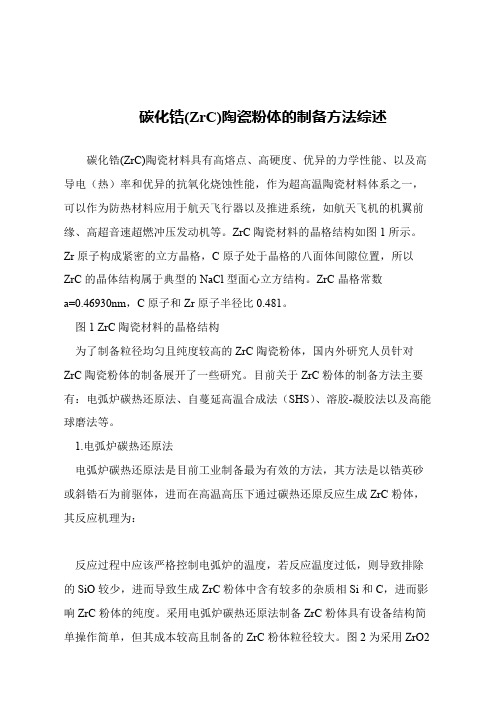
碳化锆(ZrC)陶瓷粉体的制备方法综述
碳化锆(ZrC)陶瓷材料具有高熔点、高硬度、优异的力学性能、以及高导电(热)率和优异的抗氧化烧蚀性能,作为超高温陶瓷材料体系之一,可以作为防热材料应用于航天飞行器以及推进系统,如航天飞机的机翼前缘、高超音速超燃冲压发动机等。
ZrC陶瓷材料的晶格结构如图1所示。
Zr原子构成紧密的立方晶格,C原子处于晶格的八面体间隙位置,所以ZrC的晶体结构属于典型的NaCl型面心立方结构。
ZrC晶格常数
a=0.46930nm,C原子和Zr原子半径比0.481。
图1 ZrC陶瓷材料的晶格结构
为了制备粒径均匀且纯度较高的ZrC陶瓷粉体,国内外研究人员针对ZrC陶瓷粉体的制备展开了一些研究。
目前关于ZrC粉体的制备方法主要有:电弧炉碳热还原法、自蔓延高温合成法(SHS)、溶胶-凝胶法以及高能球磨法等。
1.电弧炉碳热还原法
电弧炉碳热还原法是目前工业制备最为有效的方法,其方法是以锆英砂或斜锆石为前驱体,进而在高温高压下通过碳热还原反应生成ZrC粉体,其反应机理为:
反应过程中应该严格控制电弧炉的温度,若反应温度过低,则导致排除的SiO较少,进而导致生成ZrC粉体中含有较多的杂质相Si和C,进而影响ZrC粉体的纯度。
采用电弧炉碳热还原法制备ZrC粉体具有设备结构简单操作简单,但其成本较高且制备的ZrC粉体粒径较大。
图2为采用ZrO2。
固相法制备陶瓷粉体
固相反应法生产陶瓷粉体一、 固相反应法的特点固相法是通过从固相到固相的变化来制造粉体,其特征是不像气相法和液相法伴随有气相→固相、液相→固相那样的状态(相)变化。
对于气相或液相,分子(原子)有很大的易动度,所以集合状态是均匀的,对外界条件的反应很敏感。
另一方面,对于固相,分子(原子)的扩散很迟缓,集合状态是多样的。
固相法其原料本身是固体,这较之于液体和气体都有很大的差异。
固相法所得的固相粉体和最初固相原料可以使同一物质,也可以不是同一物质。
[1]二、 物质粉末化机理一类是将大块物质极细地分割,称作尺寸降低过程,其特点是物质无变化,常用的方法是机械粉碎(用普通球磨、振磨、搅拌磨、高能球磨、喷射磨等进行粉碎),化学处理(溶出法)等。
另一类是将最小单位(分子或原子)组合,称作构筑过程,其特征是物质发生了变化,常用的方法有热分解法(大多数是盐的分解),固相反应法(大多数是化合物,包括化合反应和氧化还原反应),火花放电法(常用金属铝产生氢氧化铝)等。
三、 固相反应的具体方法1、 机械粉碎法主要应用是球磨法,机械球磨法工艺的主要目的包括离子尺寸的减小、固态合金化、混合或融合以及改变离子的形状。
目前已形成各种方法,如滚转磨、振动磨和平面磨。
采用球磨方法,控制适合的条件可以得到纯元素、合金或者是复合材料的纳米粒子。
其特点是操作简单、成本低,但产品容易被污染,因此纯度低,颗粒分布不均匀[2]。
2、热分解法热分解反应不仅仅限于固相,气体和液体也可引发热分解反应,在此只讨论固相的分解反应,固相热分解生成新的固相系统,常用如下式子表示(S 代表固相、G 代表气相):1211212S S G S S G G →+→++第一个式子是最普通的,第二个式子是第一个式子的特殊情况。
热分解反应基本是第一式的情况。
3、 固相反应法由固相热分解可获得单一的金属氧化物,但氧化物以外的物质,如碳化物、硅化物、氮化物等以及含两种金属元素以上的氧化物制成的化合物,仅仅用热分解就很难制备,通常是按最终合成所需组成的原料化合,再用高温使其反应的方法,其一般工序如左图所示。
陶瓷喷涂工艺(3篇)
第1篇一、引言陶瓷喷涂工艺是一种将陶瓷材料通过特殊工艺喷涂到金属、塑料、木材等基材表面,形成一层具有陶瓷性能的涂层的工艺。
陶瓷喷涂具有优异的耐磨性、耐腐蚀性、耐高温性、绝缘性等性能,广泛应用于航空航天、汽车制造、化工、电力、建筑等行业。
本文将详细介绍陶瓷喷涂工艺的原理、特点、工艺流程及注意事项。
二、陶瓷喷涂工艺原理陶瓷喷涂工艺的基本原理是将陶瓷粉末和粘结剂按照一定比例混合,通过高速气流将混合物雾化,然后喷涂到基材表面。
在喷涂过程中,陶瓷粉末和粘结剂发生化学反应,形成一层具有陶瓷性能的涂层。
三、陶瓷喷涂工艺特点1. 优异的耐磨性:陶瓷喷涂涂层具有很高的硬度,耐磨性极佳,能有效延长基材的使用寿命。
2. 良好的耐腐蚀性:陶瓷喷涂涂层具有优异的耐腐蚀性能,能够抵抗各种化学介质的侵蚀。
3. 耐高温性:陶瓷喷涂涂层具有很高的熔点,能在高温环境下保持稳定的性能。
4. 绝缘性:陶瓷喷涂涂层具有良好的绝缘性能,能有效防止电流泄露。
5. 环保:陶瓷喷涂工艺采用环保材料,对环境无污染。
6. 施工简便:陶瓷喷涂工艺操作简便,可适用于各种复杂形状的基材。
四、陶瓷喷涂工艺流程1. 陶瓷粉末制备:根据需要喷涂的陶瓷材料,选择合适的陶瓷粉末,并对其进行筛选、研磨等处理。
2. 粘结剂选择:根据陶瓷粉末的性质和基材的要求,选择合适的粘结剂。
3. 混合:将陶瓷粉末和粘结剂按照一定比例混合均匀。
4. 雾化:将混合好的陶瓷粉末和粘结剂通过高速气流雾化。
5. 喷涂:将雾化的陶瓷粉末和粘结剂喷涂到基材表面。
6. 烧结:将喷涂后的涂层进行烧结处理,使其固化。
7. 后处理:对烧结后的涂层进行表面处理,如打磨、抛光等。
五、注意事项1. 陶瓷粉末选择:选择合适的陶瓷粉末是保证涂层性能的关键。
2. 粘结剂选择:粘结剂的选择应与陶瓷粉末和基材相匹配。
3. 混合比例:陶瓷粉末和粘结剂的混合比例应按照要求进行。
4. 雾化效果:雾化效果直接影响涂层的均匀性和质量。
陶瓷造粒方法
一、引言陶瓷是一种具有高温稳定性、耐腐蚀性、耐磨损性和绝缘性等特点的材料,因此在工业生产中得到了广泛的应用。
为了满足不同领域对陶瓷材料性能的要求,需要对陶瓷进行造粒处理。
本文将介绍几种常见的陶瓷造粒方法。
二、湿法造粒湿法造粒是一种将陶瓷粉末与液体混合后,在搅拌或喷雾干燥的过程中形成颗粒的方法。
该方法适用于制备粘合力强、颗粒均匀、粒径分布窄的陶瓷粉末。
例如,在一项研究中,研究人员采用湿法造粒方法制备了La2O3掺杂的氧化钆(Gd2O3)陶瓷粉末。
首先将La2O3和Gd2O3混合,加入适量的水,形成悬浊液。
然后在搅拌器中搅拌,使混合物均匀分散,最后在干燥器中喷雾干燥,得到颗粒均匀、粒径分布窄的陶瓷粉末。
三、干法造粒干法造粒是一种将陶瓷粉末在机械强制作用下,通过碰撞、磨擦和压缩等作用形成颗粒的方法。
该方法适用于制备粒径较大、形状规则的陶瓷颗粒。
例如,在一项研究中,研究人员采用干法造粒方法制备了具有高热稳定性的氧化锆(ZrO2)陶瓷颗粒。
首先将ZrO2粉末放入球磨机中,加入适量的碳酸钠(Na2CO3)作为助熔剂,然后在球磨机中进行球磨,最后在高温下烧结,得到形状规则、粒径较大的氧化锆陶瓷颗粒。
四、溶胶-凝胶法溶胶-凝胶法是一种将陶瓷前驱体在溶液中形成胶体后,通过干燥和烧结等过程形成陶瓷颗粒的方法。
该方法适用于制备粒径小、形状规则、表面光滑的陶瓷颗粒。
例如,在一项研究中,研究人员采用溶胶-凝胶法制备了具有高比表面积的氧化铝(Al2O3)陶瓷颗粒。
首先将铝异丁酸溶解在乙醇中,形成胶体,然后在恒温搅拌的条件下,使胶体凝胶化。
最后在高温下烧结,得到形状规则、表面光滑、粒径小的氧化铝陶瓷颗粒。
五、结论以上介绍了几种常见的陶瓷造粒方法,每种方法都有其适用的场合和优缺点。
在实际应用中,需要根据具体情况选择合适的方法,以满足不同领域对陶瓷材料性能的要求。
第一章特种陶瓷粉体的物理性能及其制备
Ao =A / V, 单位 m2/m3 或m-1 。
2、粉体颗粒的吸附与凝聚
粉体所以区别于一般固体而呈独立物态,是因为:一方 面它是细化了的固体;另一方面,在接触点上与其它粒 子间有相互作用力存在。此外,颗粒之间也相互附着而 形成团聚体。 附着:一个颗粒依附于其它物体表面上的现象。 附着力(force of adhesion):存在于异种固体表面的引力。 凝聚:颗粒间在各种引力作用下的团聚。 凝聚力(agglomerative force) :存在于同种固体表面间的 引力。
积、可压缩性、流动性和工艺性能有重要影响。
特种陶瓷的制备,实际上是将特种陶瓷的粉体原
料经过成型、热处理,最终成为制品的过程。因 此,学习和掌握好特种陶瓷粉体的特性,并在此 基础上有目的地进行粉体制备和粉体性能调控、 处理,是获得优良特种陶瓷制品的重要前提。粉
体的制备方法一般可分为粉碎法和合成法两种。
3) 氧化还原法
非氧化物特种陶瓷的原料粉末多采用氧化物还原方法制备。 或者还原碳化,或者还原氮化。如SiC、Si3N4等粉末的制备。 SiC粉末的制备:将SiO2与碳粉混合,在1460~1600℃的加 热条件下,逐步还原碳化。其大致历程 如下: SiO2 + C → SiO+CO SiO + 2C → SiC+CO SiO + C → Si+CO Si + C → SiC Si3N4粉末的制备:在N2条件下,通过SiO2与C的还原-氮化。 反应温度在1600℃附近。其基本反应如下: 3SiO2+6C+2N2 → Si3N4 +6CO
2) 化合反应法
两种或两种以上的固体粉末,经混合后在一定的热力学条件 和气氛下反应而成为复合物粉末,有时也伴随气体逸出。化 合反应的基本形式: A(s)+B(s)→C(s)+D(g) 钛酸钡粉末、尖晶石粉末、莫来石粉末的合成都是化学反应 法: BaCO3+TiO2→BaTiO3+CO2 Al2O3+MgO→MgAlO4 3Al2O3+2SiO2→3Al2O3· 2SiO2
- 1、下载文档前请自行甄别文档内容的完整性,平台不提供额外的编辑、内容补充、找答案等附加服务。
- 2、"仅部分预览"的文档,不可在线预览部分如存在完整性等问题,可反馈申请退款(可完整预览的文档不适用该条件!)。
- 3、如文档侵犯您的权益,请联系客服反馈,我们会尽快为您处理(人工客服工作时间:9:00-18:30)。
第五章高纯超细粉末的制备新工艺
一、概述
高技术陶瓷的制造成本
粉体的重要性质:
组成、粒子形状、结晶性、集合状态
理想的陶瓷粉末:
颗粒尺寸小、结晶形态、颗粒形态、颗粒尺寸分布、纯度、无团聚、流动性---
二、超细粉末制备方法的分类
机械方法(物理制备):球磨、砂磨、振动磨、星形磨、
气流粉碎
化学制备法:
(1)固相法:氧化还原法、热分解法、元素直接反应法(2)液相法:共沉淀法、盐溶液水解法、醇盐水解法、溶
胶-凝胶法、水热合成法、溶剂热法、微乳法、
加热煤油(石油)法、喷雾干燥法、火焰喷雾
法、冷冻干燥法---
(3)气相法:气相合成法、等离子体法、激光制粉
以ZrO2为例:
1. ZrSiO4−
H2Na2SiO3﹒nH2O
−O
−→
−NaOH Na2ZrO3-Na2SiO3−−→
过滤→Na2ZrO3−−→
−HCl过滤掉SiO2gel→ZrOCl2﹒8H2O
−煅烧ZrO2
→结晶纯ZrOCl2﹒8H2O−−→
2.ZrSiO4+4C+4Cl2→ZrCl4+SiCl4+4CO, 再氧化→ZrO2
3.ZrOCl2﹒8H2O, Zr(SO4)2﹒15H2O, ZrCl4 , Zr醇盐等
三、超细粉的测试与表征
1、粒径
沉降法(重力沉降法、离心沉降法)
激光光散射法
显微镜法(光学、电子)
XRD法
比表面积法
2、表面电性Zeta电位
3、表面成分
光电子能谱(XPS、UPS)
俄歇电子能谱
红外光谱
4、成分
化学组成:化学分析、能谱分析、光谱分析、XRF ---
相结构:XRD 、高分辨电镜晶格条纹相---
四、机械粉碎法
超细粉碎粉体特性变化:
粒子由大变小、粒度分布变化、比表面增加、容积变化、形状变化、流动性变化、分散性变化、均匀性(均匀粒子排列)、纯度变化
1、球磨法
2、砂磨(搅拌磨)
3、振动磨
4、星形磨(行星磨)
5、气流粉碎
导向式
单轨道式
机械力化学、机械合金化---
五、化学制备法
1、固相合成法及氧化还原法:
立方ZrO2、MgAl2O4、3Al2O3·2SiO2 - - - Si + C →SiC
SiO2 + 3C →SiC + 2CO
3SiO2 + 6C +2N2→Si3N4 + 6CO
2、热分解法
Al2(NH4)2(SO4)4•24H2O
各种锆盐加热时的存在相和结晶尺寸
3、酒精干燥
4、喷雾干燥法
5、喷雾热分解法
(1)火焰喷雾法(2)等离子体法6、冷冻干燥法
7、加热煤油法、加热石油法
加热石油干燥法制备的ZrO2的平均粒径
组成煅烧温度比表面积s2/g 平均粒径um
硫酸盐6MgO 800℃1h 15.9 0.064 6MgO 1200℃4h 0.89 1.18 12MgO 800℃1h 13.1 0.08 6CaO 1200℃3h 1.46 0.71 6CaO 1200℃4h 0.94 1.12 12CaO 1200℃4h 0.67 1.57
醋酸盐6CaO 1200℃4h 1.71 0.58 12CaO 1200℃4h 1.58 0.65
8、共沉淀法 [Zr 4(OH)8(H 2O)16]8+
[Zr 4(OH)8(H 2O)16]8+−−→−O H 2[Zr 4(OH)16-n (H 2O)n+8]n++(8-n)H +
a.浓度
b. pH 值
c.表面活性剂
d.洗涤
e.脱水
f.硬团聚
g.煅烧温度 9、盐水溶液水解法
ZrOCl 2 + (3+n)H 2O → Zr(OH)4•nH 2O ↓+2HCl ↑ 或 ZrOCl 2 + 3H 2O → ZrO 2•H 2O ↓+ 4HCl ↑ 10、溶胶-凝胶法(Sol – Gel )
金属醇盐:M(OR)n
(1) 金属与醇直接反应 M +nROH = M(OR)n +
2
n H 2 (2) 金属氯化物在氨的存在下与醇反应 MCl n + nROH+nHN 3 = M(OR)n + nNH 4Cl
a. 水解与聚合
水解反应:M(OR)n +xH 2O →M(OH)x (OR)n-x +xROH 失水聚缩反应:-M-OH+HO-M-→-M-O-M-+H 2O 失醇聚缩反应:-M-OH+RO-M-→-M-O-M-+ROH
形成化合物的总反应:
M(OR)n +xH 2O →M(OH)x (OR)n-x +xROH
M(OH)x (OR)n-x →MO n/2+2
x H 2O+(n-x)ROH
b. 凝胶的形成:初始粒子成核、长大、连接成键形成网络
c. 凝胶的干燥
d.煅烧
11、醇盐水解法 12、水热法 (1)水热结晶法 (2)水热分解法
ZrSiO 4 18.43 Ca(OH)2 14.9 NaOH 4.67(浓度7wt%) 液/固比 2 Ca(OH)2/ ZrSiO 4 mol 比 2
温度 350℃ 蒸汽压 170×105Pa 反应时间 8h ZrSiO 4+xCa(OH)2 → ZrO 2+xCaO •SiO 2•H 2O+(x-1)H 2O (3)水热氧化法 Zr+H 2O → ZrO 2+H2 ↘ZrH x +O 2↗ 13、气相反应法
足够的过饱和度 高的平衡常数 反应温度 成核剂
3
/106⎪
⎪⎭
⎫ ⎝⎛•=ρπN M C D
气相反应法制备的ZrO2
反应温
度
ZrCl4
注入温度
气体组成
ZrCl4 O2N2
流量
ml/min
粒径
nm
四方
相
1100 1100-1250 0.6 54.2 45.2 221 5-25 100 1100 1100-1250 0.7 52.5 46.8 229 4-8 100 1100 600 1.2 53.9 45.3 223 40-180 10 1100 600 1.2 89.8 9.0 223 120-800 7
六、高熔点氮化物及碳化物微粉体的合成
氮化物、碳化物微粉的制造法。